Trans. Nonferrous Met. Soc. China 31(2021) 3394-3404
Effects of trace Ag on precipitationbehavior and mechanical properties of extruded Mg-Gd-Y-Zr alloys
Dong-dongZHANG1, Chu-mingLIU1,2, Shu-nongJIANG1, Ying-chunWAN1,3, Zhi-yongCHEN1
1. School of Materials Science and Engineering, Central South University, Changsha 410083, China;
2. School of Materials Science and Engineering, Hunan University of Science and Technology, Xiangtan 411201, China;
3. Research Institute of Light Alloy, Central South University, Changsha 410083, China
Received 14September 2021; accepted 10November 2021
Abstract:
he effects of trace Ag element on the precipitation behaviors and mechanical properties of the Mg-7.5Gd-1.5Y-0.4Zr (wt.%) alloy by means of tensile test, X-ray diffractometry, scanning electron microscopy, electron backscattered diffractometry, and scanning transmission electron microscopy. There is an unusual texture (<0001>//extrusion direction) in the extruded Mg-Gd-Y-Zr alloys containing 0.5 wt.% Ag. During the aging periods at 225 °C, the addition of the trace Ag does not form new precipitates, just accelerates aging kinetics, and refines β′ precipitates, thereby increasing the number density of the β′ precipitates by Ag-clusters. Moreover, the Mg-Gd-Y-Zr alloy containing 0.5 wt.% Ag shows the most excellent synergy of strength and plasticity (408 MPa of ultimate tensile strength, 265 MPa of yield strength, and 12.9% of elongation to failure) after peak-aging.
Key words:
trace Ag; Mg-Gd-Y-Zr alloy;β′ phase; precipitation strengthening;
1 Introduction
Magnesium (Mg) alloys, as one of the lightest structural materials, have attracted worldwide attention in the fields of aerospace, automotive, and rail transportation. Especially, Mg-Gdalloys exhibit remarkable precipitating hardening behaviors and mechanical properties [1-3]. The main precipitate is the β′ metastable phase with a composition of Mg7Gd in the peak-aged condition at 225 °C and these precipitates effectively block dislocation slip and improve the strength of the materials. Mg-Y alloys possess similar precipitation hardening behaviors toMg-Gdalloys[3,4]. Mg-Gd-Y alloys show significant precipitation hardening after peak-aging, while much more time and energy are consumed inevitably. For example, the Mg-10Gd-3Y-0.5Zr (wt.%) alloy achieves peak hardness at about 20 h during the aging process at 225 °C [5], and the peak time is more than 100 h when Mg-6Gd-3Y-0.5Zr (wt.%) is aged at 225 °C.
Fortunately, the addition of the Ag element significantly accelerates the aging response of Mg-Gd-Y alloys. GAO and NIE[6] found that the age-hardening response of the Mg-6Gd-0.6Zr (wt.%) alloy at 200 °C is enhanced after adding 2 wt.% Ag, in which the peak hardness increases to HV 80, and the time to reach peak hardness decreases from 1200 to 50 h. ZHANG et al [7,8] stressed that the addition of 2 wt.% Ag enhances the age-hardening response of the Mg-Gd alloys, which is due to the combination of the basal γ″and prismatic β′ precipitates. On the contrary, the Mg-Y-Ag-Zr alloy shows a weakened age-hardening response after adding Ag, which is caused by the formation of the γ″ phase at the expense of the β′ phase. Furthermore, higher content of Ag increases the cost and density of the Mg alloys. Therefore, it is necessary to continue to investigate the role of the trace Ag in precipitates of the Mg-Gd-Y-Zr alloys.
According to the definition of high-strength Mg alloys with UTS above 400 MPa [9], the majority of Mg-RE alloys achieve high strength after hot deformation and heat treatment. However, the ductility of most Mg-Gd-Y series alloys is poor, and the elongation to failure (EL) is less than 10%. For instance, the UTS, YS, and EL of the Mg-14Gd-0.5Zr alloy are 446 MPa, 305 MPa, and 7.0% after extrusion and peak aging, respectively [10]. Mg-7Gd-3Y-1.4Zn-0.4Zr alloy shows mechanical properties of 431 MPa of UTS, 398 MPa of YS, and 8% of EL after multidirectional forging and peak aging [11]. On the whole, Mg alloys containing higher content of RE elements easily achieve strength performance at the expense of their elongation. But interestingly, HUANG et al [12] found that the YS and EL of the Mg-6Gd-3Y-1Zn-0.4Zr (wt.%) alloy increased to 218 MPa and 4.4% from 184 MPa and 3.3% by the addition of 0.3 wt.% Ag, respectively. Moreover, the production cost of Mg-Gd-Y-Zr alloys can be reduced by replacing part of Gd and Y elements with trace Ag. Thus, the work provides insights into the design of alloys with the synergy of strength and plasticity by adding trace Ag and significantly reducing the content of RE elements.
The Mg-7.5Gd-1.5Y-0.4Zr-xAg (wt.%, x=0, 0.1, 0.5) alloys are designed to achieve significant comprehensive mechanical performance. The addition of the Ag element dramatically enhances the age-precipitating behaviors and mechanical properties of the Mg-Gd-Y-Zr alloys in peak-aged conditions. Therefore, the goal of this work is to expand the application of Mg-RE alloys in the automotive and aerospace industries by cost-cutting with lower RE contents (<10 wt.%).
