网络首发时间: 2013-12-27 16:49
稀有金属 2014,38(02),193-201 DOI:10.13373/j.cnki.cjrm.2014.02.004
B/Zr摩尔比对Al-Zr-B合金的组织和晶粒细化效果的影响
钟芳华 戚文军 王顺成 周海涛 陈学敏 彭谦之
广东省工业技术研究院金属加工与成型技术研究所
中南大学材料科学与工程学院
新星化工冶金材料(深圳)有限公司
摘 要:
以Al, K2ZrF6和KBF4为原料, 采用熔体反应法制备不同B/Zr摩尔比Al-Zr-B合金。利用光学显微镜 (OM) 、扫描电子显微镜 (SEM) 、X射线衍射分析 (XRD) 等手段研究了B/Zr摩尔比对Al-Zr-B中间合金的组织和晶粒细化效果的影响。结果表明, 随着B/Zr摩尔比的增加, Al-Zr-B中间合金的第二相组成发生改变。当B/Zr摩尔比为1时, 第二相主要由粗大的块状ZrAl3相及少量团聚在晶界上的ZrB2粒子组成;当B/Zr摩尔比为2时, 第二相为ZrB2粒子和少量块状ZrAl3相。当B/Zr摩尔比为3时, 第二相全部为ZrB2粒子。对AZ91D合金的细化实验表明, 随着B/Zr摩尔比的增加, 晶粒细化效果越好, 添加B/Zr摩尔比为3的Al-Zr-B中间合金具有明显的细化效果, 合金由粗大的树枝晶转变成细小的等轴晶, 固溶处理后的AZ91D合金平均晶粒尺寸由约328μm下降到约120μm;抗拉强度和延伸率达到213 MPa和4.95%, 比未添加细化剂时分别提高了15.1%和30.3%。晶粒细化机制可归结为ZrB2粒子作为α-Mg的异质形核核心。
关键词:
Al-Zr-B中间合金;B/Zr摩尔比;镁合金;晶粒细化;
中图分类号: TG146.21
作者简介:钟芳华 (1988-) , 男, 广东韶关人, 硕士, 研究方向:镁合金细化剂;E-mail:zfh982298@163.com;;戚文军, 教授级高级工程师;电话:13318803859;E-mail:qiwenjun987@sohu.com;
收稿日期:2013-06-06
基金:国家科技部高技术研究发展计划 (863计划) (2013AA031001);广东省教育部产学研结合项目 (2010A090200078, 2012B090600051) 资助;
Microstructure and Grain Refinement of Al-Zr-B Alloy with Different B/Zr Mole Ratios
Zhong Fanghua Qi Wenjun Wang Shuncheng Zhou Haitao Chen Xuemin Peng Qianzhi
Institute of Metal Processing and Forming Technology, Guangdong General Research Institute of Industrial Technology
School of Materials Science and Engineering, Central South University
Xinxing Chemical & Metallurgical Materials ( Shenzhen) Co. Ltd.
Abstract:
The Al-Zr-B master alloys with different B /Zr mole ratios were prepared by the direct melt reaction method with Al, K2ZrF6powder and KBF4powder as raw materials. The influence of B / Zr ratio on the microstructure and grain refinement of Al-Zr-B master alloy was investigated by optical microscope ( OM) , scanning electron microscopy ( SEM) and X-ray diffraction ( XRD) . The results showed that the formation of the secondary