Trans. Nonferrous Met. Soc. China 31(2021) 3428-3438
Evolution of coordination between α and β phases for two-phase titanium alloy during hot working
Jian-wei XU1,2,3, Wei-dong ZENG1,2,3, Da-di ZHOU1,2,3, Sheng-tong HE1,2,3, Run-chen JIA1,2,3
1. Shaanxi Key Laboratory of High-Performance Precision Forming Technology and Equipment, School of Materials Science and Engineering, Northwestern Polytechnical University, Xi’an 710072, China;
2. Defense Technologies Innovation Center of Precision Forging and Ring Rolling, School of Materials Science and Engineering, Northwestern Polytechnical University, Xi’an 710072, China;
3. State Key Laboratory of Solidification Processing, Northwestern Polytechnical University, Xi’an 710072, China
Received 27July 2021; accepted 10 November 2021
Abstract:
he evolution of coordination between αand β phases for a two-phase titanium alloy was investigated. For this purpose, hot compression and heat treatment under different conditions were carried out. The results show that the ability of coordinated deformation between αand β phases can influence uniformity of microstructure evolution. Specifically, α phase maintains the lamellar structure and β phase has a low degree of recrystallization when the ability of coordinated deformation is good. In this case, α andβ phases still maintain the BOR (Burgers orientation relationship), and their interface relationship is not destroyed even at large deformation. Both of the deformation extent of α lamellae and recrystallization degree of β phase increase with the decline of ability of coordinated deformation. The α phase only maintains the BOR with β phase on one side, while the uncoordinated rotation with the β phase on the other side occurs within 10°. The α and β phases rotate asynchronously when ability of coordinated deformation is poor. The degree of interface dislocation increases, and α and β phases deviate from the BOR.
Key words:
coordination ability; titanium alloy; orientation relationship;globularization; recrystallization;
1 Introduction
Titanium alloys have excellent comprehensive properties such as high specific strength, high temperature resistance, high corrosion resistance, and good crack propagation resistance [1,2]. They have been widely used in aviation, aerospace, navigation, petrochemical, biomedical and other fields [3-6]. Titanium alloys are the difficult-to-deformation material, and their processing methods are generally hot working, including high-temperature deformation and subsequent heat treatment. The microstructure of titanium alloys will change significantly during hot working process, and further affect the mechanical properties and engineering applications [7]. Therefore, it is very important to research the relationship between process parameters and microstructure for titanium alloys [8,9].
Generally speaking, hot working of titanium alloy starts from single β phase field, and the initial microstructure contains large-sized β grains and flat α lamellae [10]. Subsequently, high-temperature deformation in α+β phase region is conducted to change microstructure and improve the plasticity, toughness, fatigue life, etc. In this process, a series of changes of microstructural morphology will occur [7,11]. Among them, the recrystallization of β phase and globularizationof α phase are the most common and important [12,13].
The globularization of α phase usually occurs in α+β phase region. The influence factors include strain, strain rate and temperature. Among them, the effect of strain is the most direct. There are different critical strain values of globularization for different titanium alloys. For example, the critical strains of TC11 [14], TA15 [15], and BT25 [16] alloys are respectively 0.42-0.65, 0.34-0.59 and 0.11-0.41 when materials are deformed at 100 °C below β transformation point of β phase. The globularization mechanism generally includes grain boundary splitting [17], termination migration [18], shearing model of laths [19], Rayleigh perturbation model [20], Oswald ripening [21,22] and so on.
Recrystallization can be segmented into dynamic and static recrystallization [12]. The continuous dynamic recrystallization is the most common for titanium alloys, and it has been confirmed in Ti-6Al-4V [23], Ti55531 [24] andTi-1023 [25] alloys. In addition, BALACHANDRAN et al [26] studied high temperature deformation of Ti5553 alloy and found a new form of recrystallization. The grains nucleate at the α/β phase boundary by means of the epitaxial growing up, and the authors call this epitaxial recrystallization. In general, the influence factors of recrystallization include the stacking fault energy (SFE), original grain size, thermal processing conditions and second phase particles. For titanium alloys, various morphologies of α phase have different effects on recrystallization. Furthermore, α and β phases influence each other, and their coordinated deformation ability determines the final microstructure morphology. Under the same external force conditions, the coordinated deformation behavior between αand β phases is an important reason for microstructure inhomogeneity, which is closely related to their own crystal orientation. The related phenomena have an important impact on material performance.
