- Abstract:
- 1 Introduction▲
- 2 Experimental▲
- 3 Results and discussion▲
- 4 Conclusions▲
- References
- Figure
- Fig.1 Silicon particles distribution
- Fig.2 Phase analysis of C/C-SiC composites
- Fig.3 Polarized light optical images of C/C-SiC composite: (a) Low magnification; (b) High magnification
- Fig.4 Relationship between friction coefficient and brake pressure
- Fig.5 Relationship between friction coefficient and brake velocity
- Fig.6 Friction surface of C/C-SiC composites after 300 times braking
J. Cent. South Univ. Technol. (2009) 16: 0525-0529
DOI: 10.1007/s11771-009-0087-2
Wet friction performance of C/C-SiC composites prepared by new processing route
WANG Xiu-fei(王秀飞)1, 2, 3, YIN Cai-liu(尹彩流)2, HUANG Qi-zhong(黄启忠)1,
HE Liang-ming(何良明)2, SU Zhe-an(苏哲安)1, YANG Xin(杨 鑫)1
(1. State Key Laboratory of Powder Metallurgy, Central South University, Changsha 410083, China;
2. College of Physics and Electronic Engineering, Guangxi University for Nationalities, Nanning 530006, China;
3. Beijing Zhongnan Puran High-tech Co. Ltd, Beijing 102211, China)
Abstract:
C/C-SiC composites with SiC island distribution were prepared via a new processing route. The fabrication process mainly included silicon infiltration by ultrasonic vibration, chemical vapor deposition (CVD), siliconizing, liquid phase impregnation and carbonization. The wear and friction properties were tested by an MM-1000 wet friction machine. The results show that SiC phases are mainly distributed between carbon fibers and pyrocarbons as well as among the pryocarbons. The dynamic friction coefficient of the composites decreases gradually from 0.126 to 0.088 with the increase of the surface pressure from 0.5 to 2.5 MPa at the same rotary speed. Furthermore, under the constant surface pressure, the dynamic friction coefficient increases from 0.114 to 0.126 with the increase of the rotary speed from 1 500 to 2 500 r/min. However, the coefficient decreases to 0.104 when the rotary speed exceeds 4 500 r/min. During the friction process, the friction coefficient of C/C-SiC composite is between 0.088 and 0.126,and the wear value is zero after 300 times brake testing.
Key words:
C/C-SiC composites; wet friction; wear; microstructure;
1 Introduction
Wet friction material invented in 1930s is a special material working under the closed oil lubrication. Compared with the conventional dry friction material, wet friction material has lower wear rate, higher absorbing energy, better dustproof/airproof and less environment effect, and has been widely used in the clutches of engineering machines, and in the detents with big braking torque of large and heavily loaded automobiles in bad working circumstance [1-3].
Generally, wet friction materials include the copper-based and the paper-based friction materials [4-6]. However, powder metallurgy materials result in heat distortion and short service life easily [7]. Furthermore, the workability for paper-based material is very poor under high energy condition. At present, redesigning the cooling channel and increasing the oil pressure are not efficient ways to solve the problems mentioned above [8-9].
In 1990s, for the purpose of meeting the needs on safety driving of very high-speed train, heavily loaded automobiles and luxury car, carbon fiber-enforced ceramic matrix composites with low density, good wear resistance and temperature stability were developed in western developed country [10]. At the same time, C/C-SiC composites began to be studied in China, such as Northwestern Polytechnical University [11], National University of Defense Technology [12] and Institute of Metal Research of Chinese Academy of Sciences [13] and Central South University [14]. Great progress on fabrication technology and application has been received. However, C/C-SiC composites as wet friction material are not reported in previous studies. In order to overcome low friction coefficient, large wear rate and serious deformation in the clutch of a heavy-duty vehicle [15], a C/C-SiC composite via a new processing method was prepared. And its friction and wear properties as wet friction material were investigated.
2 Experimental
2.1 Sample fabrication
In the experiment, the polyacrylonitrile (PAN)- based carbon fibers needled felts (Torayca T700, Toray Co., Japan) were chopped into a cuboid with dimensions of 200 mm×150 mm×15 mm. Then, silicon powder
(particle size≤10 ?m) was put into aqueous solution with polyvinyl alcohol (PVA) of 6%-10% (mass fraction), and stirred to mixed slurry. After that, carbon fiber preform was immerged into the slurry entirely. The ultrasonic vibration was carried out in CQX25-06 ultrasonic washer for 30 min to disperse silicon powder into the internal perform. Chemical vapour deposition (CVD) densification was conducted at 900℃ by using propylene as carbon source and hydrogen as carrier gas. The density of the sample was 1.5-1.6 g/cm3. Then, the siliconizing was finished at 2 100 ℃ for 2.5 h. At last, C/C-SiC composites with the density of 1.85-1.95 g/cm3 and SiC content of 10%-15% were fabricated by pressured impregnating and carbonization process.
