
Sinter-hardening properties of partially-diffuse alloyed Fe-Cu-Ni-Mo-C material prepared by die wall lubricated warm compaction
XIAO Zhi-yu(肖志瑜), SHEN Yuan-xun(沈元勋), NGAI Tungwai Leo(倪东惠),
WU Yuan-biao(吴苑标), LI Yuan-yuan(李元元)
School of Mechanical Engineering, South China University of Technology, Guangzhou 510640, China
Received 15 July 2007; accepted 10 September 2007
Abstract: The sinter-hardening properties of a partially-diffuse alloyed Fe-2Cu-2Ni-1Mo-1C material were investigated. Samples were formed by die wall lubricated warm compaction method, then, sintered in hydrogen atmosphere at 1 150 ℃ for 1 h and cooled at 4.6, 2.9 and 1.5 ℃/s, respectively, from 900 ℃ down to 600 ℃. Effects of cooling rate on mechanical properties and microstructure of the material were discussed. The results show that when the cooling rate increases, the tensile strength of the material increases, while, the elongation shows opposite result. The sintered material has a tensile strength of 872 MPa and an apparent hardness of HB 257 at a cooling rate of 4.6 ℃/s. Slight shrinkage is observed. Heterogeneous microstructures containing martensite, bainite, pearlite and nickel-rich retained austenite are observed in the material. Higher martensite content can be obtained at higher cooling rate, while, at lower cooling rate, pearlite and retained austenite dominated the microstructure.
Key words: powder metallurgy; die wall lubricated warm compaction; sinter-hardening; microstructure
1 Introduction
With the rapid development of the automotive industry, it presents a great increase in the application of high performance powder metallurgy (PM) parts and exploits a great market of iron-based PM materials. However, some drawbacks of these materials, such as low strength and low hardness, need to be overcame. Some advanced manufacture methods could be utilized to resolve these problems. One is using new forming technique to increase density of the material[1-2]. The second is admixing alloying elements[3-4]. The third is using suitable treatments on the powders and on the sintered materials[5]. Among those methods, sinter-hardening[6-7] and die wall lubricated warm compaction[8-9] attract much attention. Sinter- hardening combines sintering and heat-treatment in a single process by using a specially designed furnace to control the post sintering cooling rate[10]. Sinter-hardening eliminates secondary operation such as heat treatment, thus reduces cost and avoids deformation during quenching. It is suitable for producing those big and complex shape PM parts. Specially formulated powders are preferable to generate good hardenability[11]. Admixing alloying elements such as copper, nickel, manganese and molybdenum can increase hardenability. In addition, hardenability can be increased by increasing density. High density reduces porosity and result in the increase of thermal conductivity and thus enhances the hardenability[5].
Many sinter-hardenable powder metallurgy materials[12-14,] were developed over the past few decades and commonly used Fe-Cu-Ni-Mo-C system exhibited good dynamic and static properties[14-16]. The primary object of the present study was to evaluate the sinter-hardening properties of partially-diffuse alloyed Fe-2Cu-2Ni-1Mo-1C powder. Die wall lubricated warm compaction followed by sinter-hardening process was used to obtain high density and high performance PM materials.
2 Experimental
Chemical composition (mass fraction, %) of the tested material was 2% Cu, 2% Ni, 1% Mo, 1%
C(graphite) and Fe as balance. Water atomized iron powder (≤147 μm), carbonyl nickel (3-5 μm) and reduced molybdenum powder (3-5 μm), electrolytic copper powder (≤74 μm) and graphite powder (≤74 μm) were used as raw materials in this study. Table 1 lists the chemical composition and properties of the water atomized iron powder. 0.1 % HW lubricant was used.
Iron powders and other alloying elemental powders were pre-mixed and annealed at a presetted temperature in hydrogen atmosphere. Then the partially alloyed powders were milled and mixed with graphite and lubricants.
