- Abstract:
- 1 Introduction▲
- 2 Experimental▲
- 3 Results and discussion▲
- 3.1 Morphology and element distribution of semigraphitic cathode after electrolysis
- 3.2 Characteristic of cathode electrolysis expansion and its numeric characterization
- 3.3 Influence of αCR on cathode electrolysis expansion and K/Na penetration rate
- 3.4 Influence of βKR on cathode electrolysis expansion and K/Na penetration rate
- 4 Conclusions▲
- References
- Figure
- Fig.1 Element surface analysis figures (a, b, d, e) and morphology of margin part of cross section (c)
- Fig.2 Element surface analysis figures (a, b, d, e) and morphology of central part of cross section (c)
- Fig.3 Effect of αCR on electrolysis expansion at ρCD=0.8 A/cm2, tS=50 ℃ and different βKR values: (a) βKR=0.1; (b) βKR=0.2; (c) βKR=0.3; (d) βKR=0.4; (e) βKR=0.5
- Fig.4 Tendency chart of constant a vs αCR at different βKR values
- Fig.5 Tendency chart of factor Q vs αCR at different βKR values
- Fig.6 Tendency chart of constant a vs βKR at different αCR values
- Fig.7 Tendency chart of factor Q vs βKR at different αCR values
J. Cent. South Univ. Technol. (2009) 16: 0422-0428
DOI: 10.1007/s11771-009-0071-x
Electrolysis expansion performance of semigraphitic cathode in [K3AlF6/Na3AlF6]-AlF3-Al2O3 bath system
LI Jie(李 劼), FANG Zhao(方 钊), LAI Yan-qing(赖延清), L? Xiao-jun(吕晓军), TIAN Zhong-liang(田忠良)
(School of Metallurgical Science and Engineering, Central South University, Changsha 410083, China)
Abstract:
The electrolysis expansion of semigraphitic cathode in [K3AlF6/Na3AlF6]-AlF3-Al2O3 bath system was tested by self-made modified Rapoport apparatus. A mathematical model was introduced to discuss the effects of αCR (cryolite ratio) and βKR (elpasolite content divided by the total amount of elpasolite and sodium cryolite) on performance of cathode electrolysis expansion. The results show that K and Na (potassium and sodium) penetrate into the cathode together and have an obvious influence on the performance of cathode electrolysis expansion. The electrolysis expansion and K/Na penetration rate increase with the increase of αCR. When αCR=1.9 and βKR=0.5, the electrolysis expansion is the highest, which is 3.95%; and when αCR=1.4 and βKR=0.1, the electrolysis expansion is the lowest, which is 1.28%. But the effect of βKR is correlative with αCR. When αCR=1.6 and 1.9, with the increase of βKR, the electrolysis expansion and K/Na penetration rate increase. However, when αCR=1.4, the electrolysis expansion and K/Na penetration rate firstly increase and then decrease with the increase of βKR.
Key words:
1 Introduction
Compared with the deficiency of high temperature, high energy consumption of current aluminum electrolysis, low temperature electrolysis can effectively improve the current efficiency, increase the purity of primary aluminum, lower energy consumption, and prolong the lifespan of aluminum reduction cell. So it has become one of the most active research topics in current international aluminum sphere [1-2]. At present, the research effort of low temperature electrolyte system has mainly focused on Na3AlF6-AlF3-Al2O3, Li3AlF6-AlF3-Al2O3 and K3AlF6-AlF3-Al2O3 bath systems [3-8]. From the laboratory experiments, it can be known that based on Na3AlF6-AlF3-Al2O3 and Li3AlF6-AlF3-Al2O3 bath systems, the solubility and solution rate of alumina decrease with decreasing electrolysis temperature. Comparatively, the solution properties of alumina are superior in K3AlF6-AlF3-Al2O3 bath system. With decreasing electrolysis temperature, the solution properties of alumina are of great importance and related to the normal and reposeful operation of aluminum reduction cell. Therefore, the K3AlF6-AlF3-Al2O3 bath system has considerable predominance in low temperature electrolysis. However, considering the actual carbon cathode, it will be greatly destroyed by pure elpasolite used to carry out low temperature electrolysis and the lifespan of cell will also be shortened markedly. At this circumstance, the application of composite electrolyte composed of elpasolite and sodium cryolite can not only lower the electrolysis temperature and ameliorate the solution properties of alumina, but also avoid the destructive effect of pure elpasolite on carbon cathode. From the literatures reported at home and abroad [9-12], it can be seen that researches about the penetration and destructive action of alkali metal to cathode mostly include the penetration of Na and the expansion and failure of cathode in macroscopic view during the conventional electrolysis process only, but those about performance of electrolysis expansion of cathode in the new type of low temperature electrolyte containing K were barely reported. There are only a few qualitative researches which believe that leopoldite has strong penetration ability on carbon material, which is about decuple of sodium salt [4-6]. Therefore, whether or not this new type of low temperature electrolyte can be applied in electrolytic aluminum industry, it is extraordinarily necessary to study the penetration characteristics of the electrolyte on the carbon cathode profoundly and quantificationally.
