Trans. Nonferrous Met. Soc. China 23(2013) 3592-3597
Microstructure evolution of semi-solid 7075 Al alloy slurry during temperature homogenization treatment
Bin YANG, Wei-min MAO, Xiao-jun SONG
School of Materials Science and Engineering, University of Science and Technology Beijing, Beijing 100083, China
Received 4 January 2013; accepted 6 June 2013
Abstract: Semi-solid 7075 Al slurry was prepared by inverted cone-shaped pouring channel process (ICSPC) and temperature homogenization (TH) treatment was combined to make the slurry uniform and have a controllable solid fraction suitable for the follow-up rheocasting. The influence of cooling rate on the microstructure evolution of primary α(Al) during TH treatment was investigated. The results show that as the cooling rate of the slurry after being prepared reduces, the growth of primary α(Al) in the slurry tends to be nearly spherical and the uniformity of the organization is also enhanced. This may be due to the fact that lower cooling rate plays an important role in achieving the uniformity of temperature and composition in the remaining liquid, which is crucial to the formation of the spherical and homogeneous microstructure. However, a too low cooling rate will lead to a significant increase in grain growth time, which makes too coarse grains and more particles coalesce, so a certain abnormal growth of grain appears and the shape factor decreases slightly.
Key words: semi-solid slurry; 7075 Al alloy; microstructure; primary α(Al)
1 Introduction
Semi-solid metal (SSM) processing has been recognized as a unique manufacturing method to produce near-net-shape products for various industrial applications [1]. Compared with conventional die-casting, SSM processing has a number of advantages, such as low porosity, heat treatability, consistency and soundness of mechanical properties, the ability to make complex component shapes and longer die life [2-5]. A356/357 alloys are the most popular alloys used for SSM forming due to their high fluidity and good castability. However, one of the main advantages of SSM processing is that it is possible to produce near-net-shape components from alloys that are conventionally wrought (such as the 2000, 6000 and 7000 series) [6,7].
Because of a higher sensitivity of the liquid fraction to temperature fluctuation [8] and relatively wide crystallization temperature interval which can lead to hot tearing, thixoforming of 7xxx series wrought aluminum alloys has not been available in industrial application. In recent years, rheocasting process has increasingly gained attentions from many researchers because of less investment and lower raw material cost compared with thixocasting process. And various techniques for semi-solid slurry preparations of wrought aluminum alloy was proposed such as continuous rheoconversion process (CRP) [9], semi-solid rheocasting process (SSR) [10], low superheat pouring with a shear field process (LSPSF) [11], inverted cone-shaped pouring channel process (ICSPC) [12].
The present work focuses on high-strength 7075 alloy as the most common wrought aluminum alloy has a great potential to be utilized in aircraft structural parts and other highly stressed applications where very high strength and good resistance to corrosion are required. However, the difficulties in rheoforming of this alloy centre on the high sensitivity of the liquid fraction to temperature fluctuation which can lead to hot tearing and make the quality of the slurry unstable [8]. In this work, a controllable temperature homogenization treatment on the slurry after being prepared is used to obtain a certain liquid fraction and keep the uniform quality of the slurry. The purpose is to investigate the influence of subsequent temperature homogenization treatment on the solidification behavior of semi-solid 7075 aluminum alloy slurry in relation to the final microstructures.
2 Experimental
Commercial wrought 7075 aluminum alloy (5.9% Zn, 2.2% Mg, 1.7% Cu, 0.35% Fe, 0.1% Si, Al balance; mass fraction) was used for the present investigation. The solid fraction-temperature relationship was determined by differential scanning calorimetry (DSC). Samples of about 5 mm in diameter and 20 mg in mass were cut, weighed and put into carbon pans with carbon lids in an argon atmosphere. The DSC tests were carried out using a Dupont 910 differential scanning calorimeter. The samples were heated to 680 °C at 10 °C/min and cooled to room temperature at the same rate. The heat flow and temperature were monitored by thermocouples to obtain heating and cooling curves. And the curve of solid volume fraction versus temperature was obtained by integrating under the curves mentioned above, as shown in Fig. 1.
