- Abstract:
- 1 Introduction▲
- 2 Experimental▲
- 3 Results and discussion▲
- References
- Figure
- Fig.1 Effect of particle size on nickel extraction efficiency
- Fig.2 Effect of stirring speed on nickel extraction efficiency
- Fig.3 Effect of sulfuric acid concentration on nickel extraction efficiency
- Fig.4 Effect of temperature on nickel extraction efficiency
- Fig.5 Plots of 1-(1-x)1/3 vs time at various temperatures
- Fig.6 Plots of 1-2/3x-(1-x)2/3 vs time at various temperatures
- Fig.7 Arrhenius plot for leaching nickel from Ni-Co concentrate
J. Cent. South Univ. Technol. (2009) 16: 0410-0415
DOI: 10.1007/s11771-009-0069-4
Kinetics of nickel leaching from roasting-dissolving residue of
spent catalyst with sulfuric acid
FENG Qi-ming(冯其明), SHAO Yan-hai(邵延海), OU Le-ming(欧乐明),
ZHANG Guo-fan(张国范), LU Yi-ping(卢毅屏)
(School of Resources Processing and Bioengineering, Central South University, Changsha 410083, China)
Abstract:
Sulfuric acid leaching process was applied to extract nickel from roasting-dissolving residue of a spent catalyst, the effect of different parameters on nickel extraction was investigated by leaching experiments, and the leaching kinetics of nickel was analyzed. The experimental results indicate that the effects of particle size and sulfuric acid concentration on the nickel extraction are remarkable; the effect of reaction temperature is mild; while the effect of stirring speed in the range of 400-1 200 r/min is negligible. Decreasing particle size or increasing sulfuric acid concentration and reaction temperature, the nickel extraction efficiency is improved. 93.5% of nickel in residue is extracted under suitable leaching conditions, including particle size (0.074-0.100) mm, sulfuric acid concentration 30% (mass fraction), temperature 80 ℃, reaction time 180 min, mass ratio of liquid to solid 10 and stirring speed 800 r/min. The leaching kinetics analyses shows that the reaction rate of leaching process is controlled by diffusion through the product layer, and the calculated activation energy of 15.8 kJ/mol is characteristic for a diffusion controlled process.
Key words:
kinetics; leaching; nickel; sulfuric acid; spent catalyst;
1 Introduction
Nickel has strategic and industrial importance due to its extensive application in producing stainless steel, alloy, battery, and catalyst [1–2]. Recently, relatively great attention has been paid to the research on the recovery of nickel from secondary resources including spent catalyst [3-5], waste battery [6-8] and tailings [9].
The traditional method to reclaim nickel from spent catalyst is acid leaching. Al-Mansi and ABDEL MONEM [10], SAHU et al [11] and CHEN et al [12] reported their studies on the extraction of nickel from spent catalyst by sulfuric acid leaching, and 98%-99% of nickel in spent catalyst was recovered. Hydrochloric acid leaching process to extract nickel from spent catalyst was studied by Chaudhary et al [13] and MA et al [14], but nickel recovery (73%-98%) was lower as compared with that of sulfuric acid leaching. Besides acid, sodium nitrate [15] and bacteria [16] were also used to leach nickel from spent catalyst. There are many reports on the extraction of nickel from spent catalyst using different reagents, however, the kinetics of leaching has not been sufficiently studied yet.
Mulak et al [17] studied the leaching kinetics of spent nickel oxide catalyst in sulfuric acid solution. The results indicated that the reaction was controlled by
diffusion through the catalyst network with the activation energy of 15.7-17.5 kJ/mol. However, Abdel-Aal and Rashad [18] suggested that the sulfuric acid leaching of a spent nickel oxide catalyst was controlled by chemical reaction on the surface of particles, and the activation energy was calculated to be 41.1 kJ/mol.
