- Abstract:
- 1 Introduction▲
- 2 Experimental proce...▲
- 3 Results and discus...▲
- 4 Conclusions▲
- References
- Figure
- Figure 1 Microstructure of near lamellar TiAl alloy
- Figure 2 Cross-sectional BSE image of Si-Al-Y co-deposition coating
- Figure 3 Mass change of TiAl alloy and Si-Al-Y coating in (Na, K)2SO4 molten salts at 900 °C
- Figure 4 Surfaces morphologies (a, b) and XRD patterns (c) of TiAl alloy after hot corrosion in (Na, K)2SO4 melt at 900 °C for 1 h (a) and 20 h (b)
- Figure 5 Cross-sectional BSE images of TiAl alloy after hot corrosion test at 900 °C for 1 h (a) and 20 h (b)
- Figure 6 Surfaces BSE images (a, b) and XRD patterns (c) of Si-Al-Y coating after hot corrosion in (Na, K)2SO4 melt at 900 °C for 5 h (a) and 50 h (b)
- Figure 7 Cross-sectional BSE images of Si-Al-Y coatings after hot corrosion test at 900 °C for 5 h (a) and 50 h (b)
J. Cent. South Univ. (2020) 27: 2530-2537
DOI: https://doi.org/10.1007/s11771-020-4478-8
Microstructure and hot corrosion resistance of Si-Al-Y coated TiAl alloy
LI Yong-quan(李涌泉)1, 2, XIE Fa-qin(谢发勤)2, YANG Shao-lin(杨少林)1
1. School of Materials Science & Engineering, North Minzu University, Yinchuan 750021, China;
2. School of Aeronautics, Northwestern Polytechnical University, Xi’an 710072, China
Central South University Press and Springer-Verlag GmbH Germany, part of Springer Nature 2020
Abstract:
In order to obtain a high-performance surface on TiAl alloy that can meet the requirements in hot corrosion environment, Si-Al-Y coatings were fabricated by pack cementation process at 1050℃ for 4 h. Corrosion behaviors of the TiAl alloy with and without Si-Al-Y coatings are compared to illustrate the factors and corresponding mechanism in molten salt environment of 25wt% K2SO4 and 75wt% Na2SO4 at 900 °C. The obtained Si-Al-Y coating was mainly composed of a TiSi2 outer layer, a (Ti, X )5Si4 and (Ti, X )5Si3 ( X represents Nb or Cr element) middle layer, a TiAl2 inner layer and a Al-rich inter-diffusion zone. The inter-phase selective corrosion containing corrosion pits extending along α2 phase from lamellar interfaces in hot corrosion tested TiAl alloy was observed. However, by being coated with Si-Al-Y coating, the hot corrosion performance of TiAl alloy was improved remarkably.
Key words:
TiAl alloy; Si-Al-Y coating; structure; hot corrosion;
Cite this article as:
LI Yong-quan, XIE Fa-qin, YANG Shao-lin. Microstructure and hot corrosion resistance of Si-Al-Y coated TiAl alloy [J]. Journal of Central South University, 2020, 27(9): 2530-2537.
DOI:https://dx.doi.org/https://doi.org/10.1007/s11771-020-4478-81 Introduction
Possessing low density, high specific strength, excellent high temperature performance and other superior properties, TiAl alloys have been considered important high-temperature structural materials to be potentially used in industrial and aeroengine turbomachineries [1, 2]. For instance, TiAl alloys are being considered to replace Ni-based superalloy in the temperature range of 1073-1173 K in aero-engine, to achieve a component weight reduction over 50% [3, 4]. However, the low chemical activity of Al hinders the selective oxidation to form protective Al2O3 scale, and the resulted poor oxidation and corrosion resistance of TiAl has been a major barrier to its practical applications and commercialization [5, 6].
In recent years, remarkable advancements have been made in solving the aforementioned problem through adding alloying elements such as B, Nb, Cr, Al and W [7-10]. Unfortunately, further alloying usually leads to mechanical properties deterioration of TiAl alloys [11]. Therefore, a protective coating is necessary to ensure the long-term mechanical and structure integrity of TiAl alloys in oxidation and corrosion environments. For instance, in ocean environment, the deposited sodium sulfate and sylvite can cause serious corrosion and accelerate the degradation of TiAl alloys [12].
