- Abstract:
- 1 Introduction▲
- 2 Experimental▲
- 3 Results and discussion ▲
- 4 Conclusions▲
- References
- Figure
- Fig.1 Effect of n(I)/n(F) on yield of UIF resin
- Fig.2 Effect of n(I)/n(F) on softening point and hydroxyl value
- Fig.3 Effect of n(A)/n(U) on yield of UIF resin
- Fig.4 Effect of n(A)/n(U) on softening point and hydroxyl value
- Fig.5 FT-IR spectrum of resin sample
- Fig.6 1H-NMR spectrum of resin sample
- Fig.7 13C-NMR spectrum of resin sample
J. Cent. South Univ. Technol. (2009) 16: 0080-0084
DOI: 10.1007/s11771-009-0013-7
One-pot synthesis and structural characterization of urea-isobutyraldehyde-formaldehyde resin
ZHANG Yi-fu(张一甫), ZENG Xing-rong(曾幸荣)
(College of Materials Science and Engineering, South China University of Technology,Guangzhou 510640, China)
Abstract:
Urea-isobutyraldehyde-formaldehyde (UIF) resin was synthesized from urea, isobutyraldehyde, and formaldehyde using sulfuric acid as a catalyst by one pot method. The effects of molar ratios of isobutyraldehyde to formaldehyde (n(I)/n(F)) and aldehyde to urea (n(A)/n(U)) on the yield, hydroxyl value (vs KOH) and softening point of the resin were investigated. The structure of the resin was characterized by FT-IR, 1H-NMR and 13C-NMR. The results show that when the molar ratio of urea to isobutyraldehyde to formaldehyde (n(U)/n(I)/n(F)) is 1.0/3.0/3.0, the yield UIF resin is 67.1%, and the softening point and hydroxyl value are 88 ℃ and 37 mg/g, respectively. The FT-IR, 1H-NMR and 13C-NMR results show that the lactam is formed by aminomethylation from urea, isobutyraldehyde, and formaldehyde.
Key words:
urea; isobutyraldehyde; formaldehyde; resin; synthesis; structural characterization;
1 Introduction
Additives are important components of coatings. They can significantly improve the manufacturing process and the quality of coatings. Polymer additives are widely used, because they can join in making films of the coatings and have no adverse influence on the properties of coatings. Cyclohexanone-formaldehyde resin is soluble in most paint solvents and compatible with most components of coatings. It can enhance the hardness, gloss and adhesion of the coatings. However, it has slightly poor thermal stability and yellowing resistance, which limits its application in the coating’s formulation. Recently, much work has been carried out to improve its thermal stability and yellowing resistance, but the problems have not been solved completely yet [1-2]. Therefore, the research and the development of new polymer additives with good thermal stability and yellowing resistance have attracted considerable attention.
Conventional amino resins are the etherified products of condensation polymer from urea or melamine with formaldehyde. There are many industrial products, such as Luwipal and Plastopal series resins of BASF, CYMEL series resins of CYTEC, and Resimene series resins of UCB. These resins have light color and excellent yellowing resistance, and have been used in the organic coatings for a long time [3-5].
PETERSEN et al [6-8] prepared amino resin from urea, isobutyraldehyde and formaldehyde, and found that the resin had not only light color and yellowing resistance, but also excellent compatibility with solvent and components of coatings. Therefore, this resin can be used as coating additives to improve the gloss, the hardness, the adhesion, and the yellowing resistance of the coatings. ZENG et al [9-10] also synthesized amino resin from urea, isobutyraldehyde and formaldehyde (UIF resin) in two-stage and studied the effect of the synthetical condition on the properties. They found that the molar ratio of urea to isobutyraldehyde to formaldehyde (n(U)/n(I)/n(F)) had a significant influence on the structure and the properties of resin in the process of synthesis. However, few researches have been done on the structure and the properties of UIF resins synthesized by one pot method.
