文章编号:1004-0609(2014)04-0944-06
Cu-Ni-Si合金连续挤压过程中的组织演变及性能
孙 健1,刘 平1, 2,刘新宽2,陈小红2,何代华2,马凤仓2,李 伟2
(1. 上海理工大学 机械工程学院 上海 200093;
2. 上海理工大学 材料科学与工程学院 上海 200093)
摘 要:利用光学显微镜、透射电子显微镜(TEM)、维氏硬度仪和万能材料试验机对Cu-Ni-Si合金连续挤压过程中的组织演变和性能特征进行研究。结果表明:Cu-Ni-Si 合金在连续挤压过程中发生了第二相颗粒的析出,颗粒大小约为10 nm;与纯铜的连续挤压相比,Cu-Ni-Si 合金在连续挤压过程中没有发生明显的动态再结晶,因此,直角弯曲变形区可进一步划分为呈典型织构组织分布的直角弯曲前变形区和直角弯曲后变形区;各变形区的硬度值随着变形量的增加逐渐由95HV上升至194HV,并在粘着区和直角弯曲区出现明显升幅。拉伸实验结果表明:挤压前后,材料的抗拉强度由276 MPa上升至505 MPa,而塑性由22.3%下降至13.4%。
关键词:Cu-Ni-Si合金;连续挤压;组织演变;性能
中图分类号:TG 146.21 文献标志码:A
Microstructure evolution and properties of Cu-Ni-Si alloy during continuous extrusion process
SUN Jian1, LIU Ping1, 2, LIU Xin-kuan2, CHEN Xiao-hong2, HE Dai-hua2, MA Feng-cang2, LI Wei2
(1. School of Mechanical Engineering, University of Shanghai for Science and Technology, Shanghai 200093, China;
2. School of Materials Science and Engineering, University of Shanghai for Science and Technology,
Shanghai 200093, China)
Abstract: The microstructure evolution and properties of Cu-Ni-Si alloy during continuous extrusion were investigated by using optical microscopy, transmission electron microscopy, micro-Vickers hardness measurement and universal- testing machine. The results indicate that the precipitation forms during continuous extrusion, the particle size is about 10 nm. Since the completed dynamic recrystallization does not occur, the right-angle bending region can further divide into before-right-angle bending region and after-right-angle bending region. With the increase of deformation, the Vickers hardness rises from 95HV to 194HV during the