高性能稀土镁合金研究新进展
曾小勤1, 2,陈义文1,王静雅1,丁文江1
(1. 上海交通大学 轻合金精密成型国家工程研究中心,上海 200240;
2. 上海交通大学 金属基复合材料国家重点实验室,上海 200240)
摘 要:
镁合金作为最为轻质的金属结构材料,是实现航空航天、交通运输以及电子通讯等轻量化的重要材料。然而,镁合金在应用过程中仍面临一系列瓶颈问题。研究结果表明,稀土元素对于改善镁合金的性能具有至关重要的作用。本文聚焦稀土元素对镁合金组织的作用机制,讨论了稀土元素对镁合金塑性变形能力、导热性能及耐腐蚀性能的影响规律。总结发现稀土元素能够通过调控织构和变形过程中的滑移机制提高塑性,影响第二相的析出行为,改善导热性能;改变析出相的化学性质、形貌与分布等提高耐腐蚀性能。展望通过调控稀土元素设计新型高性能结构功能一体化稀土镁合金的发展方向。
关键词:
稀土镁合金;塑性;热导;耐腐蚀;
文章编号:1004-0609(2021)-11-2963-13 中图分类号:TG146.22 文献标志码:A
引文格式:曾小勤, 陈义文, 王静雅, 等. 高性能稀土镁合金研究新进展[J]. 中国有色金属学报, 2021, 31(11): 2963-2975. DOI: 10.11817/j.ysxb.1004.0609.2021-42442
ZENG Xiao-qin, CHEN Yi-wen, WANG Jing-ya, et al. Research progress of high-performance rare earth magnesium alloys[J]. The Chinese Journal of Nonferrous Metals, 2021, 31(11): 2963-2975. DOI: 10.11817/j.ysxb.1004.0609.2021-42442
随着全球资源危机和环境污染等问题日趋严重,在工业生产应用中实现结构材料的轻量化,降低能源消耗成为亟待解决的关键问题。在现有工程用金属中,镁合金是最轻的金属结构材料之一,其密度约为1.74 g/cm3,仅为铝的2/3,钛的1/3,钢的1/4。此外,镁合金具有较高的比强度和比刚度、良好的导电导热性、优异的电磁屏蔽性和阻尼减振性、较好的生物相容性及易于回收和循环利用等优良特性。随着生产技术进步以及成本降低,近年来,镁合金作为结构材料,在航空航天、国防军事、轨道交通、电子通讯、生物医疗等重要领域展现出显著的应用优势和广阔的应用前景,被称为“21世纪绿色工程材料”[1-2]。在航空航天领域,镁合金被广泛应用于制造飞机、导弹、飞船、卫星上的重要构件,以大幅减轻零件质量,提高飞行器的机动性能,降低航天器的发射成本。在民用领域,近年来镁合金在电子产品上的应用发展迅速,所制造的轻薄笔记本电脑外壳备受青睐。同时,中国拥有种类齐全的镁矿石,是世界上镁资源储量最为丰富的国家,约占全世界镁资源总量的50%以上。我国还是镁合金生产大国,80%以上的镁合金产品出口国际市场[3]。因此,如何因地制宜,合理利用我国镁资源的优势,加速高性能镁合金的设计、研发,推进镁合金的工程化应用,有效实现材料轻量化迫在眉睫。
然而,传统镁合金的性能仍旧存在一些显著的缺点:1) 绝对强度较低,尤其是高温力学性能较差,缺乏有效的析出强化相;2) 室温下塑性较低,加工变性能力较差,导致其成形性有限;3) 抗腐蚀性能较差,极易在大气及海洋环境中发生腐蚀失效行为[4]。这些问题严重制了镁合金的大规模工程应用。因此,设计研发高性能镁合金,推进镁合金在工业中的应用,是近年来研究人员主要关注的难题。
稀土元素由于具有独特的核外电子排布,且在镁中有较大的固溶度,在改善镁合金性能方面表现出非常显著的优势[5-7]。研究表明,镁合金中添加稀土元素能够有效提高镁合金的强度及塑性变形能力、影响其导电导热性能、改善其耐腐蚀性能、高温力学性能及摩擦磨损性能等[8-24]。
在早期研究中,稀土元素常被添加到镁合金中,用于改善镁合金室温及高温强度。其中,稀土元素Gd和Y在α-Mg基体中具有较大的极限固溶度,分别为4.53%和3.35%(摩尔分数),并且与Mg的原子半径差存在明显差异,可以起到良好的固溶强化作用[8-9],固溶强化效率远远高于Al和Zn等元素[10-11]。随着温度的降低,Y和Gd元素在镁中的固溶度明显下降,能够析出高硬度且弥散分布的第二相。Mg-Y系合金和Mg-Gd系合金的时效序列基本相同:SSSS→β″(D019)→β′(cbco)→β1(FCC)→ β(FCC)[12]。其中,底心正交结构的
相是一种片状的棱柱面析出相,镁基体之间的位向关系为
和
,可显著阻碍基面位错的运动,在镁合金中发挥较好的析出强化和弥散强化作用[13-16]。此外,在高温服役条件下,
相具有较高稳定性的,可有效钉扎晶界,并阻碍位错迁移,提高镁合金的抗蠕变性能[17-18]。上海交通大学轻合金中心[10]开发的Mg-Gd-Y-Zr (JDM-2)镁合金,经过变形+时效处理后,屈服强度和抗拉强度分别能够达到436 MPa和491 MPa,显著提高了镁合金的力学性能。
前期大量研究人员对高强度稀土镁合金展开了广泛深入的研究。近年来,随着对镁合金性能研究的不断深入,研究人员还发现除了传统的强化作用,稀土元素还可以有效细化晶粒,弱化织构,并且通过改变镁合金变形过程中的滑移、孪生机制,显著提升其塑性变形能力[7, 19-23]。稀土元素对镁合金性能的提高还表现在改善表面氧化膜结构,提高膜层致密性,进而提升其抗腐蚀能力[24]。此外,在材料冶炼过程中,稀土元素易与熔体中的有害杂质铁、镍等结合,形成金属间化合物,进而实现净化熔体及除杂的效果等[3]。由此可见,稀土元素的添加,为设计开发高性能镁合金提供了新的途径。因此,近年来,大量研究学者对稀土镁合金进行了广泛深入的研究。鉴于此,本文作者围绕稀土元素对镁合金性能的影响机制和规律展开深入分析,包括塑性、导热性能及抗腐蚀性能。重点介绍了近年来高塑性稀土镁合金、高导热稀土镁合金及耐腐蚀镁合金的最新研究进展。
1 高塑性稀土镁合金
1.1 镁合金的塑性变形行为
镁的晶体结构为典型的密排六方结构,其c/a为1.623,具有较为显著的各向异性。镁合金中的变形机制主要分为滑移和孪生,包括基面