2 Experimental
The nominal compositions of the alloys are Mg-7.5Gd-1.5Y-0.4Zr, Mg-7.5Gd-1.5Y-0.4Zr-0.1Ag, and Mg-7.5Gd-1.5Y-0.4Zr-0.5Ag (wt.%), which are named as Samples 0Ag, 0.1Ag, and 0.5Ag, accordingly. Three alloys were prepared from pure Mg (99.9 wt.%), pure Ag (99.99 wt.%), Mg-30Gd (wt.%), Mg-30Y (wt.%), and Mg-30Zr (wt.%) master alloys. The raw materials were melted in an electric resistant furnace at 750 °C under the protection of a mixed atmosphere of CO2 and SF6 with a volumetric ratio of 99:1, and then poured into a preheated steel mold (200 °C) to be cooled naturally to room temperature. The actual compositions of three alloys were measured by induced coupled plasma atomic emission spectro- scopy (SPECTRO BLUE SOP), as listed in Table 1.
Table 1 Chemical compositions of alloys
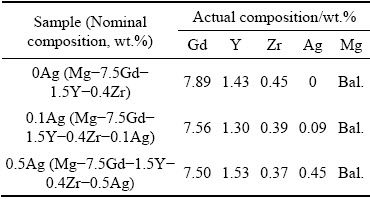
The alloys were homogenized at 520 °C for 24 h after casting, and the ingot surfaces were then scalped. The ingots with a diameter of 85 mm were extruded at 470 °C and a speed of 2.0 mm/s with an extrusion ratio of 25:1. Prior to extrusion, the specimens were immersed at an extrusion temperature for 2 h.
The samples were aged at 225 °C after extrusion. The micro-Vickers hardness tests were carried out with a load of 4.9 N and a holding time of 15 s, and the average of eight measurements was calculated to ensure reliability. The surface of the test samples was perpendicular to the extrusion direction (ED). The tensile specimens with a diameter of 5 mm and a gauge length of 30 mm were prepared from the extruded and peak-aged samples. The ambient tensile tests were conducted on Instron 3369 material test machine at a constant cross-head rate of 1 mm/min, and the tensile direction was parallel to ED. UTS, YS (offset=0.2%), and EL were reported as the average of three repeated tests.
The constituent phases were identified using X-ray diffraction (XRD) (Rigaku D/max2550) with Cu Kα radiation operated at 36 kV in the range of 10°-80° with a scanning speed of 8 (°)/min.
The microstructure of the samples was observed using Helios Nanolab 600i field emission scanning electron microscope (SEM) furnished with a backscattered electron (BSE) detector, an Oxford X-ray energy dispersive spectroscopy (EDS) detector, and an electron backscattered diffraction (EBSD) detector. EBSD test was performed in the scanning area with the number of grains above 2000 at a step size of 6 μm. The raw EBSD data were collected using Oxford Aztect software, and the off-line EBSD data were obtained using Channel 5 software. The EBSD samples were prepared by mechanical grinding using sandpapers and then electro-polishing in a solution of 4% perchloric acid and 96% ethyl alcohol at 25 V and -35 °C.
High-angle annular dark-field (HAADF) scanning transmission electron microscopy (STEM) test was performed using FEI Titan G2 60-300 operated at 300 kV. The electron beam directions were parallel to [0001]α zone axis. The HAADF-STEM specimens with a diameter of 3 mm were prepared by mechanical grinding to 50 μm, and then electro-polishing in a solution of 4% perchloric acid, 1% nitric acid, and 95% ethyl alcohol at 30 V and -35 °C, finally ion-polishing using a Gatan Precision Ion Polishing System (GATAN691). The quantitative determinations of the precipitates were acquired from more than 200 precipitate particles using Image-Pro Plus 6.0 software.
3 Results
3.1 Microstructure in extruded condition
The XRD patterns in Fig. 1show that the main phase of the extruded 0Ag, 0.1Ag, and 0.5Ag alloys isα-Mg, revealing that the addition of the trace Ag does not change the phase compositions. However, some particles of three alloys contain higher Gdand Y contents (Fig. 2), which were commonly observed and identified as the cuboid phase in the Mg-RE alloys [7,13,14]. Due to the small size and a quite low volume fraction, the cuboid phase is considered to have negligible effects on the microstructure and mechanical properties of the alloys.
Based on the statistical results of grain size in Fig. 3, the average grain size of the α-Mg in samples 0Ag, 0.1Ag, and 0.5Ag is 18.42, 18.41, and 19.55 μm, respectively. The addition of the trace Ag rarely changes the grain size of the extruded samples. The misorientation angle distribution shows that the high-angle grain boundaries (>15°) are dominant for all samples, which is a feature that three alloys are full-recrystallized after extrusion. With the increase of the Ag content from 0, 0.1 to 0.5 wt.%, the volume fraction of the grains withc axis parallel to ED increases to 11.8%, 13.9%, and 22.3%, respectively. The unusual orientation was also found in high RE contents of Mg alloys in Refs. [15-17].
