文章编号:1004-0609(2007)07-1188-07
铬盐清洁生产工艺中铝硅的脱除
王少娜1, 2,郑诗礼1,张 懿1
(1. 中国科学院 过程工程研究所,北京 100080;
2. 中国科学院 研究生院,北京 100049)
摘 要:研究铬盐清洁生产工艺中铝硅的脱除。理论计算表明:CaO加入浸出液中不会有致癌物铬酸钙的生成。结果表明:在反应温度为70~90 ℃时,添加适量的CaO,浸出液中的铝硅可以脱除到要求值。无铁渣存在时脱铝硅产物为Ca2.93Al1.97Si0.64O2.56(OH)9.44,有铁渣存在时为Ca3AlFe(SiO4)(OH)8。铁渣的存在可以加速铝硅脱除反应的速度,提高铝硅的脱除率,而溶液中K2CO3的浓度对CaO脱除铝硅的影响不大。
关键词:铬盐;清洁生产;氧化钙
中图分类号:TQ 136.1 文献标识码:A
Separation of aluminum and silicon in clean production process for potassium dichromate
WANG Shao-na1, 2, ZHENG Shi-li 1, ZHANG Yi1
(1. Institute of Process Engineering, Chinese Academy of Sciences, Beijing 100080, China;
2. Graduate University of the Chinese Academy of Sciences, Beijing 100049, China)
Abstract: The separation of Al and Si in the clean production process for potassium dichromate was studied. The thermodynamic calculation results indicate that there is no produce of poisonous CaCrO4 when CaO is added into solution. When the amount of CaO addition adequately and reaction temperature between 70 ℃ and 90 ℃, the concentrations of Al and Si in solution can decrease to required value. The main product is Ca2.93Al1.97Si0.64O2.56(OH)9.44 when reaction without iron residue, while it is Ca3AlFe(SiO4)(OH)8 when reaction with iron residue. The exist of iron residue can accelerate the rate of separate reaction, and improve the separation amount of Al and Si from solution. The concentration of K2CO3 in solution has no obvious effect on the separate reaction.
Key words: potassium dichromate; cleaner production; calcium oxide
铬盐系列产品作为化工-轻工-高级合金材料的基础原料,是我国重点发展的化工原料之一,广泛应用于高性能合金、电镀、印染、医药、合成橡胶、催化剂等诸多工业部门[1]。然而目前我国铬盐行业均采用传统的高温氧化-钠化焙烧法,资源能源利用率低,且排放大量的高毒性铬渣,严重污染环境[2-4],长期被列为我国污染行业之首。用清洁生产高新技术改造传统产业,关系到环境污染的根本性防治及产业的持续发展,是我国传统产业由高消耗、低效益的粗放型经济向节约效益型经济转变的根本途径,社会、经济和科学意义极为重大。中国科学院过程工程研究所摆脱了“末端治理”的传统思维模式,从生产源头着手,研发了一种新的清洁生产工艺[5-6]。该工艺以氢氧化钾亚熔盐液相氧化过程取代传统的大窑焙烧,以CO2酸化取代硫酸酸化,实现了碱金属离子的再生循环,开辟了铬铁矿资源高效-清洁-循环利用的生态工业新模式[7]。
