- Abstract:
- 1 Introduction▲
- References
- Figure
- Fig.1 Schematic diagram of sedimentary stability test
- Fig.2 Self-made shear yield stress test device
- Fig.3 Relationship between sedimentary stability of MRF and additives
- Fig.4 Relationship between sedimentary stability and mass fraction of carbonyl iron particles
- Fig.5 Relationship between sedimentary stability and time
- Fig.6 Relationship between viscosity and shear velocity
- Fig.7 Relationship between shear yield stress and magnetic field intensity
J. Cent. South Univ. Technol. (2008) 15(s1): 252-255
DOI: 10.1007/s11771-008-357-4
Characteristic analysis of magnetorheological fluid based on different carriers
ZHANG Jian(张 建), ZHANG Jin-qiu(张进秋), JIA Jin-feng(贾进峰)
(Department of Technical Support Engineering, Academy of Armored Force Engineering,Beijing 100072, China)
Abstract:
In order to prepare special MRFs to satisfy the demands of tracked vehicle, two different carrier fluids were used to prepare MRFs. Preparation of MRF, which are based on carrier of special shock absorption fluid and 45# transformer oil, was finished. And characteristics of these samples were tested and analyzed. The results show that Tween-80 and Span-80 can improve the sedimentary stability, and the larger mass fraction can also increase the sedimentary stability. Using 45# transformer oil instead of special shock absorption fluid as a carrier of MRF, the shear yield stress remains nearly constant but the viscosity and the sedimentary stability are reduced. The MRF with diameter of 2.73 ?m shows better sedimentary stability than that of the MRF with diameter of 2.30 ?m, or 4.02 ?m. Stearic acid obviously improves sedimentary stability and off-state viscosity, but has no function on the shear yield stress. In magnetic field of 237 kA/m, the shear yield stress of MRF based on special shock absorption fluid is 18.34 kPa and the shear yield stress of MRF based on 45# transformer oil is 14.26 kPa.
Key words:
1 Introduction
Magnetorheological fluids(MRFs) can respond to an externally applied magnetic field with a rapid and reversible change in their apparent viscosity. They have attracted much interest in their various engineering applications such as dampers, shock absorbers, isolators and brakes[1-4], especially in vehicle engineering and civil engineering structures[5-7].
MRF is a phase-controllable magnetic suspension, which contains the magnetizable particle, non-magnetizable suspending fluid and additives. MRFs behave similarly to Newton fluid without an applied magnetic field; under external magnetic field, the behavior of MRFs can be described by the Bingham plastic model. When certain magnetic field intensity is imposed, the magnetic particles form chain clusters in the direction of the external field[8].
2 Experimental2.1 The first phase experiment
In order to make clear components and additives, this set of experiments was used to evaluate the sedimentary stability of MRF samples. The additives were dispersed uniformly in carrier, and kept the mixture in 60 ℃ for 1 h, and then carbonyl iron particles were dispersed in the mixture, the MRF samples were mixed round in the colloid milling machine for 24 h. Carbonyl iron particles with diameter of 4.02 ?m were dispersed in special shock absorption fluid to prepare 7 kinds of MRF, and they were MRF11, MRF12, MRF13, MRF14, MRF15, MRF16 and MRF17. Their corresponding mass fraction were 80%, 80%, 80%, 50%, 60%, 70% and 80%, respectively, and their corresponding additives were Tween-60 and Span-60, OP and oleic acid, Tween-80 and Span-80, OP and oleic acid, OP and oleic acid, OP and oleic acid, OP and oleic acid. Then sedimentary stability of the MRF samples was tested and the results were researched.
2.2 The second phase experiment
To comprehensively investigate and analyze sedimentary stability, off-state viscosity and shear yield stress, the second phase experiment was designed.
Carbonyl iron with diameter of 2.30 ?m is produced by Beijing Mountain Technical Development Center for Non-Ferrous Metals and the purity is 98.5%; the carbonyl iron with other diameter is produced by Beijing Youxinglian Non-Ferrous Metals Co., Ltd and its purity is 99.5%. The components of MRF are listed in Table 1.
Table 1 Components of MRF
3.1 Sedimentary stability
Since the density of the dispersed iron particles was much higher than that of the carrier fluid, sedimentation of the iron particles was generally observed. Due to placing in the lab for a long period time, MRFs settled and agglomerated so easily that parts of carbonyl iron particles lost their magnetorheological effect. Sedimentary rate(R) can be determined by placing the MRF in a vertical cylindrical container at room temperature[10]. As shown in Fig.1, R can be calculated by:
R=?h/h (1)
where ?h is the length of the turbid fluid, and h is the whole length of the fluid.