滑移、柱面
滑移、锥面
滑移、锥面
滑移以及拉伸孪晶、压缩孪晶,如图1所示。纯镁中基面
滑移是最容易开动的变形机制,其室温下临界剪切应力(Critical resolved shear stress, CRSS)远远低于其他非基面滑移的临界剪切应力[25-31],如图2所示。因此,在室温下,镁合金的塑性变形通常以基面滑移系为主。然而基面滑移仅具有两个独立滑移系,无法满足Von-Mises屈服准则,需要5个独立滑移系来实现多晶材料的均匀塑性变形。由于非基面
滑移系的临界剪切应力高于基面滑移系两个数量级,因此,在变形过程中很难激活非基面滑移系。而基面
滑移系只能协调材料沿基面方向的应变,无法协调沿c轴方向的变形,使得材料具有明显的各向异性非均匀变形行为。这是直接导致镁合金塑性变形能力差的关键所在。
因此,为了改善镁合金的塑性,大量研究人员对此进行了深入的探讨。前期研究表明,弱化织构[32]以及在变形过程中促进非基面滑移系启动[33-34]是提高镁合金塑性最有效的方法。首先,弱化基面织构,使得材料组织具有随机取向分布,有利于提高非基面滑移系的施密特因子,激活更多的变形机制参与塑性变形,提高材料变形均匀性及塑性变形能力。其次,通过调控非基面滑移系与基面滑移系启动的难易程度,缩小其滑移阻力之间的差异,促进更多的非基面滑移系及交滑移参与塑性变形,为位错滑移提供更多的运动路径,进而协调变形过程中的应变,改善镁合金的塑性变形能力[35-36]。
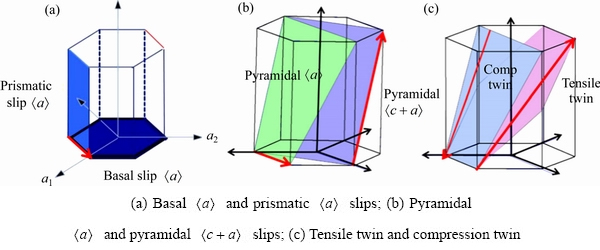
图1 镁合金中的变形机制示意图
Fig. 1 Schematic diagram of deformation mechanism in Mg alloy
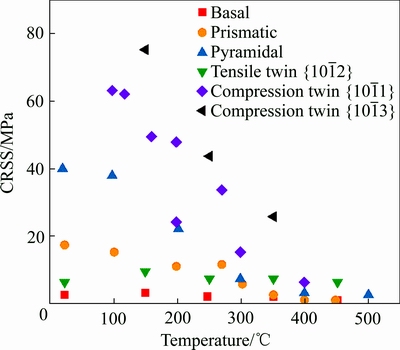
图2 不同温度下镁的基面与非基面滑移的临界剪切应力(CRSS)[25-31]
Fig. 2 Critical resolved shear stress (CRSS) of basal slip and non-basal slips in pure Mg at different temperatures[25-31]
1.2 稀土对镁合金塑性的影响
如前所述,稀土元素因其特殊的核外电子分布,对镁合金的组织影响非常显著。实验研究表明,稀土元素的添加能够有效弱化织构。LI等[37]对纯镁和Mg-0.8%Y(质量分数)轧制态合金的织构和力学性能进行了深入的研究。结果表明,微量稀土元素Y的添加,使得织构强度从纯镁的18.2降低至13.3,并且织构呈现出随机分散的分布形式,如图3(a)和3(b)所示。与此同时,Mg-0.8%Y(质量分数)合金的伸长率大幅提高至20%左右,如图3(c)所示。相比于纯镁伸长率不足5%,Y元素的添加显著改善了镁合金的塑性变形能力。随后,LI等[37]通过晶体塑性有限元方法对Mg-Y合金的变形机制进行了分析,发现柱面滑移和一级锥面
滑移系被大量激活,进而显著提升了材料的塑性。轻稀土Ce元素对弱化镁合金织构具有重要作用。CHINO等[38]通过实验手段研究了轧制态纯镁和Mg-0.2%Ce(质量分数)合金的织构和力学性能。研究发现,微量轻稀土Ce元素添加,使得镁合金的织构强度降低至4.7左右,同时大幅度提升其成形性能。究其原因,在变形过程中,大量非基面滑移系开动,促进了材料的均匀塑性变形。此外,STANFORD等[32]和WU等[39]研究发现,稀土元素Gd、La和Er对于弱化基面织构,提升镁合金的塑性亦具有显著作用。
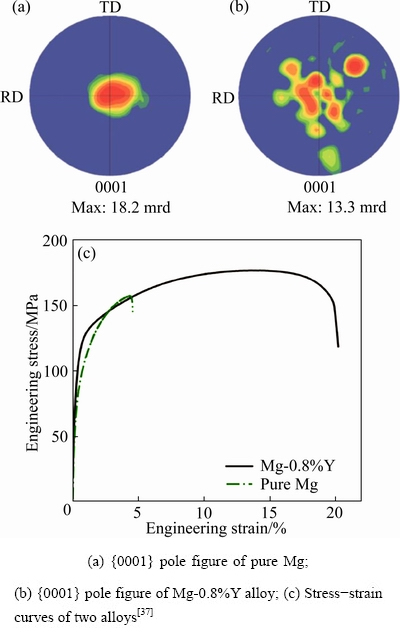
图3 Y元素对镁合金的织构及力学性能的影响
Fig. 3 Effect of Y element on texture and mechanical property of Mg alloys
除了弱化织构,稀土元素对于影响镁合金中滑移系启动难易程度(即滑移系临界剪切应力CRSS),调控变形过程中的滑移机制方面具有重要作用。前期,
等[40]通过实验研究发现,Mg-3%Y (质量分数)合金具有优异的塑性变形能力。这归功于变形过程中大量锥面
位错的开动,提高了变形均匀性。他们推测固溶稀土元素Y,能够影响不同滑移面上的层错能(Stacking fault energy, SFE),进而改变相应滑移系的启动阻力CRSS,促进非基面
位错的开动。KIM等[41]通过分子动力学模拟计算了不同Y含量下,Mg-Y合金中沿不同方向变形的应力-应变曲线以及各滑移系的CRSS,如图4所示。结果表明,Mg-1%Y(质量分数)合金中,各滑移系CRSS比值为
: CRSSpri : CRSSbasal=1.8:1.1:1.0,而当Y含量增至3%(质量分数)时,
: CRSSpri : CRSSbasal降低至1.1:0.8:1.0,远远低于纯镁(276:22:1)的值。Y元素的添加能够在提高各个滑移系CRSS的同时,降低各滑移系CRSS之间的差距,进而在塑性变形过程中促进非基面滑移系的开动。随后,上海交通大学曾小勤团队[42-43]针对Mg-Y合金的滑移机制及变形行为进行了更加深入的分析。WANG等[42]和HUANG等[43]采用3D XRD (Three-dimensional X-ray diffraction)技术,探究了Mg-3%Y(质量分数)和Mg-5%Y(质量分数)合金的变形机理并测定了不同滑移系的CRSS。研究发现,在Mg-3%Y(质量分数)合金中非基面滑移与基面滑移之间CRSS的比值为CRSSprism :
: CRSSbasal=3.2:3.0:1.0,而在Mg-5%Y(质量分数)合金中,CRSSprism/CRSSbasal和
/CRSSbasal分别约为1.8~2.7和1.6~1.8。从实验角度印证了稀土元素Y能够有效降低非基面与基面CRSS比值,改善材料的均匀塑性变形能力。此外,SABAT等[44]通过实验结合粘塑性自洽(Viscoplastic self-consistent, VPSC)模拟方法对Mg-0.2%Ce(摩尔分数)合金的变形行为及力学性能进行了研究。结果发现变形态Mg-Ce合金塑性大幅提升,可到达40%。其根源在于Ce元素添加促进了变形过程中非基面滑移系的激活。其不同滑移系及孪晶的CRSS比值为CRSSbasal: CRSSprism:
:CRSStwin=1:1.5:4:1.4,远远低于纯镁。由此可见,稀土元素Y、Ce等对于降低非基面滑移与基面滑移系CRSS比值,促进非基面位错的滑移,调控镁合金的变形机制,进而改善材料的塑性变形能力具有重要作用。
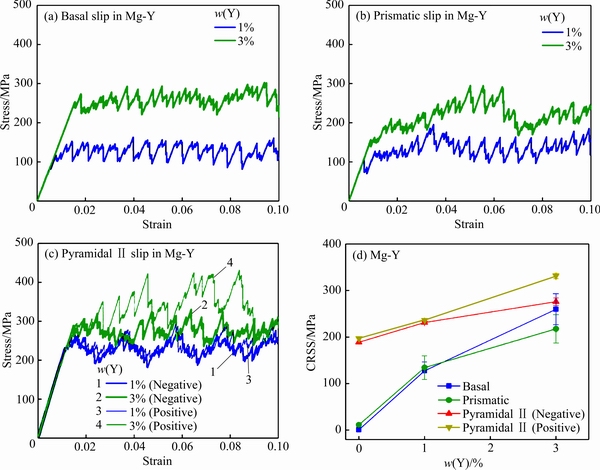
图4 分子动力学模拟得到0 K下应力-应变曲线和Mg-Y合金中基面、柱面和二级锥面滑移系的临界剪切应力[41]
Fig. 4 Simulated stress-strain curves ((a)–(c)) and critical resolved shear stress of Mg-Y alloys on basal, prismatic, and pyramidal Ⅱ planes(d) at 0 K[41]
此外,添加稀土元素除了可以影响滑移系CRSS比值之外,还能够促进位错交滑移,增加位错运动路径,进而改善镁合金的塑性变形能力。
等[45]通过透射电镜观察发现,添加稀土元素Y可以促进
位错在一级锥面和二级锥面之间的交滑移。WU等[36]采用密度泛函理论(Density functional theory, DFT)计算了不同合金元素对一级锥面与二级锥面交滑移能垒的影响,如图5(a)所示。其中稀土元素Y、Ce、Er、Gd和Nd能够显著降低交滑移能垒,有效促进
位错的交滑移,改善材料的塑性变形能力。除锥面交滑移外,LIU等[46]通过第一性原理计算得到了镁基体中添加不同溶质原子后的电子功函数(Electron work function, EWF),并基于此预测了合金的基面-柱面交滑移能力。图5(b)展示了添加合金元素后,基面-柱面交滑移软化比值和电子功函数的关系。其中具有较大比值的合金元素,即位于图中左上方区域的合金元素,能够显著降低基面-柱面交滑移所需的应力。而从图中可以发现,在此区域中主要为稀土元素。其中,稀土元素La对促进基面-柱面交滑移的作用最为明显。综上所述,稀土元素Y、Ce、Er、Gd、Nd和La等能够通过弱化织构、降低非基面与基面CRSS比值、降低交滑移能垒等方面,促进非基面滑移系的开动并为位错运动提供更多有效路径,进而改善镁合金的塑性,实现高塑性稀土镁合金。
2 高导热稀土镁合金
2.1 镁合金的导热性能
近年来,随着对镁合金研究的逐步深入以及应用的不断拓展,除了传统的结构性,镁合金优良的导热性能也引起了广泛关注。纯镁的热导率为158 W/(m·K),在常用的金属结构材料中仅低于铜(237 W/(m·K))和铝(401 W/(m·K))[47]。而镁的密度又仅为铝和铜的64.3%和19.4%,同等质量的镁合金散热性能优于后两者。由于镁合金优异的轻量化特性和良好的散热性,被认为是用于散热器、笔记本外壳、手机中框、基站、接入网络设备等与散热相关领域最具潜力的金属结构材料。
从本质上来说,当材料中存在温度梯度时,就会产生热量流动,这种现象称为热传导。固体中的热量主要通过电子载体(电子和空穴),声子(与晶格振动相关),电磁波等媒介传导。在金属和合金中,绝大部分热量通过电子传导,少部分热量通过声子传导[48]。合金中的溶质原子、相界面等均会影响电子和声子的热运动,缩短其运动的平均自由程,对合金的热导率产生显著的负面影响[49]。然而,纯镁的强度和塑性较差,又往往需要添加合金元素改善其综合力学性能。如何平衡镁合金的结构板力学性能与功能导热性能显得尤为重要。综上所述,稀土元素对镁合金的组织结构和性能具有独特的影响作用,因此,添加稀土元素是改善镁合金综合性能最有潜力的手段。一般来说,镁合金的热导率随着稀土含量的增加而有所降低,常见稀土镁合金的热导率如表1所示[50-54]。不难看出,镁合金热导率随着稀土元素的种类和含量的不同存在明显的差异。因此,探究影响稀土镁合金热导率的因素,对开发高导热镁合金具有重要的意义。
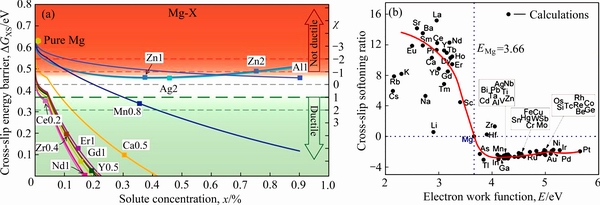
图5 合金元素对镁合金中的的一级锥面与二级锥面
交滑移能垒的影响以及纯镁中添加合金元素后基面-柱面交滑移软化比值和电子功函数的关系[36]
Fig. 5 Effect of alloying elements on activation barriers of cross slip between pyramidal Ⅱ plane and Ⅰ plane(a) and relationship between basal-prismatic cross-slip stress softening ratio and electron work function after adding alloying elements into pure Mg(b)[36]
2.2 稀土对镁合金导热性能的影响
稀土元素在镁合金中通常以固溶体或者金属间化合物的形式存在。对于固溶态稀土镁合金,陈长江等[52]实验测量了Mg-11Y-5Gd-2Zn-0.5Zr(质量分数,%)合金的热导率,发现随着高含量稀土的添加,合金的热导率从纯镁的158 W/(m·K)降低到只有23 W/(m·K)左右。这意味着稀土元素Gd和Y极大地降低了镁合金的热导率,这是由于二者在镁中的固溶度较大,极限固溶度分别为4.53%和3.35% (摩尔分数)[8-9]。稀土原子取代镁原子会产生严重的晶格畸变,破坏了镁基体原有的点阵排列。这对于电子和声子实际上是一种散射源,阻碍了电子和声子在晶格内的自由运动,减小了电子和声子的平均自由程,显著降低镁合金的热导率[55-56]。镁晶格的畸变程度强烈依赖合金元素种类,并随元素含量的升高而增加。苏创业等[55]通过实验手段研究了4种不同含量的Mg-Ce、Mg-Nd、Mg-Sm和Mg-Y二元镁合金的热导率,如图6所示。结果表明,当RE元素含量小于0.15%(摩尔分数)时,四种元素对镁合金热导率的影响相当。而当元素含量大于0.15% (摩尔分数)时,纯镁热导率的影响大小顺序为Y、Sm、Nd、Ce,其中固溶Ce元素对于镁合金导热性能的影响最小。