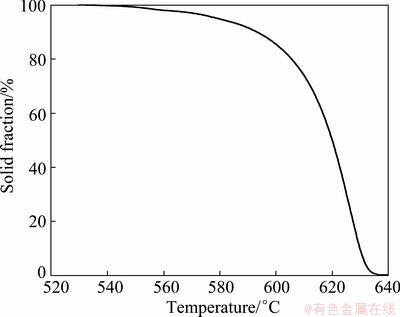
Fig. 1 Solid fraction against temperature of 7075 Al alloy estimated from DSC heating curve
In the present study, the semi-solid slurry was prepared by ICSPC process. The ICSPC equipment mainly consists of a pouring cup, diversion unit and a conical tube. Detailed description of the ICSPC slurry preparation process can be found in Ref. [12]. The 7075 alloy was melted using an electric resistance furnace at 750 °C, cooled to desired pouring temperature (660 °C) and poured into the ICSPC equipment. The length and taper of the conical tube were 400 mm and 4°, respectively. Then the melt flowing through out of the channel was collected in a slurry holder (d80 mm×60 mm) which contained heating and cooling elements to control the temperature accurately and obtain different cooling rates. The initial temperature of the slurry holder was 20 °C. When the semi-solid slurry held in the slurry holder reached a specific temperature at different cooling rates, the metallographic samples were taken by sucking a small amount of semi-solid slurry into a quartz tube with diameter of 6 mm and then quenched in water. Three samples were taken from the edge to the core part at the same process parameter to make sure that the representative microstructure of the slurry can be obtained. All the metallographic samples were then prepared by the standard technique, etched with 0.5% HF aqueous solution, and were characterized using an optical microscope with quantitative analysis system. The shape factor was calculated using F=4πA/P2, where A and P represent the area and perimeter of the primary α(Al) grain, respectively.
3 Results and discussion
3.1 Preparation of 7075 alloy semi-solid slurry
The inverted cone-shaped pouring channel (ICSPC) slurry preparation process is an innovative non-stirring SSM processing technique which can prepare excellent semi-solid slurry within just a few seconds. Compared with other processes, ICSPC process possesses such superiorities as short time, high efficiency and homogeneous microstructure. Furthermore, it is convenient to combine ICSPC equipment with conventional die-casting machine to develop rheo- diecasting process. There are three important parameters in ICSPC, including the pouring temperature, the length of channel and the taper of conical tube. The combination effects of the three parameters on semi-solid microstructure of 7075 Al alloy were deeply investigated in Ref. [12]. Figure 2 shows the typical microstructures of 7075 Al alloy produced by the ICSPC process, in comparison with the commercial starting material. It can be seen that under the optimized conditions, ICSPC can produce superior semi-solid slurry of 7075 Al alloy. The primary α(Al) presents in a mean equivalent diameter of 62 μm and shape factor of 0.78, and features zero-entrapped eutectic.
3.2 Effect of cooling rate on semi-solid microstructure
When the 7075 Al alloy melt flew throughout the ICSPC equipment, the sound semi-solid slurry was obtained and collected in the slurry holder, then different average cooling rates were selected by controlling the temperature of the slurry holder. Metallographic samples were prepared at different specific slurry temperatures and the quantitative metallographic results are illustrated in Fig. 3. It can be seen from Fig. 3(a) that as the slurry temperature decreases, the grain size of the primary α(Al) shows a significantly increase, and a relatively high cooling rate means a shorter cooling time for the primary α(Al) to grow up, so the grain size of the primary α(Al) seems much smaller. However, under the higher cooling rate (e.g. 8.25 °C/s, 2.20 °C/s), the morphology of the primary α(Al) deteriorates significantly, and the shape factor is generally below 0.6, as shown in Fig. 3(b). When the cooling rate is less than 0.55 °C/s, the primary α(Al) is mainly spherical or near-spherical and the shape factor is generally above 0.8. Figure 4 shows the morphologies of the semi-solid slurries at 600 °C with different cooling rates. The results indicate that the average cooling rate of the slurry has an important influence on the microstructures and a lower cooling rate can promote the transformation of primary α(Al) grain from a dendrite or a rosette to a spherical one.