Ti-17 titanium alloy is a near-β titanium alloy, which has the advantages of high strength, high service temperature and good fatigue performance. It is an important candidate material for manufacturing aero-engine components. However, the heterogeneity of microstructure is a key point to affect the forgings production. In this work, the microstructure evolution of α and β phases and their coordinated evolutionwill be studied to solve this technical key. The relevant studies will provide certain guidance for the processing of Ti-17 alloy, and it is of great significance for engineering application of Ti-17 alloy.
2 Experimental
Ti-17 alloy is used in this work and its normal composition is Ti-5Al-4Cr-4Mo-2Zr-2Sn. It is a typical near-β titanium alloy with 8% of β-stabilizer elements. The measured βtransus temperature is 895 °C by metallographic method. The initial microstructure of as-received Ti-17 alloy is shown in Fig. 1, and it contains fully lamellar α within β matrix. The information of crystal orientation of initial microstructure can be obtained in our previous work [13]. In the initial microstructure, the crystal orientation of α phase and parent β phase is governed by Burgers orientation relationship (BOR): (0001)α//(110)β;
//[111]β.
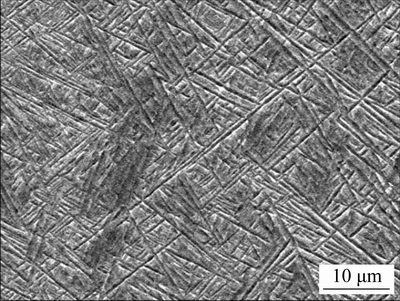
Fig. 1 Initial microstructure of Ti-17 alloy
In this work, the isothermal deformation and heat treatment experiments are carried out to investigate the evolution of microstructure and crystal orientation. The samples are cylinder billets with 75 mm in diameter and 90 mm in height, and they are compressed to height reductions of 20%, 40%, 60% and 80% at 820 °C. Heat treatment experiments are carried out at 820 °C, and heat treatment time is0.5 and 2 h, respectively. The sampling point is shown in Fig. 2. The samples are immediately water-quenched after hot working, and the microstructure observation is carried out on the axial section. The SEM (scanning electron microscope), TEM (transmission electron microscope) and EBSD (electron back-scattered diffraction) technologies are used to analyze microstructure characterization. It should be noted that the step size of the EBSD test is set to be 0.3 μm.
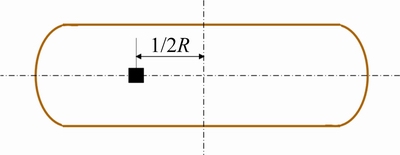
Fig. 2 Sampling point of sample
3 Results and discussion
3.1 Microstructure evolution
Figure 3 shows microstructure morphologies under different deformations. It can be found that the original α lamellae gradually transform into the globularized structure with the increaseof deformation degree, which is a typical globularization process. An α particle is considered to be a globularized structure if it possesses an aspect ratio of 2.5 or less. The related information has been analyzed in detail in our previous work [27]. The change of β phase is also very worthy of attention in addition to the globularization process of α phase. It can be vaguely seen that the β matrix is divided into small recrystallized grains by the globularizedα phase. Such phenomenon is not obvious when the deformation is low, but it is very obvious when the deformation is large, as shown in Fig. 3(d).
Microstructure morphologies after the heat treatment are shown in Fig. 4. Samples are deformed to height reductions of 20% and 60%, and then are heated for 2 and 0.5 h at 820 °C, respectively. It can be found that globularization and coarsening of α phase are obvious after heat treatment. Accordingly, it seems that more recrystallized β grains are formed, as indicated by the arrow in Fig. 4. Moreover, there is inhomogeneity in microstructure, especially under small deformation conditions.
3.2 Recrystallization behavior during hot working
Theoretically, the degree of recrystallization is directly related to deformation, and it increases with the increase of deformation degree. In order to better study the evolution behavior of β phase, the EBSD analysis is performed on samples with large deformation (80%). A larger area and step size are set during the experiment to make the analysis more accurate, which makes it difficult to identify the small α phase, as shown in Fig. 5. A completely recrystallized β structure is observed, which indicates that the complete recrystallization of β matrix occurs at a large amount of deformation. According to our previous work [13], the globularization of α phase and recrystallization of βphase influence each other. The globularization and recrystallization processes will be delayed when α and β phases have a better coordination. Otherwise, the globularization and recrystallization will proceed more easily. The coordination is better when plane of easy slip of β phase is parallel to the compression direction. However, the recrystallization of β phase will inevitably occur when the amount of deformation is large enough.