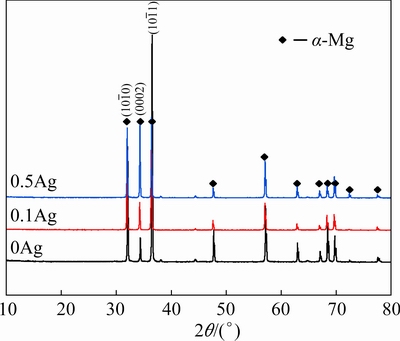
Fig. 1 XRD patterns of extruded alloys
Figure 4 shows pole figures (PF) and inverse pole figures (IPF) derived from EBSD. The extruded 0Ag, 0.1Ag, and 0.5Ag samples possess a weak
//ED texture component with thetexture intensity of 1.77, 1.90, and 1.81, respectively. The texture intensity of the extruded Mg-Gd-Y-Zr alloy is weak with and without Ag, and the texture type is still the same as that of the Mg-Al series alloys [18,19]. Remarkably, the 0.5Ag sample presents an unusual texture component with <0001>//ED except from
//ED. ZHANG et al [17] considered that the weak <0001>//ED texture in the extruded alloys is caused by the growth advantage of recrystallized grains with <0001>//ED orientation during the early stages of grain growth.
3.2 Age-hardening response
The isothermal age-hardening curves of the 0Ag, 0.1Ag, and 0.5Ag alloys at 225 °C are presented in Fig. 5, and some typical values in the age-hardening curves are listed in Table 2.
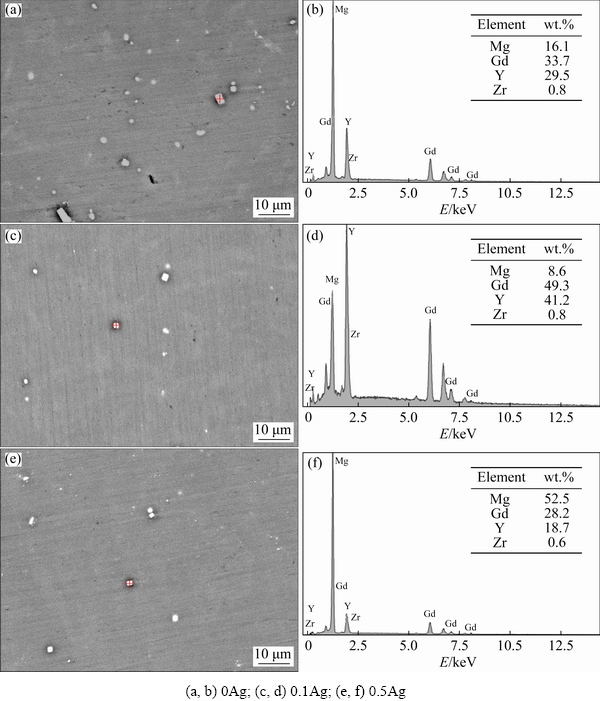
Fig. 2 SEM images(a, c, e) and EDS maps (b, d, f) of extruded alloys
The hardness of the 0Ag alloy is about HV 70 in the extruded condition, which shows a relatively slow hardening rate during the first 10 h after aging at 225 °C. After that, the hardness of the 0Ag alloy increases at an accelerated rate, reaching the peak hardness of about HV 88 at 26 h. The hardness of the extruded 0.1Ag alloy (about HV 75) is slightly higher than that of the 0Ag counterpart. The hardening rate of the 0.1Ag alloy is faster than that of the 0Ag alloy during the first 2 h aging. After that, a noticeable increase in age-hardening is detected during isothermal aging. The 0.1Ag sample achieves the peak-aged hardness of about HV 100 after aging for 13 h. The 0.5Ag alloy exhibits a similar age-hardening behavior, and the hardness in the extruded condition is about HV 78, which is higher than that of the 0Ag and 0.1Ag counterparts. The hardness of the 0.5Ag alloy increases dramatically after an incubation time of about 2 h, and reaches the peak hardness of about HV 108 at 10 h. Compared with the 0Ag sample, the 0.1Ag and 0.5Ag samples show an enhanced age-hardening response and precipitation kinetics. The incubation period is decreased, the aging process is accelerated, and the peak hardness is improved by adding trace Ag. The hardness increment of the 0Ag, 0.1Ag, and 0.5Ag samples is about 25.7%, 33.3%, and 38.4%, respectively.
3.3 Microstructure in peak-aged condition
The β′ phase is the main precipitate in the peak-aged state of the Mg-Gd-Y-Zr alloy with and without Ag according to XRD analysis (Fig. 6), which means that the Ag addition does not change the phase compositions.
