- Abstract:
- 1 Introduction▲
- 2 Experimental▲
- 3 Results and discussion▲
- 4 Conclusions▲
- References
- Figure
- Fig.1 XRD pattern of precursor
- Fig.2 XRD pattern of calcined product(α-Al2O3)
- Fig.3 SEM images of precursor (a) and α-Al2O3 (b) prepared by ordinary drying method
- Fig.4 Possible mechanism of formation of agglomerates in ordinary drying
- Fig.5 SEM images of precursor (a) and α-Al2O3 (b) prepared by alcohol exchange method
- Fig.6 SEM images of precursors ((a1), (b1), (c1)) and α-Al2O3 ((a2), (b2), (c2)) prepared by different drying methods
- Fig.7 dXRD of samples prepared by different drying methods
- Fig.8 dBET of samples prepared by different drying methods
- Fig.9 Aggregation coefficient of samples prepared by different drying methods
J. Cent. South Univ. Technol. (2007)03-0330-06
DOI: 10.1007/s11771-007-0065-5
Effects of drying method on preparation of nanometer α-Al2O3
XIAO Jin(肖 劲), WAN Ye(万 烨), DENG Hua(邓 华), LI Jie(李 劼), LIU Ye-xiang(刘业翔)
(School of Metallurgical Science and Engineering, Central South University, Changsha 410083, China)
Abstract:
Ammonium aluminum carbonate hydroxide (AACH) precursor was synthesized by the precipitation reaction of aluminum sulfate and ammonium carbonate. Then the precursor was dealt with five drying methods including ordinary drying, alcohol exchange, vacuum freeze-drying, glycol distillation, n-butanol azeotropic distillation respectively and calcined at 1 200 ℃ for 2 h to get α-Al2O3. The effects of drying methods on preparation of nanometer α-Al2O3 were discussed, and the optimal drying method was confirmed. The structural properties of powders were characterized by XRD, SEM and BET measurements. The results show that vacuum freeze-drying, glycol distillation and n-butanol azeotropic distillation can prevent the powders from aggregating, and among them the n-butanol azeotropic distillation is the best method. The nanometer α-Al2O3 powder with non-aggregation can be manufactured using n-butanol azeotropic distillation and the average particle size is about 40 nm.
key words: nanometer α-Al2O3; drying method; aggregation
1 Introduction
The nanometer α-Al2O3 powder, a kind of important structural and functional ceramic material, has excellent properties such as high surface activity, high light absorption, good wear resistance, high temperature stability and good corrosion resistance. It has been widely used in the fields of light, catalysis, electric, medical device and information[1-5]. In order to obtain good forming and sintering property, the nanometer α-Al2O3 powder with high purity, narrow grain size distribution and spherical in size is needed.
Nano-sized α-Al2O3 powder is usually prepared by means of sol-gel method[6], polyacrylamide gel method[7], hydrolysis method[8], micro-emulsion method[9], liquid-phase precipitation method[10]. DU et al[11] prepared nano-size α-Al2O3 powder by a solid-state method using (NH4)2SO4·Al2(SO4)3·24H2O as raw material and soluble starch as dispersant medium. Considering the fact that the liquid-phase precipitation methods have advantages such as easy fabrication and controllability, low-cost, and the nanometer alumina powders have excellent properties such as narrow grain-size distribution and high purity, the liquid-phase precipitation method becomes the most promising method[12]. But the liquid-phase precipitation by method also has a lot of disadvantages including the complex condition and the agglomeration. Drying processes have significant influences on the properties of the powder. The agglomeration of nanometer alumina particles will take place if the drying methods are not properly chosen,which will have the adverse effect on its operational properties. How to control good dispersion of nanometer alumina powder during drying processes is one of the most important technology for preparing nanometer alumina powder[13]. The drying methods of nanometer alumina powder such as alcohol exchange[14], n-butanol heterogeneous azeotropic distillation[12], vacuum freeze-drying[15], supercritical drying have been systematically studied. YANG et al[16] prepared non-aggregation nanometer alumina powder by using high-pressure drying method.
