
Microstructures and mechanical properties of hot-pack rolled Ti-43Al-9V-Y alloy sheet
KONG Fan-tao(孔凡涛), CHEN Yu-yong(陈玉勇), WANG Wei(王 威),
LIU Zhi-guang(刘志光), XIAO Shu-long(肖树龙)
School of Materials Science and Engineering, Harbin Institute of Technology, Harbin 150001, China
Received 26 November 2008; accepted 25 May 2009
Abstract: Ti-43Al-9V-Y alloy sheets with dimensions of 300 mm×100 mm×(1.5-2) mm were produced by hot-pack rolling. After rolling, the microstructure of Ti-43Al-9V-Y alloy sheet becomes near gamma(NG), which is comprised of γ+B2 phases. After heat treatment(HT) at 1 200-1 320 ℃ for 30 min followed by furnace cooling(FC), network shape structure of B2 phases in as-rolled microstructure is retained on the whole. Moreover, with increasing the HT temperature, precipitation of B2 phase lamellae in equiaxed γ grains is increased. Equiaxed γ grains transform partly to α2/γ/B2 lamellar structure after the heat treatment at 1 320 ℃ for 30 min. Tensile test results show that room-temperature yield strength(YS) and ultimate tensile strength(UTS) of the as-rolled material are 509 and 612 MPa, respectively. With the test temperature increasing, the YS and UTS of the as-rolled are decreased, but the elongation is improved. After HT at 1 200 ℃, both yield strength and fracture strength of Ti-43Al-9V-Y alloy sheet are the lowest. With HT temperature increasing, fracture strength is increased obviously, but yield strength of the sheet after HT at 1 280 ℃ is the highest, about 869 MPa.
Key words: titanium aluminides; sheet; heat treatment; microstructure; mechanical properties
1 Introduction
Intermetallic alloys based on γ-TiAl have potentials as high temperature materials for the application of aerospace and automobile engine, due to their attractive properties, such as relatively low density, high specific strength and specific elastic modulus, and good anti- oxidation performance[1-5].
In recent years, much emphasis has been placed on the fabrication of TiAl sheet, and it makes good sense for the preparation of hypersonic aircraft[6-7]. Nevertheless, processing of TiAl alloy sheet is difficult due to its limited ductility and poor hot workability. Recent advances, however, have allowed rolling of TiAl alloy sheets to produce a fine-grained equiaxed γ/α2 microstructure[8-10]. Additionally, the microstructure of TiAl alloys can be manipulated by heat treatment to produce a fine-grained lamellar microstructure. Such rolled sheets can be subsequently formed to engineering parts by means of superplastic forming or conventional hot-die forming[11-12].
For the rolling of TiAl alloy sheets, ingot metallurgical(IM) and powder metallurgical(PM) processing routes have been developed. At present, most as-rolled TiAl alloys are of γ+α2 microstructure[13-15]. In this study, a Ti-43Al-9V-Y alloy sheet comprised of γ+B2 phases was prepared using ingot metallurgical processing route, and the microstructure and mechanical properties of this alloy sheet, both in as-rolled state and after heat treatment, were investigated.
2 Experimental
Ti-43Al-9V-Y (molar fraction, %) alloy ingot in nominal composition was prepared by induction skull melting(ISM) technique. The starting materials used in this study were sponge titanium (>99.7% purity), highly pure aluminium (99.99% purity), Al-V and Al-Y master alloys. The impurity level of oxygen was measured to be quite low (<5×104). Subsequently, the homogenization heat treatment was performed at 900 ℃ for 48 h. The homogenized ingot by hot isostatic pressing(HIP) was conducted for 4 h at 1 250 ℃ and a pressure of 170 MPa in Ar atmosphere, followed by furnace cooling(FC). The HIPed ingot was canned with stainless steel, preheated(1 200 ℃) and forged at a nominal strain rate of about 0.5 s-1 with a total deformation ratio of about 75%, and then annealed at 900 ℃ for 48 h and de-canned.