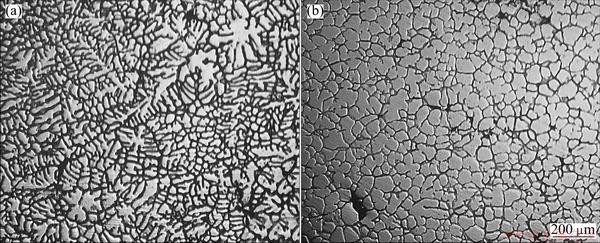
Fig. 2 Metallographs of as-cast 7075 Al alloy (a) and water quenched semi-solid slurry of 7075 Al alloy prepared by ICSPC process at pouring temperature of 660 °C, channel length of 400 mm and interior surface taper of 4° (b)
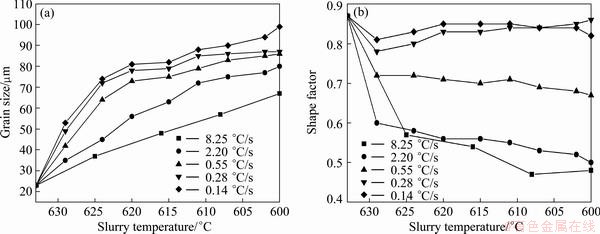
Fig. 3 Effects of cooling rate on size (a) and morphology (b) of semi-solid 7075 Al alloy slurry
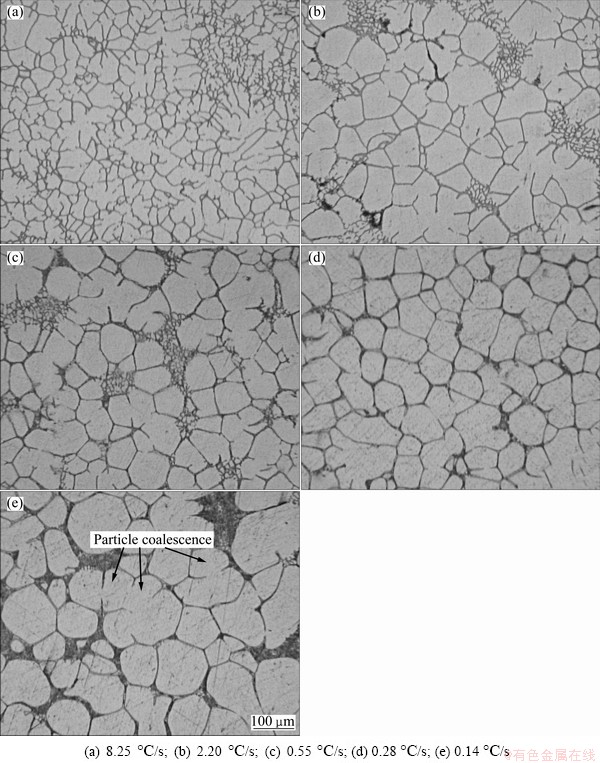
Fig. 4 Metallographs of semi-solid 7075 Al alloy slurry at 600 °C wtih different cooling rates
3.3 Microstructure evolution of primary α(Al)
In the present work, the behavior of primary solidification mainly occurs in two places, ICSPC equipment and slurry holder. When the melt was poured into the channel, heterogeneous nucleation occurs continuously and uniformly throughout the entire volume of the melt with a slight undercooling due to the rapid and continuous heat extraction. As a result of intensive forced convection, the growth of the nuclei takes place in a spherical manner. The fast and spherical growth leads to the formation of spherical globules, with the conventional dendritic primary phase morphology being eliminated, as shown in Fig. 3(b).