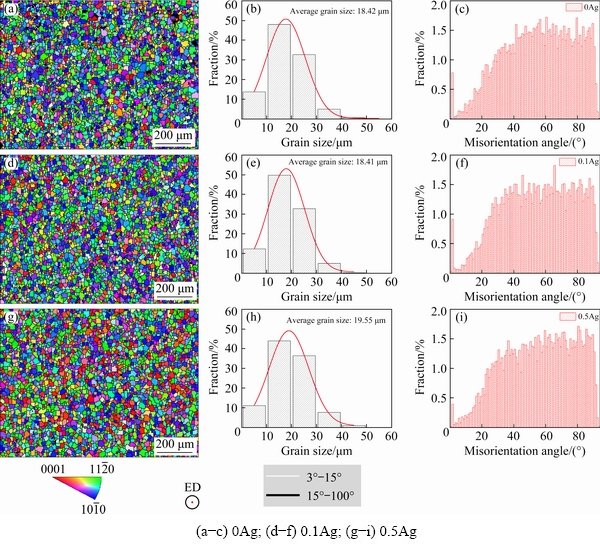
Fig. 3 Orientation maps(a, d, g), grain size distribution (b, e, h) and misorientation angle distributions(c, f, i) of extruded alloys
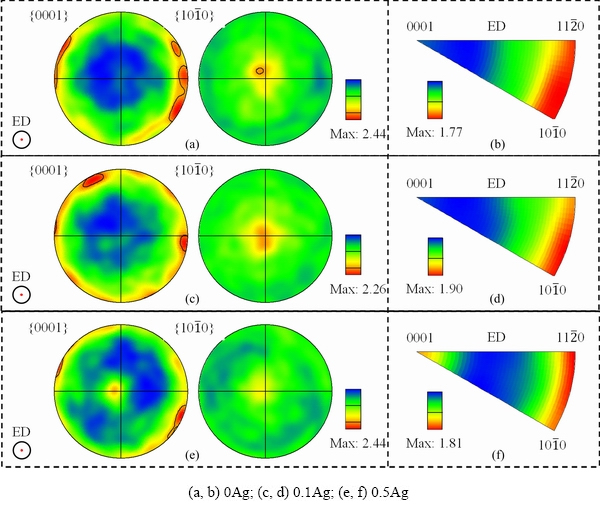
Fig. 4 PFs (a, c, e) and IPFs (b, d, f) of extruded alloys
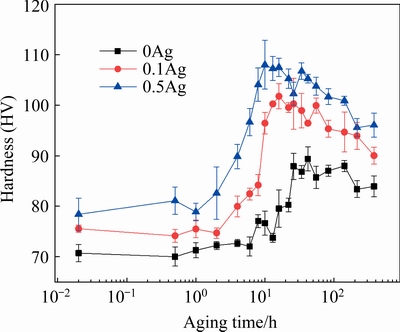
Fig. 5 Aging-hardening curves of alloys aged at 225 °C
Table 2 Results of hardness test of alloys
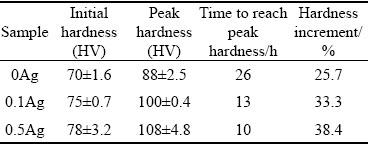
The HAADF-STEM images (Fig. 7) show that the precipitateswith a truncated-ellipse shape (shown by green arrows) are formed during the peak-aged period. The fringe spacing of the plate-shaped precipitates in 0Ag, 0.1Ag, and 0.5Ag samples is respectively 1.23, 1.14, and 1.21 nm, respectively,which is highly consistent with that of β′ precipitates [20-22]. As shown in Table 3, the volume fractionof the β′ precipitates in the three alloysmaintains consistent, which is 34.3%, 33.2%, and 37.4%, respectively. The length-to-width ratio of the precipitates is also consistent, about 1.87. However, the size of β′ precipitates decreases with the increase of the Ag content. The average length and width of β′ phases in the peak-aged 0Ag alloy are 29.13 and 15.59 nm, respectively. In contrast, the average length of the β′ precipitates in the 0.1Ag and 0.5Ag samples is respectively 25.46 and 18.12 nm, and the average width is 13.64 and 9.66 nm, respectively. The addition of Ag facilitates the formation of a high density of nano-sized β′ precipitates.
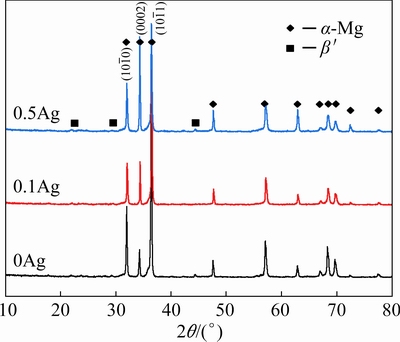
Fig. 6 XRD patterns of peak-aged alloys
The STEM mapping of the 0.5Ag sample was performed to reveal the elemental distribution in the Ag-containing Mg-Gd-Y-Zr alloys, as shown in Fig. 8. Similar to other Mg-Gd-Y-Zr alloys, Gd or Y elements are enriched in the β′ precipitates, and Zr elements are randomly distributed in the matrix and precipitates [7]. However, some β′ precipitates, locatedat A to B, are incorporated by Ag, Gd, and Y elements in the Ag-containing Mg-Gd-Y-Zralloys, as shown in Fig. 8(a).
