废旧锂离子电池回收利用
雷舒雅1,徐 睿1,孙 伟1,徐盛明2,杨 越1
(1. 中南大学 资源加工与生物工程学院,长沙 410083;
2. 清华大学 核能与新能源技术研究院,北京 100084)
摘 要:
随着电动汽车等新能源产业的发展,锂离子电池需求量不断增大,而大量锂离子电池的使用,必将引发报废潮。一方面,废旧锂离子电池易燃易爆,含有氟化物等毒害组分,必须进行无害化处理;另一方面,废旧锂离子电池具有资源属性,含有丰富的镍、钴、锰、锂等有价金属组分。因此,废旧锂离子电池的回收不仅可以保护环境,而且能缓解我国战略金属资源紧张局面,促进新能源产业健康可持续发展,已成为目前全球研究的一个热点方向。本文系统梳理了废旧锂离子电池材料回收的最新研究进展,重点介绍了火法和湿法回收方法,详细分析了湿法冶金过程中的破碎、浸出、分离和再生技术,并对未来的发展趋势和研究重点进行了展望,旨在为废旧锂离子电池有价金属组分的高效回收利用提供参考。
关键词:
废旧锂离子电池;有价组分;回收;循环利用;
文章编号:1004-0609(2021)-11-3303-17 中图分类号:TM911.1;TF111;X789 文献标志码:A
引文格式:雷舒雅, 徐 睿, 孙 伟, 等. 废旧锂离子电池回收利用[J]. 中国有色金属学报, 2021, 31(11): 3303-3319. DOI: 10.11817/j.ysxb.1004.0609.2021-42256
LEI Shu-ya, XU Rui, SUN Wei, et al. Recycling of spent lithium-ion battery[J]. The Chinese Journal of Nonferrous Metals, 2021, 31(11): 3303-3319. DOI: 10.11817/j.ysxb.1004.0609.2021-42256
锂离子电池循环性能好、比容量高、安全性好,广泛用于各种电子产品、电动汽车和航空航天等领域[1]。锂离子电池由外壳和电池内芯组成,内芯是锂离子电池的核心部分,主要由正极材料、隔膜、负极材料和电解液构成。正极材料是决定锂离子电池性能最重要的组成部分,常用的正极材料包括磷酸铁锂(LiFePO4)、钴酸锂(LiCoO2)和镍钴锰酸锂(LiNixCoyMn1-x-yO2)等。负极材料在充放电过程中完成锂离子的可逆嵌入和脱出,目前常用的负极材料主要为石墨。隔膜将锂离子电池的正负极分隔,避免因正负电极接触造成短路。锂离子电池电解液是电池中离子传输的载体。一般由锂盐和有机溶剂组成,在锂离子电池正、负极之间起到传导离子的作用[2]。锂离子电池的工作原理如图1所示[3]。充电时,锂离子从正极材料脱出,经过电解质和隔膜储存在负极;放电时,锂离子从负极脱出嵌入正极。电池的正极、负极以及总的反应式分别表示如下(以LiCoO2正极材料为例):
LiCoO2
Li1-xCoO2+xLi++xe (1)
6C+xLi++xe
LixC6 (2)
LiCoO2
Li1-xCoO2+LixC6 (3)
近年来,随着电动汽车等新能源产业的发展,锂离子电池需求量不断增多,我国成为全球主要的锂离子电池产销国。2019年,我国锂离子电池产量达到157.22亿只,2020年前三季度,我国锂离子电池产量达到125.67亿只,同比增长7.8%[4]。作为消耗品,锂离子电池平均使用寿命仅有3~5年,报废后的锂离子电池中含有残余的电能,存在安全隐患。同时,废电池中含有毒害金属组分(钴、锰等)和大量的有机物(黏结剂、电解液等),将带来严重的环境污染问题[5-6]。因此,实现废旧锂离子电池的无害化处理已迫在眉睫。
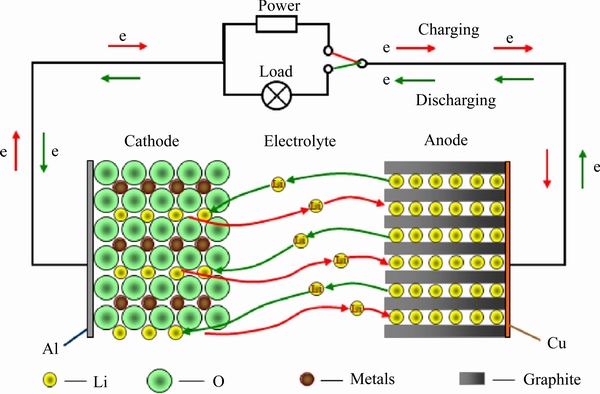
图1 锂离子电池工作原理图[3]
Fig. 1 Principles of LIBs[3]
与此同时,回收废旧锂离子电池有利于缓解我国金属资源短缺、实现锂电新能源产业可持续发展。一方面,废旧锂离子电池中富含多种有价金属元素如钴、锰、镍、锂等(见图2),镍和钴的总含量达到10%~20%、锂含量达到1%~4%,废旧锂离子电池中的金属含量远高于原生矿产资源[7],可视为储量丰富的“城市矿山”。以LiNi1/3Co1/3Mn1/3O2型废旧锂离子电池为例,其中钴和镍的含量分别为8.45%和14.84%,而硫化矿中钴和镍的含量分别为0.05%~1.0%和1.5%~3%[8]。另一方面,我国镍、钴资源匮乏,但镍、钴消费需求旺盛,供不应求,我国镍和钴资源的对外依存度分别达到80%和97%,处于较高水平[9]。虽然我国中西部地区锂矿资源储存丰富,但随着锂电池产业的发展,锂资源的需求量和价格不断攀升。锂、钴等原材料价格上涨给下游锂电产业造成巨大压力。若能将废电池安全、无害化处理,实现有价金属循环利用,不仅可以避免废电池造成的环境污染问题,而且能扩宽镍、钴、锂等紧缺资源的来源,推动锂离子电池新能源产业健康发展。目前,废锂离子电池回收按方法可分为火法回收和湿法回收,回收流程图如图3所示[10]。
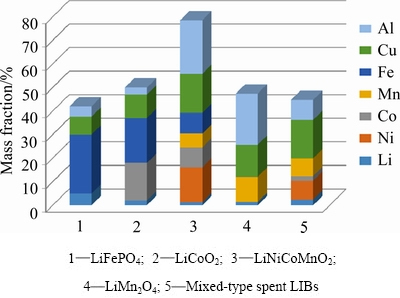
图2 不同类型废电池中有价金属含量
Fig. 2 Content of valuable metals in different types of spent LIBs
1 火法回收
火法回收是将放电后的废旧锂离子电池放入温度高于1000 ℃的熔炼炉中进行高温冶炼。在冶炼过程中,废旧锂离子电池中的隔膜、电解液、黏结剂及负极石墨等有机物燃烧脱除,熔点低于反应温度的金属形成合金,低沸点的金属及其化合物通过冷凝回收,其他杂质转移到渣相或形成气体[11]{Tang, 2019 #32}。如REN等[12]发现正极废料中的钴和镍组分可被金属铝或石墨还原生成金属镍和钴(见反应式(4)~(6)),还原产物金属镍、钴和金属铜优先形成合金相,铝以三氧化二铝的形式存在于炉渣中,石墨以一氧化碳形式蒸发。在铁橄榄石渣相系统(FeO-SiO2-Al2O3)中,控制渣相和废旧锂离子电池质量比4:1、反应温度1450 ℃和反应时间为30 min,98.83% Co、98.39% Ni和93.57% Cu以Fe-Co- Cu-Ni合金的形式被回收。在MnO-SiO2-Al2O3渣相系统中见图4)[13],废旧锂离子电池中铜、钴和镍的回收率可分别提高到98.67%、99.84%和99.77%,炉渣中锰和锂的回收率分别达到44.30%和50.28%。
