J. Cent. South Univ. (2012) 19: 155-162
DOI: 10.1007/s11771-012-0985-6
Determination of efficient superfinishing conditions for mirror surface finishing of titanium
KIM Jin-seob, LIM Eun-seong, JUNG Yoon-gyo
School of Mechatronics, Changwon National University, Changwon 641-773, Korea
? Central South University Press and Springer-Verlag Berlin Heidelberg 2012
Abstract: To determine mirror surface finishing conditions and efficient and economical superfinishing conditions for pure titanium and titanium alloys, an abrasive film is used when superfinishing is performed under varying conditions. These conditions include the workpiece rotation speed, the oscillation speed, the contact pressure of the roller, the hardness of the roller, and the type of abrasive film. The superfinishing device is applied to polishing a thin and long cylindrical bar. A micro-finishing film and a lapping film were used as abrasive films. Al2O3 grains or SiC grains were used as abrasives. The surface roughness of a polished workpiece was measured using a stylus-type surface-roughness measuring instrument. As a result, the conditions to improve the polishing surface efficiently include high values for the workpiece rotation speed, oscillation speed and contact pressure. The roller hardness has no effect on the efficient polishing conditions. The mirror finish of a surface can be created using lapping film of 3 μm with Al2O3 grains after polishing to a steady surface roughness under the efficient polishing conditions.
Key words: superfinishing; mirror surface finishing; abrasive film; surface roughness; titanium; optimal polishing time
1 Introduction
Titanium, with its infinite potential, is widely known as a highly ideal material. It is, therefore, used in various industries that require precision-machined parts, such as the automobile, chemistry and aerospace industries, due to its outstanding specific strength and corrosion resistance compared to other alloys. In the field of precision parts, it is important to select the proper polishing conditions and develop a polishing system that improves surface roughness and satisfies various conditions for maintaining airtightness and limiting the damage caused by friction sliding motions among parts. This demand is in line with the greatly increasing demand for mirror surface finishing and precision machining [1-7]. However, polishing systems for ultra-precision machining require a high level of technology for operation as well as considerable investments in equipment. In addition, it is difficult to automate a polishing process due to factors that include poor working environments, insufficient technical materials, and non-uniform polishing products. Therefore, the polishing process depends heavily on the experience of skilled workers.
In many countries, in an effort to overcome these problems, superfinishing machines using abrasive film were developed in the late 1970s. These machines are applied to the polishing of precision machinery in various industries. In addition, the polishing characteristics and polishing conditions have been studied widely [8-13]. On the other hand, in Korea, these types of machines have been applied to industrial processes only since the late 1980s. Moreover, their use has depended on foreign technology. Recently, the demands for superfinishing machines have increased, but the development of superfinishing devices and superfinishing technology remain insufficient. In recent years, several studies have been done, including a study of efficient superfinishing conditions using an abrasive film for SM45C [14]. However, few studies have centered on titanium, which is a nonferrous metal. Therefore, it is necessary to study titanium in relation to superfinishing.
The purpose of this work is to determine mirror surface finishing conditions and efficient and economical superfinishing conditions for pure titanium and titanium alloys using an abrasive film when superfinishing is performed under varying conditions. These conditions include the workpiece rotation speed, the oscillation speed, the contact pressure of the roller, the hardness of the roller, and the type of abrasive film.
2 Experimental device and experimental method
In this work, the superfinishing device to polish a thin and long cylindrical bar consists of a superfinisher body that controls feeding and oscillating of the abrasive film and control device that controls the spindle speed of the roller, the oscillation speed, the feed rate of the abrasive film and the air-pressure control. The device that supplies the cutting fluid is a special device that involves an independent system. As shown in Fig. 1, the superfinisher body is the core of a superfinishing system. The superfinisher body consists of two rollers, which supply and withdraw the abrasive film, and an oscillation unit. The oscillation unit consists of a contact roller for support between the abrasive film and the surface of the workpiece, an upper roller and a lower roller to secure the transportation path of the abrasive film, and an air pressure cylinder for forward and backward movement of the oscillation unit. The contact roller is situated at the front of the oscillation unit. The contact roller consists of urethane to decrease the oscillation by rotation and to improve the surface roughness. The oscillation unit was designed for left and right oscillation movement from 1 mm to 7 mm depending on the torque of a motor that transfers power to an eccentric cam via a camshaft. Figure 2 shows a photograph of the superfinishing device used in the experiment, and Table 1 gives the specifications of the superfinishing device.
