- Abstract:
- 1 Introduction▲
- 2 Different structure for...▲
- 3 Cutting experiments▲
- 4 Conclusions▲
- References
- Figure
- Fig.1 Different structure forms of rock seams: (a) Hard-soft- hard; (b) Soft-hard; (c) Soft-hard-soft
- Fig.2 Structure of helical cutting mechanism
- Fig.3 Motion of helical cutting machanism
- Fig.4 Modes of HCM cutting hard-soft-hard rock seam: (a) Bottom cutting hard rock; (b) Top cutting hard rock; (c) Bottom and top cutting hard rock
- Fig.5 Cutting loads of HCM cutting hard-soft-hard rock seam: (a) Bottom cutting hard rock; (b) Top cutting hard rock; (c) Bottom and top cutting hard rock
- Fig.6 Cutting torques of soft-hard rock seams with different compressive strengths of hard rock: (a) 1.43 MPa; (b) 1.97 MPa; (c) 2.48 MPa
- Fig.7 Relationship between cutting torque increment and compressive strength increment
- Fig.8 HCM cutting soft-hard-soft rock seams with different thicknesses of hard rock: (a) 60 mm; (b) 120 mm; (c) 180 mm
- Fig.9 Cutting loads of different soft- hard-soft rock seams with different thicknesses of hard rock: (a) 60 mm; (b) 120 mm; (c) 180 mm
- Fig.10 Relationship between torque increment and ξ
J. Cent. South Univ. Technol. (2011) 18: 1518-1524
DOI: 10.1007/s11771-011-0868-2
Characteristics of different rocks cut by helical cutting mechanism
LIU Song-yong(刘送永), DU Chang-long(杜长龙), CUI Xin-xia(崔新霞), GAO Kui-dong(高魁东)
College of Mechanical and Electrical Engineering, China University of Mining and Technology,Xuzhou 221116, China
? Central South University Press and Springer-Verlag Berlin Heidelberg 2011
Abstract:
To research the loading characteristic of rocks with different structures cut by helical cutting mechanism (HCM), three different structures of rock (hard-soft-hard rock, soft-hard rock and soft-hard-soft rock) were built. And each type model was further divided into three types when the experiments were carried out. To reduce the errors of cutting load caused by manually configured rock in each test, the cutting load of soft rock was taken as a benchmark, and the differences of the cutting load of the different structures of rocks and the soft rock were used to reflect the cutting load change rules of the HCM. The results indicate that, the cutting load of only the HCM top cutting hard rock is larger than that of only the HCM bottom cutting hard rock for dextral HCM, and the cutting load fluctuation is larger, too. However, when the top and the bottom of the HCM cutting hard rock simultaneously, its cutting load is the largest, but the cutting load fluctuation is the least. And the HCM cutting load increment is increased linearly with the increase of rock compressive strength. The HCM cutting load increment is increased exponentially with the increase of hard rock cutting thickness.
Key words:
helical cutting mechanism; rock model; cutting load; load fluctuation; compressive strength;
1 Introduction
Helical cutting mechanism (HCM) was widely used in mining, road construction engineering etc, such as shearer drum, roadheader cut head, cobalt-crust mining head and milling drum. And the cutting performance of the HCM directly influences the efficiency and reliability of the machine. The influence of the HCM structure parameters on the rock breaking effect was researched [1], and the neural network model among rock breaking effect and pick distance, cutting thickness was built. The relationships among the HCM cutting specific energy consumption, the respirable dust and the relevant parameters were researched [2], which indicated that the cutting specific energy consumption and respirable dust were correlated with the pick geometry, pick arrangement, haulage speed and drum rotary speed. The relationship between the HCM cutting specific energy consumption and pick geometry was studied [3], and five different pick types installed on the drums were utilized in cutting experiment. The influence of the HCM vane wrap angle on the HCM cutting performance was studied [4], which indicated that the cutting force would be increased and the cutting performance would be decreased if the wrap angle was increased. The influence of pick arrangement of HCM on the cutting performance was researched [5], illustrating that there was no difference on the cutting force when the pick circumference was arranged with equal angle or varied angle. The process of the HCM cutting rock was researched [6], in which the nonlinear finite element software, LS-DYNA, was utilized, and the results indicated that the parameters (cutting speed, pick geometry, pick tip size, pick line space) produced very large effect on the HCM impact force, and the shear failure was the main form of rock breaking. The maximum distribution characteristics of HCM were got [7-8], through building the statistics model and cutting load model based on the virtual prototyping technology, simulation and experiment. The different-structure HCMs were studied [9-10], which indicated that the cutting performance of the globoid and the hob HCM was all better than that of the cylindrical HCM. The cutting experiments with different-structure rocks were done [11-13], which indicated the cutting performance of the pick was affected mainly by the rock compressive strength, and explained basic rules governing the relationships between specific energy and chip sizes. The influence of HCM types on the cutting effect was researched, and the relationship between the heat produced by cutting rock and cutting parameters was built [14]. The cutting performance of different HCM pick arrangements was researched [15], which indicated that the aberrance form pick arrangement had the best cutting performance when the same rock was cut. The simulation and analysis of the HCM cutting graph was carried out [16], which established the basis for improving the design method and cutting performance of the HCM.