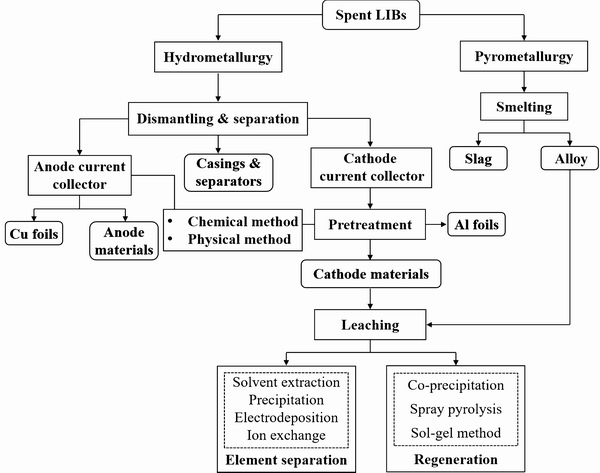
图3 废旧锂离子电池流程图[10]
Fig. 3 Flow chart of recycling spent lithium-ion battery[10]
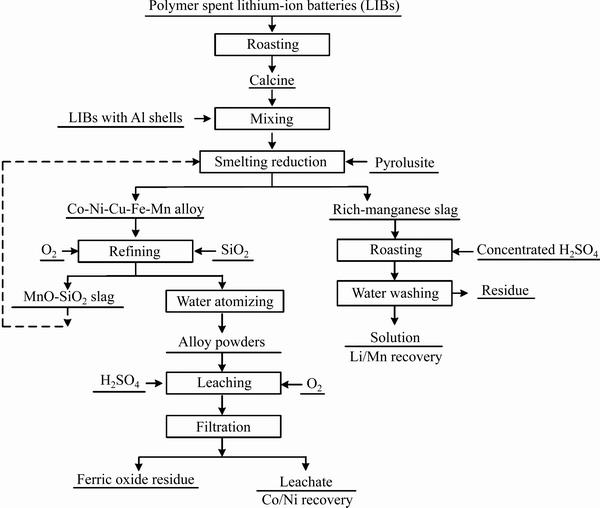
图4 火法冶金回收废旧锂离子电池流程图[13]
Fig. 4 Flow chart of Co, recycling Ni, Cu, Mn and Li from spent LIBs[13]
2LiCoO2+2Al=Li2O+2Co+Al2O3 (4)
2LiCo1-xNixO2+3C=Li2O+(1-x)/2Co+x/2Ni+3CO(g) (5)
4LiCo1-xNixO2+Al=2Li2O+(1-x)/4Co+x/4Ni+2Al2O3 (6)
目前,火法回收在比利时优美科公司得到产业化应用,开发的Val'Eas工艺能将退役锂离子电池中的镍、钴、铜、铁组分以合金产品形式回收(见图5[14]),但是仍有部分锰和锂损失在炉渣中[15]。综合来看,火法回收可混合处理不同类型废旧锂离子电池,显现出回收流程短、操作简单、处理量大等优点[16]。但在实际应用中,该回收方法存在石墨难以得到回收、损失部分金属锂和锰等问题。同时,由于反应过程中采用高温处理,电池中黏结剂和石墨的燃烧会产生有害气体造成大气污染,所以在回收过程中需要配置气体回收装置,增加基建投资[17]{Vieceli, 2018 #24}。
2 湿法回收
湿法回收主要是借助湿法冶金的方法将废旧锂离子电池中的有价金属组分进行分离和富集,得到金属可溶性盐或沉淀等产品[18-19],具有投资少、生产灵活、金属回收率高等优点。废旧锂离子电池湿法回收主要包括预处理、湿法浸出、净化分离和材料再生等步骤[20-21]。
2.1 预处理
预处理是为了将废旧锂离子电池的外壳、铝箔、铜箔和负极极粉石墨与正极极粉分开,脱除有机物,降低金属元素浸出分离和材料再生的难度和成本。目前,将正极、负极极粉从集流体铝箔、铜箔剥离的方法可分为物理法和化学法。
2.1.1 物理法
物理法利用物料的密度、粒度和磁性等差异进行分选,分别对应于重选、筛分和磁选等分选法。多级粉碎-筛分技术是剥离富集极粉最常用的一种物理分选方法,包括粉碎、过筛、磁选、精细粉碎和分级等。主要作用是将电池外壳和金属化合物分离,同时富集电极材料,提高回收率,减轻后续浸出液分离纯化难度。SHIN等[22]提出采用粉碎、筛选、磁性分离、精细粉碎技术以达到钴酸锂颗粒的富集,该方法可用于工业回收废旧锂离子电池。但是在破碎过程中,为保证正极、负极极粉从集流体铝箔、铜箔完全解离,通常需要将集流体破碎至很细的粒度,导致大量细微铜/铝粉末进入到富集的极粉中,铜、铝金属含量通常超过5%,后续再生除杂难度大。
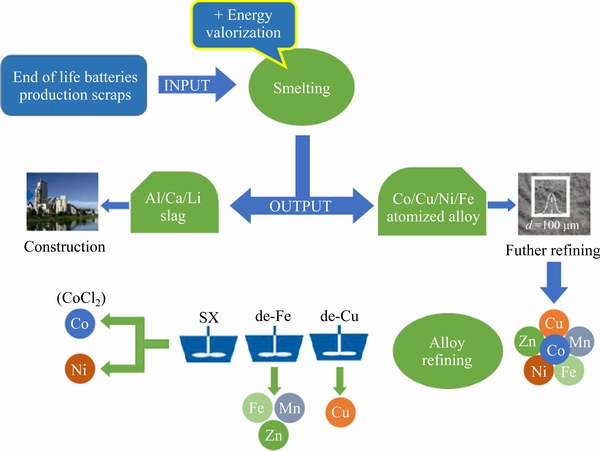
图5 优美科火法回收废旧锂电池的Val'Eas工艺流程图[14]
Fig. 5 Flow chart of Val'Eas process in Umicore for recycling spent lithium batteries[14]
2.1.2 化学法
与物理法相比,化学法分离的精度更高。从集流体上剥离极粉常用的化学方法有三种:有机溶剂溶解法、氢氧化物脱铝法和热分解法。有机溶剂溶解法利用相似相溶原理,一般采用N-甲基吡咯烷酮(NMP)、N,N-二甲基酰胺(DMF)等为溶剂,将黏结剂(聚偏氟乙烯,PVDF)直接溶解,进而使极粉与金属箔片分离[23]。采用该方法分离富集极粉的效果好,铜箔和铝箔不被损坏,可直接回收利用,但却存在成本高的缺点。氢氧化物脱铝法主要借助铝易与氢氧化物(常用氢氧化钠)发生化学反应生成偏铝酸盐的性质,采用一定浓度的氢氧化物将铝箔选择性溶解获取正极废料[24]。该方法操作简单,处理量大,但除铝过程产生大量偏铝酸钠溶液,因溶液中同时存在氟、锂、磷和重金属等杂质离子,难以实现铝的综合利用,而碱性废水处理需要消耗大量的酸进行中和处理。热分解法将正极废料高温加热处理,导电剂、黏结剂和电解液中的有机溶剂受热分解而除去[25]。热分解法操作简单,实现正极材料和导电剂、黏结剂的有效分离。但处理过程能耗大,有机物分解产生有害气体,所以在回收过程中需要配置气体净化回收装置。因此,尽管目前废旧锂离子电池预处理技术取得了一定的进展,但在分离效率、环保和经济性仍有进步的空间,亟需开发高效、绿色和低成本的物料分选技术。
2.2 浸出
根据浸出方式的不同,正极废料的浸出分为化学浸出和生物浸出两大类。
2.2.1 化学浸出
化学浸出是指利用酸性或者碱性溶剂将正极废料中的有价元素组分浸出到溶液中[26]。根据浸出试剂不同,化学浸出可分为酸浸和氨浸(见表1)。
酸浸可分为无机酸浸出和有机酸浸出[27]。无机酸浸出是最成熟的浸出技术,用于正极废料浸出的无机酸主要包括硫酸(H2SO4)[28]、盐酸(HCl)[29]或硝酸(HNO3)[30]等。HCl具有一定还原性,浸出时不需借助其他还原剂就可得到较好的浸出效果。LI等[31] 用HCl浸出钴酸锂正极材料,在4 mol/L HCl、浸出温度为80 ℃、浸出时间为2 h的条件下,钴和锂的浸出率分别为99.00%和97.00%。
2LiCoO2+8HCl=2CoCl2+4H2O+2CoLi+Cl2↑ (7)
H2SO4作为浸出剂时,需要加入适量的还原剂(过氧化氢、亚硫酸钠等)将高价金属还原成低价金属。目前,工业上一般采用硫酸和过氧化氢浸出体系,三元废料中镍、钴、锰、锂等金属的浸出率可达到100%。YANG等[32]用H2SO4+H2O2 体系浸出LiNi0.5Co0.2Mn0.3O2型正极废料,反应式如式(8)所示。在最佳浸出条件液固比为10 mL/g、硫酸浓度2 mol/L、0.97 mol/L过氧化氢、浸出温度为80 ℃、浸出时间为30 min的条件下,镍、钴和锂的浸出率几乎达到100%,锰的浸出率达到94.00%。
2LiMO2+3H2SO4+H2O2→Li2SO4+2MSO4+4H2O+O2↑ (M=Ni, Co, Mn) (8)