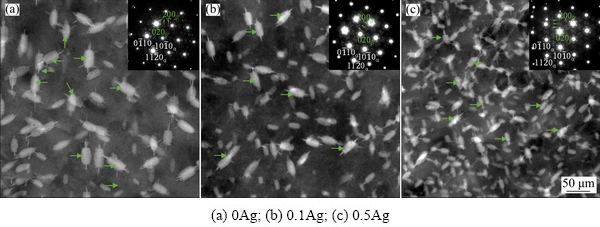
Fig. 7 HAADF-STEM images of peak-aged alloys with diffraction patterns (electron beam parallel to the [0001]α;β′ precipitates shown by green arrows)
Table 3 Quantitative measurements of β′ precipitates in peak-aged alloys

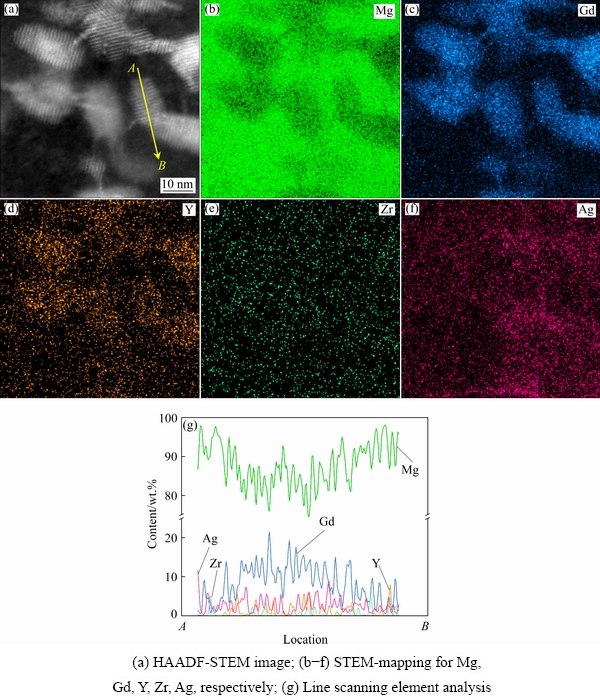
Fig. 8 Microstructures of 0.5Ag alloy in peak-aged condition
3.4 Mechanical properties at ambient temperature
The room-temperature engineering stress-strain curves and tensile properties of the extruded and peak-aged alloys with different Ag contents are presented in Fig. 9 and Table 4, respectively.
The YS of the 0.1Ag and 0.5Ag alloys in the extruded condition is respectively 191 and 198 MPa, which is higher than that of 0Ag (185 MPa). The UTS of the 0.1Ag and 0.5Ag samples is 10 and 26 MPa higher than that of the 0Ag alloy (283 MPa). The EL of the 0Ag, 0.1Ag, and 0.5Ag samples is respectively 24%, 23%, and 22%, which slightly decreases with the increase of the Ag content.
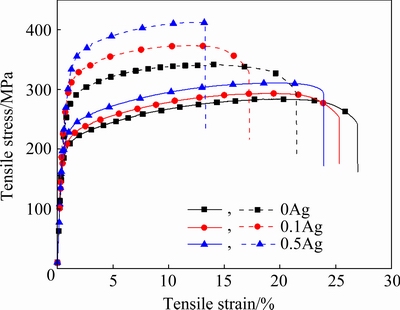
Fig. 9 Tensile stress-strain curves of extruded (E, solid line) and peak-aged (T5, dash line) alloys at room temperature
Table 4 Tensile properties of alloys at room temperature
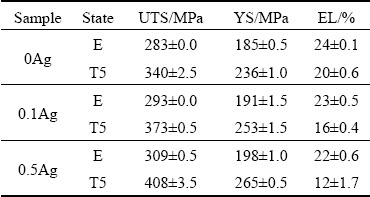
After peak-aging, the strength of these alloys is obviously improved, and the increment of strength increases with the increase of the Ag content. The YS and UTS of the 0Ag alloy increase to 236 and 340 MPa, respectively. Compared with the extruded state, the YS and UTS of the 0.1Ag sample are 253 and 373 MPa, respectively. The YS and UTS of the 0.5Ag alloy are 265 and 408 MPa, which increase by 67 and 99 MPa, respectively. Besides, the EL of the 0Ag, 0.1Ag, and 0.5Ag samples significantly decreases to 20%, 16%, and 12%, after peak-aging, respectively.
4 Discussion
4.1 Effect of trace Ag on precipitationbehaviorsof Mg-Gd-Y-Zr alloy
This work aims to investigate the effects of the trace Ag element on the age-hardening response and mechanical properties of the Mg-Gd-Y-Zr alloys at ambient temperature. As shown in Fig. 5, the addition of Ag enhances the age-hardening response of the extruded alloys, which is consistent with higher contents of Ag alloys, resulting from the dense distribution of plate-like precipitates [23]. However, different from the fact that the alloy with higher contents of Ag simultaneously generates prismatic precipitates and basal precipitates in the peak-aged condition [8,24,25], the samples with less Ag additions just precipitate β′ phase in the prismatic planes without basal γ″ precipitates. In contrast, as indicated by the quantitative measurements in Table 3, the alloys containing Ag element produce a high number density of β′ precipitates, and their size decreases with the increase of the Ag content, which results in the higher hardness of the extruded alloys after peak aging. It is observed that the Ag element is enriched in some β′ precipitates except Gd and Y (Fig. 8(g)).Considering that the atomic radius of Gd (0.179 nm) is larger than that of Mg (0.16 nm) while the atomic radius of Ag (0.144 nm) is smaller than that of Mg[8], the Gd and Ag atoms tend to co-segregate to minimize elastic strain in the matrix. The Ag-rich clusters are formed in the Ag-containing Mg-Gd-Zr alloys, which are considered as the heterogeneous nucleation sites for the formation of precipitates. ZHANGet al [24] and NIE et al [26] proved that the Ag clusters are formed in the Mg-Gd-Zr-Ag alloy by heat treatment, which play a vital role in the heterogeneous nucleation. Therefore, the trace Ag improves the nucleation rate and achieves a higher number density of precipitates, which is also found in the Mg alloys and other alloys [27-29]. Finally, the Ag-rich clusters as the precursors of the precipitates may be formed during the incubation period, accelerate the nucleation of precipitates, and lead to higher hardness and shorter peak-aging time.