Fig.1 Schematic diagram of sedimentary stability test
3.2 Off-state viscosity
In zero magnetic field (off-state), some of the MRFs behave similarly to Newton Fluid, their off-state viscosity has no relationship with shear strain rate; and some of the MRFs at off-state behave characteristics of non-Newton Fluid, whose viscosity is inversely proportional to the shear strain rate. Off state viscosity of MRFs versus shear strain rate was measured by SNB-1 viscosimeter (Shanghai Exact Science Instruments Co. Ltd).
3.3 Shear yield stress
Shear yield stress is one of important parameters in characteristics of MRF. The method of measuring the shear yield stress is shown in Fig.2. By changing current value to alter magnetic flux density, the shear yield stress is evaluated by press force. The shear yield stress[11] can be calculated from Eqn.(2):
τy=Fy/(πr2) (2)
where τy is shear yield stress, r is radius of the hole, and Fy is the press force measured by sensor.
Fig.2 Self-made shear yield stress test device
4 Results and discussions4.1 Sedimentary stability
In the first phase experiment, according to Fig.3, sedimentary stability of MRF with additives of Tween-80 and Span-80 is better than that of two other MRFs with additives of OP and oleic acid, or Tween-60 and Span-60. This result indicates that Tween-80 and Span-80 can improve the sedimentary stability of MRF.
Fig.3 Relationship between sedimentary stability of MRF and additives
Fig.4 shows the length of turbid fluid (?h) of MRF14, MRF15, MRF16 and MRF17 placed for 24 h in the lab. According to Fig.4, the higher mass fraction of carbonyl iron particles, the bigger the value of ?h, and the better sedimentary stability. Because mass fraction of carbonyl iron particles is in direct proportion to viscosity of MRFs, and the sedimentary velocity becomes slower, and then sedimentary stability is improved better.
Fig.4 Relationship between sedimentary stability and mass fraction of carbonyl iron particles
According to Fig.5, the sedimentary stability of MRF with diameter of 2.73 ?m is better than that of MRF with diameter of 4.02 ?m or 2.30 ?m. This phenomenon can be explained by Stokes equation:
V=(ρ-ρ0)gd2/(18η) (3)
where V is the sedimentary velocity of particles in carrier fluid; ρ and d are the density and radius of the particles, respectively; ρ0 and η are the density and viscosity of the carrier fluid, respectively; g is the gravitational constant.
Fig.5 Relationship between sedimentary stability and time
According to Eqn.(3), the sedimentary velocity of MRF21, MRF22 and MRF23 are calculated in Table 2, where, gravitational constant g=10 m/s2, density of the particles ρ=7.8×103 kg/m3, the density of the carrier ρ0=0.8×103 kg/m3, as shown in Table 2.
Obviously, according to Table 2, MRF22 has the slowest sedimentary velocity. This result accords well with the observed phenomenon. Thus, the sedimentary stability of MRF with diameter of 2.73 ?m is better than that of MRF with diameter of 4.02 ?m or 2.30 ?m.
Table 2 Sedimentary velocity
Additionally, according to Fig.5, the sedimentary stability of MRF24 is the worst, mostly because the viscosity of 45# transformer oil is much lower than that of special shock absorption fluid and viscosity of MRF based on 45# transformer oil is lower than that of MRF based on special shock absorption fluid. Sedimentary stability of MRF25 is much better than that of MRF21, this indicates that stearic acid can increase the viscosity of MRF and improve sedimentary stability of MRF.
4.2 Off-state viscosity
Fig.6 shows the results of MRF viscosity measured in 22.3 ℃. According to Fig.6, viscosity of all MRF exhibits shear-thinning behavior. Viscosity of MRF24 based on 45# transformer oil is the lowest, because except for MRF24 other MRFs are based on special shock absorption fluid which has a bigger viscosity than 45# transformer oil. From the viscosity of MRF21, MRF22 and MRF23, diameter of the carbonyl iron particles has strong influence on the viscosity of MRF—means that diameter of the particles is almost in direct proportion to the viscosity of MRF. Comparing the viscosity of MRF25 to MRF21, it is easy to observe that the viscosity of MRF25 is higher than that of MRF21,and that stearic acid increases the viscosity of MRF.