在亚熔盐液相氧化制取K2CrO4粗晶工艺过程中,过量KOH以液相形式存在,铬铁矿中的Fe被氧化成Fe2O3后进入渣相,Mg以Mg(OH)2形式存在,部分Si以铝硅酸盐形式进入渣相,称为“铁渣”。反应结束后将熔体稀释,进行相分离,Cr和Al以铬酸钾及铝酸钾形式进入液相,部分Si也进入溶液。因用空气作氧化剂,反应过程有小部分KOH碳酸化生成的K2CO3也进入液相。因此,分离出来的K2CrO4粗晶携带了一定量的铁渣、游离碱、K2CO3以及Al和Si等杂质。Al在粗晶溶解时,会同时溶解到K2CrO4溶液中,进入后续的碳酸化工艺,并污染最终产品K2Cr2O7,反应系统中Al、Si杂质的协同积累还会导致铬酸钾结晶相分离效率的显著下降,因此必须将浸出液中的铝硅脱除。
铬盐传统生产工艺中,Si在铬酸钠碱性液中含量极低(SiO2 0.5 g/L),对最终产品不会造成污染,而Al2O3达到2~10 g/L。除Al的工序放在铬酸钠加酸转化成重铬酸盐的工序之前,通过调节溶液的pH值使得体系中的Al沉淀析出进行分离[8]。铬盐清洁生产工艺也进行过相应的工业试验和研究,将除Al和K2CrO4加压碳酸化2个工序耦合在同一个设备(碳化塔)中进行,通过控制反应终点的pH值,使液相中的Al以Al(OH)3的形式沉淀析出[9]。但在实际清洁工艺生产中,由于Al、Si的存在和协同积累,导致K2CrO4结晶相分离效率显著下降,使得清洁工艺在K2CrO4结晶分离阶段就难以进行。因此,只有在结晶前的浸出阶段将Al、Si脱除,才能保证整个后续工艺的顺利进行。在铬盐清洁生产工艺粗晶浸出阶段,浸出液浓度大致如下:KOH 150 g/L,K2CO3 50 g/L,K2CrO4 200 g/L,SiO2≤5 g/L,Al2O3≤18.9 g/L,铁渣含量70 g/L。浸出液碱浓度高,调节pH值困难,必须采用其他方法。
在氧化铝生产中,对于深度脱硅工艺,采用不同的含钙化合物如CaO、水合铝酸钙、水合碳铝酸钙和水合硫铝酸钙等作为添加剂,能够达到很好的脱硅效果[10-12]。而CaO价廉易得,又能与铝酸钾溶液反应生成铝酸钙,因而能够对溶液脱除铝硅起到很好的作用。因此,本文作者结合清洁生产工艺的特点,首次提出了在铬盐生产中引入CaO进行铝硅的脱除。利用氧化钙(CaO)能与浸出液中的铝硅生成不溶性化合物的原理脱除杂质,主要反应式为[13-14]:
CaO+H2O=Ca(OH2)
3Ca(OH)2+2KAlO2+3H2O=3CaO?Al2O3?6H2O+2KOH
3Ca(OH)2+2KAlO2+nSiO2+(3-2n)H2O=3CaO?Al2O3?nSiO2?(6-2n)H2O+2KOH
通过实验研究了CaO添加量、反应时间、反应温度、铁渣和K2CO3含量等因素对铝硅脱除的影响。这对铬盐清洁生产新工艺的设计具有重要的理论意义和实际价值。
1 实验
1.1 原料和装置
实验所用主要原料:氧化钙由分析纯的CaO在850 ℃煅烧1.5 h得到;自制K2O·Al2O3·3H2O;分析纯的KOH、K2CO3、K2CrO4及K2SiO3·nH2O。
实验装置如图1所示。
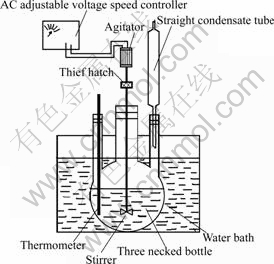
图1 实验装置图
Fig.1 Schematic diagram of experimental installation
1.2 步骤及分析方法
首先配制一定浓度组成的KOH-K2CO3-K2CrO4- Al2O3-SiO2-H2O溶液,待水浴升至指定温度后,将配制好的水溶液装入三颈瓶内,开通搅拌,使体系温度稳定。待温度计显示溶液达到指定温度时,加入CaO,反应计时。定时取样,样品经过滤后分析溶液中的Al和Si的浓度变化。根据清洁工艺现场需要,要求终液中SiO2浓度降至1 g/L以下,Al2O3浓度降至1.89 g/L以下。
实验最终所得过滤后固相用水洗涤至发白后,在100~120 ℃下烘干。
溶液及所得固相的化学分析采用ICP-OES (Optimal 5300DV, Perkin Elmer Instruments)。