Therefore, in this work, UIF resins were synthesized from urea, isobutyraldehyde and formaldehyde by one pot method using sulfuric acid as a catalyst. The effect of n(U)/n(I)/n(F) on the yield, hydroxyl value and softening point of the resins was discussed. And the structure of the UIF resin was characterized by FT-IR, 1H-NMR, and 13C-NMR techniques.
2 Experimental
2.1 Materials
Urea, xylene, formaldehyde aqueous solution (37%,mass fraction), and sulfuric acid (98%, mass fraction), which are of analytical grade, were purchased from Guangzhou Chemical Reagent Factory and used without further purification. Isobutyraldehyde (chemical grade) was provided by Shanghai Lingfeng Chemical Reagent Co. Ltd., and distilled before use.
2.2 Synthesis of UIF resin
Urea, isobutyraldehyde, and formaldehyde were put into a 500 mL four-necked glass flask equipped with an electric stirrer, a thermometer, a reflux condenser, and a dropping funnel. Sulfuric acid aqueous solution was added dropwise into the flask in 10 min (the mass fraction of sulfuric acid was 4%). The mixture was heated to 90 ℃ gradually, and stirred for 3 h. Then xylene was added into the flask. The aqueous phase was separated and washed 10 times with distilled water at 80℃. The xylene solution of resin was distilled at 500 Pa to remove xylene until the temperature reached 140 ℃, followed by keeping at 140 ℃ for 1 h. The pale brittle solid resin was obtained and designated as UIF resin. The reaction equations are shown as follows [11]:
(1)
(2)
2.3 Measurement and characterization
The softening point and hydroxyl value of UIF resin were determined according to ISO 4625-1:2004 and DIN 53240-2:1998, respectively.
FT-IR spectrum of the resin was recorded on a Bruker Vector 33 spectrophotometer using KBr pellets in the wavenumber interval between 4 000 and 500 cm-1.
13C-NMR and 1H-NMR spectra were recorded on a Bruker drx400 NMR spectrometer using CDCl3 as a solvent at a fixed magnetic induction of 9.4 T.
3 Results and discussion
3.1 Influence of molar ratio of isobutyraldehyde to formaldehyde
When the molar ratio of aldehyde (the total amount of isobutyraldehyde and formaldehyde) to urea (n(A)/n(U)) is 6.0, the effects of molar ratio of isobutyraldehyde to formaldehyde (n(I)/n(F)) on the yield, hydroxyl value and softening point of UIF resin are shown in Figs.1 and 2, respectively.
Fig.1 Effect of n(I)/n(F) on yield of UIF resin
Fig.2 Effect of n(I)/n(F) on softening point and hydroxyl value
As shown in Fig.1, the yield of UIF resin depends significantly on n(I)/n(F). When n(I)/n(F) is less than 1.0/1.0, the yield of UIF resin increases remarkably with the increase of n(I)/n(F). The yield reaches the maximum of 67.1% when n(I)/n(F) is 1.0/1.0. However, when n(I)/n(F) is larger than 1.0/1.0, the yield of UIF resin decreases with the increase of n(I)/n(F). During the synthesis, when n(I)/n(F) is less than 1.0/1.0, the amount of formaldehyde is more than that of isobutyraldehyde. Some of formaldehyde may react with urea to give hydroxymethyl-urea, bis-hydroxymethyl-urea, or tris- hydroxymethyl-urea. These substances are washed away in washing process, and thus the yield decreases. In addition, the reaction shown in Eqn.(3) may occur, resultant 3 with three hydroxyl groups is water-soluble to some extent, which can also be taken off to reduce the yield during washing process. In fact, when n(I)/n(F) is less than 1.0/1.0, the organic phase cannot be well separated with the water phase after the addition of xylene, and the separated water phase is ivory-white, indicating that some of resultant 3 comes into the water phase. When n(I)/n(F) is higher than 1.0/1.0, some of isobutyraldehyde may react with urea to give resultant 4 (see Eqn.(4)). Thus, urea and isobutyraldehyde are consumed and the yield decreases.
