文章编号:1004-0609(2008)03-0377-06
炭/炭复合材料制动过程中温度场的仿真
雷宝灵,易茂中,徐惠娟
(中南大学 粉末冶金国家重点实验室,长沙 410083)
摘 要:利用有限元热分析软件ANSYS建立炭/炭复合材料制动过程三维有限元模型,确定相关热载荷计算方法和关键参数,仿真制动过程瞬态温度场。计算结果表明:在试环轴向存在明显温度梯度,而径向温度梯度微小,摩擦表面在t=12.7 s时达到最高温度662 ℃,且最高温度出现在靠近试环外径处,与实验结果基本相符,证实了仿真计算结果的正确性。
关键词:炭/炭复合材料;温度场;有限元;制动
中图分类号:TB 332 文献标识码:A
Simulation of temperature field of carbon/carbon
composite during braking
LEI Bao-ling, YI Mao-zhong, XU Hui-juan
(State Key Laboratory of Powder Metallurgy, Central South University, Changsha 410083, China)
Abstract: The 3-dimentional finite element model of C/C composite materials during braking was established by means of finite element software ANSYSY. The calculation method of heat load and relative parameters were confirmed, and the temperature field was simulated. The calculation results show that high thermal gradient appears in the axis direction of the sample, but low thermal gradient appears in the radial direction. The temperature on friction surface raises to the maximum of 662 ℃in the big radius at 12.7 s. The simulation results are consistent with the experiment data, which verifies the validity of the simulated results.
Key words: carbon/carbon composite; temperature field; finite element; brake
在飞机刹车过程中将有大量的动能转化为刹车动静盘之间接触表面的热能,热量由摩擦表面逐渐向基体内部传递从而形成温度梯度,温度梯度的存在导致热应力产生,对刹车材料起主要破坏作用;此外,摩擦热还使炭/炭复合材料有较严重的氧化磨损。刹车盘摩擦表面温度的产生和扩散是一个复杂的过程,它将直接影响刹车性能。近年来,很多学者对这方面进行了研究,但是由于测量摩擦表面实际温度存在困难,因此对刹车装置的瞬态温度场的研究还不够完善。早期对摩擦温度场的研究多将刹车副简化成二维模 型[1],这种模型只能对整个温度场有一个大致的描述,不能反映实际的温度场分布状态。最近关于刹车盘温度场的研究主要集中在汽车、火车刹车过程,利用有限元方法计算了刹车盘温度场的变化,介绍了热载荷的求解以及边界条件的确立,得出瞬态温度场与刹车材料的热物性能密切相关[2-3],制动材料[4]和制动条件[5]对制动过程温度场及应力场的影响也尤为重要;此外,摩擦表面温度分布及最高温度对刹车材料的破坏起主要作用,与加载条件密切相关[6]。飞机刹车过程与汽车、火车制动过程在结构、材料以及最高温度上都存在很大差异。