
Isothermal oxidation behavior of cast Ni-base superalloy K44
LI Yun(李 云)1, LIU Xue-gui(刘学贵)1, GUO Jian-ting(郭建亭)2,
YUAN Chao(袁 超)2, YANG Hong-cai(杨洪才)3
1. College of Applied Chemistry, Shenyang Institute of Chemical Technology, Shenyang 110142, China;
2. Institute of Metal Research, The Chinese Academy of Sciences, Shenyang 110016, China;
3. School of Materials and Metallurgy, Northeastern University, Shenyang 110004, China
Received 28 July 2006; accepted 15 September 2006
Abstract: The oxidation behavior of a cast Ni-base superalloy K44 in air at 850-1 000 ℃ for l00 h was studied. The scales on the surface were determined by SEM and EPMA equipped with an EDXS. The results show that oxidation kinetics obey the parabolic law from which the values of activation energy Qp1=221.1 kJ/mol and Qp2=247.6 kJ/mol are estimated. The oxidation scales are composed of loose outer layer of TiO2/TiO-Cr2O3 and a small amount of NiCr2O4 and NiA12O4, compact intermediate layer Cr2O3, and precipitate of internal oxides A12O3.
Key words: K44 superalloy; high temperature oxidation; oxidation kinetics
1 Introduction
In comparison with advanced aircraft engine, the work environment of gas turbine in the industry is more hostile and working time is longer [1]. In gas turbine engines, materials are not only subjected to high stresses, but also frequently cycled from ambient to high temperature in air. Thus, the mechanical properties and the oxidation resistance of these materials are of great importance. Due to the complexity of alloy constituent, oxidation behavior exists many differences [2-6]. Therefore, a number of oxidation behavior of alloys have been proposed in the alloy systems. For instance, LITZ et al [7] found oxidation behavior of IN738 and IN993 alloys; LOU et al [8] studied oxidation resistance of sputtered micro-grain alloy K38G; GUO et al [9] researched oxidation behavior of NiAl- 28Cr-5Mo-1Hf alloy; PENG et al [10] also studied the oxidation behavior of M17, M17F and M41 alloys.
The purpose of this study is to present the results of a study which evaluates the oxidation characteristics of Ni-base cast superalloy K44 used frequently as turbine-disc material in gas turbines with the maximum service temperature of about 900 ℃. Because the superalloy K44 includes 7.4%(mass fraction) refractory elements (W+Mo+Nb) and precipitation strengthened elements (Al+Ti), the high-temperature mechanical properties are high. The oxidation behavior of the superalloy K44 is rarely studied up to now. In this study, oxidation kinetics and scales composition of K44 alloy were investigated in static air at 850-1 000 ℃ for 100 h. The results can be provided as the foundation of experiment and the basis of theory for designing and applying the alloy.
2 Experimental
A cast Ni-base superalloy K44 was prepared by melting and refusing in a vacuum induction furnace, followed by casting into ingots with diameter of 15 mm in vacuum. After the ingots were machined into specimens of 10 mm×10 mm×4 mm, the specimens were grounded down to 800-1 000 grit with SiC paper, ultrasonically cleaned in alcohol and acetone, and dried in drier before oxidation. The chemical composition (mass fraction, %) of the cast Ni-base superalloy K44 contains Cr 15.28, Al 3.10, trace Co, Ti and Hf, (W+Mo+Nb) 7.4, and balance Ni.
The Ni-base superalloy K44 specimens were oxidized in static air at 850-1 000 ℃ The oxidation kinetics was studied by means of discontinuous thermo- gravimetric analysis (TGA). The tested conditions were 850, 900, 950 and 1 000 ℃ for 1, 3, 5, 10, 25, 50, 75 and 100 h, respectively. The surface composition of the oxide scale formed on the superalloy K44 was analyzed using X-ray diffraction (XRD). The surface and cross sectional morphologies of oxide scale after oxidation were characterized by scanning-electron spectroscope (SEM), and EPMA equipped with an EDXS unit, and element distribution maps was utilized to investigate the cross section of the oxide scales.
3 Results and discussion
3.1 Oxidation kinetics
The mass change (per unit area) as a function of isothermal oxidation time is shown in Fig.1 for the cast Ni-base superalloy K44 at 850, 900, 950 and 1 000 ℃. It can be seen that the mass gain of alloy K44 increases gradually with increasing oxidation temperature. In the initial stage, oxidation rate is very fast, but it becomes slow with increasing oxidation time, and it is basically unchanged in the steady stage. The results show that oxidation resistance of superalloy K44 below 900 ℃ is better than that at 900-1 000 ℃.