phases in Al-Zr-B alloy firmly depended on the B / Zr mole ratio. The secondary phases were mainly composed of ZrAl3which was coarse and massive, and ZrB2particles which were easy to join together to form some particle clusters and distribute along the α ( Al) grain boundary when the B / Zr mole ratio was about 1. The secondary phases were mainly composed of ZrB2particles and a few ZrAl3phases when the B / Zr mole ratio was about 2. All the secondary phases were ZrB2particles when the B / Zr mole ratio was about 3. The refining experiment showed that the refining effect became better with the increase of B / Zr mole ratio, the Al-Zr-B master alloy with a B / Zr mole ratio of 3 had a desirable refining effect, which led the coarse dendrite to small equiaxial grains. After solid solution treatment on AZ91D alloy, the average grain sizes could be refined from 328 to 120 μm, and its tensile strength and elongation were 213 MPa and 4. 95%, respectively, which were increased by 15. 1% and 30. 3% compared with the AZ91D alloy without addition of Al-Zr-B master alloy. The mechanism of grain refinement was ascribed to the ZrB2particles acting as the heterogeneous nucleus of primary α-Mg phase.
Keyword:
Al-Zr-B master alloy; B /Zr mole ratio; magnesium alloy; grain refinement;
Received: 2013-06-06
镁合金是迄今在工业中应用的最轻的金属结构材料, 具有重量轻、密度小、比强度和比刚度高、电磁屏蔽性和减震性好、良好的尺寸稳定性以及机加工性能好优良等特性, 在航空航天、汽车、摩托车、3C等行业具有广阔的应用前景[1 - 3]。AZ91D镁合金是目前工业上应用最广泛的Mg-Al基合金[4 - 5], 由于凝固时其结晶温度区间较宽, 晶粒有明显的粗化倾向, 且容易产生热裂和显微疏松、缩孔等铸造缺陷[6 - 7], 对其力学性能和耐蚀性能十分不利。晶粒细化可以有效减少组织缺陷并进而提高其力学性能[8 - 10]。
对于不含铝的镁合金, 加Zr变质处理是目前最为行之有效的方法并已得到广泛的应用。然而对于Mg-Al系合金不能用Zr细化晶粒, 这主要是因为Zr和Al容易形成稳定的化合物Zr Al3, 而Zr Al3晶体为体心正方, 其晶格常数与Mg相差较大, 而且形成的Zr Al3会造成合金中Al和Zr的损失[11]。Mg-Al系合金的传统晶粒细化工艺是过热处理和碳质孕育法, 然而这些方法都存在一些问题, 特别是环保问题。过热处理过程中为防止氧化燃烧而采用的SF6 会导致大气变暖。碳质孕育法容易产生一些有毒的挥发性物质, 对环境不利。此外, 存在细化效果不佳、操作不便等缺点, 而且生成的Al4C3含量无法定量控制[12 - 13]。因此, 有必要寻求更为适宜的晶粒细化剂以提高镁合金的力学性能。