Among various coating systems, Si-Al composite coatings are considered to be suitable for high temperature protection of TiAl alloys by forming a dense, compact and stable SiO2+Al2O3 scale [12]. Thus, intensive studies involved in preparation technologies, microstructure control, high temperature oxidation and hot corrosion behavior, as well as the related mechanisms, etc., have been carried out in recent years [13-18]. WANG et al [13] studied the high temperature oxidation behavior of a Ti(Al,Si)3 composite coating prepared on TiAl alloy by cold spray method, and found that the weight gain of the obtained coating after oxidation at 900 °C for 1000 h is lower than 2.2 mg/cm2. SWADZBA et al [14] have reported the excellent cycle oxidation resistance of Si-Al composite coating prepared on TiAl alloy by slurry method. Many other studies have also confirmed the promising high temperature oxidation resistance of Si-Al composites [15-18]. However, the Si-Al composite coatings are considered to be poor in hot corrosion resistance. It is demonstrated that although aluminum helps to improve the high-temperature oxidation resistance of the Si-Al coatings by forming protective Al2O3 in the scale, it is not conducive to the hot corrosion resistance of the coatings [19, 20]. WANG et al [20] have reported that dense and protective scale can hardly form on the Si-Al coating in chlorides and sulphates containing environment in temperature range of 1050-1150 °C, mainly attributed to the rapid dissolution of the aluminum oxides by reacting with chlorine, and the formed volatile AlClx would cause secondary damages to the coating. To overcome the obstacle, adding rare earth element Y in the coating should be an effective way, as its rare earth effects (REEs) were reported to be beneficial for reducing the grain size, promoting the formation of protective and adhesive scales at high temperatures [21, 22].
The way of coating preparation also plays an important role in the high temperature protection. Till now, substantial protective coatings have been explored by various surface modification strategies on TiAl, such as, plasma spray, vacuum fusing, magnetron sputtering, electron beam physical vapor deposition and pack cementation [23-25]. Among these techniques, the pack cementation with low operating cost, high efficiency, and applicable for a wide range of shapes and sizes, has been widely accepted and used in aluminizing, siliconization, carburizing, chromizing and bording [23]. Another outstanding advantage of pack cementation technique is that gradient coating with metallurgical bonding interfaces, characterized by high bond strength and not easy to crack, can be produced by this method, which is significant for TiAl alloy to bear complex load and thermal fatigue [26, 27]. In this paper, Si-Al-Y co-deposition coatings were prepared on a Ti-Al alloy by halide activated pack cementation (HAPC) technique. The corrosion behaviors of the TiAl alloy with and without Si-Al-Y coatings are compared to illustrate the factors and corresponding mechanism in molten salt environment.
2 Experimental procedures
The TiAl alloy with nominal composition Ti-48Al-2Cr-2Nb (at%) used for the experiments was manufactured by Beijing Institute of Aerial Materials, China. As the microstructure shown in Figure 1, the TiAl substrate with lamellar structure consists of γ-TiAl and α2-Ti3Al phases. All samples were machined into the rectangle blocks with dimensions of 15 mm×15 mm×3 mm, ground with 1500-SiC paper, then ultrasonically cleaned in ethanol and dried.
Figure 1 Microstructure of near lamellar TiAl alloy
According to our previous research results [28-30], pure Si, Al and Y2O3 were used as donor sources, and AlCl3·6H2O and Al2O3 powers were utilized as activator and filler of the pack mixture, respectively. The pack mixtures used for the pack processes were chosen as 10Si-10Al-1Y2O3- 8AlCl3·6H2O-71Al2O3 (wt%), and each component of powders was weighed according to the ratio and then mixed by tumbling in a ball mill sufficiently. After that, the TiAl samples were buried in the pack mixtures and then sealed in an alumina crucible with Al2O3-based silica sol binder. The sealed crucible was heated in an electric tube furnace from room temperature to co-deposition temperature (1050 °C) at a rate of 15 °C /min. After holding at 1050 °C for 4 h, the furnace was cooled to room temperature. The TiAl alloy was then removed from the pack and ultrasonically cleaned.