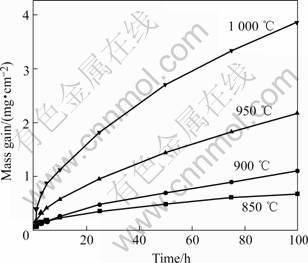
Fig.l Oxidation kinetic curves of superalloy K44 at 850-1 000 ℃ for 100 h
The square of the specific mass gain as a function of exposure time for the superalloy K44 at 850, 900, 950 and 1 000 ℃ are shown in Fig.2. It can be seen that the plots of the square of mass gain result in straight lines, indicating that the oxidation kinetics follow a parabolic oxidation law at 850-1 000 ℃. The data of the rate constant KP can be derived from Fig.2 using linear regression analysis method, and the results are listed in Table 1. From the relationship of straight lines, there are two parabolic rate constants KP1 and KP2 in each temperature, which reveals the change of the oxidation mechanism in total oxidation stages. The transient time is 25 h and Kp1>Kp2 at 850 ℃. The transient point of straight lines takes place at 39, 31 and 29 h, and Kp1<Kp2 at 900, 950 and 1 000 ℃, respectively. The experiment shows that oxidation mechanism can be controlled from surface reaction to diffusion reaction [6]. It can be explained that the diffusion of Cr3+ increases with increasing oxidation temperature in oxidation layer. According to regression analysis, the parabolic rate constant of oxidation is found to be an exponential function of temperature (Table 1) according to ARRHENIUS equation:
Kp=Aexp[-Qp/(RT)] (1)
where Kp is the oxidation rate constant, mg2/(cm4?h); Qp is the activation energy, kJ/mol; R is gas constant; and T is the oxidation temperature. The activation energy of the oxidation process was estimated to be respectively 221.1 kJ/mol and 247.6 kJ/mol from the slope of ln Kp vs. 1/T plot using data points corresponding to temperatures of 850, 900, 950 and 1 000 ℃, as shown in Table 1. It can be suggested that the activation energy is similar with that of Cr3+ diffusion being 259 kJ/mol in Cr2O3 layer of oxidation. The results show that superalloy K44 oxidation process is governed mainly by Cr3+ diffusion in Cr2O3 layer of oxidation.
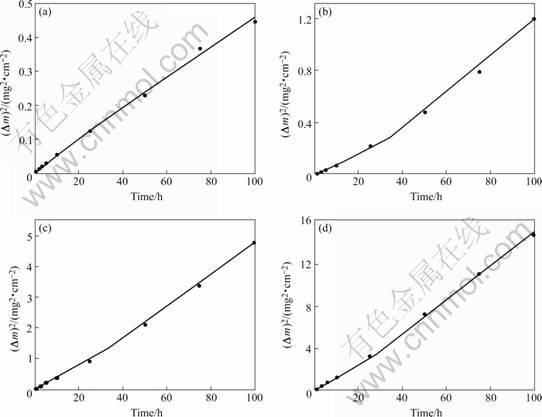
Fig.2 Dependence of square of mass gain (Δm)2 on oxidation time for superalloy K44 at different temperatures: (a) 850 ℃; (b) 900 ℃; (c) 950 ℃; (d) 1 000 ℃
Table 1 Parabolic reaction rate constants kp at different temperatures and oxidation active energy QP of superalloy K44
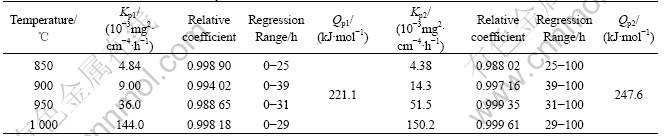
3.2 Identification of surface oxides
The results of X-ray diffraction of superalloy K44 after oxidation at 850-1 000 ℃ for 100 h are listed in Table 2, where the phases are put in order according to X-ray diffraction peaks from strong to weak. The characteristic peaks of the oxides can be observed, which is basically similar to the results found on the superalloy K35 at 850-1 000 ℃ for 100 h [7]. Surface oxides were identified as Cr2O3, TiO2, with a certain amount of Al2O3, NiCr2O4, NiAl2O4 and TiO. The major components of the surface oxides were Cr2O3 and TiO2. In order to improve the oxidation resistance of the alloys, cast Ni-base superalloy K44 is added by 15% Cr. The results show that the addition of 15% Cr to the alloy can result in the formation of Cr2O3, mainly with NiCr2O4, TiO2 and TiO, which are dense, stable and continuous. The results of X-ray diffraction coincide with those of oxidation kinetics. From an analysis of energy-dispersion spectrometry (EDXS) of the surface, most of NiO reacted with the inner Cr2O3 to produce NiCr2O4 spinel. Although there were NiCr2O4 and NiAl2O4 in the oxidation scales, the amount of these oxides was less and cannot form continuous oxidation scales.