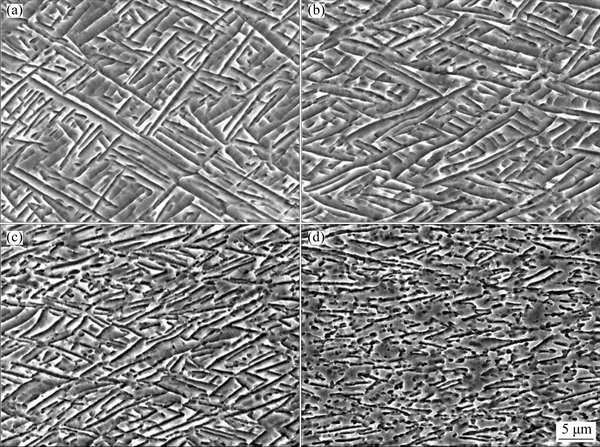
Fig. 3 SEM morphologies for materials deformed to 20%(a), 40%(b),60% (c) and 80%(d)
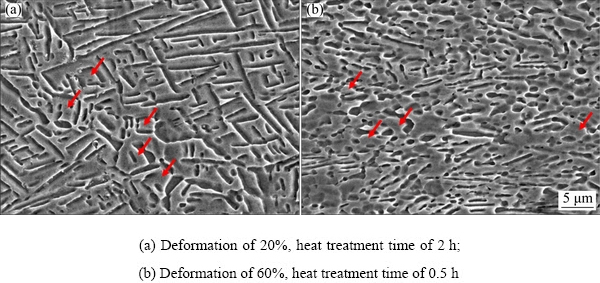
Fig. 4 SEM morphologies of samples under different conditions
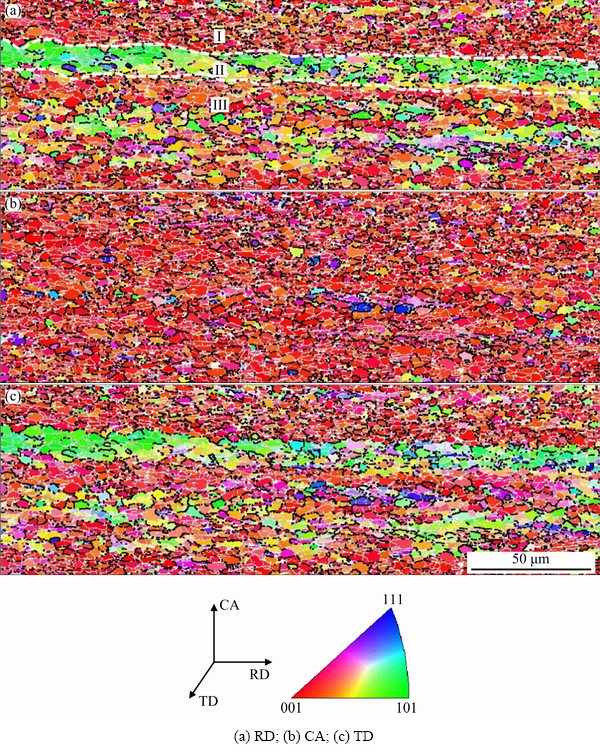
Fig. 5 IPF (inverse pole figure) in different directions
Figure 5 shows the IPF (inverse pole figure) of β phase for 80% deformation at three directions. Almost all recrystallized β grains have the same orientation from the compression axis (CA) direction, as shown in Fig. 5(b), the [001] direction of β phase is parallel to the CA. However, the crystal orientations of recrystallized β grains are different from the RD and TD directions. As shown in Fig. 5(a), the entire area is divided into three parts, namelyRegions I, II and III. The pole figures of the three regions are shown in Fig. 6. It can be seen that the textures of Regions I, II and III are [001]//CA. All recrystallized β grains show the same orientation in the CA direction, but different orientations in the RD and TD directions, which is fiber texture characteristics.
Titanium alloy has high stacking fault energy, and the continuous dynamic recrystallization (CDRX) is the major way to refine grain [12]. The CDRX is a process of the continuous rotation of sub-grains, including the formation of low and high angle grain boundaries and the final recrystallization. However, the special characteristics of the recrystallized β grains in Region II are observed: the serrated boundary and about twice thickness of subgrain size. Such characteristics belong to the geometric dynamic recrystallization (GDRX) [28]. In any case, the original β grains are severely elongated and a complete recrystallized structure is obtained after large deformation. Meanwhile, the recrystallized grains belonging to the same original β grain still have similar crystal orientation, showing obvious fiber texture characteristics.
