铝电解惰性阳极材料技术研究进展
周科朝,何 勇,李志友,沈 廷,张 雷
(中南大学 粉末冶金国家重点实验室,长沙 410083)
摘 要:
惰性阳极铝电解技术是未来铝工业持续低碳化发展并实现碳中和目标的关键技术,近年来,惰性阳极材料的研究取得了长足进展,为其工业化应用的突破性进展创造了条件。本文通过综述铝电解惰性阳极材料近期研究进展,重点关注合金阳极表面耐蚀层的生长机制、金属陶瓷组成与结构优化及阳极材料综合性能提升等研究方向,系统对比了现有惰性阳极材料的导电性及耐蚀性能,并对其未来发展趋势做出展望。
关键词:
惰性阳极;铝电解;金属阳极;金属陶瓷;
文章编号:1004-0609(2021)-11-3010-14 中图分类号:TF111.52 文献标志码:A
引文格式:周科朝,何 勇,李志友, 等. 铝电解惰性阳极材料技术研究进展[J]. 中国有色金属学报, 2021, 31(11): 3010-3023. DOI: 10.11817/j.ysxb.1004.0609.2021-42011
ZHOU Ke-chao, HE Yong, LI Zhi-you, et al. Research progress of inert anode materials and technology for aluminium electrolysis[J]. The Chinese Journal of Nonferrous Metals, 2021, 31(11): 3010-3023. DOI: 10.11817/j.ysxb.1004.0609.2021-42011
铝是第二大金属材料,我国是世界上最大的铝产品生产国与消费国。2020年我国原铝产量3708万t,占全球产量的56.8%; 消费3825万t,约占全球消费量的64%;2020年我国铝冶炼行业的碳排放总量约为5亿t,占有色金属行业总排放量的76%,占全国碳排放总量的4.6 %。
目前,国际通用的铝电解技术采用碳素阳极在高温熔盐中把氧化铝还原成原铝,同时排放CO2,吨铝电耗约1.3万度,消耗碳素材料约0.4 t。惰性阳极铝电解技术生产原铝的过程中释放氧气,没有CO2、CO等温室气体的排放;如该技术实现全国推广应用,按照2020年我国原铝产量规模折算,每年可减少碳排放量约6670万t,节省优质炭素资源约1480万t,同时产生氧气3320万t。因此,惰性阳极铝电解技术是彻底变革铝电解行业的颠覆性技术,是实现碳中和目标的核心战略性技术。
惰性阳极材料是惰性电极铝电解技术的核心之一,其材料类型主要涵盖陶瓷、合金及金属陶瓷三个体系,近年来,该领域的研究取得了长足的进步,已逐步从实验室研究向工业应用研究拓展,尽管还无法全面满足规模铝电解应用的需要,但已有成果的积累将为该技术的工程应用突破不断提供有力的支撑。本文通过梳理2010年至2020年期间,惰性阳极材料的研究进展情况,对比评价各材料体系的导电性能和耐腐蚀性,以期全面展示惰性阳极的研究现况和发展趋势。
1 惰性阳极材料的研究进展
1.1 合金体系
金属及合金类惰性阳极材料具有良好的综合力学性能、优异的导电性能和良好的抗热震能力,且易于加工和导电连接,而成为惰性阳极材料的研发重点,但金属基合金材料在700 ℃以上的耐熔盐电解腐蚀性不足限制了其电解应用进程。因而,有关合金阳极材料的研究主要集中在Cu-Al、Cu-Ni-Fe及Ni-Fe等耐蚀体系上,其研究内容主要包括中低温环境中合金材料的氧化和腐蚀机理、表面耐蚀氧化层的形成机制、耐蚀结构的保持方法及电腐蚀行为等方面。
1.1.1 Cu-Al合金
Cu-Al合金可在冰晶石熔体中形成含Al氧化层,并与熔体中的Al2O3发生溶解和再生的反应而形成独特的氧化层修复效应,据此可有效延长阳极的使用寿命,这一特点使其成为业界的研究热点。研究发现,冰晶石熔体中的Al2O3浓度对主成分为Cu2O和CuAlO2的表面氧化层的溶解-再生平衡具有显著影响,增大Al2O3浓度有利于该类型氧化层的稳定保持和耐蚀性能的提高[1-3];PADAMATA等[4-5]研究含Al2O3颗粒的饱和电解质体系对Cu-10Al阳极的电解行为发现,阳极的极限电流密度、熔体与电极表面间的传质系数均会随着悬浊液中颗粒体积分数的增加而大幅降低,并指出Cu-10Al阳极在CR=1.4,Al2O3颗粒体积分数为0.09的悬浊体系中电解反应稳定,阳极电位在2.5~3.2 V之间,电流效率达84.4%,并获得了纯度为99.4%的原铝。还有研究[6]表明,Cu的早期溶解是造成Cu-Al合金电极腐蚀的重要原因,因此通过合金元素优化来降低阳极腐蚀速率也是该类研究的重要的方向,添加微量Ni、Fe,可提升电极表面CuAlO2氧化层的成膜速度;GLUCINA等[7]发现90.25Cu-9.39Al- 0.02Ni-0.10Fe合金阳极经970 ℃、8 h电解实验后,可在阳极表面获得厚度约为500 μm的稳定的富Al氧化层,且氧化层中Cu的含量较Cu-10Al阳极有所降低。
1.1.2 Cu-Ni-Fe合金
Cu-Ni-Fe合金的表面氧化层中含有NiFe2O4、NiO等在冰晶石熔体中具有较强耐腐蚀性能的成分,使该类合金材料具有较好的抗氧化、抗氟化能力。研究发现,冰晶石熔体中Cu-Ni-Fe合金的氧化包含两个过程:一方面,O向电极内扩散与Ni、Fe结合生成NiFe2O4;同时,电极内的Cu向外扩散形成CuO并向熔体中溶解,造成阳极的质量损失[8];因此,以适当的方法促进NiFe2O4氧化层的形成和抑制Cu的向外扩散,均可起到提高阳极耐蚀性能的作用。