extrusion, and ascends significantly in adhesion region and after-right-angle bending region, respectively. The tensile test indicates that the continuous extrusion can obviously enhance the tensile strength from 276 MPa to 505 MPa, but slightly decrease the ductility from 22.3% to 13.4%.
Key words: Cu-Ni-Si alloy; continuous extrusion; microstructure transformation; property
连续挤压技术是由英国的Derek Green先生在20世纪70年代首次提出的一种新型塑性加工方法[1-2]。因其与传统挤压相比,在生产连续化、降低能耗和提高材料利用率方面具有显著优势,因此,成为一种重要的新型有色金属加工技术[3]。今天,连续挤压技术已广泛用于铝、铜及铜合金中小型材、铝及铝合金盘管、双金属导线和电缆包铝等材料的生产[4]。
近年来,被报道的用于连续挤压工艺生产的成型金属材料多为强度较低的纯铝、纯铜、镁合金及铝合金[5-8],对高强度铜合金的连续挤压研究研究较少,尤其是析出强化型高强度铜合金的连续挤压鲜见报道。国内有少量文献对KFC铜合金的连续挤压做了报道[9],但仅从工艺的角度验证连续挤压技术制备铜合金板坯的可能性。对铜合金在挤压过程中的组织结构变化未做深入研究,与纯铜相比有无不同还不清楚,有无析出也没有明确结论。随着电子工业的发展,对铜合金材料的要求越来越高。目前,超大规模集成电路所需的理想高性能铜合金基本上分为高强高导和高强度中导两类,而Cu-Ni-Si系合金最有希望出现高强度中导电率的合金,对该系列的合金的加工研究极为迫切。本研究采用金相、电子显微分析方法和显微硬度测量,研究典型析出强化型铜合金 Cu-Ni-Si 合金连续挤压过程中的组织演变规律和性能特征,为连续挤压成型析出强化型铜合金的实际生产提供理论和实验依据。
1 实验
实验材料为Cu-Ni-Si(C70250)合金,其化学成分如表1所示。材料为圆棒坯料,直径d 16 mm,棒料采用900 ℃、60 min 固溶处理,室温水淬后,再进行750 ℃、20 min预热处理,然后在MFCCE350挤压机上以5 r/min的转速进行挤压试验,制得尺寸为30 mm×11 mm的板坯,水冷至室温,完成变形过程。将挤压变形腔内的坯料取出,用线切割机沿纵向切割取样。分析不同成型阶段的材料组织变化,并测量不同变形阶段材料的硬度。组织结构分析在Axio ScopeA1型蔡司光学显微镜上进行,试样侵蚀剂为王水溶液。析出相分析在TecnaiG2F20型透射电子显微镜(TEM)进行,加速电压为200 kV,采用离子减薄法制备试样。显微硬度测试在HXD1000 TMC型数显显微硬度计上进行,载荷为0.49 N,每个试样选取5个区域进行测试,误差为±5%。拉伸试验在Zwick 50 kN万能材料试验机上进行,沿挤压板坯纵向加工拉伸试样,拉伸速度为1 mm/min。
表1 合金的化学成分
Table 1 Chemical composition of investigated alloy (mass fraction, %)

2 结果与讨论
2.1 挤压前坯料的组织
Cu-Ni-Si合金棒料挤压前的显微组织如图1所示。由图1可以看出,经过固溶、淬火处理,Ni和Si元素完全溶入Cu基体中形成过饱和单相固溶体,晶粒为等轴晶并出现较多孪晶。