浸出废旧锂离子电池的有机酸主要包括柠檬酸(C6H8O7)、草酸(H2C2O4)、苹果酸(C4H6O5)和抗坏血酸(C6H8O6)等[33]。ZHOU等[34]用苹果酸加超声强化浸出钴酸锂正极材料。在1.5 mol/L苹果酸、3% H2O2(体积分数)、固液比4 g/L、超声功率95 W、浸出温度为80 ℃、浸出时间为25 min的最佳条件下,锂和钴的浸出率达到98.13%和98.86%;ZENG等[35]用草酸作为浸出剂回收钴酸锂,在固液比15 g/L、浸出温度为95 ℃和浸出时间为150 min的条件下,钴和锂的浸出率分别为97.00%和 98.00%;LI等[36]用醋酸和过氧化氢浸出正极材料LiCo1/3Ni1/3Mn1/3O2,在6% H2O2、醋酸浓度为1 mol/L、固液比20 g/L、浸出温度为70 ℃、浸出时间为60 min条件下,锂、钴、镍和锰的浸出率分别为98.40%、97.70%、97.30%和97.10%。
ZHANG等[37]总结了不同酸浓度、温度、时间、固液比和还原剂用量等参数对金属离子浸出率的影响(见图6)。如图6可见,无机酸浸出正极废料中有价金属具有条件温和、容易控制、金属浸出率高等优点,但是硫酸、盐酸或硝酸等强酸具有强腐蚀性,对设备要求高,而且会产生硫氧化物或氯化物等物质,从而对环境造成二次污染。采用有机酸浸出废旧锂离子电池,浸出率可达到与采用无机酸相近的水平,但由于成本等因素限制,尚难以产业化推广应用。
与酸浸相比,氨浸具有选择性好的特点。有价金属镍、钴、铜等和氨的络合能力强,可形成稳定的金属络合物,而铁、铝等金属离子和氨的络合能力弱,难以被氨溶解到溶液中,进而实现金属元素的选择性浸出分离[38]。WU等[39]研究了氨水-亚硫酸铵-碳酸氢铵浸出体系中锂、镍、钴、铜和铝的浸出行为,发现亚硫酸铵和碳酸氢铵的浓度、浸出时间和温度的变化有利于锂、镍和钴的浸出。在60 ℃、1.5 mol/L氨水、1 mol/L亚硫酸铵、1 mol/L碳酸氢铵、矿浆密度20 g/L和浸出时间180 min的最佳条件下,镍和铜的浸出率接近100%,锂和钴的浸出率分别为60.53%和80.99%。CHEN等[40]采用热处理-氨浸方法,采用(NH4)2SO4-(NH4)2SO3溶液浸出正极废料中有价金属。通过控制(NH4)2SO3的用量,Mn2+形成双盐以(NH4)2Mn(SO3)2·H2O和(NH4)2Mn(SO4)2·6H2O析出,镍、锂和钴以离子或可溶性络合物的形式留在溶液中,实现选择性浸出。利用氨浸的选择性,可减少后续浸出液中金属离子分离的步骤,提高金属回收效率。但氨容易挥发,实际操作难度大,同时会产生氨氮废水,环境风险大。因此,如何实现氨的循环利用,避免二次污染,是氨浸工艺能否实现产业化需要考虑的关键问题。
2.2.2 生物浸出
生物浸出是借助某些微生物的代谢作用,使正极废料中的有价元素转换成水溶性离子,从而实现浸出提取。浸出正极废料的常用菌种包括嗜酸性硫氧化菌、铁氧化菌和黑曲霉等。嗜酸性硫氧化菌和铁氧化菌分别以单质硫和Fe2+作为营养物质,利用代谢生成的H2SO4和Fe3+等物质浸出正极废料中的金属组分[51],黑曲霉则通过在代谢过程中生成的有机酸浸出有价金属元素。XIN等[52]用硫氧化菌和铁氧化菌浸出废旧动力锂离子电池中有价金属。在硫酸和Fe3+催化还原协同作用下,镍、锂、钴和锰四种金属离子的浸出率均可达到95.00%以上;BAHALOO-HOREH等[53]提出用黑曲霉回收废旧手机锂离子电池中有价金属,在矿浆密度(w/v)为1 %下,100% Li、94% Cu、72% Mn、62% Al、45% Ni和38% Co可被浸出到溶液中;HEYDARIAN等[54] 用亚铁酸酸性硫杆菌和硫代酸酸性硫杆菌作为菌种,在3.7%硫酸铁(w/v)、0.5%硫(w/v)、初始pH=1.5、亚铁酸酸性硫杆菌和硫代酸酸性硫杆菌比例为3:2条件下,锂的浸出率达到99%以上,镍的浸出率为89%。
表1 化学浸出处理废锂电池的回收条件和结果
Table 1 Conditions and results of recycling spent LIBs by chemical leaching
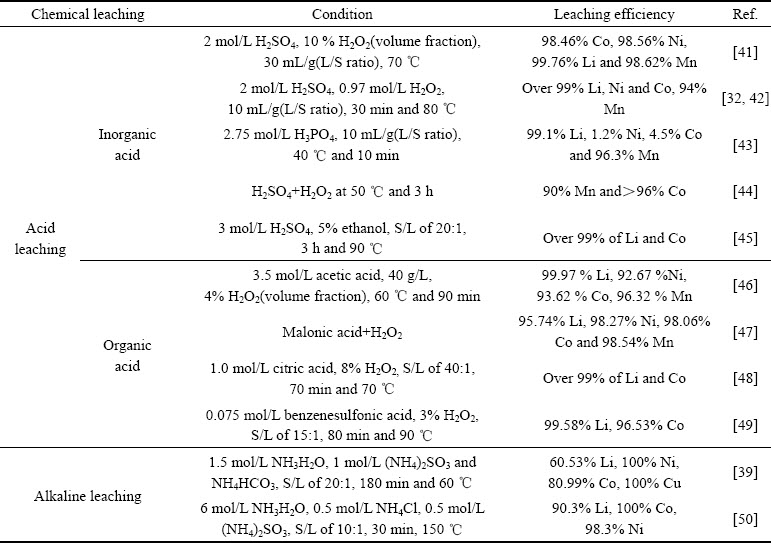
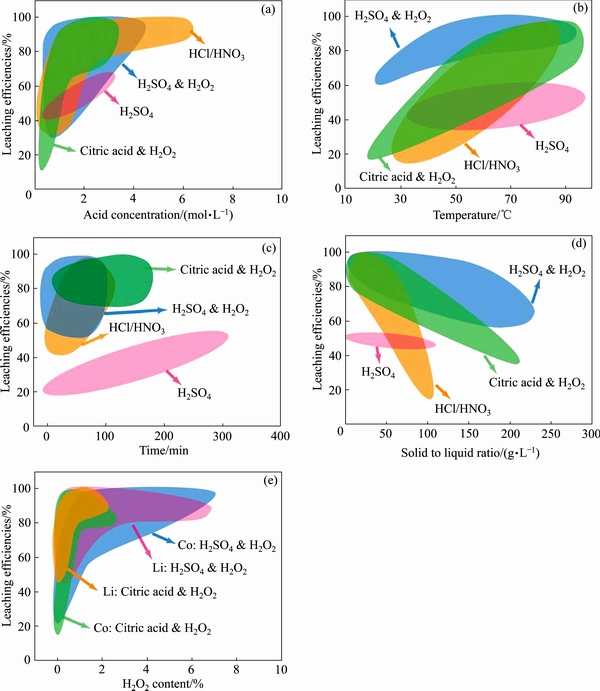
图6 酸浓度、温度、时间、固液比和过氧化氢用量对使用不同种类酸时对钴浸出率的影响[37]
Fig. 6 Effects of acid concentration(a), temperature(b), time(c), S/L ratio(d) and H2O2 content(e) on leaching efficiencies of Co using different acids[37]
表2汇总了锂电池正极废料生物浸出的最新研究成果[53-59]。生物浸出彰显了极佳的浸出效果,但由于存在浸出周期长、对环境条件要求苛刻等问题,限制了生物浸出在废旧锂离子电池回收产业化应用。
2.3 元素分离
由于锂离子电池正极材料成分复杂,导致废旧锂离子电池正极材料浸出液中所含元素种类多(如钴、镍、锂、锰、铜和铝等)。同时,钴、镍和锰均属于过渡金属元素,化学性质相近,分离十分困难。为了从多金属复杂混合溶液中逐一分离相似金属元素,需要借助溶剂萃取、化学沉淀或离子交换等一系列技术方法[60-61]。
溶剂萃取是利用正极废料浸出液中不同有价金属元素在两种互不相溶的溶剂中分配系数的不同,使目标组分从一种溶剂内转移到另外一种溶剂中,进而实现分离的方法。目前,常用的萃取剂包括二-(2-已基己基)磷酸(D2EHPA)、2-乙基己基磷酸单-2-乙基己酯(PC-88A, P507)、二(2,4,4-三甲基戊基)次膦酸(Cyanex 272)、Versatic10和LIX 84等。NGUYEN等[62]采用溶剂萃取法逐一分离回收废旧锂离子电池中的有价金属(见图7(a))。首先,采用离子溶液(ALi-SCN)萃取回收浸出液中的钴元素,钴的萃取率可达到92%;接着,调节萃余液pH值至2,以Aliquat 336和Cyanex 27为萃取剂萃取镍,镍的萃取率可达到99%;而后,再次调节萃余液pH至2,利用离子溶液(ALi-CY)萃取锰,锰的萃取率可达到99%。最后,回收萃余液中的锂,实现钴、镍、锰和锂的逐一分离和回收利用。
表2 生物浸出处理废锂电池的回收条件和结果
Table 2 Conditions and results of recycling spent LIBs by bioleaching
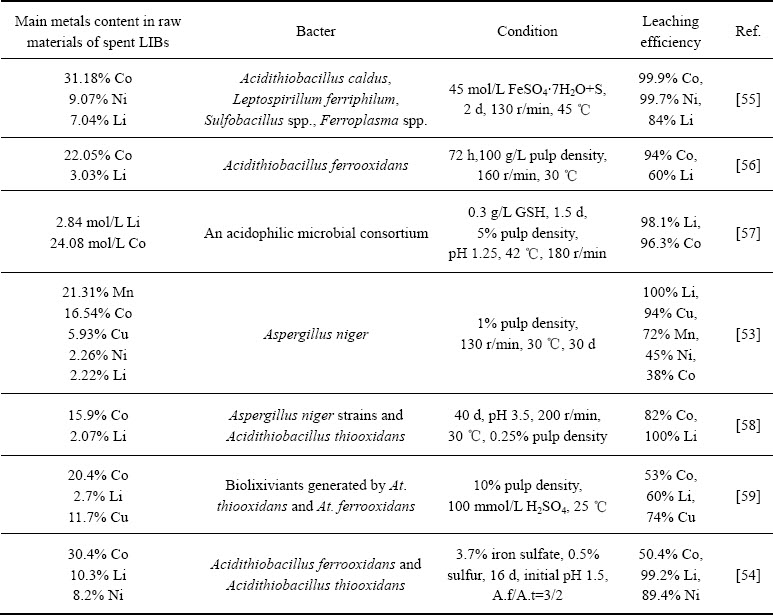