In this study, the hot corrosion tests of the TiAl alloy with and without Si-Al-Y coatings were carried out in molten salt environment of 25 wt% K2SO4 and 75 wt% Na2SO4 at 900 °C for different times. After being cooled to room temperature, the specimens were put into the distilled water to dissolve the salts adhered to surface of the samples, and then dried. The hot corrosion resistance of the specimens was evaluated via mass changes that were measured using an analytical balance (accuracy 0.1 mg).
X-ray diffraction analysis (XRD, Panalytical X’Pert PRO, 30 mA, 40 kV, CuKα) was employed to identify the phases present in the as-coated and corroded specimens. The microstructures and chemical compositions of the constituent phases were characterized by a scanning electron microscope (SEM, JSM-6360LV, a regime of secondary and backscattered electrons, acceleration voltage of 20 kV) equipped with an energy dispersive spectroscope (EDS).
3 Results and discussion
3.1 Coating structure
Figure 2 shows a typical cross-sectional BSE image of the Si-Al-Y coating prepared by co-depositing Si, Al and Y at 1150 °C for 4 h. It can be seen that the coating was about 37 μm thick and had a multilayer structure: a TiSi2 out layer, a (Ti, X)5Si4 and (Ti, X)5Si3(X represents Nb or Cr) middle layer, a TiAl2 inner layer and an Al-rich interdiffusion zone. The detailed analyses of the formation processes of the coating structure and constituent phases, as well as their oxidation behavior have been reported in other articles by our group [28-31].
Figure 2 Cross-sectional BSE image of Si-Al-Y co-deposition coating
3.2 Hot corrosion behavior of Si-Al-Y coating
3.2.1 Corrosion kinetics
Figure 3 shows the mass change of TiAl alloy and Si-Al-Y coating in (Na, K)2SO4 molten salts at 900 °C. In the initial period of hot corrosion, the mass changes of TiAl alloy and Si-Al-Y coating were respectively about -0.52 and 1.31 mg/cm2 after 1 h hot corrosion. With the increase of corrosion time to 20 h, the mass change of TiAl alloy decreased remarkably to -7.80 mg/cm2. The mass change of Si-Al-Y coating increased to 6.01 mg/cm2 after 14 h hot corrosion and then decreased to -3.83 mg/cm2 after 50 h. From the above results, it can be found that the TiAl alloy suffered from a severe hot corrosion and a large mass loss, which was related to the spallation of corrosion scales and corrosion products. Therefore, the corrosion products on surfaces of TiAl alloy cannot provide complete protection for the TiAl substrate, and the hot corrosion resistance of the Si-Al-Y coating is better than that of the substrate.
Figure 3 Mass change of TiAl alloy and Si-Al-Y coating in (Na, K)2SO4 molten salts at 900 °C
3.2.2 Hot corrosion scale morphologies
The surfaces morphologies and XRD patterns of the TiAl alloy after hot corrosion in (Na, K)2SO4 melt at 900 °C for 1 h and 20 h are shown in Figure 4. It can be seen from Figure 4(a) that the hot corrosion scale formed on the surface is loose and cracked, and local spallasion can be clearly observed. The enlarged intact area at the right position of Figure 4(a), characterized by dark gray matrix and white granular tissues, is uniform and smooth. The phase constitution and XRD patterns shown in Figure 4(c) suggest that the corrosion products of the intact scale is TiO2 and Al2O3, and the spalled area has a composition of 36.46Al-2.36S-57.11Ti-1.08Cr-2.99 Nb (at%). The XRD patterns (Figure 4(c)) and the binary Ti-Al phase diagram [9] indicate the composition of Ti3Al2 phase. Moreover, many grooves in the direction of the arrow were observed in the spalled area. These features could provide some evidences to the hot corrosion mechanism of the alloy, and it will be discussed later.
Figure 4 Surfaces morphologies (a, b) and XRD patterns (c) of TiAl alloy after hot corrosion in (Na, K)2SO4 melt at 900 °C for 1 h (a) and 20 h (b)
It can be found from Figure 4(b) that the surface morphology after hot corrosion for 20 h is similar to that after hot corrosion for 1 h. The EDS analyses determined that the intact area was mainly composed of TiO2, and the significant increased intensity of TiO2 diffraction peaks also revealed the formation of the TiO2 scale. The spalled area had a typical composition of 20.30Al-7.2S-69.73Ti- 1.7Cr-1.07Nb (at%), detected by EDS analysis. Combined with the XRD pattern in Figure 4(c), the spalled area should mainly consist of Ti3Al2 and a small amount of TiS.