The wrought alloy was then cut into pieces which were packed in stainless steel can. The canned sample was hot-rolled on a mill with two rolls of 200 mm (diameter)×300 mm (width). Preheating (approximately 1 h) and reheating (10-15 min between two passes) in a furnace were operated at a fixed temperature for the given piece. Furnace temperature of 1 200 ℃ was used. The canned preform was rolled approximately fifteen passes in which the nominal reduction per pass was approximately 8%-10%. The nominal rolling speed was below 0.5 m/s. After rolling, the rolled sheet was allowed to furnace cooling and de-canned. The final Ti-43Al-9V-Y alloy sheets with a dimension of about 300 mm×100 mm×(1.5-2) mm were successfully obtained. Sub- sequently, the sheet was heat treated at different temperatures (1 200-1 320 ℃, 30 min+FC).
The microstructure was characterized by scanning electron microscope(SEM/EDS) with backscattered electron mode(BSE), X-ray diffractometer(XRD) and transmission electron microscope(TEM). Specimens for TEM observation were prepared using standard procedures by ion beam thinner. Tensile test specimens of the as-rolled sheet were prepared by spark erosion parallel to the rolling direction with a gauge section of 15 mm×6 mm×2 mm for room temperature(RT) test and with gauge section of 30 mm×5 mm×2 mm for 700 ℃ and 950 ℃ tests in air, respectively, at an initial strain rate of 1×10-4 s-1. The mechanical properties of the samples after heat treatment were measured by compression tests at room temperature. For the compression tests, cylindrical samples with a dimension of d 1.5 mm×2 mm were used, and the strain rate was 4.17×10-3 s-1.
3 Results and discussion
3.1 Microstructure of as-cast, as-forged and as-rolled alloys
Microstructure and properties of TiAl alloys are very sensitive to hot processing. Casting, forging and rolling have significant impact on the microstructure of TiAl alloys. Fig.1 shows the microstructures of the as-cast, as-forged and as-rolled Ti-43Al-9V-Y alloys. XRD patterns of materials confirm the presence of γ, α2 and B2 phases, as shown in Fig.2.
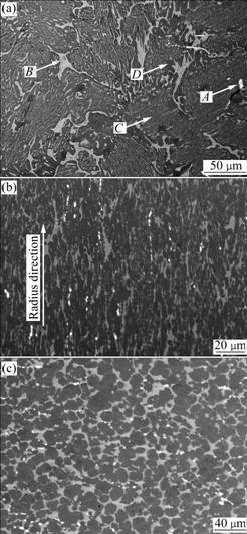
Fig.1 BSE images of Ti-43Al-9V-Y alloy: (a) As-cast; (b) As- forged; (c) As-rolled
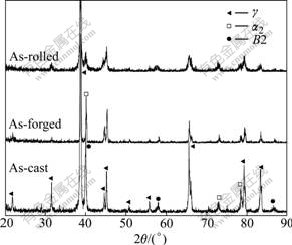
Fig.2 X-ray diffraction patterns of Ti-43Al-9V-Y alloy
The microstructure of the as-cast Ti-43Al-9V-Y alloy is fine-grained and mainly consists of lamellar structure (approximately 85%, volume fraction), and the colony size is about 80 μm, as shown in Fig.1(a). The bright particles (such as A area) are enriched in Y and Al with the Al-to-Y molar ratio of about 2?1, and Ti and V are rare in the particles. The particles can be determined as YAl2 phase according to the previous study[16]. The YAl2 phase cannot be found by XRD. The reason for the absence of YAl2 phase is that the phase is too rare to be detected by XRD. Gray phases (such as B area) along colony boundaries have an average composition of 46Ti, 32.79Al and 21.21V (molar fraction, %) and Y cannot be found. By combining with XRD result, it can be confirmed that the gray phases are B2 phase. The lamellae (such as C area) and dark single γ phase along colony boundaries (such as D area) have the average compositions of 46.41Ti, 43.52Al, 10.07V and 47.95Ti, 46.36Al, 5.69V (molar fraction, %), respectively. Y cannot be found in these regions. It should be noted that V content is obviously different in the different phases. Relatively high V content in the β phase is consistent with the viewpoint that V can stabilize the β phase in TiAl alloys. The V content in single γ phase is about 5.69%, which is slightly lower than that in lamellae.
