- Abstract:
- 1 Introduction▲
- 2 Modularized modeling of...▲
- 3 Simulation results ▲
- 4 Validation of model▲
- 4.1 Analytical solution to natural frequency of wave action and sloshing of water in cuboid container
- 4.2 Comparison between analytical solution and results of natural period of model for wave action and sloshing of water in cuboid container
- 4.3 Empirical formula of calculating natural period of wave action of water in cylinder
- 5 Conclusions▲
- References
- Figure
- Fig.1 Drum structure
- Fig.2 Module division of drum
- Fig.3 Relation between drum level and period of wave action and sloshing
- Fig.4 Relation between drum length and period of wave action and sloshing
- Fig.5 Relation between density of liquid and amplitude of wave action and sloshing
- Fig.6 Relation between number of sub-module and period of wave action and sloshing
- Fig.7 3D graphics of drum level wave action and sloshing
- Fig.8 Comparison between natural period of 1-order modal and result of model
- Fig.9 Comparison between results of model and those of empirical formula
J. Cent. South Univ. Technol. (2007)06-0814-06
DOI: 10.1007/s11771-007-0155-4
Dynamic simulation of hydrodynamic model of drum level wave action and sloshing
CAO Xiao-hua(曹晓华)1,2, CAO Xiao-ling(曹小玲)2,3, JIANG Shao-jian(蒋绍坚)3, SU Ming(苏 明)2
(1. Education College, Zhejiang Normal University, Jinhua 321004, China;
2. School of Mechanical and Power Engineering, Shanghai Jiaotong University, Shanghai 200030, China;
3. School of Energy and Power Engineering, Central South University, Changsha 410083, China)
Abstract:
In order to build the model of the drum level wave action and sloshing, based on the method of modularization modeling, the hydrodynamic model of drum level wave action and sloshing was developed, and dynamic simulation researches were carried out based on the model. The results indicate that both drum level and drum length have functional relations with period of drum level wave action and sloshing. When the drum level decreases or drum length increases, the period of drum level wave action and sloshing increases, density of liquid and number of sub-module division have little influence on the period of drum level wave action and sloshing. The model was validated by the analytical solution theory of liquid’s wave action and sloshing in cuboid container, and the 3D graphics of drum level wave action and sloshing was also obtained. The model can dynamically reflect the rules of wave action and sloshing of water in the container exactly.
Key words:
1 Introduction
Heat recover steam generator (HRSG) is the key part of combined cycle, its drum level control is the focus for the safe operation of boiler and combined cycle system, besides, its control performance can considerably affect the main performances of HRSG and combined cycle. At present, much research work about HRSG modeling has been done by different researchers by different means at home and abroad. GOU et al[1] using method of modularization modeling to investigate HRSG modeling. Also GAO et al[2], AKIYAMA et al[3] and DUMONT et al[4] have done some research work on the HRSG modeling. Studying dynamic characteristics of HRSG and providing service to system controlling are their research aims. Meanwhile, modeling research of HRSG has been done by QIU and YANG[5], KUNITOMI et al[6] and ONG’IR et al[7] using the method of transfer function as well. But until now, no papers about drum level wave action and sloshing have been published.
The practical operation of HRSG indicates that drum level is always sloshing and under wave action, and its forming principle is relatively complex. Also, at present, the great negative influence of the constant wave action and sloshing of drum level on the control system of drum level is never considered. With increasing requirement of the combined cycle for drum level controlling, how to build the model for drum level wave action and sloshing and how to eliminate the negative effect of the drum level wave action and sloshing on the controlling system have already become a very challenging research subject. Therefore, in this work, the model of drum level wave action and sloshing was set up using the method of modularized modeling, and some simulation researches were carried out.
2 Modularized modeling of drum level wave action and sloshing
2.1 Module division of drum
The drum structure is illustrated in Fig.1. A main-steam outlet and a downcomer are at the center of the drum, and the risers are installed at the drum bottom symmetrically. One feed-water inlet is installed at one end of the drum, while feed-water is sprinkled into the drum through many feed-water outlets uniformly distributed in the drum.
The module division is shown in Fig.2. The drum is divided into some segments along the level orientation. The model comprises of some modules, each of which represents a segment of the drum, including riser inlets and feed-water outlets and containing steam and mixture of water and steam[8-11]. The module corresponding to the medium segment has a downcomer and a main-steam outlet. Two adjacent modules exchange water and steam with each other. In Fig.2, WG1 represents steam exchange between module 1 and module 2, and WL1 is water exchange, WG2 and WL2 mean exchange of steam and water between module 2 and module 3, analogy in turn. In order to facilitate the research, according to the characteristics of parameters in this system, the parameters are assumed to be the values of designed point.
