
CuCr bulk alloy produced by mechanical alloying and explosive compaction
ZHAO Zheng(赵 铮)1, LI Xiao-jie(李晓杰)2, TAO Gang(陶 钢)1, DU Chang-xing(杜长星)1
1. College of Power Engineering, Nanjing University of Science and Technology, Nanjing 210094, China;
2. State Key Laboratory of Structural Analysis for Industrial Equipment, Department of Engineering Mechanics,
Dalian University of Technology, Dalian 116024, China
Received 10 August 2009; accepted 15 September 2009
Abstract: CuCr bulk alloy was produced by mechanical alloying and explosive compaction technology. Four kinds of milling time were used to analyze the function and influence on mechanical alloying. The samples were characterized by X-ray diffraction and optical microscope, and the density and hardness of the four samples were detected. The results show that the CuCr grain size is decreased with the milling time increasing, and nano-crystalline is observed in both Cu and Cr phase after 20 h milling. The density and hardness of samples are also increased with the increase of the milling time, so that the sample relative density reaches 96.6% and hardness reaches HV 217. The results indicate that high quality of CuCr bulk alloy can be manufactured using explosive compaction method when mechanical alloying and explosive compaction process parameters are reasonably selected.
Key words: explosive compaction; mechanical alloying; CuCr alloy; particle-reinforced composite
1 Introduction
Chrome particle-reinforced copper matrix composite is also called CuCr alloy, but it is a kind of pseudo-alloy that Cr particle with high hardness and high melting point embeds in Cu matrix with high electrical conductivity. CuCr bulk alloy is widely used as vacuum switch contact at present, because of its excellent electrical conductivity, high breaking current capability, high capability of resistance electric arc corrosion and resistance surface fusion welding[1-4].
High quality CuCr bulk alloy requires that Cr phase must uniformly distribute in Cu matrix, and there is no impurity and stomata. Only so can make materials possess high density and mechanical strength. At present, there are six kinds of main methods to manufacture CuCr bulk alloy, i.e. mixed powder sintering[5], vacuum casting[6], hot isostatic pressing[7], melt infiltration, arc melting and explosive compaction[8]. While the density and strength of material made by mixed powder sintering method are not high, and vacuum casting only can manufacture bulk material that the mass fraction of Cr is lower than 15%. Hot isostatic pressing, melt infiltration and arc melting method can be used to manufacture high quality CuCr bulk alloy, but these three methods all need expensive special equipments, resulting in complicated technology and high production cost.
Explosive compaction utilizes shock wave generated by detonation of explosive to densify powders, which provides extreme high pressure (1-50 GPa) within several microseconds. The duration of loading pressure is so instantaneous that the crystal grains have no time to increase their sizes, whilst particles impact scale merely produces surface heating and high quench rate in so short time. The thermal quench rate is estimated to be about 109 ℃/s[9]. Particle deforming, porosity collapsing, surface heating and local welding occur during explosive compaction densifying mixed powders to bulk materials with excellent properties[10]. In addition, it is important that explosive compaction method does not need special equipment, which leads to simple technology and low production cost[11-12].
In this work, CuCr bulk alloy was obtained by mechanical alloying and explosive compaction technology. The function and influence of mechanical alloying were discussed according to microstructure and property of bulk samples.
2 Experimental
Explosive compaction technology of manufacturing CuCr bulk alloy comprises five processes which are powder milling, packaging, sintering, explosive compaction and post treatment, respectively.
2.1 Powder milling
Cu and Cr powder (mass ratio is 1?1) were mixed and milled via planetary high energy ball mill equipment, aiming at making CuCr power mechanical alloying, and mix uniformly. Through X-ray diffraction analysis, it is observed that Cr particles have embedded in Cu particles after milling and there are nano-crystallines in Cu and Cr particles.
2.2 Packaging
CuCr milled powders were injected into steel pipe of 20 mm in diameter. The powders were pre-compacted to 60% of relative density using hydraulic machine, afterwards steel plugs with holes were fixed at two ends of the steel pipe.
2.3 Sintering
The blowpipe was welded at steel plugs. The steel pipe filled with CuCr powder was sintered for 1 h at 800 ℃, in the meantime, hydrogen was input through blowpipe to avoid Cu particles oxidation. Cu and Cr grains will not grow excessively because the sintering process belongs to solid state sintering at low sintering temperature and short sintering time. Surface melting only occur on Cu and Cr particles, which contributes to obtain higher relative density in explosive compaction.
2.4 Explosive compaction
After cutting off the blowpipe and sealing, the steel pipe was placed in a PVC pipe, and the gap between steel pipe and PVC pipe was filled with explosive. The explosive density was 0.8 g/cm3, detonation velocity is 3 112 m/s, detonation pressure is 2 GPa, and explosive thickness is 20 mm. During detonation process, CuCr milled powders were compacted under the shock waves impacting. This kind of explosive compaction method is called direct method and its experimental equipment is shown in Fig.1.