Fig.3 shows TEM image of lamellar structure of the as-cast Ti-43Al-9V-Y alloy. It can be found that some precipitates appear in the lamellar colonies, besides α2 and γ. These precipitates are identified as B2 phase by TEM. EDS results taken from the B2 precipitates show an average composition of 49.7Ti,28.5Al,21.8V (molar fraction, %).
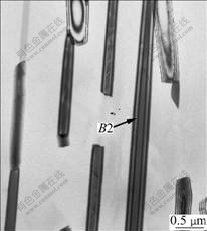
Fig.3 Microstructure of B2 lamellar
From Fig.1(b), the as-forged Ti-43Al-9V-Y alloy has refined streamline microstructure including a large number of recrystallized grains and broken lamellae. Fig.1(c) shows the microstructure of Ti-43Al-9V-Y alloy after rolling at 1 200 ℃. After rolling, the microstructure of Ti-43Al-9V-Y alloy sheet becomes near gamma(NG). In Fig.1(c), the different phases could be identified by BSE and EDS analysis. The dark phase is γ phase with the highest volume fraction. The gray phase in a form of network is B2 phase with higher V content in comparison with the actual composition of the alloy. The bright particles are enriched in Y as those in the as-cast material. Compared with the microstructures of the as-cast and as-forged alloys, it is difficult to find α2 phase in the as-rolled alloy. Therefore, after rolling, the microstructures of Ti-43Al-9V-Y alloy mainly transform to a dual-phase which are comprised of γ+B2 phases.
The as-rolled material primarily consists of equiaxed γ grains with a mean size of 20 μm. No streamline structure is found in the as-rolled material and γ grains become coarser, which proves that recrystallization occurs abundantly in the process of rolling. But the structure is still refined in comparison with the as-cast material.
3.2 Microstructure of as-rolled alloy after heat treat- ment
Heat treatment(HT) has tremendous impact on microstructure and properties of TiAl alloys. Fig.4 shows the BSE microstructures of as-rolled Ti-43Al-9V-Y alloy after different heat treatments.

Fig.4 Microstructures of as-rolled alloy after different heat treatments: (a) 1 200 ℃, 30 min+FC; (b) 1 280 ℃, 30 min+FC; (c) 1 320 ℃, 30 min+FC
From Fig.4, it can be found that network-shape structure of B2 phase in the as-rolled microstructure is retained on the whole after heat treatment of 1 200- 1 320 ℃, 30 min+FC. With enhancing the HT temperature, the precipitation of lath phase in γ equiaxed grains increases in the as-rolled alloy (such as A and C areas).
Because the ordering temperature of β→B2 is about 1 100 ℃, B2 phase can transform into disordered β phase above 1 100 ℃ during HT processing. At different HT temperatures, V element can diffuse from β phases surrounding γ equiaxed grains to high temperature phases of γ gains. During cooling processing of HT, B2 phase precipitates in the equiaxed grains again because of the lower solid solubility of V elements in γ phase, resulting in the formation of B2 laths in γ equiaxed grains. With enhancing the HT temperature, the content of B2 laths formed in γ equiaxed grains increases obviously. After heat treatment at 1 280 ℃, γ equiaxed grains are refined because the content of B2 laths formed in γ equiaxed grains increases significantly.