This work is the continuation of our previous work [19]. The material used in this work was the roasting- dissolving residue (Ni-Co concentrate) of a spent Al2O3-based catalyst. Sulfuric acid leaching was applied to extract nickel and cobalt from Ni-Co concentrate. The leaching conditions and kinetics aspects on nickel were also studied.
2 Experimental
2.1 Materials
A spent catalyst, bearing multiple valuable metals like Ni, Co, V, Mo and Al, was obtained from the hrdrodesulfurization units of China National Petroleum Corporation. The X-ray diffraction result shows that the existing form of valuable elements among the spent catalyst is very complicated. The main form of aluminum in catalyst is α-Al2O3, while silicon occurs in some kind of zeolite (C4H6Al6Na8O28Si6) and SiO2. Besides NiAl2O4, NiO and NiS are also found. Due to the special existing form of nickel, it is difficult to extract nickel directly from spent catalyst by conventional acid leaching.
According to Ref.[19], the catalyst was treated by the following steps: mixing spent catalyst with alkali at a certain proportion, then roasting the mixture at 750 ℃ for 30 min followed by dissolving in hot water. After filtration, alumina, vanadium and molybdenum were converted into alkali solution, but nickel and cobalt were enriched in dissolving residue (Ni-Co concentrate). The main chemical compositions of spent catalyst and Ni-Co concentrate are listed in Table 1. By roasting-dissolving extraction, nickel and cobalt were separated from alumina, vanadium and molybdenum. Moreover, the conversion of nickel and cobalt to oxides and the dissolving of alumina are very significant for the Ni-Co concentrate leaching with sulfuric acid. Sulfuric acid used in this study is analytical grade with a concentration of 96% (mass fraction) and a density of 1.84 kg/L. It was diluted to different concentrations during the leaching experiment.
Table 1 Main chemical compositions of materials (mass fraction/%)
2.2 Methods
The Ni-Co concentrate was leached in a glass beaker (500 mL) heated in a water bath, and the temperature control accuracy was (±1)℃. In each experiment, 30 g Ni-Co concentrate was added to the agitated sulfuric acid solution (300 mL) of a certain concentration at a required temperature. A mechanical glass agitator with stirring speed varied from 0 to 1 500 r/min was applied to agitate the reaction content. In the whole study, the mass ratio of liquid to solid was maintained constant as 10. At selected time intervals, 2 mL leach liquor was sampled for the determination of nickel and cobalt concentrations by ICP-AES method, and the nickel extraction efficiency was calculated complexometrically.
3 Results and discussion
Main reactions between Ni-Co concentrate and sulfuric acid can be written as follows:
NiO(s)+H2SO4(aq.)→NiSO4(aq.)+H2O(l) (1)
CoO(s)+H2SO4(aq.)→CoSO4(aq.)+H2O(l) (2)
Based on the above reactions, the effects of particles size, stirring speed, sulfuric acid concentration and temperature were evaluated in the following sections.
3.1 Effect of particle size
Particle size is a dominating factor influencing the leaching effect. For this study, three different size fractions of Ni-Co concentrate were prepared: (0.100-0.200), (0.074-0.100) and (0.043-0.074) mm. The initial sulfuric acid concentration and leaching temperature were kept constant as 30% (mass fraction) and 60 ℃, respectively, and the stirring speed was fixed at 800 r/min. The effect of particle size on the nickel extraction efficiency is illustrated in Fig.1. It can be found from Fig.1 that the particle size has a significant effect on dissolution of nickel. The nickel extraction efficiencies for (0.074-0.100) and (0.100-0.200) mm particle size reach 51.7% and 85.5% after 180 min leaching, respectively.
Fig.1 Effect of particle size on nickel extraction efficiency
By decreasing the particle size, the contact area of Ni-Co concentrate particle with fluid increases, and the reaction rate increases [20]. Therefore, under the same leaching conditions, nickel extraction efficiencies of (0.043-0.074) and (0.074-0.100) mm particle size are nearly equivalent but greatly higher than that of (0.100-0.200) mm particle size. The (0.043-0.074) mm particle size has the best dissolution of nickel, but the filtration of leaching residue is rather difficult. Hence, the particle size of (0.074-0.100) mm is beneficial to the leaching process.
