- Abstract:
- 3 Test and results analys...▲
- References
- Figure
- Fig.1 Calculating model of energy of bending waves
- Fig.2 Proportion curves of bending energy: 1—d=0; 2—d=0.5; 3—d=1.0; 4—d=2.0; 5—d=5.0
- Fig.3 Multifunctional testing device for rock: 1—Machine frame; 2—Axial loading oil cylinder; 3—Horizontal loading oil cylinder; 4—Impacting bar; 5—Lifting crossbeam; 6—Cutter and nipper; 7—Electric motor for adjusting impacting velocity; 8—Gear transmission device; 9—Gear wheel driving mech- anism; 10—Sample carrier; 11—Rock sample; 12—Track
J. Cent. South Univ. Technol. (2008) 15: 112-116
DOI: 10.1007/s11771-008-0022-y
Failure analysis of polycrystalline diamond compact cutters for breaking rock by bending waves theory
GONG Sheng-wu(龚声武)1, ZHAO Fu-jun(赵伏军)2
(1. School of Resources and Safety Engineering, Central South University, Changsha 410083, China;
2. School of Energy and Safety Engineering, Hunan University of Science and Technology, Xiangtan 411201, China)
Abstract:
The breakage mechanism of the polycrystalline diamond compact(PDC) cutters was analyzed by the energy theory of bending waves. The cutting tests of granite block were conducted on a multifunctional testing device by using the cutter at three kinds of negative fore angles of 30?, 45? and 60?. The results show that, when the edge of the PDC layer is broken, the layer of tungsten cobalt is broken a little under the angle of 30?, while the layer of tungsten cobalt is broken continuously under the angle of 60?, their maximum depths are about 2 and 7 mm respectively in the two cases. The eccentric distance mainly depends on the negative fore angle of the cutter. When the cutter thrusts into the rock under an attack angle of 60?, the energy of bending waves reaches the maximum since the eccentric distance is the maximum. So the damage of cutter is the most serious. This test result is consistent with the conclusion of theoretical analysis well. The eccentric distance from the axial line of cutter to the point of action between the rock and cutter has great effect on the breakage of the cutter. Thus during the process of cutting, the eccentric distance should be reduced to improve the service life of PDC cutters.
Key words:
polycrystalline diamond compact; failure analysis; breaking test; energy theory of bending waves;
1 Introduction
The breakage of cutters has been studied widely for a long time and many kinds of damage and breakage mechanism models have been put forward[1-3]. These models have their own characteristics and ranges of application. Most of them have been carried out according to the characteristics of material of the cutters and by analogy with the types of breakage of other cutters with different materials or by indentation test on rock. The results from these methods can only show the breakage situation of cutters partly and cannot show the whole breakage process when the cutter cuts into the rock. At the same time, they are mainly limited to breakage mode under cutting by static pressure. Polycrystalline diamond compact (PDC) cutters have been widely used in all kinds of engineering due to their high rigidity, good wear resistance and anti-impact of carbide. But they are rarely used in cutting hard rock. So the theory and its application of cutting process of hard rock with PDC cutters are lack of full research, especially the study on the cutting hard rock with impact loads is hardly ever covered[4-7]. With the development of the cutter technology on drilling rock, the researchers focused on drilling hard rock with PDC[8-11]. Because the PDC cutters have been used in drilling hard rock recently, there have been few papers on its breakage mechanism. Thus, the study on the breakage mechanism of cutters when the cutters cut into the rock is of theoretic and practical significance for fully using the new type material and good designed performance cutters reasonably and improving their service lives. In this work, the breakage mechanism of PDC cutters was analyzed by using the energy theory of bending waves.
2 Failure analysis of cutters by energy theory of bending waves
The critical value of bending strength of PDC cutters is only about one tenth of that of compressive strength[8-9]. When loads applied along the axial line of the cutter increase, the bending stress of cutting blade reaches the critical value more quickly than that of the compressive stress. Thus the breakage of the cutter is mainly determined by the bending stress. At the same time, it is known that the cutting force is an impact harmonic wave according to the results of test. So the bending breakage of the cutter can be analyzed and calculated by the energy theory of bending waves[9-10]. The calculating model is shown in Fig.1, in which y(x, t) is the displacement of the axis of the cutter along the cross section, u(x, t) is the axial displacement of the center of the cutter, W(x, t) is the axial displacement of the blade of the cutter, b is the eccentric distance from the axial line of cutter to the point of action between the rock and cutter(it means ideal load when b equals 0).