When heat treatment temperature reaches 1 320 ℃, microstructure of the as-rolled alloy is changed significantly (as shown in Fig.4(c)). After heat treatment at 1 320 ℃, a large number of γ equiaxed grains are changed into α2/γ/B2 lamellar structure (such as C area), indicating that the content of lamellae increases significantly. However, after heat treatment at 1 320 ℃, for 30 min, some γ equiaxed grains are still not completely changed into α2/γ/B2 lamellar structure due to the short HT time. Compared with the microstructure in Fig.4(b), the size of the equiaxed γ grains and lamellar colonies after HT at 1 320 ℃ are coarsened slightly.
3.3 Mechanical properties of sheets
The tensile and compressive properties of Ti-43Al-9V-Y alloy sheet are listed in Table 1 and Table 2. From Table 1, it is obvious that the tensile properties of the as-rolled alloy are regularly changed with temperature increasing. At room temperature, the yield strength(YS) and ultimate tensile strength(UTS) of the as-rolled material are 509 and 612 MPa, respectively. With temperature increasing, the YS and UTS of the as-rolled decrease, but the elongation is improved. At 950 ℃, the ultimate tensile strength is around 88 MPa, and elongation to failure up to 76.5% is obtained, which indicates that the high temperature ductility of Ti-43Al-9V-Y alloy sheet is excellent. From Table 2, it can be found that heat treatment produces an effect on room-temperature compressive properties of Ti-43Al-9V- Y alloy sheet. After HT at 1 200 ℃, both yield strength and fracture strength of Ti-43Al-9V-Y alloy sheet are the lowest. With HT temperature increasing, fracture strength obviously increases. However, the yield strength of the sheet after HT at 1 280 ℃ is the highest, about 869 MPa, which may be attributed to the small γ equiaxed grain size. After HT at 1 320 ℃, compared with HT at 1 280 ℃, the slight increase of the size of equiaxed γ grains and lamellar colonies results in the decrease of yield strength.
Table 1 Tensile properties of Ti-43Al-9V-Y alloy sheet
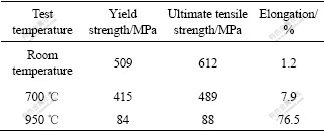
Table 2 Room-temperature compressive properties of Ti-43Al- 9V-Y alloy sheet after heat treatment
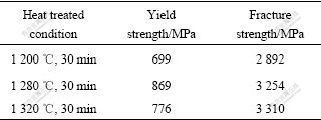
4 Conclusions
1) Ti-43Al-9V-Y alloy sheets with dimensions of about 300 mm×100 mm×(1.5-2) mm are produced by hot-pack rolling method. After rolling processing, the microstructure of Ti-43Al-9V-Y alloy sheet becomes near gamma(NG), which is comprised of γ+B2 phases. The B2 phases distribute in the network shape along γ grains and the YAl2 particles are dispersive.
2) After heat treatment at 1 200-1 320 ℃ for 30 min followed by FC, network-shape structure of B2 phase in the as-rolled microstructure is retained on the whole. Moreover, with increasing the HT temperature, precipitation of B2 phase lamellae in equiaxed γ grains is increased. Equiaxed γ grains transform partly from single γ phase to α2/γ/B2 lamellar structure after the heat treatment at 1 320 ℃ for 30 min.
3) Tensile properties of the as-rolled alloy are regularly changed with temperature increasing. At room temperature, the YS and UTS of the as-rolled material are 509 and 612 MPa, respectively. With temperature increasing, the YS and UTS of as-rolled are decreased, but elongation is improved. At 950 ℃, the ultimate tensile strength is around 88 MPa, and the elongation to failure up to 76.5% is obtained. Heat treatment produces an effect on room-temperature compressive properties of Ti-43Al-9V-Y alloy sheet. After HT at 1 200 ℃, both yield strength and fracture strength of Ti-43Al-9V-Y alloy sheet are the lowest. With HT temperature increasing, fracture strength is obviously increased, and the yield strength of the sheet after HT at 1 280 ℃ is the highest, about 869 MPa.
References
[1] KONG Fan-tao, LI Bao-hui, CHEN Yu-yong, HAN Jie-cai. Essence of room temperature brittleness of TiAl based alloys and improving approaches [J]. Journal of Advanced Materials, 2007, 39(1): 33-40.