In this paper, a series of investigations were made to compare several drying methods including ordinary drying, alcohol exchange, vacuum freeze-drying, glycol distillation, n-butanol azeotropic distillation, and the best drying method for preparing nanometer α-Al2O3 powder was determined.
2 Experimental
2.1 Experimental process
0.1 mol Al2(SO4)3(AR) was dissolved in deionized water to prepare solution with concentration of 0.3 mol/L by adding suitable amounts of PEG600 as dispersant. 0.4 mol (NH4)2CO3(AR) was dissolved in deionized water to prepare 2.0 mol/L solution by adding suitable amounts of PEG1000 as dispersant. The precursor was prepared by rapidly adding Al2(SO4)3 solution to a acutely stirred (1 400 r/min) (NH4)2CO3 solution in the 55 ℃ thermostatic bath. When the slurry pH was adjusted to 8-10, the precipitate was aged in the container with constant stirring intensively for 1 h without removing the solution, the slurry was filtered and the filter cake was washed three times by deionized water, then carried on the operation as follows.
1) The filter cake was put in 80 ℃ drying oven for 12 h ordinary drying.
2) The filter cake was washed two times with absolute ethanol, and then dried for 12 h in the 80 ℃ vacuum oven.
3) The filter cake was cooled rapidly using liquid nitrogen, followed by 12 h vacuum freeze-drying.
4) The filter cake was washed two times by absolute ethanol, followed by glycol distillation, and then dried for 12 h in the 80 ℃ vacuum oven.
5) The filter cake was washed two times by absolute ethanol, followed by n-butanol azeotropic distillation, and then dried for 12 h in the 80 ℃ vacuum oven.
The above five samples were all calcined at 1 200 ℃ for 2 h to obtain α-Al2O3 powders.
2.2 Sample characterization
The precursors and the calcined products were identified using a Rigaku X-ray powder diffractometer (XRD) with Cu Kα radiation, and the average grain size of α-Al2O3 (dXRD) was calculated through FWHM. The particle shape and the dispersion of the powders were characterized by JSM-5600LV scanning electron microscope. The powders for SEM observation were scattered in acetone ultrasonically and then the suspended powders were mounted on a copper microgrit. The surface area of the alumina powders was characterized by ST-03 surface aperture cryoscopy, and the BET-equivalent primary particle diameter of α-Al2O3 (dBET) was calculated through BET method.
3 Results and discussion
3.1 Material authentication
The X-ray diffraction patterns of five precursors and their calcined products are absolutely consentaneous. One of the X-ray diffraction patterns of precursors is shown in Fig.1, and one of the X-ray diffraction patterns of calcined products is shown in Fig.2.
Fig.1 shows that precursors have the structure of pure ammonium aluminum carbonate hydroxide (NH4Al- (OH)2CO3). When the molar ratio of Al2(SO4)3 to (NH4)2CO3 is 1?4, we could predict the reaction in the reactor as follows:
Al2(SO4)3+4(NH4)2CO3+2H2O=
2NH4Al(OH)2CO3+3(NH4)2SO4+2CO2 (1)
Fig.1 XRD pattern of precursor
Fig.2 XRD pattern of calcined product(α-Al2O3)
Fig.2 shows that the calcined products are pure α-Al2O3, which reveals that after calcining at 1 200 ℃ for 2 h, AACH is transformed into pure α-Al2O3.
3.2 Effect of drying method on dispersion of products
The SEM micrographs of the precursor treated by ordinary drying method and its calcined product are shown in Fig.3, showing that the precursor has a considerable aggregation phenomenon and the distribution of the particle size is inhomogeneous. The size of α-Al2O3 particles is large and the particles also have a visible aggregation with sintering neck.
There might be two reasons for the phenomenon described above. Firstly, massive water molecules are stored in ammonium aluminum carbonate hydroxide particles. The liquid-gas interface has not produced at the beginning of evaporation, and there is no capillary force. When the ordinary drying method is adopted, with the continuously evaporating of the liquid, the void among the particles might result in great capillary pressure which presses the particles together, and produces the bond force, and the aggregation of the particles is formed.