固相物相分析采用XRD(X’pert Pro MPD, Cu Kα 辐射,40 kV, 30 mA)
2 机理分析
因浸出液中含有较多的铬酸钾,加氧化钙除铝硅的过程中会有铬盐工业中常见致癌物铬酸钙[15]的生成,即发生如下反应:
Ca(OH)2+K2CrO4=CaCrO4↓+2KOH
各含铬化合物的溶度积常数及铬酸钙的溶解度数据如表1和表2所示[16-17]。
按温度为100 ℃,CaCrO4?0.5H2O溶解度为0.8%计,即0.8 g/100 g H2O,其Ksp为:
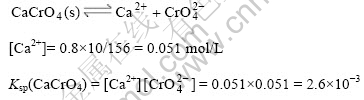
对于如下反应式:


按现设定的浸出液组成:
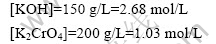
所以,
,Q?K,反应逆向进行,理论上无铬酸钙生成。
表1 各含铬化合物的溶度积常数
Table 1 Solubility product constant of some chromate compounds
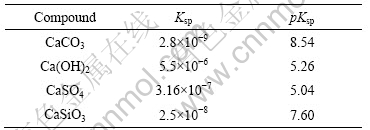
3 结果与讨论
3.1 SiO2单独存在时脱硅的主要影响因素
在无Al2O3存在情况下,讨论CaO添加量及温度对脱硅的影响。溶液模拟浸出液成分如下:KOH 150 g/L,K2CO3 50 g/L,K2CrO4 200 g/L。
图2(a)所示为反应温度90 ℃,不同CaO添加量下溶液中SiO2浓度随时间的变化。当n(CaO)/ n(SiO2)=1时,溶液中SiO2在反应5 h时仍大于1 g/L。而当n(CaO)/ n(SiO2)为3和5时,溶液中SiO2的浓度在反应时间30 min时即可降低到0.69 g/L,但反应5 h后仍为0.6 g/L。由所得固相XRD谱(图3)分析可知所生成脱硅产物为1.5CaO·SiO2·xH2O,即CaO添加量为n(CaO)/n(SiO2)=1.5时即可达到脱除SiO2的目的。这说明CaO添加过量可大大提高脱硅的反应速度,但由XRD谱同时可以看出,CaO添加过量时有大量的Ca(OH)2存在产物中,造成了CaO的浪费。图2(b)所示为CaO添加量为n(CaO)/n(SiO2)=1.5时不同反应温度下溶液中SiO2浓度随时间的变化。由图可以看出,在50 ℃下溶液脱除SiO2反应速度低,70 ℃和90 ℃下反应速度相对较高。但在反应5 h后溶液中SiO2浓
表2 铬酸钙的溶解度(以CaCrO4计)
Table 2 Solubility of CaCrO4

度都低于1 g/L。如溶液在反应温度为70~90 ℃下添加过量CaO,则可以加快SiO2脱除速度,由实验可知,CaO过量情况下可以在30~60 min将溶液中SiO2脱除到要求值。
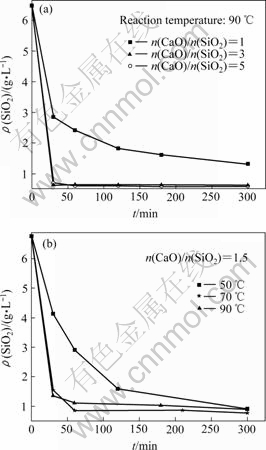
图2 CaO添加量和温度对溶液中SiO2浓度的影响
Fig.2 Effect of amount of CaO added(a) and temperature(b) on SiO2 concentration of solution
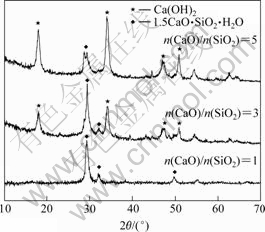
图3 不同CaO添加量下脱硅产物的XRD谱
Fig.3 XRD patterns of desilication products at different amounts of CaO addition
3.2 铝硅共存时的脱除效果
图4和图5所示为反应温度为70 ℃和90 ℃,不同m(Al2O3)/m(SiO2)溶液中Al2O3和SiO2的质量比)溶液添加CaO脱除铝硅的实验结果。溶液模拟浸出液成分,浓度如下:KOH 150 g/L,K2CO3 50 g/L,K2CrO4 200 g/L。在本实验中,为了保证脱铝硅反应充分进行,石灰的实际添加量比理论量超过20%。铝硅共存实验CaO添加量为30 g/L,是以实验中料液最高Al2O3浓度13.4 g/L,SiO2浓度2.15 g/L及以脱铝硅产物为Ca2.93Al1.97Si0.64O2.56(OH)9.44,添加CaO过量20%为依据的。为了比较不同m(Al2O3)/m(SiO2)下铝硅脱除情况,选用了相同的CaO添加量。由实验结果可知,添加CaO脱硅在70~90 ℃,CaO添加量30 g/L,反应时间2 h的情况下,终液中SiO2可降至0.5 g/L以下,Al2O3可降至1.89 g/L以下。分析所生成脱硅产物,w(K)<0.4%,w(Cr)<0.7%,所生成物相为铝硅酸钙Ca2.93Al1.97Si0.64O2.56(OH)9.44,无CaCrO4的生成。在相同CaO添加量下,随着m(Al2O3)/m(SiO2)的升高,SiO2