Figure 5 shows cross-sectional BSE images of the TiAl alloy after hot corrosion in (Na, K)2SO4 melt at 900 °C for 1 and 20 h, respectively. It can be seen from Figure 5(a) that the hot corrosion scale formed on the surface was about 1 μm thick, and EDS analysis suggested the main composition of Al and Ti oxides (arrow 1). Under the corrosion product film, many corrosion pits formed at the interface, and some of them had extended into the matrix alloy along α2 phases (arrow 2). EDS analysis determined that the contents of O and S elements in these corrosion pits are 3.51 at% and 4.78 at%, respectively, indicating that the α2 phase oxidized and vulcanized preferentially. The grooving morphology shown in Figure 4(a) should be a result of the corrosion film spallasion.
Figure 5 Cross-sectional BSE images of TiAl alloy after hot corrosion test at 900 °C for 1 h (a) and 20 h (b)
With prolonging the corrosion time to 20 h, as seen in Figure 5(b), a corrosion scale with a multilayer structure and a thickness about 22 μm formed. A large crack can be clearly observed between the scale and the matrix. EDS analyses determined that the concentrations of Ti and O in the outer white tissue of the scale were about 35.42 at% and 64.58 at%, respectively, indicating the formation of TiO2, while the Al content in the dark gray tissue of the middle layer was about 41.31 at%, suggesting the formation of Al2O3. The inner layer is mainly composed of mixed oxides of Ti and Al, and the content of S in this layer is as high as 9.43 at%.
Figure 6 shows the surfaces BSE images and XRD patterns of the Si-Al-Y co-deposition coating after hot corrosion test at 900 °C for 5 and 50 h, respectively. It can be seen that the corrosion scale formed on the surface at different time had a similar morphology, and is continuous without visible peeling. However, with the increasing corrosion time, corrosion pores increased slightly on the coating surface. XRD analysis (Figure 6(c)) revealed that the corrosion products formed on the coating were similar after oxidation for different time, mainly composed of TiO2, SiO2, Na2SiO3 and TiSi2.
Figure 7 presents the cross-sectional BSE images of the Si-Al-Y coatings after hot corrosion test at 900 °C for 5 and 50 h. As shown in Figure 7(a), it can be easily found that slight corrosion occurred in the outer layer of Si-Al-Y coating, and the corrosion scale was about 2 μm thick and consisted of dark gray phase (arrow 3). XRD patterns (Figure 6(c)) and EDS analysis indicated the composition of Ti rich TiO2 and a small amount of SiO2 and Na2SiO3. Beneath the corrosion scale, many black punctate tissues (arrow 4) formed, with O and S concentrations of respectively 3.91 at% and 0.73 at%, determined by EDS analysis.
After being corroded for 50 h, as shown in Figure 7(b), all layers in the coating have been corroded, and a hot corrosion scale with a thickness of about 2 μm formed on the surface of the coating.
Figure 6 Surfaces BSE images (a, b) and XRD patterns (c) of Si-Al-Y coating after hot corrosion in (Na, K)2SO4 melt at 900 °C for 5 h (a) and 50 h (b)
The EDS analysis results determined that the scale had a typical composition of 54.76Ti-44.52O- 0.72Si at%, suggesting the formation of Ti-rich TiO2. Moreover, a number of holes can be seen in the remaining TiSi2 out layer and TiAl2 inner layer, EDS line scanning results show that O and S increased significantly in the inner layer; especially, S element was enriched in both upper and lower part of the layer, where the cracks formed, as shown in the right position of Figure 7(b).
3.2.3 Hot corrosion mechanisms
Both oxides and sulfides, which originated from (Na, K)2SO4 molten salt, were detected in the corrosion products of TiAl alloy and Si-Al-Y coating. Since it was difficult for external O and S elements to enter the corrosion system, the O and S elements should mainly generate from the high temperature decomposition of Na2SO4 and K2SO4 according to the following thermodynamic equilibrium existing in the corrosion system [32]:
Na2SO4→Na2O+SO2+1/2O2 (1)
K2SO4→K2O+SO2+1/2O2 (2)
Actually, the molten salt is a high sulfur, low oxygen potential system.
