J. Cent. South Univ. Technol. (2008) 15: 459-462
DOI: 10.1007/s11771-008-0086-8
Influence of Mg3N2 powder on microstructures and
mechanical properties of AZ31 Mg alloy
ZHAO Hong-liang(赵红亮)1, ZHOU Zhan-xia(周占霞)2, LIU Xu-dong(刘旭东)1, GUAN Shao-kang(关绍康)1
(1. School of Materials Science and Engineering, Zhengzhou University, Zhengzhou 450002, China;
2. Teaching and Research Group of Numerical Control, Henan Industrial Technician College,
Zhengzhou 450007, China)
Abstract:
In order to obtain an effective and reliable grain refiner for Mg-Al alloys, 1% (mass fraction) Mg3N2 was added into AZ31 Mg alloy. The microstructures of the Mg alloys were studied by optical microscopy, scan electron microscopy and X-ray energy dispersive spectroscopy, and the mechanical properties were determined. The results show that adding a small amount of Mg3N2 to AZ31 Mg alloy can refine the grain size from 103 to 58 μm. The ultimate tensile strength and elongation of AZ31 Mg alloy are 174.1MPa and 8.3%, respectively. After the addition of 1% Mg3N2, the ultimate tensile strength and elongation of AZ31 Mg alloy are increased up to 198.7 MPa and 11.8%, respectively. The grain refinement mechanism is that AlN is formed after Mg3N2 is added. Both AlN and Mg phases are of HCP lattice structure, and the disregistry between Mg phases and AlN along (0001)Mg//(0001)AlN is 3.04%, which is very effective for heterogeneous nucleation.
Key words:
Mg alloy; Mg3N2; inoculation; heterogeneous nucleation;
1 Introduction
As the lightest structural alloys, Mg alloys offer good characteristics: high specific strength and stiffness, good electromagnetic shielding characteristics, superior damping capacity, etc[1-2]. So it is considered the most promising metal in the 21st century[3]. Fine grain plays an important role in further development of both wrought and cast Mg alloys[4]. Currently Al-free Mg alloys can be refined by Zr[5], but for Mg-Al alloys, a suitable grain refiner, i.e. a refiner which is effective, reliable and easy to apply has not been found yet[6].
Many researches have been performed to refine the Mg-Al alloys[7-11], but the report about AlN refining of Mg alloy is rarely found. In the fabrication of Al-Mg matrix composites, AlN particles were in-situ formed successfully by the reaction of Al with Mg3N2[12], and the possibility that AlN could be in-situ formed in the Mg-Al alloys was proved[13-14]. In order to obtain an effective and reliable grain refiner for Mg-Al alloys, 1% (mass fraction) Mg3N2 was added into AZ31 Mg alloy, and the influence of Mg3N2 powder on microstructures and mechanical properties of AZ31 Mg alloy was studied.
2 Experimental
The base composition of the alloy studied was Mg-3Al-1Zn-0.1Mn, conforming to that of AZ31 Mg alloy. The Mg3N2 powder with a size less than 10 μm was supplied by Zibo Hengshi Company, Shandong Province, China. Fig.1 shows the X-ray diffraction pattern of Mg3N2 powder. It can be seen that the powder is composed of Mg3N2 and a small quantity of MgO. The alloys were prepared in a mild steel crucible under the protection of a mixed gas atmosphere of SF6 and CO2. The alloys were melted using an electrical resistance furnace. The Mg3N2 powder was wrapped by aluminum foil and plunged into the molten melt at 750 ℃. The melt was stirred for 2 min, and then held at 720 ℃ for 30 min. Finally, the melt was poured into the permanent mold with dimensions of 25 mm×110 mm at pouring temperature of 720 ℃.
The tensile test of the as-cast bars was performed on an Instron Model 5585 material test machine. The bars were fabricated to a gauge length of 25 mm and a gauge diameter of 5 mm for ambient temperature tensile test. All the tests were carried out at a strain rate of 1 mm/min. Because the grain boundaries could not be observed clearly, solution treatment of specimens were done at 400 ℃ for 12 h and cooled in air.
The microstructural observations of the as-cast specimens were conducted using optical microscope and scan electron microscope (Philip Quanta-200). The average grain size, d, was calculated using the equation, d=1.74L, where L is the linear intercept size. The microanalysis and determination of crystal structures of the phases in the alloys were carried out by X-ray energy dispersive spectroscopy(EDS) and X-ray diffractometry (XRD).
