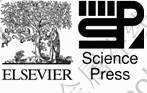

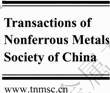
Trans. Nonferrous Met. Soc. China 22(2012) 124-128
Effect of sintering atmosphere on phase composition and mechanical properties of 5Ni/(10NiO-NiFe2O4)
CHEN Duan, ZOU Zhong, TIAN Zhong-liang, XIN Peng-fei, LIU Kai, LAI Yan-qing, LI Jie
School of Metallurgical Science and Engineering, Central South University, Changsha 410083, China
Received 23 September 2010; accepted 5 January 2011
Abstract: 5Ni/(10NiO-NiFe2O4) cermet materials were prepared by cold pressing sintering method in different atmospheres. The phase compositions were studied by XRD, microstructure was studied by SEM and mechanical properties were studied by three-point-bending strength and heat cycle. The results show that Ni/(NiO-NiFe2O4) cermet can be obtained by sintering in vacuum or atmospheres with oxygen content of 2×10-5, 2×10-4 and 2×10-3, respectively, but the phase composition of the ceramics varies greatly with oxygen content of the sintering atmosphere. The cermet tends to have a high content of NiO when sintered in vacuum. The content of NiFe2O4 and Ni in the cermet materials respectively increases and decreases with increasing oxygen in the sintering atmosphere. In the vacuum, cermet has an average grain size of 3.90 μm and bending strength of 138.59 MPa, which is able to withstand thermal shock tests 6.67 times in average.
Key words: nickel ferrite; cermet; mechanical property; sintering atmosphere
1 Introduction
Consumable carbon anodes have been used in aluminum smelting for more than 100 years. However, some problems such as mass superior carbon consumption and green house gas generation still exist. Inert anodes are not consumed during electrolysis. So, it is hopeful to solve the problems mentioned above. The application of inert anodes is significant to aluminum electrolysis energy saving and environmental protection [1, 2].
In recent years, cermet has become one of the most promising inert anode materials, because of its good electrical conductivity and resistance to high temperature corrosion in molten salts during aluminum electrolysis. NiFe2O4 is often studied as ceramic matrix for cermet inert anode because of its high melting point, excellent corrosion resistance and stable thermal and chemical properties. Aluminum Company of America (Alcoa) has conducted considerable study about cermet inert anode materials. However, the test results of 6 kA pilot cell show that both the mechanical properties and corrosion resistance of NiFe2O4 cermet could not meet requirements of thermal shock resistance and corrosion resistance [3].
As well known, good mechanical properties and corrosion resistance of ceramic materials are depended upon its phase composition and microstructure which are affected by the sintering atmosphere of the preparation process. In order to obtain NiFe2O4 cermet inert anode with desirable phase composition, ceramic inert anodes are prepared in different sintering atmospheres [4-6], and it is reported that ceramic phase of NiFe2O4 would be decomposed in vacuum. When the sintering is conducted in the inert atmosphere, not only the improved densification but also the expected composition of the material is obtained. TIAN et al [7] investigated the effects of sintering temperature, composition and dispersion of the metal phase among ceramic matrixes on the high temperature electrical resistivity of the NiFe2O4 -based cermet.
The high temperature mechanical properties and corrosion resistance of inert anode are critical for the successful application on aluminum reduction. Nevertheless, few works on mechanical properties of NiFe2O4 cermet inert anodes in sintering atmosphere are found. In this work, 5Ni/(10NiO-NiFe2O4) cermet was prepared and the phase composition, microstructure and mechanical properties were studied.
2 Experimental
2.1 Fabrication of anodes
A mixture of Fe2O3 and NiO with molar ratio of 1.35:1 was prepared. 10NiO-NiFe2O4 ceramic powder was fabricated by calcining the above mixture in a muffle furnace at 1200 °C for 6 h in air. The synthesized powder and Ni powder were ground in a medium containing dispersant and adhesive. Then, the mixed ceramic-metal powder was dried and statically pressed into cubic with size of 5 mm×5 mm×36 mm or cylinder specimen with size of d20 mm×10 mm under pressure of 2×108 Pa. Finally, the specimens were sintered at 1350 °C for 4 h in the vacuum (1.0×10-2 Pa) and atmospheres of Ar and air with oxygen content of 2×10-5, 2×10-4 and 2×10-3, respectively. To make it easy to discuss, the above atmospheres were expressed as A0, A1, A2 and A3, respectively).
