- Abstract:
- 1 Introduction▲
- 2 Experimental▲
- 3 Results and discussion▲
- 4 Conclusions▲
- References
- Figure
- Fig.1 Flow sheet of iron oxide prepared from pyrite cinders by hydrothermal method
- Fig.2 XRD pattern of hydrothermal product prepared with optimal experimental parameters
- Fig.3 SEM image of hydrothermal product prepared with optimal experimental parameters
- Fig.4 TEM images of hydrothermal product prepared with optimal experimental parameters (Inset: SAED pattern of individual hexagonal iron oxide flake)
J. Cent. South Univ. Technol. (2011) 18: 89-95
DOI: 10.1007/s11771-011-0664-z
Micaceous iron oxide prepared from pyrite cinders by hydrothermal method
LIU Zhao-cheng(刘昭成), ZHENG Ya-jie(郑雅杰)
School of Metallurgical Science and Engineering, Central South University, Changsha 410083, China
? Central South University Press and Springer-Verlag Berlin Heidelberg 2011
Abstract:
Micaceous iron oxide (MIO) with a hexagonal flaky shape was prepared by hydrothermal method. The ferric hydroxide used as precursor was obtained by an acidic leaching solution of pyrite cinders reacting with ammonia solution. The optimal experimental conditions for preparing micaceous iron oxide were investigated by orthogonal experiments. Micaceous iron oxide can be successfully prepared when optimal parameters of total iron concentration of 2.0 mol/L, pH value of 8, n(Fe2+)/n(Fe3+) of 0.1, mass of seed crystal of 1 g, reaction temperature of 260 °C and reaction time of 30 min are applied. X-ray diffractometry (XRD), scanning electron microscopy (SEM), transmission electron microscopy (TEM) and selected area electron diffractometry (SAEM) were adopted to characterize the hydrothermal products prepared under optimal conditions. The results indicate that highly crystallized α-Fe2O3 hexagonal flakes, about 1.0-1.5 ?m in diameter and 0.1 ?m in thickness, are prepared. Furthermore, the quality of micaceous iron oxide prepared can meet the required characteristics of micaceous iron oxide pigments for paints (ISO10601—2007).
Key words:
micaceous iron oxide; hydrothermal method; hexagonal flake; pyrite cinders; ferric hydroxide;
1 Introduction
Micaceous iron oxide (MIO), consisting of pure or doped hematite (α-Fe2O3), is found already in nature in form of platelets. This natural product with a density of 4.6-4.8 g/cm3 and a dark gray color of low luster is nearly exclusively used in corrosion protection coatings. Practical experience and published literatures concerning the application of MIO pigments to coatings destined to metal protection show outstanding results [1-3]. The anticorrosive coatings with MIO pigment show excellent barrier properties. They hinder the permeation of corrosive substances and water through the film, increase the adhesion of coating to the substrate, and the particles also protect the binder against UV radiation [4-5]. Due to the fact that the physical properties of MIO change significantly depending on the grain size, and that the shape and size of natural MIO are usually nonuniform, it is highly necessary to prepare monodispersed MIO particles with uniform size and shape.
Pyrite cinders as solid wastes are produced as by-products of industrial sulphuric acid manufacturing operations which are composed mainly of iron oxides (e.g. hematite (Fe2O3) in particular). Furthermore, pyrite cinders often contain hazardous heavy metals with potential environmental risks for disposal [6] and these impurities prevent their use in the production of pig iron [7]. In consideration of the environmental protection, treatment costs and limited availability of landfill/ disposal sites, searching new and cost-effective methods for the management of pyrite cinders as wastes has become increasingly important in recent years. The utilization of pyrite cinders as substitute for natural resources for the production of value-added products appears to be the propitious option. Several areas for utilization of pyrite cinders were reported, including the brick production as colouring material, the paint industry as pigment [8] and the cement production as additives [9]. The potential use of pyrite cinders in place of scrap iron in the production of iron-based products is one of the most promising methods. Many researchers have developed iron-based products by pyrite cinders [10]. ZHANG et al [11] reported their studies on the preparation of yellow iron oxide and red iron oxide with pyrite cinder. The preparations of blue potassium iron, ferric oxide and polymeric ferric sulfate from pyrite cinders were studied by ZHENG et al [12-14]. While YANG et al [15] reported the preparation of magnetite for electrostatic copying toner from pyrite cinders. However, there is less research on the micaceous iron oxide prepared from pyrite cinders. The value-added product of micaceous iron oxide is prepared from pyrite cinders, which not only can increase economic returns, but also pioneer a new way for the comprehensive utilization of pyrite cinders.
