Morphology and structure of high temperature MoSi2 coating on niobium
XIAO Lai-rong(肖来荣), YI Dan-qing(易丹青), YIN Lei(殷 磊), CAI hi-gang(蔡志刚)
(College of Materials Science and Engineering, Central South University, Changsha 410083, China)
Abstract: The high-temperature oxidation-resistant MoSi2 coating on the Nb substrate was prepared by slurry firing. The structure, compositions and phase distribution of the coating and the relationship between these features and the oxidation resistance of the coating were investigated by SEM, EDS and XRD. The results indicate that the interface between the coating and the substrate has metallurgic combination, and a transitional layer is formed by diffusion. The multi-layer structure improves the oxidation resistance of the coating. The method of slurry firing to prepare the high-temperature MoSi2 coating on Nb is feasible. The SiO2 scale, which is formed on the surface of the coating by the self-oxidation of MoSi2, prevents the further diffusion of oxygen.
Key words: Nb; high temperature oxidation resistance; MoSi2; coating CLC number: TG174.44
Document code: A
1 INTRODUCTION
Nb and Nb-based alloys are important high temperature structural materials due to their high melting point, good corrosion resistance and high temperature strength. But the applications are limited by their poor oxidation resistance[1-5]. A great deal of work has been done by many researchers. The alloying method can improve the oxidation resistance properties of the Nb-based alloys greatly. But the modified alloys still cant be used above 1200℃. On the other hand, the mechanical properties would be decreased with a great deal of modified elements. The protective coating is an effective method to insure the high temperature application of the Nb-based alloys[6, 7] .
Compared with other coating systems, the protective effect of the silicide coating is better. The R512A(Si-20Cr-5Ti) and R512E(Si-20Cr-20Fe) silicide systems have been successfully applied to the orbital attitude control engine of the spaceship and the satellite[8-11]. With the requirement for the improvement of high speed and stability on the advanced aerospace, the further investigations of the corresponding coating materials and technologies should be put on the plan as soon as possible. MoSi2, which has been widely used as a heating component, is a promising candidate for oxidation resistant coating materials. With the protective SiO2 scale formed, MoSi2 can work above 1600℃. Tiwari and Herman[12] study the MoSi2 coating prepared by plasma spraying. Although the coating showed good high-temperature oxidation resistance, the problems of destructive pest oxidation and poor mechanical properties are of critical concern. Andrew et al[13] sputtered a Mo-W layer on the surface of Nb substrate, then embedded the sample in the Ge and Si composite powder to prepare a modified MoSi2 coating. Brian et al[14, 15] studied B-modified and Ge-doped silicide coatings by pack cementation method. Among the different surface technologies, each process has its own characteristics. Powder packed cementation method needs the sample to anneal at high temperature for a long time, so the mechanical performance of the substrate is easily damaged during longer production cycle. The change of the composites is limited for the coating prepared by chemical vapor deposition. As novel surface technologies, plasma spraying and laser melting overlay are not easy to get close coating. Another shortage of these methods is that they are very difficult to treat the parts with complex shapes, especially with an inner chamber. Compared with those methods above, the slurry firing is more suitable to prepare the silicide system coating. This technology can solve the problem of complex shapes, changeable compositions and high melting point of the silicide[16]. In our work we selected MoSi2 as a coating system, used the slurry firing to produce a high temperature oxidation resistant coating on the Nb substrate. The morphology, structure and compositions of the coating are studied, and the effect of these characteristics on the properties of the sample is also studied.
2 EXPERIMENTAL
The particle size of the initial MoSi2 powders is about 50μm, and the purity is above 99.9%. The powders added by some contents of addition agents are mixed to form slurry by ball milling. A sheet of pure niobium(99.9% in mass fraction) was rolled to 2mm in thickness, and cut into pieces of 8mm×10mm. The sample surface was pretreated, and then was dropped into the slurry to cover an uniform thin layer. After drying, the sample was put into a vacuum furnace above 1700℃ to form a MoSi2 coating on Nb substrate.
Before the oxidation resistant testing, the Al2O3 crucible which contained the coating sample should be calcined to 1200℃ for several hours. The coating samples were pushed into the furnace at 1500℃ in air condition until the yellow powders appeared on the surface of the sample. Both the original coating and the samples after oxidation testing were examined by KYKY-2800 scanning electron microscope(SEM) equipped with an energy dispersive X-ray(EDX) analyzer. The phases on samples surface were identified by SIMENS-500X X-ray diffractometry(XRD) with CuKα radiation(λ=1.5406).
