网络首发时间: 2013-12-27 13:16
稀有金属 2014,38(05),868-873 DOI:10.13373/j.cnki.cjrm.2014.05.020
预处理对硫酸常压浸出废旧高温合金中镍钴的影响
董海刚 范兴祥 行卫东 吴跃东 赵家春 付光强
贵研铂业股份有限公司
稀贵金属综合利用新技术国家重点实验室
昆明贵金属研究所
摘 要:
研究了预处理对硫酸常压浸出废旧高温合金中镍钴的影响规律, 重点分析讨论了浸出过程中预处理方式、球磨时间、浸出时间对镍钴浸出率的影响。结果表明:与未预处理比较, 在相同浸出条件下, 粒度为180~380μm的废旧高温合金经过预处理, 用滚筒球磨30 min, 并采用电子扫描显微镜 (SEM) 对预处理前后的物料进行表征, 经过预处理的废旧高温合金, 其粒度变细, 比表面积增大, 表面能提高, 镍钴浸出率分别提高8.48%, 7.82%;行星球磨预处理的镍钴浸出率较滚筒球磨低;在0~3 h浸出时间内, 浸出时间对镍钴浸出率影响显著。浸出3 h后, 浸出时间对浸出率没有明显影响。
关键词:
废旧高温合金;酸浸;镍;钴;预处理;
中图分类号: TQ111.17;TG132.3
作者简介:董海刚 (1981-) , 男, 甘肃陇南人, 博士, 副研究员, 研究方向:稀贵金属冶金;E-mail:donghaigang0404@126.com;;范兴祥, 副研究员;电话:0871-68329261;E-mail:fanxingxiang@tom.com;
收稿日期:2013-07-18
基金:国家科技部高技术研究发展计划 (863计划) 项目 (2012AA063204) 资助;
Sulfuric Acid Leaching of Nickel and Cobalt from Waste Superalloys by Pretreatment
Dong Haigang Fan Xingxiang Xing Weidong Wu Yuedong Zhao Jiachun Fu Guangqiang
Sino-Platinum Metals Co., Ltd.
State Key Laboratory of Advanced Technology of Comprehensive Utilization of Platinum Metals
Kunming Institute of Precious Metals
Abstract:
The effect of pretreatment on sulfuric acid leaching Ni and Co from superalloys was studied. The influence of pretreatment, milling time and leaching time on leaching rate of nickel and cobalt were mainly investigated. The results showed that after pretreatment of superalloys with the particle size of 180 ~ 380 μm, the leaching rate of Ni and Co could significantly be improved; compared with no pretreatment, after ball milling 0. 5 h, then the materials of before and after pretreatment were examined by scanning electron microscopy ( SEM) , the surface area and surface free energy both increased, the leaching rates of Ni and Co increased by 8. 48% and 7. 82%, respectively. Compared with planet ball milling, Ni and Co leaching rate was lower than those after the pretreatment of milling in the same leaching conditions. In leaching time of 0 ~ 3 h, Ni and Co leaching rate significantly increased with the milling time increasing.After leaching 3 h, the effect of time was not obvious.