The β phase can be completely recrystallized only under the condition of large deformation. Deformation is also an energy storage process. The stored distortion energy will promote β phase to undergo static recrystallization during the heat treatment when the amount of deformation is not enough to cause the occurrence of dynamic recrystallization of β phase. The EBSD results for material deformed to height reduction of 20% and holding for 2 h can be found in Ref. [13]. As shown in Fig. 7 [13], therecrystallization degree of β phase is low and there is obvious inhomogeneity.
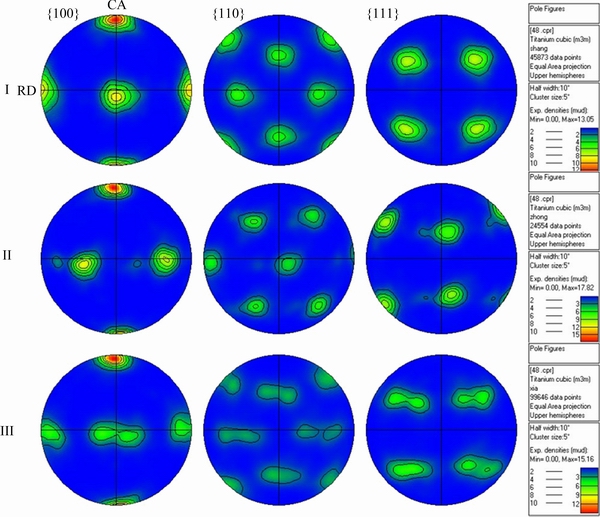
Fig. 6 PFs (pole figures) in Regions I, II and III

Fig. 7 PFs for material deformed to 20% and then heat treatment for 2h [13]
Such phenomenon is related to the coordinated deformation ability between αand β phases. The globularization of α phase and recrystallization of β phase promote each other, and the globularizedα phase has a partitioning effect on β phase, which is helpful for the occurrence of recrystallization.
The pole figures of the two regions (RegionsH and L) are shown in Fig. 7 [13]. The orientations of β grains are more scattered in the region with high degree of recrystallization. The β recrystallization progresses slowly due to insufficient deformation. In this case, the assistance of the second phase particles is necessary to increase the degree of recrystallization.
Figure 8 shows the EBSD results for material deformed to height reduction of 60% and holding for 0.5 h. The degree of globularization of α phase is very high, most α phase has been transformed into the globularized structure. In this case, the complete recrystallization of β phase has also occurred, which is the result of the combined action of dynamic and static processes.There are structural differences in Regions I and II in Fig. 8(b). The β phase in Region I is mainly composed of low angle boundaries, while the large angle boundaries increase significantly in Region II (2°-15° is defined as low angle boundaries, represented by thin black lines and greater than 15° is defined as large angle boundaries, represented by thick black lines). From the pole figures (Figs. 8(c) and (d)), the two regions basically maintain the BOR. This indicates that the BOR is difficult to be completely destroyed even if large plastic deformation occurs. However, it is found that α and β phases in Region II have more orientations, which appear to be more scattered on the pole figure, on the contrary, and α and β phases in Region I are more concentrated. The sizes of α phases are different by comparing Region I with Region II.
In this work, the coarser α phase has a more obvious promotion effect on the recrystallization of β phase, and the fine α phase cannot effectively divide the original β grains, making it impossible to become an effective site for the recrystallization of β phase. As mentioned earlier, the recrystallization of β phase requires not only external factors such as deformation and temperature, but also the assistance of the second phase particles. Under a large amount of deformation, the globularization of α phase and recrystallization of β phase proceed simultaneously. The initial β grains are effectively fragmented by α phase, and the recrystallization of β phase takes α phase as the grain boundary. In this process, α phase is also globularized, as shown in Fig. 9.

Fig. 8 EBSD analysis for material deformed to 60% and then heat-treated for 0.5 h
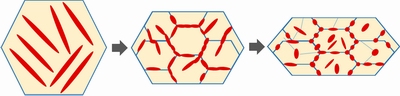
Fig. 9 Schematic diagram of globularization and recrystallization
3.3 Interaction effect of α and β phases
A more detailed analysis is performed on the typical microstructure, as shown in Fig. 10. In this part, αparticles are divided into the three types according to morphology and crystal orientation. Firstly, α phase maintains the lamellar structure, and meanwhile surrounding β phases have the same or similar crystal orientations, labeled asRegions I, II and III. Secondly, the surface of α phase has the deeper grooves, but still present the same orientation. At this time, the crystal orientations of surroundingβ phases are different, labeled asRegions IV and V. Thirdly, the globularizedαphase presents different crystal orientations, meanwhile the crystal orientations of surrounding β phases are also different, labeled as Regions VI, VII, and VIII.