3.1 Morphology and structure of original coating
The morphology of the original coating is shown in Fig.1. The surface of the coating is very coarse, most of the parts consist of the incoherent fusing island,and many globular particles can be seen at the edge of the island (Fig.1(a)). Some microholes can be seen in Fig.1(b). The analyses by XRD and EDS show that the incoherent islands are MoSi2, and those globular particles are impurity Fe. The morphology and the compositions of the original coating surface have close relations with the coating system and the technology. Due to the ball milling in the slurry, the impurity Fe has been added during impact and friction happens between the ball and the tin. Compared with the high melting point of phase MoSi2 (2047℃), the melting point of Fe is too low to affect the profiles of the coating. The coating prepared by slurry firing is formed by diffusion reaction between the solid and the liquid phases. In other words, the silicide coating is formed by the diffusion reaction between the silicide fused mass and Nb substrate when the treatment temperature is high enough. During the cooling process, the high melting point MoSi2 phases contract. Great thermal stress concentration comes into being, and the interfaces among the particles are broken. As the result, the coarse inherent island and many microholes can be seen on the surface of the coating. On the other hand, the relative low-melting-point Fe is difficult to infiltrate with MoSi2, and is discharged to the surface with liquid phase to form globular particles.
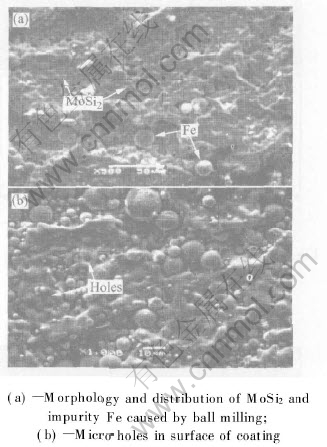
Fig.1 Original surface morphologies of MoSi2 coating on Nb substrate
The structure of the original MoSi2 coating on Nb substrate is shown in Fig.2. It can be seen from the SEM photograph of the cross-section (Fig.2(a)) that the coating has typical double-layer structures, and its thickness is about 85μm. The dark outer layer which is the body of the coating consists of MoSi2 with an average thickness of 70μm. Between the MoSi2 layer and the substrate was the transitional layer which consists of (Mo, Nb)5Si3. This layer is about 15μm thick, and combines very tightly with the substrate. Some bright prominence parts are the flaws produced during the fabrication of the SEM sample. The sketch of the structure is also given (Fig.2(b)). But no Fe is found in coating. The reason is that the impurity Fe is nonwettable with MoSi2. During the slurry-firing processing, nearly all Fe elements are discharged to the surface of the coating.
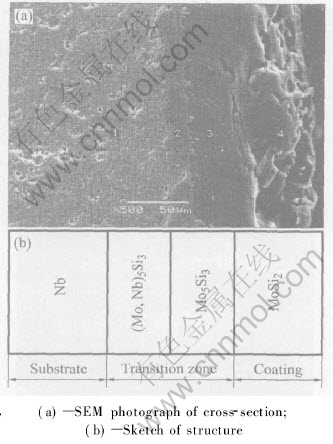
Fig.2 Structure of original MoSi2 coating on Nb substrate
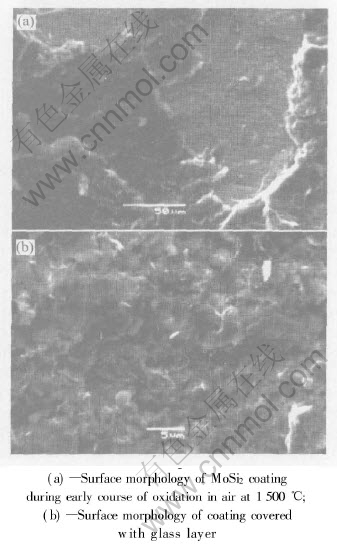
Fig.3 Surface morphologies of MoSi2 coating on Nb substrate after exposure at 1500℃
3.2 Transformation of morphology and structure of coating during oxidation
The surface morphology of the MoSi2 coating on Nb substrate after exposure at 1500℃ is shown in Fig.3. The morphology and structure of the coating change greatly after the oxidation testing. The surface of the coating is smoother compared to Fig.2, but some part of the coating flake off (Fig.3(a)). The high magnification SEM image shows not too much holes exist on the surface. The further analyses by XRD show that a thin glass SiO2 layer covers on the coating. During the high temperature oxidation atmosphere, the following reactions happen in the coating:
3Fe+2O2=Fe3O4(1)
5/7MoSi2+O2=1/7Mo5Si3+SiO2(2)
MoSi2+7/2O2=2SiO2+MoO3(3)
When the MoSi2 coating is exposed to high temperature oxidation atmosphere, a SiO2 scale is formed on the surface. This scale with liquidity can seal a part of the micro-holes on the outer layer. But the impurity Fe is oxidized rapidly, and the coarse surface of the coating provides the path for the oxygen to penetrate into the inner coating. Some part of MoSi2 can not supply enough SiO2 to form a glass layer on the outer layer. As a result, some area scale off after exposed to high temperature air in a short time, and the anti-oxidation property of the coating is descended.