Keyword:
waste superalloys; acid leaching; nickel; cobalt; pretreatment;
Received: 2013-07-18
镍、钴具有优良的物理化学性能和机械性能, 具有耐高温、耐腐蚀、高强度和强磁性等特点, 在航空、航天、以及其他相关工业部门的高温合金等新材料[1]生产中起着关键性作用。随着我国航空航天事业不断发展, 对高温合金的需求及产量越来越大, 其中对镍、钴作为关键性材料的需求日益增加, 但镍、钴矿产资源的日益匮乏, 因而对废旧高温合金中镍、钴资源的二次回收显得尤为重要, 但是在我国高温合金料的回收循环再利用却还处于一个较低水平, 导致大量优质资源浪费[2]。目前提取镍钴的主要方法有:常压酸浸和高压酸浸或氨法加压浸出、氯气浸出镍钴等[3,4,5,6,7,8,9,10,11,12];硫化物沉淀法[13,14]、电解沉积法[15,16]等湿法工艺, 以及碳热还原[17], 酸焙烧-水浸[18]等火法或火法与湿法相结合的工艺, 且这些工艺主要是针对各种原矿、废旧离子电池、废旧催化剂等原料, 用来处理废旧高温合金物料的相对较少。本文针对直接浸出废旧高温合金粉末过程中, 镍钴的浸出不彻底等问题, 提出采用滚筒球磨方式强化硫酸浸出废旧高温合金的工艺, 并探索了滚筒球磨对硫酸常压浸出废旧高温合金中镍钴的影响规律。
1实验
1.1物料
废旧高温合金物料的主要组成元素如表1, 图1 (a) 所显示的是废旧高温合金物料的形貌, 颗粒大小不一, 不规整。从图1 (b) 可以看出, Ta, Nb, W等被镍钴等包覆在内部。图2所示主要为废旧高温合金的组成, 主要元素Co, W, Mo, Ta, Al等与Ni形成固溶体。
1.2设备与仪器
实验中选用的设备有:多功能数显电动搅拌器电热套, 双配套循环水式多用真空泵。锥形球磨机, 行星智能研磨机。
分析检测设备:X射线衍射仪 (XRD) (日本理学公司, 型号:D/max-2200) , 电子扫描显微镜 (SEM) (日立高新技术 (上海) 国际贸易有限公司, 型号:S-3400N) , 原子吸收光谱仪 (日立高新技术 (上海) 国际贸易有限公司, 型号:Z-2300) ;X荧光光谱仪 (赛默飞世尔科技, 型号:ARL3460) 。
表1 废旧高温合金物料元素分析结果 (%, 质量分数) Table 1Chemical compositions of waste superalloys (%, mass fraction) 下载原图

Note:Unit of Ru being g·t-1
表1 废旧高温合金物料元素分析结果 (%, 质量分数) Table 1Chemical compositions of waste superalloys (%, mass fraction)