的脱除量升高,这是因为所生成Ca2.93Al1.97Si0.64-O2.56(OH)9.44可结合更多的SiO2的缘故。
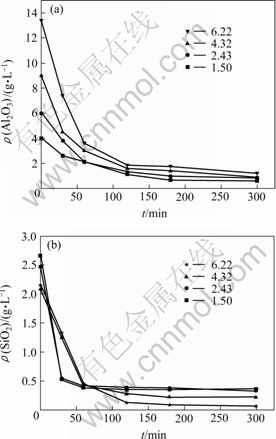
图4 反应温度70 ℃时不同m(Al2O3)/m(SiO2)溶液中铝硅脱除实验结果
Fig.4 Experimental results of different m(Al2O3)/m(SiO2) solutions at reaction temperature of 70 ℃: (a) Al2O3; (b) SiO2
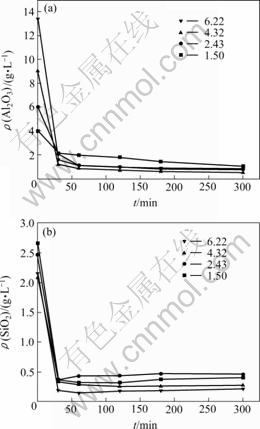
图5 反应温度90 ℃时不同m(Al2O3)/m(SiO2)溶液中铝硅脱除实验结果
Fig.5 Experimental results of different m(Al2O3)/m(SiO2) solutions at reaction temperature of 90 ℃: (a) Al2O3; (b) SiO2
3.3 铁渣对氧化钙脱除铝硅的影响
在亚熔盐铬盐清洁生产工艺的液相氧化阶段,铬铁矿和氧气在碱金属亚熔盐介质中发生高效反应。铬铁矿氧化浸出后所得到的残渣,因含铁量较高,称为“铁渣”[18]。分离出来的K2CrO4粗晶携带了一定量的铁渣,因此需要研究铁渣的存在对浸出液脱除铝硅的影响。
在反应温度90 ℃、铁渣量70 g/L(实际浸出液中铁渣量)、添加CaO 20 g/L(以理论量的1.2倍添加)条件下,进行了铁渣对CaO脱除铝硅影响的实验。溶液模拟浸出液成分浓度为:KOH 150 g/L,K2CO3 50 g/L,K2CrO4 200 g/L。图6所示为当SiO2浓度为3.43 g/L,Al2O3浓度为5.19 g/L时铝硅脱除效果。图7所示为当SiO2浓度为2.34 g/L、Al2O3浓度为9.09 g/L时铝硅脱除效果。由有无铁渣存在条件下的对比实验可知,铁渣的存在可以加速铝硅脱除反应的速度,提高铝硅尤其是铝的脱除率。
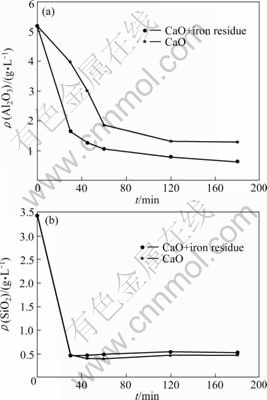
图6 铁渣对CaO脱除铝硅的影响
Fig.6 Effect of iron residue on separation of Al and Si from solution (SiO2 3.43 g/L, Al2O3 5.19 g/L): (a) Al2O3; (b) SiO2
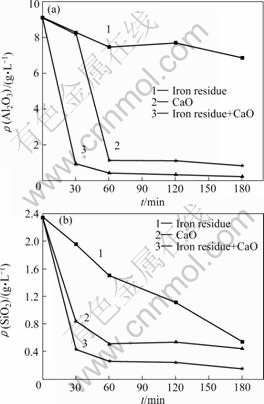
图7 铁渣对CaO脱除铝硅的影响
Fig.7 Effect of iron residue on separation of Al and Si from solution (SiO2 2.34 g/L, Al2O3 9.09 g/L): (a) Al2O3; (b) SiO2
图8所示为当SiO2浓度为2.34 g/L,Al2O3浓度为9.09 g/L时所生成脱铝硅产物的XRD谱。由XRD谱可知,无铁渣存在时脱铝硅产物为Ca2.93Al1.97- Si0.64O2.56(OH)9.44,有铁渣存在时脱铝硅产物为Ca3AlFe(SiO4)(OH)8,而且两者均无CaCrO4生成。因此,在进行加氧化钙脱除铝硅过程中,只需根据实际浸出液中Al2O3和SiO2浓度,按照生成Ca3AlFe(SiO4)- (OH)8的情况加入相应量的CaO即可。
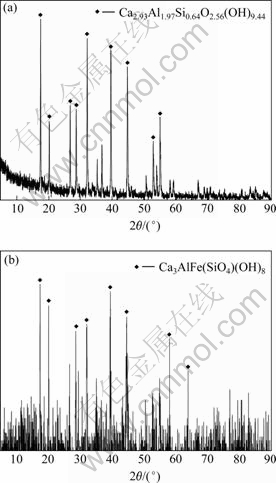
图8 有无铁渣存在时脱铝硅产物的XRD谱
