- Abstract:
- 1 Introduction▲
- 2 Experimental▲
- 3 Results and discussion▲
- 4 Conclusions▲
- References
- Figure
- Fig.1 FTIR spectra of PSDS geoopolymer with different mixture proportions
- Fig.2 XRD patterns of metakaolin and PSDS geopolymeric cement products
- Fig.3 ESEM micrograph of PSDS geopolymeric cement matrix
- Fig.4 27Al MAS-NMR spectrum of PSDS geopolymeric cement paste (Resonance is caused by spinning sideband effect)
- Fig.5 29Si MAS-NMR spectrum and deconvelution spectra of PSDS geopolymeric cement paste (Heavy line is experimental spectrum, and dotted lines are deconvelution spectra)
J. Cent. South Univ. Technol. (2009) 16: 0906-0913
DOI: 10.1007/s11771-009-0151-y
Preparation and microstructure characterization of
poly-sialate-disiloxo type of geopolymeric cement
ZHANG Yun-sheng(张云升)1, SUN Wei(孙 伟)1, LI Zong-jin(李宗津)2
(1. Jiangsu Key laboratory for Construction Materials, Southeast University, Nanjing 211189, China;
2. Department of Civil Engineering, The Hong Kong University of Science and Technology, Kowloon, China)
Abstract:
In order to investigate the influence of three key molar ratios (n(SiO2)/n(Al2O3), n(K2O)/n(Al2O3) and n(H2O)/n(K2O)), a total of nine potassium poly-sialate-disiloxo (K-PSDS) geopolymeric cement matrices were designed according to orthogonal design principle. Subsequently, XRD, ESEM-EDXA and MAS-NMR techniques were employed to further characterize the microstructure of the most fully reacted geopolymeric cement matrix. The experimental results show that n(K2O)/n(Al2O3) has the most significant effect on compressive strength amongst the three ratios. The highest compressive strength (20.1 MPa) can be achieved when n(SiO2)/n(Al2O3)=6.5, n(K2O)/n(Al2O3)=0.8 and n(H2O)/n(K2O)=10.0. The FTIR spectra of nine PSDS geopolymeric cement matrices also indicate that geopolymeric cement matrix with the highest strength is the most fully reacted one and possesses the largest amount of geopolymeric cement products. The microscopic analysis reveals that PSDS geopolymeric cement matrix possesses structural characteristics similar to gel substances in having a wide range of Si endowments, but predominantly the framework molecular chains of Si partially replaced by 4-coordinated Al tetrahedral.
Key words:
geopolymeric cement; poly-sialate-disiloxo; preparation; microstructure;
1 Introduction
A great development has been made in a new type of inorganic cementitious materials in recent years—geopolymeric cement around the world. Geopolymeric cement is one type of three dimensional CaO-free aluminosilicate gel binders, which was introduced into the inorganic cementitious world by DAVIDOVITS in the late 1970s[1]. Geopolymer can be synthesized by mixing aluminosilicate reactive materials with less or no CaO component (such as metakaolin) and strongly alkaline solutions (such as NaOH or KOH), and then curing at room temperature. In a strongly alkaline solution, aluminosilicate reactive materials are rapidly dissolved into solution to form free SiO4 and AlO4 tetrahedral units. With the development of reaction, mixing water is gradually split out and these SiO4 and AlO4 tetrahedral units are linked alternatively to yield three types of monolithic like geopolymer products: -SiO4-AlO4- (PS), -SiO4-AlO4-SiO4- (PSS), and -SiO4-AlO4-SiO4-SiO4- (PSDS) by sharing all oxygen atoms between two tetrahedral units[2]. Compared to Portland cement, geopolymer possesses low energy consumption[1-4], less CO2 emission[5-7], high early strength[8-9], less shrinkage[10-11], low permeability [12], good fire and acid resistance and good durability[13-15]. These merits make geopolymer exhibit promising potentials in the fields of civil, bridge, pavement, hydraulic, underground and militia engineering[16-22].
Compared to the PS and PSS types, PSDS geopolymeric cement shows some advantages over the other two types such as easy operation, high strength, strong bond to a concrete or steel substrate, good fire and high temperature resistance. The merits make PSDS geopolymeric cement have potentials for applications when temperature is high or fire is concerned, such as bridge, underground, tunnel and military engineering. The processing, intrinsic microstructure and properties of PSS geopolymeric cement have been investigated [23-25]. However, PSDS geopolymeric cement was not investigated systematically before. The microstructure of PSDS geopolymeric cement matrix is also not quantitatively characterized. All these seriously influence the commercial application of PSDS geopolyemric cement.