目前, 关于Al-Zr-B合金对Mg-Al系镁合金的细化研究鲜有报道。已有的报道中仅有赵玉涛等研究了原位合成Zr B2粒子对Zr B2/ AZ91D镁基复合材料晶粒细化的影响, 其研究表明Zr B2对AZ91D合金组织具有细化效果[13]。本文通过制备不同Zr/B摩尔比的Al-Zr-B中间合金, 研究了Zr/B摩尔比对Al-Zr-B中间合金的显微组织与晶粒细化效果的影响。
1 实验
实验材料为商用AZ91D镁合金、工业纯铝 ( 纯度为99. 95% ) 、氟锆酸钾 ( K2Zr F6) 粉剂 ( 纯度大于99. 0% ) 、 氟硼酸钾 ( KBF4) 粉剂 ( 纯度大于99. 0% ) 。按照不同的B / Zr摩尔比配置了3 种中间合金, 如表1 所示。实验前, 先控制锆含量占铝熔体的5% , 然后将K2Zr F6和KBF4按不同的摩尔比混合均匀后, 在200 ℃下烘烤3 h, 除去结晶水。同时将工业纯铝锭在电阻炉中融化, 并过热至800 ℃时保温, 向熔体中加入不同摩尔比的 ( K2Zr F6+KBF4) 混合粉剂, 用钟罩压入熔体中, 并用不锈钢棒搅拌以使其充分反应。反应时间为15 min, 反应结束后用熔剂精炼除渣, 静置30 min, 在720 ℃ 时浇注到 Φ100 mm ×200 mm的钢锭模中。
在8 k W井式坩埚电阻炉内加热熔化AZ91 合金, 为减少熔炼过程中的氧化和烧损, 以0. 5% ( 体积分数) SF6+ CO2混合气体保护, 熔炼温度为720 ℃ 。工艺过程为: 取适量的AZ91D合金放在电阻炉坩埚中, 在混合气体保护的条件下, 用电阻炉加热至720 ℃, 待合金完全融化后加入0. 2% 的不同B /Zr摩尔比的Al-Zr-B中间合金并搅拌至其完全熔化后静置10 min, 随后精炼, 精炼后静置20min, 然后在720 ℃ 时浇注到金属型模具中。金相试样均在中心部位切取, 经研磨、抛光后用体积分数为4% 的硝酸酒精腐蚀。为了能清晰地显示晶界, 试样在415 ℃固溶处理20 h水冷后, 用3% 草酸混合溶液腐蚀。
利用D/max-3B型X射线衍射仪进行物相分析, 利用Leica数字金相显微镜分析固溶处理前后试样的显微组织, 并用截线法测量晶粒尺寸, 并用Joel JSM-820 型扫描电子显微镜进一步观察微观组织, 采用DNS200 微机控制电子万能拉伸试验机进行拉伸试验。
表1 3 种B/Zr摩尔比试验合金成分Table 1 Chemical composition of 3 kinds of B/ Zr mole ratio alloy 下载原图
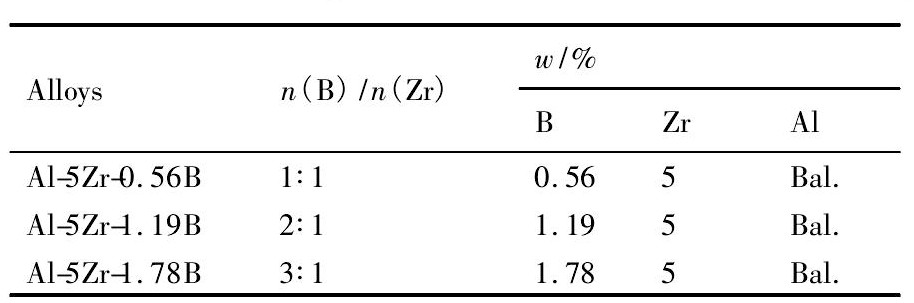
表1 3 种B/Zr摩尔比试验合金成分Table 1 Chemical composition of 3 kinds of B/ Zr mole ratio alloy
2 结果与讨论
2. 1 B / Zr摩尔比对Al-Zr-B合金组织的影响
图1 为Al-K2Zr F6-KBF4体系在850 ℃ 采用熔体直接反应法合成Al-Zr-B合金的XRD谱和显微组织。从图1 ( a) 中可以看出, 不同B /Zr摩尔比的Al-Zr-B合金的相组成是不一样的, 当B / Zr摩尔比为1 时, Al-5Zr-0. 56B合金主要由Al, Zr B2, Zr Al3三相组成; 当B /Zr摩尔比为2 和3 时, Al-5Zr-1. 19B和Al-5Zr-1. 78B合金均由Al, Zr B2两相组成。从图1 ( b) , ( c) , ( d) 还可以发现不同B /Zr摩尔比的Al-Zr-B中间合金的组织也存在一定的差异。Al-5Zr-0. 56B合金的第二相主要由呈块状或杆状的灰色相及少量团聚在晶界上的黑色颗粒组成, 灰色的块状相大小不一, 尺寸从几个微米到几十个微米不等, 如图1 ( b) 所示; 当B /Zr摩尔比增加到2 时, 合金中的灰色块状相基本消失, 只有少量的一些存在于晶界上, 而团聚在晶界上的黑色颗粒相显著增加, 如图1 ( c) 所示; 随着B /Zr摩尔比进一步增加到3, 合金的整个晶体上都分布着黑色的小颗粒相, 灰色块状相完全消失, 如图1 ( d) 所示。