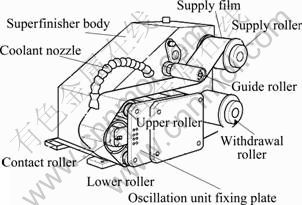
Fig. 1 Schematic diagram of experimental equipment
In this work, a series of experiments were performed with the superfinishing device in order to determine the superfinishing conditions for efficient mirror surface finishing. The workpiece used consisted of pure titanium (G2) and a titanium alloy (G5). Table 2 and Table 3 indicate the chemical composition and the mechanical properties of the titanium, respectively. G2 is the most frequently used type among all types of pure titanium, and G5 is the most commonly used titanium alloy. The abrasive films used here were a micro-finishing film (MF) and a lapping film (LF). MF is appropriate for efficient removal of the surface of the workpiece because the grain of this abrasive film is arrayed vertically. LF is expected to be appropriate for mirror surface finishing because the grain of this abrasive film is arrayed horizontally. Figure 3 shows the arrangement of the grain of the abrasive film according to a scanning electron microscope. The type of abrasive used was Al2O3 grains and SiC grains. The surface roughness of a polished workpiece was measured using a stylus-type surface- roughness measuring instrument (Kosaka Laboratory Ltd., Korea). Table 4 gives the superfinishing conditions in the experiment.
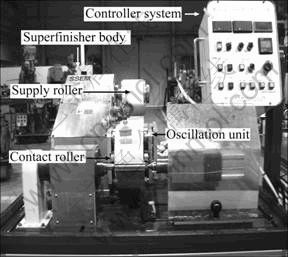
Fig. 2 Photograph of experiment equipment
Table 1 Specification of superfinishing device
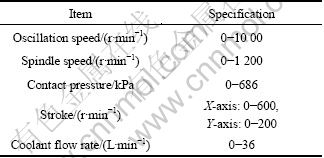
Table 2 Chemical composition of titanium (mass fraction, %)
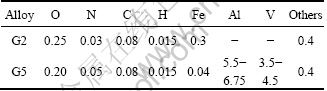
Table 3 Mechanical properties of titanium
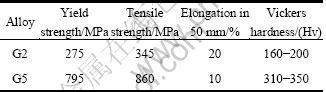
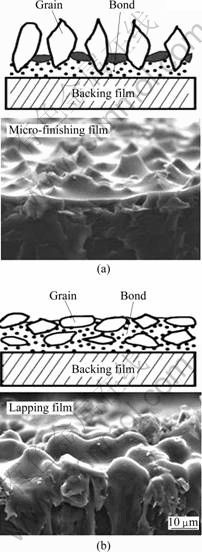
Fig. 3 SEM micrographs of abrasive films
Table 4 Experimental conditions
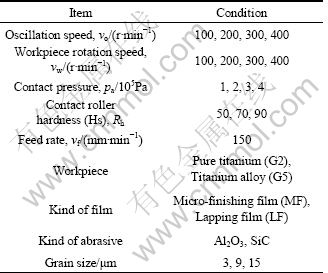
3 Determination of optimal polishing time
Figure 4 shows the characteristics of the arithmetical average roughness Ra values according to the polishing time using the micro-finishing film with a grain size of 15 μm with the abrasive being SiC grain (MF15) under conditions of a contact pressure pa of 1×105 Pa, an oscillation speed vo of 400 r/min, a film feed rate vf of 150 mm/min, a workpiece rotation speed vw of 100 r/min and a roller hardness Rh of Hs90. Ra was measured at 10 s intervals. Initially, Ra rapidly increased during the polishing process. Afterward, Ra maintained a steady value after approximately 100 s. This steady Ra value is defined here as the final surface roughness, Raf. Subsequently, despite continuous polishing, continued improvement in the surface roughness was highly unlikely. In this work, the polishing time at approximately 100 s was defined as the optimal polishing time topt under these polishing conditions. With a smaller topt value, Ra can reach the final surface roughness Raf in a short time. Hence, conditions that make topt smaller are efficient polishing conditions.