In this work, an almost fully-reacted potassium poly-sialate-disiloxo (K-PSDS) geopolymeric cement matrix was prepared at room temperature by optimizing the three key molar ratios: n(SiO2)/n(Al2O3), n(K2O)/ n(Al2O3) and n(H2O)/n(K2O). The compressive strength and microstructure as a function of the three ratios of the hardened geopolymeric cement matrices were evaluated. The influencing extent of each ratio on the compressive strength was quantitatively determined on basis of the variance analysis. The microstructural changes as a function of ratios were also investigated by using X-ray powder diffractometry (XRD) and Fourier transform infrared spectroscopy (FTIR) techniques. Based on the macroscopic and microscopic experiments, an almost fully-reacted K-PSDS geopolymeric cement matrix with the highest strength and optimum microstructure can be obtained by properly adjusting the three molar ratios. Subsequently, the coordination status of two main construction elements (Al and Si), micrographics and chemical compositions of K-PSDS geopolymeric cement matrix were further characterized and examined by using environment scanning electron microscope equipped with energy dispersion X-ray analysis (ESEM-EDXA), highly sensitive magic angle spinning-nuclear magnetic resonance spectroscopy (MAS-NMR) techniques.
2 Experimental
2.1 Materials
Metakaolin used as the most mainly aluminosilicate reactive raw materials in this work was obtained by calcining pure kaolin from China Kaolin Clay Company, Suzhou, China, at 700 ℃ for 12 h. The MAS-NMR resonance spectrum of calcined kaolin, i.e. metakaolin shows that about 95% of 6-fold coordinated Al in the origin kaolin is transformed into 4-fold coordinated one. The chemical compositions and physical properties of metakaolin are listed in Table 1. Analytical reagent KOH pellet and potassium silicate solution with n(SiO2)/ n(K2O) of 3.3 and the solid content of 40% were used as alkaline reagents. Silica fume with about 95% of SiO2 content was used as silicon additive to compensate the shortage of silicon in metakaolin. Distilled water was used throughout the experiment.
2.2 Methods
2.2.1 Specimen preparation for mechanical test
In this work, KOH, potassium silicate solution and water were firstly mixed in a beaker and cooled down to room temperature, and then metakaolin and silica fume powders were slowly added into the above pre-mixed alkaline solution and mixed for 3 min. After that, the fresh geopolymeric cement matrix was rapidly poured into cubic steel mould of 40 mm×40 mm×40 mm. All samples were vibrated for 2 min on the vibration table and set at room temperature. In order to prevent the evaporation of mixing water, the specimens were covered by plastic film during the setting and hardening process. The mould was removed after 24 h. The demoulded specimens were cured at 20 ℃ and 95% relative humidity (R.H) for 28 d. At least six specimens were made for each formula.
2.2.2 Compressive test
Compressive strength test was performed according ASTM C39-96. At least six samples of each formula were tested. The average value was served as the ultimate compressive strength. A closed-loop servo- hydraulically controlled materials testing machine (Sintech 10/D MTS 810) was used to conduct compressive test. The loading was displacement- controlled at a constant rate of 1.3 mm/min for all the compression tests.
2.2.3 Sample preparation for microanalysis
The fragments from different formulae were collected after compressive test. Some of them were used to conduct ESEM-EDXA analysis. The others were further finely crushed, and then immersed in ethanol for 3 d to stop the further geopolymerization reaction of geopolymeric cement, subsequently oven-dried at 60 ℃ for 6 h to remove the physically absorbed water. After that, these hardened geopolymeric cement paste fractions were further ground into very fine particles with agate mortar, and remove the coarse particles with the sieve of 80 μm in diameter. The fine powders were placed in desiccators for 24 h.
2.2.4 FTIR analysis
Fourier transform infrared spectroscopy (FTIR) analysis was performed on A Bio-Rad FTS 6000 FTIR by using KBr pellet techniques (3 mg of fine powders prepared previously were homogenously ground with 300 mg of KBr powder together until the mixture has the consistency of fine flour, and then pressed into a disk).
2.2.5 XRD analysis
/ the experimental arrangement. X-ray powder diffraction was recorded on a Philips PW1830 spectrometer with the following testing parameters: 40 kV, 30 mA, Cu Kα radiation. The XRD patterns were obtained at a scanning rate of 1 (?)/min from 10? to 80? (2θ) and steps of 0.05? (2θ). The wavelength was selected as 0.154 2 nm.