图1 挤压前坯料的组织
Fig. 1 Optical micrograph of feedstock before extrusion
2.2 连续挤压过程中的组织演变
根据连续挤压过程中不同变形阶段材料的组织特征,文献[4, 7, 10]将挤压过程分为5个变形区,即剪切摩擦区、镦粗变形区、粘着区、直角弯曲区和扩展成型区。实验发现:对于Cu-Ni-Si合金,其挤压过程中的组织演变规律既有与纯铜相同的部分,也有组织变化明显不同的区域,划分为6个变形区更为合适,即保留以上5个变形区,将直角弯曲区更改为直角弯曲前变形区,并添加直角弯曲后变形区。图2所示为Cu-Ni-Si合金连续挤压过程各塑形变形区的划分示意图。
Cu-Ni-Si合金在连续挤压过程中,不同塑性变形区的金相组织如图3所示。对比纯铜和黄铜的组织演变,Cu-Ni-Si合金在剪切摩擦区(见图3(a))和镦粗区(见图3(b))的组织变化与纯铜和黄铜基本相同[7, 10],坯料先被压实轮压实、镦粗并逐渐充满整个型腔,并在型腔壁形成一层剪切变形带。从粘着区(见图3(c))开始,组织的变化规律出现明显不同,Cu-Ni-Si合金内没有形成大量的剪切变形。本研究中,挤压前棒料采取的预热温度较高,引起表面皮层软化,造成摩擦因数温度分量的减小[11],这导致挤压轮对坯料摩擦作用的减弱。此时在粘着区,晶粒之间在力偶的作用下发生晶面转动,通过协调变形,朝着有利于挤压变形的方向发生转动,因而没有形成大量的剪切变形带[12]。
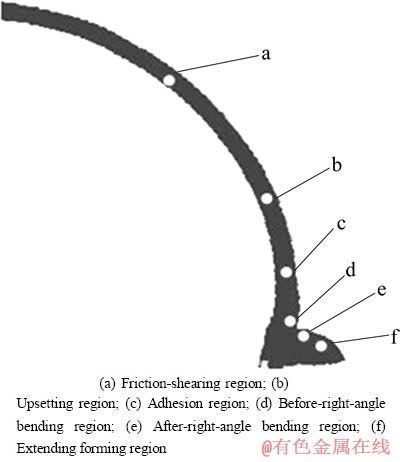
图2 连续挤压过程中各塑形变形区
Fig. 2 Plastic deformation regions of Cu-Ni-Si alloy in continuous extrusion process
图3(d)和(e)所示为直角弯曲前变形区和直角弯曲后变形区,其特征为绝大部分晶粒逐渐形成稳定的取向并沿挤压方向被拉长。这一变化与纯铜不同,在直角弯曲变形区没有发现动态再结晶组织,分析其原因为:首先,由于坯料的预热温度高,导致变形抗力及单位体积的变形功降低[13],以致挤压时的温度效应与纯铜连续挤压时相比要小,所以动态再结晶驱动力不足;其次,MFCCE350挤压机的转速为5 r/min,此时坯料通过直角弯曲区时的应变速率较高。研究表明:Cu-Ni-Si合金在600~800 ℃的热变形过程中,变形温度越高、变形速率越慢,越容易发生动态再结晶[14]。因此,高应变速率下,动态再结晶晶粒的形核与长大受到抑制。这一组织变化特征与纯铜和黄铜在直角弯曲区发生动态再结晶有显著不同,所以有必要将直角弯曲区进一步划分为直角弯曲前和直角弯曲后两个特征变形区。
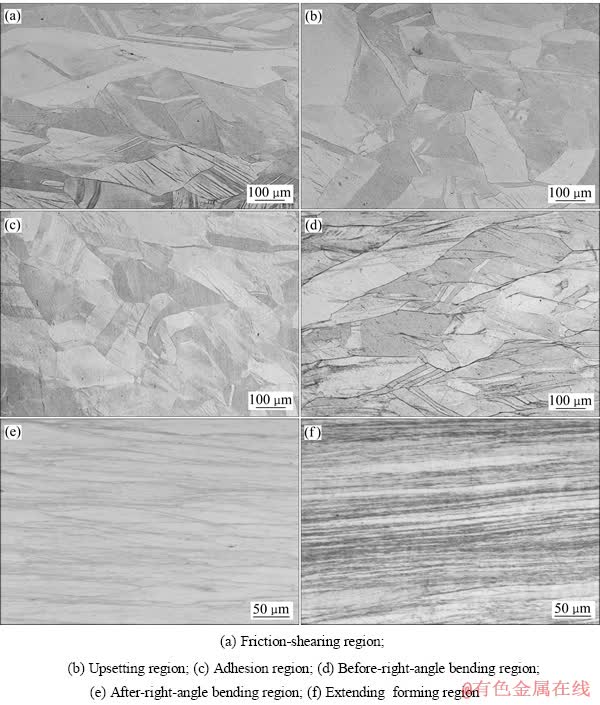
图3 Cu-Ni-Si合金连续挤压型腔内不同区域的组织演变过程
Fig. 3 Microstructure evolutions of Cu-Ni-Si alloy in different regions in continuous extrusion cavity
在扩展成型区(见图3(f)),与纯铜形成完整的动态再结晶组织明显不同的是:Cu-Ni-Si合金原先的等轴晶粒组织已经沿挤压方向被拉长,形成加工织构,层状晶粒的平均厚度由直角弯曲后变形区的20 μm减小到7 μm左右,变形量进一步加大。
2.3 Cu-Ni-Si合金的析出
Cu-Ni-Si合金是典型的时效强化型合金,合金的力学性能与合金内有无析出相密切相关。而在连续挤压过程中,由于存在较大的温升,变形均处于高温状态,极有可能存在第二相的析出。为了确定连续挤压试验过程中是否有第二相的生成,研究采用电子显微分析法对挤压后板坯的微观相组成进行了研究与分析。