GUO等[57]制备了不同稀土含量(4%~12%,质量分数)的Mg-La、Mg-Ce、Mg-Nd和Mg-Sm二元合金,并实验测量其热导率。结果表明,添加相同含量的稀土元素时,铸态的Mg-4Ce和Mg-4La合金在室温的热导率可以达到118.3 W/(m·K)和127.7 W/(m·K),远高于Mg-4Nd(98.9 W/(m·K))和Mg-4Sm (83.4 W/(m·K))合金。这是由于Ce和La在镁中的固溶度非常有限,远小于Nd和Sm,因此对镁合金的热导率的影响并不十分明显。钟丽萍等[8]研究了Gd、Ce、Nd和Y元素对镁合导热的影响,发现除固溶原子含量外,稀土原子半径尺寸差、化合价和亚电子层稳定程度也会影响镁合金热导率。原子尺寸差越大,镁基体的晶格畸变越严重,电子和声子受散射越剧烈,相应的热导率就越低。化合价规律遵循Linde规则,即每增加单位原子含量的固溶原子,合金的热阻增加值与化合价的平方成正比。固溶原子核外电子排布存在空轨道越多时,越易吸收外部电子,从而减少自由电子的数量,导致合金热导率降低[49]。
表1 常用稀土镁合金的热导率
Table 1 Thermal conductivity of representative rare earth magnesium alloy
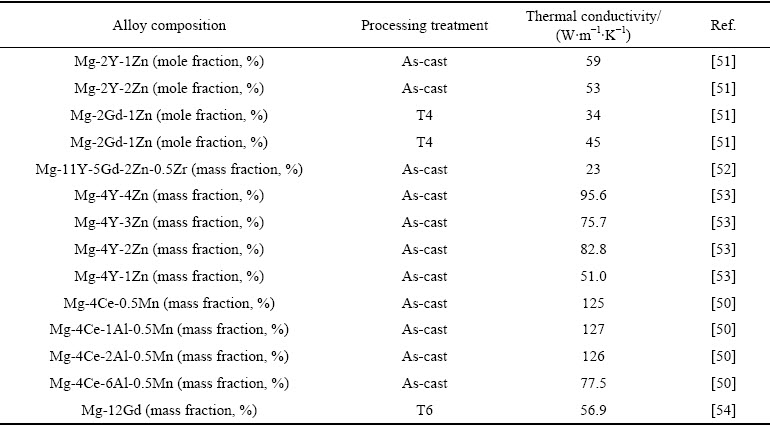
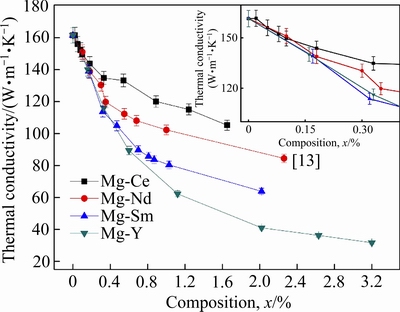
图6 稀土元素(Ce,Nd,Sm和Y)对镁合金热导率的影响[55]
Fig. 6 Effect of rare-earth elements (Ce, Nd, Sm and Y) on thermal conductivity of Mg alloys[55]
当稀土元素在镁合金中以金属间化合物的形式存在时,由于金属间化合物与镁基体晶格常数不同,在二者界面处会产生晶格畸变,成为电子和声子新的散射源。但是相比于溶质原子,金属间化合物热导率的下降要比固溶原子小得多。图7统计对比了当RE元素以固溶态存在和以金属间化合物形式存在时镁合金的热导率。研究结果表明,每1.0%(摩尔分数)的稀土元素添加到镁合金中,当以固溶原子存在时,热导率的数值下降约为123W/(m·K);而以金属间化合物形式存在时,热导率下降值仅为6.5~16.4 W/(m·K)。因此,通过调整合适的工艺和成分,使得添加的稀土元素以金属间化合物的形式存在,可以有效降低镁基体中的固溶原子含量,改善镁合金的导热性能。
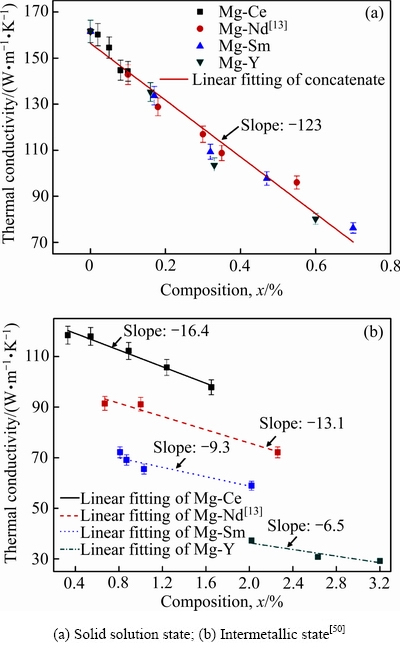
图7 稀土元素对镁合金热导率的影响
Fig. 7 Effect of RE elements on thermal conductivity
时效处理能够促进稀土元素从镁合金基体中析出,降低α-Mg中固溶元素的含量,有效改善镁合金的导热性能。钟丽萍等[54]对固溶态的Mg-12Gd (质量分数,%)合金在225 ℃下进行不同时间的时效处理,并测定了其热导率,如图8(a)所示。经过4 h时效后,合金的热导率从34.9 W/(m·K)增加到38.6 W/(m·K)。而当时效时间为24 h后,合金的热导率迅速增加到56.9 W/(m·K)。随着时效时间的增加,镁合金的热导率表现出稳步增长得趋势,在300 h时效后,热导率提高至75 W/(m·K)左右,达到峰值。这也是由于时效导致合金中析出大量的第二相,降低了基体的固溶元素含量,从而改善了合金的导热性能。苏创业等[58]在Mg-4Ce-xAl-0.5Mn(质量分数,%)体系合金中,研究了添加不同Al含量对合金导热性能的影响,如图8(b)所示。研究结果表明,在添加0~2.0%(质量分数)的Al后,合金的导热性能基本不发生变化,保持在126 W/(m·K)。这是由于添加的Al元素基本上形成了Al2Ce相、Al10Ce2Mn7和Al11Ce3相。但是,随着Al元素继续增加,多余的Al元素固溶到基体之中,因此合金的热导率呈现下降的趋势。此外,YAMASAKI等[51]的研究结果表明,在稀土镁合金中添加Zn、Al、Cu等过渡元素会消耗基体中的稀土元素,形成长程有序结构(LPSO)相,亦可提高合金的热导率。
综上所述可知,稀土元素以金属间化合物形式存在,能够降低基体中合金元素的固溶含量,有效改善镁合金的导热性能。其中,轻稀土元素Ce、La在镁中具有较低的固溶度,并且易形成化合物,表现出良好的导热性能,有望实现高导热稀土镁合金。

图8 Mg-12Gd合金热导率随时效时间增加的变化[54]和重力铸造和高压铸造Mg-4Ce-xAl-0.5Mn合金热导率随Al含量的变化[58]
Fig. 8 Variation of thermal conductivity variation of solution Mg-12Gd alloy with aging time[54](a) and variation of thermal conductivity of Mg-4Ce-xAl-0.5Mn alloy with Al content increasing in GC and HPDC condition[58](b)
3 耐腐蚀稀土镁合金
3.1 镁合金的腐蚀机制
由于镁的化学性质较为活泼,在空气中、酸性、中性环境中存在严重的电化学腐蚀问题,导致镁合金构件在服役过程中极易遭受腐蚀失效破坏。镁腐蚀性能差的根本原因在于镁的电极电位低(标准电极电位-2.37 V),比铁低约2 V,比铝低约0.7 V[59]。从镁合金微观组织来看,具有低电位的基体相(α-Mg)常作为阳极,杂质或第二作为阴极,两者之间发生微电偶腐蚀,加剧镁合金的腐蚀失效。同时,镁表面自然生成的表面膜(通常为MgO或Mg(OH)2)致密性差,在氯离子作用下极易发生破裂,无法有效保护镁基体,使得镁合金在氯离子潮湿环境下的腐蚀非常严重。
3.2 稀土对镁合金耐腐蚀性的影响
前期大量研究表明,合金化是提高镁合金耐腐蚀性能最有效的途径[59],而稀土元素由于其特殊的化学性质,能够通过影响基体相与第二相之间的电位差、调控合金中第二相的形貌与分布以及形成致密的氧化膜等方面,有效提高镁合金的耐腐蚀性能。