图2 和3 分别是图1 中灰色块状相及团聚在晶界上的黑色小颗粒的SEM照片与能谱分析结果。从图2 ( a) 中可以看出, 灰色块状相主要分布在晶界上, 尺寸从2 ~ 15 μm不等。从图2 ( b) 的能谱分析可见, 灰色相含Al和Zr, Al和Zr的质量百分数分别为43. 96% 和56. 04% , 原子百分数分别为72. 61% 和27. 39% , 证明其是Zr Al3。从图3 ( a) 中可以看出, 团聚在晶界上的小颗粒是相互独立或是由小颗粒组成小团簇, 其尺寸约为0. 5 μm。从图3 ( b) 的能谱分析可见, 其主要含B, Al, Zr, Al可能是来源于基体, B和Zr的原子分数分别为43. 97% 和15. 30% , 证明该粒子是Zr B2。
850 ℃ 左右, K2Zr F6和KBF4在铝熔体中会发生下列反应, 如表2 所示。由表2 中数据可看到, 表中各个化学反应吉布斯自由能 ΔG° 都为负值[14], 说明在热力学上这些反应都能够发生。从表中还可以看出, 当B /Zr摩尔比为2 时, 反应产物为Zr B2, 但是在图1 ( c) 中发现还存在微量的块状Zr Al3相, 其原因可能是KBF4密度更小, 反应过程中KBF4粉末更容易随反应产物上浮到溶液表面, 使KBF4粉末损耗量较大, 而多余的K2Zr F4则与Al反应生成了Zr Al3。
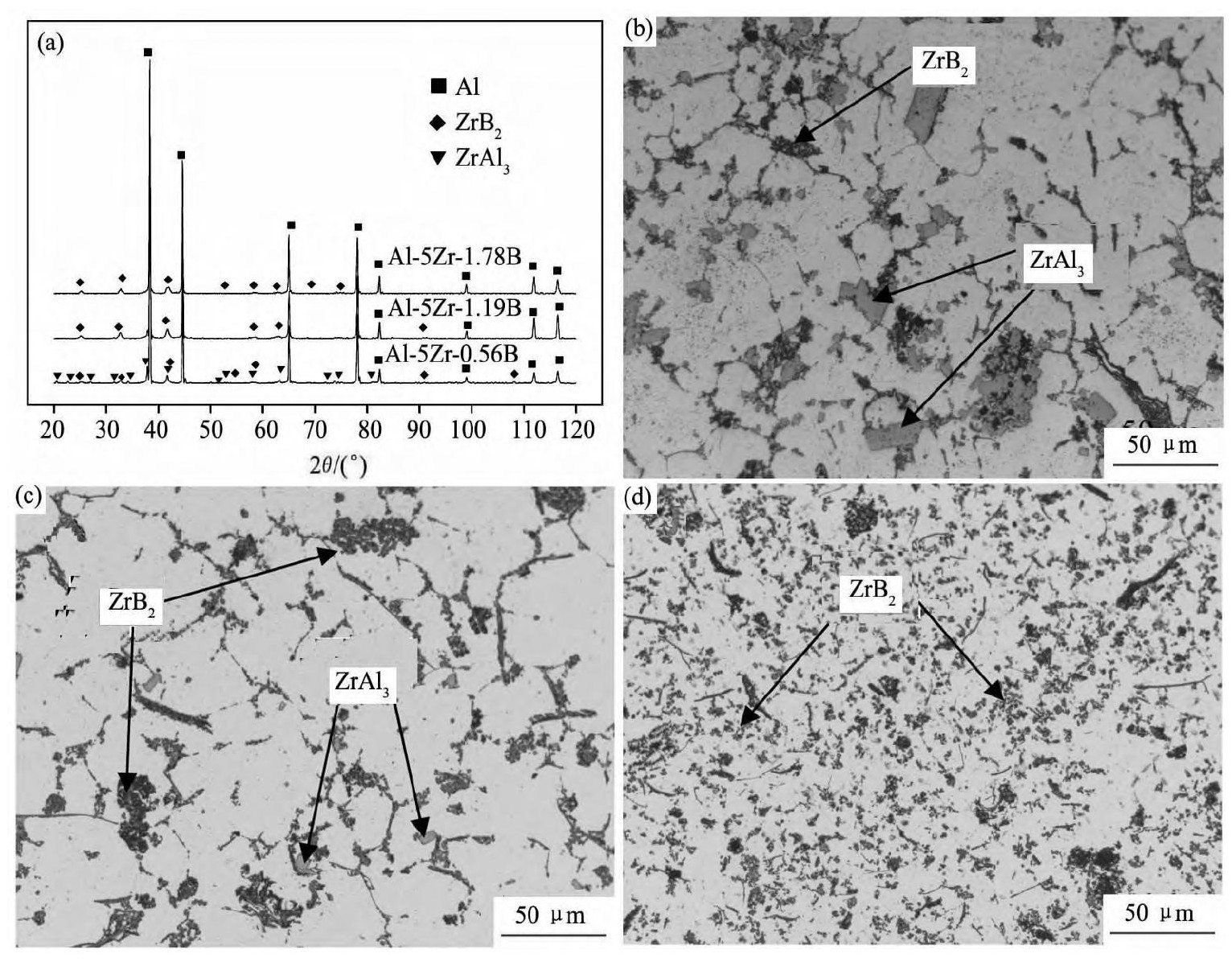
图1 不同B/Zr摩尔比Al-Zr-B中间合金的显微组织Fig. 1 Microstructures of Al-Zr-B master alloy with different B / Zr mole ratio
(a) XRD pattern; (b, c, d) OM images: (b) Al-5Zr-0.56B; (c) Al-5Zr-1.19B; (d) Al-5Zr-1.78B
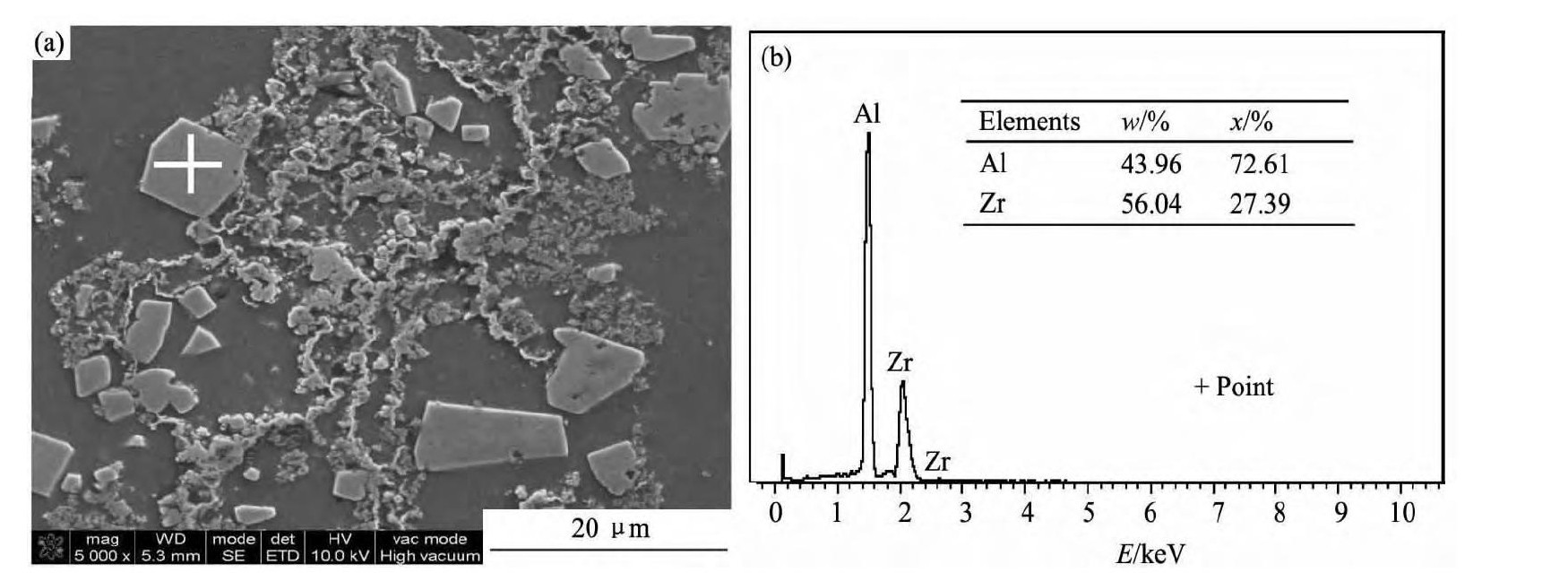
图 2 Zr Al3的 SEM 像和能谱分析Fig. 2 SEM image ( a) and EDS analysis ( b) of Zr Al3
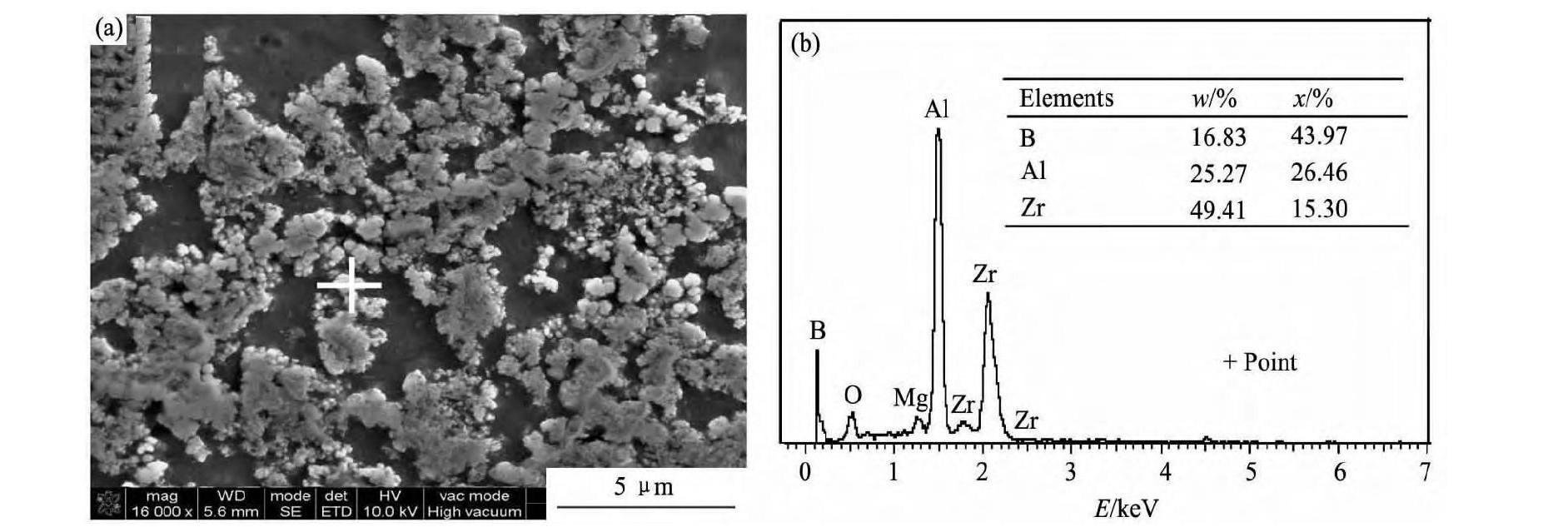
图 3 Zr B2的 SEM 像和能谱分析Fig. 3 SEM image ( a) and EDS analysis ( b) of Zr B2
表2 熔体中的化学反应和1000 K吉布斯自由能Table 2 Reactions and standard Gibbs free energy values at 1000 K 下载原图

表2 熔体中的化学反应和1000 K吉布斯自由能Table 2 Reactions and standard Gibbs free energy values at 1000 K
2. 2 不同B / Zr摩尔比的Al-Zr-B合金对AZ91D合金的晶粒细化效果的影响
图4 为AZ91D合金添加0. 2% 的不同B/Zr摩尔比的Al-Zr-B中间合金后在铸态下的显微组织。从图4 ( a) 可以看出, 未添加细化剂时, AZ91D基体合金由粗大的 α-Mg树枝晶组成, 二次枝晶臂长而粗大, 二次枝晶臂间距也较大。当加入B/Zr摩尔比为1 的Al-5Zr-0. 56B中间合金后, AZ91D合金的一次枝晶及二次枝晶稍微有些细化, 但变化程度不大 ( 图4 ( b) ) 。然而当加入B/Zr摩尔比为2 的Al-5Zr-1. 19B中间合金后, AZ91D合金的铸态组织发生了明显的转变, 粗大的 α-Mg树枝晶消失, 形成了均匀的等轴晶 ( 图4 ( c) ) 。当加入B/Zr摩尔比为3 的Al-5Zr-1. 78B中间合金后, 等轴晶变为更加细小、均匀, 说明组织得到进一步细化 ( 图4 ( d) ) 。

图 4 添加 Al-Zr-B 中间合金后 AZ91D 镁合金的铸态显微组织Fig. 4 Microstructures of AZ91D with addition of Al-Zr-B master alloy