2.2 Materials characteristic and properties tests
The microstructure of C/C-SiC composite was observed by polarized light optical microscopy (PLOM) and scanning electron microscopy (SEM). Phase analysis was examined on Rigaku-3014 X-ray diffractometer. The frictional and wear behaviors of the C/C-SiC were investigated on an MM-1000 wet friction and wear tester.
The sample for friction experiment was a ring (thickness: 13-15 mm, inner diameter: 65 mm, outer diameter: 85 mm). Twelve oil grooves (width and depth: 2 mm×0.75 mm) were uniformly machined on ring surface. 65Mn (40-45HRC) rings with the same dimension were used as the mating plate. The lubricating oil was special transmitting oil of heavy vehicle, and its oil pressure was less than 1.0 MPa and the flux was 3-5 mL/(cm2·min).
Friction test would not be carried out until the contact surface area of the friction pairs attained 80% by eyes after running-in. Friction testing conditions were shown as follows.
(1) Changing specific pressures: under the same rotary inertia, inertia wheel speed was 2 500 r/min, and brake specific pressures were 0.5, 1.0, 1.5, 2.0 and 2.5 MPa, respectively.
(2) Changing rotary velocity: under the same rotary inertia, brake specific pressure was kept at 1.0MPa, and original speeds were 1 500, 2 000, 2 500, 3 000, 3 500, 4 000 and 4 500 r/min, respectively. Every condition was tested five times, and the friction coefficient of the tested material was the average value of five times tests.
(3) Wear testing conditions: the moment inertia and the brake specific pressure were 0.2 kg/m2 and 1.0 MPa, respectively. The wear rates of three points of friction ring were measured after 300 times brake, and the average value of three points was the wear rate of the tested material. The wear rate was examined by a micrometer (precision: 0.001 mm).
3 Results and discussion
3.1 Phase analysis of C/C-SiC composites
Fig.1 shows the silicon particles distribution on carbon fibers. Obviously, a lot of silicon particles with less than 10 ?m well-distributed adhered to the surface of carbon fibers. XRD analysis was preformed to investigate the phase composition of C/C-SiC composites. Diffraction pattern is shown in Fig.2. From XRD pattern, only carbon peaks and b-SiC peaks are determined, which confirms that infiltrated silicon particles entirely react with the excessive pyrocarbon to form b-SiC through heat treatment at 2 100 ℃.
Fig.1 Silicon particles distribution
Fig.2 Phase analysis of C/C-SiC composites
3.2 Microstructure of C/C-SiC composites
The PLOM images of C/C-SiC composites are shown in Fig.3. From Fig.3(a), it is seen that for the low magnification of the composites, there are some dark irregular pores on their smooth microstructure surface. The irregular bulks with micro-pores are resin carbon, between which there exist optically active pyrocarbons wrapping on the fiber external surface. The bonding form between the resin carbon and the pyrocarbon is very
Fig.3 Polarized light optical images of C/C-SiC composite: (a) Low magnification; (b) High magnification
special. Their borders are inter-crossing and penetrated. The borders of resin carbon have thin pyrocarbon. There are some big pores or cracks between annular pyrocarbons. This phenomenon is explained as follows. Shrinkage constraint originating from curing and carbonation produce leads to the rupture of two pyrocarbons, and shrinkage and gas releasing also are causes of pore development. In addition, fine physical compatibility between pyrocarbons with easy graphitization and carbon fiber makes the pyrocarbon envelop the carbon fibers. High magnification image of Fig.3(b) displays the SiC phases’ distribution in composites. SiC phases are mainly distributed between carbon fibers and pyrocarbons as well as among the pryocarbons.
3.3 Friction and wear properties
Evaluation methods for the friction properties of wet friction material are mainly the dynamic friction coefficient and its stability, so the main design idea of C/C-SiC friction material is to increase the dynamic coefficient. According to GB13826—98, the friction coefficients of material, the effects of the different brake surface pressure and the initial speed on the friction performance of C/C-SiC composites were studied therefore.