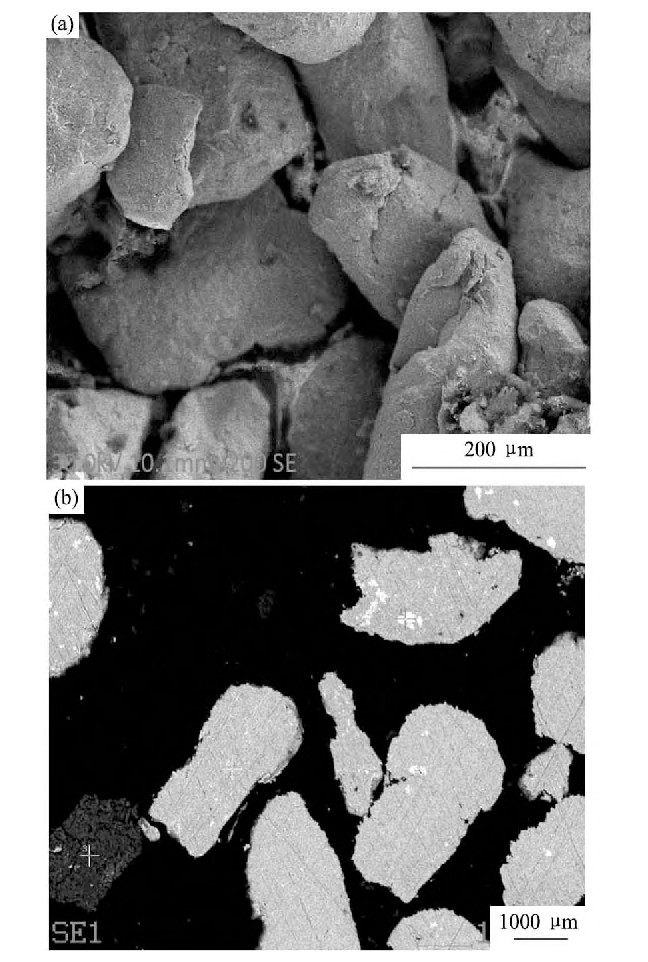
图1 废旧高温合金粉末在SEM和偏光显微镜下的形貌Fig.1 SEM image (a) and OM image (b) of waste superal-loys
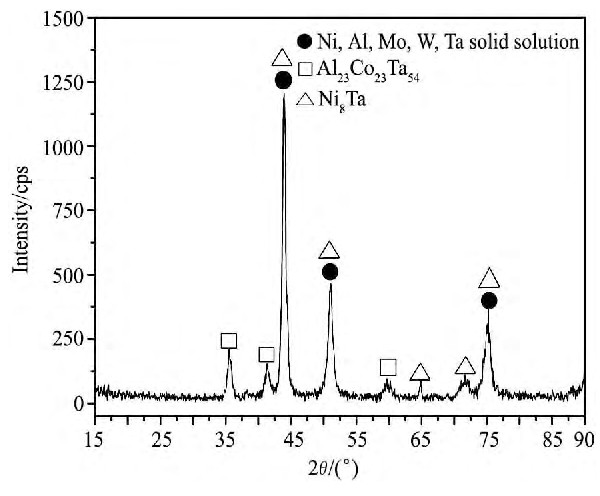
图2 废旧高温合金XRD衍射分析结果Fig.2 XRD pattern of waste superalloys
1.3方法
实验分成滚筒球磨预处理和硫酸浸出两个步骤。
1.3.1机械活化
滚筒锥形球磨机化:锥筒转速 (96±2) r·min-1, 钢球直径30 mm占40% (质量比) 、25 mm占33% (质量比) 、20 mm占27% (质量比) , 活化介质为空气, 球料比为60∶1 (质量比) 。
1.3.2浸出过程
按液固比加入25%的稀硫酸, 待实验温度达到后, 在搅拌状态下, 加入实验要求的机械活化后的物料, 进行浸出, 反应结束后, 过滤和洗涤, 浸出渣烘干, 浸出液量体积, 并测浸出渣和浸出液中的Ni, Co含量, 计算镍和钴的浸出率。
2结果与讨论
2.1预处理对废旧高温合金物料的影响
采用扫描电子显微镜分别对粒度为180~380μm的废旧高温合金未经预处理及滚筒球磨预处理1.0 h进行表征, 图3和4分别为其扫描电子显微镜的分析结果。
从图3和4可以看出, 粒度为180~380μm的废旧高温合金经预处理1.0 h, 平均粒度由400μm变到340μm, 粒度变细, 说明经过滚筒球磨预处理可使粒度变细, 增加其比表面积, 有利于与溶液充分接触。
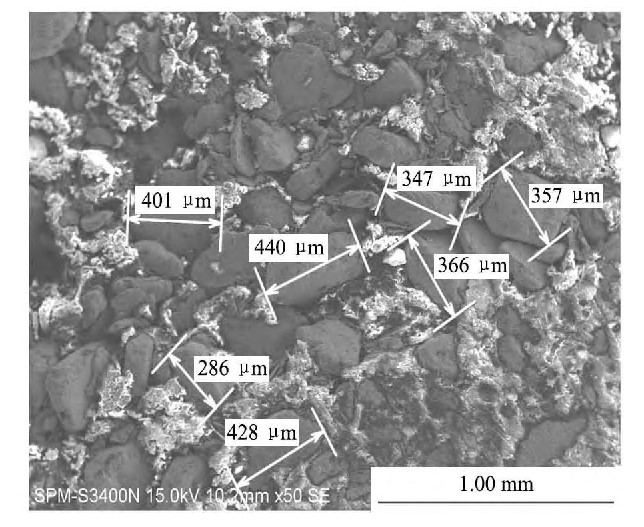
图3 粒度为180~380μm的废旧高温合金SEM照片Fig.3SEM image of waste superalloys with particle size of180~380μm
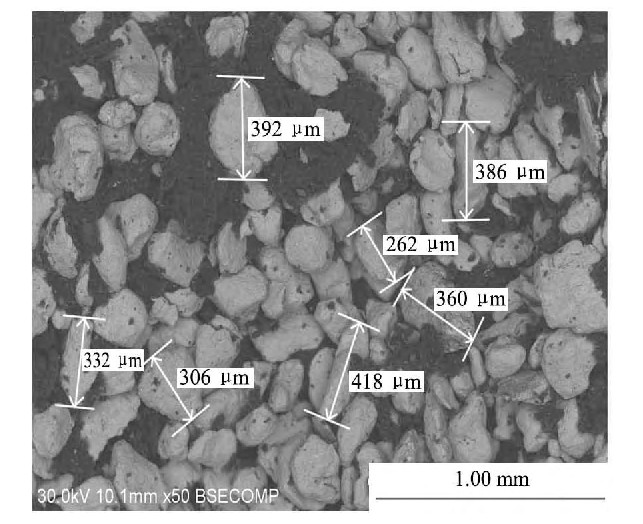
图4 粒度为180~380μm的废旧高温合金经预处理1.0 h的SEM照片Fig.4SEM image of waste superalloys with particle size of180~380μm after pretreatment
2.2预处理方式对镍钴浸出率的影响