(3)
(4)
It is clear from Fig.2 that the softening point decreases and the hydroxyl value increases along with the increase of n(I)/n(F), because the possibility of reaction shown in Eqn.(4) increases when n(I)/n(F) increases. Resultant 4 with two hydroxyl groups cannot be removed completely in distillation, which leads to the increase of hydroxyl value and the decrease of softening point.
3.2 Influence of molar ratio of aldehyde to urea
When the molar ratio of isobutyraldehyde to formaldehyde (n(I)/n(F)) is 1.0/1.0, the effects of n(A)/n(U) on the yield, the hydroxyl value, and the softening point of UIF resin are shown in Figs.3 and 4, respectively.
Fig.3 Effect of n(A)/n(U) on yield of UIF resin
Fig.4 Effect of n(A)/n(U) on softening point and hydroxyl value
As shown in Fig.3, the yield of UIF resin increases remarkably with the increase of n(A)/n(U), and reaches the maximum of 67.1% when n(A)/n(U) is 6.0/1.0. When n(A)/n(U) exceeds 6.0/1.0, however, the yield decreases gradually.
When n(A)/n(U) is less than 6.0/1.0, some of resultant 1 cannot react with formaldehyde and isobutyraldehyde under acidic condition [11]. Resultant 1 with two amidogroups and one hydroxyl may be partly washed away in the washing process. However, if n(A)/n(U) exceeds 6.0/1.0, some of formaldehyde and isobutyraldehyde cannot react with urea to form resin. Therefore, the yield of resin decreases when n(A)/n(U) is not equal to 6.0/1.0.
It can be seen clearly from Fig.4 that the softening point and the hydroxyl value increase initially, and then decrease with the increase of n(A)/n(U). According to Eqn.(2), n(U)/n(I)/n(F) is about 1.0/2.0/2.0 in the molecular chains of the UIF resin. Therefore, the softening point reaches the highest value of 126 ℃ when n(A)/n(U) is 4.0/1.0 (i.e. n(U)/n(I)/n(F)=1.0/2.0/ 2.0). When n(A)/n(U) is less than 4.0/1.0, some of resultant 1 cannot react with formaldehyde and isobutyraldehyde, and thus the softening point of resin decreases. However, when n(A)/n(U) is more than 4.0/1.0, the possibility of the reaction shown in Eqn.(5) increases. Resultant 5 has no hydroxyl groups and will result in the reduction in the softening point and the hydroxyl value of resin.
(5)
In the same way, if n(A)/n(U) is too small, some of resultant 1 with one hydroxyl cannot react with isobutyraldehyde and formaldehyde to form resin. If n(A)/n(U) exceeds 6.0/1.0, the reaction shown in Eqn.(5) may occur. Therefore, the hydroxyl values firstly increase and then decrease along with the increase of n(A)/n(U).
3.3 FT-IR spectrum of UIF resin
The FT-IR spectrum of UIF resin sample (n(U)/n(I)/n(F)=1.0/3.0/3.0) is shown in Fig.5. The broad band at 3 377 cm-1 is ascribed to the stretching vibration of the O—H groups involved in the hydrogen-bonding interaction [12]. The absorption peak at 1 730 cm-1 and relatively weak peak at 2 717 cm-1 are assigned to the stretching vibration modes of the C=O and C—H bonds in aldehyde group, respectively [13], suggesting the existence of aldehyde groups in the resin structure. It is clear that the aldehyde group in the resin should be from isobutyraldehyde. The peaks at 2 964 and 2 873 cm-1 are assigned to the asymmetric and symmetric stretching vibration of C—H bonds in the methyl and methylene, while the strong bands at 1 490 and 1 446 cm-1 are ascribed to the deforming vibration of methyl and methylene, respectively, indicating that there are methyl and methylene in the structure of UIF resin. It is sure that methyl is from isobutyraldehyde. In addition, the strongest peak at 1 650 cm-1 is from urea, which is corresponding to the stretching vibration of C=O in the structure of amide groups.