GALLINO等[9]通过均匀化热处理提高了Cu-Ni-Fe浇铸合金的成分均匀性,增大了NiFe2O4耐蚀层的成膜速率,从而使Cu-Ni-Fe合金阳极表面的熔体侵蚀区厚度较均匀化处理前降低了1/3;JUCKEN等[10-11]对65Cu-20Ni-15Fe合金进行了预氧化处理,在合金表面获得了NiFe2O4预氧化层,该电极在700 ℃、0.5 A/cm2电流密度下持续电解 20 h后,阳极的合金/氧化物界面上仅有少量FeF3和NiF2生成,熔体中的杂质含量大幅降低,原铝纯度达99.6 %,阳极腐蚀率仅0.4 cm/a;LIU等[8]发现,掺杂La元素能够抑制Cu原子的向外迁移过程,从而促进NiFe2O4氧化层的生成,其中La掺杂量为0.5%(质量分数)的52Cu-30Ni-18Fe惰性阳极在电解试验后其表面形成了超过100 μm厚的NiFe2O4耐蚀层(见图1),经测试850℃下阳极腐蚀率为1.8~1.9 cm/a。
1.1.3 Ni-Fe合金
Ni-Fe合金具有较强的高温抗氧化性,相较于Cu基合金也具有更好的熔体稳定性。研究认为,Fe-Ni合金的电解腐蚀过程可分为几个阶段:首先,Fe离子在电极表面聚集并达到临界浓度,形成初始的钝化膜;随后,熔盐界面处的FeO进一步被氧化形成Fe2O3层;最后,已形成的Fe2O3氧化膜在气泡的冲击下剥离,露出表面的部分金属相,阳极也在这一过程中不断被侵蚀[12-13]。因此,Ni-Fe合金阳极材料的研究重点是从组份和结构上减少Fe2O3的生成、提高耐蚀层的结合强度和稳定性,以提高表面氧化膜的耐腐蚀性能。
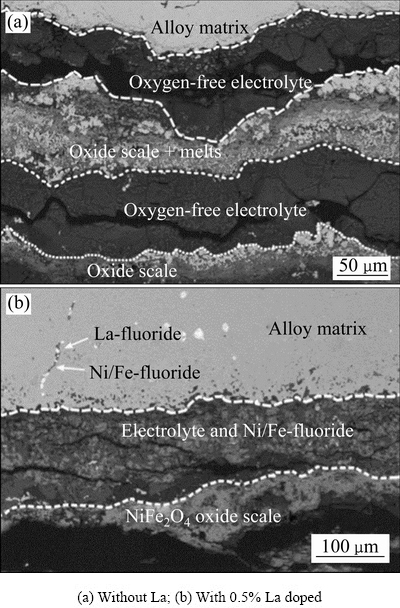
图1 52Cu-30Ni-18Fe合金阳极电解试验后腐蚀层的SEM像(850 ℃, 0.75 A/cm2, 24 h)[8]
Fig. 1 Cross-sectional SEM images of 52Cu-30Ni-18Fe anode after electrolysis (850 ℃, 0.75 A/cm2, 24 h)
研究发现,合适配比的Ni-Fe合金可以在表面获得含Fe2O3和NiFe2O4的复合氧化层结构,其比单纯的Fe2O3层更能抵御气泡的冲蚀,HUANG等[14]和CHAPMAN等[15]都对Fe-Ni合金阳极的氧化过程进行了研究,认为合金的氧化动力学遵循抛物线规律,镍含量在50%~60%之间的预氧化Ni-Fe合金阳极的氧化层中NiFe2O4的相对含量较高,使其具有更高的耐腐蚀能力。此外,添加Cu、Al等活泼金属,可在耐蚀层与合金间生成结合力强的过渡层,增加NiFe2O4氧化物的结合强度,进而提高材料的抗腐蚀性能[16-17];另一方面,一些元素能抑制Fe离子向表面聚集,从而减少Fe2O3的产生,如CHAPMAN等[18]发现Co含量为10%~30%的Ni-Fe-Co合金表面形成的氧化层中Fe2O3的含量很少;REZA等[19]将预氧化处理后的Ni-11Fe-10Cu- 15Cr-6Al合金阳极置于930 ℃的冰晶石熔体中进行了100 h的电解试验,发现氧化层中的主要成分为Al2O3、Cr2O3以及NiO,其中的Cu、Fe总含量仅为0.68%(质量分数)。
1.2 氧化物陶瓷体系
SnO2和NiFe2O4类陶瓷在冰晶石熔体中溶解度小,电化学稳定性好,是备受关注的惰性阳极材料体系之一。然而,氧化物陶瓷的导电能力不足,限制了该类材料的应用,SnO2陶瓷在960 ℃下的电阻率为0.208 Ω·cm,NiFe2O4在950 ℃下电导率仅有0.57 S/cm,而工业用预焙碳素阳极的电导率却可达到200 S/cm[20]。此外,陶瓷体系还存在抗热震性差、力学性能和焊接性能不佳的问题,使得氧化物陶瓷阳极的工业应用前景受限。
1.2.1 SnO2基陶瓷
SnO2在1035 ℃的Na3AlF6熔体中的溶解度只有0.08%(质量分数)[21],而且,向SnO2陶瓷中添加Sb2O3、CuO、ZnO、Fe2O3、CeO2和In2O3等氧化物可改善SnO2基陶瓷阳极的高温导电性能和材料强度。ADLER[22]向SnO2中添加了1%(质量分数)的Sb2O3和2%(质量分数)的Fe2O3后,发现添加剂能够促进陶瓷材料的烧结过程,使陶瓷烧结坯密度提升了50%;添加了2%Sb2O3和2%CuO(质量分数)的SnO2基陶瓷材料的电导率可比纯SnO2陶瓷高出4~6倍;VIRGIL[23]使用SnO2-Sb2O3-CuO 陶瓷阳极,在0.7~0.8 A/cm2的电流密度下进行了940~960 ℃的电解试验,发现使用SnO2基陶瓷阳极时最小极间距可缩短至2~3 cm,从而使电流效率较相同测试条件下使用碳素阳极时提升了91.5%。尽管SnO2的溶解度较低,但在电解过程中Sn+离子容易被还原成金属,导致原铝纯度控制困难。
1.2.2 NiFe2O4基陶瓷
1990年,AUGUSTIN等[24]证实了铁酸镍能有效抵抗高温氧化及冰晶石熔体的侵蚀,并指出NiFe2O4可做为耐腐蚀阳极材料。NiFe2O4的尖晶石型晶体结构具有离子键键能高、结构稳定且热膨胀系数小的特点,具有良好的抗冰晶石熔体腐蚀性能。MEYERA等[25]对比了同为尖晶石晶体构型的NiFe2O4和Fe3O4在冰晶石熔体体系中的化学稳定性,发现熔体中的Al3+更易向Fe3O4中扩散,取代Fe3+离子并形成FeAl2O4;而在NiFe2O4中,由于Ni2+的存在占据了更大的空位体积,使Al3+的扩散难度增大,因此在高温冰晶石熔盐中的化学稳定性更好。