LIU等[60]研究发现,在AM60合金中添加少量的轻稀土元素Ce和La后,稀土合金元素能够与Al元素形成杆状形貌的γ-Al4(Ce,La)相,同时减少了β-Mg17Al12相的生成。与β相相比,γ相具有较低的电位,缩小了γ相与α-Mg相之间的电位差,从而降低发生微电偶腐蚀的驱动力。另外,镁合金表面生成的含稀土的氧化膜的致密性也优于氧化镁,能够有效阻断腐蚀反应的持续进行,从而大幅度降低镁合金的腐蚀速率,改善镁合金的耐腐蚀性。ZHOU等[61]实验探究了稀土元素Ho对AZ91D镁合金耐蚀性能的影响。结果表明,Ho元素加入后,可以形成更加活泼的含Ho元素金属间化合物,降低了与镁基体之间的电位差,削弱了合金的微电偶腐蚀。除了与镁基体的电位差较大的第二相,镁合金中往往还存在较多的杂质,这些杂质相与基体电位差较大,因此极易加速镁合金的电偶腐蚀。稀土元素的添加能够与杂质形成中间化合物,净化镁合金基体,降低有害杂质对腐蚀性能的影响。研究表明,Ce、La、Nd、Pr和Ho元素能够和有害杂质元素(Fe、Ni和Cu)形成金属间化合物,进而减少杂质相的含量,缓解由杂质与镁基体的电位差而导致的微电偶腐蚀问题[59, 61-62]。ZHOU等[61]在AZ91D中添加Ho元素,发现镁合金中杂质Fe元素含量大大降低,抗腐蚀性能得到显著提高。
除了改变第二相与基体相之间的电位差,稀土元素对于调控合金中第二相形貌及分布,改善镁合金的耐腐蚀性能具有重要的作用。前期,ZHANG等[63]在AZ91中添加稀土元素Y,能够减小β相尺寸的同时,使其在α-Mg晶界处的网状分布更连续且均匀,这种分布可以产生腐蚀阻挡效应,提高合金的耐蚀性能,使其自腐蚀速率减小至 0.6 g/(m2·h),仅为AZ91的1/10。此外,LUNDER等[64]发现AE42合金中的Al11MM3相(MM为混合稀土:50% Ce,25% La,20% Nd,3% Pr)也可以起到类似β相的阻止腐蚀扩展的作用,形成细小、均匀网状分布的第二相,有利于提升镁合金的耐蚀性能。上海交通大学曾小勤团队[24]研究发现具有包晶组织形貌的Mg-4Sc-1Y合金的耐腐蚀性能十分优异,在3.5%NaCl(质量分数)溶液中的析氢速度仅为0.13 mL/(cm2·d)(见图9(a)),其腐蚀速率已经与高纯镁相当。究其原因,首先由于Y元素易在包晶组织中的贫Sc区富集,降低了贫Sc区和富Sc区的电位差,同时形成了富Y区包围富Sc区的连续胞状网络结构,产生良好的腐蚀阻挡效应,从而有效抑制微电偶腐蚀的发生,如图9(b)所示。除此之外,表面膜中同时含有Sc2O3和Y2O3,改善膜层致密性,进一步提高了Mg-Sc-Y的抗腐蚀性。
除此以外,通过加入稀土元素有可能在镁表面形成致密和稳定的氧化物或氢氧化物膜层,阻断腐蚀反应的持续进行,从而大幅度降低镁合金的腐蚀速率。ROSALBINO等[65-66]报道在Mg-Al合金中添加Er,合金表面会生成Mg(OH)2和稀土氧化物的致密复合膜层,其膜层的保护性得到大幅度提高,合金的腐蚀电流仅为AM60的一半。另外,相关研究表明,La、Ce、Y、Nd、Gd、Er等稀土元素能够提高镁合金腐蚀后的氧化物或者氢氧化物的致密度,有效地保护合金基体不被继续腐蚀[62]。综上所述可知,稀土元素在改善镁合金耐腐蚀性能方面发挥了显著作用。
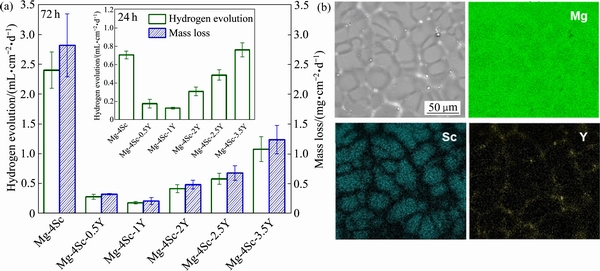
图9 Mg-Sc-Y 合金在3.5%NaCl溶液中的析氢和质量损失腐蚀速率和Mg-4Sc-1Y合金的SEM像和EDS分析结果[24]
Fig. 9 Hydrogen evolution and mass loss of Mg-Sc-Y alloys immersed in 3.5%NaCl(a) and SEM image and EDS mappings of Mg, Sc, Y in Mg-4Sc-1Y alloys[24](b)
4 总结与展望
如前所述,添加稀土元素是改善镁合金结构性能及功能性最直接有效的手段。除了传统的强化作用,稀土元素能够通过调控镁合金中织构、变形机制、第二相析出行为以及析出相化学性质、形貌分布等,有效改善镁合金的塑性变形能力、导热性能及耐腐蚀性能,有望实现结构力学性能及功能性能的同时提升,为研发结构功能一体化的高性能镁合金提供新的设计思想。
然而,稀土元素种类众多,各种稀土元素对镁合金性能的影响较为复杂,其影响机制仍处于研究阶段。也正是由于稀土元素的复杂作用,如何高效准确地调控稀土元素的种类及含量,兼顾镁合金结构性能与功能性,是科研工作者急需思考的问题。因此,未来高性能稀土镁合金的设计和研发还需要在多个方面进行完善和发展。一是深化不同稀土元素对镁合金性能影响机理的研究。从更深层物理角度剖析稀土对镁合金本征性能的影响规律,从而有针对性的对镁合金性能进行优化。二是基于稀土元素对镁合金性能的影响机制,建立准确的高性能镁合金设计准则。通过合理地优化筛选稀土元素种类并调控其含量,实现兼顾镁合金结构性能与功能性能,真正实现高性能镁合金的科学设计。
REFERENCES
[1] POLLOCK T M. Weight loss with magnesium alloys[J]. Science, 2010, 328(5981): 986-987.
[2] 丁文江, 曾小勤. 中国Mg材料研发与应用[J].金属学报, 2010, 46(11): 1450-1457.
DING Wen-jiang, ZENG Xiao-qin. Research and applications of magnesium in China[J]. Acta Metallurgica Sinica, 2010, 46(11): 1450-1457.
[3] 曾小勤. 稀土镁合金研究与应用进展[J]. 稀土信息, 2016(2): 26-29.
ZENG Xiao-qin. Research and applications progress of Mg-RE alloys[J] Rare Earth Information, 2016(2): 26-29.
[4] 丁文江, 吴玉娟, 彭立明, 等. 高性能镁合金研究及应用的新进展[J]. 中国材料进展, 2010, 29(8): 37-45, 36.