Fig.1 Drum structure
Fig.2 Module division of drum
2.2 Hypotheses of modeling
In order to facilitate the main factors that affect the wave action and sloshing, the basic hypotheses for modeling are made as follows:
1) The density of water in drum is constant,and water is uncompressible.
2) The effect of the steam pressure on the surface of the water on the wave action and sloshing is ignored.
3) The effect of the steam in water on the wave action and sloshing is ignored.
4) The effect of energy exchange between water and steam on the wave action and sloshing is not considered.
5) The effect of the steam’s fluid on the drum level wave action and sloshing is ignored, as the speed of steam’s fluid is too fast.
2.3 Structure of module
From the above-mentioned method of module division and hypotheses of modeling, three types of modules need to be built for the model of drum level wave action and sloshing, namely DD module, DN module, and MS module. The module DN is used to describe the middle segments of the drum, the module DD is used to describe the left one of the drum. The difference between the module DD and DN is that some parameters of module DD are set to be zero firstly, and have different module joints. The module MS is used to describe the right segment of the drum, its some parameters are also set to be zero firstly, and it has no momentum equation compared with the above- mentioned two modules. Equations used in these 3 modules are illuminated as follows.
2.3.1 DD and DN modules
Mass conservation equation for water inside drum is[9-11]
(1)
where m is the mass of module, kg; we is mass input flow of module, kg/s; wl is mass output flow of module, kg/s.
Momentum conservation equation for water inside drum is[9-11]
(2)
where is average flow rate of whole water in module, m/s;
and
are total input and output flow rates of module, m/s; gc and g are acceleration ratio of gravity and acceleration of gravity, m/s2; pe and pl are input and output pressures, MPa; Ae and Al are input and output areas, m2; pw is the pressure of friction caused by the flowing, MPa; τ is the force of friction caused by the flowing, N; θ is the angle between the control volume and level, rad.
Simplifying the left parts of the above two equations, we obtain
(3)
(4)
where w is the mass flow rate of all water in module, kg/s; V is the volume of all water in module, m3; ρ is the density of water in drum, kg/m3; A is the across area of water in module, m2. Substituting Eqns.(3) and (4) into Eqns.(1) and (2), and according to hypothesis of modeling, these equations can be further simplified as follows:
(5)
(6)
where h and h2 are the heights of water inside border upon two modules, m; A′ is vertical area of water in module, m2.
2.3.2 MS module
Mass conservation equation of water in drum is[9-11]
(7)
According to above method of simplifying, Eqn.(7) can be further simplified as
(8)
2.4 Configuration of drum model based on EASY5 software
According to the division of the above-mentioned modules, hypotheses of modeling, and structure of modules, the drum from certain famous electric company in America is divided into 20 sub-modules: one DD sub-module, 18 DN sub-modules, one MS sub-module. And based on the EASY5 software, the hydrodynamic model of drum level wave action and sloshing was set up.
3 Simulation results
3.1 Size of drum and running parameters
According to the configuration and running parameters of the present HRSG-barglan from certain famous electric company in America, the size and related parameters of drum are calculated as follows: length of drum 13.05 m, diameter of drum 1.67 m, flow-rate of main-steam 35.278 kg/s, drum pressure 13.18 MPa, temperature of water 337 ℃, feed-water flow rate 35.278 kg/s.
3.2 Simulation results
Based on the model and the above-mentioned basic parameters of the drum, when the model runs under different conditions that some particular parameters change, some rules and conclusions of drum level wave action and sloshing are obtained.
3.2.1 Relation between drum level and period of wave action and sloshing
Supposing that the other conditions are stable, and the model runs under different drum levels, some results are obtained, and the results observed in simulation indicate that there exists the function relation between drum level and period of wave action and sloshing. Fig.3 shows the relation between drum level and period of wave action and sloshing. It can be seen that the period of wave action and sloshing decreases when the drum level increases, and the drum level is the average water level of all segments inside the drum.
Fig.3 Relation between drum level and period of wave action and sloshing
3.2.2 Relation between drum length and period of wave action and sloshing
When the drum level is 0.55 m, and other parameters are not changed, the model runs under different drum lengths. The results observed in simulation indicate that there exists the function relation between drum length and period of wave action and sloshing. Fig.4 shows the relation between drum length and period of wave action and sloshing. It can be concluded that period of wave action and sloshing increases when drum length increases.