Fig.8 XRD patterns of products reacting with and without iron residue: (a) Without iron residue; (b) With iron residue
3.4 K2CO3含量对CaO脱除铝硅的影响
图9所示为反应温度90 ℃、添加CaO 20 g/L条件下,不同K2CO3含量对添加CaO脱除铝硅的影响。由图可以看出,浸出液中K2CO3含量变化对添加CaO脱除铝硅的影响不大。生成脱铝硅固相均为Ca2.93Al1.97Si0.64O2.56(OH)9.44。
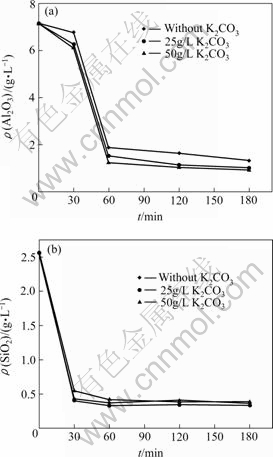
图9 K2CO3含量对CaO脱除铝硅的影响
Fig.9 Effect of K2CO3 concentration on separation of Al and Si from solution: (a) Al2O3; (b) SiO2
4 结论
1) 添加CaO脱除铝硅,无铁渣存在时生成固相为Ca2.93Al1.97Si0.64O2.56(OH)9.44,有铁渣存在时脱铝硅产物为Ca3AlFe(SiO4)(OH)8。
2) 在反应温度70~90 ℃,根据实际浸出液成分,按照生成Ca3AlFe(SiO4)(OH)8或Ca2.93Al1.97Si0.64- O2.56(OH)9.44添加CaO情况下,浸出液中的铝硅可以脱除到要求值。
3) 铁渣的存在以及添加过量CaO均可以加速铝硅脱除反应的速度,提高铝硅的脱除率。
4) 溶液中K2CO3浓度对CaO脱除铝硅的影响不大。
REFERENCES
[1] 丁 翼. 我国铬盐生产状况及发展建议[J]. 无机盐工业, 2000, 32(4): 28-30.
DING Yi. Present status and development proposal on chromate production in China[J]. Inorganic Chemicals Industry, 2000, 32(4): 28-30.
[2] 李兆山. 铬盐行业的现状及发展建议[J]. 无机盐工业, 2006, 38(4): 1-5.
LI Zhao-shan. The current status and development suggestion of chromium salts industry[J]. Inorganic Chemicals Industry, 2006, 38(4): 1-5.
[3] 丁 翼. 中国铬盐生产状况与展望[J]. 化工进展, 2004, 23(4): 345-348.
DING Yi. Present status and prospect of chromate production in China[J]. Chemical Industry and Engineering Progress, 2004, 23(4): 345-348.
[4] 顾宗勤. 浅议我国铬盐行业的规划发展[J]. 化工技术经济, 1999, 16(3): 11-13.
GU Zong-qin. On planning and developing of China chromate industry[J]. Chemical Technology Economy, 1999, 16(3): 11-13.
[5] 郑诗礼, 张 懿, 李佐虎, 齐 涛. 铬酸钾的清洁生产方法[P]. 中国专利01141683.1. 2001-10-08.
ZHENG Shi-li, ZHANG Yi, LI Zuo-hu, QI Tao. A cleaner production process of K2CrO4[P]. CN 01141683.1, 2001-10-08.
[6] 李佐虎, 张 懿, 郑诗礼, 齐 涛, 李会泉, 徐红彬, 王志宽. 铬酸盐的生产方法[P]. 美国PCT/CN03/00199. 2003-03-19.
LI Zuo-hu, ZHANG Yi, ZHENG Shi-li, QI Tao, LI Hui-quan, XU Hong-bin, WANG Zhi-kuan. A production method of chromate[P]. US PCT/CN03/00199. 2003- 03-19.