Fig.6 Relationship between viscosity and shear velocity
4.3 Shear yield stress
Fig.7 shows the relationship of shear yield stress with different magnetic field intensities. For an increase in magnetic field intensity, a similar increase in the shear yield stress is observed. This is because the stronger magnetic field intensity makes the pull force among the soft magnetic particles bigger, and thus the shear stress becomes bigger to break the column-like structures formed by magnetic particles. According to the curves of MRF21, MRF22 and MRF23, for an increase in diameter, a similar increase in shear yield stress is observed. From the curves of MRF21 and MRF25, the shear yield stress is similar and has not strongly difference and this indicates that stearic acid don’t change the shear yield stress of MRF. From the curves of MRF21 and MRF24, although the MRFs are based on different carriers they have similar shear yield stress but different viscosities. In practice, 45# transformer oil can also be used instead of special shock absorption fluid to prepare MRF with low viscosity, to some extent. In magnetic field of 237 kA/m, the shear yield stress of MRF23 is 18.34 kPa and the shear yield stress of MRF24 is 14.26 kPa.
Fig.7 Relationship between shear yield stress and magnetic field intensity
5 ConclusionsNumerous MRFs based on such carriers as special shock absorption fluid and 45# transformer oil are prepared, and their sedimentary stability, off-state viscosity and shear yield stress are tested and analyzed. The results indicate:
1) Tween-80 and Span-80 can improve the sedimentary stability, and the larger mass fraction can also increase the sedimentary stability.
2) Viscosity and shear yield stress are in direct proportion to the diameter of carbonyl iron particles.
3) 45# transformer oil can also be used as a carrier and MRF based on this oil can have a low viscosity.
4) Sedimentary stability of MRF with particle diameter of 2.73 ?m is the best among the three kinds of diameters.
5) Stearic acid can increase the viscosity and sedimentary stability of MRF, but can’t improve shear yield stress of MRF.
6) In magnetic field of 237 kA/m, the shear yield stress of MRF based on special shock absorption fluid is 18.34 kPa and the shear yield stress of MRF based on 45# transformer oil is 14.26 kPa.
References
[1] JOLLY M R, BENDER J W, CARLON J D. Properties and applications of commercial magnetorheological fluids [J]. Journal of Intelligent Material Systems and Structures, 1999, 10(1): 5-13.
[2] CARLSON J D, CHRZAN M J, RALEIGH N C, GIRARD F J. Magnetorheological fluid devices: US, 5284330 [P]. 1994-02-08.
[3] CAO Zhen, JIANG Wan-quan, YE Xing-zhu, GONG Xing-long. Preparation of superparamagnetic Fe3O4/PMMA nano composites andtheir magnetorheological characteristics [J]. Journal of Magnetism and Magnetic Materials, 2008, 320: 1499-1502.
[4] VIOTA J L, VICENTE J D, DURAN J D G, DELGADO A V. Stabilization of magnetorheological suspensions by polycyclic acid polymers [J]. Colloid and Interface Science, 2005, 284: 527-541.
[5] ISMO V. MR fluid-based damping force control for vehicle cabin vibration suppression [C]// ISMO V. Smart Materials and Structures VTT Research Program 2000-2002. Espoo, Finland: VTT Technical Research Center of Finland, 2002: 51-66.
[6] GORDANINEJAD F, KELSO S P. Fail-safe magneto-rheological fluid dampers for off-highway, high-payload vehicles [J]. Journal of Intelligent Material System and Structures, 2000, 11(5): 395-406.
[7] YANG G, SPENCER B F, CARLSON J D. Large-scale MR fluid damper: Modeling and dynamic performance considerations [J]. Engineering Structures, 2002, 24: 309-323.
[8] FERNANDO D G, CARLSON J D. Investigating the time dependence of the MR effect [C]// GORDANINEJAD F. Proceeding of the 10th International Conference on ER Fluids, MR Suspensions. Lake Tahoe, USA: World Scientific, 2006: 165-171.
[9] PARK J H, CHIN B D, PARK O O. Rheological properties and stabilization of magnetorheological fluids in a water-in-oil emulsion [J]. Journal of Colloid and Interface Science, 2001, 240: 349-354.
[10] JUN J, UHM S, RYU J, SUH K. Synthesis and characterization of monodisperse magnetic composite particles for magnetorheological fluid materials [J]. Colloids and Surfaces A: Physicochem Eng Aspects, 2005, 260: 157-164.
[11] FUCHS A, XIN M, GORDANINEJAD F, WANG X, HITCHCOCK G H, GECOL H, EVRENSEL C, KOROL G. Development and characterization of hydrocarbon polyol polyurethane and silicone magnetorheological polymeric gels [J]. Journal of Applied Polymer Science, 2004, 92: 1176-1182.
Received date: 2008-06-25; Accepted date: 2008-08-05
Corresponding author: ZHANG Jian, Doctor candidate; Tel: +86-10-66717632; E-mail: zhangjian5682028@163.com
- Characteristic analysis of magnetorheological fluid based ondifferent carriers
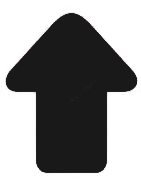