Figure 7 Cross-sectional BSE images of Si-Al-Y coatings after hot corrosion test at 900 °C for 5 h (a) and 50 h (b)
For TiAl, oxidation occurred on the surface of the alloy at the initial stage of hot corrosion [33]:
Ti+O2→TiO2 (3)
2Al+3/2O2→Al2O3 (4)
As the above process progressed, O and S elements penetrated the matrix interface through the loose oxide film, and reacted with α2 phase preferentially due to the two-phase laths morphology and high activity of Ti in the α2 phase, which means that inter-phase selective corrosion occurred, as demonstrated by the cross-sectional morphologies of TiAl alloy shown in Figure 5 and ZHAO et al [34]. Moreover, the corroded α2 phase spread laterally in horizontal direction, leading to fracture and premature failure of TiAl alloy.
For the Si-Al-Y coating, the surface is slightly oxidized to form a thin SiO2 and TiO2 scale (about 2 μm) at the beginning of hot corrosion process, such a thin scale cannot effectively prevent the inward diffusion of S and O. Moreover, the Ti element has a higher diffusion rate along the grain boundaries compared with other elements, and thus, the outward diffusion of Ti caused intensive Kirkendall vacancies in the remained coating and increased TiO2 in the scale, as demonstrated by Figure 7(b). These vacancies can act as the inward diffusion channel of S and O elements, and accelerate the corrosion process of the coating. Accompanied with the inward diffusion of S and O, Al should be the preferentially oxidized element due to its more negative oxidation Gibbs free energy, while Ti is prone to initially react with S to form TiS in the case that oxygen been consumed [35]:
S+Ti→TiS (5)
With the continually inward diffusion of O, TiS was then oxidized to release S, and subsequently led to internal oxidation and sulfidation.
4 Conclusions
1) A uniform and compact Si-Al-Y coating with a TiSi2 outer layer, (Ti, X)5Si4 and (Ti, X)5Si3 ( X represents Nb or Cr element) middle layer, TiAl2, γ-TiAl inner layer and a Al-rich inter-diffusion zone is prepared on TiAl alloy by pack cementation at 1050 °C for 4 h.
2) Inter-phase selective corrosion presents during the hot corrosion process of TiAl alloy in the molten salt corroding environment consisting of 25%K2SO4+75%Na2SO4 (mass fraction). TiO2 and Al2O3 are the main products during hot corrosion of the alloy, and the oxide scale is loose and porous with poor adhesive ability to matrix alloy.
3) The Si-Al-Y co-deposition shows better hot corrosion resistance at the initial stages of hot corrosion. However, with the time prolongation, the Si-Al-Y co-deposition coating fails for the formation of internal sulfidation, leading to the occurrence of cracks.
Contributors
The overarching research goals were developed by XIE Fa-qin and LI Yong-quan. The initial draft of the manuscript was written by LI Yong-quan. All authors replied to reviewers’ comments and revised the final version.
Conflict of interest
LI Yong-quan, XIE Fa-qin and YANG Shao-lin declare that they have no conflict of interest.
References
[1] WANG S Q, XIE F Q, WU X Q, CHEN L Y. CeO2 doped Al2O3 composite ceramic coatings fabricated on γ-TiAl alloys via cathodic plasma electrolytic deposition [J]. Journal of Alloys and Compounds, 2019, 788: 632-638. DOI: 10.1016/j.jallcom.2019.02.065.
[2] CHANG J, LI F, ZHU S Y, YU Y, QIAO Z H, YANG J. Electrochemical corrosion and tribological evaluation of TiAl alloy for marine application [J]. Tribology International, 2017, 115: 483-492. DOI: 10.1016/j.triboint.2017.06.027.
[3] XIANG Z D, ROSE S R, BURNELL-GRAY J S. Co-deposition of aluminide and silicide coatings on-Ti-Al by pack cementation process [J]. Journal of Materials Science, 2003, 38: 19-28. DOI: 10.1023/A:1021149413017.
[4] SINGH V, MONDAL C, KUMAR A, BHATTACHARJEE P, GHOSAL P. High temperature compressive flow behavior and associated microstructural development in a β-stabilized high Nb-containing γ-TiAl based alloy [J]. Journal of Alloys and Compounds, 2019, 788: 573-585. DOI: 10.1016/ j.jallcom.2019.02.207.