Table 1 Chemical compositions and physical properties of metakaolin
2.2.6 ESEM-EDXA analysis
XL30-ESEM equipped with EDXA was used to characterize the microstructure and chemical compositions of the fully reacted PSDS geopolymeric cement matrix. The following test parameters were employed in this work: accelerating voltage of 20 keV, pressure and relative humidity in sample chamber of 559.952 Pa and 80%, respectively.
2.2.7 MAS-NMR analysis
A JEOL NM-ESH40MU nuclear magnetic resonance spectroscopy (NMR) with the magic angle spinning technique was adopted. In this work, the spinning speed of the capsule was 4.8 kHz. 29Si and 27Al spectra were measured and recorded at NMR frequency of 79.3 and 72.18 MHz, respectively. The spectrometer was interfaced with a computer and equipped with a MAS broad-band probe for the solid state experiments. The peaks were fitted by Gaussian lines.
2.3 Experimental program
A fully-reacted potassium poly-sialate-disiloxo (K-PSDS) geopolymeric cement was synthesized. The main objective of the study was to investigate the effects of three factors: n(SiO2)/n(Al2O3) (factor A), n(K2O)/ n(Al2O3) (factor B) and n(H2O)/n(K2O) (factor C) on mechanical strength and microstructure. The three molar ratios were varied in the following ranges respectively: 5.5≤n(SiO2)/n(Al2O3)≤6.5, 0.8≤n(K2O)/n(Al2O3)≤1.2, and 7.0≤n(H2O)/n(K2O)≤10.0. The levels for each of the factors were set at three grades (low, intermediate, and high). Thus the experimental program here was three factors experiment with three levels for each factor. Based on the factor-level table, a total of nine experimental formulae were designed according to a L9(34) orthogonal design principle, as shown in Table 2. The interaction effect between different factors was not taken into account in the experimental arrangement.
3 Results and discussion
3.1 Preparation of fully-reacted PSDS geopolymeric cement matrix
The compressive strengths of nine different PSDS geopomymeric cement matrices are given in Table 2. The effects of the three molar ratios (n(SiO2)/n(Al2O3), n(K2O)/n(Al2O3) and n(H2O)/n(K2O)) were quantita- tively determined by using the gradation analysis and variance analysis. Subsequently, XRD and FTIR analysis of each geopolymeric cement formula was also conducted. On basis of the macroscale and microscale results, an almost fully-reacted PSDS geopolymeric cement matrix with the highest compressive strength and optimum microstructure can be obtained by properly selecting the three molar ratios.
3.1.1 Compressive test
In order to determine the influencing extent of the three molar ratios (n(SiO2)/n(Al2O3), n(K2O)/n(Al2O3) and n(H2O)/n(K2O)) and the optimum mixture proportion of PSDS geopolymeric cement matrix, the gradation analysis was first employed. The analysis was illustrated in tabular form in order that it can be clearly understood, as shown in Table 2. It can be seen from Table 2 that n(K2O)/n(Al2O3) exhibits the most significant influencing extent on the compressive strength of the harden geopolymeric cement matrices among the three molar ratios. The corresponding gradation range is 8.6. Comparatively, n(SiO2)/n(Al2O3) and n(H2O)/n(K2O) have relatively little influence on the compressive strength, whose gradation ranges are 2.4 and 4.1, respectively. Carefully comparing the difference
Table 2 Experimental program and compressive strength of PSDS geopolymeric cement matrices
among,
and
shows that the hardened geopolymeric cement matrix has the highest compressive strength at n(SiO2)/n(Al2O3)=6.5, n(K2O)/n(Al2O3)=0.8 and n(H2O)/n(K2O)=10.0.
The significance and influencing extent of the three molar ratios on compressive strength can be easily observed through the above simple gradation analysis. However, it is well known that the gradation analysis cannot quantitatively distinguish whether the compressive strength difference among different levels is caused by testing errors or by different levels in the case of the same factor. In order to solve the problem, variance analysis was employed in the following studies. Table 3 lists the variances analysis results of different factors involving in the synthesis of PSDS geopolymeric cement matrices.
Table 3 Variance analysis results of PSDS geopolymeric cement matrices
Note: “*” indicates significance at 10% level.