Fig.4 demonstrates that at the same initial speed, the friction coefficient decreases slowly from 0.126 to 0.088 when the brake pressure changes from 0.5 to 2.5 MPa.
Fig.4 Relationship between friction coefficient and brake pressure
At the same brake velocity, with the brake specific pressure increasing, the lubricate viscosity becomes lower when the pressure is low. Oil film is thick, and the shear force in the oil film is the most part of friction torque. Large velocity shear force results in large friction torque. This is due to that the lubrication of friction pair has Newtonian fluid character [16]. Reynolds formula of its visco-temperature performance is expressed as
(1)
where η0 and η are viscosities of temperature T0 and T, and β is viscosity-temperature coefficient.
With the increase of brake pressure, the brake time decreases and the temperature of the friction surface increases in a short time, which would result in a thinner lubricating film and the decrease of friction torque produced from the oil film shearing strength. MUKHERJEEA and SARKAR [17] reported that the increase of temperature would decrease the oil film thickness between the friction planes obviously, which enlarged the mechanical contact of friction border. The adhesion and plough effect by the mechanical contact and the absorbing and repulsive interaction increased the contact friction torque. But the decrease of lubricating velocity caused by the increase of torque that was dominant. Generally, with the increase of specific pressure, the dynamic friction torque and the friction coefficient decrease [18].
Fig.5 shows the relationship between friction coefficient and brake velocity. The friction coefficient changes from 0.118 to 0.126 when the original speed increases from 1 500 to 2 500 r/min. When the original speed is higher than 2 500 r/min, the moving friction coefficient decreases slowly to 0.104 when the brake velocity is 4 500 r/min.
Under the same specific pressure, with the increase of brake velocity, the absorbing energy from the braking process results in the increase of temperature on the material surface and the decrease of lubricating viscosity and friction coefficient. Furthermore, with the increase of bake speed, shearing thinner under the high speed also leads to the decrease of lubricate viscosity and non-Newtonian character [16]. The high shearing force is helpful for the regular arrangement of molecule, which decreases the action of near layers, the apparent viscosity and the friction coefficient.
The friction surface of C/C-SiC composites after 300 times braking is shown in Fig.6. The material surface after experiment is covered by a layer of oil film without the abrasive dusts. The pores of material are filled with the lubricant. The wear value is zero after 300 times braking, which further verified the excellent friction and wear properties of C/C-SiC composites.
Fig.5 Relationship between friction coefficient and brake velocity
Fig.6 Friction surface of C/C-SiC composites after 300 times braking
Two causes can be interpreted for zero wear rate of this material. Firstly, the absorption of this composite is very strong, which makes the lubricant tightly adhered to the surface. The friction process is carried out between the lubricants of two friction surfaces, which causes the decrease of wear rate. Secondly, the rich and connected porous structure of the material surface has good cooling effect for the material during the friction process. Therefore, the wear process of material is limited in the elastic-hydrodynamic lubrication and adhesive wear, which results in a very low wear rate.
Based on the analysis above, it is found that the dynamic friction efficient of C/C-SiC composites is 0.09-0.13, which is better than that of the in-service wet friction materials (0.05-0.09). This composite has excellent friction and wear resistance, and the wear value (0/300 times) is better than the standard of the in-service materials (0.002 mm/100 times).
4 Conclusions
(1) Ultrasonic vibration is an effective method for siliconizing of carbon fibers needled felts, because it disturbs the aggregation of silicon particles and is beneficial to Si-C reaction. The higher the original density of carbon felt, the less the content, and the smaller the dimension of penetrated silicon powder.
(2) The external surface of carbon fiber in the so-prepared C/C-SiC composites is compactly coated by pyrocarbon, and resin carbon surrounding the pryocarbons is of porous structure. Mono-dispersed SiC particles in the borders of carbon fibers and pyrocarbon are island-like.
(3) Friction coefficient of C/C-SiC composites is in the range of 0.088-0.126. At the same rotary speed, the friction coefficient decreases with the increase of brake pressure; under the same bake pressure, the friction coefficient increases firstly and then decreases with the increase of the original speed.
(4) The wear value of C/C-SiC composites is zero after 300 times wear tests.
References[1] POSER K, GAHR K H ZUM, SCHNEIDER J. Development of Al2O3 based ceramics for dry friction systems [J]. Wear,2005, 259(1/6): 529-538.
[2] YU Hai-jiao, ZHOU Xin-gui, WANG Hong-lei, ZHAO Shuang, YANG Jian-gao, HUANG Ze-lan. Processing and properties of 2D SiC/SiC composites by precursor infiltration and pyrolysis [J]. Journal of Central South University of Technology, 2009, 16(2): 190-194.