DING Wen-jiang, WU Yu-juan, PENG Li-ming, et al. Research and application developmente of advanced magnesium alloys[J]. Materials China, 2010, 29(8): 37-45, 36.
[5] 李德辉, 董 杰, 曾小勤, 等. 高性能稀土镁合金研究进展[J]. 材料导报, 2005, 19(8): 51-54.
LI De-hui, DONG Jie, ZENG Xiao-qin, et al. Research progress of high-performance magnesium rare-earth alloys[J]. Materials Review, 2005, 19(8): 51-54.
[6] ALI Y, QIU D, JIANG B, et al. Current research progress in grain refinement of cast magnesium alloys: a review article[J]. Journal of Alloys and Compounds, 2015, 619: 639-651.
[7] STANFORD N. The effect of rare earth elements on the behaviour of magnesium-based alloys: Part 2-recrystallisation and texture development[J]. Materials Science and Engineering: A, 2013, 565: 469-475.
[8] ZHONG L, PENG J, SUNG S, et al. Microstructure and thermal conductivity of as-cast and as-solutionized Mg-rare earth binary alloys[J]. Journal of Materials Science & Technology, 2017, 33(11): 1240-1248.
[9] DAS S K, KANG Y B, HA T, et al. Thermodynamic modeling and diffusion kinetic experiments of binary Mg-Gd and Mg-Y systems[J]. Acta Materialia, 2014, 71: 164-175.
[10] 何上明. Mg-Gd-Y-Zr(-Ca)合金的微观组织演变、性能和断裂行为研究[D]. 上海: 上海交通大学, 2007.
HE Shang-ming. Study on the microstructural evolution, properties and fracture behavior of Mg-Gd-Y-Zr(-Ca) alloys[D]. Shanghai: Shanghai JiaoTong University, 2007.
[11] TEHRANCHI A, YIN B, CURTIN W A. Solute strengthening of basal slip in Mg alloys[J]. Acta Materialia, 2018, 151: 56-66.
[12] HE S M, ZENG X Q, PENG L M. Precipitation in a Mg-10Gd-3Y-0.4Zr(wt.%) alloy during isothermal ageing at 250 ℃[J]. Journal of Alloys and Compounds, 2006, 421(1/2): 309-313.
[13] 曾小勤, 朱庆春, 李扬欣, 等. 镁合金中的第二相颗粒强化[J]. 中国材料进展, 2019, 38(3): 193-204, 250.
ZENG Xiao-qin, ZHU Qing-chun, LI Yang-xin et al. Second phase particle strengthening in magnesium alloys[J]. Materials China, 2019, 38(3): 193-204, 250.
[14] NIE J F. Effects of precipitate shape and orientation on dispersion strengthening in magnesium alloys[J]. Scripta Materialia, 2003, 48(8): 1009-1015.
[15] NIE J F. Precipitation and hardening in magnesium alloys[J]. Metallurgical and Materials Transactions A, 2012, 43(11): 3891-3939.
[16] 周丽萍, 曾小勤, 李德江, 等. Mg-12Gd 合金的时效析出行为[J]. 中国有色金属学报, 2015, 25(6): 1409-1416.
ZHOU Li-ping, ZENG Xiao-qin, LI De-jiang, et al. Ageing precipitation behavior of Mg-12Gd alloy[J]. The Chinese Journal of Nonferrous Metals, 2015, 25(6): 1409-1416.
[17] SMOLA B,
J, et al. Significance of stable and metastable phases in high temperature creep resistant magnesium-rare earth base alloys[J]. Journal of Alloys and Compounds, 2004, 378(1/2): 196-201.