In this work, a sequence of processes was performed to give credibility to the value of topt under various polishing conditions. As shown in Fig. 4, after the obtained experiment data were curve-fitted with a quadratic function using an application of the least-squares method, topt was defined in which a derivative of the obtained curve is zero. The value of topt is shown to be 105 s in Fig. 4. To instill objectivity in the value of topt under various conditions, this experiment paid equal attention to the initial surface roughness, the amount of data after topt and the measurement time interval [15].
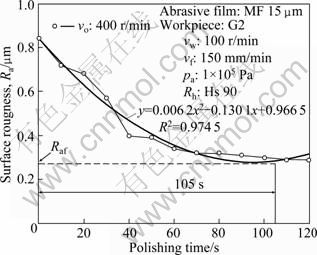
Fig. 4 Decision of optimal polishing time
4 Efficient superfinishing conditions
To polish titanium to mirror surface finish efficiently, it is necessary to perform the polishing process in two steps. The first step involves polishing to the final surface roughness in a short time, and a second step is to create the mirror surface. To perform the first process, we sought to determine the efficient superfinishing conditions for G2 and G5 by measuring the behavior of the Ra value while varying several fundamental conditions, including the oscillation speed vo, the workpiece rotation speed vw, the contact pressure pa, and the roller hardness Rh during the superfinishing process [16].
Figure 5 and Figure 6 show the behavior of the optimal polishing time topt and the final surface roughness Raf according to the oscillation speed and the workpiece speed when the polishing process is performed using MF15. Deformation-induced heating is deemed inappropriate because the thermal conductivity of the titanium is very low; hence, it is impossible to polish this material due to delamination when vo and vw have high values [9]. Therefore, the maximum values of vo and vw are limited to 400 r/min. The type of abrasive used is SiC grains in one of the fundamental experiments. As shown in Fig. 5 and Fig. 6, in the case of G5, topt becomes smaller due to the larger values of vo and vw and the greater amount of polishing per time unit. A smaller topt indicates that Raf can be reached more quickly, which confirms that the efficient polishing conditions include large values of vo and vw. However, in the case of G2, vo and vw change according to the variation of Raf because G2 has more ductility than G5. Accordingly, Raf dramatically increases according to increases of vo and vw. Therefore, it is necessary to avoid these conditions in order to polish the surface of G2 to a mirror finish, although increases in the values of vo and vw signify efficient polishing conditions.
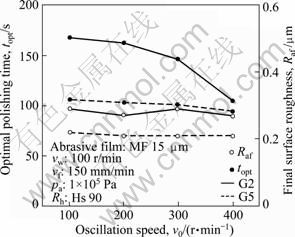
Fig. 5 Behavior of optimal polishing time and final surface roughness according to oscillation speed
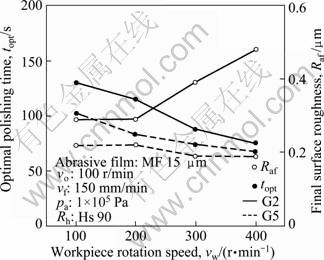
Fig. 6 Behavior of optimal polishing time and final surface roughness according to workpiece rotation speed
In addition, as shown in Fig. 7 and Fig. 8, topt becomes smaller because a larger value of pa implies a larger area of interference between the grain of the abrasive film and the workpiece, whereas the variation of Raf does not change much. Moreover, varying the value of Rh has no effect on the characteristics of Raf and topt. Therefore, efficient superfinishing conditions include large values of pa, vo and vw according to the experimental results.