当铝电解过程中产生的气泡无法及时排出并附着在电极表面时,会造成阳极表面局部电位增加,产生所谓的“阳极效应”,不仅破坏电解过程的稳定性,还会加速阳极的消耗。NiFe2O4阳极表面气泡的析出过程包括气泡成核、长大、合并、再次生长、迁移和逃逸几个阶段[26],向NiFe2O4陶瓷中添加V2O5、MnO2或TiO2等氧化物助烧剂,能够提高烧结陶瓷的致密度和表面光洁度,使表面气泡析出速度更快,形成气泡尺寸更小,分布也更加均匀,从而有效降低阳极过电位和电极腐蚀速率;WANG等[27]对TiO2掺杂的NiFe2O4陶瓷基惰性阳极的电解行为进行了研究,并指出含有1.0%TiO2 (质量分数)的NiFe2O4陶瓷惰性阳极在0.6~1.2 A/cm2的电流密度下电解时,电极过电位为0.17~ 0.34 V,比碳素阳极低45%。
1.3 金属陶瓷体系
金属陶瓷阳极材料是一种由合金和氧化物陶瓷构成的复合材料,其中以镍铁尖晶石为陶瓷相的金属陶瓷阳极材料由Alcoa公司[28-29]最先提出,因其同时具备金属的导电能力和陶瓷的冰晶石熔体稳定性,自诞生以来一直被认为是一种极具工程应用潜力的惰性阳极材料。
1.3.1 M/NiFe2O4金属陶瓷
M/NiFe2O4是目前发展较为成熟的金属陶瓷惰性阳极材料体系,其中,金属相以Cu、Ni、Fe及其二元或三元合金为主,陶瓷相中则多采用NiO为添加剂。M/NiFe2O4金属陶瓷也具有形成表面致密耐蚀层的能力,现有研究表明,该耐蚀层是在金属相优先氧化、NiO等添加剂的相转变以及熔体中Al2O3在电极表面的沉积等现象的共同作用下形成的[30]。因此,通过合金相的组分设计、制备工艺的优化来提升金属陶瓷材料的耐蚀性能是近年来研究的重点方向。
Cu主要用于提升金属陶瓷材料电导率,但铜的初期氧化和溶解也是造成金属陶瓷腐蚀率增大的重要原因。为此,TAO等[31-32]制备了成分为Cu-10Cu2O/NiFe2O4-10NiO的金属陶瓷,发现掺杂Cu2O与合金阳极的预氧化处理具有相似的机制,能够在一定程度上降低Cu的早期侵蚀速率,从而延长惰性阳极的使用寿命。通常,采用合金作为金属相往往比使用纯Cu更能提高金属陶瓷阳极的耐腐蚀性能;研究发现,以Cu-Ni合金作为金属相时,金属陶瓷表面形成多种具有尖晶石结构的致密氧化,包括FeAl2O4、NiAl2O4和CuAl2O4等[33-34];张啸等[35]研究(Cu-20Ni)/(NiFe2O4-10NiO)金属陶瓷惰性阳极的电解腐蚀行为发现,该材料在熔体中同时存在着化学腐蚀和电化学腐蚀两种机制,当阳极电流密度逐渐增大时,化学腐蚀速率逐渐降低而电化学腐蚀逐渐上升,总的腐蚀速率则表现出先下降后上升的趋势,其中电流密度为0.8 A/cm2时腐蚀率最小,所得原铝中Cu、Fe、Ni的杂质总含量为0.24%(质量分数)。采用适当成分的Cu-Ni-Fe三元合金作为金属相时,金属相的氧化产物会与陶瓷相作用构成动态膜层结构,MEYER等[36]指出,在(Cu-Ni-Fe)/(NixFe3-xO4)金属陶瓷的电解腐蚀行为中,Fe有向陶瓷相中迁移的趋势,当NixFe3-xO4尖晶石的成分趋于x=0.90,镍铁含量达到热力学的稳定平衡;杨文杰[37]认为,14Fe-13Ni-13Cu/NiFe2O4 金属陶瓷电解腐蚀过程所形成的表面氧化腐蚀结构可分为三层(见图2),最外层为10 μm厚的电解质层,向内为50 μm厚的电解质氧化物混合层,再向内的10 μm厚度内,金属相被NiO层包覆,NiO包覆层可有效抵抗电解质的持续侵蚀,该金属陶瓷阳极经1000 h电解后,平均工作电压4.05 V,腐蚀率为0.99 cm/a,获得原铝杂质含量为0.509%。
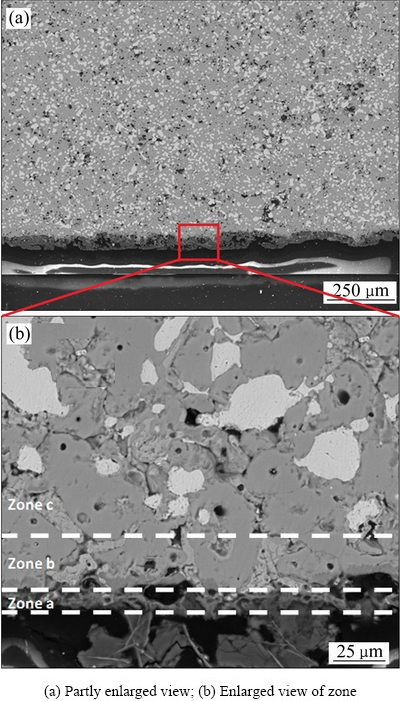
图2 14Fe-13Ni-13Cu/NiFe2O4金属陶瓷阳极电解试验后腐蚀层的SEM像(820 ℃, 0.5 A/cm2, 1000 h)[37]
Fig. 2 Cross-sectional SEM images of (14Fe-13Ni-13Cu)/ NiFe2O4 anode after electrolytic (820 ℃, 0.5 A/cm2, 1000 h)[37]
1.3.2 Cu/Cu2O金属陶瓷
Cu/Cu2O金属陶瓷是一种半导体元件材料,具有高温高电导率的优势,且金属相只含有Cu,获得原铝中的杂质较为单一。冯立超等[38-39]研究了Cu/Cu2O的高温导电机制,通过原位还原-热压烧结法制备出了孔隙率低于3%的Cu/Cu2O金属陶瓷,发现当Cu含量超过金属陶瓷的“导电渗流阈值”时,体系的导电行为由半导体向良导体转变,其中Cu含量为20%的金属陶瓷在950 ℃时的电导率达到了562 S/cm。FENG等[40]对Cu/Cu2O金属陶瓷惰性阳极在960 ℃的Na3AlF6-AlF2-Al2O3熔体中的高温腐蚀行为的研究发现,阳极表面形成的腐蚀层的主要成分是CuAlO2,并指出腐蚀层是在电解早期快速形成的,随着金属陶瓷中Cu含量的上升,阳极腐蚀率显著提高,其中Cu含量为25%(质量分数)的金属陶瓷阳极的腐蚀率在1.5~7.2 mg/(cm2·h)之间,获得的原铝中含有6.3%(质量分数)的铜。尽管导电性能较好,但Cu/Cu2O金属陶瓷的特殊之处在于,合金相中大量的Cu极易被熔体侵蚀,原铝中的含Cu量较高,目前,采用Cu/Cu2O金属陶瓷阳极只能进行含Cu铝合金的制备而难以获得纯度较高的原铝。
2 惰性阳极材料的性能差异