实验在浸出时间为7 h, 球磨时间为30 min的条件下, 考查了预处理方式对镍钴浸出率的影响, 结果见表2。从表2可看出, 粒度为180~380μm的废旧高温合金经过滚筒球磨或行星球磨预处理, 可以显著提高镍钴的浸出率, 说明预处理对提高镍钴浸出率具有重要作用;与未预处理比较, 滚筒球磨30 min, 镍钴浸出率可提高8.48%, 7.82%;与滚筒球磨处理条件相比, 在相同浸出条件下, 在行星球磨处理的情况下镍钴浸出率较滚筒球磨低, 说明滚筒球磨处理效果好。因此, 实验确定采用滚筒球磨预处理废旧高温金。
2.3滚筒球磨时间对镍钴浸出率的影响
实验在浸出时间为7 h, 用滚筒球磨机预处理的条件下, 考查了滚筒球磨时间对镍钴浸出率的影响, 结果见图5。从图5可以看出, 镍钴的浸出率随着预处理时间延长而逐渐提高, 当滚筒预处理时间为90 min, 镍钴的浸出率较处理30 min分别提高了2.15%和2.08%, 当预处理时间为120 min时, 镍钴的浸出率与预处理90 min比较, 提高不明显, 说明预处理时间为90 min较合理。从图7还可以看出, 镍钴的浸出曲线基本重合, 说明镍钴的浸出率较接近。
表2 预处理对镍钴浸出率的影响 (%) Table 2 Effect of pretreatment on Ni and Co leaching rate (%) 下载原图
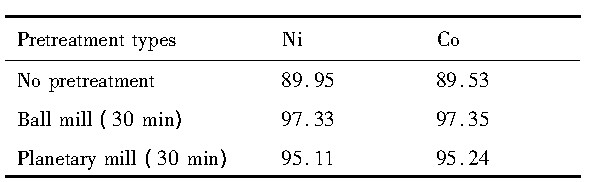
表2 预处理对镍钴浸出率的影响 (%) Table 2 Effect of pretreatment on Ni and Co leaching rate (%)
2.4浸出时间对镍钴浸出率的影响
实验在以滚筒球磨机预处理, 球磨时间为30min的条件下, 考查了浸出时间对镍钴浸出率的影响, 结果见图6。
从图6可以看出, 在0~3 h, 浸出时间对镍钴浸出率影响显著, 当浸出1 h, 镍和钴的浸出率仅为47.53%和47.12%, 浸出3 h, 镍和钴的浸出率分别为93.94%和94.15%, 镍和钴的浸出率分别提高了46.41%和47.03%, 说明在浸出时间内, 反应速率较快;浸出3 h后, 镍和钴的浸出率随着浸出时间延长而缓慢提高;当浸出5 h时, 镍和钴的浸出率为95.32%和95.04%, 较浸出3 h比, 镍和钴的浸出率仅分别提高了1.48%和0.89%, 说明浸出3 h后, 硫酸浓度降低, 导致反应速率较慢;当浸出7 h时, 镍钴的浸出率分别为97.56%和97.23%, 镍钴浸出较完全。因此, 确定浸出时间为7 h较适宜。
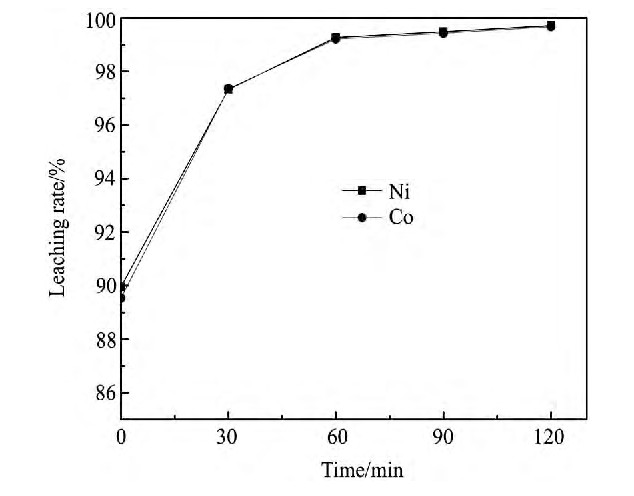
图5 预处理时间对镍钴浸出的影响Fig.5 Effect of pretreatment time on Ni and Co leaching rate
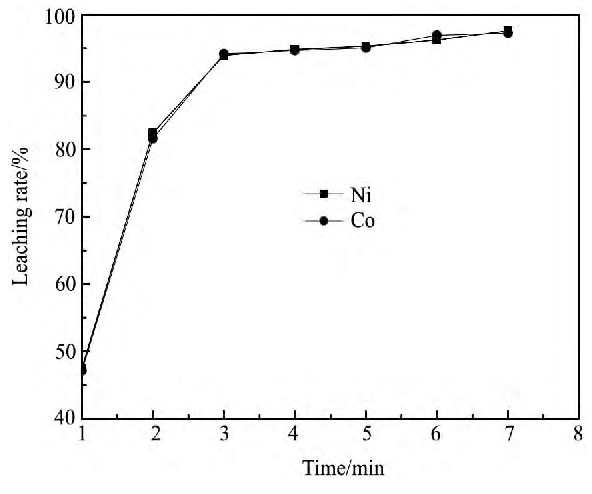