目前,飞机刹车片用的摩擦材料主要是粉末冶金材料和炭/炭复合材料,有关飞机刹车温度场的研究集中在粉末冶金材料[7-8]。由于炭/炭复合材料的热稳定好、热扩散率高、比强度高、摩擦性能好以及磨损率低,目前已逐步取代金属刹车副,成为先进的刹车材料。因此,有必要对炭/炭复合材料刹车盘温度场作深入研究。但是,在实际刹车过程中,摩擦表面瞬态温度的测量很难实现,以往的温度场计算也很难用实验证实。因此,本文作者在摩擦实验机上模拟飞机刹车过程,测量摩擦试环表面及内部温 度,利用有限元软件仿真刹车过程温度场变化;对比仿真与实验结果,观察仿真结果中试环的温度变化过程,从而有利于更进一步分析热应力以及设计飞机刹车材料。
1 温度场仿真
本实验采用的炭/炭复合材料经准三维针刺预制件增密得到,摩擦试环以给定的实验条件在MM-1000摩擦实验机上进行摩擦实验。如图1所示,试环呈轴对称结构,通过摩擦背面的4个凹槽经机座连接到摩擦实验机。图2所示给出了实验装置的截面,包括摩擦试环、隔热层、机座和测温点分布。仿真计算中以摩擦试环为研究对象。
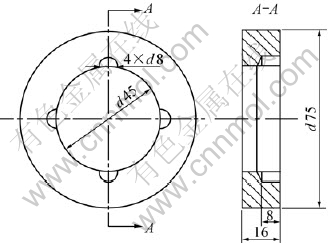
图 1 摩擦试环
Fig.1 Friction sample (unit: mm)
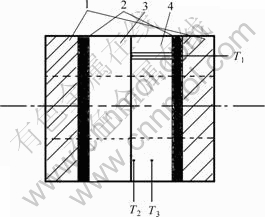
图 2 刹车装置截面图
Fig.2 Schematic diagram of brake set up: 1—Pedestal; 2—Heat insulation layer; 3—Rotor; 4—Stator; T1, T2, T3— Temperatures of friction surface, 1 mm to friction surface and half of thickness respectively
根据传热学理论,柱坐标系中轴对称结构的不稳定热传导方程为[9]
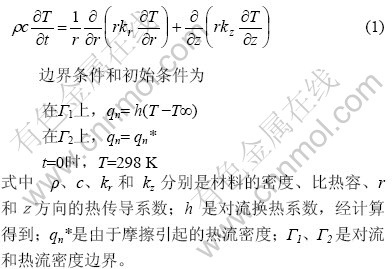
瞬态传热过程是指一个系统的加热或冷却过程,在这个过程中系统的温度、热流率、热边界条件以及系统内能随时间都有明显变化。根据能量守恒原理,对非稳态温度场进行离散化,并进行单元分析及总体合成得瞬态热平衡,以矩阵形式表达为:
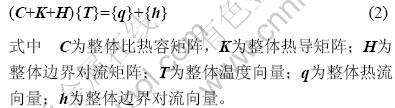
1.1 建模
采用ANSYS有限元分析软件进行刹车片三维立体建模,观察试环各个方向上的温度分布变化,作出测温点处温度变化曲线并与实验结果对比。ANSYS温度场分析过程为:实体建模—网格划分—加载与计算—后处理显示结果。
以整个摩擦试环为研究对象。由图1可知,试环呈轴对称结构,故以半个摩擦试环建模,划分网格如图3所示。
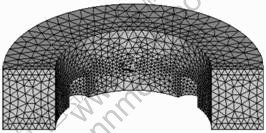
图 3 三维立体模型
Fig.3 Three-dimensional model
1.2 定解条件
1.2.1 对流换热系数
能量传递存在3种基本方式:导热、对流和热辐射。在模拟刹车实验中,摩擦试环与空气的对流换热为其最主要的散热途径,热辐射传递的热量可以忽略不计。对流换热系数与材料无关,而与周围流体的温度、流体的物性参数、壁面的温度和壁面外形等参数相关。
表面换热系数取决于流体流动状态、流体物理性质、壁面温度以及壁面的几何形状,如式(3)所示:
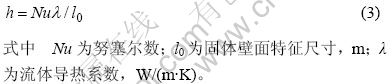
1) 试环外表面
a. 刹车过程中试环外表面与空气属于受迫流动换热状态
对于圆柱扰流问题,努塞尔数根据下述经验公式计算[10]:

b. 刹车停止后试环外表面与空气呈自然对流换热状态
对于圆柱扰流问题,努塞尔数根据下述经验公式计算[10]:
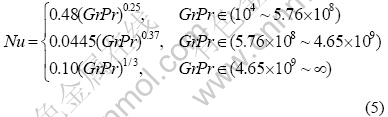
2) 试环内表面
整个过程中试环内表面属于有限空间的自然对流传热[10]:

1.2.2 热流密度的计算
为了便于模拟计算,假设摩擦过程中材料的密度保持恒定,且在整个过程压力分布均匀。摩擦面热流密度随时间、半径的变化如式(7)所示:

1.3 热物性能
图4所示为实验用的炭/炭复合材料的比热容与温度的关系,根据GJB330A—2000固体材料比热容测试方法测得。由图可见,比热容随温度的升高而升高。图5和图6所示分别为炭/炭复合材料垂直于纤维方向和平行于纤维方向的材料导热系数与温度的关系。导热系数跟比热容和热扩散率相关,热扩散率采用激光闪光法在JR-3热物性测试仪测得。从图5和6可见,两个方向的导热系数均随温度升高而下降,但是平行于纤维方向的导热系数明显高于垂直于纤维方向的导热系数,这主要是因为碳纤维的导热性能比基体碳的好。
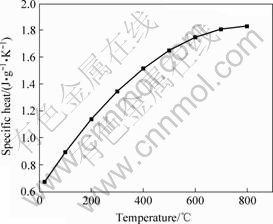
图4 炭/炭复合材料比热容与温度的关系
Fig.4 Relationship between specific heat and temperature for carbon/carbon composite
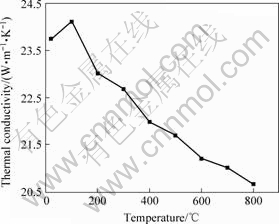
图5 炭/炭复合材料垂直于纤维方向导热系数与温度的关系
Fig.5 Relationship between thermal conductivity vertical to fibre orientation and temperature for carbon/carbon composite
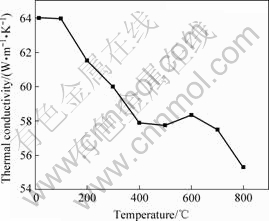
图6 炭/炭复合材料平行于纤维方向导热系数与温度的关系
Fig.6 Relationship between thermal conductivity parallel to fibre orientation and temperature for carbon/carbon composite
2 摩擦实验
摩擦试环装置如图2所示,实验中采用三路温度信号同时测温,分别测得静环中径面上摩擦表面温度T1、距表面1 mm处温度T2、试环厚度一半处温度T3随时间的变化。
众所周知,测量摩擦表面温度一直非常困难,我们采用热电偶在摩擦表面置热交合点的方法[11]测量摩擦表面温度,将两根热电偶丝一端焊合成“焊点”埋入摩擦表面,丝的其他部分用高温绝缘材料绝缘,热电偶丝的冷端通过补偿导线与计算机数据采集系统相连。
表1 试样尺寸及实验条件
Table 1 Size of sample and condition of experiment
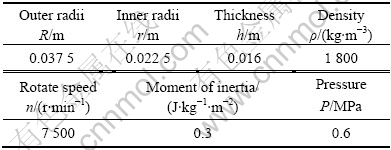
将上述尺寸的炭/炭复合材料摩擦试环以给定的实验条件在MM-1000摩擦实验机上进行摩擦实验,实验动静环采用相同的材料,根据摩擦热冲击法,将动环通过键槽与驱动主轴相连并随驱动主轴和惯性飞轮一同加速到规定的制动速度下,施加一定的压力使静环和旋转的动环发生摩擦而实现制动刹车,通过测量制动力矩可以计算制动摩擦因数[12]。多次重复实验,直到摩擦因数稳定为止。
3 结果与讨论
利用ANSYS软件仿真计算后,得到了摩擦试环的瞬态温度场。图7所示为7.635 s时试环的温度场分布图,由图可以看出t=7.635 s时试环温度在300~662 ℃之间成梯度分布。轴向温度梯度分布尤为明显,热量从摩擦表面扩散到摩擦背面并逐渐变小。径向温度变化不那么明显,但从试环外径到内径存在小的温度梯度,并且最高温度出现在靠近外径处,这主要是热流密度和对流换热引起的。从式(7)可以看出,热流密度是与半径成正比的,半径越大热载荷越大,即产生的热量越多,导致摩擦材料温度越高;同时,试环内外表面与空气存在对流换热,起到降温作用。因此,最高温度会出现在外表面附近。此外,由图5和6可知,试样平行于纤维方向上的导热系数明显大于垂直纤维方向的导热系数,因此,平行方向传热快,温度梯度小;垂直方向传热慢,温度梯度大。