The structure of the MoSi2 coating on Nb substrate after exposure in air at 1500℃ is shown in Fig.4. It can be seen from the SEM photograph of the cross-section that a porous structure appears in the layer of the coating after exposure to high temperature air. The thickness increases to about 30μm, and many cavities appear in the interface between the substrate and the transitional layer. The porous structures can effectively reduce the elastic modulus of the layer, and improve the thermal shook property of the coating. The formation of the loosen structure in the coating is relative to the diffusion of Si element. The diffusion of Si atoms through the silicide needs the reverse flow of the vacancy in the sublattices or the movement along the grain boundary. The cavities are formed by the gradual aggregation of vacancies in a gross. The formation of the continuous low silicides in coating is due to the short-distance diffusion of Si atoms. There is one thing to be noticed that the double-phase zone can not exist in the diffusion zone of binary system. In other words, each layer is single-phase zone. From the view of the thermodynamics, the driving force of the diffusion is chemical potential gradients. The diffusion is induced by the difference of the chemical potential gradients, and the atoms of the variant components always diffuse from high chemical potential zone to low chemical potential zone. According to the phase rule, if a double phase mixture zone which is composed of the two phases with same chemical potential exists at a certain temperature, the chemical potential gradients should be zero, i.e. dμ/dx=0 . There is no driving force of the diffusion, and the diffusive flux is zero, so the diffusion can be interrupted in this zone. But the assumption does not agree with the fact. So the double phase mixture zone can not appear in the variant layer of the MoSi2 coating. The double phase zone only exists in the system with two or more components. The quarter-phase structure can provide the rapid path for the diffusion of Si element in the interfaces of the coating, promote the formation of the Nb5Si3 transitional layer, and also accelerate the formation of the cavities and the consumption of Si element near the interface between the coating and the substrate.
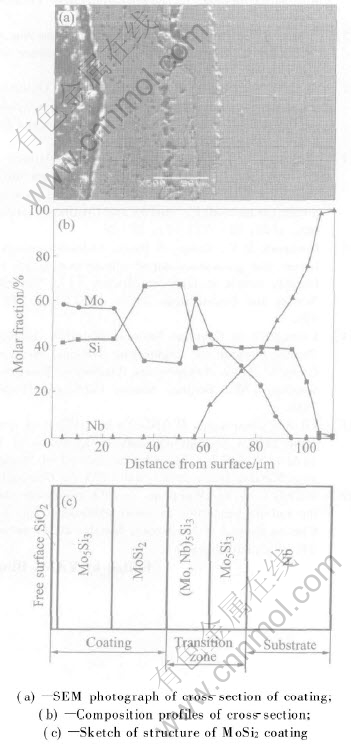
Fig.4 Structure of MoSi2 coating on Nb substrate after exposure in air at 1500℃
After exposed to the high temperature air for several hours, some massive areas scale off. But the coating can still withstand the oxidation for a short time. The structure of the MoSi2 coating breaks through the interface between the coating and the transitional layer as shown in Fig.5. It can be seen that a Nb5Si3 transitional layer still exists at the outer zone of the substrate. The coating is broken at the interface between the outer layer and the transitional layer. The Si element of the coating diffuses to Nb substrate continuously, and the low silicide transitional layer is formed due to the reaction of the Si and Nb. Great deal of continuous and dense cavities are formed in the interface between the outer layer and the transitional layer. As the time expands, these cavities perforate transversely, so the coating breaks through the interface and scales off. As the oxidation time prolongs further, the yellow powder appears on the surface of the sample, and the coating is invalidated. The analyses of EDS and XRD show that the yellow powder is Nb2O5. The morphology of the oxide on the surface of Nb substrate after the invalidation of the MoSi2 protective coating is shown in Fig.5(b). It can be seen that a great deal of disorderly coarse arborescent crystals grow to the outer surface. Because of the characteristic of the Nb2O5, the oxygen can penetrate into the inner zone, and the substrate “pest” oxidation rapidly.
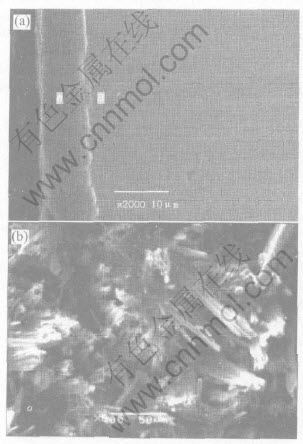
Fig.5 Structure of MoSi2 coating after coating breaks interface between coating and transitional layer(a); and morphology of oxide on surface of Nb substructure after invalidation of MoSi2 protective coating(b)
4 CONCLUSIONS
The interface between the coating and the substrate has metallurgic combination, and a transitional layer is formed by diffusion. The multi-layer structure improves the oxidation resistance of the coating. The method of slurry firing to prepare the high temperature MoSi2 coating on Nb is feasible. The SiO2 scale, which is formed on the surface of the coating by the self-oxidation of MoSi2, prevents the further diffusion of oxygen. After a long time exposure in high temperature oxidizing environment, the porous microstructure is formed as a result of the diffusion of silicon in the coating. As further inter-diffusion of the element between the coating and the substrate, a large number of cavities are formed and perforated transversely. The coating breaks through the interface between the outer coating and the transitional layer.