Fig.1 Calculating model of energy of bending waves
Using a viscous damper to represent the rock, the force (F) is in proportion to the axial displacement of the cutter blade (W), that is
(1)
where m is the mass of the cutter, and d is the damping constant determined by the contact area of rock and cutter. d>1 means faintish counterforce, d<1 means strong counterforce, and d=1 means fixed end.
Assuming that the cutter bend obeys to Euler-Bernoulli equation, then there exists
(2)
where c is the velocity of longitudinal wave, and r is the radius of gyration of the circle cross section, the change of the point of blade can be calculated by the following four equations.
(3)
Eqn.(3) shows the relationship between the velocity and stress of particles. Among them, σi is stress of incident wave, and σr is stress of reflected wave.
(4)
Eqn.(4) shows the balance of the force. Among them, A is the contact section of the cutter and the rock.
(5)
Eqn.(5) shows the balance of the moment.
(6)
Eqn.(6) shows the geometry conditions.
Eliminating and
from the four equations mentioned above, the following equations can be obtained.
(7)
(8)
where
and
.
The energy of bending waves of the cutter can be considered as the integral of the moment of the cutter end multiplying the cutting velocity on the whole time:
(9)
Eqn.(9) can be rewritten as
(10)
Given, the relationship between the energy of incident stress waves (
) and the ratio(K) of the energy of bending waves to that of incident stress waves is
(11)
Eqn.(11) means that the energy of bending waves equals the incident energy minus the sum of reflected energy and the transmission energy.
Assuming stress waves are exponential waves, then we have
,
and
(12)
where and
, g is the
parameter of the boundary conditions of the blade. g =1 means that the cutter is fixed along the cross section, whereas g =0.5 means that the cutter is free along the cross section, D is the diameter of the cutter, L is the outstretched length of the cutter. Then the energy of bending waves can be shortened as
(13)
Fig.2 shows the relation between K and P when d changes.
Fig.2 Proportion curves of bending energy: 1—d=0; 2—d=0.5; 3—d=1.0; 4—d=2.0; 5—d=5.0
During the practical cutting process, the eccentric distance (b) is varied. When the rock and cutter start to contact, b is small. When the depth of cutting increases, the point of action will depart from the axial line of the cutter, b increases. Then parameter P will decrease as four times power function. Thus K increases and the energy of bending waves increases obviously. So the breakage of the cutter will be more serious.
3 Test and results analysis
3.1 Appratus
Appratus (shown in Fig.3) mainly consists the hydraulic pump pressure system for loading the axial static pressure (shown as 2 and 5 in Fig.3), the device for loading impact loads (shown as 4, 7 and 9 in Fig.3), and the pump pressure system for horizontal cutting[12-16].
Fig.3 Multifunctional testing device for rock: 1—Machine frame; 2—Axial loading oil cylinder; 3—Horizontal loading oil cylinder; 4—Impacting bar; 5—Lifting crossbeam; 6—Cutter and nipper; 7—Electric motor for adjusting impacting velocity; 8—Gear transmission device; 9—Gear wheel driving mech- anism; 10—Sample carrier; 11—Rock sample; 12—Track
3.2 Methods of test
During test, put the cutter on the surface of the sample and apply the vertical static loading, impact loading and horizontal cutting force respectively by the loading equipment. If the vertical static loading is small and only the blade can keep close to the sample surface, then the sample can only be acted under the vertical impact loading and horizontal cutting force. This situation belongs to the fragmentation mode by impact and cutting. If the vertical static loading cannot be ignored, this situation belongs to the mode of cutting under impact and static pressure. If the horizontal cutting force is so small that the cutter can only put forward brokenly and has no practical effect on the fragmentation of the rock, this situation belongs to the mode of crashing by impact and static pressure. If the impact load or the static pressure equals 0, this situation belongs to the mode of crashing by impact loading or cutting by static pressure.