In order to research the K/Na penetration characteristics of this composite electrolyte composed of elpasolite and sodium cryolite, semigraphitic cathode was employed as the research object, which is widely used in the current electrolytic aluminum industry. A self-made modified Rapoport apparatus was adopted to review its performance of electrolysis expansion in [K3AlF6/Na3AlF6]-AlF3-Al2O3 bath system, and the influences of αCR and βKR on the performance of electrolysis expansion of semigraphitic cathode were studied. Moreover, the morphology and element distribution about the cross section of specimens after electrolysis were analyzed.
2 Experimental
2.1 Cathode specimens
Semigraphitic cathode widely used in electrolytic aluminum industry was selected as cathode specimen, and the quality of which accorded with criterion YS/T287—2005. The cathode was machined into the cylinder of 20 mm×60 mm (diameter×length), and a circle hole with a diameter of 5 mm in one side surface was drilled in order to connect steel rod with specimen.
2.2 Experimental method and condition
The specimen was put into a cell made of high purity graphite in the vertical tube furnace, and the cylindrical cathode specimen was immersed into the molten electrolyte by 25 mm. The chemical reagents used in the experiment were: K3AlF6 (analytical grade), Na3AlF6 (analytical grade), Al2O3 (analytical grade) and AlF3 (commercial grade). According to the difference of αCR, the experiments could be grouped into three teams. In one team, αCR was constant and βKR was respectively 0.1, 0.2, 0.3, 0.4 and 0.5, as shown in Table 1. The
Table 1 αCR, βKR and tL of electrolyte in each experiment
concentration of alumina in the electrolyte was saturated in every experiment. The current density (ρCD) was 0.8 A/cm2 and the superheat temperature (tS) was 50 ℃. The specimens were subjected to electrolyte for 1.5 h. Testing temperature was determined by the liquidus temperature (tL) of each electrolyte and superheat. The whole experimental process was taken in the high-purity argon atmosphere.
2.3 Test of electrolysis expansion
A self-made modified Rapoport apparatus was used to test the linear expansion displacement of specimen and the cathode electrolysis expansion was figured out by the following equation [9-10]:
ρ=?L/L (1)
where ρ is the cathode electrolysis expansion, ?L is the linear displacement of cathode expansion, and L is the initial length of specimen.
2.4 Characterization of cathode specimens after electrolysis
The cross sections of specimens after electrolysis were analyzed by a JEOL JSM-5600LV backscatter electron image (BEI). NORAN VANTAGE4105 X-ray energy dispersive spectrometry was used to test the element distribution in the cross sections of specimens.