( a) 0; ( b) Al-5Zr-0. 56B; ( c) Al-5Zr-1. 19B; ( d) Al-5Zr-1. 78B
图5 为AZ91D合金添加0. 2% 的不同B /Zr摩尔比的Al-Zr-B中间合金后经415 ℃固溶20 h后的金相照片。固溶处理后, 晶粒并没有长大, β 相完全溶入 α-Mg基体, 组织为单相过饱和的 α-Mg固溶体, 无规则分布于晶界及基体上的黑色颗粒相为Al-Mn化合物。研究表明, Al-Mn化合物对Mg-Al系合金没有细化作用[15]。从图5 可以看出, 未添加细化剂时, AZ91D基体合金的晶粒粗大且尺寸分布不均匀, 平均晶粒尺寸约为328 μm ( 图5 ( a) ) 。添加Al-5Zr-0. 56B中间合金后, 晶粒大小并没有得到明显变化, 平均晶粒尺寸约为320 μm ( 图5 ( b) ) 。但添加Al-5Zr-1. 19B中间合金后, AZ91D基体合金的晶粒明显得到细化, 晶粒大小也比较均匀 ( 图5 ( c) ) 。与Al-5Zr-1. 19B中间合金相比, 添加Al-5Zr-1. 78B中间合金后的AZ91D合金晶粒更加细小, 平均晶粒尺寸降低到120 μm ( 图5 ( d) ) 。
伴随着AZ91D镁合金的晶粒细化, 其第二相的形貌及分布也发生改变。图6 所示为添加不同B / Zr摩尔比的Al-Zr-B中间合金前后AZ91D合金的SEM组织, 图6 中白色颗粒为Al-Mn化合物, 灰色部分为共晶相Mg17Al12。从图6 ( a) 中可以看出, 未添加细化剂前, α 枝晶周围的Mg17Al12相粗大且易于聚集成团状, 呈网格状分布在 α 枝晶界面上; 当添加Al-5Zr-0. 56B的中间合金后, Mg17Al12相仍呈半连续状分布在晶界面上, 如图6 ( b) 所示; 但添加Al-5Zr-1. 19B中间合金后, 合金的第二相发生明显改变, 原来网状的Mg17Al12相完全消失, 变成长条状或颗粒状, 第二相尺寸也明显减小, 如图6 ( c) 所示; 而添加Al-5Zr-1. 78B中间合金后, Mg17Al12相变得更加细小、离散分布在晶界上, 如图6 ( d) 所示。Mg17Al12相形貌的这种变化主要是源于初生 α-Mg相的细化, 晶粒细化过程减小了位于晶粒间的高溶质含量熔体的体积, 增加了晶界的数量, 从而使凝固的最后阶段达到共晶成分的液相分布比较均匀, 单位晶界面积上的共晶相减少。
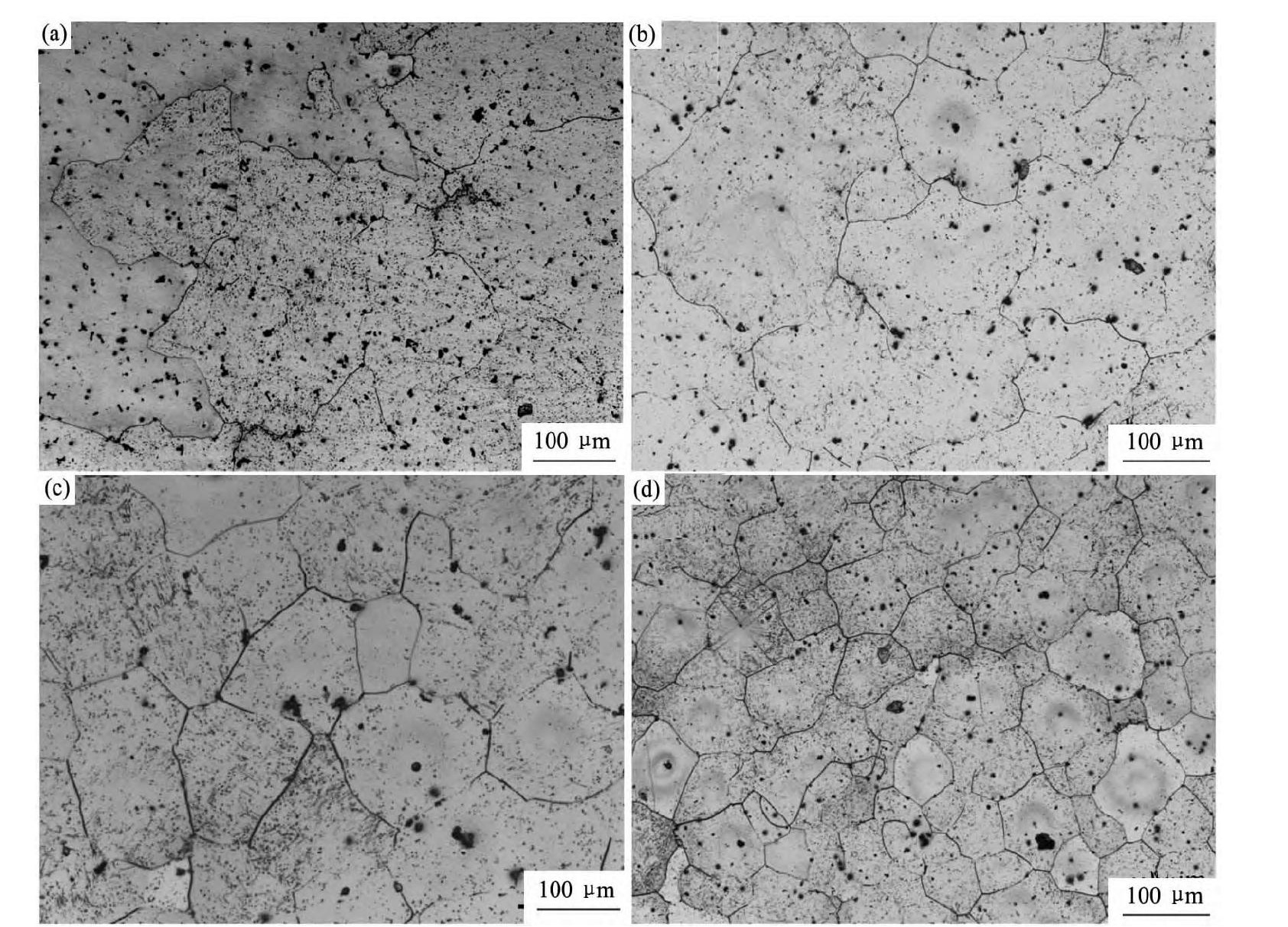
图 5 添加 Al-Zr-B 中间合金固溶处理后 AZ91D 镁合金的显微组织Fig. 5 Microstructures of AZ91D with addition of Al-Zr-B master alloy and solid solution treatment
( a) 0; ( b) Al-5Zr-0. 56B; ( c) Al-5Zr-1. 19B; ( d) Al-5Zr-1. 78B
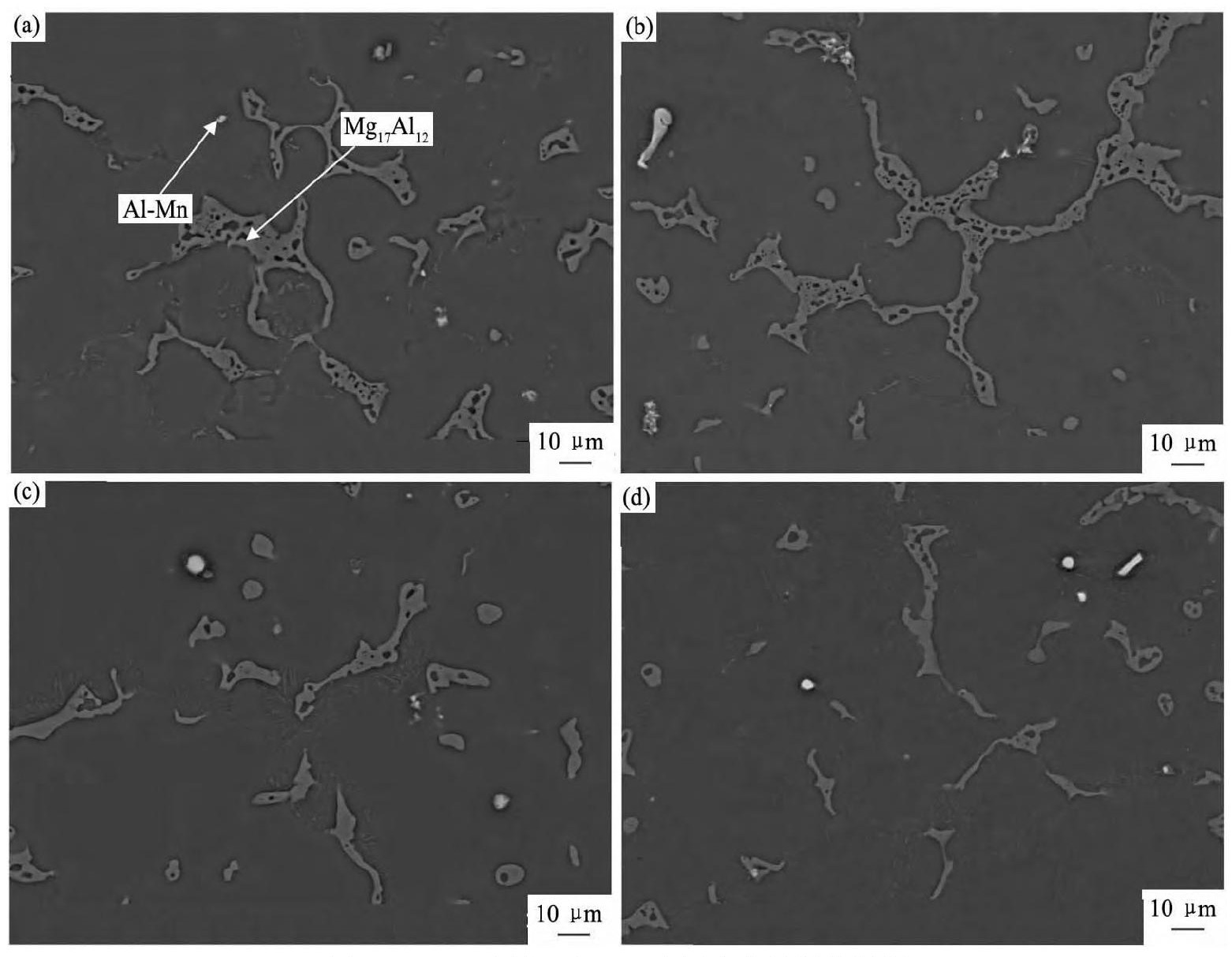
图6 AZ91D添加Al-Zr-B中间合金的显微组织Fig. 6 Microstructures of AZ91D with addition of Al-Zr-B master alloy
(a) 0; (b) Al-5Zr-0.56B; (c) Al-5Zr-1.19B; (d) Al-5Zr-1.78B
2. 3 细化机制
图7 所示为添加0. 2% Al-5Zr-1. 78B中间合金的AZ91D合金的面扫描结果, 从图7 中可以看出, Zr和B元素确实存在于镁合金中, 主要位于晶界上和晶粒中心。Mg-Al系合金中的铝本身对合金具有晶粒细化作用, 根据Lee等[16]的研究结果, 当铝含量达到5% 时, 其晶粒细化作用基本达到极限。在本文的研究过程中发现, 添加Al-5Zr-0. 56B中间合金对AZ91D合金基本没有细化效果; 而添加Al-5Zr-1. 78B中间合金后, 细化效果十分显著, 其结果表明AZ91D合金的细化显然是与加入的Al-Zr-B合金的B元素含量密切相关。在不同B和Zr摩尔比的Al-Zr-B中间合金中, B元素含量及第二相具有较大差别。在Al-5Zr-0. 