图6 浸出时间对镍钴浸出的影响Fig.6 Effect of leaching time on Ni and Co leaching rate
采用X射线衍射仪对不同浸出时间获得的渣进行表征, 结果见图7。从图7可以看出, 在相同浸出条件下, 随着预处理时间延长, 废旧高温合金中主要物相镍和钴峰强逐渐减弱, 并逐渐消失, 其余钨、钼、铼、铌等物相的峰逐渐出现, 并逐渐增加, 得到很好的富集。
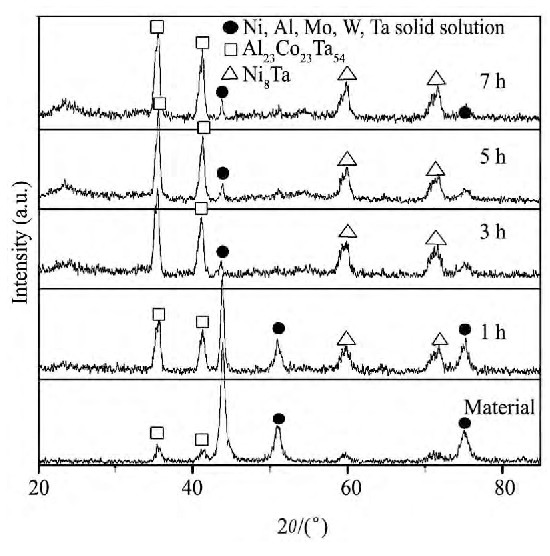
图7 浸出渣的XRD表征结果Fig.7 XRD patterns of different leaching time
3结论
1.通过研究预处理方式对硫酸浸出废旧高温合金中镍钴浸出率的影响, 表明预处理可以提高镍钴的浸出率。
2.滚筒球磨和行星球磨30 min, 在相同浸出条件下, 滚筒球磨的镍钴浸出率比行星球磨高。
3.采用电子扫描显微镜对预处理前后的物料进行表征, 经过预处理的废旧高温合金, 其粒度变细, 比表面积增大, 表面能提高, 有利于镍钴浸出。
4.在0~3 h的浸出过程中, 镍钴浸出率提高非常显著, 浸出3 h后, 浸出时间对镍钴浸出率影响不明显。
参考文献
[1] Li A L, Zeng X R, Cao L M.Current status of research on high temperature meterials for advanced aircraft engines[J].2003, 17 (2) :26. (李爱兰, 曾變榕, 曹腊梅.航空发动机高温材料的研究现状[J].材料导报, 2003, 17 (2) :26.)
[2] Su Q L, Shi Z W, John Hunsaker, Liu D H, Dong T X.Status and consideration of recycling of superalloys in our country[J].Nonferrous Metals Recycling and Utilization, 2006, (4) :19. (苏庆伦, 史战旺, John Hunsaker, 刘大海, 董天祥.我国高温合金循环利用的现状与思考[J].有色金属再生与利用, 2006, (4) :19.)
[3] Shen Y F, Xue W Y, Niu W Y.Recovery of Co (Ⅱ) and Ni (Ⅱ) from hydrochloric acid solution of alloy scrap[J].Transaction of Nonferrous Metals Society of China, 2008, 18 (5) :1262.