3 Results and discussion
3.1 Morphology and element distribution of semigraphitic cathode after electrolysis
The obtained cathode specimen A4 was carved after electrolysis along the radial direction. The cross section is about 10 mm from the bottom. Japanese JEOL JSM-5600LV SEM was used to analyze the morphology of the margin and the central part of the cross section. Fig.1 shows the morphology and element surface analysis figures about the margin part of cross section. The white zone in morphology figure is mainly the electrolyte penetrating in cathode’s pores, and the grey zone is the semigraphitic cathode. It can be clearly seen that because of the electrocapillarity, a mass of electrolyte penetrates into the cathode and fills in the pores of it. It is this electrolyte existing in the pores of the cathode that makes the interface between electrolyte and cathode increment. Consequently, the penetration of K/Na to the cathode is aggravated. Meanwhile, in the process of electrolysis, once K and Na precipitate on the surface of cathode, they will penetrate into carbon cathode under the bonding action between the electron in orbit s of alkali metal and electron in orbit π in carbon. From elements surface analysis figures, it can be seen that both K and Na penetrate into the cathode, but K, Na, and F do not entirely appear in the same area. This suggests that K and Na penetrating into the cathode are not totally K and Na contained in the electrolyte penetrating into the cathode. The amounts of K and Na shown in the figures that are not in the same area of F are just K and Na precipitated on the surface of cathode that penetrate into the cathode and cause the expansion and failure of cathode in macroscopic view. Meanwhile, the penetration capacity of K is larger than that of Na. This suggests that both K and Na have strong penetration ability to cathode, and the penetration ability of K is stronger than that of Na under the same electrolysis condition.
Fig.2 shows the morphology and element surface analysis figures about the central part of the cross section. It can be clearly seen that the central part of the specimen is also filtered by electrolyte, most of which concentrates in the pores of cathode. But compared with Fig.1, the electrolyte reduces apparently. Element surface analysis figures show that K, Na, and F do not entirely appear in the same area also. Both K and Na precipitated on the surface of cathode penetrate into cathode in various degrees, and the penetration capacity of K is larger than that of Na, but both of them abate compared with Fig.1. This suggests that K and Na penetrate into cathode from exterior to interior gradually, and K has stronger penetrating ability than Na.
3.2 Characteristic of cathode electrolysis expansion and its numeric characterization
Fig.3 shows respectively the curves of electrolysis expansion of specimens as a function of electrolysis time in the new type of low temperature electrolyte with the same βKR and different αCR, where the abscissa is the electrolysis time and ordinate is the linear electrolysis expansion of specimens. As shown in Fig.3, when αCR=1.9, βKR=0.5, the cathode electrolysis expansion is the highest, which is 3.95%; when αCR=1.4, βKR=0.1, the cathode electrolysis expansion is the lowest, which is 1.28%.
As shown in Fig.3, it can be seen that the curves of electrolysis expansion of specimens all take a parabolic shape, which are analogous to the curves of sodium expansion obtained in common sodium cryolite bath
Fig.1 Element surface analysis figures (a, b, d, e) and morphology of margin part of cross section (c)
Fig.2 Element surface analysis figures (a, b, d, e) and morphology of central part of cross section (c)
Fig.3 Effect of αCR on electrolysis expansion at ρCD=0.8 A/cm2, tS=50 ℃ and different βKR values: (a) βKR=0.1; (b) βKR=0.2; (c) βKR=0.3; (d) βKR=0.4; (e) βKR=0.5
[11]. At the beginning of electrolysis, the increasing speed of electrolysis expansion is fast, with the proceeding of electrolysis, the increasing speed of electrolysis expansion reduces gradually and in the end, the electrolysis expansion becomes constant as a whole. This illustrates that the mathematic model (Eqn.(2)) can be roundly and quantificationally used to numerically character the curves of electrolysis expansion obtained in the new type of low temperature electrolyte that contains elpasolite [12]. It can be used not only to analyze
the electrolysis expansion simply and intuitively, but also to study the K/Na penetration rate that is difficult to make out in the figures above.
y=aexp(-b/x) (2)
Through Eqn.(2), constant a and factor Q are introduced, which can numerically character the electrolysis expansion of material and K/Na penetration rate, respectively. Q is related to both a and b, and Q equals a/b. Based on Fig.3, constant a and factor Q are calculated through Eqn.(2), and listed in Table 2.
Table 2 Characterization of performance of electrolysis expansion by constant a and factor Q
3.3 Influence of αCR on cathode electrolysis expansion and K/Na penetration rate
Fig.4 and Fig.5 respectively show the tendency chart of constant a and factor Q as a function of αCR at different βKR values. As shown in Fig.4 and Fig.5, it can be clearly seen that both constant a and factor Q present an elevated tendency with the increase of αCR. This illustrates that electrolysis expansion and K/Na penetration rate increase with the increase of αCR.