Careful observation of Table 3 shows that the sum of square of Serro is close to SC, and greater than SA. This means that the difference of experimental results between factors C and A is probably caused by the testing error, rather than by the factor’s difference. Therefore, the sum of square of factors A and C can sum up to error term, i.e. Scollect=(SA+SC+Serro). The observed mean square (SB) is to be tested against the error mean square (Scollect/6=11.26) with six degrees of freedom. The proper test statistic is the F statistic with two and six degrees of freedom. At the 10% significance level (α=0.1) the critical region of F is F≥4.98, which is usually taken as the upper tail of the F distribution, rejecting H0 if F≥F1-α, where α is the area above F1-α. A significant F indicates that the difference between factor B and testing error has something in it besides the estimate of variance. This probably implies that there is a real difference in the means, and H0 should be rejected.
Comparing each mean square with the error mean square (Scollect) indicates that factor B, i.e. n(K2O)/n(Al2O3) has a considerable impact on the compressive strength of the hardened geopolymeric cement matrix at α=0.1, while the effects of other factors such as n(SiO2)/n(Al2O3) and n(H2O)/n(K2O) are negligible. A comparison of the values of ,
and
for factor B shows that the compressive strength decreases with an increase in n(K2O)/n(Al2O3). The geopolymeric cement matrix with n(K2O)/n(Al2O3)= 0.8 has the highest compressive strength. Considering that there is little effect of the other two factors, n(SiO2)/n(Al2O3)=6.5 and n(H2O)/n(K2O)=10.0 are selected in order to reduce the amount of expensive KOH in this work. The optimum mixture proportion determined according to the variance analysis is consistent with that according to the gradation analysis. The conclusion induced by the variance analysis can be used as “feedback” to design a better experiment.
As a results, the optimum mixture of K-PSDS geopolymeric cement matrix is made on the basis of compressive strength with n(SiO2)/n(Al2O3)=6.5, n(K2O)/n(Al2O3)=0.8 and n(H2O)/n(K2O)=10.0, i.e. formula PSDS7.
3.1.2 FTIR analysis
The above mechanical test shows that the compressive strength of the hardened geopolymeric cement matrices made with different mixture proportions has a considerable difference. In order to elucidate in a microscopic scale the difference of the compressive strength for different formulae mentioned above (PSDS1 to PSDS9), FTIR technique was employed to characterize the microstructure of these hardened geopolymeric cement pastes.
The FTIR spectra of various geopolymeric cement matrices are presented in Fig.1. The chemical shifts of main FTIR bands and the corresponding species are determined based on Refs.[26-27]. By carefully comparing FTIR spectra, the following phenomena can be observed.
Fig.1 FTIR spectra of PSDS geoopolymer with different mixture proportions
(1) The strong band at 1 086 cm-1 in the FTIR spectrum of metakaolin shifts towards the low wavenumber after geopolymerization reaction of geopolymeric cement. The shift is approximately 78 cm-1. This demonstrates that an obvious change in the microstructures takes place during hydration reaction, resulting in a formation of new products with different microstructure from metakaolin. Similar results are also seen in the XRD patterns, as shown in Fig.2. According to Refs.[26-27], peak at 1 086 cm-1 is caused by stretching vibration of Si—O bond, while peak at 1 008 cm-1 is ascribed to asymmetrical vibration of Si—O bond. The large shift toward the low wavenumber may be attributed to the partial replacement of SiO4 tetrahedron by AlO4 tetrahedron, resulting in a change in the local chemical environment of Si—O bond. In addition, The band at 1 006 cm-1 is very strong, but a lack of sharp feature is a indicative of the general disorder in the Si(Al)—O— network, reflecting the wide distribution of the SiQn(mAl) unit in the polymeric molecular chains of geopolymeric cement products. SiQn(mAl) unit is the conventional notation used to describe the structural units in aluminosilicates, where “n” represents the degree of condensation of SiO4 tetrahedra. In this way, if n=0, 1, 2, 3 and 4, then silicon is respectively in isolated mono-group (SiQ0), in dislicates and chain end groups (SiQ1), in middle groups in chains (SiQ2), in sheet sites (SiQ3), and in three-dimensional cross-linked sites (SiQ4). “m” represents the number of aluminum atoms in the second coordination sphere of silicon. In general, if there is no aluminum atom in the second coordination sphere of silicon, the notation becomes SiQn(nSi). The stretching modes of the Si—O bonds of the SiQn units are FTIR-active in the 850-1 200 cm-1 region with the absorption bands of the SiQn unit with n=4, 3, 2, 1, 0 centered at around 1 200, 1 100, 950, 900 and 850 cm-1, respectively[28]. These values shift to lower wavenumbers when the degree of silicon substitution by aluminum in the second coordination sphere increases, as a consequence of the weaker Al—O bond.