56B中间合金中, 熔体中Zr与B反应生成Zr B2相后, 熔体中过剩的Zr与Al生成Zr Al3相, Zr Al3属于四方结构, 与镁的晶体结构不匹配, 不能细化镁合金; 而在Al-5Zr-1. 78B中间合金中, 由于B元素过量, 可以保证生成的第二相中不含Zr Al3相, Zr B2 ( 熔点为3273 K) 和 α-Mg同属于六方晶系, 在镁熔体中以固态质点形式稳定存在, 其晶格常数 ( aZr B2= 0. 3169 nm, cZr B2= 0. 3530 nm ) 与 α-Mg的晶格常数 ( aMg=0. 3203 nm, cMg= 0. 5200 nm) 相近[13]。
一般认为, 异质形核能力的大小取决于形核基底与结晶相之间的界面能。而影响界面能的主要因素包括基底与结晶相间的点阵错配度、颗粒的大小和分布、基底的表面形态、化学性质以及基底与结晶相间的静电位。当点阵错配引起弹性能急剧升高时, 基底与结晶相间的点阵错配度是决定界面能的主要因素。Bramfitt提出[17], 错配度的计算使晶核的低指数基面与作为基底物质的低指数晶面重合。
根据Bramfitt建立的二维点阵错配度理论模型, Zr B2和Mg在低指数晶面上的错配度可按下式计算:
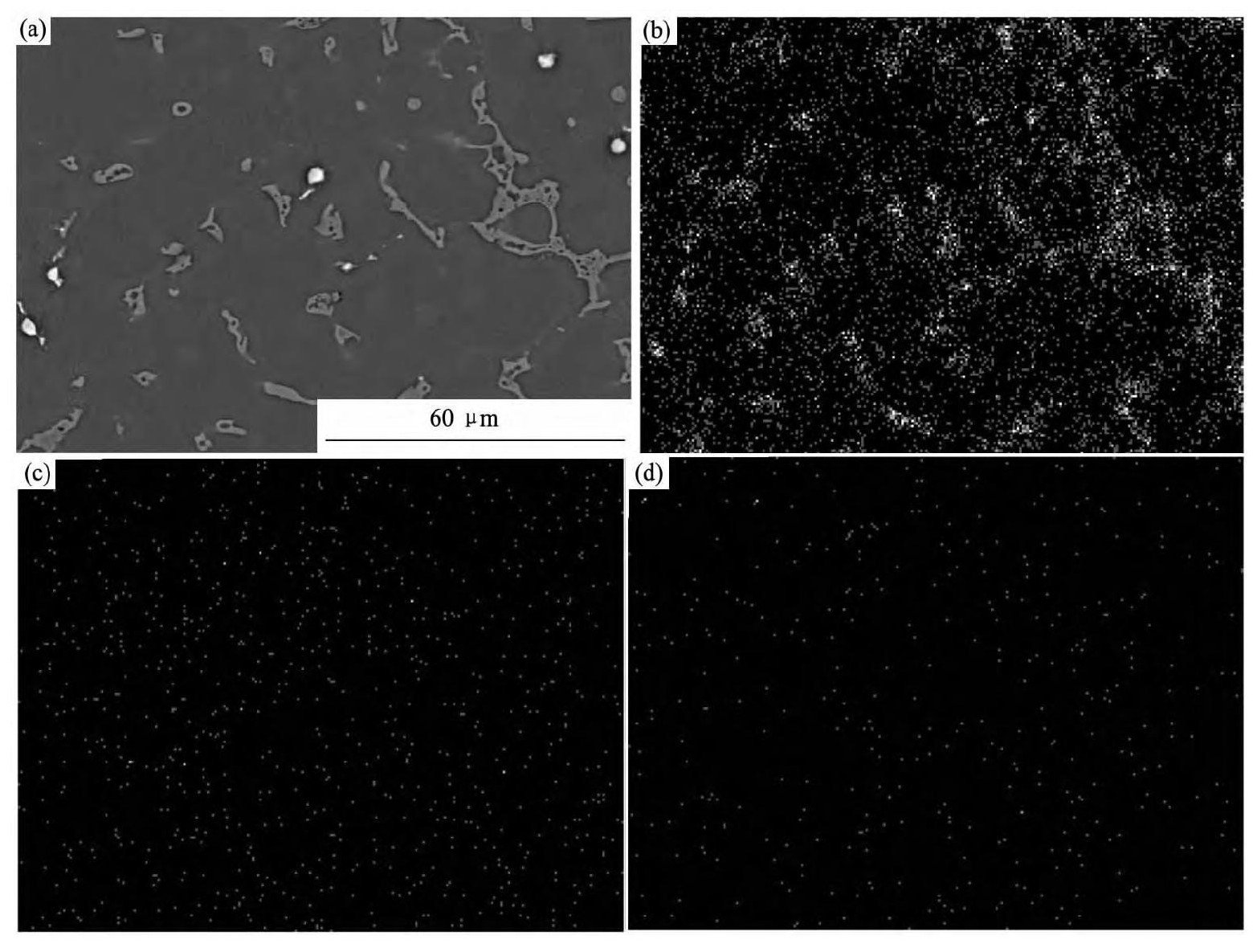
图7 添加0. 2% Al-5Zr-1. 78B中间合金的AZ91D合金的面扫描照片Fig. 7 SEM images of AZ91D with addition of 0. 2% Al-5Zr-1. 78B master alloy
(a) Secondary electron image; (b) Mapping of Al element; (c) Mapping of Zr element; (d) Mapping of B element
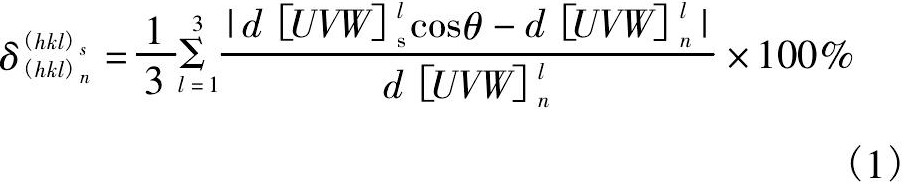
式中: ( hkl) s为基底的低指数晶面; [UVW]为 ( hkl) s晶面上的低指数晶向; ( hkl) n为核的低指数晶面; d[UVW]s和d[UVW]n分别为沿[UVW]s和[UVW]n晶向的阵点间距; θ 为[UVW]s和[UVW]n的夹角。Bramfitt的结果表明: 在非均质形核时, δ < 6% 的核心最有效; δ 为6%~ 15% 的核心中等有效; 而 δ > 15% 的核心无效。
根据式 ( 1) 可以计算Zr B2的 ( 0001) 面与Mg的 ( 0001) 面的错配度, 经计算, Zr B2的 ( 0001) 面与Mg的 ( 0001) 面的错配度为5. 11% , 基本满足共格对应的错配条件, 因此, Zr B2可以成为 α-Mg良好的异质形核核心, 使得 α-Mg晶粒细化。
2. 4不同B / Zr摩尔比的Al-Zr-B中间合金对AZ91D合金力学性能的影响
表3 所列为Al-Zr-B中间合金对AZ91D合金拉伸性能的影响。从表3 中可以看出, 当在AZ91D合金中加入Al-5Zr-0. 56B中间合金时, 合金的抗拉强度和延伸率基本基本没什么变化。但加入Al-5Zr-1. 56B中间合金后, 抗拉强度和延伸率明显增加, 随着B /Zr摩尔比的进一步增加, 合金的抗拉强度和延伸率继续增大, 当加入Al-5Zr-1. 78B中间合金时, 合金的抗拉强度和延伸率分别为213MPa和4. 95% , 比未添加细化剂时分别提高了15. 1% 和30. 3% 。AZ91D合金力学性能的这种变化趋势与合金的晶粒细化及相形态的变化是分不开的。根据Hall-Petch公式:

式中 σs为屈服应力, σ0为单晶体的屈服强度, K为滑移位向有关的系数, D为晶粒直径。从式 ( 2) 可知, 晶粒直径D与合金强度 σs成反比, 即晶粒直径D越小, 合金强度 σs越高。又依据式 ( 2) 中的系数K∝M2Tc ( M为Taylor因子, Tc为剪切应力) 可知, K与M的平方成正比, 通常Taylor因子依赖于滑移系的数目, 同面心立方 ( 如Al合金) 金属相比, 密排六方结构的镁, 其滑移系少, Taylor因子较大, 因此镁合金晶粒尺寸的大小对强度影响很大。当晶粒尺寸减小时, 晶体比表面积增加, 表面张力增加, 同时晶粒之间的相互作用力也发生变化, 这引起晶粒表面层晶格发生扭转, 使在接近晶粒界面处产生阻碍晶体变形的难变形区, 从而增加了变形抗力, 提高合金强度; 与此同时, 当合金的晶粒比较细小时, 塞积群的长度比较小, 塞积的位错数目也比较少, 应力继续作用时迫使相邻晶粒的位错源启动, 把同样的变形量分配在更多的晶粒中, 可以认为晶粒越小, 塑性也越好。当添加Al-5Zr-1. 78B中间合金时, AZ91D合金的晶粒最细小, 故其力学性能最好。另外, β 相由连续或断续网状结构变为颗粒状, 也减少对基体的割裂作用, 提高材料的力学性能。