As the slurry was collected in the slurry holder, the second stage of solidification has been started due to the very low solid fraction (less than 5%) in the slurry. Investigations [13,14] showed that the uniformity of temperature and composition in the remaining liquid are crucial to the formation of the fine and homogeneous microstructure. And lower cooling rate of the slurry after being prepared plays an important role in achieving such uniformity. Figure 5 and Table 1 show the microstructure evolution of the primary α(Al) under the cooling rate of 0.14 °C/s. The solid fraction at different temperatures was estimated by Scheil equation. Note that the liquid content apparent in the micrographs is not indicative of the quantity present at temperature because the quenching is not sufficiently rapid for the liquid content to be entirely ‘frozen in’, and some liquid phase deposits onto the existing solid surfaces, appearing to be ‘solid’ in the quenched microstructures [15]. It can be seen that as soon as the slurry flew into the slurry holder, the spherical primary α(Al) was obtained, the shape factor almost remained at a high level (above 0.80) during the coarsening, and there is no entrapped liquid in the primary α(Al)s. So, the grain growth mechanisms proposed for the coarsening are most likely to be Ostwald ripening, which is considered to be dominant in a long time and at a high liquid fraction [16]. During the coarsening, the smaller primary α(Al) particles with size below the crucial diameter dissolved gradually but the larger primary α(Al) particles with size above the crucial diameter grew up, which is in favor of the spheroidizing of solid particles because of the reduction of surface energy and overlapped solution fields of neighboring particles. However, if the cooling rate is too slow, the duration of TH treatment will be too long and the particle coalescence will show a significant increase, so certain abnormal growth of grain appears and the shape factor decreases slightly, as shown in Fig. 3(b) and Fig. 4(e).
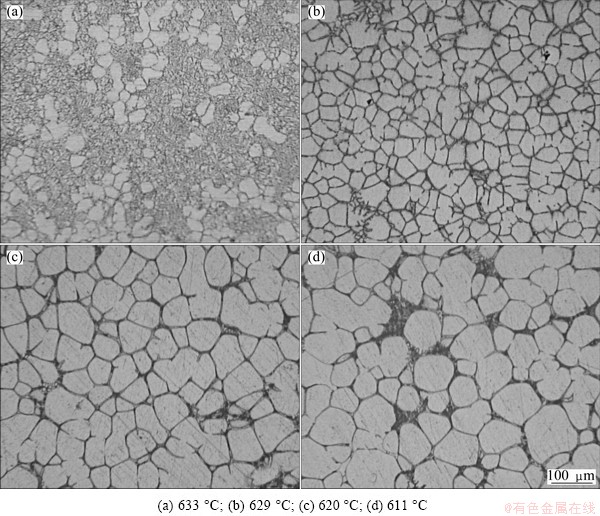
Fig. 5 Microstructural evolution of primary α(Al) under cooling rate of 0.14 °C/s at different temperatures
Table 1 Characteristics of primary α(Al) during different solidification stages corresponding to Fig. 5
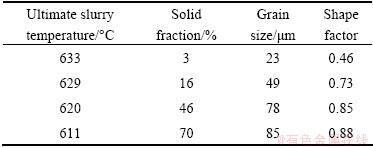
4 Conclusions
1) After the semi-solid 7075 Al slurry is prepared by the ICSPC process, the controllable temperature homogenization treatment is necessary to make the slurry uniform and have a controllable solid fraction suitable for the follow-up rheocasting.
2) The average cooling rate of the slurry has an significant effect on the morphology of the primary α(Al) and a lower cooling rate can promote the transformation of primary α(Al) grain from a dendrite or a rosette to a spherical one.
3) The grain growth mechanism proposed for the coarsening is most likely to be Ostwald ripening, which is in favor of the spheroidizing of solid particles because of the reduction of surface energy and overlapped solution fields of neighboring particles.
References
[1] ATKINSON H V. Modelling the semisolid processing of metallic alloys [J]. Progress in Materials Science, 2005, 50(3): 341-412.
[2] DAS A, KOTADIA H R. Effect of high-intensity ultrasonic irradiation on the modification of solidification microstructure in a Si-rich hypoeutectic Al-Si alloy [J]. Mater Chem Phys, 2011, 125: 853-859.
[3] FAN Z. Semisolid metal processing [J]. International Materials Reviews, 2002, 47(2): 1-37.
[4] WANNASIN J, CANYOOK R, BURAPA R, SIKONG L, FLEMINGS M C. Evaluation of solid fraction in a rheocast aluminum die casting alloy by a rapid quenching method [J]. Scripta Mater, 2008, 58: 1091-1094.
