- Abstract:
- 1 Introduction  ...▲
- 2 Experimental ▲
- 3 Results and discussion▲
- 4 Conclusions ▲
- References
- Figure
- Fig.1 Change curves of bending strength and porosity with CaO content for 10NiO-NiFe2O4 composite ceramics
- Fig.2 Change curve of fracture toughness with CaO content for 10NiO-NiFe2O4 composite ceramics
- Fig.3 SEM images of 10NiO-NiFe2O4 composite ceramics: (a) Undoped ceramics; (b) CaO doped ceramics
- Fig.4 SEM images of 10NiO-NiFe2O4 composite ceramics after thermal shock cycle: (a) Undoped ceramics; (b) CaO doped ceramics
J. Cent. South Univ. Technol. (2008) 15: 25-28
DOI: 10.1007/s11771-008-0006-y
Effect of CaO doping on mechanical properties and thermal shock resistance of 10NiO-NiFe2O4 composite ceramics
LAI Yan-qing(赖延清), ZHANG Yong(张 勇), ZHANG Gang(张 刚), TIAN Zhong-liang(田忠良), LI Jie(李 劼)
(School of Metallurgical Science and Engineering, Central South University, Changsha 410083, China)
Abstract:
The CaO doped 10NiO-NiFe2O4 composite ceramics were prepared by the cold isostatic pressing-sintering process, and the effects of CaO content on the phase composition, mechanical property and thermal shock resistance of 10NiO-NiFe2O4 composite ceramics were studied. The results show that the samples mainly consist of NiO and NiFe2O4 when content of CaO is less than 4%(mass fraction), bending strength increases obviously by CaO doping. Bending strength of the samples doped with 2% CaO is above 185 MPa, but that of the samples without CaO is only 60 MPa. Fracture toughness is improved obviously by CaO doping, the samples doped with 2% CaO have the maximum fracture toughness of 2.12 MPa ·m1/2 , which is about two times of that of the undoped ceramics. CaO doping is bad to thermal shock resistance of 10NiO-NiFe2O4 composite ceramics.
Key words:
mechanical property; thermal shock resistance; CaO doping; 10NiO-NiFe2O4; inert anode;
1 Introduction
The new technics of aluminum electrolysis with inert anodes and wetted cathodes has been an important research item in aluminum electrolysis industry for many years, which resolved the ultimate disadvantages, such as high energy, carbon consumption and environmental pollution[1-2]. The NiFe2O4-based cermets have been deemed to be the most potential inert anode materials with combination of good electrical conductivity of metals and low corrosion of ceramics[3-4].
The service condition for aluminum electrolysis is very rigorous for the mechanical performance of inert anodes. The NiFe2O4-based inert anodes were chapped or shelled due to their poor mechanical properties and thermal shock resistance. So the above problems have been the main technical obstacles for development of inert anode[4-6]. Modifying agent or sintering assistant is always used to improve mechanical properties and thermal shock resistance in the preparation of ceramic material. Many studies have been done on the effect of CaO doping on the mechanical property and densification of ferrite material. MEER[7] found that CaO can restrain grain growth and improve mechanical property of Mn-Zn ferrite. JOHNSON[8] pointed out that densification of Mn-Zn ferrite can be promoted and fracture toughness can be improved with CaO doping.
Based on our previous study, the CaO doped 10NiO-NiFe2O4 composite ceramics were prepared with the cold isostatic pressing-sintering process, and the
effects of CaO content on the phase composition, bending strength, fracture toughness and thermal shock resistance of 10NiO-NiFe2O4 composite ceramics were studied.
2 Experimental
2.1 Preparation of samples
Proper amount of analytic grade NiO and Fe2O3 was mixed by ball milling and then calcined at 1 200 ℃ for 6 h in static air atmosphere to obtain the 10NiO-NiFe2O4 ceramic powder. Analytic grade CaO powder with different contents of 0, 0.5%, 1.0%, 2.0% and 4.0% was added to the 10NiO-NiFe2O4 ceramic powder prepared in advance. The calcined powders were mixed with dispersant and adhesive by ball milling again for 150 min in stainless steel ball mixing pot and then compressed to form cylindrical blocks (d 20 mm×13 mm) and bars (6 mm×5 mm×42 mm) at the pressure of 200 MPa. Then they were sintered at 1 200 ℃ for 4 h in nitrogen atmosphere of efficaciously controlled oxygen partial pressure to get the desired samples.