Table 1 Chemical composition and properties of water atomized iron powder

Tensile bars were pressed according to GB/T 7963—1987. Alcohol solution of HW was used as die wall lubricant. The mixed powder was heated to (120±2) ℃ in a steel mold and pressed at a compacting pressure of 700 MPa. Sintering was carried out in a modified sintering furnace equipped with a rapid cooling system. Samples were sintered at 1 150 ℃ for 1 h in hydrogen atmosphere. Samples were placed in the furnace chamber and tied together with a thermocouple, which was used to measure the actual cooling rate. After sintering the samples were pulled to the cooling zone quickly. When the temperature fell to 900 ℃, nitrogen gas was blown directly onto the samples. Time needed to reach 600 ℃ was recorded. Cooling rates of 4.6, 2.9 and 1.5 ℃/s were obtained.
Green density and sintered density were measured by water displacement method. Tensile properties were measured by a CMT5105 universal testing machine. Apparent hardness was measured on both the top and bottom surfaces of the tensile bars. Samples were etched with 3% nital solution. Microstructure was characterized with a Lecia optical microscope and a Scanning Electron Microscope (SEM, PHILIPS×L30FEG) coupled with an Energy Dispersive Spectroscopy analyzer (EDS). Dimensional change percentage (ΔLDG) is defined as: ΔLDG = [(LS–LG)/LG]×100%, where LG and LS are the length of the green and sintered compacts, respectively.
3 Results and discussion
3.1 Mechanical properties
Figs.1 and 2 show the effects of cooling rate on tensile strength and apparent hardness of the sintered material. It can be seen that tensile strength increases with increasing cooling rate. Tensile strength increases from 771 to 794 MPa when the cooling rate increases from 1.5 to 2.9 ℃/s. The tensile strength achieves 872 MPa when the cooling rate reaches 4.6 ℃/s.
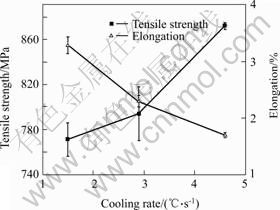
Fig.1 Effects of cooling rate on tensile strength and elongation
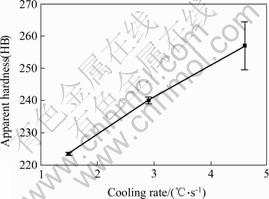
Fig.2 Effect of cooling rate on apparent hardness
The reported data apparent hardness was the average of three indentations on the top and another three on the bottom surfaces of the tensile bars. As shown in Fig.2, when the cooling rate increases, the apparent hardness increases. The apparent hardness values of HB 257, HB 241 and HB 223 were obtained at cooling rates of 4.6, 2.9 and 1.5 ℃/s, respectively. Elongation decreases while the cooling rate increases. These results can be explained by the amount of martensite formed at different cooling rate.
3.2 Density and dimensional change of sintered material
Table 2 lists the data of green density, sintered density and dimensional change of the sintered material. It can be seen that the sintered densities are less than the green densities. The maximum decrease is 0.07 g/cm3 and the minimum is 0.02 g/cm3. Die wall lubricated warm compaction could increase green density of the compacts effectively and reduce the admixed lubricant content[17]. Less admixed lubricant produces fewer ashes inside the compacts and results in higher sintered density. Dimensional change results show that there is a slight shrinkage after sinter-hardening for all three cooling rates.
Table 2 Green density, sintered density and dimensional change of materials prepared with different cooling rates

3.3 Microstructure
Fig.3 shows the microstructures of the material prepared at three cooling rates. In Fig.3, M denotes martensite; B+P denote bainite and fine lamellar pearlite; P denotes coarse lamellar pearlite; RA denotes retained austenite). Microstructure consists of martensite, bainite
and pearlite, and retained austenite. At cooling rate of 4.6℃/s, the microstructure is mainly martensite with some fine lamellar pearlite and few nickel-rich retained austenite as balance. Fig.3(d) shows a martensite plus the nickel-rich austenite region.
