
Dry friction and wear performance of SiC 3D continuous ceramic frame reinforced 7075Al alloy
HUANG Dan(黄 丹), CHEN Wei-ping(陈维平), ZHANG Shao-yang(章少阳), HE Zeng-xian(何曾先)
School of Mechanical and Automotive Engineering, South China University of Technology, Guangzhou 510640, China
Received 10 October 2008; accepted 14 January 2009
Abstract: The dry friction and wear behavior of 7075 Al alloy reinforced with SiC 3D continuous ceramic network against Cr12 steel was studied with oscillating dry friction and wear tester under the testing conditions of 70 ℃, 30 min, and the load range of 40-100 N. The experimental result shows that the characteristic of abrasive wear and oxidation wear mechanisms are present for 3D continuous SiC/7075 Al composite. 3D continuous network ceramic as the reinforcement can avoid composite from the third body wear that usually occurs in traditional particle reinforced composite. Under low load, the composite with low volume fraction of ceramic reinforcement exhibits better wear resistance due to the homogeneous reinforcement distribution with small pore size; on the contrary, under high load, the composite with high reinforcement volume fraction exhibits better wear resistance because of the coarse frame size. Hard SiC frame leads to the wear of Cr12 steel mainly. The frame with high volume fraction corresponds to the high Fe content.
Key words: continuous reinforcement; Al-based composite; wear behavior; dry friction
1 Introduction
Composites have been applied widely to dry friction and wear applications since they can effectively enhance the tribological performance of the materials. Aluminum alloy is an important choice as matrix for metal-based composites in industrial application[1]. According to the experimental results of MINDIVAN et al[2], among the composites reinforced by SiC particle with 2618, 6082, 7012 and 7075 matrix, the wear resistance of SiCp/7075 is the best. Many experiments on Al-based metal matrix composites (MMCs) have been conducted to investigate the effects of various factors, such as particle diameter[3], particles volume fraction[4], load[5-6] and sliding velocity[5, 7] on the tribological behavior. The applied particles include SiC, Al2O3, B4C, graphite, and even fly ash and so forth[2, 8]. Simultaneously, it is found that the wear resistance would reduce due to the fact that the particles or fibers are pulled out from matrix for traditional un-continuously reinforced metal-based composites[9-11].
3D continuous ceramic/metal composite is composed of ceramic reinforcement with 3D distributed network structure, which has aroused extensive interesting worldly[12-13]. The new internal structure endows composites with higher hardness and lower brittleness than traditional ceramics. In addition, such composites could avoid from the reduction of wear resistance raised from the separation of un-continuous reinforcement from matrix and matrix softening and leaking at high temperature[14-15]. At present, the study on such aluminum-based composites has been in progress. Nevertheless, many influencing factors on wear mechanism have not been involved, especially the behaviors of the friction pairs.
The dry friction and wear test was conducted for SiC 3D network reinforced 7075 Al alloy against Cr12 steel. The dry friction and wear properties of such composites are reported by analyzing friction coefficient, wear depth, wear surface and sub-surface micrography, debris components and the wear behavior of Cr12 steel.
2 Experimental
SiC foam ceramic was selected as the reinforcement (Foshan Jingang Materials Co. Ltd., China) with two sorts of mean pore diameters of 3 mm and 1 mm, as shown in Figs.1(a) and (b), and with chemical components of 65%-75%SiC, 20%-25%Al2O3, 3%-8%SiO2 and others ≤5%.