(2) The intensities of the bands at 914 and 798 cm-1 in FTIR spectrum of metakaolin caused by 6-fold coordinated Al(VI)—OH stretching vibration and 6- coordinated Al(VI)—O stretching vibration, respectively, are considerably reduced or disappeared after geopolymerization reaction of geopolymeric cement. In addition, a similar trend is also found for the Si—O symmetrical stretching band at about 697 cm-1. This shows that 6-coordinated Al(VI) maybe changes into 4-corrdinated one, and participates in the framework structure of geopolymeric cement products during the process of hydration reaction.
(3) A weak band at around 840 cm-1 can be observed in some geopolymeric mixtures. The band cannot be found in the FTIR spectrum of metakaolin. The new band is assigned to the bending vibration of Si—OH. This can be caused by some bond breakage sites in the network structure of geopolymeric cement products for some geopolymeric cement mixtures. The existence of Si—OH will cause a decrease in the degree of condensation, thus a reduction in mechanical strength.
Based on the above analysis of FTIR spectra, we can conclude that during geopolymerizaiton reaction of geopolymeric cement, SiO4 and AlO4 tetrahedaron will be released from the surface of metakaolin particles under the attack of strongly alkaline solution. The Ⅵ coordinated Al introduced by the metakaolin will also be leached out in strongly alkaline solution, and the coordination state will transform from Ⅵ to Ⅳ. As the dissolution proceeds, more and more SiO4 and AlO4 tetrahedarons go into the alkaline solution. After undergoing structural reorientation to a certain extent, the SiO4 and AlO4 tetrahedarons will produce polycondensation reaction, thus a formation of geopolymeric cement products with a framework structure. It is the bonding of AlO4 (Ⅳ) with SiO4 that causes the great changes in the original Si—O chemical environment, resulting in different chemical shifts, reduction or disappearance of some characteristic bands in FTIR spectra. When the mixture proportion of geopolymeric cement matrix is not designed properly, incomplete poycondensation reaction will occur, thus resulting in some bond breakages in the framework structure. The breakage bonds will be saturated by —OH. As a result, the Si—OH bending band at 840 cm-1 will appear in some geopolymeric cement formulae such as PSDS1, PSDS2, PSDS3, and PSDS9. From Fig.1, it is clear that PSDS7 has a prominent band at 1 006 cm-1, which is the characteristic band of K-PSDS geopolymeric cement products. The Si—OH bending band at 840 cm-1 cannot be seen. Thus, it is reasonable to assume that PSDS7 is the optimum one among the nine formulae. The hydration degree of PSDS7 is the largest and the compressive strength is also the highest.
The above macroscopic and microscopic experimental results reveal that an almost fully-reacted PSDS geopolymeric cement matrix can be obtained when n(SiO2)/n(Al2O3)=6.5, n(K2O)/n(Al2O3)=0.8 and n(H2O)/n(K2O)=10.0, i.e. formula PSDS7. n(K2O)/ n(Al2O3) has a very important influence on strength gain and desirable microstructure of PSDS geopolymeric cement matrix. Comparatively, n(SiO2)/n(Al2O3) and n(H2O)/n(K2O) exhibit little impact. However, the potassium content is used to satisfy the charge-balance requirements within the structure, without proving that an excess can form potassium carbonate and may destroy the polycondensation process. The water content for a critical polycondensation reaction is less obvious. Whereas it is clearly necessary to provide sufficient water to facilitate initial mixing and act as a carrier for ionic transport. The excessive water maybe dilutes the polycondensation reaction or leaches more soluble components and transports them away from the reaction zone.
3.2 Microstructural characteristics of fully-reacted PSDS geopolymeric cement matrix
According to the above analysis, PSDS7 is almost fully-reacted PSDS geopolymeric cement matrix. In order to further characterize the microstructure of the geopolymeric cement matrix, XRD, ESEM-EDXA and MAS-NMR techniques were adopted for the PSDS7.
3.2.1 XRD analysis
It is seen from Fig.2 that there is a large diffuse halo peak at 20?-40? (2θmax, Cu Kα) in X-ray diffractogram of the fully-reacted PSDS geopolymeric cement matrix, i.e. formula PSDS2. This indicates that PSDS geopolymeric cement products are mainly X-ray amorphous materials. In addition, several sharp peaks (0.333, 0.198, 0.137 nm) are also seen from Fig.2. According to the XRD patterns, these sharp peaks are identified as quartz. With respect to X-ray diffractogram of metakaolin, quartz is an impurity in the metakaolin and does not take part in geopolymerization reaction.