[5] LIN H, LIANG W P, JIA Y L, MIAO Q, HU R Y, YU L J. Effect of Al-Y gradient coating on hot corrosion resistance of γ-TiAl alloy at different temperatures [J]. Applied surface Science, 2019, 487: 868-875. DOI: 10.1016/j.apsusc.2019. 05.168.
[6] WU L K, WU J J, WU W Y, HOU G Y, CAO H Z, TANG U P, ZHANG H B, ZHENG G Q. High temperature oxidation resistance of γ-TiAl alloy with pack aluminizing and electrodeposited SiO2 composite coating [J]. Corrosion Science, 2019, 146: 18-27. DOI: 10.1016/j.corsci.2018. 10.031.
[7] ZHANG N, LIN J P, WANG Y L. Influence of W, B, and Y elements on antioxidation of high temperature and long term for Ti-Al based alloys with high Nb content [J]. Rare Metal Materials and Engineering, 2007, 36: 884-887. DOI: CNKI:SUN:COSE.0.2007-05-031.
[8] XIAO Z X, ZHENG L J, WANG L. Microstructure evolution of Ti-47Al-2Cr-2Nb alloys in the liquid-metal-cooling (LMC) directional-solidification process [J]. Journal of Wuhan University of Technology-Materials Science Edition, 2011, 26: 197-201. DOI: CNKI:SUN:WLGY.0.2011-02- 005.
[9] CLEMENS H, SMARSLY W. Light-weight intermetallic titanium aluminidesstatus of research and development [J]. Advanced Materials Research, 2011, 278: 551-556. DOI: 10.4028/www.scientific.net/AMR.278.551.
[10] IMAYEV V, IMAYEV R, KHISMATULLIN T, OLENEVA T, GUHTER V, FECHT H J. Microstructure and processing ability of β-solidifying TNM-based γ-TiAl alloys [J]. Materials science forum, 2010, 638: 235-240. DOI: 0.4028/ www.scientific.net/MSF.638-642.235.
[11] LI X Y, FAN A L, TANG B. Tribological behavior of molybdenum alloying layer on Ti6Al4V by double glow discharge technique [J]. Tribology, 2003, 23: 108-111. DOI: CNKI:SUN:MCXX.0.2003-02-007.
[12] GORAL M, SWADZBA L, MOSKAL G, HETMANCZYK M, TETSUI T. Si-modified aluminide coatings deposited on Ti46Al7Nb alloy by slurry method [J]. Intermetallics, 2009, 17: 965-967. DOI: 10.1016/j.intermet.2009.04.006.
[13] WANG J Q, KONG L Y, LI T F, XIONG T Y. High temperature oxidation behavior of Ti(Al,Si)3 diffusion coating on γ-TiAl by cold spray [J]. Transactions of Nonferrous Metals Society of China, 2016, 26: 1155-1162. DOI: 10.1016/S1003-6326(16)64214-0.
[14] SWADZBA L, MACIEJNY A, MENDALA B, MOSKAL G, JARCZYK G. Structure and resistance to oxidation of an Al-Si diffusion coating deposited by arc-PVD on a TiAlCrNb alloy [J]. Surface and Coatings Technology, 2003, 165: 273-280. DOI: 10.1016/s0257-8972(02)00742-9.
[15] LI X T, HUANG L J, JIANG S, GAO Y N, WANG Q S, ZHANG R, GENG L. Microstructure and super oxidation resistance of the network structured Ti-Al-Si coating [J]. Journal of Alloys and Compounds, 2019, 80730: No. 151679. DOI: 10.1016/j.jallcom.2019.151679.
[16] LUO Q, LI Q, ZHANG J Y, CHEN S L, CHOU K C. Experimental investigation and thermodynamic calculation of the Al-Si-Ti system in Al-rich corner [J]. Journal of Alloys and Compounds, 2014, 602: 58-65. DOI: 10.1016/ j.jallcom.2014.02.107.
[17] LUO Q, LI Q, ZHANG J Y, CHEN S L, CHOU K C. Microstructural evolution and oxidation behavior of hot-dip 55wt.% Al-Zn-Si coated steels [J]. Journal of Alloys and Compounds, 2015, 646: 843-851. DOI: 10.1016/j.jallcom. 2015.05.257.