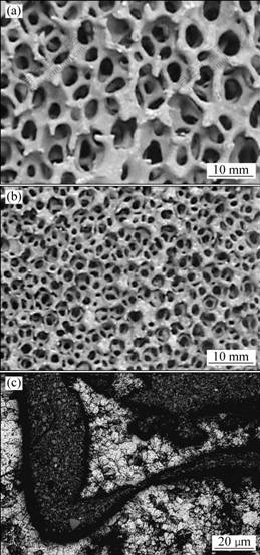
Fig.1 Metallographs of SiC reinforcement with mean pore diameter of 3 mm (a) and mean pore diameter of 1 mm (b), and Composite A (c)
3D continuous SiC/7075 Al composites were prepared by squeeze casting method. Herein, the composite whose SiC frame is with mean pore diameter of 3 mm was marked as Composite A and that with mean pore diameter of 1 mm as Composite B. Fig.1(c) shows the metallograph of Composite A.
Friction and wear experiments were conducted on SRV oscillating sliding friction and wear tester (Optimal Schwingung Reibungudn Verschleiss, Germany), as shown in Fig.2. The dimensions of composite specimens were 18 mm×16 mm×(7±1) mm. The wear surfaces were polished to roughness of 0.7 μm. The upper specimen was heat-treated Cr12 steel (GB/T 1299—1985) with hardness of HRC 56 and dimensions of 5 mm× 8 mm×7 mm. Herein, the friction surface was 5 mm× 8 mm.
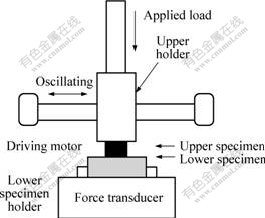
Fig.2 Schematic diagram of oscillating sliding friction and wear testing system
Dry friction testing conditions were as follows: imposed load 40 N (1 MPa), 60 N (1.5 MPa), 80 N (2 MPa) and 100 N (2.5 MPa), and testing temperature 70 ℃. Sliding stroke was 10 mm; therefore, the wear area on composite sample was 15 mm×8 mm. Pre-wearing was conducted for 5 min before the formal testing.
Wear depth in worn region was measured by 3D profiler. On the worn area of 5 mm×10 mm on lower specimen of composite, line scan transverse with profiler to measure on centre line and 2 mm and 4 mm right and left away from center, and the average was taken as the mean wear depth from five values. For investigating the friction and wear mechanism of SiC/7075 Al against Cr12 steel, the worn surface was observed with scanning electronic microscope (SEM) (LEO 1530 VP, Germany) after 30 min ultrasonic cleaning to remove most debris attached on worn surface. Debris was collected from surface after every testing to analyze the chemical components with EPMA.
3 Results and discussion
3.1 Friction coefficient
Fig.3 shows that the mean friction coefficient (COF) of Composite A reduces from 1.00 to 0.85 with the load increasing. As for Composite B, the evolution of mean COF is similar to that of Composite A. However, the reduction of COF is larger, from 1.06 to 0.76. There is not a sharp increase of initial COF which results from the hard ceramic bulge on friction surface due to the 5 min pre-wearing[16].
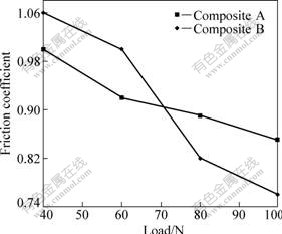
Fig.3 Relationship between mean friction coefficients of composites A and B and testing load
3.2 Wear behavior
3.2.1 Wear micrography
Fig.4(a) shows the worn surface morphology of Composite A under 40 N. The characteristic of mild wear can be seen, where the white particles are rich in Fe and O, directed by the arrow. Fig.4(b) shows the worn surface morphology under 100 N (namely 2.5 MPa pressure). The characteristic of wear groove can be seen parallel to sliding direction and white particles distribute along the grooves with increased quantity, whereas the width of grooves is merely several microns. It can be seen that, even after ultrasonic cleaning with acetone, there are still a great deal of white powders retained on worn surface. Such powders are initiated by ploughing out during friction from both lower and upper specimens, and it is very possible for them to be embedded into worn surface again. With the applied load increasing, the quantity of particles embedded is increased[17-18]. However, the wear grooves can still be distinguished.