化学沉淀法是通过向浸出液中加入沉淀剂,生成难溶于水的沉淀物而使目标元素分离的方法。目前,常用来处理正极废料浸出液的沉淀剂包括氢氧化钠、磷酸钠、高锰酸钾、次氯酸钠、碳酸钠、二甲基乙二肟和硫化钠等。KUMAR等[63]采用常温有机酸浸出正极废料,过滤得到的浸出液经过浓缩后,通过控制pH将其中的铝、铁和铜沉淀,再采用碳酸钠沉淀法回收锂,得到碳酸锂产品的纯度可达到99.22%;VERMA等[64]以草酸和草酸氢铵为浸出剂,将锂以Li2C2O4提取到水相中,钴在固相中以草酸钴的形式沉淀。然后,再用碳酸钾沉淀回收水相中的锂,同时实现草酸溶液的循环再生(见图7(b))。
离子交换法借助离子交换剂和溶液中金属离子进行交换,以达到提取或去除正极废料浸出液中目标离子的目的。冯佳等[65]用TP207型离子树脂选择性的去除浸出液中的铜,提纯得到钴溶液。控制浸出液pH=2.5,浸出液在树脂中循环通过10次,97.44%的铜离子被去除,同时钴的回收率为90.20%;BADAWY等[66]采用螯合聚酰胺型肟树脂吸附回收浸出液中的钴,在树脂比例为0.04 g/mL、pH=5.5和吸附时间为30 min的条件下,钴的回收率为97%。离子交换法对金属离子的选择性好,但树脂的吸附速率和吸附容量不理想、吸附循环周期较长、成本较高,制约了离子交换法在废旧锂电池有价元素分离产业化上的推广应用。
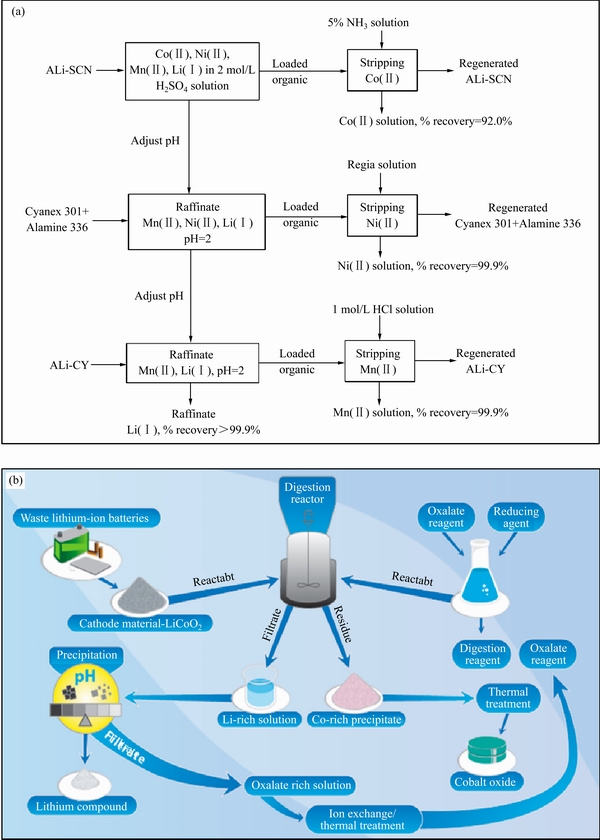
图7 从废LIBs酸浸液中分离Co、Ni、Mn[62]和Li(a)及回收LiCoO2的流程图(b)[64]
Fig. 7 Flow chart(a)[62] of separating Co, Ni, Mn and Li from acid leaching solution of spent LIBs and flow chart(b)[64] of recycling LiCoO2
电沉积法是在外加电场存在的条件下,利用浸出液中的正负离子迁移产生电流,并且在电极上发生氧化还原反应,进而实现目标元素的选择性析出分离。申勇峰[67]设计了从废锂离子电池正极材料酸性浸出液中电沉积回收钴的工艺流程。以钴极片作为阴极、钛板作为阳极,在电流密度为235 A/m2、55~60 ℃的条件下,钴的直收率大于93%,且得到的电积钴符合GB65 17—86中 1A#电钴标准。电沉积回收得到的产品纯度高,但反应过程存在着能耗大、成本高等缺点。
图8比较了溶剂萃取、化学沉淀、离子交换和电沉积四种元素分离方法在能耗、成本、回收效果、产品纯度、适用性和操作简易性方面的优缺点[2, 37]。相比于离子交换和电沉积法,溶剂萃取法和化学沉淀法具有操作简单、回收率高等优点。但是,化学沉淀法存在回收产品纯度低的问题,而溶剂萃取法在工业应用时存在萃取级数长、基建投资高的缺点。因此,在实际应用中,往往将各种方法结合使用,经济、高效地从废旧锂离子电池中回收有价金属元素。
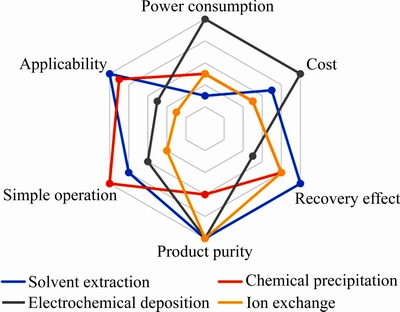
图8 溶剂萃取、化学沉淀、离子交换和电沉积四种元素分离方法在能耗、成本、回收效果、产品纯度、适用性和操作简易性方面的优缺点比较
Fig. 8 Comparison of advantages and disadvantages of four element separation methods of solvent extraction, chemical precipitation, ion exchange and electrodeposition in power consumption, cost, recovery effect, product purity, applicability and simple operation
2.4 材料再生
浸出和元素分离实现金属组分的提取,但存在元素分离流程长、得到过渡金属硫酸盐或碳酸锂等产品的附加值低等问题。为了解决上述问题,有研究者提出了以浸出液为原料,通过加入金属盐调整浸出液中的元素比例,直接再生正极材料的思路。该方法不仅可以规避镍、钴、锰、锂混合溶液体系元素分离繁琐的难题,而且能显著提升再生产品的附加值,提高回收效率和经济性,实现废旧锂离子电池材料的闭路循环。目前,报道的废旧正极材料循环再生的方法主要有沉淀法、溶胶-凝胶法和喷雾热解法。
沉淀法是再生正极材料最有效的方法。浸出液经过除杂净化后,加入金属盐调节溶液中金属离子的比例,再加入沉淀剂反应生成前驱体,最后,将得到的前驱体和一定量的锂盐混合烧结再生制备正极材料[68]。CHU等[69]以正极废料酸性浸出液为料液,通过共沉淀法和固相烧结的方法直接再生LiNi0.6Co0.2Mn0.2O2正极材料(见图9(a))。结果表明,再生的前驱体为球状团块且粒径均匀(见图9(b)),经过煅烧后生成粒径1 μm的正多边形LiNi0.6Co0.2Mn0.2O2颗粒(见图9(c))。再生材料具有较高的容量,在0.2C首次充放电容量可达到196.26和180.072 mA·h/g(见图9(d))。LIU等[70]用马来酸浸出废钴酸锂电池正极粉末(见图9(e)),同样采用共沉淀法和固相烧结法再生LiNi0.8Co0.1Mn0.1O2正极材料,并研究比较了不同浸出液用量对再生材料电化学性能的影响。结果表明,当浸出液添加量低于60%时,再生材料均呈直径6~8 μm的球形,电化学性能也较为合理。YANG等[18]同样采用共沉淀法和固相烧结法,直接从混合正极废料浸出液中再生球形富锰正极材料(见图9(f))。再生材料具有层状结构、结晶度较好、粒径均匀分布,在0.1C下循环50次后放电容量可达248.3 mA·h/g,容量保持率可维持在88%(见图9(g))。
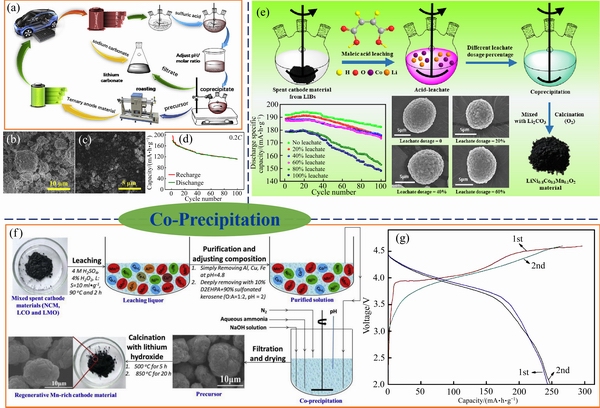
图9 回收和再生过程流程图、三元材料前驱体和(c)LiNi0.6Co0.2Mn0.2O2的电镜图、0.2C下的充放电曲线图[69]、正极材料再生过程及性能图[69-70]、正极材料再生流程图和再生正极材料充放电曲线图[18, 70]
Fig. 9 Flow chart of recovery and regeneration process(a),SEM images of ternary material precursor(b) and LiNi0.6Co0.2Mn0.2O2(c), charge and discharge curves at 0.2C[69](d), patterns of regeneration process and performance of cathode material[69-70](e), flow chart of regenerated cathode material(f), charge and discharge curves of regenerated cathode material[18, 70](g)