电解铝用阳极材料需要在800~960 ℃的冰晶石熔体中稳定长期使用,理想的惰性阳极材料应当满足以下要求[41-43]:1) 导电性能好,阳极电流密度为0.6~0.8 A/cm2时,工作电压稳定,电极过电位不超过0.5 V;2) 具有高化学稳定性和耐蚀性,能够抵抗高温电解质以及环境氧的腐蚀和电化学侵蚀,有生成稳定耐蚀层的能力,最大电流密度下电极腐蚀率应低于10 mm/a;3) 综合力学性能好,易加工,易更换,并需要具有良好的抗热冲击能力;4) 易与导电杆进行连接;5) 材料和制造成本低,制造工艺环境友好。
当前,惰性阳极材料尚无法全面满足上述要求,其中导电性和耐蚀性是影响阳极使用寿命的重要因素,一方面,提高材料的导电性可降低槽电压,降低能耗;另一方面,材料的耐腐蚀能力则直接决定了惰性阳极的消耗速度,以及获得原铝的纯度。因此,同时具有高电导率和低腐蚀率的特征是惰性阳极材料能够工程应用的前提。
通过综合近十年文献报道的部分惰性阳极的电解温度及其电导率数据,形成了惰性阳极材料电导率对比分布图(见图3),该图在全面展示多种惰性阳极材料的电导率特性的同时,可以发现合金阳极在导电性能方面优势显著,合金类阳极材料960 ℃时的电导率可达8000~20000 S/cm,而金属陶瓷的电导率处于10~90 S/cm之间,金属陶瓷材料电导率的最大值较纯NiFe2O4陶瓷提升了224倍。在金属陶瓷中,尽管金属相的添加能够有效的提高金属陶瓷的电导率,但基体陶瓷相的导电性能变化仍起决定作用。图4所示为惰性阳极材料的电导率随温度变化的趋势图。由图4可看出,随着电解温度的提高,金属的电导率下降明显,说明合金类阳极更适于在低温条件下工作;SnO2和NiFe2O4陶瓷具有半导体材料的导电性质,M/NiFe2O4金属陶瓷整体上也呈现出这种负温度系数电阻效应,因此,金属陶瓷在传统铝电解工艺条件下的电导率高于低温电解时的数值,这一特征使得金属陶瓷惰性阳极在直接替代传统Hall电解槽碳素阳极方面更具优势。
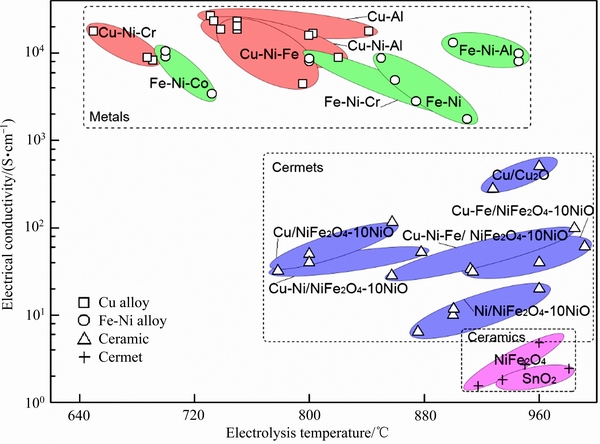
图3 惰性阳极材料电导率综合对比[3, 5-9, 12, 15, 19-20, 23, 25, 27, 30, 32, 34, 36-38, 44-50]
Fig. 3 Comparison of electrical conductivity of different inert anode materials[3, 5-9, 12, 15, 19-20, 23, 25, 27, 30, 32, 34, 36-38, 44-50]
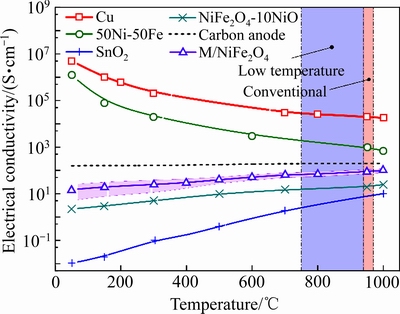
图4 惰性阳极材料的电导率随温度的变化趋势[20, 50]
Fig. 4 Variation trend of electrical conductivity of different materials with temperature[20, 50]
高温冰晶石熔体对阳极的侵蚀主要包括三个方面:一是高温环境下的新生氧的氧化;二是阳极表面物质向熔体中的溶解和化学腐蚀;三是电流作用下的电化学腐蚀。通过分析近十年文献报道中的部分惰性阳极的电解温度及其腐蚀率,形成了各类惰性阳极材料腐蚀率对比分布图(见图5)。分析图5数据发现,合金阳极的腐蚀率远高陶瓷及金属陶瓷阳极,平均值是纯陶瓷的200多倍;而金属陶瓷阳极很好的保留了陶瓷材料高耐蚀性的优点,其中部分Ni/NiFe2O4-10NiO和Cu-Ni-Fe/NiFe2O4-10NiO金属陶瓷在800~900 ℃下的腐蚀率可低于20 mm/a。合金阳极的腐蚀速率取决于Cu、Fe活性成分的氧化和侵蚀,生成氧化膜的速率以及结合强度;金属陶瓷在电解过程中的腐蚀速率,主要由金属相的高温氧化和电腐蚀,以及NiFe2O4基体陶瓷相的溶解两个过程决定,其中金属相会优先发生氧化和侵蚀,该过程在金属陶瓷的电腐蚀过程中起决定作用,且随着电解温度的提高,金属相的氧化及侵蚀速率提升。
综上所述可知,金属陶瓷类材料的耐蚀性优势显著,且性能调控手段方法丰富,性能提升空间较大;金属阳极的导电能力优异,但其高温耐腐蚀性能不足,很多合金体系仅在700 ℃以下电解时才具有低的腐蚀率。因而,金属陶瓷材料体系更具有应用推广前景,其研发需要以提高材料整体耐腐蚀性能为核心,从组分、结构、工艺等多角度出发,消除腐蚀率与电导率间的矛盾,逐步提升材料性能,以实现该材料体系的稳定电解应用。

图5 惰性阳极材料腐蚀率综合对比[4-11, 15, 17-23, 26-27, 29-30, 32-37, 40, 48-51]
Fig. 5 Comparison of corrosion rate of different inert anode materials[4-11, 15, 17-23, 26-27, 29-30, 32-37, 40, 48-51]
3 惰性阳极技术应用研究进展
3.1 国外专利进展