At cooling rate of 2.9 ℃/s, the martensite content decreases while pearlite, bainite and nickel-rich retained austenite content increase. It can also be seen that fine lamellar pearlite zones are surrounded by coarse lamellar pearlite zones. Fig.3(c) shows that microstructure is predominately pearlite and retained austenite at cooling rate of 1.5 ℃/s. Few free martensite islands and transition region of martensite and retained austenite can be observed. Comparing the microstructures, it is clear that the amount of martensite formed increases with the increase of cooling rate. Higher martensite content improves the tensile strength and hardness while decrease the elongation of the sintered material.
Fig.4 shows a typical SEM micrograph of the material cooled at 4.6 ℃/s. EDS was used to determine the distribution of alloying elements in randomly selected zone. EDS result shows that nickel concentration in the retained austenite region is about 10%. EDS mapping also reveals that the nickel-rich area is rich in copper. At high cooling rate, martensitic transformation takes place and few pearlite and retained austenite are formed.
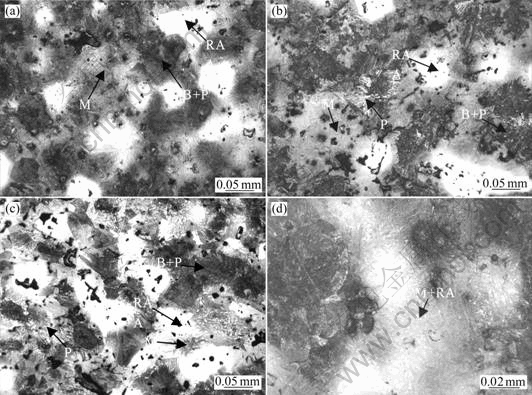
Fig.3 Optical microstructures of material for different cooling rates: (a), (d) 4.6 ℃/s; (b) 2.9 ℃/s; (c) 1.5 ℃/s
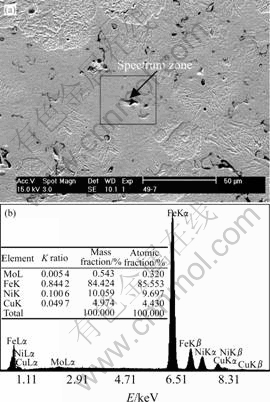
Fig.4 SEM image(a) of material prepared with cooling rate of 4.6 ℃/s and EDS(b) of spectrum zone
4 Conclusions
1) Partially-diffuse alloyed Fe-2Cu-2Ni-1Mo-1C powder shows a satisfactory response to sinter-hardening process. The sintered material exhibits high mechanical property and good dimensional consistence. Tensile strength and apparent hardness improve as the cooling rate increases. Material with tensile strength of 872 MPa, hardness of 257 HB and elongation of 1.7% is obtained.
2) At high cooling rate, microstructure consists of martensite, pearlite, bainite and nickel-rich retained austenite. Martensite content increases as the cooling rate increases. At lower cooling rate, the martensite content decreases and the microstructure is mainly composed of pearlite and retained austenite.
References
[1] RICHARD F. HVC punches PM to new mass production limits[J]. Metal Powder Report, 2002, 57(9): 26-30.