溶胶-凝胶法同样需要根据再生正极材料类型调节浸出液中金属离子比例,然后再加入络合剂,利用水解和聚合反应先形成凝胶,再经过煅烧得到正极材料[68]。LI等[36]用柠檬酸和过氧化氢浸出混合型正极废料(LiCoO2,LiCo1/3Ni1/3Mn1/3O2和LiMn2O4),采用溶胶-凝胶法从浸出液中再生LiCo1/3Ni1/3Mn1/3O2材料。电化学性能测试结果表明,在0.2C充放电条件下,再生材料的初始放电容量达到152.8 mA·h/g;100次循环后,放电容量为140.7 mA·h/g;在1C充放电条件下,循环300次后,放电容量为113.2 mA·h/g。
喷雾热解法再生正极材料步骤如下:1) 配置再生材料前驱体溶液,包括净化浸出液和调整金属离子比例;2) 喷雾热解反应,将配置的溶液经雾化器雾化得到粒径小且均匀的液滴,再进入高温反应炉得到前驱体粉末;3) 高温煅烧再生制备正极材料。ZHENG等[71]采用喷雾热解法从浸出液中直接再生三元正极材料。通过向浸出液中加入醋酸锂、醋酸镍、醋酸钴、醋酸锰调节锂、钴、镍和锰的摩尔比为3.2:1:1:1;然后在600 ℃条件下,通过喷雾热解得到再生前驱体颗粒;最后,在800 ℃下煅烧6 h,得到直径约为200 nm的三元正极材料。在0.2C充放电条件下,半电池和全电池的初始放电容量分别为157.1和154.3 mA·h/g,100次循环后,再生三元正极材料容量保持率在95%以上。
3 工业化应用
废旧锂离子电池回收技术的发展推动了相关产业化的进步(见图10)[72-75]。目前,废旧锂离子电池回收产业化技术可分为部分有价金属元素回收、全金属元素回收和高附加值材料再生制备。部分有价金属元素回收以提取正极废料中的高值金属镍和钴为主,代表性的企业有Sumitomo-Sony、Umicore和Glencore plc等。如Umicore采用火法冶炼工艺,将废旧锂离子电池中的镍和钴以合金形式富集,然后再通过湿法精炼过程获取钴镍产品。该工艺在产业化过程中取得了巨大成功,特别是在处理3C产品钴酸锂电池时显示出极好的经济性,成为了经典的火法冶炼工艺。然而,随着锂离子电池材料技术的发展,特别是三元动力锂离子电池大规模应用,经典的火法冶炼技术因为难以适应废料中锰含量的升高,在处理退役动力锂离子电池时渣量大、金属回收率降低。与此同时,随着锂价格的攀升,实现电池全元素,特别是锂元素的提取变得日益重要。在此背景下,锂离子电池回收产业逐渐由镍钴等部分高值元素回收转移至全元素回收。在此过程中,湿法冶炼技术显示了极大的优势,通过放电、拆解、破碎、分选等预处理过程,成功回收铝、铜、铁等组分。富集得到的正极废料通过湿法浸出、溶剂萃取等方法,成功制备硫酸镍、硫酸钴、硫酸锰和碳酸锂等产品,涌现出了浙江天能新材料、赣锋锂业等代表性回收企业。
废旧锂离子电池湿法回收工艺的进步,特别是共沉淀法直接制备前驱体技术的发展,为短流程、高附加值三元材料循环再生的产业化奠定了基础。邦普循环、华友钴业等一批实力强劲的企业先后建立了年处理万吨级规模的废旧锂离子电池回收和三元前驱体制备生产线,通过湿法过程得到纯净的镍、钴、锰混合溶液,然后采用共沉淀法制备LiCo1/3Ni1/3Mn1/3O2、LiNi0.5Co0.2Mn0.3O2、LiNi0.6Co0.2Mn0.2O2和LiNi0.8Co0.1Mn0.1O2等系列三元材料的前驱体产品,在满足市场需求的同时,实现了废旧锂离子电池有价组分的闭路循环,促进废旧离子电池回收产业走向新的阶段。
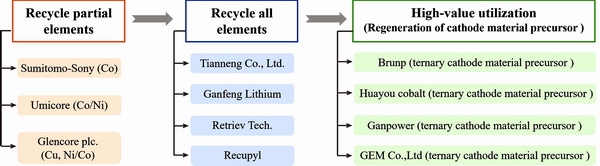
图10 回收废旧锂离子电池产业化发展历程
Fig. 10 Industrialization of recycling spent lithium-ion batteries
4 总结与展望
综上所述,废旧锂离子电池火法和湿法回收利用均取得了研究进展。从整体效果上看,目前从废旧锂离子电池中已经成功提取分离出镍、钴、锰、铜、铁、铝和锂等多种金属组分,基本原理和工艺技术方法已日趋成型。但从局部角度分析,废旧锂离子电池回收仍有巨大的进步空间。
1) 高精度智能分选。目前,废旧锂离子电池回收前端预处理通过放电、破碎、分选等步骤可实现活性物质材料的富集,铜、铝、铁等资源的回收。但由于电池拆解破碎等过程精细化程度不足,仍会有铜、铝、铁等物料进入到活性材料中,增大了后续浸出过程药剂用量和除杂难度。通过开发高精度的智能分选技术,预先分离正负极集流体、铁壳、隔膜等组分,不仅有利于降低活性物质材料中杂质的含量,而且对整个回收流程和最终再生产品质量的控制意义重大。
2) 污染防控和电解液回收。废旧锂离子电池易燃易爆,含氟电解液等毒害组分极易暴露到空气中,污染环境,如何在废旧锂电池回收的全生命周期中理清污染点,实现污染物的有效防控是非常值得关注的一个问题。此外,现有的技术多注重有价组分的提取和利用,但对电解液回收给予的关注不够。由于电解液沸点低、易水解,如不能无害化处理,必然引起严重的环境问题,成为制约废旧锂离子电池回收的瓶颈问题。
3) 短流程绿色回收与高附加再生材料可控制备。废旧锂离子电池浸出液组分复杂、分离难度大、效率低。通过设计闭路循环,直接再生正极材料,解决了相似过渡金属分离流程长和产品附加值低的问题,但由于溶液中杂质的存在,特别是痕量杂质对再生产品性质的影响作用机理不清晰,导致再生产品一致性不足。因此,系统探讨浸出溶液性质、材料制备方法与再生产品之间的关联性关系,构建基于高附加值功能材料可控制被为导向的短流程绿色回收体系,对实现废旧锂离子电池经济循环利用具有重要的作用。
REFERENCES
[1] YANG Y, SUN W, BU Y J, et al. Recovering valuable metals from spent lithium ion battery via a combination of reduction thermal treatment and facile acid leaching[J]. ACS Sustainable Chemistry & Engineering, 2018, 6(8): 10445-10453.