图4所示为 Cu-Ni-Si 合金连续挤压后成型板坯的TEM明场和暗场形貌。Cu-Ni-Si 合金早期时效的转变机制有两类[15]:即位错缠结处的择优析出及析出与再结晶协同作用的不连续析出。图4 (a)和(b)中含有大量沿位错线分布的弥散细小第二相颗粒(照片中尺寸为100 nm左右的黑色颗粒为原材料中未充分溶解的Si)。由图4可以看出,第二相的尺寸非常的细小,约为10 nm左右,并且有一部分的析出颗粒是沿着位错择优析出。弥散分布的第二相颗粒对位错形成了有效的钉扎,这必将造成材料力学性能的提高。除此之外,也可以在晶界处观察到细小的第二相颗粒,细小的第二相颗粒可以有效地钉扎位错及亚晶界,这样可以有效地阻碍小角度晶界向大角度晶界的转变,并提升晶内位错的累积。因此,可以判定Cu-Ni-Si 合金在连续挤压过程中是有析出相生成的。
2.4 性能测试及分析
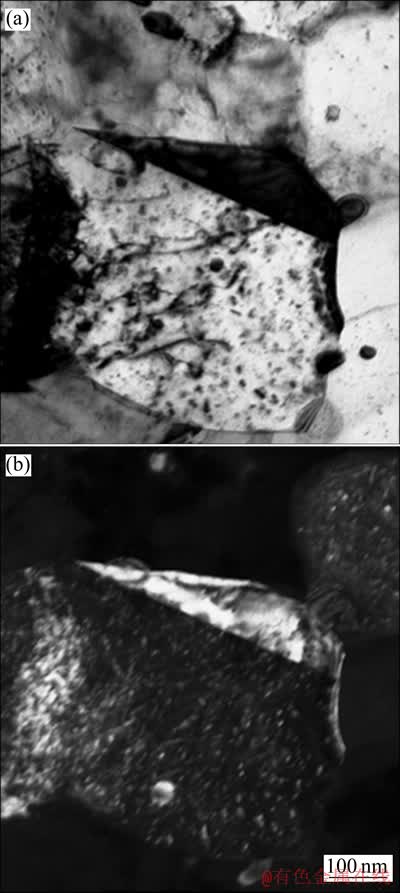
图4 C70250 Cu-Ni-Si合金挤压板坯的TEM明场及暗场
Fig. 4 Bright-field (a) and dark-field (b) TEM images of extruded C70250 Cu-Ni-Si alloy plate
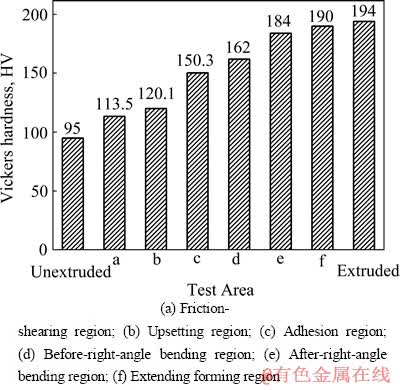
图5 Cu-Ni-Si合金各挤压变形区及挤压前后的硬度变化
Fig. 5 Vickers hardness change of different deformation regions of Cu-Ni-Si alloy before and after extrusion
图5所示为Cu-Ni-Si合金连续挤压变形区及挤压前后的硬度变化。从图5中可以看出,坯料在连续挤压过程中随着变形的增加,显微硬度值总体呈上升趋势,并在粘着区和直角弯曲后变形区出现两次较大的升幅。挤压前,试样采用固溶处理后显微硬度较低。在剪切摩擦区(a)和镦粗区(b),实际上是变形空间逐渐填充直至全部充满的过程[16],变形量不大,相比挤压棒料,显微硬度只是略有上升。在粘着区(c)和直角弯曲前变形区(d)坯料已充满型腔,随着温度和压力的升高,将促使摩擦因数的增加,此时晶粒在摩擦力的作用下扭转变形,显微硬度明显上升。在直角弯曲后变形区(e),随着变形量的增加,机械咬合加强,摩擦因数进一步提升[11],坯料在不断升高的静水压力作用下,进入扩展成型区,形成加工织构,出现挤压过程中第二次硬度峰值。这与黄铜的连续挤压在直角弯曲区由于动再结晶,组织软化,导致硬度值下降有着明显不同[4]。在扩展成型区(f),虽然层状晶粒的厚度进一步减小,但在动态回复的作用下,显微硬度没有太大的增加。合金硬度的变化与连续挤压过程中组织的演变规律相吻合。
图6所示为Cu-Ni-Si合金挤压前采用固溶处理后的棒料和挤压板坯的拉伸实验曲线。从图6中可以看出:挤压后,材料的抗拉强度比挤压前有明显提高,由原先的276 MPa上升到505 MPa,强度增加了一倍左右。但同时,成型板材的断后总伸长率也由原先的22.3%下降到了13.4%。这是因为原材料经过连续挤压转变为加工织构,而没有发生明显的动态再结晶,动态回复不足以软化晶粒在挤压过程中所造成的加工硬化,所以造成强度的提高和塑性的下降。从总体来说,产品的综合力学性能有所提高。
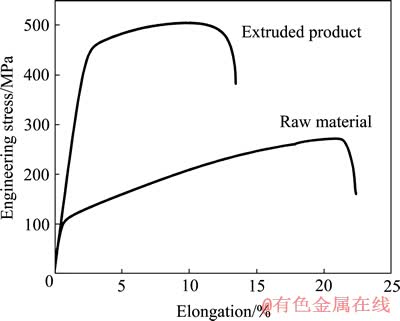
图6 Cu-Ni-Si合金挤压前后拉伸曲线
Fig. 6 Tensile curves of Cu-Ni-Si alloy before and after continuous extrusion