2010年至2021年期间,Elysis、Alcoa、Rusal、Rio Tinto等企业公开的与惰性阳极铝电解技术相关的美国、俄国、欧洲及其他国家专利有40余项(CNKI检索),其中2015以后公开的专利数量占总发明量的71%,国别上欧洲专利的数量最多,占比为41.1%(见图6)。惰性阳极技术专利涉及阳极材料、电连接、电极排布、电解槽结构、电解槽热防护、喂料系统、气体回收等诸多领域,有超过1/5的专利与惰性阳极材料相关,且多为合金和金属陶瓷体系。其中,早年的合金阳极以Cu、Fe合金为主,通过添加Ni、Al等元素进行成分优化,并以铸造或粉末冶金工艺完成制备,如CA2075892A、US5006209A公开的Cu-Ni合金阳极,EP1244826A、CA2393429A等专利所述的预氧化Ni-Fe合金阳极, 以及EP0783597A、US2007278107A、CA2524848A中的Fe-Cu-Ni合金阳极。金属陶瓷惰性阳极多采用NiFe2O4陶瓷为基体,通过粉末冶金工艺路线进行制备,如EP3161187B1、US20180073109A1及US20170130351A1等专利中,均对尖晶石基金属陶瓷的成分和组成进行了详细的优选。此外,一些特殊复合结构的惰性阳极也被公开,如美国专利US5725744公开的一种将惰性阳极与可润湿阴极相结合的竖式双结构电极、US6562224A中的一种具有氧化物陶瓷外壳结构的Ni-Fe基合金阳极多层结构电极等。从发展趋势上来看,国外惰性阳极材料的专利数量在近些年来呈逐渐上升的趋势,说明上述企业正加快惰性阳极技术开发和研究的进程。
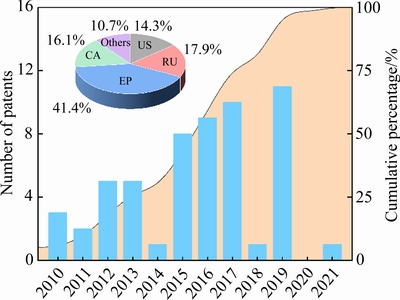
图6 2010~2021(6月)年惰性阳极技术海外专利数及国别比例
Fig. 6 Number and country ratio of overseas patents for inert anode technology, June in 2010-2021
3.2 惰性阳极铝电解工业化应用研究现状
近三年来,随着全球降碳减排的呼声不断提高,发达国家迅速加大了惰性阳极技术的投入,称之为“无碳铝电解技术”的惰性阳极铝电解工业化研究取得了突破性进展[52-57]。2018年5月,加拿大政府、美铝、力拓和苹果公司联合投资1.88亿加元成立了Elysis公司,开展金属陶瓷惰性阳极铝电解技术工业化研究,并声明将于2024年前建立起工业化级别的无碳铝生产路线;2019年12月,Elysis生产了第一批无碳铝,用于苹果手机外壳制备;2021年4月,Elysis公司宣布,将在加拿大魁北克Alma铝冶炼厂的450 kA电解槽末端安装工业惰性阳极电解槽原型,以证明该技术在工业运行环境中的有效性。与此同时,2021年4月,俄罗斯铝业集团宣布其140 kA新型惰性阳极电解槽实现了行业最低的碳排放,即每吨铝的二氧化碳当量低于0.01 t,该电解槽产能达1 t/d,铝纯度大于99%。上述进展显示,欧美国家在惰性阳极铝电解技术的工程化应用方面已取得突破性进展,并对惰性阳极铝电解核心技术、关键工艺和成套装备高度保密,构筑了系统的技术壁垒,其战略重要性可见一斑。
我国的惰性阳极研发起步于1990年代,基本与发达国家同步发展。迄今为止,包括中国铝业、中南大学、东北大学、郑州大学、贵州大学和昆明理工大学在内的诸多企业和高校均开展了惰性阳极技术的研究[20, 35, 50-52]。如2011年,中南大学与中国铝业集团联合开展了金属陶瓷惰性阳极20 kA铝电解工程化试验[20, 37, 50],这是国内首次中长期惰性阳极铝电解试验,系统地考察了金属陶瓷惰性阳极规模铝电解的可行性,获得了详实可靠的技术参数和丰富的操作经验。目前,我国惰性阳极技术仍处于工业化应用开发的起步阶段,与发达国家的差距逐渐拉大,需进一步加强研发力度和规模。
表1 近十年间公开的部分海外惰性阳极技术专利
Table 1 Some overseas patents on inert anode technology disclosed in last 10 years
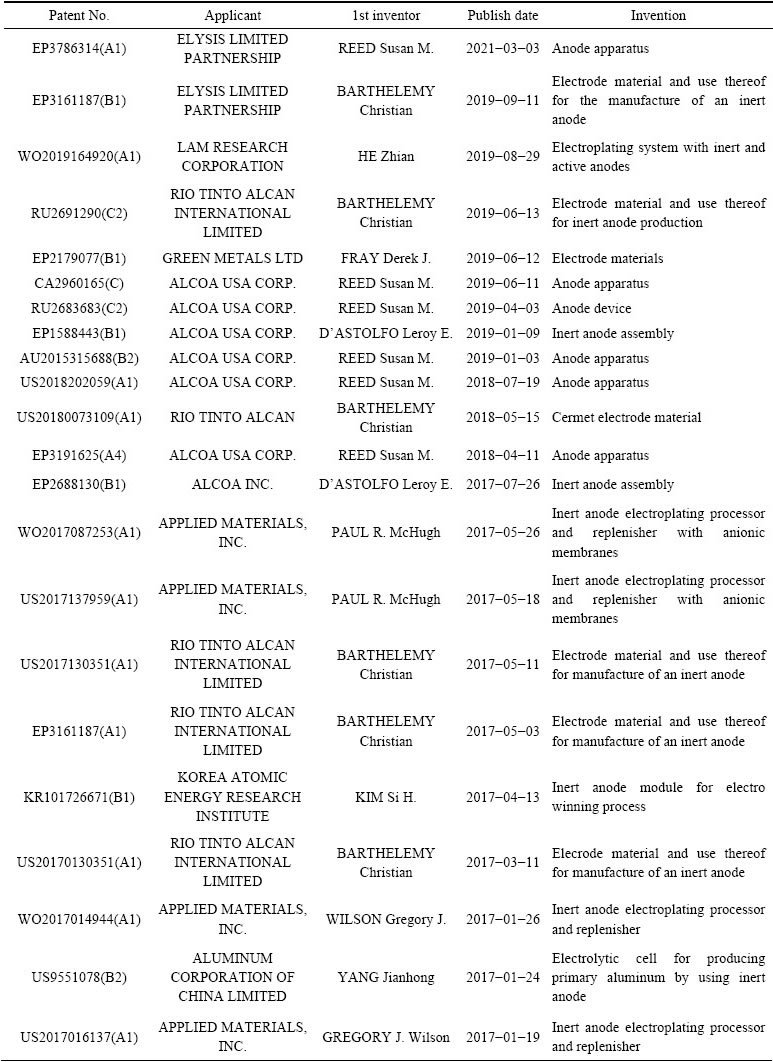
(Continued)
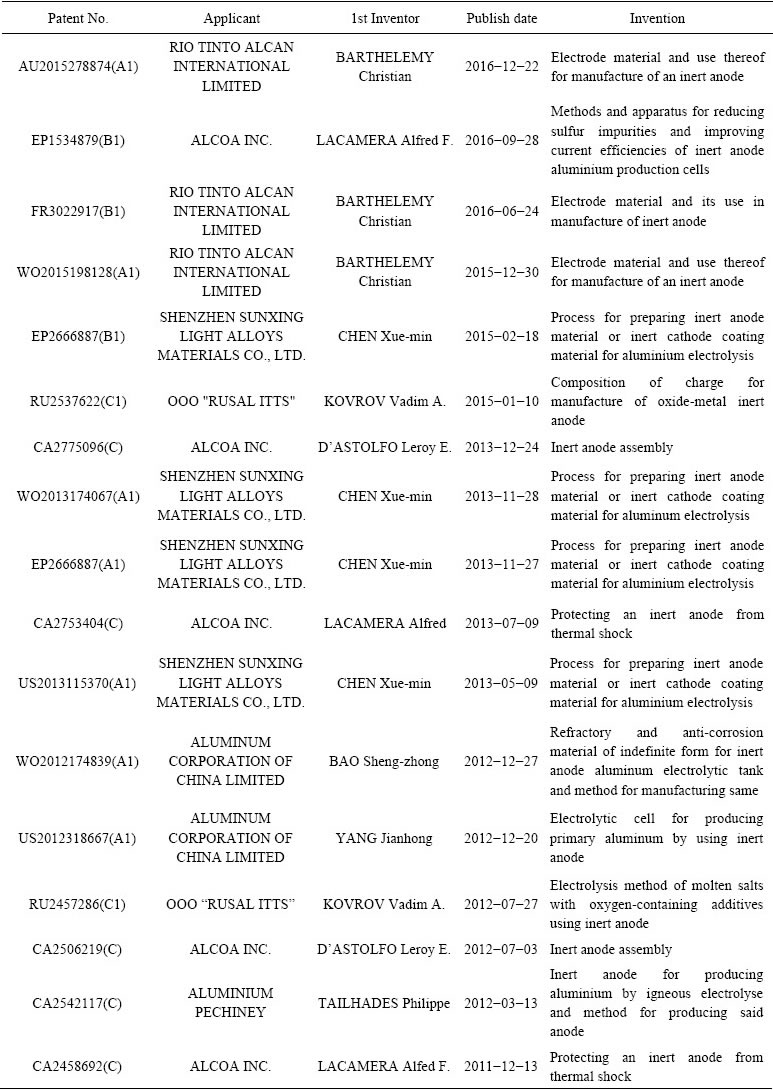
(Continued)

3.3 加快工业化研究进程的必要性及建议
国外惰性阳极技术的大规模应用,将迅速改变全球铝业的技术链和市场格局,对我国铝业的发展带来冲击和挑战。首先,欧美正在推动设立碳关税,建立新的贸易壁垒。2021年3月,欧洲议会通过有关“碳边境调整机制(CBAM)”的决议,欧盟将于同年提出关于碳关税的具体方案,并按照该方案从2023年起对进口商品征收碳关税,铝将成为欧盟征收碳关税的首选品种。据海关总署数据,2020年我国铝产品贸易总额达272亿元,其中出口贸易额135亿元,同比下降13.6%;出口铝材463万t,已同比下降10%[58],照此趋势,如果中国电解铝和下游产业的碳足迹无法削减,出口时将被征收高额的碳关税。其次,发达国家掌握大宗商品定价权,正利用其先进的降碳减排技术优势,重构商品定价机制,如伦敦金属交易所2021年将推出“低碳”铝交易平台,推动低碳铝的溢价交易。再次,惰性阳极技术具有环保、智能的特点(惰性阳极能够长期稳定服役,无需换极操作,可实现自动化槽控),是新一代铝电解生产技术,如果国内不抓紧攻关突破,可能出现核心技术受制于人的状况。在当前情势下,国内团队应加快推进我国无碳铝技术的工业化应用,打破国外的技术封锁和碳交易壁垒,确保中国铝工业持续、健康、绿色、高质量发展。
当前惰性阳极技术的发展现状表明,我国在无碳铝电解技术的开发与应用方面的机遇与挑战并存:在惰性阳极材料体系的研究方面,我国与欧美国家的发展进度基本持平,近40年来均经历了从合金阳极逐步向金属陶瓷惰性阳极的过渡,金属陶瓷材料体系的开发趋于成熟;另一方面,相较于发达国家,我国开展的5 kA及以上规模的惰性阳极铝电解试验较少,致使该项技术的工业化应用开发进程滞后。因此,在未来相当长的一段时间内,我国需要将研究重点集中在惰性阳极的工程化制备及其铝电解工业应用技术研究上,加速中等规模(5~100 kA级)惰性阳极铝电解试验研究,并在这一过程中深入探索阳极/电解质界面的交互作用机制、低温高氧化铝浓度电解质稳定工程应用基础、惰性阳极铝电解腐蚀抑制方法等问题,为惰性阳极技术的工业化应用提供系统支持。