表3Al-Zr-B中间合金对AZ91D镁合金平均晶粒尺寸、力学性能的影响Table 3Effect of Al-Zr-B master alloy on average grain size and mechanical properties of AZ91D alloy 下载原图

表3Al-Zr-B中间合金对AZ91D镁合金平均晶粒尺寸、力学性能的影响Table 3Effect of Al-Zr-B master alloy on average grain size and mechanical properties of AZ91D alloy
3 结论
1. B / Zr摩尔比对Al-Zr-B中间合金的相组成具有明显影响, Al-5Zr-0. 56B合金由Al, Zr B2, Zr Al33 相组成, 而Al-5Zr-1. 19B和Al-5Zr-1. 78B合金均由Al和Zr B2两相组成。Zr Al3主要呈块状分布在晶界上, 晶粒尺寸从2 ~ 15 μm不等; 而Zr B2主要以小颗粒状的形式团聚在晶界上, 晶粒尺寸约为0. 5 μm, 随着B /Zr摩尔比的增加, Zr B2粒子数量逐渐增加。
2. B / Zr摩尔比为3 的Al-5Zr-1. 78B中间合金对AZ91D镁合金的细化效果明显, 添加0. 2% 的Al-5Zr-1. 78B后即可使AZ91D镁合金晶粒尺寸由细化前的328 μm下降到120 μm; 抗拉强度和延伸率达到213 MPa和4. 95% , 比未添加细化剂时分别提高了15. 1% 和30. 3% ; 同时 β 相形貌发生明显改变, 分布更趋于弥散。
3. Al-5Zr-1. 78B中间合金对AZ91D镁合金具有细化作用的原因可归结为Al-5Zr-1. 78B中间合金中存在大量的Zr B2粒子的异质形核的作用。
参考文献
[1] Zhao H, Peng X D, Wang Y G, Yang Y, Wei Q Y.Research status about plasticity improvement of wrought magnesium alloys[J].Chinese Journal of Rare Metals, 2012, 36 (1) :161. (赵辉, 彭晓东, 王艳光, 杨艳, 魏群义.变形镁合金的塑性改善研究现状[J].稀有金属, 2012, 36 (1) :161.)
[3] Takuda H, Enami T, Kubota K.The formability of a thin sheet of Mg-8.5Li-1Zn alloy[J].Journal of Materials Processing Technology, 2000, 101 (3) :281.
[4] Wang Y S, Sun B D, Wang Q D, Zhu Y P, Ding W J.An understanding of the hot tearing mechanism in AZ91magnesium alloy[J].Materials Letters, 2002, 53:35.
[5] Celotto S.TEM study of continuous precipitation in Mg-9wt%Al-1wt%Zn alloy[J].Acta Mater., 2000, 48:1775.