According to the above analysis, we can know that a lot of research works about structure parameters and kinematic parameters of the HCM have been done, and many useful results have been obtained. But sometimes, the cutting object is not a uniform rock with the same characteristics, and the structure forms of rock seams are different. So, to master the cutting characteristics and the cutting load change rule to improve the adaptability and reliability of the HCM, experiments are done in this work.
2 Different structure forms of rock seams
To research the load change rule and the desired HCM structure parameters when different structure forms of rocks were cut, three different structure forms of rock seams were built according to the relative form of soft rock and hard rock in site, based on the similarity theory and referred to the method of manufacturing analog rock seam in Ref.[17], and the similitude ratio was 1/3. The structure forms of rock seams are shown in Fig.1. Figure 1(a) shows the hard-soft-hard rock seam in the horizontal direction, Fig.1(b) shows the soft-hard-soft rock seam in the horizontal direction, and Fig.1(c) shows the soft-hard rock seam in the vertical direction.
3 Cutting experiments
The HCM used in experiment is shown in Fig.2, and its motion mode is shown in Fig.3. HCM structure and kinematic parameters are as follows: diameter (D) of 530 mm, helical angle (θ) of 20°, pick impact angle (α) of 45°, cutting line space (t) of 30 mm, cutting depth (d) of 210 mm, rotary speed (n) of 80 r/min and haulage speed (v) of 1.5 m/min. To decrease the errors caused by manually configured rock seams and research the change rules when different structure rock seams were cut, the relative value method was utilized. That was to say, the cutting load of the same soft-rock was set as a benchmark, and the difference of the cutting load of other rock seams was used to show the change rules of cutting load.
3.1 Hard-soft-hard rock seams
To research the load characteristics when only the HCM top or bottom cutting different rocks and the HCM top and bottom cutting different rocks simultaneously, three rock seams with different structure forms were built, as shown in Fig.4. The cutting thicknesses of hard rock in three different rock seams were all 60 mm, the compressive strengths of soft rock were all 0.73 MPa, and the compressive strengths of hard rock were all 1.97 MPa. The experiments were done on the cutting test-bed for rock and coal [17]. The loads under different conditions are shown in Fig.5.
Fig.1 Different structure forms of rock seams: (a) Hard-soft- hard; (b) Soft-hard; (c) Soft-hard-soft
Fig.2 Structure of helical cutting mechanism
Fig.3 Motion of helical cutting machanism
Fig.4 Modes of HCM cutting hard-soft-hard rock seam: (a) Bottom cutting hard rock; (b) Top cutting hard rock; (c) Bottom and top cutting hard rock
The cutting load was analyzed under three different conditions and the results are listed in Table 1. The torque increment was the difference value of the cutting torque of the HCM part cutting hard rock and that of the whole HCM cutting soft rock. And the cutting torque of the HCM cutting hard rock includes three parts: only the HCM top cutting hard rock, only the HCM bottom cutting hard rock and the HCM top and bottom cutting hard rock simultaneously.
It can be seen in Table 1 that the mean and standard deviations of the cutting torque of only the HCM top cutting hard rock are all larger than the values of only the HCM bottom cutting hard rock. The mean cutting torque of the HCM bottom and top cutting hard rock simultaneously is larger than that of only the HCM top or bottom cutting hard rock, but the standard deviation of the HCM bottom and top cutting hard rock simultaneously is smaller than that of only the HCM top cutting hard rock, namely the load fluctuations of the HCM bottom and top cutting hard rock simultaneously and only the HCM bottom cutting hard rock are smaller than that of only the HCM top cutting hard rock. This is because the HCM bottom and top bear basically the same load when the HCM bottom and top cutting hard rock simultaneously, and the HCM top load is in balance with the HCM bottom load, which makes the load fluctuation decrease. And the difference value of the HCM bottom and top cutting hard rock simultaneously is not twice the difference value of only the HCM bottom or top cutting hard rock. At the same time, it can be seen in Fig.5 that the cutting torque change rate of only the HCM bottom cutting hard rock is smaller than the other two cutting forms, which illustrates that the impact force when only the HCM bottom cutting hard rock is smaller than that of the others.