4 结语
无碳铝电解技术是铝电解行业实现“碳达峰”、“碳中和”目标的颠覆性技术,未来逐步取代现行铝电解技术的趋势明显,中国作为世界上最大的铝工业国和消费市场,应加速推进惰性阳极铝电解工业化应用的进程。
在现有的惰性阳极材料体系中,金属陶瓷惰性阳极更有望实现工业化应用突破。近期,该技术的研发重点应集中在其工程铝电解应用研究方面,具体包括以金属陶瓷材料的成分优化、结构设计提升材料的综合性能,以电极和电解槽结构设计、电解质研究等改善阳极的服役环境,从而使惰性阳极服役寿命达到工业规模应用的要求。与此同时,清洁能源、污染物治理、铝合金回收利用、能源综合利用等技术的进步也将为铝产业实现碳中和目标提供驱动力,相信在国外的激烈技术竞争和国内的政策激励下,惰性阳极铝电解技术将飞速进步并获得更多突破性进展。
REFERENCES
[1] YASINSKIY A S, PADAMATA S K, POLYAKOV P V, et al. Electrochemical behaviour of Cu-Al oxygen-evolving anodes in low-temperature fluoride melts and suspensions[C]//TOMSETT A. Light Metals 2020. San Diego: TMS, 2020: 591-599.
[2] YASINSKIY A S, PADAMATA S K, POLYAKOV P V, et al. Electrochemical characterization of the liquid aluminium bipolar electrode for extraction of noble metals from spent catalysts[J]. Non-ferrous Metals, 2019, 47(2): 23-30.
[3] YASINSKIY A S, PADAMATA S K, POLYAKOV P V, et al. Anodic process on aluminium bronze in low-temperature cryolite-alumina melts and suspensions[J]. Tsvetnye Metally, 2019, 9(1): 42-49.
[4] PADAMATA S K, YASINSKIY A S, POLYAKOV P V. Electrode processes in KF-AlF3-Al2O3 melts[J]. New Journal of Chemistry, 2020, 44(13): 5152-5164.
[5] PADAMATA S K, YASINSKIY A S, POLYAKOV P V. Anodic process on Cu-Al alloy in KF-AlF3-Al2O3 melts and suspensions[J]. Transactions of Nonferrous Metals Society of China, 2020, 30(5): 1419-1428.
[6] HRYN J, TKACHEVA O, SPANGENBERGER J. Initial 1000 A aluminum electrolysis testing in potassium cryolite-based electrolyte[C]//PABEL T. Light Metals 2013, San Antonio: TMS, 2013: 1289-1294.
[7] GLUCINA M, HYLAND M. Laboratory scale testing of aluminium bronze as an inert anode for aluminium electrolysis[C]//SCHNEIDER W. Light Metals 2005, San Francisco: TMS, 2005: 523-528.
[8] LIU Y, ZHANG Y, WANG W, et al. The effect of La on the oxidation and corrosion resistance of Cu52Ni30Fe18 alloy inert anode for aluminum electrolysis[J]. Arabian Journal for Science and Engineering, 2018, 43(11): 6285-6295.
[9] GALLINO I, KASSNER M E, BUSCH R. Oxidation and corrosion of highly alloyed Cu-Fe-Ni as inert anode material for aluminum electrowinning in as-cast and homogenized conditions[J]. Corrosion Science, 2012, 63: 293-303.