Table 2 Phase constitutions of scales formed on K44 after 100 h oxidation
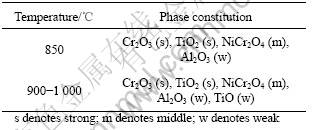
3.3 Scale morphologies
The surface morphologies of the superalloy K44 at 900 ℃ after 100 h oxidation are shown in Fig.3(a), and the magnified views of the zones A and B are shown in Fig.3(b) and Fig.3(c), respectively. It can be seen that the surface of oxide scales can be divided into two parts. The bright(B) and the dark(A) zones have been found to be rich in Cr2O3 and TiO2 in this oxide scale, respectively. The corresponding representative EDX results show element components (mole fraction, %) of O 59.58, Al 0.88, Ti 10.85, Cr 23.31, Ni 4.45, Co 0.93 in the light region; and O 76.98, Al 0.90, Ti 12.53, Cr 9.41, Ni 0.35, Co 0.10 in the dark region. Fig.3(b) shows that rich-Ti phase is the rutile-shaped oxide particles, having a size of several microns, while Fig.3(c) shows that rich-Cr is composed of very fine oriental-shaped grains, about 1 μm. It can be seen that the Cr2O3 and TiO2 scales coexist on the surface of the specimen oxidized at 900 ℃ for 100 h.
The surface morphology of the superalloy K44 at 1 000 ℃ for 100 h is shown in Fig.3(d). Because the evaporation of Cr2O3 was increased in this temperature [11], the surface oxide scales of rich-Ti were observed in the bright(B) and the dark(A) zones. The corresponding representative EDX results show element components (mole fraction, %) of O 69.96, Al 0.12, Ti 27.97, Cr 1.44, Ni 0.17, Co 0.08, Mo 0.26 in the light region and O 64.85, Al 0.78, Ti 17.71, Cr 15.70, Ni 0.73, Co 0.04, Mo 0.19 in the dark region.
3.4 Cross-section morphologies and analysis
The microstructure changes of the cross-section of specimens at 850-1 000 ℃ for 100 h are shown in Fig.4. The cross-section of oxide layer can be divided into the upper oxide layer and inner oxide zone. The thickness of the upper oxide layer increases with increasing temperature, where the oxide layer thickness of 2.2, 5.1, 10 and 20 μm at 850-1 000 ℃ for 100 h is detected, respectively. A large number of root-like internal oxides are formed in the alloy matrix below the surface oxide scale in the inner oxide zone. The corresponding representative EDX results of C and D locations show element components(mole fraction, %) of O 59.40, Al 2.65, Ti 5.97, Cr 31.6, Ni 0.81 in the C location, and O 49.02, Al 29.44, Ti 0.46, Cr 2.16, N 15.71, Co 3.21 in the D location at 900 ℃ for 100 h, respectively. The major component of the scale is Cr oxide, which is identified as Cr2O3 by combining with X-ray diffraction analysis in the upper oxide layer, and Al2O3 mainly formed in the inner oxide layer.
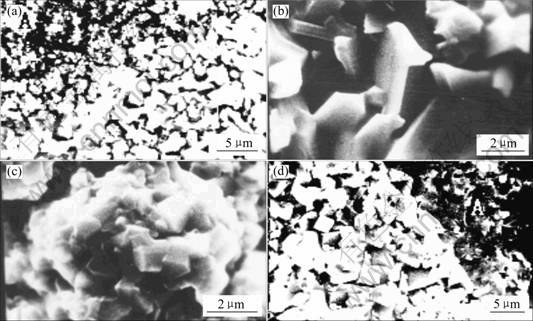
Fig.3 SEM images of superalloy K44 oxidized for 100 h at 900 ℃(a), A zone at 900 ℃(b), B zone at 900 ℃(c) and B zone at 1 000 ℃(d)
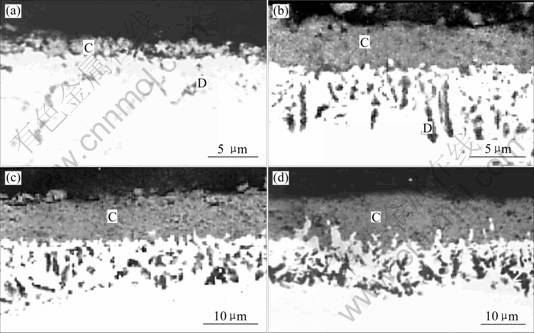
Fig.4 Cross-sectional SEM images of superalloy K44 oxidized for 100 h at 850 ℃(a), 900 ℃ (b), 950 ℃(c) and 1 000 ℃ (d)
EPMA micrographs of element mapping of the cross-section of the specimen oxidized at 900 ℃ for 100 h are shown in Fig.5. It is clearly displayed that a dense, continuous and protective Cr2O3 oxide layer can be formed. The oxide layer can be divided into three layers. The outer layer is rich in Ti containing certain amount of Cr; the intermediate layer is rich in Cr with Ti and a small amount of Al, Ni and Co; while the inner layer is rich in Al plus little amount of Ti, Cr and Co. Oxygen was detected in the three layers.