Fig.2 XRD patterns of metakaolin and PSDS geopolymeric cement products
3.2.2 ESEM-EDXA
Fig.3 shows ESEM micrograph of the hardened PSDS geopolymeric cement matrix. It can be clearly
Fig.3 ESEM micrograph of PSDS geopolymeric cement matrix
seen that the microstructure of geopolymeric cement products is sponge-like. No crystal with regular shape is observed in the bulk geopolymeric cement matrix.
EDXA is also performed in the whole region shown in the above ESEM micrograph to determine its chemical composition after polycondensation reaction. Great cautions should be taken due to the large volume of the electronic interaction sphere at 20 kV accelerating voltage. n(SiO2)/n(Al2O3) and n(K2O)/n(Al2O3) are 6.54 and 1.28, respectively, which are close to the theoretical values of K-PSDS geopolymeric cement matrix (n(SiO2)/n(Al2O3)=6.0, n(K2O)/n(Al2O3)=1.0).
3.2.3 MAS-NMR analysis
Magic-angle spinning MAS-NMR spectroscopy can provide useful structural data for aluminosilicates. In particular, 29Si and 27Al MAS-NMR studies represent a very powerful tool[29].
(1) 27Al MAS-NMR
Earlier investigations[30-32] showed that in aluminate anions, 4-coordinated Al (with respect to oxygen) resonates at 60-80 (chemical shift), and that in aluminosilicates, 4-coordinated Al resonates at 50-20, while 6-coordinated Al resonates at 0-10 from [Al(H2O)6]3+.
The 27Al MAS-NMR spectrum of the fully-reacted PSDS geopolymeric cement matrix is shown in Fig.4. It can be seen that there is a predominant resonance at 40, which is assigned to the 4-coordinated Al and belongs to AlQ4(4Si) type with respect to Ref.[2]. In addition to the resonance at 40, a small resonance at -15.5 that is assigned to the 6-coordinated Al can also be observed. The 6-coordinated Al is caused by traces of kaolin in metakaolin due to the uncompleted calcinations. The absence of any other resonance excludes any residual singular building units of low molecular weight such as AlQ4(0Si), AlQ4(1Si) and AlQ4(2Si). Thus, PSDS geopolymeric cement products are mainly three- dimensional framework aluminosilicates with polymeric building units.
Fig.4 27Al MAS-NMR spectrum of PSDS geopolymeric cement paste (Resonance is caused by spinning sideband effect)
Although 27Al MAS-NMR is a powerful tool in determining the coordination environment of Al, it cannot differentiate various molecular configurations proposed for geopolymeric cement: poly(sialate) (Si— O—Al—O—)n, poly(sialate-siloxo) (Si—O—Al—O—Si—O—)n or poly(sialate-disiloxo) (Si—O—Al—O— Si—O—Si—O—)n polymeric building units. This differentiation can be achieved by using 29Si MAS-NMR spectrum. Therefore, the combination of the 27Al MAS-NMR and 29Si MAS-NMR spectra makes it possible to better understand the structure nature of PSDS.
(2) 29Si MAS-NMR
29Si MAS-NMR spectrum of PSDS geopolymeric cement matrix is illustrated in Fig.5. It can be seen that K-PSDS gives a broad resonance in the range of -70 to -110 associated with a strong resonance at -85.0, a very strong resonance at -90.8 and a small resonance at -103.0. Broad resonances are generally found in zeolitic gels before crystallization of the zeolites. The 29Si broad resonances indicate that the Si and Al tetrahedras in PSDS geopolymeric cement matrix are not regularly ordered along the polymeric chains.
Fig.5 29Si MAS-NMR spectrum and deconvelution spectra of PSDS geopolymeric cement paste (Heavy line is experimental spectrum, and dotted lines are deconvelution spectra)
A previous study has shown that the chemical shift of 29Si in an amorphous or highly disordered state as geopolymer would be increased by approximately 5 when comparing with zeolite with the same chemical compositions[1, 33]. The three main resonances in 29Si MAS-NMR spectrum of K-PSDS geopolymeric cement matrix, namely -85.0, -90.8 and -103.0, corresponding to the ordered 29Si chemical shifts of -90, -96, -108 in zeolite, can be assigned to SiQ4(4Al), SiQ4(2Al) and SiQ4(4Si) units, respectively[33]. However, the three resonances assigned to the three different SiQ4(mAl) units are so close that the interaction between resonances occurs, resulting in a lack of spectral resolution. In order to address it, Gaussian peak deconveolution was adopted to separate and quantify SiQ4(mAl) units, as shown in Fig.5. Quantification of network ordering may allow to establish the molecular model for describing speciation of silicon according to the types and relative proportions of SiQ4(mAl) units.
