J. Cent. South Univ. Technol. (2007)02-0153 -04
DOI: 10.1007/s11771-007-0031-2 
Special epoxy silicone adhesive for inertial confinement fusion experiment
LI Zhi-hua(李芝华)1, LI Bo(李 波)2, ZHENG Zi-qiao(郑子樵)1
(1. School of Materials Science and Engineering, Central South University, Changsha 410083, China;
2. Institute of Nuclear Physics and Chemistry, China Academy of Engineering Physics, Mianyang 621009, China)
Abstract: The effects of toughener and coupling agent on special epoxy silicone adhesive were discussed by researching the surface morphology characters, thermal properties and shear strength of the adhesive. The results indicate that silicone coupling agent (KH-550) can improve the shear strength of the epoxy silicone adhesive effectively. The mass fraction of the toughener in the epoxy silicone adhesive plays an important role in its properties. When the mass fraction of the toughener is less than 14%, the shear strength of the adhesive is low. When the mass fraction of the toughener is over 33%, thermal properties and shear strength of the adhesive decrease with the increasing of the toughener. The mass fraction of toughener of 25% results in good integral properties of the epoxy silicone adhesive. The morphologic analysis indicates that the micro-phase separation exists in the epoxy molecular chain and the silicone molecular chain of the epoxy silicone adhesive.
Key words: inertial confinement fusion experiment; epoxy silicone; toughener; coupling agent; micro-phase separation
1 Introduction
The special epoxy silicone adhesive for inertial confinement fusion (ICF) experiment must satisfy the following requirements: low curing temperature, high-temperature resistance, excellent gas-holding properties[1], etc. So it presents higher demand to prepare the special adhesive. At present, the research of this special adhesive is vacant in China. The special sealing adhesive developed for the application in the inertial confinement fusion experiments is necessary.
In this paper, a special epoxy resin adhesive consisting of epoxy silicone[2-5], curing agent[6-7], toughener[8] and coupling agent[9], was prepared for the application in the inertial confinement fusion experiment. The effects of the coupling agent and mass fraction of toughener on low-temperature resistance, high- temperature resistance and mechanical properties were discussed by researching the surface morphology characters, thermal properties and shear strength of the adhesive. Meanwhile, the relationship of the material structure and properties was also discussed.
2 Experimental
2.1 Raw materials
Epoxy silicone (tech grade, epoxy value: 0.03-0.08, Dalian Institute of Light Chemical Engineering), curing agent T31 (Changsha Institute of Chemical Engineering), toughener 6350 (active epoxy resin with soft segment, epoxy value: 0.36-0.42, Shanghai Zhengrui Chemical Co. Ltd), and coupling agent KH550 (Zhejiang Institute of Chemical Engineering) were used as raw materials.
2.2 Preparation of adhesive
The adhesive was made from two components: A and B. The basic formulation is given in Table 1. A certain amount of epoxy silicone resin, toughener and coupling agent were mixed together by vigorous stirring to obtain component A, and component B was the curing agent. An emulsion was obtained by mixing the components A and B according to the ratio presented in Table 1. Films were prepared by coating the emulsion onto Teflon plate, followed by curing at room temperature for 24 h. The resulted film was cut into square pieces with size of 1 cm2 for test.
2.3 Characterization of adhesive
2.3.1 Shear strength
An aluminum alloy LY-12 was used as adherend, the sample was fed with WD-10A feeding machine. The value of shear strength was collected according to the GB7124-86 standard.
2.3.2 Surface morphology of adhesives
Samples 2 and 3 of the adhesive were treated by different curing and thermal treatment processes: process 1 (cured at room temperature) and process 2 (cured at 60 ℃, heated to 200 ℃, then cooled at -196 ℃). The morphology of the resulted samples was observed using an optical microscopy (OM).