In the present study, micaceous iron oxide with uniform particles was prepared from an acidic leaching solution of pyrite cinders by hydrothermal method via an ammonia process as the precipitant. The optimal conditions for preparing micaceous iron oxide were investigated by orthogonal experiments based on our previous report [8].
2 Experimental
2.1 Materials and reagents
Analytically pure H2SO4, H2O2 and NH3·H2O (Tianjin Kaitong Chemical Co., China) were used as reagents without further purification. Ultrafine iron oxide particles (Hunan Three-ring Pigment Co., China), with uniformity in spherical shape and approximately 0.3 ?m in diameter, were used as seed crystal for hydrothermal reaction. The pyrite cinders used as raw materials for iron source in the experiment were obtained from Guangdong Pyrite Mine Corporation, Guangdong Province, China. Its chemical composition was examined by X-ray fluorescence spectroscopy (XRF), and the results are presented in Table 1.
Table 1 Chemical composition of investigated pyrite cinders by XRF (mass fraction, %)
The pyrite cinders mainly consist of 58.15% Fe, 1.951% S, 5.545% Si, 1.04% Ca and 1.62% Al (mass fraction), as listed in Table 1. The mixture of ferric and ferrous sulfates was prepared from pyrite cinders through sulfuric acid leaching process according to the report of ZHENG and FU [14]. In detail, 6.5 L 50% sulfuric acid solution, obtained by diluting 98% sulfuric acid in deionized water, was added to a three-necked flask (10 L in volume). Then, 3 kg pyrite cinders were gradually added into the 50% sulfuric acid solution under vigorous stirring. The leaching temperature was controlled at 115 °C by an electric heating jacket, and kept for 4 h. After filtration, the leached solution was diluted to 9.0 L with deionized water, which was mainly composed of the mixture of ferric and ferrous sulfates (Table 2) and contained trace impurity elements such as Al, Mg and Ca. The as-prepared acid-leached solution was used as the starting material to prepare micaceous iron oxide.
2.2 Procedure
The typical procedure used to prepare iron oxide particles from the acid-leached solution of pyrite cinders is summarized in Fig.1. It was reported that a small
Table 2 Chemical composition of acid-leached solution of pyrite cinders (g/L)
Fig.1 Flow sheet of iron oxide prepared from pyrite cinders by hydrothermal method
amount of Fe2+ could catalyze the formation of hematite [16]. In the first step, hydrogen peroxide solution was added dropwise into the prepared filtrate in order to regulate ferrous concentration of acid-leached solution under vigorous stirring. Then, ammonia solution (25%, mass fraction) was added into 200 mL iron solution dropwise to a desired pH value. After that, some amount of ultrafine hematite seed crystals was added into the solution which was sequentially diluted to 400 mL with deionized water. Then, it was transferred to a pressure-resistant autoclave (SUS316, 0.5 L) with a mechanical stirrer for hydrothermal reaction. During the reaction period, the suspensions were agitated at a rate of 300 r/min. The reaction was performed at different temperatures for a given time. The reactor was quenched quickly by cooling water flowing through the internal pipes when the experiments finished. Finally, the resulting precipitate was taken out of the reactor to be filtered, and rinsed with deionized water. The products were dried at 105 °C for 12 h, and (NH4)2SO4 was reclaimed by evaporation crystallization process.
2.3 Analytical methods
Chemical analysis of the liquids and solids was performed to examine the ferrous and ferric ion content and the content of Fe2O3 by a titration method according to GB1863—2008 (China Industrial Standard), respectively. The results were the mean values of the two experiments using the same sample. The oil absorption of hydrothermal products was measured according to GB1863—2008. The color assessment of hydrothermal products based on GB9285—88 was performed by comparison with the standard sample from Hunan Three-ring Pigment Co., China (Poor: 0-30; Somewhat: 30-60; Slight: 60-80; Close: 80-100). X-ray diffraction (Rigaku, D/max-rA) with Cu Kα (λ=1.541 78 nm) radiation was used to check the formation and to identify the compositions of the obtained particles. 2θ scanning scope was from 10.0° to 70.0° with a step of 0.01 (°)/s. TEM images were recorded on a Hitachi Model H-800 transmission electron microscope at an accelerating voltage of 200 kV. The samples were dispersed in absolute ethanol in an ultrasonic bath. Then, a drop of suspension was put onto a copper grid and dried naturally. Selected area electron diffraction (SAED) was further performed to identify the crystallinity. The mean particle size and surface morphology of the typical particles were observed with a scanning electron microscope (SEM, JSM-6360LV, JEOL, Ltd., Tokyo, Japan).