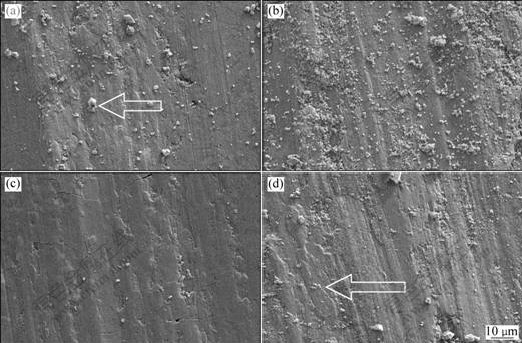
Fig.4 Worn surface micrographs: (a) Composite A, 40 N; (b) Composite A, 100 N; (c) Composite B, 40 N; (d) Composite B, 100 N
Figs.4(c) and (d) show the micrographs of worn surfaces of Composite B under 40 N and 100 N, respectively. Compared with Composite A under 40 N (Fig.4(a)), the degree of wear of Composite B (Fig.4(c)) is mild. With load increasing to 100 N, wear degree exceeds that of Composite A, since plastic deformation of matrix can be surveyed directed by the arrow with wear groove deeper than that in Composite A (Fig.4(b)). There is no SiC particles resulted from SiC frame breakage observed on all worn surfaces.
3.2.2 Wear depth
Fig.5 shows the relationship between the mean wear depth of specimen and testing load. It can be seen that the mean wear depth of Composite A increases a little with the imposed load increasing from 40 N to 60 N; and decreases at 80 N; then, depth value gets recovered with continuous increase of load, close to the value at low load. The mean depth of Composite B increases with the imposed load increasing monotonically. It can be found that the mean wear depth of Composite A is larger than that of Composite B at low load; however, at high load, the mean wear depth of Composite A becomes smaller than that of Composite B.
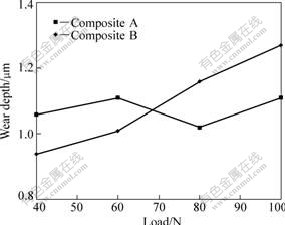
Fig.5 Effect of testing load on wear depth
3.2.3 Wear behavior of Cr12 steel
Fig.6 shows the micrograph of worn surface of upper specimen, where Fig.6(a) is for the worn surface of Cr12 steel against Composite A under 100 N, and Fig.6(b) for the one against Composite B under the same conditions. The results indicate that the wear degree of Cr12 steel against Composite A is more severe than that against Composite B at high applied load (100 N).
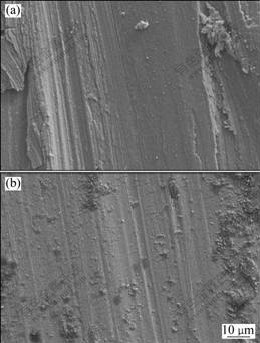
Fig.6 Worn surface micrographs of Cr12 steel against Composite A (a) and Composite B (b) at 100 N
3.2.4 Debris components
Fig.7(a) shows the EPMA result of the debris from Composite B under 40 N, which indicates that the main chemical components of debris are O, Fe and Si where Fe is from upper specimen, Cr12 steel; Al and Si are from composite; and Si is mainly from reinforcement frame. Fig.7(b) shows the variety of Fe content in debris with applied load in Composite A and B, which indicates that Fe content in debris increases with testing load increasing. Furthermore, all values of Fe content in debris from Composite A are higher than those from Composite B.