2.2 Characterization techniques
The phase composition of ceramic materials (powder) was analyzed by Rigaku3014 X-ray diffraction system and the microstructure was analyzed by JSM-6360LV scanning electron microscope. The sample preparation includes cutting, inlaying and polishing. The three-point-bending strength of the sintered specimen was evaluated with a CSS-44100 electrical universal testing machine with span of 30 mm at cross-head speed of 0.5 mm/min. Bending strength data were recorded by calculating the average value of 5 samples. Also, thermal shock resistance was tested with heat cycle. The sample was placed in the electric furnace at 960 °C for 30 min, and then taken out in air to room temperature. This operation was repeated until the sample burst. In addition, the phase composition and thermal shock resistance were measured three times to ensure the reliability of the results.
3 Results and discussion
3.1 Phase and microstructure
The XRD analysis results of 5Ni/(10NiO-NiFe2O4) cermet sintered in different atmospheres (A0, A1, A2 and A3) are shown in Fig. 1. It is found that all the samples obtained in the four different sintering atmospheres contain Ni, NiFe2O4 and NiO phases. The phase quantitative analysis results (Table 1) reveal that all the phase contents vary with the oxygen content in atmosphere. With the increase of oxygen content, NiFe2O4 in the cermet increases at the beginning and then decreases, while NiO appears a contrary trend, and Ni decreases gradually, which has the same experiment results as Refs. [9, 10]. It must be pointed out that NiFe2O4 content of 60.6% is the lowest, while Ni content of 8.5% is the highest in the atmosphere A0. While the sample is sintered in the atmosphere A2, NiFe2O4 content is 70.7% which is the highest of all, NiO content is 23.8% which is the lowest.
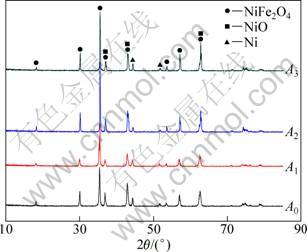
Fig. 1 X-ray diffraction patterns of 5Ni/(10NiO-NiFe2O4)
Table 1 Relative content of phases by XRD quantitative analysis in 5Ni/(10NiO-NiFe2O4) cermet
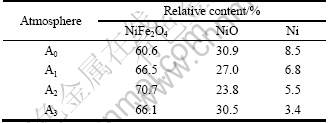
The reasons for the variation of different phase content in the ceramics can be expressed as
?
(1)
?NiO (2)
Under vacuum condition, reaction (1) moves to the right and reaction (2) moves to the left, therefore, the content of Ni in A0 is higher than that in other atmospheres, and the content of NiFe2O4 is the lowest. Moreover, it needs to point out that the stoichiometric compound NiFe2O4 and the nonstoichiometric compound NiFe2xO4-y-z cannot be distinguished in the XRD analysis. There are two forms of elemental Fe in NiFe2xO4-y-z, Fe2+ and Fe3+. When the oxygen content in the atmosphere increases, Fe2+ in NiFe2xO4-y-z is oxidized to Fe3+, then Fe3+ together with NiO transforms to NiFe2O4. As a result, NiFe2O4 content increases. The change of NiO content is caused by both reactions (1) and (2), when the samples are sintered under atmospheres A1 and A2, the reaction rate of metal Ni oxidated to NiO is slower than that of NiO reacted to NiFe2O4. Consequently, the variation of phase content of NiO is getting less. When the sintering process is conducted in A3, reaction (2) takes place mainly. Therefore, the content of NiO appears a rising trend, while the content of Ni phase presents a downward trend.