Meanwhile, such bond force may be increased with the further drying process, and the aggregation becomes
Fig.3 SEM images of precursor (a) and α-Al2O3 (b) prepared by ordinary drying method
more serious. Secondly, the redundant free water molecules and the free hydroxyl on the surface of the powder particles interact each other by hydrogen bonding. When the particles contact closely, the hydrogen function between the redundant free water molecules and the hydroxyl on the surface of the particles is produced, and the bridging function appears. This bridging water molecules will be removed at the beginning of the drying, which causes the hydroxyl hydrogen bond function between the particles, and the covalent bonder will be introduced in the further dehydration process, then aggregation is produced. Fig.4 shows the possible mechanism of the formation of agglomerates in ordinary drying.
The SEM images of precursor treated by alcohol exchange method and its calcined product are shown in Fig.5, indicating that compared with the ordinary drying method, the dispersivity of the precursor and α-Al2O3 are improved by using alcohol exchange method. But the particle size of the precursor is still inhomogeneous, and the shape is also irregular. The particle size of α-Al2O3 powders which connect together is larger and considerable aggregation still exists. It can be concluded that when the precursor is washed by absolute ethanol, water among the particles is removed, and the capillary pressure is reduced, so the aggregation of the particles decreases. But water among the particles cannot be thoroughly removed by absolute ethanol, therefore, the hard aggregation of the particles can only be partially eliminated.
Fig.4 Possible mechanism of formation of agglomerates in ordinary drying
The SEM images of the precursors treated by vacuum freeze-drying, glycol distillation and n-butanol azeotropic distillation respectively and their calcined products are shown in Fig.6, showing that after the treatment of the three drying methods, the dispersion of precursors and their calcined products is improved, and the precursors are in non-aggregation with regular shape and even distribution of particle size. The obtained α-Al2O3 powders are also in non-aggregation with regular shape, and the average particle size is about 40 nm.
When the freeze drying method is used, water can be
Fig.5 SEM images of precursor (a) and α-Al2O3 (b) prepared by alcohol exchange method
Fig.6 SEM images of precursors ((a1), (b1), (c1)) and α-Al2O3 ((a2), (b2), (c2)) prepared by different drying methods
(a1), (a2)—Vacuum freeze-drying; (b1), (b2)—Glycol distillation; (c1), (c2)—n-butanol heterogeneous azeotropic distillation
removed by freezing drying method by the agency of sublimation under reduced pressure. In order to obtain a satisfactory drying rate, very low pressure is required. Most freeze drying is done at -50 ℃, and absolute pressures of about 2 666 Pa or less. In the freeze-drying process, the “liquid bridge” between the particles is frozen to “solid bridge”, the relative position of the two particles is fixed, and the surface tension of gas-liquid interface between the two particles is also eliminated. The hard aggregation can be effectively prevented by freezing drying with the decreased “solid bridge”. The freezen water within the microspheres can be easily removed, but the fraction of bound water is more slowly sublimed and still remained after freeze-drying for 12 h, so there is still some sintering neck in α-Al2O3 particles.
Water can be removed by glycol distillation method from the precipitation by distillation due to the high boiling point of the glycol. The boiling point of the glycol is 197.4 ℃ which is higher than that of the water. Water is evaporated when heating the mixture. Compared with the alcohol exchange method, the effect of removing water is greatly improved by glycol distillation. But water cannot be thoroughly removed, and there is still some sintering necks in α-Al2O3 particles.