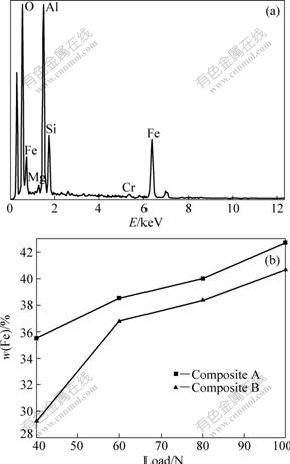
Fig.7 Chemical components analysis results on debris: (a) EPMA analysis on debris from Composite B under 40 N; (b) Relationship between Fe content in debris and applied load
3.3 Wear mechanism
The wear resistance of composites would increase with the volume fraction of reinforcement in certain range. However, once the volume fraction of reinforcement exceeds a certain critical value, it would be not of benefit to wear resistance due to the pull-off of reinforcing particles from matrix[19]. One of distinguishing characteristics of Al-based composite reinforced by 3D continuous network SiC frame from particle reinforced composite is the ceramic network frame distributes continuously in 3D space, and the load would be borne and transferred through the whole frame of reinforcement instead of single particle.
For particle reinforced composite, the resultant stress concentration is inadequate to destruct or excavate out large particles from the matrix, since the wear load borne by small abrasive is much less than that by large one[20]. Even the destruction of frame occurs, the large SiC particles separated from the frame structure are still difficult to be ploughed out or delaminated away from the surface by small abrasive particles among composites reinforced by 3D continuous reinforcement. Wear is mainly resulted from the metal matrix. The abrasive particles could penetrate into a shallow surface layer of the composite. For Composite A and B, the volume fractions of reinforcing frame are 38% and 25%, respectively; whereas the mean rib diameters of frames are 1.5 mm and 1 mm, respectively. Under low applied load, Composite B, whose pore size of SiC frame is less, provides more SiC hard bulges in given friction region (15 mm×8 mm) than Composite A, which leads to higher COF and less wear depth finally. Nevertheless, under high applied load, since the frame has better load-bearing capacity with coarse rib and better wear-resistance with high volume fraction, the COFs of Composite A exceed those of Composite B. As for Composite B, it is indicated that its wear behavior is close to that of metallic Al alloy because of the plastic deformation on its worn surface, and the wear mechanism is the combination of abrasive wear, oxidation wear and plastic deformation.
Fe content in debris attributes to the wear of Cr12 steel against composite. Under testing load range, Fe content in Composite A is higher than that in Composite B, which indicates that hard SiC frame leads to the wear of Cr12 steel mainly. The frame with high volume fraction corresponds to the high Fe content value.
4 Conclusions
1) The friction and wear behavior of 3D continuous SiC/7075 Al composite has characteristic of abrasive wear and oxidation wear.
2) 3D continuous network ceramic as the reinforcement of Al-based composite could avoid from the third body wear.
3) Wear resistance at low load for Composite B is better than that for Composite A due to the homogeneous distribution of reinforcement; however, at high load, wear resistance of Composite A is better because the coarse frame reinforcement bears and disperses load. In addition, there is no plastic deformation in metallic matrix in Composite A.
4) Hard SiC frame leads to the wear of Cr12 steel mainly. The frame with high volume fraction corresponds to the high Fe content.
References
[1] WANG D Z, PENG H X, LIU J, YAO C K. Wear behaviour and microstructural changes of SiCw-Al composite under unlubricated sliding friction [J]. Wear, 1995, 184(2): 187-192.
[2] MINDIVAN H, KAYALI E S, CIMENOGLU H. Tribological behavior of squeeze cast aluminum matrix composites [J]. Wear, 2008, 265(5/6): 645-654.
[3] MANISH N, SURAPPA M K, PRAMILA B N. Dry sliding wear of Al alloy 2024-Al2O3 particle metal matrix composites [J]. Wear, 1995, 181/183: 563-570.
[4] CHO K H, JANG H, HONG Y S, KIM S J, BASCH R H. The size effect of zircon particles on the friction characteristics of brake lining materials [J]. Wear, 2008, 264(3/4): 291-297.
[5] KWOK J K M, LIM S C. High-speed tribological properties of some Al/SiCp composites: I. Frictional and wear-rate characteristics [J]. Composites Science and Technology, 1999, 59(1): 55-63.