3.2 Effect of stirring speed
Most leaching processes involved fine particles require agitation to suspend solid particles and provide efficient mixing for the leaching content. Using 30% (mass fraction) sulfuric acid to leach Ni-Co concentrate of (0.074-0.100) mm particle size at 60 ℃, the effect of stirring speed in the range of 400-1 200 r/min was studied. As seen from Fig.2, the stirring speed shows a negligible effect on the dissolution of nickel. When the leaching time is 180 min, the nickel extraction efficiency with stirring speed of 1 200 r/min is only 1.7% higher than that with stirring speed of 400 r/min.
Fig.2 Effect of stirring speed on nickel extraction efficiency
In the study on a spent nickel oxide catalyst leaching with sulfuric acid, Mulak et al [17] also observed similar behavior of stirring speed on the leaching kinetics. This indicates that the external diffusion of H2SO4 and NiSO4 between the fluid and the surface of particles is fast, and hence does not control the dissolution of nickel within the investigated range of stirring speed. All subsequent experiments were carried out at a stirring speed of 800 r/min in order to assure the invariance of this parameter.
3.3 Effect of sulfuric acid concentration
The effect of sulfuric acid concentration on the nickel extraction efficiency was studied at 60 ℃ and a stirring speed of 800 r/min and a mass ratio of liquid to solid of 10 for Ni-Co concentrate of (0.074-0.100) mm particle size, acid concentration was varied in the range of 10%-40% (mass fraction). As shown in Fig.3, the
Fig.3 Effect of sulfuric acid concentration on nickel extraction efficiency
nickel extraction efficiency increases with increasing the sulfuric acid concentration. For 10% concentration, there is virtually an acid deficiency effect. Nevertheless, there is no beneficial effect of increasing acid concentration more than 30%. However, after elapsing a certain time, namely, 180 min, the nickel extraction efficiency practically remains constant. This behavior may be explained by the fact that as the acid concentration in the medium increases, the apparent rate of solid product (CaSO4) increases, and the internal diffusion resistance of H2SO4 and NiSO4 through the product layer is enhanced. Consequently, the dissolution process slows down.
The nickel extraction efficiencies after 180 min leaching with 20%, 30% and 40% sulfuric acid are found to be 62.7%, 85.5% and 85.8%, respectively.
3.4 Effect of leaching temperature
The effect of leaching temperature was examined in the range of 40-80 ℃ under the conditions of sulfuric acid concentration of 30% (mass fraction), particle size of (0.074-0.100) mm, stirring speed of 800 r/min and mass ratio of liquid to solid of 10. The obtained results are plotted in Fig.4. It is suggested that leaching temperature only mildly affects the nickel extraction efficiency, which indicates that the dissolution process of nickel does not seem to be controlled by chemical reaction. As temperature increases from 40 to 80 ℃, the nickel extraction efficiency after 180 min leaching improves from 75.0% to 93.5%. In order to extract more than 90% of nickel in Ni-Co concentrate, a leaching temperature above 80 ℃ is necessary.
Fig.4 Effect of temperature on nickel extraction efficiency
3.5 Leaching kinetics analysis
Fluid-solid heterogeneous reaction systems have applications in hydrometallurgical and chemical processes. A successful reactor design for these processes depends basically on kinetic data. In the fluid-solid systems, the reaction rate may be generally controlled by one of the following steps [21]: diffusion through the fluid film, diffusion through the ash/product layer and the chemical reaction on the surface of the particle or unreacted core. The rate of the process is controlled by the slowest of these sequential steps.
If ash/solid product layer covers the unreacted core, as the reaction proceeds, there could be only two controlling steps, namely, diffusion through the product layer or chemical reaction on the surface. For reaction without ash/solid product layer, diffusion through fluid film or chemical reaction on the surface may control the reaction rate.