[2] LAROUCHE F, TEDJAR F, AMOUZEGAR K, et al. Progress and status of hydrometallurgical and direct recycling of Li-ion batteries and beyond[J]. Materials (Basel), 2020, 13(3): 801.
[3] 百度文库. 新能源材料——锂离子电池材料[EB/OL]. [2017-06-08]. https://wenku.baidu.com/view/469e742ea88271 fe910ef12d2af90242a895ab8a.html.
Wenku.baidu. New energy materials—Lithium ion battery materials[EB/OL]. [2017-06-08]. https://wenku.baidu.com/ view/469e742ea88271fe910ef12d2af90242a895ab8a.html.
[4] 前瞻产业研究院. 2020年中国锂电池行业生产现状与发展趋势分析 正极材料成本占据40%[EB/OL]. [2020-11-25]. https://www.sohu.com/a/434195275_473133.
Prospective Industry Research Institute. Analysis on production status and development trend of China’s lithium battery industry in 2020: The cost of cathode materials accounts for 40%[EB/OL]. [2020-11-25]. https://www.sohu. com/a/434195275_473133.
[5] MROZIK W, RAJAEIFAR M A, HEIDRICH O, et al. Environmental impacts, pollution sources and pathways of spent lithium-ion batteries[J]. Energy & Environmental Science, 2021. DOI: 10.1039/d1ee00691f.
[6] 黄海港, 何利华. 退役锂电池回收知识图谱分析[J]. 中国有色金属学报, 2021, 31(7): 1965-1978.
HUANG Hai-gang, HE Li-hua. Knowledge map analysis of recycling of waste lithium ion battery[J]. The Chinese Journal of Nonferrous Metals, 2021, 31(7): 1965-1978.
[7] YANG Y, OKONKWO E G, HUANG G Y, et al. On the sustainability of lithium ion battery industry—A review and perspective[J]. Energy Storage Materials, 2021, 36: 186-212.
[8] LEI S Y, CAO Y, CAO X F, et al. Separation of lithium and transition metals from leachate of spent lithium-ion batteries by solvent extraction method with Versatic 10[J]. Separation and Purification Technology, 2020, 250: 117258.
[9] 同花顺财经. 钴板块迎来政策红利!机构预计2021年或将开始出现短缺龙头企业率先受益[EB/OL]. [2020-11-03]. https://baijiahao.baidu.com/s?id=1682304860071267407&wfr=spider&for=pc.
Flush Finance. Cobalt plate ushers in policy dividend! The agency expects that there may be a shortage in 2021, and leading enterprises will take the lead in benefiting[EB/OL]. [2020-11-03]. https://baijiahao.baidu.com/s?id=1682304860071267407&wfr=spider&for=pc.
[10] YUN L, LINH D, SHUI L, et al. Metallurgical and mechanical methods for recycling of lithium-ion battery pack for electric vehicles[J]. Resources, Conservation and Recycling, 2018, 136: 198-208.
[11] TANG Y Q, XIE H W, ZHANG B L, et al. Recovery and regeneration of LiCoO2-based spent lithium-ion batteries by a carbothermic reduction vacuum pyrolysis approach: Controlling the recovery of CoO or Co[J]. Waste Management, 2019, 97: 140-148.
[12] REN G X, XIAO S W, XIE M Q, et al. Recovery of valuable metals from spent lithium ion batteries by smelting reduction process based on FeO-SiO2-Al2O3 slag system[J]. Transactions of Nonferrous Metals Society of China, 2017, 27(2): 450-456.
[13] XIAO S W, REN G X, XIE M Q, et al. Recovery of valuable metals from spent lithium-ion batteries by smelting reduction process based on MnO-SiO2-Al2O3 slag system[J]. Journal of Sustainable Metallurgy, 2017, 3(4): 703-710.
[14] Docin. 基于“锰媒”的废旧锂离子电池资源循环利用新技术讲述[EB/OL]. [2017-03-02]. https://www.docin.com/ p-1858516226.html.
Docin. New technology of recycling spent lithium ion battery resources based on “manganese medium”[EB/OL]. [2017-03-02]. https://www.docin.com/p-1858516226.html.
[15] 苟海鹏, 裴忠冶, 周国治, 等. 火法处理废旧三元锂离子电池工艺研究[J]. 中国有色冶金, 2019, 48(4): 79-83.
GOU Hai-peng, PEI Zhong-ye, ZHOU Guo-zhi, et al. Study on recycle of spent ternary Li-ion battery by pyrometallurgical process[J]. China Nonferrous Metallurgy, 2019, 48(4): 79-83.
[16] 李之钦, 庄绪宁, 宋小龙, 等. 废锂离子电池正极材料的火法资源化技术研究进展[J]. 环境工程, 2021, 39(4): 115-122, 146.
LI Zhi-qin, ZHUANG Xu-ning, SONG Xiao-long, et al. Research progress on recovery of cathode material from spent lithium-ion batteries by pyrometallurgy[J]. Environmental Engineering, 2021, 39(4): 115-122, 146.
[17] VIECELI N, NOGUEIRA C A, GUIMARAES C, et al. Hydrometallurgical recycling of lithium-ion batteries by reductive leaching with sodium metabisulphite[J]. Waste Management, 2018, 71: 350-361.
[18] YANG Y, SONG S L, JIANG F, et al. Short process for regenerating Mn-rich cathode material with high voltage from mixed-type spent cathode materials via a facile approach[J]. Journal of Cleaner Production, 2018, 186: 123-130.
[19] YANG Y, XU S M, HE Y H. Lithium recycling and cathode material regeneration from acid leach liquor of spent lithium- ion battery via facile co-extraction and co-precipitation processes[J]. Waste Management, 2017, 64: 219-227.
[20] 赵 磊, 殷 进, 龚佳豪, 等. 废锂离子电池正极材料湿法冶金回收技术研究进展[J]. 化工环保, 2021, 41(3): 255-262.
ZHAO Lei, YIN Jin, GONG Jia-hao, et al. Research progresses in hydrometallurgical recovery of spent cathode materials of lithium ion batteries[J]. Environmental Protection of Chemical Industry, 2021, 41(3): 255-262.
[21] 郭苗苗, 席晓丽, 张云河, 等. 报废动力电池镍钴锰酸锂三元正极材料高温氢还原-湿法冶金联用回收有价金属[J]. 中国有色金属学报, 2020, 30(6): 1415-1426.
GUO Miao-miao, XI Xiao-li, ZHANG Yun-he, et al. Recycling valuable metals from waste ternary cathode materials of power battery by combined high temperature hydrogen reduction and hydrometallurgy[J]. The Chinese Journal of Nonferrous Metals, 2020, 30(6): 1415-1426.
[22] SHIN S M, KIM N H, SOHN J S, et al. Development of a metal recovery process from Li-ion battery wastes[J]. Hydrometallurgy, 2005, 79(3/4): 172-181.
[23] ZHANG X, BIAN Y, XU S, et al. Innovative application of acid leaching to regenerate Li(Ni1/3Co1/3Mn1/3)O2 cathodes from spent lithium-ion batteries[J]. ACS Sustainable Chemistry & Engineering, 2018, 6(5): 5959-5968.
[24] ZHENG R J, WANG W H, DAI Y K, et al. A closed-loop process for recycling LiNixCoyMn(1-x-y)O2 from mixed cathode materials of lithium-ion batteries[J]. Green Energy & Environment, 2017, 2(1): 42-50.
[25] ZHANG B L, XIE H W, LU B H, et al. A green electrochemical process to recover Co and Li from spent LiCoO2-based batteries in molten salts[J]. ACS Sustainable Chemistry & Engineering, 2019, 7(15): 13391-13399.