[6] Liu S F, Wang X H, Han H, Liu L Y, Li B, Su W.Effect of Al4C3on the as cast microstructure and properties of AZ91D magnesium alloy[J].Rare Metal Materials and Engineering, 2009, 38 (7) :1247. (刘生发, 王小虎, 韩辉, 刘林艳, 李波, 苏伟.Al4C3对AZ91D镁合金铸态显微组织与性能的影响[J].稀有金属材料与工程, 2009, 38 (7) :1247.)
[7] Edward J, Vinarci K.Light metal advances in the automotive industry[J].Light Metal Age, 2001, 59 (4) :22.
[8] Liu S F, Liu L Y, Kang L G.Refinement role of electromagnetic stirring and strontium in AZ91 magnesiumalloy[J].Journal of Alloys and Compounds, 2008, 450 (1/2) :546.
[9] Bamberger M.Structural refinement of cast magnesium alloys[J].Mater.Sci.Tech., 2001, 17 (1) :15.
[10] Stjohnd H, Ma Q, Easton M A, Cao P, Hildebrand Z.Grain refinement of magnesium alloy[J].Metall.Mater.Trans.A, 2005, 36 (7) :1699.
[11] Li Y J, Tang A T.Recent development of grain refining technologies for magnesium alloys[J].Materials Review, 2013, 27 (9) :126. (李玉娟, 汤爱涛.镁合金晶粒细化的研究进展[J].材料导报, 2013, 27 (9) :126.)
[12] Lu Y H, Liu X F, Bian X F.Grain refinement of MgAl alloys with Al4C3-SiC/Al master alloy[J].Materials Lerters, 2004, 58 (7/8) :1282.
[13] Wu J J, Zhao Y T, Zhang S, Chen G, Zhang Z Y.Effects of in-situ ZrB2particle on grain refinement of ZrB2/AZ91D magnesium matrix composite[J].China Foundry, 2012, 9 (1) :28.
[14] Zhao D G, Liu X F, Pan Y C, Qiao J G, Liu Y X.Fabrication and microstructure of (ZrAl3+ZrB2) composites[J].Foundry, 2005.54 (6) :542. (赵德刚, 刘相法, 潘义川, 乔进国, 刘玉先. (ZrAl3+ZrB2) /Al复合材料的制备和微观组织结构[J].铸造, 2005, 54 (6) :542.)
[15] Nishino N, Kawahara H, Shimizu Y, Iwahori H.Grain refinement of magnesium casting alloys by boron addition[J].Mater.Sci.Tech., 2000, 16 (10) :59.
[16] Lee Y C, Dahle A K, Stjohn D H.The role of solute in grain refinement of magnesium[J].Matall.Mater.Trans.A, 2000, 31A:2895.
[17] Bramfitt Bruce L.The effect of carbide and nitride additions on the heterogeneous nucleation behavior of liquid iron[J].Metallurgical Transaction, 1970, 1 (7) :1987.