In order to determine the kinetic parameters and rate controlling step for leaching nickel from Ni-Co concentrate in sulfuric acid solution, the experimental data presented in Fig.4 were analyzed on the basis of the shrinking core model [22].
3.5.1 Controlling models for reaction rate
(1) Rate control by chemical reaction on surface of unreacted core
If the reaction is controlled by the surface reaction, the shrinking core model for the reaction is as follows:
(3)
where kc is the apparent rate constant for reaction controlled process (min-1), t is the reaction time (min), b is the stoichiometric coefficient of nickel in leaching reaction (dimensionless), M is the molar mass of nickel (kg/mol), ks is the chemical reaction rate constant (m/min), c(H2SO4) is the concentration of H2SO4 (mol/m3), ρ is the density of Ni-Co concentrate (kg/m3), r0 is the initial particle radius of Ni-Co concentrate (m), n is the reaction order, and x is the reacted fraction of nickel:
x=y/100 (4)
where y is the nickel extraction efficiency.
According to the experimental data in Fig.4 and Eqns.(3) and (4), plots of 1-(1-x)1/3 vs time t are depicted in Fig.5. It can be found that the data derived from Eqn.(3) cannot be correlated by this model, as there are neither straight lines nor zero point intercepts.
(2) Rate control by diffusion through product layer
If the reaction is controlled by diffusion through the product layer, Eqn.(3) transforms to the following equation [13, 20]:
(5)
where kp is the apparent rate constant for product diffusion controlled process (min-1), Deff is the diffusion coefficient of nickel ions in porous medium (m2/min).
Again, according to the experimental data in Fig.4 and Eqn.(5), plots of 1-2/3x-(1-x)2/3 vs time t are depicted in Fig.6. Obviously, the results reveal that the correlation coefficients (R2) in Fig.6 are closer to 1 than those in Fig.5. So, Eqn.(5) is found to fit the data better. Such results indicate that the linear relationship between 1-2/3x-(1-x)2/3 and leaching time t is significant and that the leaching process of nickel is controlled by diffusion through the product layer.
Fig.5 Plots of 1-(1-x)1/3 vs time at various temperatures
Fig.6 Plots of 1-2/3x-(1-x)2/3 vs time at various temperatures
3.5.2 Calculation of activation energy
The activation energy of a diffusion controlled process is characterized as 4-13 kJ/mol [23], 8-21 kJ/mol [24] or 13-25 kJ/mol [25]. While for chemical reaction controlled process, it is usually greater than 40 kJ/mol [18]. In order to calculate the activation energy, the plot of lnkp against 1/T should be a straight line with a slope of -E/R and an intercept of lnk, according to Arrhenius equation:
ln kp=ln k-E/(RT) (6)
The apparent rate constants (kp) were calculated as slopes of the straight lines in Fig.6. lnkp against 1/T is plotted in Fig.7. The activation energy of the overall reaction is calculated as 15.8 kJ/mol. The magnitude of
Fig.7 Arrhenius plot for leaching nickel from Ni-Co concentrate
this activation energy clearly confirms that the leaching of nickel from Ni-Co concentrate in sulfuric acid solution is most likely controlled by diffusion of ions through the product layer. Furthermore, this activation energy is in consistent with that (15.7 kJ/mol) calculated for nickel leaching from spent catalyst in sulfuric acid solution [17], that (13.4 kJ/mol) calculated for sulphuric acid leaching of low grade zinc silicate ore [23] and that (18.4 kJ/mol) calculated for vanadium leaching from spent sulphuric acid catalysts by sulphuric acid solution [25].