Fig.5 Cutting loads of HCM cutting hard-soft-hard rock seam: (a) Bottom cutting hard rock; (b) Top cutting hard rock; (c) Bottom and top cutting hard rock
Table 1 Cutting torque statistics for roof and floor
3.2 Soft-hard rock seams
To research the cutting load characteristics of the HCM cutting soft-hard rock seams, three soft-hard rock seams were manufactured. The structures of them were the same as Fig.1(c). The soft rock seam compressive strength was 0.73 MPa, and the compressive strengths of the three hard rock seams were 1.43 MPa, 1.97 MPa and 2.48 MPa, respectively. The cutting load was got by cutting experiment on the cutting test-bed for rock and coal, as shown in Fig.6.
It can be seen from Fig.6 that the HCM cutting torque increases with increasing the cut width of hard rock seam until loading smoothly. And the transition time and load fluctuation are all increased with increasing the compressive strength of hard rock seams. To obtain the relationship between the cutting load and the compressive strength increment, the experimental values were calculated statistically, as listed in Table 2.
Fig.6 Cutting torques of soft-hard rock seams with different compressive strengths of hard rock: (a) 1.43 MPa; (b) 1.97 MPa; (c) 2.48 MPa
Table 2 Cutting torques of different soft-hard rock seams
The results indicate that the difference value of the HCM cutting torque increment increases with the increase of the difference value between compressive strength of hard rock and soft rock, but the difference values of cutting torque increment are the same basically. To research the relationship between the cutting torque increment and the difference value of compressive strength, the experiment data in Table 2 are analyzed, and the relationship is shown in Fig.7. It can be seen that the cutting torque increment increases with the difference value increase of the compressive strength between hard rock and soft rock in the range of experiments, and the difference values of cutting torque increment are increased gradually with the difference value of the compressive strength between hard rock and soft rock.
Fig.7 Relationship between cutting torque increment and compressive strength increment
3.3 Soft-hard-soft rock seam
To research the load characteristics of the HCM cutting soft-hard-soft rock seam, three analogy soft-hard- soft rock seams were manufactured, as shown in Fig.8. The compressive strength cutting soft rock seam was 0.73 MPa, and the compressive strength cutting hard rock seam was 1.97 MPa. The experiment was done on the cutting test-bed for rock and coal, and the loads are shown in Fig.9.
It can be seen from Fig.9 that the cutting torque increases as the hard rock thickness increases, and the transition time and the load fluctuation increase, too. To research the relationship between the hard rock seam thickness and the HCM cutting torque increment, the experiment values were analyzed, and the results are listed in Table 3.
Fig.8 HCM cutting soft-hard-soft rock seams with different thicknesses of hard rock: (a) 60 mm; (b) 120 mm; (c) 180 mm
Fig.9 Cutting loads of different soft- hard-soft rock seams with different thicknesses of hard rock: (a) 60 mm; (b) 120 mm; (c) 180 mm
Table 3 Statistics of cutting torque of coal seam with gangue
To obtain the relationship between the cutting torque increment and the hard rock thickness, the ratio ξ of the hard rock thickness to the HCM diameter was set as a variable, and the torque increment was utilized when the compressive strength of the hard rock was 1.97 MPa in Table 2. The relationship between them is shown in Fig.10, The result indicates that the cutting torque increment varies exponentially with the hard rock thickness in the range of the experiments, but the difference value between the cutting torque increment is decreased gradually with the hard rock thickness. And the cutting torque increment will have no change when ξ is greater than or equal to 1.
Fig.10 Relationship between torque increment and ξ
4 Conclusions
1) Under the condition of the HCM cutting the hard-soft-hard rock seams, the load fluctuation and mean load of only the HCM top cutting the hard rock are all larger than the values of only the HCM bottom cutting the hard rock, and the load fluctuation of the HCM top and bottom cutting hard rock simultaneously is smaller than the value of only HCM top cutting hard rock, but the mean load of the HCM top and bottom cutting hard rock is larger.
2) Under the condition of the HCM cutting the soft-hard rock in the vertical direction, the HCM cutting load increment varies linearly with the difference value of compressive strength between hard rock and soft rock, and the increment increases gradually in the range of the experiments. Under the condition of the HCM cutting the soft-hard-soft rock seams, the HCM cutting load increment varies exponentially as the hard rock thickness increases, but the increment decreases gradually in the range of the experiments.
3) According to the cutting load of different working conditions, when the other parameters are invariable, the design cutting power of the HCM bottom and top cutting hard rock simultaneously should be larger than that of only the HCM bottom or top cutting hard rock. And the design cutting power should be increased linearly and exponentially with the increase of the rock compressive strength and the hard rock thickness, so as to chieve better cutting efficiency.