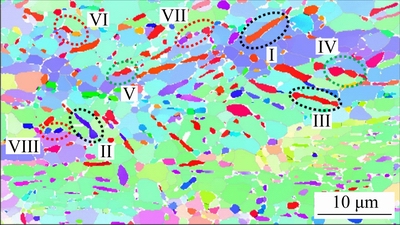
Fig.10 EBSD analysis of crystal orientation for material deformed to 60% and then heat-treated for 0.5 h
The pole figures of RegionsI, II and IIIin Fig. 10 and their schematic diagrams for the first type are shown in Fig. 11. The pole figures showthat α phase and surrounding β phases basically maintain the BOR after hot working. Although the initial lamellar α is slightly disturbed and bent, it still maintains the lamellar structure in general. Moreover, its crystal orientation maintains the BOR relationship with surrounding β phases, which shows that α and β phases rotate almost simultaneously during deformation process. In this case, the semi-coherent interface between them also rotates at the same time, and it is not broken. Large deformation does not break the BOR between αand β phases, and there is a good ability of coordinated deformation between the two phases. It is speculated that the three conditions must be met to cause this phenomenon: on the one hand, the crystal orientations of α and β phases are in a favorable position for deformation relative to deformation direction, and it is not easy to occur for dislocation plugging. On the other hand, α andβ phases maintain the BOR, and dislocations can easily pass through the phase interface. Finally, deformation of the two phases is relatively uniform, without extreme conditions such as adiabatic shear bands. Under such conditions, the degrees of αglobularization and β recrystallization are relatively low.
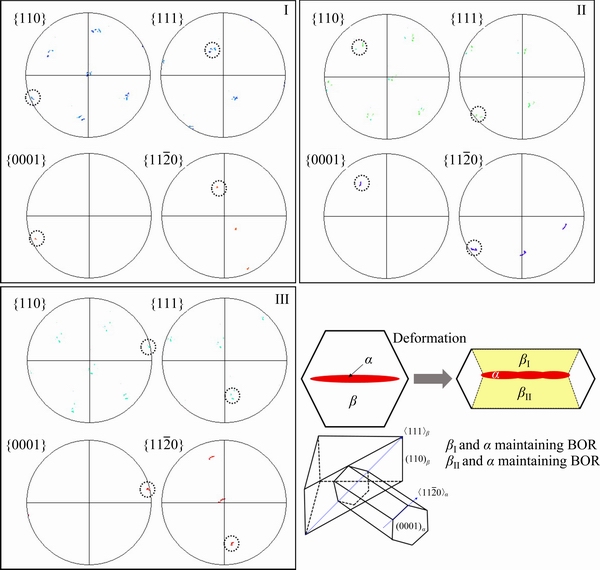
Fig. 11 PFs of Regions I, II, and III in Fig. 10 and schematic of crystal orientation
Figure 12 shows the pole figures of RegionsIV, and Vin Fig. 10 and schematic of crystal orientation for the second type. This type of α phase only maintains the BOR with β phase on one side. The BOR is not strictly corresponding, and deviates by a certain anglewithin 10°. Such behavior is caused by the weakening of ability of coordinated deformation between αand β phases. The α phase only maintains a good ability of coordinated deformation with β phase on one side, the two phases rotate synchronously during deformation, so that the BOR is basically not destroyed. On the other side, the relationship between αand βphases cannot be effectively coordinated. The corresponding relationship between αand βphases deviates in order to adapt to the external force during deformation, which ultimately leads to changes in the microstructure morphology and crystal orientation.
Figure 13 shows the pole figures and theschematic of crystal orientation of the third type. The α and β phases deviate from the BOR, and thedeviation angles are 15°-20°. The αphase and surrounding β phase cannot effectively coordinate the deformation during hot working. In this case, β phase is deformed preferentially, and the crystal structure rotates accordingly. But α phase does not rotate synchronously at this time. It is in the unfavorable position of slip system and becomes a hard particle, and then, a high-energy interface is formed between αand β phases. Energy is stored in the phase boundary and within the two phases in the form of distortion energy. It will cause changes in the structure and crystal orientation when the distortion energy reaches a certain level. As observed earlier, the globularization of αphase and the recrystallization of β phase occur. Compared to other cases, both globularizationand recrystallization degree are higher.