4.2 Effect of precipitateson mechanical properties of Mg-Gd-Y-Zr alloy
Based on the data in Table 4, the YS of the 0Ag, 0.1Ag, and 0.5Ag samples increases respectively by 51, 62, and 67 MPa after peak-aging, respectively, and the increment of UTS in three samples is 57, 80, and 99 MPa, respectively. The aged Ag-containing alloy has higher increments of YS and UTS, which is in good accordance with the aging responses shown in Fig. 5. The average grain size does not show any change during the aging period[30], and the contribution of the grain size to the YS is not changed. After peak aging, β′ phase is the main precipitate and isdensely distributed in the three alloys, and the precipitation strengthening is the main effective factor to obtain higher strength increments with higher Ag contents. According to Ref. [31], the CRSS increments produced by the prismatic plates increase substantially with the increase of the plate aspect ratio. For a given distribution of the precipitate plates, the effective planar interplate spacing decreases with the increase of the plate aspect ratio. As shown by the quantitative measurements in Table 3, the size of β′ precipitates decreases, the ratio of length to width is equal to 1.87, and the volume fraction of the phase maintains almost unchanged with the increase of the Ag content. Therefore, the alloys containing higher Ag contents comprise higher strength, which is due to the fact that nano-sized β′ phase with a high density can effectively block dislocation slip. The decrease of the EL is associated with the increase of the YS in the peak-aged alloys, which is a normal phenomenon of the materials. The grain boundaries of the peak-aged alloys are decorated by β′ precipitates. These particles reduce the cohesion of the grain boundaries, and the interiors of the grains in the peak-aged condition are relatively strong, so the micro-cracks are prone to propagate along the grain boundaries [7]. Furthermore, with the increase of the Ag content, very small inter-precipitate distance of the precipitates significantly hinders dislocation slip and deformation twinning, which results in poor plasticity [32,33].
5 Conclusions
(1) The unusual texture (<0001>//extrusion direction) forms in the extruded Mg-Gd-Y-Zr alloys with Ag content increasing from 0 to 0.5 wt.%.
(2) During aging periods, the trace Ag addition does not produce new precipitates, just accelerates aging kinetics, refines β′ precipitates, and the number density is increased by Ag-clusters.
(3) The Mg-Gd-Y-Zr alloy containing 0.5 wt.% Ag shows the best comprehensive properties (408 MPa of ultimate tensile strength, 265 MPa of yield strength, and 12.9% of elongation to failure) after peak-aging.
Acknowledgments
The authors are grateful for the financial supports from the National Natural Science Foundation of China (Nos. 51574291, 51874367).
References
[1] DING Zhi-bing, ZHAO Yu-hong, LU Ruo-peng, YUAN Mei-ni, WANG Zhi-jun, LI Hui-jun, HOU Hua. Effect of Zn addition on microstructure and mechanical properties of cast Mg-Gd-Y-Zr alloys [J]. Transactions of Nonferrous Metals Society of China, 2019, 29: 722-734.
[2] YOU Chao, LIU Chu-ming, WAN Ying-chun, TANG Bei, WANG Bi-zheng, GAO Yong-hao, HAN Xiu-zhu. Dislocations-induced precipitates and their effect on mechanical properties of Mg-Gd-Y-Zr alloy [J]. Journal of Magnesium and Alloys, 2019, 7: 414-418.
[3] LIU Hong, GAO Yan, LIU J Z, ZHU Yu-man, WANG Yun-zhi, NIE Jian-feng. A simulation study of the shape of β′ precipitates in Mg-Y and Mg-Gd alloys [J]. ActaMaterialia, 2013, 61: 453-466.
[4] SOLOMON E L S, NATARAJAN A R, ROY A M, SUNDARARAGHAVAN V, VEN V D, MARQUIS E. Stability and strain-driven evolution of β′ precipitate in Mg-Y alloys [J]. ActaMaterialia, 2018, 166: 148-157.
[5] LIU Xian-bin, CHEN Rong-shi, HAN En-hou. Effects of ageing treatment on microstructures and properties of Mg-Gd-Y-Zr alloys with and without Zn additions [J]. Journal of Alloys and Compounds, 2008, 465: 232-238.
[6] GAO Xiang, NIE Jian-feng. Enhanced precipitation-hardening in Mg-Gd alloys containing Ag and Zn [J]. ScriptaMaterialia, 2008, 58: 619-622.
[7] ZHANG Yu, RONG Wei, WU Yu-juan, PENG Li-ming, NIE Jian-feng, BIRBILIS N. A comparative study of the role of Ag in microstructures and mechanical properties of Mg-Gd and Mg-Y alloys [J]. Materials Science and Engineering A, 2018, 731: 609-622.