References
[1] MAZURKIEWICZ D. Empirical and analytical models of cutting process of rock [J]. Journal of Mining Science, 2000, 36(5): 481-486.
[2] VENKATARAMAN M. Effect of rate of sumping on fragmentation process in laboratory rotary cutting simulator [D]. West Virginia: College of Mineral and Energy Resources, West Virginia University. 2003.
[3] QAYYUM R A. Effects of bit geometry in multiple bit rock interaction [D]. West Virginia: College of Engineering and Mineral Resources, West Virginia University. 2003.
[4] HEKIMOGLY O Z, OZDEMIR L. Effect of angle of wrap on cutting performance of drum shearers and continuous miners [J]. Transactions of the Institutions of Mining and Metallurgy, 2004, 113(2): 118-122.
[5] EYYUBOGLU E M, BOLUKBASI N. Effects of circumferential pick spacing on boom type roadheader cutting head performance [J]. Tunneling and Underground Space Technology, 2005, 20(5): 418-425.
[6] BO Yu. Numerical simulation of continuous miner rock cutting process [D]. West Virginia: College of Engineering and Mineral Resources, West Virginia University. 2005.
[7] XIA Yi-min, BU Ying-yong, MA Zhi-guo, ZHAO Hai-ming, LUO Bo-wen. Modeling and simulation of ocean mining subsystem based on virtual prototyping technology [J]. Journal of Central South University of Technology, 2005, 12(2): 176-180.
[8] XIA Yi-min, NIE Si-jun, BU Ying-yong, ZHAO Hai-ming. Distribution properties of cutting tooth’s maximum load of spiral mining head for cobalt-crust [J]. Journal of Central South University: Science and Technology, 2007, 38(3): 512-516. (in Chinese)
[9] AYHAN M, EYYUBOGLU E M. Comparison of globoid and cylindrical shearer drums’ loading performance [J]. The Journal of South African Institute of Mining and Metallurgy, 2006, 106(1): 51-56.
[10] LIU Song-yong, DU Chang-long, CUI Xin-xia, SONG Jing. Experiment research on a new shearer drum [J]. Procedia Earth and Planetary Science, 2009(1): 1393-1397.
[11] BILGIN N, DEMIRCM M A, COPUR H, BALCIA C, TUNCDEMIRA H, AKCIN N. Dominant rock properties affecting the performance of conical picks and the comparison of some experimental and theoretical results [J]. International Journal of Rock Mechanics & Mining Sciences, 2006, 43(1): 139-156.
[12] BALCI C, BILGIN N. Correlative study of linear small and full-scale rock cutting tests to select mechanized excavation machines [J]. International Journal of Rock Mechanics & Mining Sciences, 2007, 44(3): 468-476.
[13] TUNCDEMIR H., BILGIN N, COPUR H, BALCI C. Control of rock cutting efficiency by muck size [J]. International Journal of Rock Mechanics & Mining Sciences, 2008, 45(2): 278-288.
[14] MISHRA B. Analysis of cutting parameters and heat generation on bits of a continuous miner–using numerical and experimental approach [D]. West Virginia: College of Engineering and Mineral Resources, West Virginia University. 2007.
[15] DU Chang-long, LIU Song-yong, CUI Xin-xia, LI Ti-jian. Study on pick arrangement of shearer drum based on load fluctuation [J]. Journal of China University of Mining & Technology, 2008, 18(2): 305-310.
[16] LI Xiao-huo, SONG Bo, WANG Dan, LIN Qi-yue. Design and Simulation study of man-machine contact surface system for grooving section pattern of horizontal cutting head [J]. Journal of Liaoning University of Technology: Natural Science Edition, 2009, 29(6): 392-395. (in Chinese)
[17] LIU Song-yong, DU Chang-long, CUI Xin-xia. Experimental research on picks arrangement of shearer drum [J]. Journal of Central South University: Science and Technology, 2009, 40(5): 1281-1287. (in Chinese)
(Edited by YANG Bing)
Foundation item: Project(51005232) supported by the National Natural Science Foundation of China; Project(20100481176) supported by the China Postdoctoral Science Foundation
Received date: 2010-09-09; Accepted date: 2010-12-31
Corresponding author: LIU Song-yong, PhD; Tel: +86-13912033086; E-mail: liusongyong@cumt.edu.cn
- Characteristics of different rocks cut by helical cutting mechanism
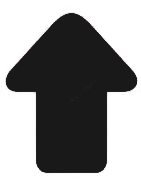