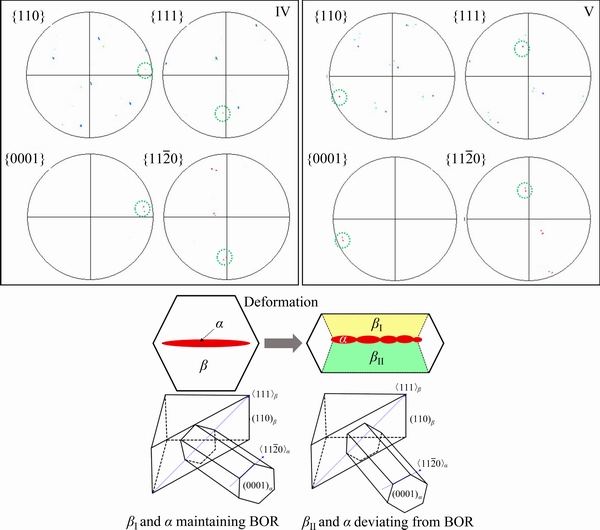
Fig. 12 PFs of Regions IV and V in Fig. 10 and schematic of crystal orientation
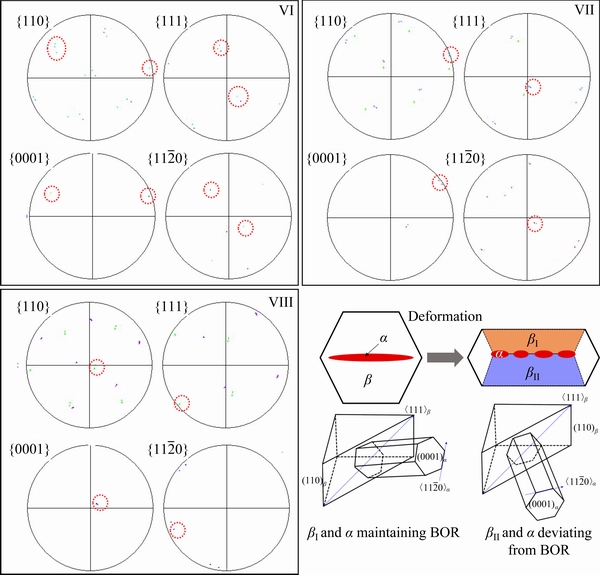
Fig. 13 PFs of Regions VI, VII and VIII in Fig. 10 and schematic of crystal orientation
The evolution of coordination is more likely to occur when the crystal orientations of β phases around α phase are consistent or similar, which leads to the lower degrees of globularization and recrystallization. The α phase only maintains the BOR with one of β grains when the crystal orientations of β phases around α phase are different. At this time, α phase is easier to globularize during the deformation, and the globularization of α phase will in turn promote the recrystallization of β phase. Therefore, a series of measures in single β phase region are advised to adopt in order to refine β grain and increase the dispersity of crystal orientation of β phase. The measures include larger deformation, more forge fire, shorter holding time (ensure through heating) and so on. Such measures will help to increase the globularization friction of α phase.
4 Conclusions
(1) The globularization of α phase and recrystallization of β phase in Ti-17 alloy influence each other, and the two processes will be delayed when α and β phases have a better coordination. The inhomogeneity of microstructure is related to the coordinated deformation ability between αand β phases.
(2) The CDRX is main mechanism for β recrystallization. The recrystallization of β phase requires not just external factors such as deformation and temperature, but the assistance of α phase.
(3) Through the EBSD analysis, the orientation relationship between αand β phases has an important influence on the coordinated behavior. Three types of correspondence have been found and analyzed.
Acknowledgments
TheauthorsaregratefulforthefinancialsupportsfromtheNational Natural Science Foundation of China (No. 51905436) and the Natural Science Foundation of Shaanxi Province, China (No. 2020JQ-156).
References
[1] ZHAO Z B, WANG Q J, HU Q M, LIU J R, YU B B, YANG R. Effect of β(110) texture intensity on α-variant selection and microstructure morphology during β to α transformation in near α titanium alloy [J]. ActaMaterialia, 2017, 126: 372-382.