[4] Li J H, Li X H, Hu Q Y.Study of extraction and purification of Ni, Co and Mn from spent battery material[J].Hydrometallurgy, 2009, 99 (1-2) :7.
[5] van Tonder G J, Cilliers P J.Cobalt and nickel removal from zinc or impure electrolyte by molecular recognition technology (MRT) -pilot plant demonstration[J].Journal of the South African Institute of Mingan Metalleurgy, 2002, 7 (2) :11.
[6] Yu Z J, Feng Q M, Ou L M, Lu Y P, Zhang G F.Leaching of cobalt bearing metallic matte in sulfuric acid at normal pressure[J].Journal of Central South University (Science and Technology) , 2006, 37 (4) :675. (喻正军, 冯其明, 欧乐明, 卢毅屏, 张国范.常压下硫酸体系中钴冰铜的浸出[J].中南大学学报 (自然科学版) , 2006, 37 (4) :675.)
[7] Rane M V, Bafna V H, Sadanandam R.Recovery of high purity cobalt from spent ammonia cracker catalyst[J].Hydrometallurgy, 2005, 77 (3-4) :247.
[8] Zheng Y J, Teng H, Yan H Q.Nitric acid oxidation leaching of cobalt from refractory high-arenic cobalt ores[J].Chinese Journal of Nonferrous Metals, 2010, 20 (7) :1418. (郑雅杰, 滕浩, 闫海泉.硝酸氧化浸出难冶炼高砷钴矿[J].中国有色金属学报, 2010, 20 (7) :1418.)
[9] Kang N J.Development of application of hot pressure leaching technology in recovery of nickel and cobalt in China[J].China Nonferrous Metallurgy, 1995, 24 (2) :1. (康南京.我国镍钴冶炼应用热压浸出技术的进展[J].中国有色冶金, 1995, 24 (2) :1.)
[10] Liu J H, Zhang H R, Wang R X.Process of ammonium leaching oxidation ore of cobalt and copper at high pressure[J].Chinese Journal of Rare Metals, 2012, 36 (1) :149. (刘建华, 张焕然, 王瑞祥.氨法加压浸出钴铜氧化矿工艺[J].稀有金属, 2012, 36 (1) :149.)
[11] Shen Y F, Xue W Y, Li W.Selective recovery of nickel and cobalt from cobalt-enriched Ni-Cu matte by two-stage counter-current leaching[J].Separation and Purification Technology, 2007, 60 (2) :113.
[12] Hou X C, Xiao L S, Gao C J.Experimental study on leaching of nickel and cobalt from waste high-temperature Ni-Co alloys[J].Hydrometallurgy of China, 2009, 28 (3) :164. (侯小川, 肖连生, 高从堦.从废高温镍钴合金中浸出镍和钴的实验研究[J].湿法冶金, 2009, 28 (3) :164.)
[13] Zhou Y M, Hu B L.Nickel and cobalt recovered from cobalt-nickel matte leaching lixivium[J].Nonferrous Metals (Extractive Metallurgy) , 2012, (6) :11. (周雍茂, 胡宝磊.从钴冰镍浸出液中回收镍钴[J].有色金属 (冶炼部分) , 2012, (6) :11.)
[14] Xu Y B, Xie Y T, Liu J S.Enrichment of valuable metals from the sulfuric acid leach liquors of nickeliferous oxide ores[J].Hydrometallurgy, 2008, 95 (1-2) :28.
[15] Pradhan N, Singh P, Tripathy B C.Electrowining of cobalt from acidic sulphate solutions-effect of chloride ion[J].Minerals Engineering, 2001, 14 (7) :775.
[16] Zhang W P.Study on the processing of low-Co cemented carbide scraps by electrochemical method[J].Cenmented Carbide, 2006, 23 (2) :107. (张外平.电溶法处理低钴硬质合金废料的研究[J].硬质合金, 2006, 23 (2) :107.)
[17] Jones R T, Denton G M, Reynolds Q G.Recovery of cobalt from slag in a DC arc furnace at Chambishi, Zambia[J].Journal of the South African Institute of Mining and Metallurgy, 2002, 7 (1) :5.
[18] Cüneyt Arslan, Fatma Arslan.Recovery of copper, cobalt and zinc from copper smelter an converter slags[J].Hydrometallurgy, 2002, 67 (2) :1.