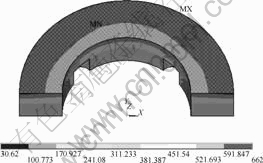
图7 t=7.635 s时试环温度场分布
Fig.7 Temperature field of sample at 7.635 s
图8和9所示是试环中径面上摩擦表面、距表面1 mm处、试环厚度一半处温度随时间变化的仿真与实验结果。对比二图可以看出,两者的温度变化趋势一致,最高温度以及达到最高温度的时间均吻合,摩擦表面在t=12.7 s时达到最高温度Tmax=935 K,其他两路温度分别在t=15 s和t=17.5 s时达到最高值,这主要是热量从摩擦表面传递到摩擦背面延时导致的。同时,可以看出曲线变化的一些差异。首先,刹车开始后实测温度急剧上升,斜率大于仿真计算结果,原因是实际摩擦制动过程中,摩擦表面微观上呈凹凸状,实际接触面积占表观接触面积的很小部分,表面接触点附近形成半球形的等温面[13],再由热传导作用传递到基体内部。因此,摩擦表面存在“热点”[14-16]现象,热点与基体间存在高温度梯度。而仿真模拟中摩擦表面为平面,相当于实际摩擦中的表观接触面,经表面接触点热传递后升温,因此,其温度比实际接触面上升得慢,呈稳步上升状态。其次,实测的摩擦表面温度下降得比仿真计算结果快,这是因为实验中用气压实现刹车,刹车一旦结束气压停止,动、静环脱离,导致它们之间存在空隙,摩擦表面参与空气对流换热。

图8 测温点温度仿真结果
Fig.8 Simulated temperature results of test points
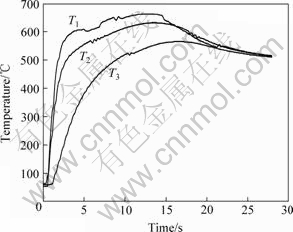
图9 测温点温度实验结果
Fig.9 Experimental temperature results of test points
4 结论
1) 利用有限元热分析软件ANSYS建立了某炭/炭复合材料制动过程三维有限元模型,阐述了相关热载荷计算方法和关键参数的确定。在计算过程中合理地考虑了各相关参数的变化,使得计算结果比较准确。
2) 通过仿真计算以及实验得到了任一时刻的温度场理论和实际分布状况,了解了热量在摩擦试环中的传递过程以及试环各处温度随时间的变化:摩擦热从试环表面传递到摩擦背面,在试环轴向存在明显温度梯度,而在径向温度梯度微小。摩擦表面在t=12.7 s时达到最高温度662 ℃,且最高温度出现在靠近试环外径处。
3) 仿真计算结果与实验结果基本相符,证明了此三维温度场模拟的有效性。但同时两者之间存在微小差异,说明实验方法和仿真计算还需改进。
REFERENCES
[1] ABDI R E, SMAROUT H. An isothermal modeling applying to brake discs[J]. International Journal of Non-linear Mechanics, 1999, 34: 797-805.
[2] 丁 群, 谢基龙. 基于三维模型的制动盘温度场和应力场计算[J]. 铁道学报, 2002, 24(6): 34-38.
DING Qun, XIE Ji-long. The temperature field and stress field calculation of brake disc based on 3-dimension model[J]. Journal of the China Railway Society, 2002, 24(6): 34-38.
[3] 鲁国富, 郭世永. 盘式制动器瞬态温度场的数值模拟[J]. 机械研究与应用, 2006, 19(1): 31-35.
LU Guo-fu, GUO Shi-yong. Numerical simulation of transient temperature field of disc-pad brake[J]. Mechanical Research and Application, 2006, 19(1): 31-35.