3.6 Recovery of nickel and cobalt
According to the experimental results presented in Figs.1-4, the suitable leaching conditions are as follows: sulfuric acid concentration 30% (mass fraction), particle size (0.074-0.100) mm, reaction temperature 80 ℃, reaction time 180 min, mass ratio of liquid to solid 10 and stirring speed 800 r/min. On the other hand, cobalt is leached along with nickel. Based on determination and calculation, 93.5% of nickel and 94.2% of cobalt in Ni-Co concentrate can be extracted under the above conditions. The study on separating nickel and cobalt in acidic solution is not discussed here because it is a successful process [26-27].
4 Conclusions(1) In the sulfuric acid leaching of Ni-Co concentrate, the effects of particle size and sulfuric acid concentration on the nickel extraction efficiency are remarkable; the effect of reaction temperature is mild; while the effect of stirring speed in the range of 400-1 200 r/min is negligible. Extraction efficiency of nickel is improved by decreasing particle size or increasing sulfuric acid concentration and reaction temperature.
(2) 93.5% of nickel and 94.2% of cobalt in Ni-Co concentrate can be extracted under suitable experimental conditions, including sulfuric acid concentration 30% (mass fraction), particle size (0.074-0.100) mm, reaction temperature 80 ℃, reaction time 180 min, mass ratio of liquid to solid 10 and stirring speed 800 r/min.
(3) Leaching kinetics analysis of nickel by different models indicates that the rate of nickel leaching process is controlled by diffusion through the product layer. The activation energy is calculated as 15.8 kJ/mol, which is consistent with that reported for diffusion controlled processes.
References
[1] Jiang Yuan, HOU Meng-xi. The study of global nickel supply and demand [J]. Non-ferrous Mining and Metallurgy, 2008, 24(2): 55-57. (in Chinese)
[2] Hanson D J. Nickel [J]. Chemical and Engineering News, 2003, 81(36): 82.
[3] MARAFI M, STANISLAUS A. Spent hydroprocessing catalyst management: A review. Part II. Advances in metal recovery and safe disposal methods [J]. Resources, Conservation and Recycling, 2008, 53(1/2): 1-26.
[4] VALVERDE J I M, PAULINO J F, AFONSO J C. Hydrometallurgical route to recover molybdenum, nickel, cobalt and aluminum from spent hydrotreating catalysts in sulphuric acid medium [J]. Journal of Hazardous Materials, 2008, 160(2/3): 310-317.
[5] GHANEM R, FARAG H, ELTAWEEL Y, OSSMAN M E. Recovery of nickel from spent catalyst by single- and multi-stage leaching process [J]. International Journal of Environment and Waste Management, 2008, 2(6): 540-548.
[6] Carla L, Pasquali M. Electrolytic nickel recovery from lithium-ion batteries [J]. Minerals Engineering, 2003, 16(6): 537-542.
[7] Lupi C, Pasquali M, Dell'Era A. Nickel and cobalt recycling from lithium-ion batteries by electrochemical processes [J]. Waste Management, 2005, 25(2): 215-220.
[8] Tzanetakis N, Scott K. Recycling of nickel-metal hydride batteries. II: Electrochemical deposition of cobalt and nickel [J]. Journal of Chemical Technology and Biotechnology, 2004, 79(9): 927-934.
[9] Zhuang J M, Walsh T, Hobenshield E. Nickel recovery and stabilization of nickel waste tailings [J]. International Journal of Mining, Reclamation and Environment, 2006, 20(2): 127-141.
[10] Al-Mansi N M, Abdel Monem N M. Recovery of nickel oxide from spent catalyst [J]. Waste Management, 2002, 22(1): 85-90.
[11] SAHU K K, AQARWAL A, PANDEY B D. Nickel recovery from spent nickel catalyst [J]. Waste Management and Research, 2005, 23(2): 148-154.
[12] CHEN Yun, FENG Qi-ming, ZHANG Guo-fan, OU Le-ming, Lu Yi-ping. Study on the recycling of valuable metals in spent Al2O3-based catalyst [J]. Minerals and Metallurgical Processing, 2007, 24(1): 30-34.