Table 1 Formulation of adhesive (g)
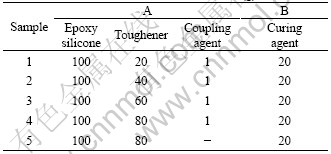
2.3.3 Thermal property
The thermal analysis was performed on a DT-40 thermal analytical system, the heating rate was 10℃/ min.
3 Results and discussion
3.1 Mechanical properties of adhesives
Shear strength is an important factor for the mechanical properties of the adhesive. The testing results of the adhesive’s shear strength under different methods of curing and thermal treatment are given in Table 2.
Table 2 Testing results of adhesive’s shear strength
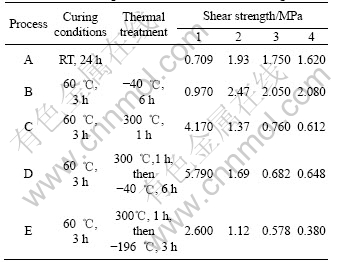
3.1.1 Effect of toughener
From sample 1 to sample 4, the mass fractions of toughener are 14%, 25%, 33%, 40%, respectively. It’s shown in Table 2 that the shear strength of samples 2, 3 and 4 is close after cured in the room temperature or cured at 60℃ and disposed in –40℃ for 6 h. The shear strength of samples 2, 3 and 4 is higher than that of sample 1. Sample 1 with the lowest shear strength is because the mass fraction of the toughener in sample 1 is less.
In processes C, D and E shown in Table 2, all the samples were heated at 300 ℃ for 1 h. It is found that the shear strength decreases gradually with the content increase of the toughener, that is because the toughener is a kind of epoxy resin with soft segment which has relatively low thermal property[10].
The shear strength of the sample 1 cured at 300 ℃ is higher than that cured at room temperature. Because the content of toughener in sample 1 is relative low, the component with low thermal property is less and the adhesive has a good heat resistant, at the same time, the adhesive is cured more perfectly with high-temperature treatment, so the shear strength of the adhesive is improved. With the increasing of the toughener , the component with low thermal property increases, the heat resistant properties of the adhesive declines. So the shear strength of all the adhesives decreases after the sample is heated to 300 ℃. Through the processes C, D and E, the shear strength of sample 2 decreases less compared with the shear strength at the room temperature. This result indicates that sample 2 retains good mechanical properties. Compared with the shear strength at room temperature, the shear strengths of sample 3 and 4 after the process C or E decrease remarkably. The shear strength of sample 3 decreases by 56.6%, 66.9% respectively. The shear strength of sample 4 decreases by 66.7%, 76.5% respectively. The results indicate that the mechanical properties of samples 3 and 4 become worse under high or very low temperature.
3.1.2 Effect of coupling agent
As shown in Table 1, the only difference of the formulation between samples 4 and 5 is the coupling agent, sample 4 has coupling agent, but sample 5 has not. The shear strength of sample 4 is higher than that of sample 5 under all the treatments(Table 3). It is indicated that the coupling agent improves the mechanical properties of the adhesives effectively.
Table 3 Comparison of shear strength of samples 4 and 5
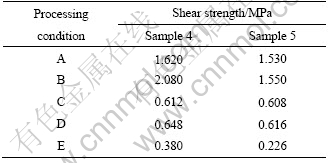
The coupling agent KH-550 is a kind of amino-substituted silane with the chemical structure shown in Fig.1. There are two different groups in the molecular structure. One is inorganophilic siloxane, and the other is organophilic γ-aminopropyl triethoxy(Y). The inorganophilic group becomes Y—Si—(OH)3 after hydrolysis, and the product reacts with the hydroxyl of the metal to form Si—O—Me. It improves the adhesive strength. The organophilic group on the other end can react with the epoxy resin. KH-550 can form a transition phase in the epoxy silicone resin system to improve the miscibility between the epoxy resin and the organic silicone resin, which also results in high shear strength.
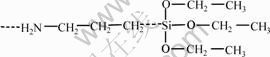
Fig.1 Stucture of KH550
3.2 Characteristics of morphology of adhesives
The optical microscopy images of samples 2 and 3 are shown in Fig.2.