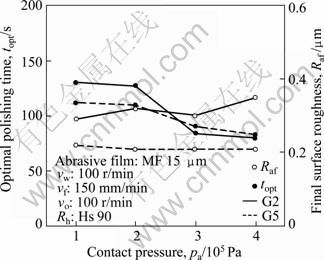
Fig. 7 Behavior of optimal polishing time and final surface roughness according to contact pressure
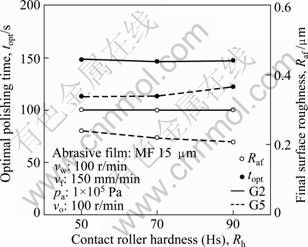
Fig. 8 Behavior of optimal polishing time and final surface roughness according to contact roller hardness
5 Determination of mirror surface finishing conditions
Additional experiments are conducted in order to select conditions of the mirror surface finishing about titanium. These experiments are based on efficient superfinishing conditions.
Figure 9 shows behavior of surface roughness according to polishing time after superfinishing using LF15 with SiC grains on G2 and G5 under conditions of a contact pressure pa of 1×105 Pa and 4×105 Pa. As shown in Fig. 9, it is possible to polish pure titanium (G2) efficiently when contact pressure pa is 4×105 Pa. However, in order to conduct the mirror surface finishing, it is confirmed that selecting a contact pressure pa of 1×105 Pa has an advantage over 4×105 Pa. In the case of G5, it is reasonable to assume that efficient polishing conditions for mirror surface finishing are to select a contact pressure pa of 4×105 Pa, because Raf has almost steady value regardless of value of the contact pressure.
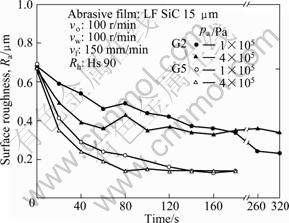
Fig. 9 Variation in surface roughness with polishing time at different contact pressures
Also, after additional experiments about vo and vw, it is confirmed that results of additional experiments indicate the same behavior obtained in Section 4. Therefore, in the case of G2, it is advantageous to increase vo and decrease vw in order to polish the mirror surface. In the case of G5, it is confirmed that it is advantageous to increase both vo and vw for mirror surface finishing.
6 Mirror surface finishing of titanium
In order to obtain a mirror surface roughness that is independent of the polishing time, mirror surface finishing conditions in Section 5 are applied in this experiment. A polished surface in which the arithmetical average roughness Ra is less than 0.03 μm is defined as a mirror surface.
Figure 10 shows the characteristics of the surface roughness according to the polishing time after superfinishing using the abrasive films of LF15, LF9 and LF3 with SiC grains on G2. In addition, Fig. 10 shows SEM photographs captured of the final roughness surface after the polishing operation under the polishing conditions. The initial surface roughness is defined as the surface roughness polished up to the optimal polishing time using the abrasive film MF15 in an experiment according to the determination of the mirror surface finishing conditions. In order to polish the mirror surface, the fundamental polishing conditions are chosen according to the set of conditions (vo, vw, vf, pa, Rh) for which the final surface roughness Raf is as small as possible. As shown in these images, the smaller the grain size is, the more the final surface roughness is improved. However, this experiment using SiC grains cannot produce a mirror surface of less than 0.03 μm. Moreover, it is evident that the use of SiC grains is not proper for mirror surface finishing because the variation of the surface roughness according to the polishing time by LF3 is irregular. On the other hand, the variation of the surface roughness according to the polishing time by LF3 with Al2O3 grains is slight (Fig. 11). The final surface roughness obtains a mirror surface of less than 0.03 μm when LF3 with Al2O3 is used. The smaller the grain is, the more the tip of the grain is blunt because the hardness value of the Al2O3 grain is less than that of the SiC grain. This result is assumed to have a positive influence on the mirror surface finishing process. Figure 12 shows the final surface polished using LF3 with SiC grains and Al2O3 grains for G2. It is confirmed that the surface can be polished to a mirror finish when the Al2O3 grains are used.