Fig.4 Tendency chart of constant a vs αCR at different βKR values
This phenomenon can be explained as follows. Many graphitic compositions are included in semigraphitic cathode, the structures of which are well lamellar. Carbon atoms in every layer can shape the rocky hexagonal reticular planes through the combination of covalent bond formed by sp2 hybrid orbital electrons and metallic bond formed by 2pz orbital electrons. The bonding energy among carbon atoms is
Fig.5 Tendency chart of factor Q vs αCR at different βKR values
very strong (345 kJ/mol), but the layers are combined by faint van der Waals force (16.7 kJ/mol). Various atoms, molecules and particle clusters can break through barriers and insert into interlamination because of the great difference of bonding force within the layer and interlamination as well as the faint binding force between layers, thus finally forming graphite intercalation compounds (GICs) [13]. Alkali-graphite intercalation compounds [CxM(K/Na)] belong to one type of them.
The process of aluminum electrolysis needs higher temperature, which may lead to the replacement reaction between liquid aluminum and NaF or KF in the molten bath and the precipitation of Na and K. Meanwhile, in some conditions, Na+ and K+ in molten bath can directly discharge on the surface of cathode, and Na and K precipitate. Evolution reactions of Na and K in molten salt are as follows [10]:
Na+/K++e=Na/K(dissolved) (3)
or
Al(l)+3NaF/KF(in electrolyte)=
3Na/K(dissolved)+AlF3(in electrolyte) (4)
The precipitated Na and K will penetrate into the inner part of cathode through pores and carbon lattice, and react with the carbon, forming CxM(K/Na) and resulting in the increase of interlayer spacing of graphite. In the macroscopic view, the expansion and failure of cathode can be observed. Therefore, the amount of the precipitated Na and K will directly influence the concentration of Na and K on the cathode surface, and then influence the diffusion kinetic parameters of Na and K, finally making a great impact on the performance of cathode electrolysis expansion. With increasing αCR, the D-value of evolution potential among K, Na and Al decreases [14], which directly results in the increase of precipitation amount, thereby pricking up the penetration of K and Na to cathode and impelling the generation of CxM(K/Na), finally causing the increase of cathode electrolysis expansion and K/Na penetration rate. Meanwhile, αCR also influences the balance of chemical reaction (4). As αCR goes up, the contents of K+ and Na+ in the electrolyte increase, and chemical reaction (4) moves to the right side, which will also cause the increasing amount of precipitated K and Na, consequently causing the increase of cathode electrolysis expansion and K/Na penetration rate.
3.4 Influence of βKR on cathode electrolysis expansion and K/Na penetration rate
Figs.6 and 7 respectively show the tendency chart of constant a and factor Q as a function of βKR at different αCR values. As shown in Figs.6 and 7, it can be clearly seen that when αCR=1.6 and 1.9 both constant a and factor Q present elevated tendency with the increase of βKR. This illustrates that electrolysis expansion and K/Na penetration rate increase with the increase of βKR. The reason of this phenomenon is that when αCR maintains a certain value, the increase of βKR can be considered that the equivalent elpasolite is substitute for sodium cryolite. Atomic radius of K is 0.227 2 nm, while that of Na is 0.190 0 nm. The former preponderates over the latter.
Fig.6 Tendency chart of constant a vs βKR at different αCR values
Fig.7 Tendency chart of factor Q vs βKR at different αCR values
Therefore, when the same amount of K penetrates into carbon cathode and generates CxM(K/Na), the electrolysis expansion caused by K is larger than that caused by Na. That is to say, so long as the αCR keeps constant, the increase of βKR will cause a larger expansion of cathode. Therefore, the cathode electrolysis expansion gradually increases with the increase of βKR. But in this work, K does not exhibit decuples penetration ability to Na, which is different from that mentioned in Refs.[4-6]. The reason is that when electrolysis is conducted at correspondingly lower temperature, the D-values of evolution potential among K, Na and Al increase, and the precipitation amount of K and Na reduces, so does the penetration ability [14]. Furthermore, the current density used in the experiment is 0.8 A/m2. At this circumstance, the wettability of liquid aluminum to carbon cathode can be improved. During the process of electrolysis, the surface of cathode may be covered by a flat of liquid aluminum, thereby preventing the penetration of K and Na to a certain extend [15-16].