Fig.1 XRD pattern of Mg3N2 powder
3 Results and discussion
3.1 Microstructures and mechanical properties
As shown in Figs.2 (a) and (b), the microstructures of the as-cast alloys consist of the matrix (α-Mg) and β(Mg17Al12) precipitates. Coarse dendrites (shown in Fig.2(a)) appear in the AZ31 Mg alloy, and the dendrite size obviously decreases after Mg3N2 is added (Fig.2(b)). Figs.2(c) and (d) show the microstructures after solution treatment, indicating that the grain becomes fine and uniform after Mg3N2 is added. The average grain size of the alloys decreases from 103 to 58 μm with the addition of 1% Mg3N2. The mechanical properties of the specimens are listed in Table 1. It can be seen that the addition of Mg3N2 to the AZ31 Mg alloy makes a modest improvement in mechanical properties. The ultimate tensile strength and elongation of AZ31 Mg alloy are 174.1 MPa and 8.3%, respectively. After the addition of 1% Mg3N2, the ultimate tensile strength and elongation are increased up to 198.7 MPa and 11.8%, respectively, which are improved by 14% and 42%, respectively.
3.2 Heterogeneous nucleus of α-Mg
Heterogeneous nucleus of α-Mg is found in AZ31 Mg alloy with addition of 1% Mg3N2, as shown in Fig.3. There is a crystallization center (spot A) in α-Mg, and the EDS spectrum of spot A is shown in Fig.3(b), revealing that 39.48% Mg, 39.29% O, 9.79% Al and 7.08% N with small amount of Zn and C exist in the AZ31 Mg alloy after addition of 1% Mg3N2. It can be thought that this nucleus is mainly composed of MgO and AlN. MgO maybe comes from Mg3N2 powder, as shown in Fig.1. It should be noted that the deviation of the molar ratio of Al to N from stoichiometry is probably caused by the analytical error of EDS for light elements and the original Al in AZ31 Mg alloy.
Fig.2 Microstructures of AZ31 Mg alloys: (a) AZ31 (as-cast); (b) AZ31+1% Mg3N2 (as-cast); (c) AZ31 after solution treatment; (d) AZ31+ 1% Mg3N2 after solution treatment
Table 1 Mechanical properties of AZ31 Mg alloys with and without Mg3N2
Fig.3 SEM image (a) and EDS spectrum (b) showing heterogeneous nucleus of α-Mg
3.3 Mechanism of grain refinement
It is generally believed that the final grain structure of casting is determined by the nucleation and growth conditions prevailing during solidification. A solute with excellent segregation ability is expected to have a good grain refining potency due to its stronger constitutional supercooling. The suitable nucleation substrates are required in the melt to stimulate a high nucleation frequency[15].
Heterogeneous nucleus of α-Mg was found in this work. According to the classical nucleation theory, the interfacial free energy at the nucleating interface is believed to be a key factor to control the heterogeneous nucleation efficiency. However, a simple description of such energy is impossible since the total interfacial energy of the system is very complicated and influenced by many factors, such as the disregistry and the electrostatic potential between the substrate and the nucleated crystal, the morphology of the substrate, the composition of the interface, the particle size and the distribution, etc. When the chemical parameters of the substrate and the nucleated crystal are similar, the only energy barrier to heterogeneous nucleation is the disregistry of the crystal/substrate interface, and this energy is minimum when the interface is coherent. BRAMFITT introduced the following planar disregistry model to include crystallographic combinations of two phases with planes of different atomic arrangements[16]:
(1)
where (hkl)s is the low index plane of the substrate; [uvw]s is the low index direction in (hkl)s; (hkl)n is the low index plane in the nucleated solid; [uvw]n is the low index direction in (hkl)n; and
are the atomic spacings along [uvw]s and [uvw]n; θ is the angle between [uvw]s and [uvw]n.
The result of BRAMFITT shows that in the heterogeneous nucleation, the nucleus is effective when elongation δ<6%, and mildly effective when δ=6%- 15% and not effective when δ>15%.
According to thermodynamic and experimental results in Refs.[13-14], when Mg3N2 powder is added into the Mg-Al alloy melts, the following reaction will occur:
2Al(l)+3Mg3N2(s)→2AlN(s)+3Mg(g) (2)
and AlN is formed.
Table 2 lists the lattice parameters of Mg and AlN. It can be seen that the lattice structures of AlN and Mg have high coherency. The melting point of AlN is 3 214 ℃, much higher than that of Mg (659 ℃). The crystal structure of AlN belongs to Wurtzute structure of HCP lattice, and Al and N atoms constitute HCP lattice, respectively. The two lattices stagger c/3 along axis c. That is to say, one lattice occupies the region of tetrahedron gap of the other lattice. Table 3 lists the matching parameters of some possible crystallographic orientation relationship between AlN and Mg. According to Eqn.(1), the disregistry along (0001)Mg//(0001)AlN between Mg phases and AlN is calculated to be 3.04%,which is less than 15%. Hence, it can be concluded that the grain size is refined by using AlN as the heterogeneous nucleation site. AlN can serve as the nucleating sites for α-Mg during solidification (shown in Fig.3).