4 Conclusions
1) The oxidation kinetics of a cast Ni-base superalloy K44 obey parabolic law in air at 850-1 000 ℃ for l00 h, where the values of activation energy were QPl = 221.1 kJ/mol and Qp2=247.6 kJ/mol.
2) The oxidation scales are composed of loose upper layer of TiO2/TiO-Cr2O3 and a small amount of NiCr2O4 and NiA12O4, compact intermediate layer Cr2O3, and precipitates of internal oxides A12O3.
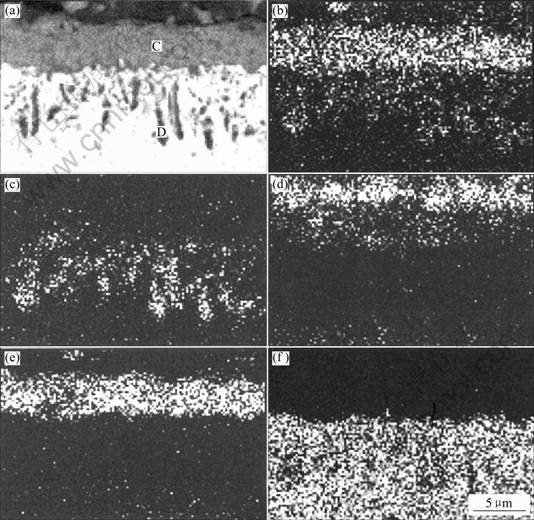
Fig. 5 SEM micrographs of cross-sectional images of K44 superalloy at 900 ℃ for 100 h and its X-ray element maps: (a) SE; (b) O Kα; (c) Al Kα; (d) Ti Kα; (e) Cr Kα; (f) Ni Kα
References
[1] CHEN Rong-zhang, WANG Lou-bao, LI Jian-hua. Review and prospect on developments of cast superalloys [J]. J Aero Mater, 2000, 20(1): 55-61.
[2] BERTHOD P. Kinetics of high temperature oxidation and chrome volatilization for a binary Ni-Cr alloy [J]. Oxid Met, 2005, 64(3/4): 235-252.
[3] ABE F, ARAKI H, YOSHIDA H, OKADA M. The role of aluminum and titanium on the oxidation process of a nickel-base superalloy in steam at 800 ℃ [J]. Oxid Met, 1987, 27(1/2): 21-36.
[4] HUANG L, SUN X, HU Z. Oxidation behavior of the directionally solidified Ni-base superalloy DS951 in air [J]. Oxid Met, 2005, 64(5/6): 303-318.
[5] CHEN J H, ROGERS P M, LITTLE J A. Oxidation behavior of several chromia-forming commercial nickel-base superalloys [J]. Oxid Met, 1997, 47(5/6): 381-410.
[6] CHEN Guo-feng, LOU Han-yi. Oxidation behavior of sputtered Ni-3Cr-20Al alloy [J]. Mater Sci Technol, 2000, 16(1): 88-90.
[7] LITZ J, RAHMEL A, SCHORR M, WEISS J. Scale formation on the Ni-base superalloys IN939 and IN738LC [J]. Oxid Met, 1989, 32(3/4): 167-184.
[8] LOU Han-yi, WANG Fu-hui, XIA Bang-jie, ZHANG Li-xin. High-temperature oxidation resistance of sputtered micro-grain superalloy K38G [J]. Oxid Met, 1992, 38(3/4): 299-307.
[9] GUO J T, XU C M. Effect of NiAl microcrystalline coating on the high-temperature oxidation behavior of NiAl-28Cr-5Mo-1Hf [J]. Oxid Met, 2002, 58(5/6): 475-468.
[10] PENG Xiao, SHEN Jian-lan, HU Wu-sheng, YUAN Ke-qi, ZHOU Long-jiang, LI Tie-fan. A comparative investigation of oxidation performance of superalloys M17 and M17F at high temperatures [J]. J Chin Soci Prot, 1996, 16(1): 20-28.
[11] YAMAUCHI A, KUROKAWA K, TAKAHASH H. Evaporation of Cr2O3 in atmospheres containing H2O [J]. Oxid Met, 2003, 59(5/6): 529-542.
(Edited by YANG You-ping)
Foundation item: Project(59895152) supported by the National Natural Science Foundation of China
Corresponding author: LI Yun; Tel: +86-24-89383241; E-mail: liyun195735@163.com