REFERENCES
[1]FENG Jing-su. The recent advance in application of niobium [J]. Rare Metal Materials and Engineering, 1994, 23(3): 7-12.(in Chinese)
[2]QU Shi-yu, WANG Rong-ming, HAN Ya-fang. Recent progress in research on Nb-Si system intermetallics [J]. Materials Review, 2002, 16(4): 31-34.(in Chinese)
[3]Subramanian P R, Mendiratta M G, Dimiduk D M. The development of Nb-based advanced intermetallic alloys for structural applications[J]. JOM, 1996, 48(1): 33-38.
[4]QU Nai-qin. Properties and applications of Ta/Nb and their alloys [J]. Rare Metals and Cemented Carbides, 1998,133(6): 48-54.(in Chinese)
[5]HUANG Hong, HUANG Jin-chang. Nb-based composite for aeronautics and space propulsion system [J]. Rare Metals and Cemented Carbides, 1999, 138(9): 61-65.(in Chinese)
[6]YIN Lei, YI Dan-qing, XIAO Lai-rong, et al. Progress in research on high temperature oxidation resistance of Nb and Nb-based alloys [J]. Materials Protection, 2003, 6(8): 4-8.(in Chinese)
[7]McDonald W K. Fabrication of niobium and niobium alloys [J]. International Journal of Refractory & Hard Metals, 1982, 1(3): 119-122.
[8]ZHAI Jin-kun, MA Xiang, BAI Xin-de , et al. Studies of modified Si-Cr-Ti slurry fusion coating on C-103 niobium alloys [J]. Acta Aeronautica et Astronautica Sinica, 1994, 15(4): 499-506.
[9]WANG Yu, GAO Jia-ping, LI Yun-peng, et al. Microstructure and oxidation-resistance of silicide coating on C-103 niobium alloys [J]. Journal of Inorganic Materials, 2000, 15(2): 143-149.(in Chinese)
[10]WANG Yu, GAO Jia-ping, LI Yun-peng, et al. Study on heat resistance of modified Ti-Cr-Si silicide coatings on C-103 niobium alloys [J]. Chinese Journal of Space Science, 2000, 20(3): 262-270.(in Chinese)
[11]JIA Zhong-hua. High-temperature oxidation-resistant coatings for columbium alloys and molybdenum alloy with slurry method [J]. Powder Metallurgy Technology, 2001, 19(2): 74-76.(in Chinese)
[12]Tiwari R, Herman H. Vacuum plasma spraying of MoSi2 and its composites[J]. Materials Science and Engineering, 1992, A155(1-2): 95-100.
[13]Andrew Mueller, Ge Wang, Robert A R. Oxidation behavior of tungsten and germanium-alloyed molybdenum disilicide coatings[J]. Materials Science and Engineering, 1992, A155: 199-207.
[14]Cockeram B V. Growth and oxidation resistance of boron-modified and germanium-doped silicide diffusion coatings formed by the halide-activated pack cementation method[J]. Surface and Coatings Technology, 1995, 76-77(1-3): 20-27.
[15]Cockeram B V, Robert A Rapp. Oxidation-resistant boron- and germanium-doped silicide coating for refractory metals at high temperature [J]. Materials Science and Engineering, 1995, A192(19): 980-986.
[16]Committee on Coatings National Materials Advisory Broad, Division of Engineering National Research Council. High Temperature Oxidation Resistance Coatings [M]. Beijing: Science Publishing House, 1980.
[17]GUAN Chun-hong, WANG Fu-hui. Effect of sputtered TiAlCr coatings on oxidation resistance of Ti-24Al-14Nb-3V[J]. The Chinese Journal of Nonferrous Metals, 1999, 19(2): 249-252.(in Chinese)
[18]MENG Lin, YU Wei-ping. Zn-SiO2 composite coating and its properties to resist oxidation [J]. The Chinese Journal of Nonferrous Metals, 2003, 13(4): 992-995.(in Chinese)
(Edited by YANG Bing)
Foundation item: Project(20010533003) supported by the Special Research Foundation of PhD Study
Received date: 2004-08-27; Accepted date: 2004-10-26
Correspondence: XIAO Lai-rong, Associate Professor; Tel: +86-731-8830263; E-mail: xiaolr368@sina.com