When the precursor is treated by n-butanol azeotropic distillation method, at first, water in the distilled gels is replaced by n-butanol that has a low surface tension stress, leading to a decrease of aggregation. Secondly, vander Waals bonding instead of hydrogen bonding may be responsible for eliminating agglomeration by n-butanol azeotropic distillation treatment. In fact, the surface reaction between precursor and n-butanol may take place during distillation:
Al(OH)n+HOC4H9→HO+(OH)n-1…Al—O—C4H9 (2)
The OH- groups of the hydrates on the surface are substituted by —OC4H9, which corresponds to hydrophilicity and hydrophobicity, respectively. As a result, strong hydrogen bonding between the hydrate gels with H—O—H bridges becomes a van der Waals bond with —O—C4H9 bridges after distillation. So it is the best method to prevent the powder from forming aggregation.
3.3 Effect of drying method on properties of alumina particles
The precursors treated by the above five drying methods are calcined at 1 200 ℃ for 2 h to obtain pure α-Al2O3 particles, the average grain size was calculated from the Scherrer formula:
dXRD=Kλ/(βcos θ) (3)
where dXRD is the average grain size in nm, K=0.89 is the Scherrer constant, λ=0.154 1 nm is the wave length of X-ray, β is the broadening of diffraction line measured half of its maximum intensity in radians, θ is the diffraction angle.
The average grain sizes of the samples are estimated from the line width of the (113) XRD peaks and are shown in Fig.7.
Assuming monodisperse, spherical primary particles, the BET-equivalent primary particle diameter (dBET) of different samples was calculated by:
dBET=6/(ρpSm) (4)
where ρp is the density of α-Al2O3, Sm is the specific surface area. The BET-equivalent primary particle diameters of different samples are shown in Fig.8.
Fig.7 dXRD of samples prepared by different drying methods
A—Ordinary drying; B—Alcohol exchange; C—Vacuum freeze-drying; D—Glycol distillation; E—n-butanol azeotropic distillation
Fig.8 dBET of samples prepared by different drying methods
A—Ordinary drying; B—Alcohol exchange; C—Vacuum freeze-drying; D—Glycol distillation; E—n-butanol azeotropic distillation
The aggregation coefficient (fa) of different samples can be calculated from the following relationship:
fa= dBET/dXRD (5)
The aggregation coefficients of different samples are shown in Fig.9. If fa is close to 1, the aggregation of the sample will be slightly, and if fa deviates from 1, the aggregation of the sample will be serious. Fig.9 shows that the massive aggregation is formed by ordinary drying method (sample A), the slightly aggregation is formed by alcohol exchange method (sample B), and the products with good dispersion are formed by vacuum freeze-drying (sample C), glycol distillation (sample D) and n-butanol azeotropic distillation (sample E). It is demonstrated that vacuum freeze-drying, glycol distillation and n-butanol azeotropic distillation can effectively prevent the powder from forming aggregation during drying process, and obtain the α-Al2O3 powder with excellent properties, among them the n-butanol azeotropic distillation is the best method to prevent the powders from forming aggregation.
Fig.9 Aggregation coefficient of samples prepared by different drying methods
A—Ordinary drying; B—Alcohol exchange; C—Vacuum freeze-drying; D—Glycol distillation; E—n-butanol azeotropic distillation
4 Conclusions
1) Ammonium aluminum carbonate hydroxide (AACH) was synthesized by the precipitation and calcined at 1 200 ℃ for 2 h to obtain nanometer α-Al2O3 powder.
2) The gravely hard aggregation is formed by ordinary drying. The dispersity of powder is partially improved by alcohol exchange method, but the hard aggregation cannot be thoroughly solved.
3) Vacuum freeze-drying, glycol distillation and n-butanol azeotropic distillation can effectively prevent the powder from forming aggregation in drying process, among them the n-butanol azeotropic distillation is the best. Nanometer α-Al2O3 powder with non-aggregation can be manufactured though n-butanol azeotropic distillation and the average particle size is about 40 nm.