2.2 Measurement methods
Microstructure was analyzed on JSM-6360LV scanning electron microscope and XJP-6A metallurgical microscope. Bulk density and porosity of composite ceramics were tested according to the Archimedes’ method. Three-point-bending strength of the sintered specimen was evaluated with a CSS-44100 electrical universal testing machine using span of 30 mm and cross-head speed of 0.5 mm/min. Each bending strength datum was an average of values tested of six bars. Fracture toughness and Vickers’ hardness were measured with indentation strength (IS) method based on the equation given by MU[9] using a AKASHI (AVK-A) Vickers’ hardness tester at 98 N with a load time of 10 s.
Thermal shock resistance of material was measured according to the method of thermal shock cycle index. In view of inert anode in aluminum electrolysis industry, the real electrolysis temperature of 960 ℃ was the best choice. The samples with size of d 20 mm×13 mm were put in the furnace at 960 ℃ for 30 min, then fetched out and cooled down to room-temperature. The change of crack was noted and then the samples was put in furnace at 960 ℃ for 30 min again. Repeating this thermal shock cycle till the samples cracked.
3 Results and discussion
3.1 Effect of CaO doping on bending strength of 10NiO-NiFe2O4 composite ceramics
Change curves of bending strength and porosity of CaO doping of 10NiO-NiFe2O4 composite ceramics sintered at 1 200 ℃ are shown in Fig.1. From Fig.1, it can be seen that the bending strength of sample increases obviously by CaO doping, bending strength of the samples doped with 2% CaO is above 185 MPa, but bending strength of the samples without CaO doping is only 60 MPa.
Fig.1 Change curves of bending strength and porosity with CaO content for 10NiO-NiFe2O4 composite ceramics
As shown in Fig.1, the change tendency of porosity is opposite to bending strength with increasing CaO content, when porosity is higher, the bending strength is lower. This is because the strength of ceramic material is affected by pore inside material, the relation between porosity and strength is shown as follows[9-10]:
σ=σ0 exp(-bP) (1)
where σ is strength; σ0 is strength when porosity is 0; b is constant; P is porosity.
From Eqn.(1), the strength of material decreases with increasing the porosity, the reason is that the reduction of matrix area for support load leads to the increase of stress, and the most important is that pores lead to intense stress concentrate which is the weakness place of material, otherwise, the feasibility of pores conglobates and composed cracks is very big because of the high porosity, pores and cracks are the fracture origins of stress concentration that makes material fracture under the low stress and the strength descends[9,11].
3.2 Effect of CaO doping on fracture toughness of 10NiO-NiFe2O4 composite ceramics
Change curve of fracture toughness with CaO content for 10NiO-NiFe2O4 composite ceramics sintered at 1 200 ℃ is shown in Fig.2. Fracture toughness is improved obviously by CaO doping, but the fracture toughness is reduced when the content of CaO is more than 2%. The sample doped with 2% CaO has the maximum fracture toughness of 2.12 MPa·m1/2, which is improved about one times than fracture toughness of undoping ceramic.
Fig.2 Change curve of fracture toughness with CaO content for 10NiO-NiFe2O4 composite ceramics
As Fig.3 shown that fracture manner of 10NiO-NiFe2O4 composite ceramics is changed when CaO is added to the body of ceramic. Intercrystalline fracture is the main fracture manner of undoping ceramics (Fig.3(a)), but there are both intercrystalline fracture and transcrystalline fracture in CaO doped ceramics and transcrystalline fracture is the main manner (Fig.3(b)).