[2] ZHAO Z B, WANG Q J, LIU J R, YANG R. Effect of heat treatment on the crystallographic orientation evolution in a near-α titanium alloy Ti60 [J]. ActaMaterialia, 2017, 131: 305-314.
[3] XIN H J, LIAO M Q, WANG X H, CHEN Z H, CHEN Z C, WANG P. Effect of volume fracture of primary α phase on mechanical property in TC18 alloy [J]. Journal of Netshape Forming Engineering, 2021, 13(3): 143-147. (in Chinese)
[4] MORAKABATI M, HAJARI A. Hot working behavior of near alpha titanium alloy analyzed by mechanical testing and processing map [J]. Transactions of Nonferrous Metals Society of China, 2020, 30: 1560-1573.
[5] XU Z Z, DONG Z Q, YU Z H, WANG W K, ZHANG J X. Relationships between microhardness, microstructure, and grain orientation in laser-welded joints with different welding speeds for Ti6Al4V titanium alloy [J]. Transactions of Nonferrous Metals Society of China, 2020, 30: 1277-1289.
[6] SHI S X, LIU X S, ZHANG X Y, ZHOU K C. Comparison of flow behaviors of near beta Ti-55511 alloy during hot compression based on SCA and BPANN models [J]. Transactions of Nonferrous Metals Society of China, 2021, 31: 1665-1679.
[7] GAO P F, FU M W, ZAHN M, LEI Z N, LI Y X. Deformation behavior and microstructure evolution of titanium alloys with lamellar microstructure in hot working process: A review [J]. Journal of Materials Science and Technology, 2020, 39: 56-73.
[8] XIAO H, FAN X G, ZHAN M, LIU B C, ZHANG Z Q. Flow stress correction for hot compression of titanium alloys considering temperature gradient induced heterogeneous deformation [J]. Journal of Materials Processing Technology, 2021, 288: 116868.
[9] SHAO Y R, YANG F, CHEN C G, GUO Z M. Microstructure and performance of gelcasting Ti6Al4V alloys [J]. Journal of Netshape Forming Engineering, 2021, 13(2): 7-12. (in Chinese)
[10] XU J W, ZENG W D, ZHAO Q Y, ZHOU D D, HE S T, JIA R C, ZHOU X F. Analysis of deformation behavior and microstructure of a near-α titanium alloy in single phase region [J]. Materials Science and Engineering A, 2021, 803: 140723.
[11] XU J W, ZENG W D, ZHANG X Y, ZHOU D D. Analysis of globularization modeling and mechanisms of α/β titanium alloy [J]. Journal of Alloys and Compounds, 2019, 788: 110-117.
[12] LI K, YANG P. Strain-induced α-to-β phase transformation during hot compression in Ti-5Al-5Mo-5V-1Cr-1Fe alloy [J]. Transactions of Nonferrous Metals Society of China, 2019, 29: 296-304.
[13] XU J W, ZENG W D, ZHOU D D. Analysis of crystallographic orientation and morphology of micro- structure during hot working for anα/β titanium alloy [J]. Journal of Materials Science and Technology, 2020, 59: 1-13.
[14] SONG H W, ZHANG S H, CHENG M. Dynamic globularization kinetics during hot working of a two phase titanium alloy with a colony α microstructure [J]. Journal of Alloys and Compounds, 2009, 480: 922-927.
[15] WU C B, YANG H, FAN X G, SUN Z C. Dynamic globularization kinetics during hot working of TA15 titanium alloy with colony microstructure [J]. Transactions of Nonferrous Metals Society of China, 2011, 21(9):1963-1969.
[16] MA X, ZEGN W D, TIAN F. The kinetics of dynamic globularization during hot working of a two phase titanium alloy with starting lamellar microstructure [J]. Materials Science and Engineering A, 2012, 548: 6-11.
[17] XU J W, ZENG W D, JIA Z Q, SUN X, ZHOU J H. Static globularization kinetics for Ti-17 alloy with initial lamellar microstructure [J]. Journal of Alloys and Compounds, 2014, 603: 239-247.
[18] PARK C H, WON J W, PARK J W. Mechanisms and kinetics of static spheroidization of hot-worked Ti-6Al-2Sn-4Zr-2Mo-0.1Si with a lamellar microstructure [J]. Metallurgical and Materials Transactions A, 2012, 43: 977-985.
[19] SESHACHARYULU T, MEDEIROS S C, MORGAN J T. Hot deformation mechanisms in ELI grade Ti-6A1-4V [J]. ScriptaMaterialia, 1999, 41: 283-288.