2.5 Post treatment
After explosive compaction, the diameter and length of steel pipe both reduce, which indicates pores in particles are eliminated and powder is densified. The steel pipe filled with CuCr powder is sintered secondly for 0.5 h at 800 ℃ so as to eliminate residual pores and microcracks in particles, so that bonding strength between particles increases.
CuCr bulk alloy shown in Fig.2 is obtained after removing steel pipe. The cylinder diameter of CuCr is 20 mm and the length is 50 mm. Besides post sintering, hot extrusion or cold drawing also can improve the density and strength of the bulk material.
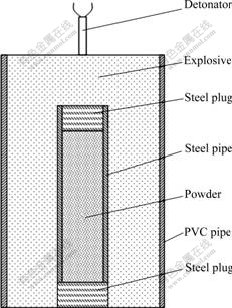
Fig.1 Equipment of direct explosive compaction
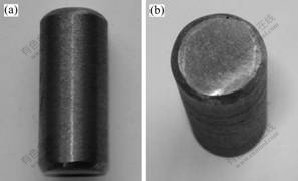
Fig.2 CuCr alloy prepared by explosive compaction: (a) Side view; (b) Front view
3 Influence of mechanical alloying
Mechanical alloying(MA) is a powerful powder processing method, which has been used to synthesize oxide dispersion strengthened alloys, amorphous alloys, and various intermetallics compounds, thermoelectric and magnetic materials. Mechanical alloying belongs to a kind of solid nonequilibrium material processing technology. It uses milling balls at high speed moving to impact and extrude powder particles, thus makes particles deform, fracture and cold weld. Finally mutual diffuseness or solid state reaction occurs, and consequently alloy powder is obtained. Mechanical alloying can not only conveniently control the powder material’s mass ratio, but also extend solid solubility and refine grain size to obtain powder material with nano-crystalline structure[13-14]. LAHIRI et al[15] got finer crystallites (<40 nm) of CuCr powder by mechanical alloying technology.
The sizes of Cu powder and Cr powder used in experiment particle were both 74 μm. Cu powder and Cr powder were mixed with mass ratio of 1?1 and were milled using planetary high energy ball mill equipment. The mass ratio of milling ball to powder was 10?1, and the rotating velocity was 300 r/min. While milling, argon atmosphere was used to avoid Cu powder oxidation. Through impacting and extruding, in CuCr particles deformation, fracture and cold welding occur. Finally, nano-crystalline shape was observed in Cu and Cr particles, and Cr particles embed in Cu particles. CuCr pseudo-alloy was obtained.
The milling process was interrupted at intervals of 5, 10, 15 and 20 h and small quantities of milled powder were drawn for examination. The structural evolution of the powder blends milled for different time was characterized by X-ray diffraction (XRD), and the XRD patterns are shown in Fig.3. The XRD patterns show that the width of diffraction peaks increase with the increase of milling time. According to Scherrer formula: D= kλ/(Bcosθ) (where D is the average grain size of powder, k=0.89, λ is the wavelength of X-ray, B is the full width at half maximum of XRD curves, θ is diffraction angle), the grain size can be calculated from the XRD curves. The broadening and weakening of the diffraction peaks indicate that the effective CuCr grain size decreases with the increase of milling time. After milling for 20 h, the Cu grain size is 92.72 nm and the Cr grain size is 70.54 nm, which indicates that there is nano-crystalline shape in Cu and Cr particles.
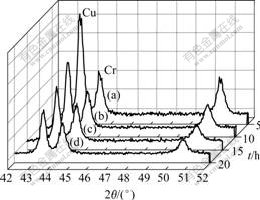
Fig.3 XRD patterns of CuCr powder after 5(a), 10(b), 15(c) and 20 h(d) milling
The morphologies of CuCr powder after milling for 5 h and 20 h are shown in Fig.4. After 5 h milling, the particle size is almost 74 μm and the particle shape is nearly ellipse. After 20 h milling, the particle size is almost 400 μm and the particle shape is nearly flake. During long time milling, continuous extruding and cold welding make Cr particle embed in Cu particle, in the meantime Cu particle deforms to flake. The microstructure of CuCr bulk alloy obtained by explosive compaction is shown in Fig.5. In Fig.5, the deep color region is Cu and the light color region is Cr. Fig.5(a) shows that Cr particles uniformly distribute in Cu matrix after 5 h milling. Fig.5(b) shows that Cu and Cr particles stack to layered structure and the Cr distribution is also homogeneous.
The density of CuCr bulk alloy obtained by explosive compaction was detected using drainage and Vickers hardness was also tested. The density and hardness of sample after different time milling are shown in Table 1. It is obvious that the density and hardness of CuCr bulk alloy increase with the increase of milling time. The relative density of sample after 20 h milling reaches 96.6%, which can be further improved through optimizing explosive compaction parameters. The hardness of sample after 20 h milling is HV 217 that is almost twice that of sample for 5 h milling.