At the point of αCR=1.4, constant a and factor Q present elevated tendency as βKR increases from 0.1 to 0.3, which is analogous to that when αCR =1.6 and 1.9. But if βKR keeps on increasing, constant a and factor Q decrease sharply. That is to say, when βKR increases from 0.1 to 0.3, cathode electrolysis expansion and K/Na penetration rate increase gradually; and when βKR keeps on increasing, cathode electrolysis expansion and K/Na penetration rate decrease sharply. In terms of the migration mechanism of sodium vapor proposed by DELL [17], and HOP et al [18] and diffusion mechanism through the carbon lattice reported in Ref.[19], it can be known that both temperature and vapor pressure have great impacts on Na penetration. Both K and Na belong to IA group, and their valence electron structures are both ns1. Therefore, K may also penetrate into carbon cathode like Na, and forms C-K intercalation compounds, resulting in the failure of cathode during the process of electrolysis [18, 20]. When βKR=0.4, the practical electrolysis temperature lies between the steam point of Na and K; and when βKR=0.5, it lies below the steam point of Na and K. At this temperature, the vapor pressures of Na and K are not very high, causing the decrease of penetration ability of Na and K [21]. Besides, the lower temperature also affects the D-value of evolution potential among K, Na and Al, which increases with the decrease of temperature. This makes Na and K difficult to deposit on the surface of cathode, also causing the decrease of their penetration ability. So, when βKR=0.4 and 0.5, although βKR increases, the cathode electrolysis expansion and K/Na penetration rate do not increase but decrease because of the effect of temperature. This reveals that the influence of temperature on the performance of cathode electrolysis expansion exceeds that of βKR at a certain circumstance.
4 Conclusions
(1) During the process of electrolysis, K and Na penetrate into semigraphitic cathode from exterior to interior and have obvious effects on the performance of carbon cathode expansion. K has stronger penetration ability than Na, but does not present decuples of penetration ability than Na.
(2) In the [K3AlF6/Na3AlF6]-AlF3-Al2O3 bath system, the curves of cathode electrolysis expansion are analogous to those of sodium expansion obtained in common electrolyte. Constant a and factor Q can be introduced to numerically character the performance of cathode electrolysis expansion.
(3) αCR has a marked influence on the cathode electrolysis expansion and K/Na penetration rate which are caused by the co-action of K and Na. The cathode electrolysis expansion and K/Na penetration rate can be decreased through reducing αCR.
(4) The influence of βKR on the performance of cathode electrolysis expansion differs with the change of αCR. Under a certain αCR, a proper addition of elpasolite can reduce the destructive effect of K to cathode and actualize its predominance adequately. The decrease of temperature can counteract the increment of cathode electrolysis expansion and K/Na penetration rate caused by the increment of βKR to a certain extent and reduce the destructive effect of K/Na to cathode.
(5) In this new type of low temperature composite electrolyte containing K, electrolysis expansion of semigraphitic cathode is one of the most important performances referring to the quality of cathode materials that will directly affect the cell life. There are several other factors that will probably influence the electrolysis expansion of semigraphitic cathode such as current density and superheat, which need to be further studied in the next research work.
References
[1] JAMES W E, HALVOR K. Sustainability, climate change, and greenhouse gas emissions reduction: Responsibility, key challenges, and opportunities for the aluminum industry [J]. JOM, 2008, 60(8): 25-31.
[2] JAMES W E. The evolution of technology for light metals over the last 50 years: Al, Mg, and Li [J]. JOM, 2007, 59(2): 30-38.
[3] LAI Yan-qing, WANG Jia-wei. Commentary on the status quo of low temperature aluminum electrolysis in the Na3A1F6-A12O3 bath system [J]. Light Metal, 2006(9): 37-42. (in Chinese)
[4] WANG Jia-wei, LAI Yan-qing. Commentary on the status quo of low temperature aluminum electrolysis in M(K or Li)3AlF6-Al2O3 bath system [J]. Light Metal, 2007(1): 31-36. (in Chinese)
[5] YANG J H, DONALD G G, CATHERINE W, JOHN N H. Alumina solubility in KF-AlF3-based low-temperature electrolyte system [C]// Light Metals 2007. Orlando, 2007: 537-541.