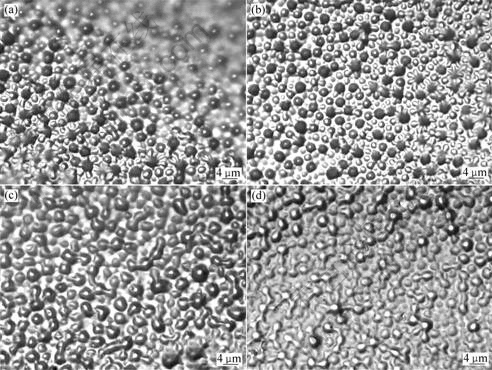
Fig.2 OM images of adhesive with different curing processes
(a) Sample 2 cured at room temperature;
(b) Sample 2 cured at 60 ℃, then high temperature (200 ℃) treated for 2 h and low temperature (-196 ℃) treated for 3 h;(c) Sample 3 cured at room temperature;(d) Sample 3 cured at 60 ℃, then high temperature (200 ℃) treated for 2 h and low temperature (-196 ℃) treated for 3 h
As shown in the OM images, there is no crack on the surface of the two materials. The epoxy silicone organic compound, used in this study, is from the chemical modification of the epoxy resin and methyl phenyl siloxane in organic solvent. The main-chain of this resin is Si—O bond, epoxy group is introduced to the side-chain and end-group. So this kind of material has relatively strong adhesion, and high- and low- temperature resistance.
A multi-phase system is found in the two materials by comparing the OM images. This is due to the large difference of the solubility between the epoxy resin and the silicone compound. The two components can not dissolve each other, so a multi-phase system forms between organic silicone and epoxy resin. The phases of samples 2 and 3 are well dispersing, but the phase separation degree is bigger for samples 2 and 3. This is because the organic silicone and epoxy resin are connected with a chemical bond, and a strong interaction exists in the interface between the two phases[11-12]. The difference of the phase separation degree is due to the contents of the toughener and the curing agent. The increase of toughener results in the decrease of crosslinking degree in the system, and the decrease of the crosslinking points between organic silicone and epoxy resin results in a worse miscibility of the two components, so the phase separation degree becomes bigger.
3.3 Thermal analysis of adhesives
The thermogravimetric analysis results of the adhesives are listed in Table 4. The thermal decomposing temperatures of all the samples are around 300 ℃, showing good high-temperature durability. The bonding energy of Si—O—C bond in the epoxy silicone resin is high, which results in the high decomposition temperature[13-14]. The thermostability decreases slightly along with the increase of toughener. This is because the toughener is a kind of epoxy resin with low thermal property. So the mass fraction increasing of the toughener results in bad thermostability of the epoxy silicone adhesive[15-16].
Table 4 Thermogravimetric analysis results of adhesives
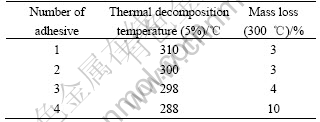
4 Conclusions
1) The epoxy silicone adhesives designed appear micro-phase separation between the epoxy molecular chains and silicone molecular chains.
2) The mass fraction of the toughener in the epoxy silicone adhesive plays an important role in the properties. The thermal decomposition temperatures of the adhesive decrease with the increasing of the toughener mass fraction. When the mass fraction of the toughener is less than 14%, the shear strength of the adhesive is low. When the mass fraction of toughener is over 33%, the thermal properties and shear strength of the adhesive decrease with increasing of toughener. The toughener mass fraction of 25% results in good integral properties of the epoxy silicone adhesive.
3) Silicone coupling agent (KH-550) can effectively improve the bonding strength of the interface between adhesive and substrate and the mechanical properties of the epoxy silicone adhesive.