3 Results and discussion
3.1 Orthogonal experiments
Iron oxide red-pigments have been successfully prepared from pyrite cinders by hydrothermal method [8]. The investigation of single factor indicates that the optimal parameters for preparing iron oxide red-pigments are total iron concentration of 2.0 mol/L, n(Fe2+)/n(Fe3+) of 0.11, reaction temperature of 200 ?C, reaction time of 30 min, and pH value of 8. The orthogonal experiments were carried out to optimize the conditions of hydrothermal process in order to obtain high-quality iron oxide red-pigments. The content of Fe2O3, oil absorption and color tone are the most important factors that influence the performance of iron oxide red-pigments. The effects of n(Fe2+)/n(Fe3+), mass of seed crystal, total iron concentration, reaction temperature, reaction time and reaction pH value were investigated by orthogonal experiment. The factor level of the orthogonal experiment is shown in Table 3.
Table 4 shows the results of orthogonal experiments and range analysis. As shown in Table 4, the effect significance sequences of factors on the content of Fe2O3, oil absorption and color of iron oxide are DABECF, DEFCAB and ADEBCF, respectively. The better level combination for the former two is A3B2C4D5E3F5, while the better level combination for the later is A3B5C3D5E4F3. Experiments were carried out according to the results of orthogonal experimental analysis and the results gained were compared with the result of the eleventh experiment of orthogonal experiments.
The results of better experimental combination are shown in Table 5. The contents of Fe2O3 of combination A3B2C4D5E3F5, A3B5C3D5E4F3 and the eleventh experiment A3B1C3D5E2F4 are very close, which are 98.19%, 97.91% and 98.54%, respectively. The oil absorption among them shows similar result. However, the apparent color of the eleventh experiment is the best among the three while the color of combination A3B2C4D5E3F5 and A3B5C3D5E4F3 is only 90, which indicates the quality of iron oxide obtained at the level combination A3B1C3D5E2F4 is excellent. From the orthogonal experiments, it can be concluded that the n(Fe2+)/n(Fe3+) (factor A) and reaction temperature (factor D) are the leading factors influencing the results. n(Fe2+)/n(Fe3+) has an obvious effect on the formation of hematite. The hematite prepared at n(Fe2+)/n(Fe3+) of 0 shows a serious phenomenon of agglomeration among the particles, and when n(Fe2+)/n(Fe3+) is 0.1, the obtained hematite particles give an excellent dispersion property. This is because Fe2+ can catalyze the transformation from Fe(OH)3 to hematite and accelerate Fe(OH)3 dehydration to form the primary particles of hematite and then to grow into hematite particles [17]. While n(Fe2+)/n(Fe3+) is more than 0.1, the appearance of the prepared hematite presents dark red because of the formation of Fe3O4 phases. Besides, high reaction temperature can also accelerate the transformation from Fe(OH)3 to hematite. Thus, the optimal experimental parameters for preparing iron oxide are total iron concentration of 2.0 mol/L, n(Fe2+)/n(Fe3+) of 0.1, reaction temperature of 260 ?C, reaction time of 30 min, and pH value of 8.
Table 3 Factor levels of orthogonal experiment
Table 4 Results of orthogonal experiments and range analysis
Table 5 Results of better experimental combinations
3.2 Structure identification of prepared iron oxide by hydrothermal method
Fig.2 shows the XRD pattern of the resulting product hydrothermally synthesized at 260 °C for 30 min, under the conditions of n(Fe2+)/n(Fe3+), mass of seed crystal, total iron concentration and reaction pH value of 0.1, 1 g, 2.0 mol/L and 8, respectively. The XRD pattern can be finely indexed to the rhombohedra phase [space group: R-3c (167)] of α-Fe2O3, and its cell parameters are a=5.036 ?, b=5.036 ?, c=13.749 ? (JCPDS file Card, No.33-0664). Moreover, no impurity peaks are observed, indicating that hematite (α-Fe2O3) is successfully synthesized under the optimal experimental conditions.
Fig.2 XRD pattern of hydrothermal product prepared with optimal experimental parameters
Fig.3 shows the morphology of hydrothermal product prepared with the optimal experimental parameters. It can be seen from Fig.3 that the synthesized hematite (α-Fe2O3) is in the shape of hexagonal flakes with a diameter of 1.0-1.5 mm and a thickness of around 0.1 ?m, giving an aspect ratio of 10-15. With careful observation, the hexagonal iron oxide flakes appear to be quite loose, which reveals that the synthesized hematite has an excellent dispersion property.