[2] WU X H. Review of alloy and process development of TiAl alloys [J]. Intermetallics, 2006, 14: 1114-1122.
[3] KIM J S, LEE Y H, KIM Y W, LEE C S. High temperature deformation behavior of beta-gamma TiAl alloy [J]. Materials Science Forum, 2007, 539/543: 1531-1536.
[4] EDWARD A L. Gamma titanium aluminides as prospective structural materials [J]. Intermetallics, 2000, 8: 1339-1345.
[5] CHEN Yu-yong, KONG Fan-tao, TIAN Jing, CHEN Zi-yong, XIAO Shu-long. Recent developments in engineering γ-TiAl intermetallics research [J]. Trans Nonferrous Met Soc China, 2002, 12(4): 605- 609.
[6] DIMIDUK D M. Gamma titanium aluminide alloys—An assessment within competition of aerospace structural materials [J]. Mater Sci Eng A, 1999, 263: 281-288.
[7] DRAPER S L, KRAUSE D, LERCH B, LOCCI I E, DOEHNERT B, NIGAM R, DAS G, SICKLES P, TABERNIG B, REGER N, RISSBACHER K. Development and evaluation of TiAl sheet structures for hypersonic applications [J]. Mater Sci Eng A, 2007, 464(1/2): 330-342.
[8] BYSTRZANOWSKI S, BARTELS A, CLEMENS H, GERLING R, SCHIMANSKY F P, DEHM G, KESTLER H. Creep behaviour and related high temperature microstructural stability of Ti-46Al-9Nb sheet material [J]. Intermetallics, 2005, 13: 515-524.
[9] GERLING R, SCHIMANSKY F P, STARK A, BARTELS A, KESTLER H, CHA L, SCHEU C, CLEMENS H. Microstructure and mechanical properties of Ti-45Al-5Nb+(0-0.5C) sheets [J]. Intermetallics, 2008, 16: 689-697.
[10] GERLING R, BARTELS A, CLEMENS H, KESTLER H, SCHIMANSKY F P. Structural characterization and tensile properties of a high niobium containing gamma TiAl sheet [J]. Intermetallics, 2004, 12: 275-280.
[11] KOEPPE C, BARTELS A, CLEMENS H, SCHRETTER P, GLATZ W. Optimizing the properties of TiAL sheet materials for application in heat protection shields or propulsion systems [J]. Mater Sci Eng A, 1995, 201: 182-193.
[12] SHAGIEV M R, SALISHCHEV G A, IMAYEV R M, IMAYEV V M, KUZNETSOV A V. Production of γ-TiAl sheets with improved superplastic properties by pack rolling [J]. Materials Science Forum, 2004, 447/448: 317-322.
[13] ADAMS A G., RAHAMAN M N, DUTTON R E. Processing and characterization of dense thin sheets of gamma titanium aluminide [J]. Materials Science and Technology, 2005, 4: 159-166.
[14] ADAMS A G, RAHAMAN M N, DUTTON R E. Microstructure of dense thin sheets of TiAl fabricated by hot isostatic pressing of tape-cast monotapes [J]. Mater Sci Eng A, 2008, 477: 137-144.
[15] BARTELS A, KESTLER H, CLEMENS H. Deformation behavior of differently processed γ-titanium aluminides [J]. Mater Sci Eng A, 2002, 329/331: 153-162.
[16] CHEN Yu-yong, KONG Fan-tao, HAN Jie-cai, CHEN Zi-yong, TIAN Jing. Influence of yttrium on microstructure, mechanical properties and deformability of Ti-43Al-9V alloy [J]. Intermetallics, 2005, 13: 263-266.
Corresponding author: KONG Fan-tao; Tel: +86-451-86418802; E-mail: kft@hit.edu.cn
DOI: 10.1016/S1003-6326(08)60418-5
(Edited by YANG Bing)