[26] 赖延清, 杨 健, 张 刚, 等. 废旧三元锂离子电池正极材料的淀粉还原浸出工艺及其动力学[J]. 中国有色金属学报, 2019, 29(1): 153-160.
LAI Yan-qing, YANG Jian, ZHANG Gang, et al. Optimization and kinetics of leaching valuable metals from cathode materials of spent ternary lithium ion batteries with starch as reducing agent[J]. The Chinese Journal of Nonferrous Metals, 2019, 29(1): 153-160.
[27] 方荣华, 张文华, 欧阳志昭, 等. 酸浸回收锂离子电池有价金属的研究现状[J]. 电池, 2021, 51(3): 300-304.
FANG Rong-hua, ZHANG Wen-hua, OUYANG Zhi-zhao, et al. Research status of recovery of valuable metals from Li-ion battery by acid leaching[J]. Battery Bimonthly, 2021, 51(3): 300-304.
[28] YAO Y L, ZHU M Y, ZHAO Z, et al. Hydrometallurgical processes for recycling spent lithium-ion batteries: A critical review[J]. ACS Sustainable Chemistry & Engineering, 2018, 6(11): 13611-13627.
[29] BARIK S P, PRABAHARAN G, KUMAR L. Leaching and separation of Co and Mn from electrode materials of spent lithium-ion batteries using hydrochloric acid: Laboratory and pilot scale study[J]. Journal of Cleaner Production, 2017, 147: 37-43.
[30] MESHRAM P, ABHILASH, PANDEY B D, et al. Acid baking of spent lithium ion batteries for selective recovery of major metals: A two-step process[J]. Journal of Industrial and Engineering Chemistry, 2016, 43: 117-126.
[31] LI J H, SHI P X, WANG Z F, et al. A combined recovery process of metals in spent lithium-ion batteries[J]. Chemosphere, 2009, 77(8): 1132-1136.
[32] YANG Y, LEI S Y, SONG S L, et al. Stepwise recycling of valuable metals from Ni-rich cathode material of spent lithium-ion batteries[J]. Waste Management, 2020, 102: 131-138.
[33] 李林林, 曹林娟, 麦永雄, 等. 废旧锂离子电池有机酸湿法冶金回收技术研究进展[J]. 储能科学与技术, 2020, 9(6): 1641-1650.
LI Lin-lin, CAO Lin-juan, MAI Yong-xiong, et al. Research progress of organic acid of the hydrometallurgical recovery technology in spent Li ion batteries[J]. Energy Storage Science and Technology, 2020, 9(6): 1641-1650.
[34] ZHOU S Y, ZHANG Y J, MENG Q, et al. Recycling of LiCoO2 cathode material from spent lithium ion batteries by ultrasonic enhanced leaching and one-step regeneration[J]. Journal of Environmental Management, 2021, 277: 111426.
[35] ZENG X L, LI J H, SHEN B Y. Novel approach to recover cobalt and lithium from spent lithium-ion battery using oxalic acid[J]. Journal of Hazardous Materials, 2015, 295: 112-118.
[36] LI L, BIAN Y F, ZHANG X X, et al. Economical recycling process for spent lithium-ion batteries and macro- and micro-scale mechanistic study[J]. Journal of Power Sources, 2018, 377: 70-79.
[37] ZHANG X X, LI L, FAN E S, et al. Toward sustainable and systematic recycling of spent rechargeable batteries[J]. Chemical Society Reviews, 2018, 47(19): 7239-7302.
[38] WANG C, WANG S B, YAN F, et al. Recycling of spent lithium-ion batteries: Selective ammonia leaching of valuable metals and simultaneous synthesis of high-purity manganese carbonate[J]. Waste Management, 2020, 114: 253-262.
[39] WU C B, LI B S, YUAN C F, et al. Recycling valuable metals from spent lithium-ion batteries by ammonium sulfite-reduction ammonia leaching[J]. Waste Management, 2019, 93: 153-161.
[40] CHEN Y M, LIU N N, HU F, et al. Thermal treatment and ammoniacal leaching for the recovery of valuable metals from spent lithium-ion batteries[J]. Waste Management, 2018, 75: 469-476.
[41] CHEN W S, HO H J. Recovery of valuable metals from lithium-ion batteries NMC cathode waste materials by hydrometallurgical methods[J]. Metals, 2018, 8(5): 321.
[42] YANG Y, LEI S Y, SONG S L, et al. Stepwise recycling of valuable metals from Ni-rich cathode material of spent lithium-ion batteries[J]. Waste Management, 2020, 102: 131-138.
[43] ZHANG Y C, WANG W Q, HU J H, et al. Stepwise recovery of valuable metals from spent lithium ion batteries by controllable reduction and selective leaching and precipitation[J]. ACS Sustainable Chemistry & Engineering, 2020, 8(41): 15496-15506.
[44] WANG W Y, YEN C H, LIN J L, et al. Recovery of high-purity metallic cobalt from lithium nickel manganese cobalt oxide (NMC)-type Li-ion battery[J]. Journal of Material Cycles and Waste Management, 2019, 21(2): 300-307.
[45] ZHAO J J, ZHANG B L, XIE H W, et al. Hydrometallurgical recovery of spent cobalt-based lithium-ion battery cathodes using ethanol as the reducing agent[J]. Environmental Research, 2020, 181: 108803.
[46] GAO W F, SONG J L, CAO H B, et al. Selective recovery of valuable metals from spent lithium-ion batteries—Process development and kinetics evaluation[J]. Journal of Cleaner Production, 2018, 178: 833-845.
[47] DAS D, MUKHERJEE S, CHAUDHURI M G. Studies on leaching characteristics of electronic waste for metal recovery using inorganic and organic acids and base[J]. Waste Management & Research, 2021, 39(2): 242-249.
[48] YU M, ZHANG Z H, XUE F, et al. A more simple and efficient process for recovery of cobalt and lithium from spent lithium-ion batteries with citric acid[J]. Separation and Purification Technology, 2019, 215: 398-402.
[49] FU Y P, HE Y Q, QU L L, et al. Enhancement in leaching process of lithium and cobalt from spent lithium-ion batteries using benzenesulfonic acid system[J]. Waste Management, 2019, 88: 191-199.
[50] WANG S B, WANG C, LAI F J, et al. Reduction- ammoniacal leaching to recycle lithium, cobalt, and nickel from spent lithium-ion batteries with a hydrothermal method: Effect of reductants and ammonium salts[J]. Waste Management, 2020, 102: 122-130.
[51] 邹 超, 潘君丽, 刘维桥, 等. 湿法回收锂离子电池三元正极材料的进展[J]. 电池, 2018, 48: 130-134.
ZHOU Chao, PAN Jun-li, LIU Wei-qiao, et al. Progress in hydrometallurgical process of recycling ternary cathode material of Li-ion battery[J]. Battery Bimonthly, 2018, 48: 130-134.
[52] XIN Y Y, GUO X M, CHEN S, et al. Bioleaching of valuable metals Li, Co, Ni and Mn from spent electric vehicle Li-ion batteries for the purpose of recovery[J]. Journal of Cleaner Production, 2016, 116: 249-258.
[53] BAHALOO-HOREH N, MOUSAVI S M, BANIASADI M. Use of adapted metal tolerant Aspergillus niger to enhance bioleaching efficiency of valuable metals from spent lithium-ion mobile phone batteries[J]. Journal of Cleaner Production, 2018, 197: 1546-1557.
[54] HEYDARIAN A, MOUSAVI S M, VAKILCHAP F, et al. Application of a mixed culture of adapted acidophilic bacteria in two-step bioleaching of spent lithium-ion laptop batteries[J]. Journal of Power Sources, 2018, 378: 19-30.
[55] GHASSA S, FARZANEGAN A, GHARABAGHI M, et al. Novel bioleaching of waste lithium ion batteries by mixed moderate thermophilic microorganisms, using iron scrap as energy source and reducing agent[J]. Hydrometallurgy, 2020, 197: 105465.
[56] ROY J J, MADHAVI S, CAO B. Metal extraction from spent lithium-ion batteries (LIBs) at high pulp density by environmentally friendly bioleaching process[J]. Journal of Cleaner Production, 2021, 280: 124242.
[57] LIU X C, LIU H, WU W J, et al. Oxidative Stress Induced by Metal Ions in Bioleaching of LiCoO2 by an Acidophilic Microbial Consortium[J]. Frontiers in Microbiology, 2019, 10: 3058.
[58] BISWAL B K, JADHAV U U, MADHAIYAN M, et al. Biological leaching and chemical precipitation methods for recovery of Co and Li from spent lithium-ion batteries[J]. ACS Sustainable Chemistry & Engineering, 2018, 6(9): 12343-12352.