[2] LEMIEUX P, THOMAS Y, MONGEON P E, PELLETIER S, ST-LAURENT S, GUO R. Combining electrostatic die wall lubrication and warm compaction to enhance green and sintered properties of P/M components[J]. Powder Metallurgy Technology, 2006, 24(3): 227-232. (in Chinese)
[3] ZHANG Lin, LI Zhi-you, ZHOU Ke-chao, LIU Fang. Influence of elements powder pre-alloying technology on microstructure and property of sintered alloy-steel[J]. Materials Science and Engineering of Powder Metallurgy, 2005, 10(4): 225-230. (in Chinese)
[4] LIU Shi-min, HUANG Bo-yun, ZENG De-lin, CUI Jian-min. Effect of alloying methods on properties of ferrous powders[J]. Powder Metallurgy Industry, 2002, 12(6): 26-29. (in Chinese)
[5] HAN Feng-lin. Heat treatment of ferrous P/M parts[J]. Powder Metallurgy Industry, 2006, 16(6): 27-30. (in Chinese)
[6] ENGSTROM U. Evaluation of sinter hardening of different materials[C]// HOWARD F, DONALD T W. Advances in Powder Metallurgy & Particulate Materials. Princeton: Metal Powder Industries Federation, 2000: 147-157.
[7] GUO R, POIRIER J, CHAGON F, DANAHER J A, ILIA E, KRISE S. Transfer case sprocket production through the sinter hardening process[J]. Powder Metallurgy, 2003, 21(6): 327-333.
[8] BALL W G, HIBNER P F, HINGER F W. Replacing internal with external lubricants: Phase III Tribostatic application of lubricants onto die walls[C]// Advances in Powder Metallurgy & Particulate Materials. Princeton: Metal Powder Industries Federation, 1996: 3-14.
[9] LI Yuan-yuan, NGAI Tungwai Leo, ZHANG Da-tong, LONG Yan, XIA Wei. Effect of die wall lubrication on warm compaction powder metallurgy[J]. Journal of Materials Processing Technology, 2002, 129(1/3): 354-358.
[10] JAMES B. What is sinter-hardening[J]. Metal Powder Report, 1999, 54(1): 38-39.
[11] SKENA C, PRUCHER T. Hardenability characteristics of P/M alloy steels[J]. The International Journal of Powder Metallurgy, 1997, 33: 25-27.
[12] CHAGON F, TRUDEL Y. Designing low alloy steel powders for sinter-hardening applications[C]// CADLE T M, NARASIMHAN K S. Advances in Powder Metallurgy and Particulate Materials. Princeton: Metal Powder Industries Federation, 1996: 211-220.
[13] GUO Rui-jin. Low alloy steel powders for sinter hardening[J]. Powder Metallurgy Industry, 2003, 13(4): 1-5. (in Chinese)
[14] HIRONORI S, MASAAKI S, MASAKI Y, YOSHIKAZU S. Sinter hardening properties of pre-alloyed powder, 46F3H[C]// HOWARD F, DONALD T W. Advances in Powder Metallurgy & Particulate Materials. Princeton: Metal Powder Industries Federation, 2000: 125-136.
[15] CHAWLA N, MURPHY T F, NARASIMHAN K S, KOOPMAN M, CHAWLA K K. Axial fatigue behavior of binder-treated versus diffusion alloyed powder metallurgy steels[J]. Materials Science and Engineering A, 2001, 308(1/2): 180-188.
[16] XIAO Zhi-yu, ZHANG Ju-hong, WU Yuan-biao, WEN Li-ping, LI Yuan-yuan. Influence of sintering parameters on tensile strength of warm compacted Fe-2Ni-2Cu-1Mo-1C material[J]. The Chinese Journal of Nonferrous Metals, 2006, 16(8): 1326-1330. (in Chinese)
[17] LI Yuan-yuan, LI Jin-hua, NGAI Tungwai Leo, XIA Wei, CHEN Wei-ping. Effect of the admixed lubricant content on die wall lubrication in warm compaction[J]. Powder Metallurgy Technology, 2004, 22(6): 341-344. (in Chinese)
(Edited by YANG You-ping)
Foundation item: Project(50574041) supported by the National Natural Science Foundation of China; Projects(06105411, cgzhzd0502, 2006Z1-D6081) supported by Guangdong Science and Technology Project; Project(NCET-05-0739) supported by NCET, China
Corresponding author: XIAO Zhi-yu; Tel: +86-20-87112948; E-mail: zhyxiao@scut.edu.cn