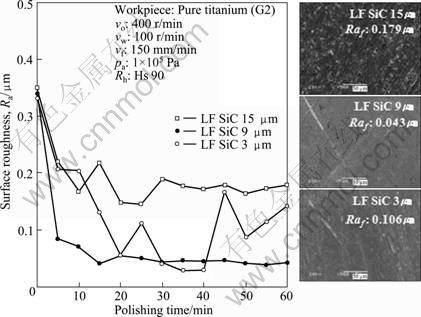
Fig. 10 Variation in surface roughness (G2) with polishing time at difficult sizes of abrasive grain SiC and SEM images of final roughness surface
Figure 13 and Figure 14 indicate the experimental results for G5 under mirror surface finishing conditions. The surface roughness does not change when using LF3 with SiC grains because the mechanical properties of G5 are much better than those of G2. In the case of G2, it is confirmed that the surface can be polished to a mirror finish using Al2O3 grains. Figure 15 shows the morphologies of final surface, confirming that it can be polished to a mirror surface finishing with Al2O3 grains.
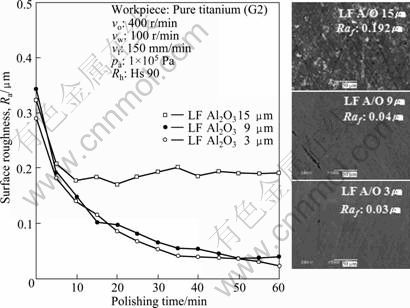
Fig. 11 Variation in surface roughness (G2) with polishing time at difficult sizes of abrasive grain Al2O3 and SEM images of final roughness surface
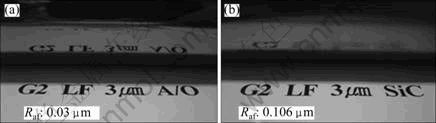
Fig. 12 Photographs of superfinished surface (G2): (a) Abrasive grain Al2O3; (b) Abrasive grain SiC
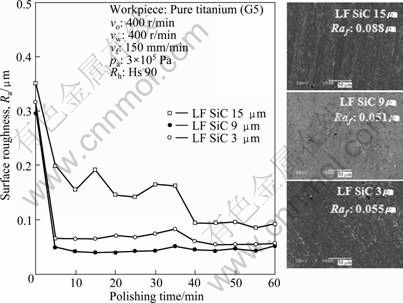
Fig. 13 Variation in surface roughness (G5) with polishing time at difficult sizes of abrasive grain SiC and SEM images of final roughness surface
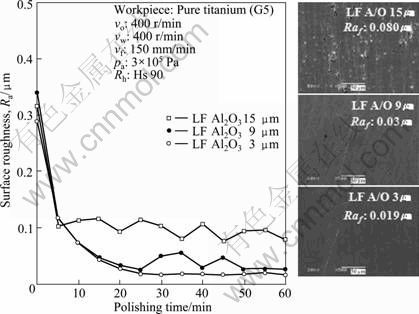
Fig. 14 Variation in surface roughness (G5) with polishing time at difficult sizes of abrasive grain Al2O3 and SEM images of final roughness surface
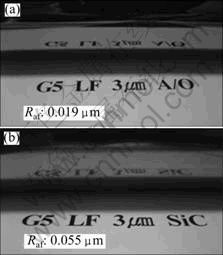
Fig. 15 Photographs of superfinished surface (G5): (a) Abrasive grain Al2O3; (b) Abrasive grain SiC
7 Conclusions
1) The conditions to improve the polishing surface efficiently include high values for the workpiece rotation speed, oscillation speed and contact pressure. The roller hardness has less effect on the efficient polishing conditions.
2) For pure titanium and titanium alloy, it is confirmed that the mirror finish of a surface can be created using LF3 with Al2O3 grains after polishing to a steady surface roughness under the efficient polishing conditions.
Acknowledgement
This work is partly supported by the Second Stage of Brain Korea21 Projects.
This work was supported by Grant No. RTI04-01-03 from the Regional Technology Innovation Program of the Ministry of Knowledge Economy (MKE) of Korea.