[5] WU S, XIE L, ZHAO J, NAKAE H. Formation of non-dendritic microstructure of semisolid aluminum alloy under vibration [J]. Scripta Mater, 2008, 58: 556-559.
[6] TANG Meng-ou, XU jun, ZHANG Zhi-feng, BAI Yue-long. New method of direct casting of Al-6Si-3Cu-Mg semisolid billet by annulus electromagnetic stirring [J]. Transactions of Nonferrous Metals Society of China, 2010, 20(9): 1591-1596.
[7] CURLE U A. Semi-solid near-net shape rheocasting of heat treatable wrought aluminum alloys [J]. Transactions of Nonferrous Metals Society of China, 2010, 20(9): 1719-1724.
[8] TAHAMTAN S, FADAVI B A. Microstructural characteristics of thixoforged A356 alloy in mushy in mushy state [J]. Transactions of Nonferrous Metals Society of China, 2010, 20(s3): s781-s787.
[9] MATTHEW M F. Semi-solid slurry formation via liquid metal mixing [D]. America: Worcester Polytechnic Institute, 2003.
[10] MARTINEZ R A, FLEMINGS M C. Evolution of particle morphology in semisolid processing [J]. Metallurgical and Materials Transactions A, 2005, 36(8): 2205-2210.
[11] LIU Xu-bo, YANG Xiang-jie, GUO Hong-min. On-line preparation technology for semi-solid slurry of aluminum alloy based on LSPSF (Low shearing pouring semi-solid forming) method [J]. Special Casting & Nonferrous Alloys, 2008, 28(10): 762-765. (in Chinese)
[12] YANG Bin, MAO Wei-min, ZENG Jian-nan, SONG Xiao-jun. Effect of the parameters in inverted cone-shaped pouring channel process on the microstructure of semi-solid 7075 aluminum alloy slurry [J]. Solid State Phenomena, 2013(192-193): 415-421.
[13] MANSON-WHITTON E D, STONE I C, JONES J R, GRANT P S, CANTOR B. Isothermal grain coarsening of spray formed alloys in the semi-solid state [J]. Acta Materialia, 2002, 50(10): 2517-2535.
[14] GUO Hong-min, YANG Xiang-jie. Formation mechanism of spherical particles in undercooled melt [J]. The Chinese Journal of Nonferrous Metals, 2008, 18(4): 651-659. (in Chinese)
[15] TZIMAS E, ZAVALIANGOS A. Mechanical behavior of alloys with equiaxed microstructure in the semisolid state at high solid content [J]. Acta Materialia, 1999, 47(2): 517-528.
[16] KIM H S, STONE I C, CANTOR B. Microstructure evolution in semi-solid AA7034 [J]. Journal of Materials Science, 2008, 43(4): 1292-1304.
半固态7075铝合金浆料温度均匀化处理过程中的组织演化规律
杨 斌,毛卫民,宋晓俊
北京科技大学 材料科学与工程学院,北京 100083
摘 要:采用ICSPC法制备半固态7075铝合金浆料,再结合温度均匀化处理,使浆料组织相对均匀并获得可控的固相率,以适合后续的流变压铸。主要研究温度均匀化处理过程中冷却速率对初生α(Al)组织演化规律的影响。结果表明,随着冷却速率的降低,半固态浆料中的初生α(Al)趋向于近球状方式生长,其组织的均匀性也相对提高。这可能是由于冷却速度的降低有利于半固态浆料剩余液相中各部分温度及成分的一致性,而这种一致性则是形成均匀球状晶的关键。然而,过低的冷却速度将会显著延长晶粒的生长时间,导致晶粒过分粗大和更多的晶粒合并,因而出现部分异常长大的晶粒,并导致形状因子的轻微下降。
关键词:半固态浆料;7075铝合金;微观组织;初生α(Al)
(Edited by Hua YANG)
Foundation item: Project (2011CB606302-1) supported by the National Basic Research Program of China; Project (51074024) supported by the National Natural Science Foundation of China
Corresponding author: Bin YANG; +86-10-62332882; E-mail: yang_bin19@163.com
DOI: 10.1016/S1003-6326(13)62905-2