[6] BAI M W, XUE Q J, GUO H F. Reciprocal sliding wear of SiC particle-reinforced Al-Cu aluminium matrix composites against stainless steel, high speed tool steel and ceramics II. Wear mechanisms [J]. Wear, 1996, 194(1/2): 126-136.
[7] RAVIKIRAN A, SURAPPA M K. Effect of sliding speed on wear behaviour of A356 Al-30 wt.% SiCp MMC [J]. Wear, 1997, 206(1/2): 33-38.
[8] SUDARSHAN, SURAPPA M K. Dry sliding wear of fly ash particle reinforced A356 Al composites [J]. Wear, 2008, 265(3/4): 349-360.
[9] GUL F, ACILAR M. Effect of the reinforcement volume fraction on the dry sliding wear behaviour of Al-10%Si/SiCp composites produced by vacuum infiltration technique [J]. Composites Science and Technology, 2004, 64(13/14): 1959-1970.
[10] KOK M, OZDIN K. Wear resistance of aluminum alloy and its composites reinforced by Al2O3 particles [J]. Journal of Materials Processing Technology, 2007, 183(2/3): 301-309.
[11] CHEN Yue, XING Jian-dong, ZHANG Yong-zhen, SHEN Bai-ling, NI Feng. The tribological behavior of aluminum-matrix composites reinforced with ceramic particulates in dry sliding against a semi-metallic frictional material [J]. Tribology, 2001, 21(4): 251-255.
[12] PAVESE M, VALLE M, BADINI C. Effect of porosity of cordierite performs on microstructure and mechanical strength of co-continuous ceramic composites [J]. Journal of the European Ceramic Society, 2007, 27: 131-141.
[13] PAVESE M, FINO P, UGUES D, BADINI C. High cycle fatigue study of metal-ceramic co-continuous composites [J]. Scripta Materialia, 2006, 55: 1135-1138.
[14] GLENN S D, BRESLIN M C. Co-continuous composite materials for friction and braking applications[J]. JOM Journal of the Minerals, Metals and Materials Society, 2006, 58(11): 87-92.
[15] YAO Jun-ping, WANG Wei-wei, YANG Bin. Dry friction and wear properties of aluminum matrix composites reinforced with 3D-network ceramics [J]. The Chinese Journal of Nonferrous Metals, 2004, 14(5): 766-771. (in Chinese)
[16] ZHANG L, HE X B, QU X H, DUAN B H, LU X, QIN M L. Dry sliding wear properties of high volume fraction SiCp/Cu composites produced by pressureless infiltration [J]. Wear, 2008, 265(11/12): 1848-1856.
[17] RODRIGUEZ J, POZA P, GARRIDO M A, RICO A. Dry sliding wear behaviour of aluminium-lithium alloys reinforced with SiC particles [J]. Wear, 2007, 262(3/4): 292-300.
[18] YU S Y, ISHII H, TOHGO K, CHO Y T, DIAO D F. Temperature dependence of sliding wear behaviour in SiC whisker or SiC particulate reinforced 6061 aluminum alloy composite [J]. Wear, 1997, 213 (1/2): 21-28.
[19] LIM S C, GUPTA M, REN L, KWOK J K M. The tribological properties of Al-Cu/SiCp metal-matrix composites fabricated using the rheocasting technique [J]. Journal of Materials Processing Technology, 1999, 89/90: 591-596.
[20] SHOROWORDI K M, HASEEB A S M A, CELIS J P. Tribo-surface characteristics of Al-B4C and Al-SiC composites worn under different contact pressures [J]. Wear, 2006, 261(5/6): 634-641.
Foundation item: Project(50575076)supported by the National Natural Science Foundation of China; Project(36547) supported by the Natural Science Foundation of Guangdong Province, China
Corresponding author: CHEN Wei-ping; Tel: +86-20-87113832; E-mail: mewpchen@scut.edu.cn
DOI: 10.1016/S1003-6326(09)60096-0
(Edited by YANG Bing)