In ceramic composites, there is a kind of grain boundary with thickness of several atoms existing among different grain crystallines, where impurity and second-phase are easy to concentrate and pores are easy to eliminate at grain boundary. Grain boundary is the source or trap of structure defect, initiation and expansion of crack lead to fracture and the fracture energy is low, then finally induce fracture toughness of ceramic low with intercrystalline fracture. However, the origin of transcrystalline fracture and crack are from transgranular[9]. In the view of crystal geometry, cracks expand in transgranular firstly, and may get across grain boundary only when the further energy is obtained, then the cracks access adjacent grains and continue to expand, so the fracture toughness is high. The fracture manner of 10NiO-NiFe2O4 composite ceramics is changed by CaO doping, and the fracture toughness is improved to a certain extent. However, grain boundary is embrittled and feebled because CaO concentrates at grain boundary when CaO over adding.
Fig.3 SEM images of 10NiO-NiFe2O4 composite ceramics: (a) Undoped ceramics; (b) CaO doped ceramics
3.3 Effect of CaO doping on thermal shock resistance of 10NiO-NiFe2O4 composite ceramics
Thermal shock resistance is the capacity of material that can endure temperature change and not be destructed, and it is the synthetical assessement of mechanical property and thermotics property to heat condition[12]. Thermal shock resistance of CaO doped 10NiO-NiFe2O4 composite ceramics was measured according to the method of thermal shock cycle index in this paper, results are listed in Table 1.
As shown in Table 1, thermal shock resistance of undoping 10NiO-NiFe2O4 ceramics is the best, and the samples crack after 7 cycles. But thermal shock resistance of CaO doped 10NiO-NiFe2O4 composite ceramics becomes bad due to the increase of content of CaO. When CaO content is 0.5%, samples crack after four or five thermal shock cycles, but when CaO content is 2% or 4%, samples crack only after two or three thermal shock cycles.
Table 1 Thermal shock resistance of CaO doped 10NiO- NiFe2O4 composite ceramics
Temperature field and stress field are continuously changed during thermal shock process, thermal shock cycle leads to continuous change of temperature field that certainly induces the change of stress field[13]. Internal stress is generated during the process of thermal shock cycle because there are different coefficients of thermal expansion in CaO doped 10NiO-NiFe2O4 composite ceramics, increase of heat stress in temperature rise period is just the inverse process of residual heat stress development in cooling process. Mismatch of thermal behavior is aggravated in process of thermal shock cycle due to CaO doping, and the transitions between elastic stage and plastic stage are not simultaneous with different degrees, residual stress field and residual thermal stress are not counteracted but aggravated. The formation and expansion of cracks are caused by different coefficients of thermal expansion, and the increase of CaO content induces mismatch of thermal behavior aggravated, which accelerates the shock destroying process and makes the thermal shock resistance of material reduce obviously.
SEM images of 10NiO-NiFe2O4 composite ceramics after thermal shock cycle are shown in Fig.4. It can be seen from Figs.3 and 4, fracture pattern of samples undoped CaO is not changed during thermal shock process, however, fracture pattern of CaO doped samples is changed obviously. Comparing Fig.3(b) with Fig.4(b), transcrystalline fracture is the main fracture method in samples without thermal shock cycle, but in samples with thermal shock cycle intercrystalline fracture is the main fracture method, furthermore, grain and grain boundary become indistinct, fracture plane is almost a flat. The reason may be that second-phase impurities are segregated at grain boundary during thermal shock process. CaO, Ca2Fe2O5 or CaFe2O4 exist in ceramic body and grain boundary, and segregation of them at grain boundary is possible, the segregation of Ca2+ at grain boundary may be the important reason of grain boundary embrittled[14] . Along with increasing the content of Ca2+ segregation at grain boundary, the mismatch of thermal behavior is aggravated in grain boundary, then grain boundary becomes the breeding ground of cracks, fracture method of material is changed finally, and the thermal shock resistance is reduced.
Fig.4 SEM images of 10NiO-NiFe2O4 composite ceramics after thermal shock cycle: (a) Undoped ceramics; (b) CaO doped ceramics
4 Conclusions
1) Phase composition and crystal structure of 10NiO-NiFe2O4 composite ceramics are not affected by addition of CaO. The XRD patterns show that the CaO doped 10NiO-NiFe2O4 composites mainly consist of NiO and NiFe2O4.
2) The bending strength is improved obviously by CaO doping. The samples doped with 2% CaO have the maximum bending strength of 185 MPa, it is more than two times of bending strength (60 MPa) of undoped samples.