[18] MORENO I P, NANDY T K, JONES J W, et al. Microstructural stability and creep of rare-earth containing magnesium alloys[J]. Scripta Materialia, 2003, 48(8): 1029-1034.
[19] HUANG Y, GAN W, KAINER N. Role of multi- microalloying by rare earth elements in ductilization of magnesium alloys[J]. Journal of Magnesium and Alloys, 2014, 2(1): 1-7.
[20] IMANDOUST A, BARRETT C D, AL-SAMMAN T, et al. A review on the effect of rare-earth elements on texture evolution during processing of magnesium alloys[J]. Journal of Materials Science, 2017, 52(1): 1-29.
[21] YIN H M, JIANG B, HUANG X Y, et al. Effect of Ce addition on microstructure of Mg-9Li alloy[J]. Transactions of Nonferrous Metals Society of China, 2013, 23(7): 1936-1941.
[22] 袁付庆, 张 静, 方 超. 稀土元素对镁合金晶粒细化的研究[J]. 热加工工艺, 2012, 41(2): 30-33, 37.
YUAN Fu-qing, ZHANG Jing, FANG Chao. Effects of rare earth addition on grain refinement of magnesium alloy[J]. Hot Working Technology, 2012, 41(2): 30-33, 37.
[23] 刘婷婷, 潘复生. 镁合金“固溶强化增塑”理论的发展和应用[J]. 中国有色金属学报, 2019, 29(9): 2050-2063.
LIU Ting-ting, PAN Fu-sheng. Development and application of “solid solution strengthening and ductilizing” for magnesium alloys[J]. The Chinese Journal of Nonferrous Metals, 2019, 29(9): 2050-2063.
[24] ZHAO P, XIE T, XU X, et al. Designing high corrosion resistant peritectic magnesium alloys via Sc and Y addition[J]. Metallurgical and Materials Transactions A, 2020, 51(5): 2509-2522.
[25] BURKE E C, HIBBARD W R. Plastic deformation of magnesium single crystals[J]. JOM, 1952, 4: 295-303.
[26] CHAPUIS A, DRIVER J H. Temperature dependency of slip and twinning in plane strain compressed magnesium single crystals[J]. Acta Materialia, 2011, 59(5): 1986-1994.
[27] YOSHINAGA H,HORIUCHI R. On the nonbasal slip in magnesium crystals[J]. Transactions of the Japan Institute of Metals, 1964, 5(1): 14-21.
[28] YOSHINAGA H, HORIUCHI R. Deformation mechanisms in magnesium single crystals compressed in the direction parallel to hexagonal axis[J]. Transactions of the Japan Institute of Metals, 1963, 4(1): 1-8.
[29] OBARA T, YOSHINGA H, MOROZUMI S. {1122}〈1123〉slip system in magnesium[J]. Acta Metallurgica, 1973, 21(7): 845-853.
[30] WONSIEWICZ B C, BACKOFEN W A, et al. Plasticity of magnesium cyrstals[M]. The Metallurgical Society of AIME, 1967: 239-1422.
[31] WANG J. High throughput investigation of diffusion and solid solution hardening of HCP Mg alloys[D]. Madrid: Universidad Politecnica de Madrid, 2019.
[32] STANFORD N, BARNETT M R. The origin of “rare earth” texture development in extruded Mg-based alloys and its effect on tensile ductility[J]. Materials Science and Engineering: A, 2008, 496(1/2): 399-408.
[33] LIU B Y, LIU F,YANG N, et al. Large plasticity in magnesium mediated by pyramidal dislocations[J]. Science, 2019, 365(6448): 73-75.
[34] SOMEKAWA H, YAMAGUCHI M, OSAWA Y, et al. Material design for magnesium alloys with high deformability[J]. Philosophical Magazine Structure & Properties of Condensed Matter, 2015, 95(8): 869-885.
[35] LIU G, ZHANG J, XI G. Designing Mg alloys with high ductility: Reducing the strength discrepancies between soft deformation modes and hard deformation modes[J]. Acta Materialia, 2017, 141: 1-9.
[36] WU Z, AHMAD R, YIN B, S, et al. Mechanistic origin and prediction of enhanced ductility in magnesium alloys[J]. Science, 359(6374): 447-452.
[37] LI W, WANG L, ZHOU B C, et al. Grain-scale deformation in a Mg-0.8wt%Y alloy using crystal plasticity finite element method[J]. Journal of Materials Science & Technology, 2019, 35(10): 2200-2206.
[38] CHINO Y, KADO M, MABUCHI M, et al. Enhancement of tensile ductility and stretch formability of magnesium by addition of 0.2wt%(0.035at%)Ce[J]. Materials Science and Engineering: A, 2008, 494(1/2): 343-349.
[39] WU B L, WAN G, DU X H, et al. The quasi-static mechanical properties of extruded binary Mg-Er alloys[J]. Materials Science and Engineering: A, 2013, 573: 205-214.
[40]
S, ZAEFFERER S, SCHESTAKOW I, et al. On the role of non-basal deformation mechanisms for the ductility of Mg and Mg-Y alloys[J]. Acta Materialia, 2011, 59(2): 429-439.
[41] KIM K H, JEON J B, KIM N J, et al. Role of yttrium in activation of
slip in magnesium: an atomistic approach[J]. Scripta Materialia, 2015, 108: 104-108.
[42] WANG L, HUANG Z, WANG H, et al. Study of slip activity in a Mg-Y alloy by in situ high energy X-ray diffraction microscopy and elastic viscoplastic self-consistent modeling[J]. Acta Materialia, 2018, 155: 138-152.
[43] HUANG Z.WANG L, ZHOU B, et al. Observation of non-basal slip in Mg-Y by in situ three-dimensional X-ray diffraction[J]. Scripta Materialia, 2018, 143: 44-48.
[44] SABAT R K, BRAHME A P, MISHRA R K, et al. Ductility enhancement in Mg-0.2%Ce alloys[J]. Acta Materialia, 2018, 161: 246-257.
[45]
NEUGEBAUER J, et al. Basal and non-basal dislocation slip in Mg-Y[J]. Materials Science and Engineering: A, 2013, 576: 61-68.
[46] LIU Z R, LI D Y. The electronic origin of strengthening and ductilizing magnesium by solid solutes[J]. Acta Materialia, 2015, 89: 225-233.
[47] 杨嘉傲, 房宇轩, 刘宝胜, 等. 导热镁合金的发展和研究现状[J]. 铸造设备与工艺, 2019(6): 55-58, 64.
YANG Jia-ao, FANG Yu-xuan, LIU Bao-sheng, et al. Development and research status of thermal conductive Mg alloys[J]. Foundry Equipment and Technology, 2019(6): 55-58, 64.
[48] KLEMENS P G, WILLIAMS R K. Thermal conductivity of metals and alloys[J]. International Metals Reviews, 1986, 31(1): 197-215.