Fig.4 Relation between drum length and period of wave action and sloshing
3.2.3 Relation between density of liquid and wave action and sloshing
As the HRSG works, the density of mixed water and steam inside drum changes. So, it is important to study the effect of density of mixture on the wave action and sloshing. When the drum level is 0.55 m, and other parameters are not changed, only the density of wave action and sloshing liquid changes from 400 to 1000 kg/m3, the simulation results of the model indicate that the period of wave action and sloshing does not change when the density of wave action and sloshing liquid changes, and the amplitude of wave action and sloshing increases when the density of wave action liquid decreases. Fig.5 shows the relation between the density of liquid and amplitude of wave action and sloshing.
Fig.5 Relation between density of liquid and amplitude of wave action and sloshing
3.2.4 Effect of number of sub-module on wave action and sloshing
It is found that the more the number of sub-modules is divided, the closer the simulation result is to the fact. But too many sub-modules for the model will cause the slower speed of calculation. In order to get reasonable number of sub-module division, it is necessary to study the effect of number of sub-module division on the wave action and sloshing. The boundary condition is not changed, and the drum level is 0.835 m, the drum is divided into different models that include different numbers of sub-modules. When these models run, some results can be obtained. The results indicate that if number of sub-module is more than 15, the effect of number of sub-module on the period of wave action and sloshing is very small. Fig.6 shows the effect of sub-module number on the period of wave action and sloshing. It can be seen that the sub-module number has little effect on period of wave action and sloshing. Table 1 lists the effect of sub-module number on amplitude of wave action and sloshing. It can be concluded from Table 1 that the sub-module number also has little effect on the amplitude of wave action and sloshing, and the error of amplitude is far less than 5%.
Fig.6 Relation between number of sub-module and period of wave action and sloshing
Table 1 Error of wave action and sloshing amplitude in different ranges of sub-module number
3.2.5 3D graphic of drum level wave shape
Fig.7 shows the drum level at different times and different sub-modules. From this figure, it can be seen that how the drum level wave acts and sloshes. Only wave shape of drum level wave action and sloshing between 0 and 40 s is shown. In this way, the 3D wave shape graphic can be seen clearly. Every sub-module represents the drum length is 0.65 m.
Fig.7 3D graphics of drum level wave action and sloshing
4 Validation of model
4.1 Analytical solution to natural frequency of wave action and sloshing of water in cuboid container
The results in Refs.[12-13] indicate that the natural frequency of wave action and sloshing of water in cuboid container can be calculated by analytical formula, and once the water gets power, it will wave motion and slosh mainly with 1-order modal. The energy of the other modals is very small, and can be ignored in application of engineering[14]. At the same time, the following equation has been already used and validated in engineering:
(9)
where δi,j is the angle frequency, rad/s; i is the rank of horizontal modal; j is the rank of longitudinal modal; a is the length of horizontal of cuboid container, m; b is length of longitudinal of cuboid container, m; h is water level, m; g is acceleration of gravity, m/s2.
4.2 Comparison between analytical solution and results of natural period of model for wave action and sloshing of water in cuboid container
In order to validate the model based on EASY5 software, the natural frequency of wave action and sloshing of water in cuboid container is calculated by analytical formula. The size of cuboid container and the other data in this calculating example are as follows: a=13.05 m, b=1.48 m;water levels are 0.15, 0.35, 0.55, 0.75, 0.95, 1.15 and 1.35 m.
Table 2 and Fig.8 show the results of analytical formula, namely, the 1-order natural period of landscaper orientation.
The above example is calculated with the model based on EASY5 software, comparison between analytical solution of 1-order modal of and results of the model for natural period of the wave action and sloshing of water in cuboid container are also shown in Fig.8 and Table 2.
According to Fig.8 and Table 2, it can be found that the results of the model agree with analytical solution of 1-order modal well. The maximal error of the two results is within 5%, so the model based on EASY5 software can satisfy the demand of engineering application.
Table 2 Analytical solution of 1-order modal and results of model for water in cuboid container
Fig.8 Comparison between natural period of 1-order modal and result of model
4.3 Empirical formula of calculating natural period of wave action of water in cylinder
According to analytical formula of the angle frequency of water in cuboid container and combining with the results of model for water in cylinder, the cylinder is the drum from certain famous electric company in America, the empirical formula of angle frequency of water in cylinder can be obtained, as follows:
(10)
According to the results of empirical formula and those of the model based on EASY5 software, it can be found that error between results of empirical formula and those of model based on EASY5 software is little, every error is within 5%. Fig.9 shows the comparison between the results. This empirical formula will be helpful for eliminating the effect of the wave action and sloshing on the control system[15].