[10] JUCKEN S, TOUGAS B, DAVIS B, et al. Study of Cu-Ni-Fe alloys as inert anodes for Al production in low-temperature KF-AlF3 electrolyte[J]. Metallurgical and Materials Transactions B, 2019, 50(6): 3103-3111.
[11] JUCKEN S, SCHAAL E, TOUGAS B, et al. Impact of a post-casting homogenization treatment on the high- temperature oxidation resistance of a Cu-Ni-Fe alloy[J]. Corrosion Science, 2019, 147(1): 321-329.
[12] CAO D, SHI Z, SHI D, et al. Electrochemical oxidation of Fe-Ni alloys in cryolite-alumina molten salts at high temperature[J]. Journal of the Electrochemical Society, 2019, 166(4): E87-E96.
[13] CAO D, MA J, SHI Z, et al. Corrosion behavior of Fe-Ni alloys in molten KF-AlF3-Al2O3 salts at 700 ℃[J]. Corrosion Science, 2019, 156: 32-43.
[14] HUANG Y, YANG Y, ZHU L, et al. Electro chemical behavior of Fe-Ni alloys as an inert anode for aluminum electrolysis[J]. International Journal of Electrochemical Science, 2019, 14(1): 6325-6336.
[15] CHAPMAN V, WELCH B J, SKYLLAS K M. Anodic behaviour of oxidized Ni-Fe alloys in cryolite-alumina melts[J]. Electrochimica Acta, 2011, 56(3): 1227-1238.
[16] GUNNARSSON G, ONNARSSON G, FROSTASON S, et al. Aluminum electrolysis with multiple vertical non- consumable electrodes in a low temperature electrolyte[C]// CHESONIS C. Light Metals 2019. Pittsburgh: TMS, 2019: 803-810.
[17] GUAN P P, LIU A, SHI Z N, et al. Corrosion behavior of Fe-Ni-Al alloy inert anode in cryolite melts[J]. Metals, 2019, 9(4): 399-405.
[18] CHAPMAN V, WELCH B J, SKYLLAS-KAZACOS M. High temperature oxidation behaviour of Ni-Fe-Co anodes for aluminium electrolysis[J]. Corrosion Science, 2011, 53(9): 2815-2825.
[19] REZA, KUROSH. An investigation into dissolution behavior of pre-oxidized Ni-6Al-10Cu-11Fe-15Cr nickel base alloy in molten cryolite[J]. Anti-Corrosion Methods and Materials, 2015, 62(1): 1-6.
[20] 周科朝, 李志友, 张 雷. 铝电解金属陶瓷惰性阳极[M]. 1版. 长沙: 中南大学出版社, 2012: 6-24.
ZHOU Ke-chao, LI Zhi-you, ZHANG Lei. Cermet inert anode for aluminium electrolysis[M]. 1st ed . Changsha: Central South University Press, 2012: 6-24.
[21] HAARBERG G M. The interaction between tin oxide and cryolite-alumina melts[J]. ECS Proceedings Volumes, 1994, 13(1): 568-577.
[22] ALDER H. Electrolysis of a molten charge using in comsumable electrodes: US 3960678US[P]. 1976-06-01.
[23] VIRGIL C. Influence of the operating parameters over the current efficiency and corrosion rate in the Hall–Heroult aluminum cell with tin oxide anode substrate material[J]. Chinese Journal of Chemical Engineering, 2015, 23(4): 722-726.
[24] AUGUSTIN C O, SEN U. Green anode for aluminium production[J]. Bulletin of Electrochemistry, 1990, 6(3): 296-297.
[25] MEYERA P, GIBILAROA M, MASSOTA L, et al. Comparative study on the chemical stability of Fe3O4 and NiFe2O4 in molten salts[J]. Materials Science and Engineering B, 2018, 228: 117-122.
[26] DU J, WANG B, LIU Y, et al. Study on the bubble behaviour and anodic over voltage of NiFe2O4 ceramic based inert anode[C]//MARGARET H. Light Metals 2015. Pittsburgh: TMS, 2015: 1193-1197.
[27] WANG B, DU J, LIU Y. Effect of TiO2 addition on grain growth, anodic bubble evolution and anodic overvoltage of NiFe2O4-based composite inert anodes[J]. Journal of Materials Engineering and Performance, 2017, 26(11): 5610-5619.
[28] RAY S P, RAPP R A. Composition suitable for use as inert electrode having good electrical conductivity and mechanical properties: US 4454015US[P]. 1984-06-12.
[29] RAY S P, RAPPR A. Method of making composition suitable for use as inert electrode having good electrical conductivity and mechanical properties: US 4584172US[P]. 1986-04-22.
[30] LIU J Y, LI Z Y, TAO Y Q, et al. Phase evolution of 17(Cu-10Ni)-(NiFe2O4-10NiO) cermet inert anode during aluminium electrolysis[J]. Transactions of Nonferrous Metals Society of China, 2011, 21(3): 566-572.
[31] TAO Y Q, LI Z Y, ZHANG D, et al. Microstructural evolution of a nickel ferrite-copper alloy cermet during sintering and high-temperature oxidation[J]. Journal of the American Ceramic Society, 2012, 95(10): 3031-3036.
[32] TAO Y Q, LI Z Y, SHAO H P, et al. Oxidation and corrosion behavior of (Cu-10Cu2O)-(NiFe2O4-10NiO) cermet inert anode with interpenetrating structure[J]. International Journal of Electrochemical Science, 2020, 15: 7833-7847.
[33] TIAN Z L, YANG S. Anodic corrosion behavior of NiFe2O4- based cermet in Na3AlF6-K3AlF6-AlF3 for aluminium electrolysis[J]. Metallurgical and Materials Transactions B, 2015, 46(3): 1257-1261.
[34] TIAN Z L, GUO W C, LAI Y Q, et al. Effect of sintering atmosphere on corrosion resistance of Ni/(NiFe2O4-10NiO) cermet inert anode for aluminum electrolysis[J]. Transactions of Nonferrous Metals Society of China, 2016, 26(11): 2925-2929.
[35] 张 啸, 张志刚, 夏鹏程, 等. 阳极电流密度对NiFe2O4基惰性阳极电解腐蚀行为的影响[J]. 材料与冶金学报, 2019, 18(2): 114-120.
ZHANG Xiao, ZHANG Zhi-gang, XIA Peng-cheng, et al. Effect of anode current density on electrolysis corrosion behavior of NiFe2O4-based inert anode[J]. Journal of Materials and Metallurgy, 2019, 18(2): 114-120.
[36] MEYER P, MASSOT L, GIBILARO1 M, et al. Electrochemical degradation mechanism of a cermet anode for aluminum production[J]. Materials Sciences and Applications, 2019, 10(9): 614-629.
[37] 杨文杰. 基于工业化铝电解惰性阳极材料的制备与耐蚀性能优化[D]. 长沙: 中南大学, 2017.
YANG Wen-jie. Inert anode material preparation a corrosion resistance optimization based on industrialization of aluminum electrolysis[D]. Changsha: Central South University, 2017.
[38] 冯立超. Cu2O-Cu金属陶瓷制备及组织性能研究[D]. 哈尔滨: 哈尔滨工业大学, 2009.