[59] BOXALL N J, CHENG K Y, BRUCKARD W, et al. Application of indirect non-contact bioleaching for extracting metals from waste lithium-ion batteries[J]. Journal of Hazardous Materials, 2018, 360: 504-511.
[60] 张晨露, 王碧侠, 李卓阳, 等. 废旧锂离子电池正极有价金属回收试验研究[J]. 有色金属工程, 2020, 10(11): 73-78.
ZHANG Chen-lu, WANG Bi-xia, LI Zhuo-yang, et al. Experiment study on recovery of valuable metals from cathode of the spent lithium ion battery[J]. Nonferrous Metals Engineering, 2020, 10(11): 73-78.
[61] 蒋 玲, 詹 路, 张秋卓. 废旧三元电池正极活性材料酸性浸出液中钴镍锰锂的分离与回收[J]. 中国有色金属学报, 2020, 30(11): 2684-2694.
JIANG Ling, ZHAN Lu, ZHANG Qiu-zhuo. Separation and recovery of cobalt, nicker, manganese and lithium from acidic leaching solution of old ternary battery positive active material[J]. The Chinese Journal of Nonferrous Metals, 2020, 30(11): 2684-2694.
[62] NGUYEN V N H, LEE M S. Separation of Co(Ⅱ), Ni(Ⅱ), Mn(Ⅱ) and Li(Ⅰ) from synthetic sulfuric acid leaching solution of spent lithium ion batteries by solvent extraction[J]. Journal of Chemical Technology & Biotechnology, 2021, 96(5): 1205-1217.
[63] KUMAR J, SHEN X, LI B, et al. Selective recovery of Li and FePO4 from spent LiFePO4 cathode scraps by organic acids and the properties of the regenerated LiFePO4[J]. Waste Management, 2020, 113: 32-40.
[64] VERMA A, JOHNSON G H, CORBIN D R, et al. Separation of lithium and cobalt from LiCoO2: A unique critical metals recovery process utilizing oxalate chemistry[J]. ACS Sustainable Chemistry & Engineering, 2020, 8(15): 6100-6108.
[65] 冯 佳, 章 骅, 邵立明, 等. 废旧锂离子电池中钴的离子交换法回收[J]. 环境卫生工程, 2008, 16(6): 1-3.
FENG Jia, ZHANG Hua, SHAO Li-ming, et al. Cobalt recovery from lithium-ion batteries by ion-exchange method[J]. Environmental Sanitation Engineering, 2008, 16(6): 1-3.
[66] BADAWY S M, NAYL A A, EL KHASHAB R A, et al. Cobalt separation from waste mobile phone batteries using selective precipitation and chelating resin[J]. Journal of Material Cycles and Waste Management, 2013, 16(4): 739-746.
[67] 申勇峰. 从废锂离子电池中回收钴[J]. 有色金属, 2002, 54(4): 69-70, 77.
SHE Yong-feng. Recovery cobalt from discarded lithium ion cells[J]. Nonferrous Metals Engineering, 2002, 54(4): 69-70, 77.
[68] 王皓逸, 邹昱凌, 孟 奇, 等. 退役三元锂离子电池正极材料高效清洁回收技术研究进展[J]. 人工晶体学报, 2021, 50(6): 1158-1169.
WANG Hao-yi, ZOU Yu-ling, MENG Qi, et al. Research progress on efficient and clean recycling technology of spent ternary lithium battery cathode materials[J]. Journal of Synthetic Crystals, 2021, 50(6): 1158-1169.
[69] CHU W, ZHANG Y L, CHEN X, et al. Synthesis of LiNi0.6Co0.2Mn0.2O2 from mixed cathode materials of spent lithium-ion batteries[J]. Journal of Power Sources, 2020, 449: 227567.
[70] LIU B R, HUANG Q, SU Y F, et al. Synthesis of Ni-rich cathode material from maleic acid-leachate of spent lithium-ion batteries[J]. ACS Sustainable Chemistry & Engineering, 2020, 8(21): 7839-7850.
[71] ZHENG Y, WANG S Q, GAO Y L, et al. Lithium nickel cobalt manganese oxide recovery via spray pyrolysis directly from the leachate of spent cathode scraps[J]. ACS Applied Energy Materials, 2019, 2(9): 6952-6959.
[72] 胡杨低碳频道. 动力电池回收系列3—海外公司电池回收技术路线[EB/OL]. [2021-09-04]. https://baijiahao.baidu. com/s?id=1709920581379485008&wfr=spider&for=pc.
Populus Euphratica Low Carbon Channel. The series three of power battery recycling-battery recycling technology route of overseas companies[EB/OL]. [2021-09-04]. https:// baijiahao.baidu.com/s?id=1709920581379485008&wfr=spider&for=pc.
[73] MARINOS D. An approach to beneficiation of spent lithium-ion batteries for recovery of materials[D]. Boulder: University of Colorado, 2014.
[74] VALIO J. Critical review on lithium ion battery recycling technologies[D]. Helsinki: Aalto University, 2017.
[75] 人民资讯. 锂离子电池回收再生商业模式及国内外头部企业市场动态[EB/OL]. [2021-05-21]. https://baijiahao. baidu.com/s?id=1701242204832869158&wfr=spider&for=pc.
People Information. Business model and market dynamics of lithium ion battery recycling of domestic and foreign top enterprises[EB/OL]. [2021-05-21]. https://baijiahao.baidu. com/s?id=1701242204832869158&wfr=spider&for=pc.
Recycling of spent lithium-ion battery
LEI Shu-ya1, XU Rui1, SUN Wei1, XU Sheng-ming2, YANG Yue1
(1. School of Minerals Processing and Bioengineering, Central South University, Changsha 410083, China;
2. Institute of Nuclear & New Energy Technology, Tsinghua University, Beijing 100084, China)
Abstract: With the development of new energy industries, the demand for lithium-ion battery (LIB) continues to increase. The massive use of LIBs will inevitably generate a large amount of spent LIBs. On one hand, spent LIBs contain toxic components such as fluoride and must be treated in a harmless manner. On the other hand, spent LIBs contain many valuable metal components, such as nickel, cobalt, manganese, and lithium, which have resource properties. Therefore, the recycling of spent LIBs can not only protect the environment, but also alleviate the shortage of metal resources, and promote the sustainable development of the new energy industry. Currently, recycling spent LIBs has become a hot topic all over the world. This paper systematically reviews the latest research progress in the recovery of spent LIBs, with emphasis on pyrometallurgical and hydrometallurgical process, especially the detailed analysis of the technologies of crushing, leaching, separation and regeneration, in the hydrometallurgical process, and prospects the development trend and research focus, in order to provide reference for the efficient recovery and utilization of valuable metal components of spent LIBs.
Key words: spent lithium-ion battery; valuable component; recovery; recycling
Foundation item: Projects(2019YFC1907801, 2019YFC1907804) supported by the National Key Research and Development Program; Projects(51904340, 51834008) supported by the National Natural Science Foundation of China; Projects(2020JJ4733, 2021JJ20066) supported by the Natural Science Foundation of Hunan Province, China
Received date: 2021-08-30; Accepted date: 2021-10-22
Corresponding authors: YANG Yue; Tel: +86-18570681655; E-mail: eric1911@126.com
XU Sheng-ming; E-mail: smxu@tsinghua.edu.cn
(编辑 何学锋)
基金项目:国家重点研发计划资助项目(2019YFC1907801,2019YFC1907804);国家自然科学基金资助项目(51904340,51834008);湖南省自然科学基金资助项目(2020JJ4733,2021JJ20066)
收稿日期:2021-08-30;修订日期:2021-10-22
通信作者:杨 越,副教授,博士;电话:18570681655;E-mail:eric1911@126.com
徐盛明,教授,博士;E-mail:smxu@tsinghua.edu.cn
摘 要:随着电动汽车等新能源产业的发展,锂离子电池需求量不断增大,而大量锂离子电池的使用,必将引发报废潮。一方面,废旧锂离子电池易燃易爆,含有氟化物等毒害组分,必须进行无害化处理;另一方面,废旧锂离子电池具有资源属性,含有丰富的镍、钴、锰、锂等有价金属组分。因此,废旧锂离子电池的回收不仅可以保护环境,而且能缓解我国战略金属资源紧张局面,促进新能源产业健康可持续发展,已成为目前全球研究的一个热点方向。本文系统梳理了废旧锂离子电池材料回收的最新研究进展,重点介绍了火法和湿法回收方法,详细分析了湿法冶金过程中的破碎、浸出、分离和再生技术,并对未来的发展趋势和研究重点进行了展望,旨在为废旧锂离子电池有价金属组分的高效回收利用提供参考。