[8] ZHANG Yu, ZHU Yu-man, RONG Wei, WU Yu-juan, PENG Li-ming, NIE Jian-feng, BIRBILIS N. On the precipitation in an Ag-containing Mg-Gd-Zralloy [J]. Metallurgical and Materials Transactions A, 2018, 49: 673-694.
[9] SUN Jia-peng, XU Bing-qian, YANG Zhen-quan, ZHOU Hao, HAN Jing, WU Yu-na, SONG Dan, YUAN Yu-chun, ZHUO Xio-ru, LIU Huan, MA Ai-bin. Achieving excellent ductility in high-strength Mg-10.6Gd-2Ag alloy via equal channel angular pressing [J]. Journal of Alloys and Compounds, 2019, 817: 1-7.
[10] LI Rong-guang, NIE Jian-feng, HUANG Guang-jie, LIU Qing. Development of high-strength magnesium alloys via combined processes of extrusion, rolling and ageing [J]. ScriptaMaterialia, 2011, 64: 950-953.
[11] HUANG Cen, LIU Chu-ming, WANG Bi-zheng. Microstructures and tensile properties of Mg-6Gd-3Y-1.4Zn-0.4Zr alloys [J]. Materials Science Forum, 2016, 849: 148-153.
[12] HUANG Cen, LIU Chu-ming, JIANG Shu-nong, WAN Ying-chun. Enhanced age-hardening response and mechanical properties of the Mg-Gd-Y-Zn-Zr alloy by trace Ag addition [J]. Journal of Alloys and Compounds, 2021, 874: 1-13.
[13] WANG Zhao-hui, DU Wen-bo, WANG Xu-dong, LIU Ke, LI Shu-bo. Microstructure evolution of Mg-9Gd-2Er-0.4Zr alloy during solid solution treatment [J]. Transactions of Nonferrous Metals Society of China, 2013, 23: 593-598.
[14] NAJAFI S, MAHMUDI R. Enhanced microstructural stability and mechanical properties of the Ag-containing Mg-Gd-Y alloys [J]. Journal of Magnesium and Alloys, 2020, 8: 1109-1119.
[15] ALIZADEH R, MAHMUDI R, NGAN A H W, LANGDON T G. An unusual extrusion texture in Mg-Gd-Y-Zr alloys [J]. Advanced Engineering Materials, 2016, 18: 1044-1049.
[16] ROBSON J D, TWIER A M, LORIMER G W, ROGERS P. Effect of extrusion conditions on microstructure, texture, and yield asymmetry in Mg-6Y-7Gd-0.5wt.%Zr alloy [J]. Materials Science and Engineering A, 2011, 528: 7247-7256.
[17] ZHANG Yu, RONG Wei, WU Yu-juan, PENG Li-ming. Tuning texture and precipitation using Y/Gd atomic ratio in iso-concentration Mg-Y-Gd-Ag-Zr extruded alloys [J]. Materials Characterization, 2020, 167: 1-9.
[18] JIANG Ming-guang, XU Chao, YAN Hong, FAN Guo-hua, NAKATA T, LAO Chang-shi, CHEN Rong-shi, KAMADO S, HAN En-hou, LU Bing-heng. Unveiling the formation of basal texture variations based on twinning and dynamic recrystallization in AZ31 magnesium alloy during extrusion [J]. ActaMaterialia, 2018, 157: 53-71.
[19] CHAO Hong-ying, YANG Yu, WANG Xin, WANG Er-de. Effect of grain size distribution and texture on the cold extrusion behavior and mechanical properties of AZ31 Mg alloy [J]. Materials Science and Engineering A, 2011, 528: 3428-3434.
[20] ZHANG Fan, WANG Ya-fei, DUAN Yun-biao, WANG Kai-jun, WANG Yu-tian, ZHANG Wei-jun, HU Jin. Precipitation processes during the peak-aged and over-aged stages in an Mg-Gd-Y-Zr alloy [J]. Journal of Alloys and Compounds, 2019, 788: 541-548.
[21] ZHENG Jing-xu, LI Zhi, TAN Li-da, XU Xue-song, LUO Rui-chun, CHEN Bin. Precipitation in Mg-Gd-Y-Zralloy: Atomic-scale insights into structures and transformations [J]. Materials Characterization, 2016, 117: 76-83.
[22] PENG Chong-hao, LI De-jiang, ZENG Xiao-qin, DING Wen-jiang. First principles investigation of β′-short and β′-long in Mg-Gd alloy [J]. Journal of Alloys and Compounds, 2016, 671: 177-183.
[23] CUI Xiao-fei, FU Wei, FANG Da-qing, BI Guang-li, REN Zi-jun, GUO Sheng-wu, LI Su-zhi, DING Xiang-dong, SUN Jun. Mechanical properties and deformation mechanisms of a novel fine-grained Mg-Gd-Y-Ag-Zr-Ce alloy with high strength-ductility synergy [J]. Journal of Materials Science and Technology, 2021, 66: 64-73.