[4] 陈德玲, 张建武, 周 平. 高速轮轨列车制动盘热应力有限元研究[J]. 铁道学报, 2006, 28(2): 39-43.
CHEN De-ling, ZHANG Jian-wu, ZHOU Ping. FEM thermal stress analysis of high speed locomotive braking discs[J]. Journal of the China Railway Society, 2006, 28(2): 39-43.
[5] 赵海燕, 张海泉, 汤晓华, 林 健, 蔡志鹏. 快速列车盘型制动热过程有限元分析[J]. 清华大学学报: 自然科学版, 2005, 45(5): 589-592.
ZHAO Hai-yan, ZHANG Hai-quan, TANG Xiao-hua, LIN Jiang, CAI Zhi-peng. Thermal FEM analysis of passenger railway car brake discs[J]. J Tsinghua Univ: Sci & Tech, 2005, 45(5): 589-592.
[6] GAO C H, LIN X Z. Transient temperature field analysis of a brake in a non-axisymmetric three-dimensional model[J]. Journal of Material Processing Technology, 2002, 129: 513-517.
[7] 李 涛, 吴瑞祥. 飞机刹车装置的三维瞬态温度场的分析[J]. 机械工程师, 2006(6): 104-107.
LI Tao, WU Rui-xiang. 3-D transient temperature field analysis for aircraft brake system[J]. Mechanical Engineer, 2006(6): 104-107.
[8] 姚萍屏, 汪 琳, 熊 翔, 黄伯云. 粉末冶金航空刹车副温度场的研究[J]. 粉末冶金材料科学与工程, 2005, 10(4): 241-246.
YAO Ping-ping, WANG Ling, XIONG Xiang, HUANG Bo-yun. Research on temperature field of powder metallurgy aviation brake assemblage[J]. Materials Science and Engineering of Powder Metallurgy, 2005, 10(4): 241-246.
[9] CHOI J H, LEE I. Finite element analysis of transient thermoelastic behaviors in disk brakes[J]. Wear, 2004, 257: 47-58.
[10] 王补宣. 工程传热传质学[M]. 北京: 科学出版社, 1998: 139-226.
WANG BU-xuan. Engineering heat and mass transfer[M]. Beijing: Science Press, 1998: 139-226.
[11] QI H S, DAY A J. Investigation of disc/pad interface temperatures in friction braking[J]. Wear, 2007, 262: 505-513.
[12] 熊 翔, 黄伯云, 徐惠娟, 吉冬英, 彭剑昕. 不同制动速度下炭布叠层炭/炭复合材料的摩擦磨损行为及机理[J]. 中国有色金属学报, 2002, 12(2): 255-259.
XIONG Xiang, HUANG Bai-yun, XU Hui-juan, JI Dong-ying, PENG Jian-xin. Frictional and wear behaviors of C/C composites from carbon fiber cloth at different braking speeds[J]. The Chinese Journal of Nonferrous Metals, 2002, 12(2): 255-259.
[13] 温诗铸, 黄 平. 摩擦学原理[M]. 北京: 清华大学出版社, 2002: 312-313.
WEN Shi-zhu, HUANG Ping. Tribology principle[M]. Beijing: Tsinghua University Press, 2002: 312-313.
[14] DU S, ZAGRODZKI P, BARBER J R, HULBERT G M. Finite element analysis of frictionally excited thermoelastic instability[J]. Therm Stresses, 1997, 121: 185-201.
[15] PANIER S, DUFR?NOY P, WEICHERT D. An experimental investigation of hot spots in railway disc brakes[J]. Wear, 2004, 256: 764-773.
[16] ZAGRODZKI P. Numerical analysis of temperature fields and thermal stresses in the friction discs of a multidisc wet clutch[J]. Wear, 1985, 101: 255-271.
基金项目:国家重点基础研究计划资助项目(2006CB600906)
收稿日期:2007-06-04;修订日期:2007-10-26
通讯作者:易茂中,男,博士,教授;电话:0731-8830894;E-mail: yimaozhong@126.com
(编辑 何学锋)