References
[1] SHIN O C, JUNG S R, JUNG Y G. Development of internal superfinishing system use abrasive film [J]. The Korean Society of Machine Tool Engineers, 2007: 154-159. (in Korean)
[2] JUNG S Y, SHIN O C, JUNG Y G. A study on the practical application conditions of polishing film for high-efficiency superfinishing [J]. The Korean Society of Manufacturing Process Engineers, 2008(11): 115-121. (in Korean)
[3] KIM J S, SHIN O C, JUNG Y G. A study on mirror surface finishing conditions of titanium using polishing film [J]. The Korean Society of Manufacturing Process Engineers, 2010(5): 245-246. (in Korean)
[4] KIM J S, PARK K B, SHIN O C, JUNG Y G. A study on superfinishing characteristics of titanium using polishing film [J]. The Korean Society for Precision Engineering, 2009(10): 259-260. (in Korean)
[5] LEE S M, CHAE S S, LEE C S, KIM T S, PARK H K, JUNG J S, JUNG H T, JUNG C Y, LEE J C. A study on the development of miniaturization & module for super finishing unit using lapping film [J]. The Korean Society of Manufacturing Process Engineers, 2009(11): 96-97. (in Korean)
[6] SHIN O C, JUNG S R, JUNG S Y. A basic study on the polishing conditions of internal superfinishing using abrasive film [J]. The Korean Society of Machine Tool Engineers, 2008: 155-160. (in Korean)
[7] SHIN O C. A basic study on the internal superfinishing effect using abrasive film [J]. The Korean Society of Manufacturing Process Engineers, 2009(11): 61-62. (in Korean)
[8] CHANG S H, FARRIS T N, CHANDRASEKAR S. Contact mechanics of superfinishing [J]. American Society Mechanical Engineers, 2000, 122(2): 388-393.
[9] CHANG S H, FARRIS T N, CHANDRASEKAR S. Experimental characterization of superfinishing [J]. Proceedings of the Institution of Mechanical Engineers: Part B, 2003, 217(7): 941-952.
[10] PUTHANANGADY T K, MALKIN S. Experimental investigation of the superfinishing process [J]. Wear, 1995, 185(1/2): 173-182.
[11] RECH J, KERMOUCHE G, CLAUDIN C, KHELLOUKI A, GRZESIK W. Modelling of the residual stresses induced by belt finishing on a AISI52100 hardened steel [J]. International Journal of Material Forming, 2008, 1(1): 567-570.
[12] RECH J, KERMOUCHE G, GRZESIK W, GARCIA-ROSALES C, KHELLOUKI A, GARCIA-NAVAS V. Characterization and modelling of the residual stresses induced by belt finishing on a AISI52100 hardened steel [J]. Journal of Materials Processing Technology, 2008(1/3): 187-195.
[13] KHELLOUKI A, RECH J, ZAHOUANI H. The effect of abrasive grain's wear and contact conditions on surface texture in belt finishing [J]. Wear, 2007, 263(1-6): 81-87.
[14] KIM H B, KIM K S, NAMGUNG S. A study on the mirror surface finishing of SM45C using micro abrasive film [J]. The Korean Institute of Industrial Educators, 1997, 22(1): 190-198.
[15] JUNG S Y, PARK K B, JUNG Y G, JUNG S Y. An experimental study on the determination of efficient superfinishing conditions using polishing film [J]. The Korean Society for Precision Engineering, 2009, 26(8): 55-61. (in Korean)
[16] KIM J S, JUNG Y G, SHIN O C. The determination of efficient superfinishing conditions for the mirror surface finishing of titanium [J]. The Korean Society of Manufacturing Process Engineers, 2010(11): 25-26. (in Korean)
(Edited by YANG Bing)
Foundation item: Work supported by the Second Stage of Brain Korea 21 Projects of Korea
Received date: 2011-04-26; Accepted date: 2011-10-10
Corresponding author: JUNG Yoon-gyo, Professor, PhD; Tel: +82-55-213-3604; E-mail: ygjung@changwon.ac.kr