According to the types of SiQ4(mAl) units and their relative proportions given in Table 4, we can calculate the molar ratio of Si to Al using Eq.(1) proposed in Ref.[31]. The molar ratio of Si to Al equals 2.86?1 for PSDS synthesized in this work, which is approximate to the theoretical value of PSDS geopolymeric cement matrix (n(Si)?n(Al)=3.0?1).
Table 4 Main resonance models and their relative proportions of PSDS geopolymeric cement matrix
(1)
where Isi(mAl) is the intensity of each peak in the deconveluted 29Si MAS-NMR spectra.
4 Conclusions
(1) n(K2O)/n(Al2O3) has an important impact on mechanical strength and microstructure amongst the three key parameters.
(2) PSDS geopolymeric cement with compressive strength (20.1 MPa) can be achieved when n(SiO2)/ n(Al2O3)=6.5, n(K2O)/n(Al2O3)=0.8 and n(H2O)/ n(K2O)=10.0.
(3) PSDS geopolymeric cement possesses structural characteristics similar to gel substances in having a wide range of Si endowments, but predominantly the framework molecular chains of Si partially replaced by 4-coordinated Al tetrahedral.
(4) Although the preparation and microstructure are investigated in this work, long term mechanical behavior, shrinkage and creep, durability of geopolymeric cement still need to be further studied to widely apply this novel type of cement in practical engineering.
References
[1] DAVIDOVITS J. Geopolymers and geopolymeric new materials[J]. Journal of Thermal Analysis, 1989, 35(2): 429-441.
[2] DAVIDOVITS J. Geopolymer chemistry and properties[C]// Proceedings of the First European Conference on Soft Mineralog. Compiegne: The Geopolymer Institute, 1988: 25-48.
[3] DUXSON P, FENANDEZ J A, PROVIS J L, LUKEY G C, PALOMO A, van DEVENTER J S J. Geopolymer technology: The current state of the art[J]. Journal of Materials Science: Special Section, 2007, 42(9): 2917-2933.
[4] RANGAN V. Advances in geopolymer concrete[J]. Engineers Australia, 2003, 75(1): 7-10.
[5] DAVIDOVITS J, DOUGLAS C C, JOHN H P, DOUGLAS J R. Geopolymeric concretes for environmental protection[J]. Concrete International: Design & Construction, 1990, 12(7): 30-40.
[6] DUXSON P, PROVIS J L, LUKEY G C, van DEVENTER J S J. The role of inorganic polymer technology in the development of green concrete[J]. Cement and Concrete Research, 2007, 37(12): 1590-1597.
[7] NOWAK R. Geopolymer concrete opens to reduce CO2 emissions[J]. The New Scientist, 2008, 197(2640): 28-29.
[8] ZHANG Yu-sheng, SUN Wei. Fly ash based geopolymer concrete[J]. Indian Concrete Journal, 2006, 80(1): 20-24.
[9] HONGLING W, HAIHONG L, FENGYUAN Y. Synthesis and mechanical properties of metakaolinite-based geopolymer[J]. Colloid Surface A, 2005, 268(1/3): 1-6.
[10] SOFI M, van DEVENTER J S J, MENDIS P A, LUKEY G C. Engineering properties of inorganic polymer concretes (IPCs)[J]. Cement and Concrete Research, 2007, 37(2): 251-257.
[11] DAEIK K, LAI H T, CHILINGAR G, TEN F Y. Geopolymer formation and its unique properties[J]. Environmental Geology, 2006, 51(1): 103-111.
[12] van JAARSVELD J G S, van DEVENTER J S J. The potential use of geopolymeric materials to immobilize toxic metals: Part I. Theory and applications[J]. Mineral Engineering, 1997, 10(7): 659-669.
[13] BAKHAREV T. Resistance of geopolymer materials to acid attack[J]. Cement and Concrete Research, 2005, 35(4): 658-670.
[14] LYON R E, FODEN A, BALAGURU P N, FODEN A J, SORATHIA U, DAVIDOVITS J. Fire-resistant aluminosilicate composites[J]. Journal of Fire and Materials, 1997, 21(2): 67-73.