[49] LI S, YANG X, HOU J, et al. A review on thermal conductivity of magnesium and its alloys[J]. Journal of Magnesium and Alloys, 2020, 8(1): 78-90.
[50] 苏创业. 基于固溶原子和第二相的镁合金导热机制研 究[D]. 上海: 上海交通大学, 2019.
SU Chuang-ye. Thermal mechanism of magnesium alloys based on solute atom and second phase[D]. Shanghai: Shanghai Jiao Tong University, 2019.
[51] YAMASAKI M, KAWAMURA Y. Thermal diffusivity and thermal conductivity of Mg-Zn-rare earth element alloys with long-period stacking ordered phase[J]. Scripta Materialia, 2009, 60(4): 264-267.
[52] CHEN C J, WANG Q D, YIN D D. Thermal properties of Mg-11Y-5Gd-2Zn-0.5Zr (wt.%) alloy[J]. Journal of Alloys and Compounds, 2009, 487(1/2): 560-563.
[53] LIU X, WU Y, LIU Z, et al. Thermal and electrical conductivity of as-cast Mg-4Y-xZn alloys[J]. Materials Research Express, 2018, 5(6): 066532.
[54] ZHONG L, WANG Y, GONG M, et al. Effects of precipitates and its interface on thermal conductivity of Mg-12Gd alloy during aging treatment[J]. Materials Characterization, 2018, 138: 284-288.
[55] SU C, LI D, LUO A A, et al. Effect of solute atoms and second phases on the thermal conductivity of Mg-RE alloys: A quantitative study[J]. Journal of Alloys and Compounds, 2018, 747: 431-437.
[56] TAO B, QIU R, ZHAO Y, et al. Effects of alloying elements (Sn, Cr and Cu) on second phase particles in Zr-Sn-Nb-Fe-(Cr,Cu) alloys[J]. Journal of Alloys and Compounds, 2018, 748: 745-757.
[57] GUO H, LIU S, HUANG L D, et al. Thermal conductivity of As-cast and annealed Mg-RE binary alloys[J]. Metals, 2021, 11(4): 554.
[58] SU C, LI D, LUO A A, et al. Quantitative study of microstructure-dependent thermal conductivity in Mg-4Ce-xAl-0.5Mn alloys[J]. Metallurgical and Materials Transactions A, 2019, 50(4): 1970-1984.
[59] 李凌杰, 李芳君, 雷惊雷, 等. 合金元素对镁合金耐腐蚀性能影响的研究进展[J]. 材料导报A, 2011, 25(9): 110-113.
LI Ling-jie, LI Fang-jun, LEI Jing-lei, et al. Research progress in effect of alloying elements on anti-corrosion performance of magnesium alloys[J]. Materials Review, 2011, 25(9): 110-113.
[60] LIU W, CAO F, CHANG L, et al. Effect of rare earth element Ce and La on corrosion behavior of AM60 magnesium alloy[J]. Corrosion Science, 2009, 51(6): 1334-1343.
[61] ZHOU X, HUANG Y, WEI Z, et al. Improvement of corrosion resistance of AZ91D magnesium alloy by holmium addition[J]. Corrosion Science, 2006, 48(12): 4223-4233.
[62] XIE J, ZHANG J, YOU Z, et al. Towards developing Mg alloys with simultaneously improved strength and corrosion resistance via RE alloying[J]. Journal of Magnesium and Alloys, 2021, 9(1): 41-56.
[63] ZHANG J, NIU X, QIU X, et al. Effect of yttrium-rich misch metal on the microstructures, mechanical properties and corrosion behavior of die cast AZ91 alloy[J]. Journal of Alloys and Compounds, 2009, 471(1/2): 322-330.
[64] LUNDER O, NISANCIOGLU K. Progress in the understanding and prevention of corrosion[M]. London: The Institute of Materials, 1993.
[65] ROSALBINO F, ANGELINI E, DE-NEGRI S, et al. Effect of erbium addition on the corrosion behaviour of Mg-A1 alloys[J]. Intermetallics, 2005, 13 (1): 55-60.
[66] ROSALBINO F, ANGELINI E, DE-NEGRI S, et al. Electrochemical behaviour assessment of novel Mg-rich Mg-Al-RE alloys (RE=Ce, Er)[J]. Intermetallics, 2006, 14(12): 1487-1492.
Research progress of high-performance rare earth magnesium alloys
ZENG Xiao-qin1, 2, CHEN Yi-wen1, WANG Jing-ya1, DING Wen-jiang1
(1. National Engineering Research Center of Light Alloy Net Forming, Shanghai Jiao Tong University, Shanghai 200240, China;
2. State Key Laboratory of Metal Matrix Composites, Shanghai Jiao Tong University, Shanghai 200240, China)
Abstract: Magnesium alloys, as the lightest structural metals, are considered to be the promising materials to achieve the lightweight of aerospace, transportation and digital electronic communication. However, magnesium alloys still exhibit several limitations in the application. It has been reported that rare earth (RE) elements generally play a critical role in the improvement of the performance for Mg alloys. This work focuses on the effect of RE elements on the microstructure and the performance of Mg alloys, including the plastic deformation behavior, thermal conductivity and corrosion resistance. It has been found that the addition of RE elements can improve the ductility through weakening the texture and controlling the deformation mechanisms. Furthermore, the thermal conductivity of Mg alloys can be enhanced through altering the precipitation behavior. The corrosion resistance is significantly promoted by influencing the chemical properties, morphology and distribution of precipitates. This work looks forward to the development of high-performance structure-function integration Mg-RE alloys.
Key words: rare earth-magnesium alloys; ductility; thermal conductivity; corrosion resistance
Foundation item: Project(51825101, 52001199) supported by the National Natural Science Foundation of China
Received date: 2021-09-29; Accepted date: 2021-10-29
Corresponding author: ZENG Xiao-qin; Tel: +86-21-54742301; E-mail: xqzeng@sjtu.edu.cn
(编辑 李艳红)
基金项目:国家自然科学基金资助项目(51825101, 52001199)
收稿日期:2021-09-29;修订日期:2021-10-29
通信作者:曾小勤,教授,博士;电话:021-54742301;E-mail:xqzeng@sjtu.edu.cn
摘 要:镁合金作为最为轻质的金属结构材料,是实现航空航天、交通运输以及电子通讯等轻量化的重要材料。然而,镁合金在应用过程中仍面临一系列瓶颈问题。研究结果表明,稀土元素对于改善镁合金的性能具有至关重要的作用。本文聚焦稀土元素对镁合金组织的作用机制,讨论了稀土元素对镁合金塑性变形能力、导热性能及耐腐蚀性能的影响规律。总结发现稀土元素能够通过调控织构和变形过程中的滑移机制提高塑性,影响第二相的析出行为,改善导热性能;改变析出相的化学性质、形貌与分布等提高耐腐蚀性能。展望通过调控稀土元素设计新型高性能结构功能一体化稀土镁合金的发展方向。