Fig.5 FT-IR spectrum of resin sample
According to the FT-IR spectrum, there exist aldehyde, methyl, methylene, and carbonyl groups in the structure of resin. Therefore, it is possible that three- component aminomethylation from urea, formaldehyde, and isobutyraldehyde occurs [12], and the addition reaction between aldehyde group and hydrogen atom of amidogroup takes place to give hydroxyl group.
3.4 1H-NMR spectrum of resin
The 1H-NMR spectrum of the resin sample is shown in Fig.6. The strong resonance peaks in the chemical shift range of 0.4-1.3 are assigned to the hydrogen atoms in methyls. Methyl is also conformed in the structure of resin in Fig.6. The peaks in the chemical shift range of 2.6-3.7 are assigned to hydrogen atoms in methine and methylene connected to hydroxyl. The peaks in chemical shift range of 4.0-4.7 are ascribed to the hydrogen atoms of methylene connected to carbon and nitrogen [14]. The peaks in the chemical shift range of 4.8-5.4 are assigned to hydrogen atoms in hydroxyl [15]. The peak at chemical shift of 9.4 also confirms the existence of hydrogen atoms in aldehyde groups.
Fig.6 1H-NMR spectrum of resin sample
According to 1H-NMR results, there exist aldehyde, methyl, methylene, methine, and carbonyl groups in the structure of the resin. Furthermore, some of methylene may connect with nitrogen and carbon atom, which also supports that three-component aminomethylation from urea, formaldehyde and isobutyraldehyde takes place.
3.5 13C-NMR spectrum of resin
The 13C-NMR spectrum of the resin sample is shown in Fig.7. The resonance peak at chemical shift of 204 is assigned to carbon in aldehyde group [14]. The peak at chemical shift of 155 is due to the carbon atoms in amide groups. In general, the chemical shift of the resonance peak of carbon atom in urea is in the range of 160-164, which is slightly influenced by the substituted groups on the nitrogen [16-17]. However, the chemical shift of the resonance peak of carbon atoms in amide groups of the resin is shifted to 155, which is attributed to carbonyl of amide groups in the ring structure, indicating that the lactam is formed by aminomethylation and dehydration from urea, isobutyraldehyde, and formaldehyde [11]. The peaks in the chemical shift range of 84-87 are due to carbon atoms of methine connected with hydroxyl, and the peaks in the chemical shift range of 72-77 are assigned to carbon atoms of methylene connected with nitrogen and carbon. The peaks in the chemical shift range of 16-24 are attributed to carbon atoms of methyl. These results are in accordance with FT-IR and 1H-NMR data.
Fig.7 13C-NMR spectrum of resin sample
4 Conclusions
(1) UIF resin can be synthesized from urea, isobutyraldehyde, and formaldehyde using sulfuric acid as a catalyst by “one pot” method.
(2) n(I)/n(F) and n(A)/n(U) have a significant influence on the hydroxyl value, softening point and yield of the resin. The yield increases firstly and then decreases, the hydroxyl value increases, and the softening point decreases along with the increase of n(I)/n(F). When n(U)/n(I)/n(F) is 1.0/3.0/3.0, the yield of the resin reaches the highest value of 67.1%, and the softening point and hydroxyl value of the resin are 88 ℃ and 37 mg/g, respectively.
(3) The FT-IR, 1H-NMR and 13C-NMR results show that there are aldehyde groups and lactam groups in the structure of the UIF resins. It is suggested that aminomethylation reaction has occurred among α-hydrogen atom in isobutyraldehyde, amide hydrogen atom in urea and formaldehyde, and has cyclized further to form a lactam.
References
[1] PATRICK G, WERNER A, PETER B, HANS-PETER B, IRIS B, PETER D, MICHAEL E, THBMAS W. Ketone-aldehyde resins having low water content, high thermal stability and yellowing resistance: USA, 2005043499 [P]. 2005-02-24
[2] KIZILCAN N, AKAR A. Modification of cyclohexanone- formaldehyde resins with silicone tegomers [J]. Journal of Applied Polymer Science, 2005, 98(1): 97-101.