References
[1] HUO Cai-xia, HE Li-jun. The preparation of nano-sized γ-Al2O3 powders by using urea as precipitating agent[J]. Journal of Gansu Lianhe University: Natural Science, 2004, 18(4): 45-47. (in Chinese)
[2] GU Feng, SHENG Yue, XU Chao, et al. The influence of polymerization degree of dispersing agent on the powder properties of nano alumina[J]. Journal of Functional Materials, 2005, 36(2): 318-320. (in Chinese)
[3] XIAO Jin, DENG Hua, WAN Ye, et al. Preparation of ultrafine α-Al2O3 powders by catalytic sintering of ammonium aluminum carbonate hydroxide at low temperature[J]. Journal of Central South University of Technology, 2006, 13(4): 367-372.
[4] RAJENDRAN M, BHATTACHARYA A K. Low-temperature formation of alpha alumina powders from carboxylate and mixed carboxylate precursors[J]. Materials Letters, 1999, 39(5): 188-195.
[5] SHIAU F S, FANG T T. Low-temperature synthesis of α-alumina using citrate process with α-alumina seeding[J]. Materials Chemistry and Physics, 1999, 60(1): 91-94.
[6] HUANG Chuan-zhen, ZHANG Shu-sheng, WANG Bao-you. Preparation nanometer alumina powder using sol-gel method[J]. Diamond and Abrasives Engineering, 2002(1): 22-25.(in Chinese)
[7] WANG Hong-zhi, GAO Lian, LI Wei-qun. Preparation of nanoscale- Al2O3 powders by the polyacrylamide gel method[J]. Journal of Inorganic Materials, 2000, 15(2): 356-360. (in Chinese)
[8] TANG Fang-qiong, GUO Guang-sheng, HOU Li-ping. Preparation of nanometer Al2O3 particles[J]. Photographic Science and Photochemistry, 2001, 19(3): 198-201. (in Chinese)
[9] ANANTHAPADMANABHAN P V, THIYAGARAJAN T K, SREEKUMAR K P, et al. Formation of nano-sized alumina by in-flight oxidation of aluminum powder in a thermal plasma reactor[J]. Scripta Materialia, 2004, 50: 143-147.
[10] WU Yi-quan, ZHANG Yu-feng, HUANG Xiao-feng. Preparation of nano-sized alumina powders at low temperatures[J]. Journal of Inorganic Materials, 2001, 16(2): 349-351. (in Chinese)
[11] DU Yan-jun, WANG Li-juan, WANG Mao-sheng, et al. Preparation of nano-sized-Al2O3 powders by solid-state method[J]. Chemistry World, 2004, 45(3): 115-117. (in Chinese)
[12] PENG Tian-you, DU Ping-wu, HU Bin, et al. Preparation of nanoscale alumina powder by heterogeneous azeotropic distillation processing[J]. Journal of Inorganic Materials, 2000, 15(6): 1097-1101.(in Chinese)
[13] WANG Bao-he. Study and progress of the nanometer materials drying method[J]. General Machine, 2004(12): 12-13; 72-73. (in Chinese)
[14] ZHANG Ai-fei, LIU Ji-ping. A new precipitation method for the preparation of alumina nanopowders[J]. Inorganic Chemicals Industry, 2003, 25(2): 27-28. (in Chinese)
[15] LIU Jun, XU Hai-cheng, DOU Xin-sheng. Preparation of nano alumina ceramic powders by vacuum freeze-drying method[J]. Vacuum, 2004, 41(4): 80-83. (in Chinese)
[16] YANG Yong-lai, LIN Gui-ling, LIN Yuan, et al. Hard-agglomeration-free Al2O3 nanometer-powder prepared by high-pressure drying method[J]. Chinese Journal of Materials Research, 1999, 13(1): 63-67. (in Chinese)
(Edited by CHEN Wei-ping)
Foundation item: Project (5JJ30103) supported by the Natural Science Foundation of Hunan Province, China
Received date: 2006-08-26; Accepted date: 2006-10-18
Corresponding author: XIAO Jin, PhD; Tel: +86-731-8876454;E-mail: 13607445108@hnmcc.com
- Effects of drying method on preparation of nanometer α-Al2O3
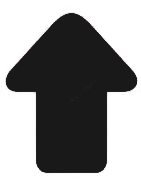