[15] BAKHAREV T. Durability of geopolymer materials in sodium and magnesium sulfate solutions[J]. Cement and Concrete Research, 2005, 35(6): 1233-1246.
[16] DAVIDOVITS J. High alkali cements for 21st century concretes[C]// Concrete Technology, Past, Present, and Future. Detroit: American Concrete Institute, 1994: 383-397.
[17] ZUHUA Z, MAO Y, HUAJUN Z, YUE C. Role of water in the synthesis of calcined kaolin-based geopolymer[J]. Applied Clay Science, 2009, 43(2): 218-223.
[18] DUXSON P, PROVIS J L. Designing precursors for geopolymer cements[J]. Journal of the American Society, 2009, 91(12): 3864-3869.
[19] ZHANG Y S, SUN W. Study on polycondensation process of metakaolin based geopolymeric cement using semi-empirical AM1 calculations[J]. Advances in Cement Research, 2008, 21(2): 67-73.
[20] ZHANG Y S, SUN W, LI Z J. Geopolymer extruded composites with incorporated fly ash and polyvinyl alcohol short fiber[J]. ACI Materials Journal, 2009, 106(1): 3-10.
[21] de SILVA P, SAGOE-CRENSTIL K. Medium-term phase stability of Na2O-Al2O3-SiO2-H2O geopolymer systems[J]. Cement and Concrete Research, 2008, 38(6): 870-876.
[22] DOMBROWSKI K, WEIL M, BUCHWALD A. Geopolymer binders[J]. ZKG International, 2008, 61(3): 70-80.
[23] KRIVEN W, BELL J L, GORDON M. Microstructure and microchemistry of fully-reacted geopolymers and geopolymer matrix composites[J]. Ceramic Transactions, 2004, 153: 227-250.
[24] SCHMUCKER M. Microstructure of sodium polysialate siloxo geopolymer[J]. Ceramics International, 2005, 31(3): 433-437.
[25] DAVIDOVITS J. Chemistry of geopolymeric systems terminology[C]//Proceedings of Geopolymere ’99 Institute Geopolymer. Saint-Quentin, 1999: 9-44.
[26] VALERIA F F B, KENENETH J D M, CLELIO T. Synthesis and characterization of materials based on inorganic polymers of alumina and silica: Sodium polysialate polymers[J]. International Journal of Inorganic Materials, 2000, 2(4): 309-317.
[27] AKOLEKAR D, CHAFFEE A, RUSSELL F H. The transformation of kaolin to low-silica X zeolite[J]. Zeolites, 1997, 19(5): 356-365.
[28] van JAARSVELD J G S, van DEVENTER J S J, SCHWARTZMAN A. The potential use of geopolymeric materials to immobilize toxic metals: Part II. Material and Leaching Characteristics[J]. Minerals Engineering, 1999, 12(1): 75-91.
[29] ENGELHARDT G, FAHLKE B, MNGI M, LIPPMAA E. High resolution 29Si NMR of dealuminated Y-zeolites. 2. Silicon, aluminium ordering in the tetrahedral zeolite lattice[J]. Zeolites, 1983, 3(3): 239-243.
[30] WANG Pu, PAN Zhao-lu, WENG Ling-bao. Mineralogy[M]. Beijing: China Geological Press, 1984. (in Chinese)
[31] DUXSON P, PROVIS J L, LUKEY G C, SEPAROVIC F, van DEVENTER J S J. 29Si NMR study of structural ordering in aluminosilicate geopolymer gels[J]. Langmuir, 2005, 21(7): 3028-3036.
[32] DAVIDOVITS J. Geopolymers: Man-made rock geosynthesis and resulting development of very early high strength cement[J]. J Materials Education, 1994, 16(2/3): 91-139.
[33] ENGELHARDT G, MICHEL D. High-resolution solid-state NMR of silicates and zeolites[M]. New York: Wiley, 1987.
(Edited by YANG You-ping)
Foundation item: Project(2009CB623200) supported by the National Basic Research Program of China; Projects(50702014, 50878043) supported by the National Natural Science Foundation of China; Project(NCET-08-0116) supported by the Program for New Century Excellent Talents in University of Ministry of Education, China
Received date: 2008-12-26; Accepted date: 2009-04-21
Corresponding author: ZHANG Yun-sheng, Professor, PhD; Tel: +86-13770936908; E-mail: zhangys279@163.com
- Preparation and microstructure characterization ofpoly-sialate-disiloxo type of geopolymeric cement
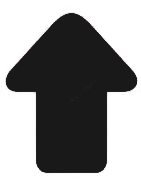