[7] ZHANG Yi, LI Zuo-hu, QI Tao, WANG Zhi-kuan, ZHENG Shi-li. Green chemistry of chromate cleaner production[J]. The Chemistry, 1999, 17(3): 258-265.
[8] 成思危, 丁 冀, 杨春荣. 铬盐生产工艺[M]. 北京: 化工出版社, 1998: 133-142.
CHENG Si-wei, DING Ji, YANG Chun-rong. Chromate production process[M]. Beijing: Chemical Industry Press, 1998: 133-142.
[9] 徐红彬, 张 懿, 李佐虎, 李会泉. 铬盐清洁生产工艺中铝的脱除[J]. 化工进展, 2003, 1: 46-48.
XU Hong-bin, ZHANG Yi, LI Zuo-hu, LI Hui-quan. Separation of aluminum in the clean production process for potassium dichromate[J]. Chemical Industry and Engineering Progress, 2003, 1: 46-48
[10] 元炯亮, 张 懿. 高苛性化系数铝酸钠溶液深度脱硅[J]. 化工冶金, 1999, 20(4): 342-346.
YUAN Jiong-liang, ZHANG Yi. Deep desilication of sodium aluminate solution with a high caustic module[J]. Engineering Chemistry & Metallurgy, 1999, 20(4): 342-346.
[11] 刘连利, 翟玉春, 田彦文. 六方水合铝酸钙的性质研究[J]. 轻金属, 2003, 3: 19-21.
LIU Lian-li, ZHAI Yu-chun, TIAN Yan-wen. Property study of hexagonal calcium aluminate hydrate[J]. Light Metals, 2003, 3: 19-21.
[12] 刘连利, 翟玉春, 田彦文, 王雅静, 韩跃新. 水合硫铝酸钙的合成[J]. 中国有色金属学报, 2003, 13(2): 506-510.
LIU Lian-li, ZHAI Yu-chun, TIAN Yan-wen, WANG Ya-jing, HAN Yue-xin. Synthesis of calcium hydroaluminosulfate[J]. The Chinese Journal of Nonferrous Metals, 2003, 13(2): 506-510.
[13] 刘桂华, 李小斌, 彭志宏, 张传福, 刘祥民. 氧化钙或氢氧化钙与浓碱铝酸钠溶液的反应特性[J]. 中国有色金属学报, 2000, 4(2): 266-269.
LIU Gui-hua, LI Xiao-bin, PENG Zhi-hong, ZHANG Chuan-fu, LIU Xiang-min. Reaction behavior between calcium oxide or calcium hydroxide and aluminate solution with heavy caustic soda[J]. The Chinese Journal of Nonferrous Metals, 2000, 4(2): 266-269.
[14] 刘连利, 刘玉静, 翟玉春. 铝酸钠溶液深度脱硅的研究[J]. 化学世界, 2005, 8: 458-461.
LIU Lian-li, LIU Yu-jing, ZHAI Yu-chun. Study on deep desilication in alumina production[J]. Chemical World, 2005, 8: 458-461.
[15] 韩登仑. 无钙铬渣湿法解毒技术[J]. 铬盐工业, 2004, 2: 57-58.
HAN Deng-lun. Hydro-based detoxification technology of chromium slag produced by calcinations[J]. Chromate Industry, 2004, 2: 57-58.
[16] 高胜利. 无机化合物性质手册[M]. 西安: 陕西科学技术出版社, 1987: 102-103.
GAO Sheng-li. Properties of inorganic compound[M]. Xi’an: Shaanxi Scientific and Technical Press, 1987: 102-103.
[17] Linke W F. Solubilities of inorganic and metal-organic compounds[M] (4th Ed). Washington DC: American Chemical Society 1958.
[18] 徐红彬. 铬系亚熔盐法铬盐清洁工艺的分离工程应用基础研究与优化[D]. 北京: 中国科学院过程工程研究所, 2003.
XU Hong-bin. Applied fundamental research on the separation operations in the chromate cleaner production process based on potassic sub-molten salt techniques[D]. Beijing: Institute of Process Engineering, Chinese Academy of Sciences, 2003.
(编辑 李向群)
基金项目:国家自然科学基金重点资助项目(50234040);国家高技术研究发展计划资助项目(2005AA647010)
收稿日期:2006-09-21;修订日期:2007-04-11
通讯作者:郑诗礼,副教授,博士;电话:010-82610244;E-mail: slzheng@home.ipe.ac.cn