The microstructures of samples obtained in different atmospheres are illustrated in Fig. 2. Through EDAX, the dark-gray region, light-gray region and white region represent NiFe2O4, NiO and Ni, respectively. This shows that the change of porosity in 5Ni/(10NiO-NiFe2O4) materials is not obvious with the increase of oxygen content. Moreover, metal Ni in nickel ferrite-based cermet most appears spheroidal or long chain-shaped, and forms forked structure, which was also found by ZHANG [10]. It also reveals that Ni appears cross linking to some extent when the oxygen concentration is less than 2×10-4, and the grain size of metal Ni is bigger than that obtained in other atmospheres. While in A2 and A3, the distribution of Ni is relatively uniform in nickel ferrite-based cermet.
3.2 Bending strength
As shown in Table 2, the result indicates that the shrinkage of cermet material decreases from 11.95% to 10.75% with the increase of oxygen content from 0 to 2×10-4, and the grain size ranges from 3.9 to 3.28 μm. NiFe2O4 is a type of stoichiometric compound with anti-structure defect which makes the grains of NiFe2O4 vary in different oxygen contents. When the oxygen content in atmosphere is lower, the oxygen defect concentration of NiFe2O4 lattice increases conspicuously, which accelerates the atomic diffusion and makes the grains grow [11-13].
Table 2 Properties of 5Ni/(10NiO-NiFe2O4) cermet under different atmospheres
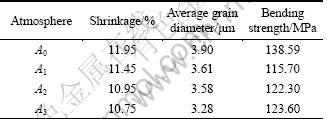
Generally speaking, there are many factors affect the bending strength, such as material grain size, relative density and phase content [14-16]. The relation of all the factors can be expressed in the mixing rule as [17]
(2)
(3)
where σf is the material bending strength, MPa; σm is the bending strength of matrix phase, MPa; σr is the bending strength of strengthening phase, MPa; Vm is the volume fraction of matrix phase, %; and Vr is the volume fraction of strengthening phase, %.
Although the shrinkage and average grain size of the ceramic materials obtained in different sintering atmospheres vary inconspicuously, the bending strength decreases obviously with the increase of O2 content in the atmosphere. It is the result of comprehensive influence of metallic phase (σm), strengthening phase (σr) and grain size, etc. From Table 2, it is observed that the highest bending strength of NiFe2O4-based cermet of 138.59 MPa can be obtained in A0 atmosphere. The main reason is that the density of the materials is the highest, and both the contents of strengthening phase and Ni are higher, which can enhance the bending strength to some extent. However, the bending strength of 5Ni/(10NiO-NiFe2O4) materials increases with the increase of oxygen content in atmosphere. This is because the strengthening phase (NiO) in 5Ni/(10NiO-NiFe2O4) cermet increases with the increase of oxygen content, as seen in Table 1.
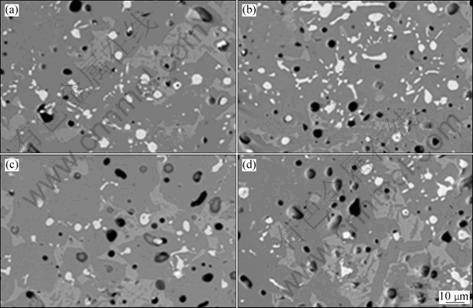
Fig. 2 SEM images of 5Ni/(10NiO-NiFe2O4) cermet in different sintering atmospheres: (a) A0; (b) A1; (c) A2; (d) A3
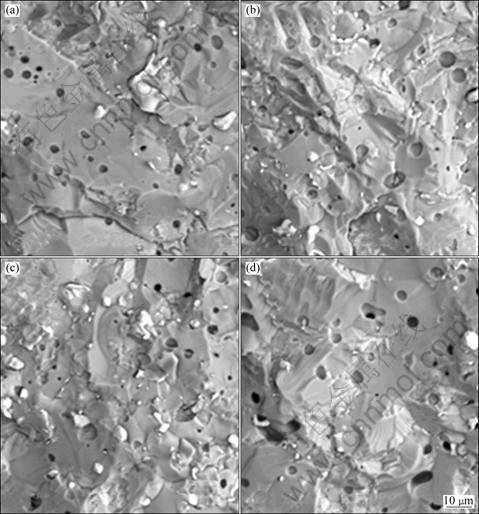
Fig. 3 Fracture surface images of 5Ni/(10NiO-NiFe2O4) cermet in different sintering atmospheres: (a) A0; (b) A1; (c) A2; (d) A3
As shown in Fig. 3, the fracture of material appears crystalloid, so the fracture is brittle rupture. The fracture shows ice-sugar shape as traditional intercrystalline fracture, and the grains cannot be found obviously. Therefore, the main fracture mechanism of the materials obtained in four atmospheres is transgranular fracture. This illustrates that the bond strength of grain boundary is good.