[20] TIAN Y L, KRAFT R W. Mechanisms of pearlite spheriodization [J]. Metallurgical and Materials Transactions A, 1987, 18(8): 1403-1414.
[21] LI J J, GUO C W, WANG Z J. Effect of initial particle size distribution on the dynamics of transient Ostwald ripening: A phase field study [J]. ActaMaterialia, 2015, 90:10-26.
[22] XU J W, ZENG W D, MA H Y, ZHOU D D. Static globularization mechanism of Ti-17 alloy during heat treatment [J]. Journal of Alloys and Compounds, 2018, 736: 99-107.
[23] OHNISHI H, TAKAMOTO K, MATSUMOTO H, MATSUMOTO R. Microstructural evolution of a Ti-6Al-4V alloy produced by forging process combined with torsional motion [J]. Journal of Manufacturing Processes, 2020, 58: 1161-1170.
[24] ZHANG H, SHAO H, SHAN D. Influence of strain rates on high temperature deformation behaviors and mechanisms of Ti-5Al-5Mo-5V-3Cr-1Zr alloy [J]. Materials Characterization, 2021, 171: 110794.
[25] ZHAO J, ZHONG J, YAN F, CHAI F, DARGUSCH M. Deformation behaviour and mechanisms during hot compression at supertransus temperatures in Ti-10V-2Fe-3Al [J]. Journal of Alloys and Compounds, 2017, 710: 616-627.
[26] BALACHANDRAN S, KUMAR S, BANERJEE D. On recrystallization of the α and β phases in titanium alloys [J]. ActaMaterialia, 2017, 131: 423-434.
[27] XU J W, ZENG W D, SUN X, JIA Z Q. Microstructure evolution during isothermal forging and subsequent heat treatment of Ti-17 alloy with a lamellar colony structure [J]. Journal of Alloys and Compounds, 2015, 637: 449-455.
[28] GHOLINIA A, HUMPHREYS F J, PRANGNELL P B, Production of ultra-fine grain microstructures in Al-Mg alloys by coventional rolling [J]. ActaMaterialia, 2002, 50: 4461-4476.
热加工过程中两相钛合金的α相与β相的协调演变
徐建伟1,2,3,曾卫东1,2,3,周大地1,2,3,贺胜通1,2,3,贾润晨1,2,3
1. 西北工业大学 材料学院 陕西省高性能精确成形技术与装备重点实验室,西安 710072;
2. 西北工业大学 材料学院 国防科技工业精密锻造与环轧技术创新中心,西安 710072;
3. 西北工业大学 凝固技术国家重点实验室,西安 710072
摘 要:为了研究两相钛合金中α和β相的协调演变行为,在不同条件下对合金进行热压缩和热处理。研究结果表明,α和β相之间的协调变形能力能影响显微组织演变的均匀性。当变形协调能力较好时,α相保持原来的片状结构,β相的再结晶程度较低。此时,尽管变形较大,但α相与两侧的β相仍保持Burgers取向关系,α和β相之间的原始相界面没有被破坏。随着变形协调能力的下降,片状α相的变形程度及β相的再结晶程度增加。此时,α相仅与一侧的β相保持Burgers取向关系,而与另一侧的β相取向产生偏移,偏移角度在10°以内。当变形协调能力较差时,α相和β相发生较为严重的偏移,界面位错程度增大,α相与周围的β相偏离Burgers取向关系。
关键词:协调变形能力;钛合金;取向关系;球化;再结晶
(Edited by Wei-ping CHEN)
1003-6326/
2021 The Nonferrous Metals Society of China. Published by Elsevier Ltd & Science Press
Abstract:The evolution of coordination between αand β phases for a two-phase titanium alloy was investigated. For this purpose, hot compression and heat treatment under different conditions were carried out. The results show that the ability of coordinated deformation between αand β phases can influence uniformity of microstructure evolution. Specifically, α phase maintains the lamellar structure and β phase has a low degree of recrystallization when the ability of coordinated deformation is good. In this case, α andβ phases still maintain the BOR (Burgers orientation relationship), and their interface relationship is not destroyed even at large deformation. Both of the deformation extent of α lamellae and recrystallization degree of β phase increase with the decline of ability of coordinated deformation. The α phase only maintains the BOR with β phase on one side, while the uncoordinated rotation with the β phase on the other side occurs within 10°. The α and β phases rotate asynchronously when ability of coordinated deformation is poor. The degree of interface dislocation increases, and α and β phases deviate from the BOR.