References
[1] LIU Cai-lin, WU Wei-dong, MAO Ying, et al. Hydrogen Isotopes Low Permeation Polymer Materials[J]. Material Review, 1998, 12(6): 53-55. (in Chinese)
[2] LI Zhi-min, LIU Wen-xi, CHEN Yu-ru. The toughening materials of epoxy adhesives[J]. China Adhesives, 2003, 5(12): 46-48. (in Chinese)
[3] OCHI M, SHIMAOKA S. Phase structure and toughness of silicone-modified epoxy resin with added silicone graft copolymer[J]. Polymer, 1999, 40(5):1305-1312.
[4] CHEN Wei-jun, ZHANG En-tian, GUO Xu, et al. The research present state and the development trend of Two part room temperature curing epoxy adhesives[J]. Chemistry and Adhesion, 2000, 3(10): 127-129.(in Chinese)
[5] HUANG Yue-wen. Silicone adhesives[J]. Chemistry and Adhesion, 2001( 1): 25-28.(in Chinese)
[6] ZHU Ming, ZHAO Shi-qi, ZHANG Wei. Study of adhesion of T31 epoxy resin cured at ambient temperature[J]. Chemistry Materials for Construction, 2000(3): 27-30. (in Chinese)
[7] HE Ping-sheng, LI Chun-e, OU Run-qing, et al. Study on T31-epoxy resin system[J]. Chemistry and Adhesion, 1996(4): 187-189.(in Chinese)
[8] ZHANG Bao-long, TANG Guang-liang, SHI Ke-yu,et al. Studies on properties of epoxy resin modified by a modifier containing liquid crystalline unit—influence of the molecular weight of the flexible chains[J]. Acta Scientiarum Naturalium Universitatis Nankaiensis, 1999, 32(2): 1-5.(in Chinese)
[9] LI Hai-bing, CHEN Yuan-yin. The sol-gel technique to prepare calyx[6]crown-containing organosilicon resins and their adsorption properties towards metal ions[J]. Reactive & Functional Polymers, 2003, 55(2): 171-178.
[10] ZHANG Qiu-yu, ZHANG He-peng, XIE Gang, et al. Effect of surface treatment of magnetic particles on the preparation of magnetic polymer microspheres by miniemulsion polymerization[J]. Journal of Magnetism and Magnetic Materials, 2007, 311(1): 152-157.
[11] OCHI M, TAKAHASHI R, TERAUCHI A. Phase structure and mechanical and adhesion properties of epoxy/silica hybrids[J]. Polymer, 2001, 42(11): 5151-5158.
[12] ROBERT C, CRESPY A, BASTIDE S, et al. Adhesive properties of silicone polymers on some typical opto-eletronic substrates: influence of the network density[J]. International Journal of Adhesion & Adhesives, 2004, 24(1): 55-68.
[13] ANANDA KUMAR S, DENCHEV Z, ALAGAR M. Synthesis and thermal characterization of phosphorus containing siliconized epoxy resins[J]. European Polymer Journal, 2006, 42(10): 2419-2429.
[14] ZHANG Bing, LIU Xiang-luan, HUANG Ying. Effects of the amino group content of polydimethylsiloxane bearing pendant amino groups on the morphology and properties of modified epoxy resin[J]. Journal of Functional Polymers, 2000, 13(1): 69-72.(in Chinese)
[15] ANANDA KUMAR S, SANKARA NARAYANAN T S N. Thermal properties of siliconized epoxy interpenetrating coatings[J]. Progress in Organic Coatings, 2002, 45(4): 323-330.
[16] WANG W J, PERNG L H, HSIUE G H, et al. Characterization and properties of new silicone-containing epoxy resin[J]. Polymer, 2000, 41(16): 6113-6122.
Foundation item: Project supported by the National High-Tech Research and Development Program of China
Received date: 2006-03-28; Accepted date: 2006-05-29
Corresponding author: LI Zhi-hua, PhD; Tel: +86-731-8830838; E-mail: ligfz@mail.csu.edu.cn
(Edited by YUAN Sai-quan)