[18] CHOU K C, LUO Q, LI Q, ZHANG J Y. Influence of the density ofoxide on oxidation kinetics [J]. Intermetallics, 2014, 47: 17-22. DOI: 10.1016/j.intermet.2013.11.024.
[19] LI Y Q, QIN C, LI J L, JIANG L, GENG G H. Microstructure and hot corrosion behavior of Al-Ce-Y coatings on DZ125 nickel-based alloy prepared by pack cementation process [J]. Journal of Central South University, 2020, 27: 381-387. DOI: https://doi.org/10. 1007/s11771-020-4303-4.
[20] WANG H Y, ZHANG X, XU Z, WANG H, ZHU C S. Hot corrosion behaviour of Al-Si coating in mixed sulphate at 1150 °C [J]. Corrosion Science, 2018, 147: 313-320. DOI: 10.1016/j.corsci.2018.11.026.
[21] TIAN X D, GUO X P, SUN Z P, LI M, WANG L J. Effects of Y2O3/Y on Si-B co-deposition coating prepared through HAPC method on pure molybdenum [J]. Journal of Rare Earths, 2016, 34: 952-957. DOI: 10.1016/S1002-0721(16) 60120-5.
[22] ZHANG P, GUO X P. Y and Al modified silicide coatings on an Nb-Ti-Si based ultrahigh temperature alloy prepared by pack cementation process [J]. Surface and Coating Technology, 2011, 206: 446-454. DOI: 0.1016/j.surfcoat. 2011.07.056.
[23] PFLUMM R, FRIEDLE S, SCHUTZE M. Oxidation protection of γ-TiAl-based alloys (A review) [J]. Intermetallics, 2015, 56: 1-14. DOI: 10.1016/j.intermet. 2014.08.002.
[24] ZHOU W, ZHAO Y G, QIN Q D. A new way to produce Al-Cr coating on Ti alloy by vacuum fusing method and its oxidation resistance [J]. Materials Science and Engineering A, 2006, 430: 254-259. DOI: 10.1016/j.msea.2006.05.101.
[25] XU Y, MIAO Q, LIANG W P, YU X S, JIANG Q, ZHANG Z G, REN B L, YAO Z J. Tribological behavior of Al2O3/Al composite coating on γ-TiAl at elevated temperature [J]. Materials Characterization, 2015, 101: 122-129. DOI: 10.1016/j.matchar.2015.01.009.
[26] LI Y Q, XIE F Q, WU X Q. Effects of Y2O3 on the microstructures and wear resistance of Si-Al-Y Co-deposition coatings prepared on Ti-Al Alloy by pack cementation technique [J]. Applied Surface Science, 2013, 287: 30-36. DOI: 10.1016/j.apsusc.2013.09.050.
[27] LIN N M, ZHAO L L, LIU Q, ZOU J J, XIE R Z, LI D L, TANG B. Preparation of titanizing coating on AISI 316 stainless steel by pack cementation to mitigate surface damage: Estimations of corrosion resistance and tribological behavior [J]. Journal of Physics and Chemistry of Solids, 2019, 129: 387-400. DOI: 10.1016/j.jpcs.2019.01.029.
[28] LI Y Q, XIE F Q, Wu X Q, LI X. Microstructure and high temperature oxidation resistance of Si-Al-Y Co-deposition coatings prepared on TiAl alloy by pack cementation process [J]. Journal of Inorganic Materials, 2013, 28(12): 1369- 1375. DOI: 10.1016/S1003-6326(15)63666-4.
[29] LI Y Q, XIE F Q, WU X Q. Si-Al-Y Co-deposition coatings prepared on Ti-Al Alloy for enhanced high temperature oxidation resistance [J]. Journal of Wuhan University of Technology-Material, 2018, 33: 959-964. DOI: 10.1007/ s11595-018-1919-4.
[30] LI Y Q, XIE F Q, WU X Q. Effects of Y2O3 on the microstructures and wear resistance of Si-Al-Y co-deposition coatings prepared on Ti-Al alloy by pack cementation technique [J]. Applied Surface Science, 2013, 287: 30-36. DOI: 10.1016/j.apsusc.2013.09.050.