3 结论
1) 与纯铜连续挤压过程中组织的演变规律相比:由于未发生明显的动态再结晶,Cu-Ni-Si合金在连续挤压过程可以分为6个变形区,即直角弯曲变形区可进一步划分为呈典型织构组织分布的直角弯曲前变形区和直角弯曲后变形区。
2) Cu-Ni-Si合金在连续挤压过程中有第二相析出,大小约为10 nm。
3) Cu-Ni-Si合金在连续挤压过程中材料的显微硬度随变形量的增加而增大,在粘着区和直角弯曲区增幅明显,体现出明显的加工硬化效果,这与组织变化规律相符。挤压后,材料的强度由276 MPa上升至505 MPa,而塑性由22.3%下降至13.4%
REFERENCES
[1] GEREK D. The continuous extrusion forming of wire sections[J]. Journal of the Institute of Metals, 1972, 100(8): 296-300.
[2] ETHERINGTON C. The UKAEA conform method of continuous extrusion forming[J]. New Development in Wire Technology, 1977, 44: 85-89, 161-163.
[3] 彭大暑. CONFORM—一种实用的有色金属连续挤压技术[J]. 重型机械, 1986, 11: 39-44, 31.
PENG Da-shu. CONFORM—A practical nonferrous metal continuous extrusion technology[J]. Journal of Heavy Machinery, 1986, 11: 39-44, 31.
[4] 隋 贤, 宋宝韫, 李 冰, 运新兵, 高 飞. H65黄铜合金连续挤压过程中的组织和性能演变特征[J]. 中国有色金属学报, 2009, 19(6): 1049-1054.
SUI Xian, SONG Bao-yun, LI Bing, YUN Xin-bing, GAO Fei. Characteristic of microstructure and properties evolution of H65 brass alloy during continuous extrusion process[J]. The Chinese Journal of Nonferrous Metals, 2009, 19(6): 1049-1054.
[5] ZHANG Hui, YAN Qi-qi, LI Luo-xing. Microstructures and tensile properties of AZ31 magnesium alloy by continuous extrusion forming process[J]. Materials Science and Engineering A, 2008, 486(1/2): 439-443.
[6] 宋宝韫, 周传河. 纯Al颗粒CONFORM连续挤压工艺的实验研究[J]. 金属学报, 1991, 27(2): 140-144.
SONG Bao-yun, ZHOU Chuan-he. A study of pure Al grain CONFORM continuous extrusion technology[J]. Acta Metallurgica Sinica, 1991, 27(2): 140-144.
[7] 王 军, 运新兵, 李 冰, 樊志新, 宋宝韫. 纯铜连续挤压全过程的组织演变[J]. 有色金属: 冶炼部分, 2011, 5: 38-41.