3.3 Thermal shock resistance
The results of the thermal shock resistant test of the materials are listed in Table 3. The results reveal that 5Ni/(10NiO-NiFe2O4) cermet has better thermal shock resistance in A0 and A1 than that in A2 and A3. The reason for the above phenomenon can be attributed to the high content of metal phase, which contributes to restrain crack propagation [18, 19]. Moreover, the density has certain influence on the materials thermal expansion, the higher the density of materials is, the smaller interstice of grain is.
Table 3 Thermal shock resistance of 5Ni/(10NiO-NiFe2O4)
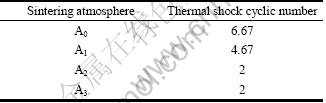
4 Conclusions
1) 5Ni/(10NiO-NiFe2O4) cermet inert anode can be obtained in vacuum or atmospheres with oxygen content of 2×10-5, 2×10-4 and 2×10-3, respectively. But the sintering atmosphere has a great influence on the phase content. With the increase of oxygen content in sintering atmosphere, NiFe2O4 content increases at the beginning and then decreases, while NiO content appears the contrary trend and Ni phase content decreases gradually.
2) With the increase of oxygen content in sintering atmosphere, both the shrinkage and the average grain size of 5Ni/(10NiO-NiFe2O4) decrease gradually. In vacuum atmosphere, 5Ni/(10NiO-NiFe2O4) cermet has an average grain size of 3.90 μm and bending strength of 138.59 MPa, which are able to withstand thermal shock tests averaged 6.67 times.
References
[1] PAWLEK R P. Inert anodes: An update [C]//Wolfgang Schneider. Light Metals, Warreudale PA, USA: TMS, 2002: 449-456.
[2] LIU Ye-xiang. Advance on the research and development of inert anode and wettable cathode in the aluminum electrolysis [J]. Light Metals, 2001(5): 26-29. (in Chinese)
[3] XIAO H, HOVLAND R, ROLSETH S, THONSTAD J. Studies on the corrosion and the behavior of inert anodes in aluminum electrolysis [J]. Metallurgical and Materials Transactions B, 1996, 27 (2): 185-193.
[4] WEYAND J D. Manufacturing process used for the production of inert anodes[J]. Light Metals, 1986: 321-339.
[5] ZHANG Lei, ZHOU Ke-chao, LI Zhi-you, ZHANG Xiao-yong. Effect of atmosphere on densification in sintering nickel ferrite ceramic for aluminum electrolysis [J]. Powder Metallurgical Materials Science and Engineering, 2004(9): 65-71. (in Chinese)
[6] ZHANG Gang, LI Jie, LAI Yan-qing, SUN Xiao-gang. Effect of sintering atmosphere on the relative density and conductive properties of Ni-Fe spinel ceramics [J]. Functional Materials, 2005, 36(11): 1709-1711.