The sample of test is granite made in Dingziwang. The parameters of physical mechanics of the samples are shown in Table 1. The cutter with diameter of 13.4 mm, is made in Hunan Feidie Carbide Alloy Factory and is made of 1 mm-thick wafer-like PDC and 3 mm-thick tungalloy. In order to study the effect of the angle of the blade on the stress and the breakage of the cutter, the PDC cutters with three kinds of angles, were tested, which are -30?, -45? and -60?, respectively. Before test, the surface of samples should be planished and polished with grinding wheel machine and then the tests of cutting under static pressure and under impact and static pressure could be carried out respectively.
Table 1 Mechanical parameters of granite
3.3 Test results and analysis
The tests of cutting under static pressure and under impact and static pressure were conducted with PDC cutters on the granite respectively. The situation of the breakage of the cutters is shown in Table 2.
When the PDC cutters cut into the hard and brittle granite as the mode of cutting under static pressure or impact and static pressure, these cutters with three negative fore angles all are broken to different degrees, and the larger the negative fore angle, the more serious the breakage of PDC cutter. Both the layer of PDC and the layer of tungsten cobalt are broken. The maximum broken depths of the three kinds of cutters at the negative fore angles of 30?, 45? and 60? are 2, 4 and 7 mm, respectively. The main reason is that the larger the negative fore angle, the longer the eccentric distance of the action point of force, so the energy of the bending energy is more. If the cutting depth reaches 1 mm, the eccentric distances from the axial line to the action point between the rock and the three kinds of cutters at the negative fore angles of 30?, 45? and 60? are 0.288, 0.500 and 0.866 mm, respectively. When b increases, the energy of bending waves of cutter increases. Thus the breakage of the cutter is more serious. In the test, the cutter that cuts into the rock at 60? is broken most seriously since its eccentric distance is the largest, which is consistent with the conclusion of theoretical analysis.
Table 2 Situation of breakage of cutters
Whether with PDC cutter or hard carbide cutter when positive fore angle of the cutter is used, rock volume of compacting core formed by the tip of the cutter is small and does not change with the variation of the fore angle. Furthermore, the cutter has the advantages of small cutting force and fast cutting speed. However, cutters with positive fore angle are not good to transfer the impact stress waves, because the interface of the impact force mainly occurs in the area of cutter’s relief angle under impact loading, so the cutter is easy to be damaged as well as difficult to obtain better breaking effect. Therefore, positive fore angle cutters are mainly suitable for soft and uniform materials, while negative fore angle is mainly suitable for hard and middle hard rock. So the negative fore angle cutter is used in the test for the impact-cutting test of hard rock sample. With the increase of negative fore angle of the cutter, the interface area between the rock and the tip of cutter is larger so as to form more powder chips and a larger volume of fragmentation at the same cutting depth. So the larger the negative fore angle, the larger the volume of fragmentation. But the damage expends faster with the fast increase of cutting negative fore angles[17-18].
4 Conclusions
1) The discontinuous breakage of edge of the PDC cutter is mainly determined by the eccentric distance from axial line to action point between the rock and the cutter. When b increases, the energy of the bending wave increases, thus the breakage of the cutter is more serious. At the same time, the value of b is determined by the negative former angle of the cutter. When the negative fore angle equals -60?, the eccentric distance is the largest, so the breakage of the cutter is the most serious.
2) On the multifunctional testing device, the cutting tests under the static pressure and impact are conducted. The results show that the PDC cutters with three negative fore angles are broken with different degrees. The test results are consistent with the conclusion of theoretical analysis.
3) In the practical engineering, in order to reduce the breakage of the cutters, improve the effect of rock fragmentation and prolong the service life, the eccentric distance from the axial line to the point of action between the rock and the cutter should be reduced to the greatest extent and make the cutter cut into the rock at small negative fore angle.
References
[1] LI Xiao-hong. A experimental study of wear and brittle fracture to PDC bits[J]. Quarterly of the Changsha Institute of Mining Research, 1991, 11(1): 58-64. (in Chinese)
[2] ZOU De-yong, WANG Rui-he. Experimental study on the abrasive property of PDC bits on rock[J]. Journal of the University of Petroleum, China, 2003, 27(2): 41-43. (in Chinese)
[3] SCHLUMBERGER J G. New PDC bit cutters improve wear life and ROP[J]. Drilling Contractor, 2002,1: 55-56.