WANG Jun, YUN Xin-bing, LI Bing, FAN Zhi-xin, SONG Bao-yun. Microstructure evolution of copper during continuous process[J]. Nonferrous Metals: Extractive Metallurgy, 2011, 5: 38-41.
[8] 张新宇, 王延辉, 高 飞, 贺旭东. 6063铝合金连续挤压工艺研究[J]. 锻压技术, 1999, 24(1): 31-32, 48.
ZHANG Xin-yu, WANG Yan-hui, GAO Fei, HE Xu-dong. Research on continuous extrusion technology for 6063 Al alloy[J]. Forging & Stamping Technology, 1999, 24(1): 31-32, 48.
[9] 孙海洋, 闫志勇, 樊志新. KFC铜合金引线框架带材的连续挤压制造技术[J]. 现代制造工程, 2011, 12: 83-87.
SUN Hai-yang, WANG Yan-hui, FAN Zhi-xin. Continual extrusion manufacturing technology of KFC copper alloy lead frame strip[J]. Modern Manufacture Engineering, 2011, 12: 83-87.
[10] 隋 贤, 宋宝韫, 李 冰, 运新兵. H62黄铜合金连续挤压的变形行为和组织演变特征[J]. 有色金属, 2011, 63(1): 11-13, 18.
SUI Xian, SONG Bao-yun, LI Bing, YUN Xin-bing. Deformation characteristic and microstructure evolution of H62 brass copper during continuous extrusion[J]. Nonferrous Metals, 2011, 63(1): 11-13, 18.
[11] 储灿东, 王东哲, 彭颖红, 阮雪榆. 连续挤压成形过程的温度场研究[J]. 塑性工程学报, 2001, 8(1): 9-12.
CHU Can-dong, WANG Dong-zhe, PENG Ying-hong, RUAN Xue-yu. Research on temperature field during continuous extrusion[J]. Journal of Plasticity Engineering. 2001, 8(1): 9-12.
[12] 余永宁. 材料科学基础[M]. 北京: 高等教育出版社, 2006: 561-570.
YU Yong-ning. Fundamentals of materials science[M]. Beijing: China Higher Education Press, 2006: 561-570.
[13] 俞汉清, 陈金德. 金属塑性成型原理[M]. 北京: 机械工业出版社, 1999: 46-50.
YU Han-qing, CHEN Jin-de. Metal plastic forming principle[M]. Beijing: China Machine Press, 1999: 46-50.
[14] 范 莉, 刘 平, 贾淑果, 陈少华, 于志生. 集成电路用铜-镍-硅合金的动态再结晶行为[J]. 机械工程材料, 2009, 33(6): 25-28.
FAN Li, LIU Ping, JIA Shu-guo, CHEN Shao-hua, YU Zhi-sheng. Dynamic recrystallization behavior of Cu-Ni-Si alloy for integrated circuit materials[J]. Materials for Mechanical Engineering, 2009, 33(6): 25-28.
[15] ZHAO Dong-mei, DONG Qi-ming, LIU Ping, KANG Bu-xi, WANG Dong-feng, JIN Zhi-hao. Aging behavior of Cu-Ni-Si alloy[J]. Materials Science and Engineering A, 2003, 361(1/2): 93-99.
[16] 樊志新, 宋宝韫, 刘元文, 运新兵. 连续挤压变形力学模型与接触应力分布规律[J]. 中国有色金属学报, 2007, 17(2): 283-289.
FAN Zhi-xin, SONG Bao-yun, LIU Yuan-bing, YUN Xin-bing. Mechanical model and stress distribution of continuous extrusion process[J]. The Chinese Journal of Nonferrous Metals, 2007, 17(2): 283-289.
(编辑 李艳红)
基金项目:上海市教委创新项目(11YZ112);上海市科委基础研究重点项目(10JC1411800);上海市教育委员会重点学科建设项目(J50503)
收稿日期:2013-07-05;修订日期:2013-11-20
通信作者:刘 平,教授;电话:18511795137;E-mail: usstsunjian@163.com