FENG Li-chao. Preparation and microstructure and properties of Cu2O-Cu cermets[D]. Harbin: Harbin Institute of Technology, 2009.
[39] FENG L C, SHAO W Z, ZHEN L. Cu2O/Cu cermet as a candidate inert anode for Al production[J]. International Journal of Applied Ceramic Technology, 2007, 4(5): 453-462.
[40] FENG L C, XIE N, SHAO W Z, et al. Exploring Cu2O/Cu cermet as a partially inert anode to produce aluminium in a sustainable way[J]. Journal of Alloys and Compounds, 2014, 610: 214-223.
[41] DENORA V. How to find an inert anode for aluminium cells[C]//HAARBERG G M. Norway: Eleventh International Aluminium Symposium, 2001: 155-160.
[42] PAWLEK R P. Inert anodes, an update[C]//SCHNEIDER W. Light Metals 2014. Warrendale: TMS, 2002: 449-456.
[43] BENEDYK J C. Status report on inert anode technology for primary aluminium[J]. Light Metal Age, 2001, 59(1): 36-37.
[44] YANG W J, WANG Y, ZHAI H F, et al. Effect of NiO addition on the high-temperature oxidation and corrosion behaviors of Fe-Ni alloy as inert anode material for aluminum electrolysis[J]. Journal of Materials Science, 2020, 55(9): 4065-4072.
[45] CHEN J, HUANG Z H, REN Y J, et al. Air oxidation of porous Cu-35wt.%Ni-(5,10,15)wt.%Cr alloys at 650 ℃[J]. Applied Mechanics and Materials, 2013, 365/366: 987-990.
[46] YASINSKIY A S, PADAMATA S K, POLYAKOV P V, et al. An update on inert anodes for aluminium electrolysis[J]. Non-ferrous Metals, 2020. DOI:10.17580/nfm.2020.01.03.
[47] ZHANG Z G, ZU G Y, CAO Z K, et al. Fabrication and properties of U-shaped NiFe2O4 ceramic tube produced by slip casting and pressureless sintering[J]. Journal of the Australian Ceramic Society, 2021, 57(2): 459-467.
[48] PADAMATA S K, YASINSKIY A S, POLYAKOV P V. Progress of inert anodes in aluminium industry: Review[J]. Journal of Siberian Federal University Chemistry, 2018, 11(1): 18-30.
[49] GUPTA A, BASU B. Sustainable primary aluminium production: Technology status and future opportunities[J]. Transactions of the Indian Institute of Metals, 2019, 72(8): 2135-2150.
[50] 田忠良, 赖延清. 金属陶瓷惰性阳极低温铝电解[M]. 1版. 长沙: 中南大学出版社, 2016: 5-22.
TIAN Zhong-liang, LAI Yan-qing. Low temperature aluminum electrolysis of cermet inert anode[M]. 1st ed. Changsha: Central South University Press, 2016: 5-22.
[51] 李国勋, 王传福, 层树岭, 等. 铝电解惰性阳极材料的制备及抗腐蚀研究[J]. 有色金属, 1993(2): 53-57.
LI Guo-xun, WANG Chuan-fu, CENG Shu-ling, et al. Studies on fabrication and corrosion of inert anode in fluoride melt for aluminum electrolysis[J]. Nonferrous Metals, 1993(2): 53-57.
[52] 张竞赛, 侯 琴. 铝电解惰性阳极专利技术分析[J]. 江西化工, 2020(2): 156-158.
ZHANG Jing-sai, HOU Qin. Patent analysis of aluminum electrolytic inert anode[J]. Jiangxi Chemical Industry, 2020(2): 156-158.
[53] ASBJ
RN S. Inert anodes—The blind alley to environmental friendliness?[C]//MARTIN O. San Diego: Light Metals 2018. TMS, 2018: 1252-1260.
[54] WU Xian-xi. Inert anodes for aluminum electrolysis[M]. Gewerbestrasse: Springer Nature Switzerland AG, 2021: 23-122.
[55] YASINSKIY A, SUZDALTSEV A, PADAMATA S K. Electrolysis of low-temperature suspensions: An update[C]// TOMSETT A. Light Metals 2020. San Diego: TMS, 2020: 626-636.
[56] POLYAKOV P V, KLYUCHANTSEV A B, YASINSKIY A S, et al. Conception of friendship cells in aluminium electrolysis[C]//WILLIAMS E. Light Metals 2016, Warrendale: TMS, 2016: 283-288.
[57] BROUGH D, JOUHARA H. The aluminium industry: A review on state-of-the-art technologies, environmental impacts and possibilities for waste heat recovery[J]. International Journal of Thermofluids, 2020, 1/2: 100007. https://doi.org/10.1016/j.ijft.2019.100007.
[58] 工业和信息化部原材料工业司. 2020年铝行业运行情况[EB/OL]. https://www.miit.gov.cn/jgsj/ycls/ysjs/art/2021/ art_ed796979fa4f441fa1bd77ce5da4bfde.html, 2020-02-05/ 2020-06-30.
Department of Raw Materials Industry, Ministry of Industry and Information Technology. Aluminium industry operations in 2020[EB/OL]. https://www.miit.gov.cn/jgsj/ycls/ysjs/art/ 2021/art_ed796979fa4f441fa1bd77ce5da4bfde.html, 2020- 02-05/2020-06-30.
Research progress of inert anode materials and technology for aluminium electrolysis
ZHOU Ke-chao, HE Yong, LI Zhi-you, SHEN Ting, ZHANG Lei
(State Key Laboratory of Powder Metallurgy, Central South University, Changsha 410083, China)
Abstract: The inert anode is the key technology for the future low-carbon development of aluminium electrolysis industry, which is also an important aspect of the carbon neutrality. In recent years, the significant advances in inert anode material research and engineering have provided new opportunities for the breakthrough in industrial applications. Therefore, this paper presents a comprehensive review of the research progress of inert anode materials in recent years. The following aspects were emphasized, including the formation of the protective film on the metallic anode surface, composition and structure optimization of cermet anode, the improvement of performance of anode materials, and so on. The comparison of the conductivity and corrosion resistance of inert anode materials was discussed, with the aim to provide the prospects of development trend.
Key words: inert anode; aluminium electrolysis; metallic anode; cermet
Received date: 2021-07-08; Accepted date: 2021-09-26
Corresponding author: ZHANG Lei; Tel: +86-13975801816; E-mail: zhanglei@csu.edu.cn
(编辑 李艳红)
收稿日期:2021-07-08;修订日期:2021-09-26
通信作者:张 雷,研究员,博士;电话:13975801816;E-mail:zhanglei@csu.edu.cn
摘 要:惰性阳极铝电解技术是未来铝工业持续低碳化发展并实现碳中和目标的关键技术,近年来,惰性阳极材料的研究取得了长足进展,为其工业化应用的突破性进展创造了条件。本文通过综述铝电解惰性阳极材料近期研究进展,重点关注合金阳极表面耐蚀层的生长机制、金属陶瓷组成与结构优化及阳极材料综合性能提升等研究方向,系统对比了现有惰性阳极材料的导电性及耐蚀性能,并对其未来发展趋势做出展望。