[7] TIAN Zhong-liang, LAI Yan-qing, LI Jie, ZHANG Gang, LIU Ye-xiang. Electrical resistivity of NiFe2O4ceramic and NiFe2O4-based cermet [J]. The Chinese Journal of Nonferrous Metals, 2004, 14(3): 421-425. (in Chinese)
[8] LI Bo, ZHANG Shu-ren, WANG Shang. Effect of sintering atmosphere on the dialectric properties of Er-Mg and Er-Mn doped BaTiO3 [J]. Journal of Inorganic Materials, 2007, 5(22): 821-827. (in Chinese)
[9] MAO Yu, DING Shi-hua, YAO Xi, ZHANG Ling-ying. Effect of doping and sintering atmosphere on the properties of BiNbO4 materials [J]. Piezoelectric and Acoustooptic, 2006, 1(28): 79-81. (in Chinese)
[10] ZHANG Gang. Study on density and obdurability of nickel ferrite cermet in aluminium electrolysis [D]. Changsha: Central South University, 2007: 28-33. (in Chinese)
[11] ABENOJAR J, VELASCO F, BAUTISTA A,CAMPOS M, BAS J A, TORRALBA J M. Atmosphere influence in sintering process of stainless steels matrix composites reinforced with hard particles [J]. Composites Science and Technology, 2003(63): 69-79.
[12] ZHANG Jian, HUANG Bai-yun, LI Yi-min, ZHONG Wei, QU Xuan-hui. Effect of sintering atmosphere on Fe/2Ni alloy injection moulding [J]. Journal of Central South University of Technology: Natural Science, 2000(31): 152-155. (in Chinese)
[13] ZHANG Lei. Study on material fabrication and property of NiFe2O4/M cermet inert anode in aluminium electrolysis [D]. Changsha: Central South University, 2006: 27-38. (in Chinese)
[14] ZHOU Shi-quan, CHENG Xiao-min, SHEN Yu-li, SHEN Qing. Microstructure and properties of Al2O3/Al ceramic matrix composites [J]. Special Metal Casting and Non-Ferrous Alloys, 1998(4): 41-43. (in Chinese)
[15] LI Wen-hu. Study on structure and properties of Mo2FeB2 cermet cladding material [J]. Ceramics, 2008(8): 18-20. (in Chinese)
[16] RODRIGUEZ C M, MUNO Z A, DOMINQUEZ R A. Effect of atmosphere and sintering time on the microstructure and mechanical properties at high temperatures α-SiC sintered with liquid phase Y2O3-Al2O3 [J]. Journal of the European Ceramic Society, 2006, 26(12): 2397-2405.
[17] FLINN B D, LO C S, ZOK F W, EVAN A G. Fracture resistance characteristics of a metal-toughened ceramic [J]. Journal of the American Ceramic Society, 1993, 76: 369-375.
[18] GUAN Zhen-duo. Physical properties of inorganic materials [M]. Beijing: Publishing House of Tsinghua University, 1992: 159. (in Chinese)
[19] ZHOU Yu. Science of Ceramic materials [M]. Harbin: Publishing House of Harbin Institute of Technology, 1995: 471. (in Chinese)
烧结气氛对5Ni/(10NiO-NiFe2O4)金属陶瓷物相组成及力学性能的影响
陈 端,邹 忠,田忠良,辛鹏飞,刘 恺,赖延清,李 劼
中南大学 冶金科学与工程学院,长沙 410083
摘 要:在不同烧结气氛下采用冷压烧结法制备5Ni/(10NiO-NiFe2O4)金属陶瓷,通过XRD研究其物相组成,SEM研究其显微结构,并用三点抗弯测试和抗热震实验检测其力学性能。结果表明:在真空气氛及氧含量分别为2×10-5、2×10-4和2×10-3的气氛中均可获得Ni/(10NiO-NiFe2O4)金属陶瓷,但气氛中氧含量对物相含量影响较大。在真空气氛中NiO含量相对较高。材料中NiFe2O4和Ni的含量分别随着气氛中氧含量的上升而增加和减小;在真空烧结气氛中,可获得晶粒尺寸为3.90 μm的5Ni/(10NiO-NiFe2O4)金属陶瓷,其抗弯强度可达138.59 MPa,且在960 °C实验条件下平均抗热震循环次数可达6.67次,具有相对较好的力学性能。
关键词:NiFe2O4;金属陶瓷;力学性能;烧结气氛
(Edited by FANG Jing-hua)
Foundation item: Project (2001AA335013) supported by the National High-tech Research and Development Program of China
Corresponding author: TIAN Zhong-liang; Tel: +86-731-88830649; E-mail: tianzhongliang@126.com
DOI: 10.1016/S1003-6326(11)61150-3