[3] EGUCHI M, YAMAMOTO T. Shear characteristics of a boundary film for a paper-based wet friction material: friction and real contact area measurement [J]. Tribology International,2005, 38(3): 327-335.
[4] PAN X D. Wet sliding friction of elastomer compounds on a rough surface under varied lubrication conditions [J]. Wear, 2007, 262(5/6): 707-717.
[5] WIRTH A, EGGLESTON D, WHITAKER R. A fundamental tribochemical study of the third body layer formed during automotive friction braking [J]. Wear, 1994, 179(1/2): 75-81.
[6] FAN Yi, LIU Bo-wei. Effect of sintering pressure on behaviours of copper-base wet frictional materials [J]. Materials Science and Engineering of Powder Metallurgy, 2002, 7(3): 228-232. (in Chinese)
[7] CAI Dan, WEI Chen-guan, SONG Wen-yue. Friction discs distortion phenomena in wet clutch [J]. Journal of Beijing Institute of Technology, 2000, 20(4): 449-451. (in Chinese)
[8] WANG Xiu-fei. Investigation on fabrication and performance of C/C-SiC composites for tank clutch [D]. Changsha: Central South University, 2007. (in Chinese)
[9] AUDEBERT N, BRABER J R, ZAGRODZKI P. Buckling of automatic transmission clutch plates due to thermo-elastic/plastic residual stresses [J]. Journal of Thermal Stresses, 1998, 21(3): 309-326.
[10] KRENKEL W, HEINDENREICH B, RENZ R. C/C-SiC composites for advanced friction systems [J]. Advanced Engineering Materials, 2002, 4(7): 427-436.
[11] YU Yong-dong, ZHANG Li-tong, CHENG Lai-fei, HAN Jin-tan. Fiber reinforced ceramic matrix composites prepared by chemical vapor infiltration [J]. Journal of the Chinese Ceramic Society, 1995, 23(3): 319-326. (in Chinese)
[12] HE Xin-bo, ZHANG Chang-rui, ZHOU Xin-gui. Effect of pyrolytic carbon coating on mechanical properties of Cf/SiC composites [J]. High Technology Letters, 2000, 10(9): 92-94.
[13] ZHANG G B, GUO Q G, WANG K J, ZHANG H, SONG Y, SHI J L, LIU L. Finite element design of SiC/C functionally graded materials for ablation resistance application [J]. Materials Science and Engineering: A,2008, 488, (1/2): 45-49.
[14] MA Yun-zhu, HUANG Bai-yun, XIONG xiang, XIAO Peng, LI Jiang-hong, HUANG Qi-zhong, YI Mao-zhong. Effect of infiltrating Si on friction properties of C/C composites [J]. Journal of Central South University of Technology, 2003, 10(3): 173-176.
[15] DING Hua-dong, HAN Wen-zheng, FU Su-li, DU Jian-hua, YU Yuan-hong. Design and manufacture of intelligent Cu-based wet friction materials [J]. Transactions of Nonferrous Metals Society of China, 2004, 14(5): 864-869.
[16] XIONG X, CHEN J, YAO P P, LI S P, HUANG B Y. Friction and wear behaviors and mechanisms of Fe and SiO2 in Cu-based P/M friction materials [J]. Wear, 2007, 262(9/10): 1182-1186.
[17] MUKHERJEEA S, SARKAR K. Effects of viscosity ratio on deformation of a viscoelastic drop in a Newtonian matrix under steady shear [J]. Journal of Non-Newtonian Fluid Mechanics, 2009, 160(2/3): 104-112.
[18] HOLGERSON M. Apparatus for measurement of engagement characteristics of a wet clutch [J]. Wear,1997, 213(1/2): 140-147.
(Edited by YANG You-ping)
Foundation item: Project(2006CB600901) supported by the Major State Basic Research and Development Program of China; Project(0991015) supported by Guangxi Science Found, China; Project(200808MS083) supported by Guangxi Education Department Found
Received date: 2008-09-15; Accepted date: 2008-11-20
Corresponding author: HUANG Qi-zhong, Professor, PhD; Tel: +86-731-88836078; E-mail: qzhuang2007@163.com
- Wet friction performance of C/C-SiC composites prepared bynew processing route
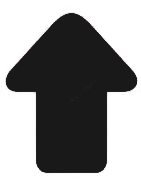