3) Fracture toughness of 10NiO-NiFe2O4 composite ceramics is improved obviously by CaO doping, the samples doped with 2% CaO have the maximum fracture toughness of 2.12 MPa·m1/2 , which is improved about one times than fracture toughness (1.16 MPa·m1/2) of undoped ceramics. Fracture method is changed and fracture energy is improved due to CaO doping. However, when CaO over adding, grain boundary is embrittled and feebled because CaO concentrates at grain boundary, cracks are easy to initiate and expand, which is bad to improve fracture toughness.
4) CaO doping is bad to thermal shock resistance of 10NiO-NiFe2O4 composite ceramics, and thermal shock resistance becomes worse due to the increased content of CaO. The reason is that mismatch of thermal behavior is aggravated and heat stress is improved in process of thermal shock cycle due to CaO doping, and the segregation of Ca2+ at grain boundary induces grain boundary embrittle and fracture method change.
References
[1] LI Jie, LAI Yan-qing, ZHOU Ke-chao, LI Zhi-you, LIU Ye-xiang. Preparation and preliminary testing of cermet inert anode for aluminum electrolysis[J]. Trans Nonferrous Met Soc China, 2003, 13(3): 663-670.
[2] KENIRY J. The economics of inert anodes and wettable cathodes for aluminum reduction cells[J]. JOM, 2001, 53(5): 43-47.
[3] SADOWAY D R. Inert anodes for the Hall-Héroult cell: The ultimate materials challenge[J]. JOM, 2001, 53(5): 34-35.
[4] PAWLEK R P. Inert anodes: An update[C]// SCHNEIDER W. Light Metals 2002. Warreudale, PA: TMS, 2002: 449-456.
[5] WEYAND J D, DEYOUNG D H, RAY S P, TAKCY G P, BAKER F W. Inert anodes for aluminum smelting[R]. DOE/CS/40158-20. Washington D. C: Aluminum Company of America, 1986.
[6] ALCOM T R, TABEREAUX A T, RICHARDS N E, WINDISDO C F, Dr STRACHAN D M Jr, GREGG J S, FREDERICK M S. Operational results of pilot cell test with cermet inert anodes[C]// SUBODH K D. Light Metals. Warrendale, PA: TMS, 1993: 433-443.
[7] van der MEER A B D. Mechanical strength of magnesium zinc ferrites for Yokerings[C]// HIROSHI W. Ferrite: Proceedings of International Conference. Tokyo: D Reidel Publishing Company, 1980: 301-305.
[8] JOHNSON D W. Recent progress on mechanical properties of ferrites[C]// FERRITE H W. Proceedings of International Conference. Tokyo: D Reidel Publishing Company, 1980: 285-291.
[9] ZHANG Qing-chun. Mechanical properties of ceramics[M]. Beijing: Science Press, 1987. (in Chinese)
[10] MU Bai-chun. Tenacious of ceramics[M]. Beijing: Metallurgical Industry Press, 2002.
[11] HUANG Pei-yun. Powder metallurgical principle[M]. Beijing: Metallurgical Industry Press, 1997. (in Chinese)
[12] SONG Shi-xue, AI Xing, HUANG Chuan-zhen. Study development for thermal shock resistance and it’s mechanisms of ceramics[J]. Journal of Ceramics, 2002, 23(4): 233-237. (in Chinese).
[13] SUI Wan-mei, HUANG Yong. Behavior and mechanism of thermal shock resistance in multiphase ceramics[J]. Materials Review, 2000, 14(2): 34-35.(in Chinese).
[14] MU Bai-chun. Influence of thermal shock on the properties of high-temperatural structural ceramic[J]. Journal of Jinzhou Institute of Technology, 1991, 10(4): 27-32. (in Chinese)
Foundation item: Project(2005CB623703) supported by the National Basic Research Program of China
Received date: 2007-07-02; Accepted date: 2007-09-18
Corresponding author: LAI Yan-qing, Professor; Tel: +86-731-8876454; E-mail: 13975808172@126.com
- Effect of CaO doping on mechanical properties and thermal shock resistance of 10NiO-NiFe2O4 composite ceramics
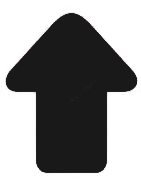