[13] Chaudhary A J, Donaldson J D, Boddington S C, Grimes S M. Heavy metals in the environment. Part II: A hydrochloric acid leaching process for the recovery of nickel value from a spent catalyst [J]. Hydrometallurgy, 1993, 34(2): 137-150.
[14] MA Cheng-bin, WANG Shu-fang, YUAN Ying-bin. Study on the recovery of spent catalysts containing molybdenum, nickel, bismuth and cobalt [J]. China Molybdenum Industry, 2007, 31(5): 23-25. (in Chinese)
[15] Lai Y D, Liu J C. Leaching behaviors of Ni and V from spent catalyst [J]. Journal of Hazardous Materials, 1997, 53(2): 213-224.
[16] BOSIO V, VIERA M, DONATI E. Integrated bacterial process for the treatment of a spent nickel catalyst [J]. Journal of Hazardous Materials, 2008, 154(1/3): 804-810.
[17] Mulak W, Miazga B, Szymczycha A. Kinetics of nickel leaching from spent catalyst in sulphuric acid solution [J]. International Journal of Mineral Processing, 2005, 77(4): 231-235.
[18] Abdel-Aal E A, Rashad M M. Kinetic study on the leaching of spent nickel oxide catalyst with sulfuric acid [J]. Hydrometallurgy, 2004, 74(3): 189-194.
[19] FENG Qi-ming, CHEN Yun, SHAO Yan-hai, ZHANG Guo-fan, OU Le-ming, LU Yi-ping. New technique of comprehensive utilization of spent Al2O3-based catalyst [J]. Journal of Central South University of Technology, 2006, 13(2): 151-155.
[20] SOUZA A D, PINA P S, LIMA E V O, DA SILVA C A, LE?O V A. Kinetics of sulphuric acid leaching of a zinc silicate calcine[J]. Hydrometallurgy, 2007, 89(3/4): 337-345.
[21] DENG C H, FENG Q M, CHEN Y. Studies on the leaching kinetics of cobalt from spent catalyst with sulphuric acid [J]. Mineral Processing and Extractive Metallurgy, 2007, 116(3): 159-162.
[22] ZHU Bing-chen. Chemical reaction engineering [M]. Beijing: Chemical Industry Press, 1993: 353-357. (in Chinese)
[23] Abdel-Aal E A. Kinetics of sulfuric acid leaching of low-grade zinc silicate ore [J]. Hydrometallurgy, 2000, 55(3): 247-254.
[24] Anand S, Das S C, Das R P, Jena P K. Leaching of manganese nodules at elevated temperature and pressure in the presence of oxygen [J]. Hydrometallurgy, 1988, 20(2): 155-167.
[25] Lozano L J, Juan D. Leaching of vanadium from spent sulphuric acid catalysts [J]. Minerals Engineering, 2001, 14(5): 543-546.
[26] LUO L, WEI J H, WU G Y, TOYOHISA F, ATSUSHI S. Extraction studies of cobalt (II) and nickel (II) from chloride solution using PC88A [J]. Transactions of Nonferrous Metals Society of China, 2006, 16(3): 687-692.
[27] Tsakiridis P E, Agatzini S L. Process for the recovery of cobalt and nickel in the presence of magnesium and calcium from sulphate solutions by Versatic 10 and Cyanex 272[J]. Minerals Engineering, 2004, 17(4): 535-543.
(Edited by CHEN Wei-ping)
Foundation item: Project (50574101) supported by the National Natural Science Foundation of China; Project (2003UDBEA00C020) supported by the Collaborative Project of School and Province of Yunnan Province, China
Received date: 2008-09-12; Accepted date: 2008-11-20
Corresponding author: FENG Qi-ming, Professor, PhD; Tel: +86-731-8836817; E-mail: qmfeng@mail.csu.edu.cn
- Kinetics of nickel leaching from roasting-dissolving residue of spent catalyst with sulfuric acid
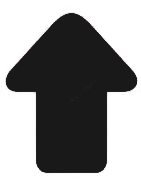