Fig.4(a) shows the transmission electron microscope image of a typical sample of hexagonal iron oxide flakes obtained with the optimal experimental parameters. This further reveals that the iron oxide particles with a good uniformity in size could be successfully prepared by this approach. Fig.4(b) shows
Fig.3 SEM image of hydrothermal product prepared with optimal experimental parameters
Fig.4 TEM images of hydrothermal product prepared with optimal experimental parameters (Inset: SAED pattern of individual hexagonal iron oxide flake)
the image of an individual hexagonal iron oxide flake. Herein, the iron oxide flake with a regular hexagonal shape can be clearly observed. The inset of Fig.4(b) showing a selected electron diffraction pattern of an individual hexagonal iron oxide flake reveals the satisfactory crystallinity of the sample, which can be indexed to rhombohedra phase of hematite (α-Fe2O3) and exhibits that each iron oxide flake is a single crystal. With respect to the growth mechanism for iron oxide flakes, metal ions exert a very important role in morphology modification. Since, in the current experiments, the acidic-leached solution of pyrite cinders contains a few metal ions, in particular, there is a relatively large amount of aluminum ions. CAO et al [18] pointed out that aluminium ion substitution has a significant effect on the morphological change of hematite. They have prepared discoid hematite particles by a catalytic phase transformation method using co-precipitates of Fe3+ and Al3+ as precursors. SCHWERTMANN et al [19] also demonstrated that Al substitution promoted the anisotropic growth of hematite particles in the c crystal direction in the iron and aluminum nitrate systems, although they found that increasing substitution actually retarded the crystal growth along the c axis, and their work involved more dilute solutions. So, the characteristic shape of the hexagonal flakes is formed due to stronger adsorption of Al3+ to the
and
planes is relatively fast, resulting in a flaky shape. The iron oxide flakes with regular hexagonal structure are formed primarily because of the lack of preferred growth direction in the recrystallization step. Chemical compositions of the hydrothermal products prepared with optimal experimental parameters were investigated by X-ray fluorescence spectroscopy (XRF). The results (Table 6) show that the Fe2O3 content of hydrothermal product is 98.54%, and a few contamination compounds are detected. This indicates that some metal ions have incorporated the internal structure of iron oxide flakes.
Table 6 Chemical composition of hydrothermal product synthesized with optimal experimental parameters (mass fraction, %)
3.3 Quality of micaceous iron oxide prepared by hydrothermal method
The quality of micaceous iron oxide prepared with optimal experimental parameters by hydrothermal method is presented in Table 7. As can be seen from Table 7, the quality of the prepared micaceous iron oxide can meet the required characteristics of micaceous iron oxide pigments for paints, ISO10601—2007 (Inter- national Standard). Therefore, micaceous iron oxide could be successfully prepared from pyrite cinders by hydrothermal method.
Table 7 Quality of micaceous iron oxide prepared from pyrite cinders by hydrothermal method
4 Conclusions
1) The preparation of micaceous iron oxide from pyrite cinders was investigated by orthogonal experiments. The n(Fe2+)/n(Fe3+) and reaction temperature are leading factors influencing the preparation of iron oxide. The optimal parameters for preparing micaceous iron oxide are total iron concentration of 2.0 mol/L, pH value of 8, n(Fe2+)/ n(Fe3+) of 0.1, mass of seed crystal of 1 g, reaction temperature of 260 °C and reaction time of 30 min. Fe2+ takes the catalytic action during the formation of hematite particles, accelerating the transformation from Fe(OH)3 to hematite.
2) Typical hexagonal iron oxide flakes, about 1.0-1.5 ?m in diameter and 0.1 ?m in thickness, are prepared under the optimal experimental conditions by hydrothermal method. Aluminium ion of acidic-leached solution is responsible for the formation of iron oxide flakes in the hydrothermal process.
3) The Fe2O3 content of micaceous iron oxide obtained under the optimal experimental conditions is 98.54%, and the prepared micaceous iron oxide can meet the required characteristics of micaceous iron oxide pigments for paints (ISO10601—2007).
References
[1] KAZUAKI A, SOICHIO N, TAKASHI A. Method for manufacture of iron oxide flakes: US, 4233283 [P]. 1980-11-11.
[2] FRAND G, HUND F. Production of lamellar iron oxide pigments: US, 4404254 [P]. 1983-09-13.
[3] GIUDICE C A, BENITEZ J C. Optimising the corrosion protective abilities of lamellar micaceous iron oxide containing primers [J]. Anti-corrosion Methods and Materials, 2000, 47(4): 226-232.