[3] RAMESH S, LESSEK P, HARRIS P. Coating systems containing modified crosslinkers: USA, 6812297 [P]. 2004-11-02.
[4] LING Dong, LING Ping, REN Bi-ye. Effect of methanol and butanol etherized amino resin curing agent on acrylic cathodic electrophoretic coating [J]. Material Protect, 2004, 37(9): 10-12. (in Chinese)
[5] ZHANG Xiu-mei, GUO Shu-jing. Handbook of domestic and foreign coatings resin [M]. Beijing: Chemical Industry Press, 2006: 194-256. (in Chinese)
[6] PETERSEN H, FISCHER K, KLUG H, TRIMBORM W, SCHMIDT H. Process for the manufacture of soft and hard resins of urea, formaldehyde and a CH-acidic aldehyde, and their use: USA, 4243797 [P]. 1981-01-06.
[7] PETERSEN H, IMMEL G, WEISS W, SCHMIDT H, BUSSE G. Preparation of curable etherified aminoplast resins and of surface coating resins: USA, 4621133 [P]. 1986-11-04.
[8] FISCHER K, PETERSEN H, KASCH H, SCHMIDT H. Urea-aldehyde polycondensates, preparation thereof and use thereof as surface coating binders: USA, 4906727 [P]. 1990-03-06.
[9] ZENG Xing-rong, ZHANG Yi-fu, XU Ying-bin, LING Xiao-dan, LI Peng. Preparation method of urea isobutyraldehyde formaldehyde resin: China, 1817931 [P]. 2006-08-16. (in Chinese)
[10] ZHANG Yi-fu, ZENG Xing-rong, ZHOU Ai-hua. Synthesis and characterization of urea-isobutyraldehyde-formaldehyde terploy- condensate [J]. Polymer Materials Science and Engineering, 2007, 23(6): 73-76. (in Chinese)
[11] PETERSEN H. Syntheses of cyclic ureas by a-ureidoalkylation [J]. Synthesis, 1973, 73(5): 243-292.
[12] YANG Qing, FAN Bo-lin, TANG Rui-ren. Synthesis and characterization of mibolerone [J]. Journal of Central South University of Technology, 2007, 14(4): 524-527.
[13] ZHANG Xin-ya, SUN Zhi-juan, HUANG Hong, LI Yong-jin, LAN Ren-hua, CHEN Huan-qin. Synthesis and properties of acrylate latex modified by vinyl alkoxy siloxane [J]. Journal of Central South University of Technology, 2007, 14(5): 666-672.
[14] PRETSCH E, BUHLMANN P, AFFOLTER C. Structure determination of organic compounds tables of spectral date [M]. Berlin: Springer-Verlag, 2000: 245-298.
[15] AHMAD S, ASHRAF S M, KUMAR G S. Studies on epoxy- butylated melamine formaldehyde-based anticorrosive coatings from a sustainable resource [J]. Progress in Organic Coatings, 2006, 56(2/3): 207-213.
[16] HE G, YAN N. 13C NMR study on structure, composition and curing behavior of phenol-urea-formaldehyde resole resins [J]. Polymer, 2004, 45(20): 6813-6822.
[17] TAYLOR R E, BACHER A D, DYBOWSKI C. 1H NMR relaxation in urea [J]. Journal of Molecular Structure, 2007, 846(1): 147-152.
Foundation item: Project(2006A10902001) supported by the Science and Technology Plan of Guangdong Province, China; Project(2007Z3-D0351) supported by the Science and Technology Plan of Guangzhou City, China
Received date: 2008-06-11; Accepted date: 2008-09-22
Corresponding author: ZENG Xing-rong, Professor; Tel: +86-20-87114248; E-mail: psxrzeng@scut.edu.cn
(Edited by CHEN Wei-ping)
- One-pot synthesis and structural characterization of urea-isobutyraldehyde-formaldehyde resin
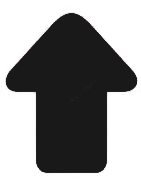