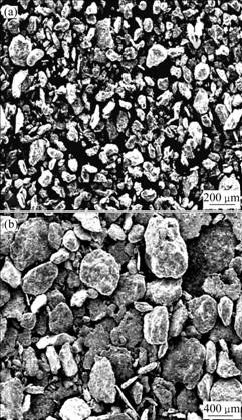
Fig.4 Morphologies of CuCr milled powder: (a) After 5 h milling; (b) After 20 h milling
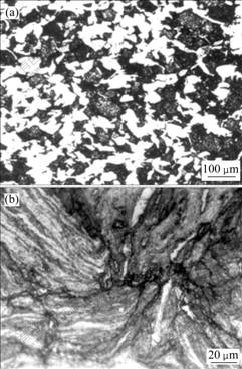
Fig.5 Microstructure of CuCr bulk alloy by explosive compaction: (a) After 5 h milling; (b) After 20 h milling
Table 1 Density and hardness of CuCr samples after different milling time
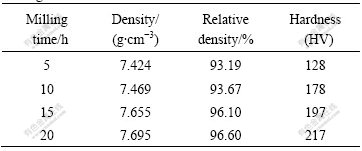
4 Conclusions
1) CuCr bulk alloy with over 96% relative density can be obtained using direct explosive compaction method. The material has higher hardness. The microstructure shows that Cr particles uniformly distribute in Cu matrix and there is no Mach hole in sample.
2) Mechanical alloying technology can not only make Cu and Cr powder mix uniformly, but also embed Cr particles into Cu particles. After continuous fracture and cold welding, Cr particles dispersively distribute in Cu matrix and CuCr super saturated solid solution can be obtained.
3) CuCr grain size decreases with the increase of milling time. After milling for 20 h, there is nano-crystalline shape in both Cu and Cr particles. The density and hardness of CuCr bulk alloy also increase with the increase of milling time, which leads to the improvement of materials properties.
References
[1] HE Wen-xiong, WANG Er-de, CHEN Hui. Effects of deformation on microstructures and properties of submicron crystalline Cu-5%Cr alloy [J]. Trans Nonferrous Met Soc China, 2007, 17: 384-388.
[2] SUN Zhan-bo, WANG You-hong, GUO Juan. Liquid phase separation of Cu-Cr alloys during rapid cooling [J]. Trans Nonferrous Met Soc China, 2006, 16: 998-1002.
[3] ZHOU Z M, WANG Y P, GAO J, KOLBE M. Microstructure of rapidly solidified Cu-25wt.% Cr alloys [J]. Mater Sci Eng A, 2005, 398: 318-322.
[4] LAMPERTI A, OSSI P M, ROTSHTEIN V P. Surface analytical chemical imaging and morphology of Cu-Cr alloy [J]. Surf Coat Technol, 2006, 200: 6373-6377.
[5] LAHIRI I, BHARGAVA S. Compaction and sintering response of mechanically alloyed Cu-Cr powder [J]. Powder Technol, 2009, 189(3): 113-117.
[6] SHUAI G W, ZHANG M, DING Y. Effect of vacuum casting process on microstructure and properties of CuCr alloy [J]. J Mater Sci Technol, 2007, 1: 68-71.
[7] LU D M, LIN X Y, ZHOU W P. Preparation of vacuum contact material for Cu-Cr system by use of HIP process [J]. Powder Metall Industry, 1997, 1: 17-22. (in Chinese)
[8] LI Xiao-jie, ZHAO Zheng, QU Yan-dong. Producing CuCr alloy by explosive sintering [J]. Explo Shock Wave, 2005, 3: 251-254. (in Chinese)
[9] BENSON D J, NELLIS W J. Dynamic compaction of copper powder: Computation and experiment [J]. Appl Phys Lett, 1994, 65: 418-420.
[10] MAMALIS A G, VOTTEA I N, MANOLAKOS D E. On the modeling of the compaction mechanism of shock compacted powders [J]. J Mater Process Tech, 2001, 108: 165-178.
[11] ZHAO Zheng, LI Xiao-jie, YAN Hong-hao. Explosive compaction of nano-lumina particle-reinforced copper alloy [J]. Combust Explo Shock, 2008, 44(1): 119-121.
[12] ZHAO Zheng, LI Xiao-jie, TAO Gang. Manufacturing nano-alumina particle-reinforced copper by explosive compaction [J]. J Alloy Compd, 2009, 478: 237-239.
[13] ZAKERI M, ALLAHKARAMI M, KAVEI G H. Synthesis of nanocrystalline Bi2Te3 via mechanical alloying [J]. J Mater Process Tech, 2009, 209: 96-10.
[14] ZHENG H Z, LU S Q, DONG X J, OUYANG D L. Effect of mechanical alloying on microstructure, mechanical properties and oxidation behavior of hot pressed nanocrystalling Cr-33 Nb alloys [J]. Mater Sci Eng A, 2008, 496: 524-529.
[15] LAHIRI I, BHARGAVA S. Compaction and sintering response of mechanically alloyed Cu-Cr powder [J]. Powder Technol, 2008, 189: 433-438.
(Edited by CHEN Can-hua)
Foundation item: Project(10802038) supported by the National Natural Science Foundation of China; Project(0802019C) supported by Jiangsu Planned Projects for Postdoctoral Research Funds
Corresponding author: ZHAO Zheng; Tel: +86-25-84315491; E-mail: zhaozheng@126.com