[4] KALENDA P, KALENDOVA A, STENGL V, ANTOS P, SUBRT J, KVACA Z, BAKARDJIEVA S. Properties of surface-treated mica in anticorrosive coatings [J]. Progress in Organic Coatings, 2004, 49(2): 137-145.
[5] SORENSEN P A, KIIL S, DAM-JOHANSEN K, WEINELL C E. Anticorrosive coatings: A review [J]. Journal of Coating Technology and Research, 2009, 6(2): 135-176.
[6] GIUNTI M, BARONI D, BACCI E. Hazard assessment to workers of trace metal content in pyrite cinders [J]. Bulletin of Environmental Contamination and Toxicology, 2004, 72(2): 352-357.
[7] TUGRUL N, DERUN E M, PISKIN M. Utilization of pyrite ash wastes by pelletization process [J]. Powder Technology, 2007, 176(2): 72-76.
[8] LIU Zhao-cheng, ZHENG Ya-jie. Preparation of iron oxide red powders from pyrite cinders by hydrothermal method [C]// EPD Congress 2009 Proceedings. Warrendale, PA: The Minerals, Metals & Materials Society, 2009:943-947.
[9] AIL I, DEVECI H, YAZICI E Y, TRRK T, SRNGRN Y H. Potential use of pyrite cinders as raw material in cement production: Results of industrial scale trial operations [J]. Journal of Hazardous Materials, 2009, 166(1): 144-149.
[10] ZHENG Ya-jie, GONG Zhu-qing, CHEN Bai-zhen, CHEN Wen-mi. Preparation principle and path analysis of iron-based products from iron pyrite cinder by wet method [J]. Techniques and Equipment for Environmental Pollution Control, 2001, 2(1): 48-54. (in Chinese)
[11] ZHANG Shun-li, MA Tong-sen, WU Zhi-shen, CHEN Wei-ping, LI Ming-yu. Preparation of iron oxide yellow and iron oxide red with pyrite cinder [J]. Chemical Researches, 1999, 10(1): 48-51. (in Chinese)
[12] ZHENG Ya-jie, CHEN Meng-jun, HUANG Gui-lin. Preparation of potassium iron blue from pyrite cinders [J]. Journal of Central South University: Science and Technology, 2006, 37(2): 252-256. (in Chinese)
[13] ZHENG Ya-jie, GONG Zhu-qing, CHEN Bai-zhen, LIU Li-hua. Preparation of solid polyferric sulfate from pyrite cinders and its structure feature [J]. Transactions of Nonferrous Metals Society of China, 2003, 13(3): 690-694.
[14] ZHENG Ya-jie, FU Li-chun. Preparation of ferric oxide from pyrite cinders by hydrothermal method [J]. Journal of Central South University: Science and Technology, 2007, 38(4): 674-680. (in Chinese)
[15] YANG Xi-yun, GONG Zhu-qing, ZHENG Ya-jie. Preparation of magnetite for electrostatic copying toner from pyrite cinders [J]. Journal of Functional Materials, 2005, 36(5): 667-670. (in Chinese)
[16] LIU Hui, GUO Hui, LI Ping, WEI Yu. Transformation from β-FeOOH to hematite in the presence of trace Fe(Ⅱ) [J]. Journal of Physics and Chemistry of Solids, 2009, 70(1): 186-191.
[17] LIU Hui, WEI Yu, SUN Yu-han. The formation of hematite from ferrihydrite using Fe(Ⅱ) as a catalyst [J]. Journal of molecular catalysis A: Chemical, 2005, 226(1): 135-140.
[18] CAO Fu-ling, WU Yu-fei, LIU Hui, WEI Yu. Preparation and property of discoid aluminum-doped α-Fe2O3 particles [J]. Acta Chimica Sinica, 2008, 66(12): 1405-1410. (in Chinese)
[19] SCHWERTMANN U, FITZPATRICK R W, TAYLOR R M, LEWIS D G. The influence of aluminum on iron oxides. Ⅱ: Preparation and properties of aluminum-substituted hematites [J]. Clays and Clay Minerals, 1979, 27: 105-112.
Foundation item: Project(2008A090300016) supported by Major Science & Technology Special Program of Guangdong Province, China
Received date: 2009-11-12; Accepted date: 2010-03-08
Corresponding author: ZHENG Ya-jie, Professor, PhD; Tel: +86-731-88836285; Fax: +86-731-88710171; Email: zzyyjj01@yahoo.com.cn
- Micaceous iron oxide prepared from pyrite cinders by hydrothermal method
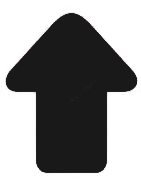