[6] ROLSETH S, GUDBRANDSEN H, THONSTAD J. Low temperature aluminium electrolysis in a high density electrolytes. PartⅠ [J]. Aluminum, 2005, 81(5): 448-450.
[7] ROLSETH S, GUDBRANDSEN H, THONSTAD J. Low temperature aluminium electrolysis in a high density electrolytes. Part Ⅱ [J]. Aluminum, 2005, 81(6): 565-568.
[8] SKYBAKMOEN E, SOLHEIM A, STEREN A. Phase diagram data in the system Na3AlF6-Li3AlF6-AlF3-Al2O3 [C]// Light Metals 1990. Anaheim, 1990: 317-323.
[9] XUE Ji-lai, LIU Qing-sheng, OU Wen-li. Sodium expansion in carbon/TiB2 cathodes during aluminum electrolysis [C]// Light Metals 2007. Orlando, 2007: 651-654.
[10] ZOLOCHEYSKY A, HOP J G, SERVANT T, FOOSNAS T, OYE H A. Rapoport-Samoilenko test for cathode carbon materials Ⅱ. Swelling with external pressure and effect of creep [J]. Carbon, 2005, 43(6): 1222-1230.
[11] L? Xiao-jun, LI Qing-yu, LAI Yan-qing, LI Jie. Digital characterization and mathematic model of sodium penetration into cathode material for aluminum electrolysis [J]. Journal of Central South University of Technology, 2009, 16(1): 96-100.
[12] LI Qing-yu. Development and industrial application of wettable inert TiB2 cathodic composite coating for aluminum electrolysis [D]. Changsha: Central South University, 2003: 39-46. (in Chinese)
[13] CHUAN Xiu-yun. Formation mechanism of graphite intercalation compounds [J]. New Carbon Materials, 2000, 15(1): 52-56. (in Chinese)
[14] QIU Zhu-xian. Smelting aluminum in pre-baked cell [M]. Beijing: Metallurgical Industry Press, 2005: 311-314. (in Chinese)
[15] ARNE P R, ANNE S, ASBJORN S, FOOSNAES T. The effect of current density on cathode expansion during strat-up [C]// Light Metals 2008. New Orleans, 2008: 973-978.
[16] XUE J L, OYE H A. Sodium and bath penetration into TiB2-carbon cathodes during laboratory aluminum electrolysis [C]// Light Metals 1992. San Diego, 1992: 773-778.
[17] DELL M B. In Extractive metallurgy of aluminium [M]. New York: Interscience Publishers, 1963: 403-405.
[18] HOP J, STORE A, FOOSNAES T, OYE H A. Chemical and physical changes of cathode carbon by aluminium electrolysis [J]. Transactions of the Institutions of Mining and Metallurgy, 2005, 114(3): 181-187.
[19] MORTEN S, OYE H A. Cathodes in aluminium electrolysis [M]. Düsseldorf: Aluminium-Verlag, 1994: 184-190.
[20] CHAN B K C, THOMAS K M, MARSH H. The interactions of carbons with potassium [J]. Carbon, 1993, 31(7): 1071-1082.
[21] YURI M, OYE H A. Absorption of metallic sodium in carbon cathode materials [J]. Carbon, 1996, 34(1): 37-41.
(Edited by CHEN Wei-ping)
Foundation item: Project (2005CB623703) supported by the Major State Basic Research and Development Program of China; Project (2008AA030502) supported by the National High-Tech Research and Development Program of China
Received date: 2008-09-28; Accepted date: 2008-11-12
Corresponding author: L? Xiao-jun, Doctoral candidate; Tel: +86-731-8876454; E-mail: lxj8886@yahoo.com.cn
- Electrolysis expansion performance of semigraphitic cathode in [K3AlF6/Na3AlF6]-AlF3-Al2O3 bath system
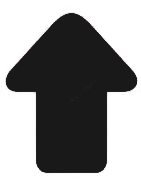