[4] LI Yu-he, ZHANG Hong-tao. Research on the negative cutting force when cutting hard and brittle materials using PDC tool[J]. Diamond and Abrasives Engineering, 2000, 15(1): 20-22. (in Chinese)
[5] ZHOU Ze-hua, ZHENG Han-qing, ZENG Zhi-xin, YANG Xiao-bin. The cutting mechanism, cutting model and cutting process of the glass[J]. Chinese Journal of Mechanical Engineering, 1993, 29(2): 15-18. (in Chinese)
[6] Jr MISHNAEVSKY L L. A brief review of Soviet theoretical approaches to dynamic rock failure[J]. Int J Rock Mech Min Sci Geomech Abstr, 1993, 30(6): 663-668.
[7] LINDQVIST P A. Rock fragmentation by indentation and disc cutting: Some theoretical and experimental studies[D]. Sweden: University of LULEA, 1982: 1-13.
[8] LI Xiao-hong. Study on the PDC cutters cutting the hard and very hard rock assisted by water jets[D]. Chongqing: Chongqing University, 1992. (in Chinese)
[9] ZHAO Tong-wu. Percussion drilling dynamics[M]. Beijing: Metallurgical Industry Press, 1996. (in Chinese)
[10] ZHAO Fu-jun. Theoretical and experimental research on rock fragmentation under coupling dynamic and static loads[D]. Changsha: Central South University, 2004. (in Chinese)
[11] LI Xi-bing, ZHAO Fu-jun, SUMMERS D A, RUPERT G. Cutting capacity of PDC cutters in very hard rock[J]. Transactions of Nonferrous Metals Society of China, 2002, 12(2): 305-310.
[12] LI Xi-bing, ZHAO Fu-jun, SUMMERS D A. Failure modes of PDC cutters under different loads[J]. Transactions of Nonferrous Metals Society of China, 2002, 12(3): 504-507.
[13] LI Xi-bing, ZHAO Fu-jun. Multifunctional testing device for rock fragmentation by combining cut with impact[J]. Tunnlling and Underground Space Technology, 2004, 19(4/5): 526-528.
[14] LI Xi-bing, SUMMERS D A, RUPERT T, TYLER J. Experimental investigation on the breakage of hard rock by PDC cutters with combined action modes[J]. Tunnlling and Underground Space Technology, 2001, 16(2): 107-115.
[15] ZUO Yu-jun, LI Xi-bing, ZHOU Zi-long, MA Chun-de, ZHANG Yi-ping, WANG Wei-hua. Damage and failure rule of rock undergoing uniaxial compressive load and dynamic load[J]. Journal of Central South University of Technology, 2005, 12(6): 742-748.
[16] LI Xi-bing, ZUO Yu-jun, WANG Wei-hua, MA Chun-de, ZHOU Zi-long. Constitutive model of rock under static-dynamic coupling loading and experimental investigation[J]. Transactions of Nonferrous Metals Society of China, 2006, 16(3): 714-722.
[17] YANG Xiao-li, WANG Zhi-bin, ZOU Jin-feng, LI Liang. Bearing capacity of foundation on slope determined by energy dissipation method and model experiments[J]. Journal of Central South University of Technology, 2007, 14(1): 125-128.
[18] YANG Xiao-li, GUO Nai-zheng, ZHAO Lian-heng, ZOU Jin-feng. Influences of nonassociated flow rules on seismic bearing capacity factors of strip footing on soil slope by energy dissipation method[J]. Journal of Central South University of Technology, 2007, 14(6): 842-847.
(Edited by CHEN Wei-ping)
Foundation item: Project(06JJ20094) supported by the Natural Science Foundation of Hunan Province, China
Received date: 2007-07-21; Accepted date: 2007-09-29
Corresponding author: GONG Sheng-wu, Doctoral candidate; Tel: +86-13974954369; E-mail: gsw650202@163.com
- Failure analysis of polycrystalline diamond compact cutters forbreaking rock by bending waves theory
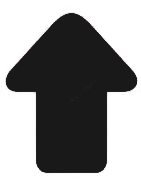