Fig.9 Comparison between results of model and those of empirical formula
5 Conclusions
1) There exists the function relation between the period of drum level wave action and sloshing and drum level. When the drum level rises, the period of drum level wave action and sloshing decreases.
2) There exists the function relation between the period of drum level wave action and sloshing and drum length. When the drum length increases, the period of drum level wave action and sloshing also increases.
3) The liquid density has little effect on the period of drum level wave action and sloshing, but the amplitude of drum level wave action and sloshing decreases when the liquid density increases.
4) The number of sub-module has little effect on the period of drum level wave action and sloshing, and the number of sub-module has little effect on the amplitude of drum level wave action and sloshing. The error of wave action and sloshing amplitude is within 5%. When number of the drum sub-module are 20, the 3D graphics of drum level wave action and sloshing is obtained, from this graphics, the course of drum level wave action and sloshing can be seen clearly.
5) The model can reflect the rule of drum level wave action and sloshing dynamically, its error is within engineering application requirements.
References
[1] GOU Jian-bing, NI Wei-dou, LI Zheng. Visual modular modeling research of heat recovery steam generator[J]. Journal of Tsinghua University, 1999, 39(3): 121-124. (in Chinese)
[2] GAO Jian-qiang, CHANG Xi-mao. An engineering modular simulation model of nature circulation boiler evaporation system[J]. Journal of North China Electric Power University, 1999, 26(4): 39-43. (in Chinese)
[3] AKIYAMA T, MATSUMOTO H, ASAKURA K. Dynamic simulation and its applications to optimum operation support for advanced combined cycle plants[J]. Energy Conversion and Management, 1997, 38(15): 1709-1723.
[4] DUMONT M N, HEYEN G. Mathematical modeling and design of an advanced once-through heat recovery steam generator[J]. Computer and Chemical Engineering, 2004, 28: 651-660.
[5] QIU Xun-jun, YANG Yu-wen. Numerical model and simulation of the heat recovery steam generator[J]. Power Engineering, 2002, 22(6): 2078-2083. (in Chinese)
[6] KUNITOMI K, KURITA A, TADA Y, et al. Modeling combined- cycle power plant for simulation of frequency excursions[J]. IEEE Transaction on Power System, 2003, 22(11): 45-58.
[7] ONG’IR A, UGURSAL V I. Modeling of heat recovery steam generator performance[J]. Applied Thermal Engineering, 1997, 17(5): 427-446.
[8] CAO Xiao-ling. The research of the drum level dynamic simulation modeling based on level sloshing[D]. Shanghai: Shanghai Jiaotong University, 2007: 20-29. (in Chinese)
[9] ZUPANCIC B. Modular hierarchical modeling with SIMCOS language[J]. Mathematic and Computers in Simulations, 1998, 46(6): 67-76.
[10] YANG Wen-bin, SU Ming. Influence of moist combustion gas on performance of a sub-critical turbine[J]. Energy Conversion and Management, 2005, 46(5): 821-832.
[11] SADOUN B. Applied system simulation: A review study[J]. Information Sciences, 2000, 124(4): 173-192.
[12] BAO Guang-wei. Equivalent mechanical model of liquid sloshing horizontal cylindrical container[J]. Journal of Shanghai Jiaotong University, 2003, 37(12): 1961-1968. (in Chinese)
[13] LIU Yi-cai, YANG Zhi-hui. Mechanism of cutoff frequency of resonator tube in thermoacoustic engine[J]. Journal of Central South University: Science and Technology, 2006, 37(4): 759-762. (in Chinese).
[14] NA M G. Auto-tuned PID controller using a model predictive control method for the steam generator water level[J]. IEEE Transactions on Nuclear Science, 2001, 48(1): 1664-1671.
[15] LING Yu-hua, CHEN Lin. Optimum water level control and realization of waste heat boiler in copper converter smelting process[J]. Journal of Central South University: Science and Technology, 2005, 36(1): 108-112. (in Chinese)
Foundation item: Project(200310) supported by Edison Research Foundation from General Electric (GE) in USA; Project(59976022) supported by the National Natural Science Foundation of ChinaReceived date: 2007-04-02; Accepted date: 2007-07-08
Corresponding author: CAO Xiao-ling, PhD; Tel: +86-13918472349; E-mail: xiaolingcao@sjtu.org
- Dynamic simulation of hydrodynamic model of drum level wave action and sloshing
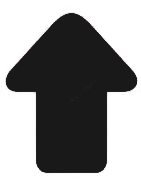