Table 2 Lattice parameters of Mg and potential nucleation particle
Table 3 Matching parameters between AlN and Mg
4 Conclusions
1) Adding a small amount of Mg3N2 to AZ31 Mg alloys can refine the grain size. When 1% Mg3N2 is added, the mean grain size of AZ31 Mg alloys is decreased from 103 to 58 mm, and the ultimate tensile strength and elongation are increased by 14% and 42%, respectively.
2) The grain refinement mechanism is that AlN is formed when Mg3N2 is added into the melt. Both AlN and Mg are of the HCP lattice structures, and the disregistry along (0001)Mg//(0001)AlN between Mg phases and AlN is 3.04%, which is less than 15%. The grain size can be refined because AlN is served as the heterogeneous nucleation site.
[1] KINJI H, HIDETOSHI S, YORINOBU T, KENJI H. Effects of Ca and Sr addition on mechanical properties of a cast AZ91 magnesium alloy at room and elevated temperature [J]. Materials Science and Engineering A, 2005, A403: 276-280.
[2] TONY S, VESSELINA R NIKOLAY N. Nanocrystallization and hydrogen storage in rapidly solidified Mg-Ni-RE alloys [J]. Journal of Alloys and Compounds, 2001, 334: 219-223.
[3] MORDIKE B L, EBERT T. Magnesium: Properties—Applications— Potential [J]. Materials Science and Engineering A, 2001, A302(1): 37-45.
[4] KUBOTA K, MABUCHI M, HIGASHI K. Review processing and mechanical properties of fine-grained magnesium alloys [J]. Journal of Materials Science, 1999, 34(10): 2255-2262.
[5] TAMURA Y, KONO N, MOTEGI T. Grain refining of pure magnesium by adding Mg-Zr master alloy [J]. Journal of Japan Institute of Light Metals, 1997, 47(12): 679-684.
[6] STJOHN D H, MA Q, MARK A E. Grain refinement of magnesium alloys [J]. Metallurgical and Materials Transactions A, 2005, 36(7): 1669-1679.
[7] LEE Y, DAHLE A, STJOHN D. The role of solute in grain refinement of magnesium [J]. Metallurgical and Materials Transactions A, 2000, 31(11): 2895-2906.
[8] LIU Yan-hui, LIU Xiang-fa, BIAN Xiu-fang. Grain refinement of Mg-Al alloys with Al4C3-SiC/Al master alloy [J]. Materials Letters, 2004, 58(7/8): 1282-1287.
[9] JIN Q L, EOM J P, LIM S G. Grain refining mechanism of carbon addition method in Mg-Al magnesium alloy [J]. Scripta Mater, 2003, 49(11): 1129-1132.
[10] YANO E, TAMURA Y, MOTEGI T. Effect of carbon powder on grain refinement of an AZ91E magnesium alloy [J]. Materials Transactions, 2003, 44(1): 107-110.
[11] CHEN Jing-yang, GUAN Shao-kang, SHI Guang-xin. Effects of B on microstructure and properties of Mg-7Al-0.4Zn-0.2Mn alloy [J]. Special Casting and Nonferrous Alloys, 2005, 25(8): 454-456. (in Chinese)
[12] HOU Q H, RAJ M, MICHAEL K. Feasibility of aluminium nitride formation in aluminium alloys [J]. Materials Science and Engineering A, 1995, A195: 121-129.
[13] YE H Z, LIU X Y, BEN L. In situ synthesis of AlN in Mg-Al alloys by liquid nitridation [J]. Journal of Materials Processing Technology, 2005, 166(1): 79-85.
[14] YE H Z, LIU X Y, BEN L. In situ synthesis of AlN particles in Mg-Al alloy by Mg3N2 addition [J]. Materials Letters, 2004, 58(19): 2361-2364.
[15] LU L, DAHLE A K, TAYLOR J A. Theoretical and practical considerations of grain refinement of Mg-Al alloys [J]. Materials Science Forum, 2005, 488/489: 299-302.
[16] LU L, DAHLE A K, STJOHN D H. Grain refinement efficiency and mechanism of aluminium carbide in Mg-Al alloys [J]. Scripta Materialia, 2005, 53(5): 517-522.
Foundation item: Project(2007430023) supported by the Office of Education, Henan Province, China; Project(0612002500) supported by the Excellent Young Scientists Foundation of Henan Province, China
Received date: 2007-10-23; Accepted date: 2008-01-05
Corresponding author: ZHAO Hong-liang, Professor, PhD; Tel: +86-13523080674; E-mail: zhlwkr@zzu.edu.cn
- Influence of Mg3N2 powder on microstructures and mechanical properties of AZ31 Mg alloy
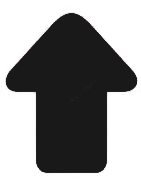