[24] ZHANG Yu, ALAM T, GWALANI B, RONG Wei, BANERJEE R, PENG Li-ming, NIE Jian-feng, BIRBILIS N. On the role of Ag in enhanced age hardening kinetics of Mg-Gd-Ag-Zr alloys [J]. Philosophical Magazine Letters, 2016, 96: 1-8.
[25] YAMADA K, HOSHIKAWA H, MAKI S, OZAKI T, KUROKI Y, KAMADO S, KOJIMA Y. Enhanced age-hardening and formation of plate precipitates in Mg-Gd-Ag alloys [J]. ScriptaMaterialia, 2009, 61: 636-639.
[26] NIE Jian-feng, MUDDLE B C, AARONSON H I, RINGER S P, HIRTH J P. On the roles of clusters during intragranular nucleation in the absence of static defects [J]. Metallurgical and Materials Transactions A, 2002, 33: 1649-1658.
[27] MIAO Jia-shi, SUN Wei-hua, KLARNER A D, LUO A A. Interphase boundary segregation of silver and enhanced precipitation of Mg17Al12phase in a Mg-Al-Sn-Ag alloy [J]. ScriptaMaterialia, 2018, 154: 192-196.
[28] WENG Yao-yao, DING Li-peng, ZHANG Ze-zhong, JIA Zhi-hong, WEN Bo-yang, LIU Ying-ying, MURAISHI S, LI Yan-jun, LIU Qing. Effect of Ag addition on the precipitation evolution and interfacial segregation for Al-Mg-Si alloy[J]. ActaMaterialia, 2019, 180: 301-316.
[29] QIAN Feng, JIN Shen-bao, SHA Gang, LI Yan-jun. Enhanced dispersoid precipitation and dispersion strengthening in an Al alloy by microalloying with Cd [J]. ActaMaterialia, 2018, 157: 114-125.
[30] ZHANG Yu, RONG Wei, WU Yu-juan, PENG Li-ming. Achieving ultra-high strength in Mg-Gd-Ag-Zr wrought alloy via bimodal-grained structure and enhanced precipitation [J]. Journal of Materials Science and Technology, 2020, 54: 160-170.
[31] NIE Jian-feng. Effects of precipitate shape and orientation on dispersion strengthening in magnesium alloys [J]. ScriptaMaterialia, 2003, 48: 1009-1015.
[32] LIN Dan, WANG Lei, LIU Yang, CUI Jian-zhong, LE Qi-chi. Effects of plastic deformation on precipitation behavior and tensile fracture behavior of Mg-Gd-Y-Zr alloy [J]. Transactions of Nonferrous Metals Society of China, 2011, 21: 2160-2167.
[33] YU Zi-jian, XU Xi, MANSOOR A, DU Bao-tian, SHI Kang, LIU Ke, LI Shu-bo, DU Wen-bo. Precipitate characteristics and their effects on the mechanical properties of as-extruded Mg-Gd-Li-Y-Zn alloy [J]. Journal of Materials Science and Technology, 2021, 88: 21-35.
微量Ag对挤压态Mg-Gd-Y-Zr合金析出行为和力学性能的影响
张冬冬1,刘楚明1, 2,蒋树农1,万迎春1, 3,陈志永1
1. 中南大学 材料科学与工程学院,长沙 410083;
2. 湖南科技大学 材料科学与工程学院,湘潭411201;
3. 中南大学 轻合金研究院,长沙410083
摘 要:通过拉伸试验、X射线衍射、扫描电镜、电子背散射衍射和扫描透射电镜等手段研究微量Ag元素对Mg-7.5Gd-1.5Y-0.4Zr(质量分数,%)合金析出行为和力学性能的影响。结果表明,含0.5% Ag(质量分数)的Mg-Gd-Y-Zr合金挤压后存在<0001>//挤压方向的织构组分。在225 °C时效过程中,添加Ag元素不会形成新相,而是通过Ag偏聚加速析出动力学,细化β′相并增加其密度。此外,含0.5 wt.% Ag的Mg-Gd-Y-Zr合金峰时效后具有最好的强度和塑性协同性(抗拉强度为408 MPa;屈服强度为265 MPa;伸长率为12.9%)。
关键词:微量Ag;Mg-Gd-Y-Zr合金;β′相;析出强化
(Edited by Wei-ping CHEN)
1003-6326/
2021 The Nonferrous Metals Society of China. Published by Elsevier Ltd & Science Press
Abstract:The effects of trace Ag element on the precipitation behaviors and mechanical properties of the Mg-7.5Gd-1.5Y-0.4Zr (wt.%) alloy by means of tensile test, X-ray diffractometry, scanning electron microscopy, electron backscattered diffractometry, and scanning transmission electron microscopy. There is an unusual texture (<0001>//extrusion direction) in the extruded Mg-Gd-Y-Zr alloys containing 0.5 wt.% Ag. During the aging periods at 225 °C, the addition of the trace Ag does not form new precipitates, just accelerates aging kinetics, and refines β′ precipitates, thereby increasing the number density of the β′ precipitates by Ag-clusters. Moreover, the Mg-Gd-Y-Zr alloy containing 0.5 wt.% Ag shows the most excellent synergy of strength and plasticity (408 MPa of ultimate tensile strength, 265 MPa of yield strength, and 12.9% of elongation to failure) after peak-aging.