[31] LI Y Q, XIE F Q, WU X Q, YAO X F. Effects of Temperature on microstructures of Si-Al-Y co-deposition coatings on TiAl alloy [J]. Journal of Materials Engineering, 2014, 6: 22-27. DOI: 10.3969/j.issn.1001-4381.2013.06. 001v.
[32] LIN H, LIANG W P, JIA Y, MIAO Q, HU R Y, DING Z, YU L J. Effect of Al-Y gradient coating on hot corrosion resistance of γ-TiAl alloy at different temperatures [J]. Applied Surface Science, 2019, 487: 868-875. DOI: 10.1016/j.apsusc.2019.05.168.
[33] BRADY M P, BRINDLEY W J, SMIALEK J L. The oxidation and protection of gamma titanium aluminides [J]. JOM, 1996, 11: 46-50. DOI: 10.1007/bf03223244.
[34] ZHAO W Y, XU B W, MA Y, GONG S K. Inter-phase selective corrosion of γ-TiAl alloy in molten salt environment at high temperature [J]. Progress in Nature Science: Materials International, 2011, 21: 322-329. DOI: CNKI:SUN:ZKJY.0.2011-04-010.
[35] SHIRVANI K, SAREMI M, NISHIKATA A, TSURU T. Electrochemical study on hot corrosion of Si-modified aluminide coated In-738LC in Na2SO4-20wt.% NaCl melt at 750 °C [J]. Corrosion Science, 2003, 45: 1011-1021. DOI: 10.1016/ S0010-938X(02)00127-0.
(Edited by FANG Jing-hua)
中文导读
TiAl合金表面Si-Al-Y渗层的组织及热腐蚀性能
摘要:为了提高TiAl合金的抗热腐蚀性能,采用1050 °C下扩散共渗4 h的方法在TiAl合金表面制备了Si-Al-Y渗层。研究了TiAl合金基体及渗层在900 °C的25%K2SO4+75%Na2SO4熔盐(质量分数)中的热腐蚀行为,探讨了其腐蚀速率和腐蚀机理。结果表明:Si-Al-Y共渗层由外向内依次为 TiSi2外层、(Ti,X)5Si4及(Ti,X)5Si3(X表示Nb, Cr)中间层、TiAl2和γ-TiAl内层及富Al 的过渡层。在K2SO4+Na2SO4熔盐中,TiAl合金沿着层片状的α2相发生了选择性的腐蚀;经过制备Si-Al-Y渗层后,TiAl合金的抗热腐蚀性能得到了显著的提高。
关键词:TiAl合金;Si-Al-Y渗层;组织;热腐蚀
Foundation item: Project(2020AAC02025) supported by the Natural Science Foundation of Ningxia Province, China; Project(51961003) supported by the National Natural Science Foundation of China; Project(TJGC2019040) supported by the Ningxia Youth Talents Supporting Program, China; Project(2020xyzc103) supported by the Foundation of North Minzu University, China
Received date: 2019-11-26; Accepted date: 2020-07-07
Corresponding author: LI Yong-quan, PhD; Tel/Fax: +86-951-2067378; E-mail: 8386595@163.com; ORCID: https://orcid.org/0000- 0001-6095-8761
Abstract: In order to obtain a high-performance surface on TiAl alloy that can meet the requirements in hot corrosion environment, Si-Al-Y coatings were fabricated by pack cementation process at 1050℃ for 4 h. Corrosion behaviors of the TiAl alloy with and without Si-Al-Y coatings are compared to illustrate the factors and corresponding mechanism in molten salt environment of 25wt% K2SO4 and 75wt% Na2SO4 at 900 °C. The obtained Si-Al-Y coating was mainly composed of a TiSi2 outer layer, a (Ti, X )5Si4 and (Ti, X )5Si3 ( X represents Nb or Cr element) middle layer, a TiAl2 inner layer and a Al-rich inter-diffusion zone. The inter-phase selective corrosion containing corrosion pits extending along α2 phase from lamellar interfaces in hot corrosion tested TiAl alloy was observed. However, by being coated with Si-Al-Y coating, the hot corrosion performance of TiAl alloy was improved remarkably.
- Microstructure and hot corrosion resistance of Si-Al-Y coated TiAl alloy
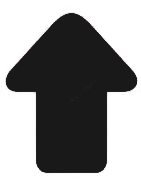