Microstructure evolution of aluminum-lithium alloy 2195
undergoing commercial production
JIANG Na(蒋 呐)1, 2, GAO Xiang(高 翔)3, ZHENG Zi-qiao(郑子樵)1
1. School of Materials Science and Engineering, Central South University, Changsha 410083, China;
2. Technical Center, Southwest Aluminum (Group) Corporation Limited, Chongqing 401326, China;
3. ARC Centre of Excellence for Design in Light Metals, Monash University, Clayton 3800, Australia
Received 22 February 2009; accepted 19 April 2009
Abstract:
Microstructures of three kinds of typical product states for commercially fabricated alloy 2195 were observed. It is found that the hot-rolled plate is characterized by a fibrous structure containing fine, polygonized substructures; and the cold-rolled sheet was characterized by a “pan-caked” grain structure containing high density dislocation cells. The product under near peak-aging temper is proved to contain a large amount of dispersive, plate-shaped T1(Al2CuLi) precipitates, together with a small fraction of θ′(Al2Cu) plates, exhibiting a desirable combination of mechanical properties. Analyses using scanning electron microscopy reveal that many coarse, irregular-shaped Al7Cu2Fe constituent particles exist in all product states, which indicates that intermediate heat treatments have little influence on this iron-caused, detrimental phase. The formation and evolution of microstructures for different product states of alloy 2195 were discussed in view point of the commercial production condition.
Key words:
Al-Li alloy; commercial production; microstructure evolution; rolling; heat treatment;
1 Introduction
Aluminum-lithium alloys, due to their low densities, have been regarded as competitive structural materials for aerospace applications[1-2]. The high-strength, weldable Al-Li alloy 2195 (Al-4.0Cu-1.0Li-0.4Mg- 0.4Ag-0.12Zr, mass fraction, %) was developed to take the place of AA2219 which was conventionally used to build the huge external tank of USA space shuttles[3-4], and first achieved commercial application in NASA’s mission STS-91. In that launch, the super light weight tank built of 2195 plates provides a mass reduction of 3 175 kg and 50% increase of the payload capability for the shuttle. Because of the huge success, alloy 2195 has attracted worldwide attention.
So far, most researches on alloy 2195 have been focused on fundamental aspects[5-6], such as strengthening mechanism and microstructural design. As for studies at commercial level, HALES and HAFLEY[7], KALU and ZHANG[8] have investigated the texture evolution and anisotropic nature of several 2195 wrought products with commercial sizes, including near-net-shape extrusions, hot-rolled plates and ring roll forgings. Their results show that alloy 2195 has complex evolutions of grain morphology, texture, through- thickness anisotropy when it undergoes multi-stage deformation. However, these investigations are associated with hot-deformed products only, and few are extended to further product states in which the cold working will be involved.
With a view to obtain some in-depth understandings about the microstructure evolution of alloy 2195 during the whole commercial production procedures, the present work has conducted an overall observation on microstructures of commercially fabricated 2195 plates and sheets, with product states covering hot rolling, cold rolling and artificial aging.
2 Experimental
2.1 Materials
Commercial fabrication of 2195 rolled products consists of a series of processing procedures, such as homogenization, hot rolling, intermediate annealing, cold rolling, solution treatment and quenching, cold-working and artificial aging, as schematically shown in Fig.1.
The slab of 3 000 kg, with thickness around 300 mm was homogenized at temperature up to 495 ℃, and then hot-rolled to plate of 10 mm in thickness at a 2 800 mm four-high, reversible hot-rolling mill. The plate was annealed and then cold-rolled to sheets with thickness ranging 2-5 mm at a 1 650 mm four-high, reversible cold-rolling mill. Sheets of 2 mm were solution treated in salt bath at 500 ?C and quenched into water of room temperature, then cold-worked by 3% and artificially aged (T851 processing) at 160 ℃ for 2, 16 and 100 h, respectively, to achieve so-called under-aged, near peak-aged and over-aged products.
Fig.1 Schematic diagram of commercial production procedures of 2195 rolled product
Three kinds of typical product states, i.e., hot-rolled plate of 10 mm, cold-rolled sheet of 5 mm and aged sheets (including three aging stages) of 2 mm, were selected to represent the primary processing procedures of commercial production. All specimens were taken from above-mentioned plates or sheets.
2.2 Experimental methods
As-rolled (hot-rolled and cold-rolled) products were optically observed on cross-sections along rolling, transverse and normal directions, respectively. Substructures from hot working or intermediate annealing were displayed using transmission electron microscopy(TEM). The precipitation behavior of aged products was studied by means of TEM and tensile test. Constituent particles inside products were analyzed by means of scanning electron microscopy(SEM).
Metallographic observation was performed under an Olympus-BHM optical microscope; TEM observation was performed on a Philips CM20 transmission electron microscope operated at 200 kV; SEM analyses were carried out with a JEOL-840A scanning electron microscope equipped with energy dispersive X-ray spectrometer (EDS) operated at 20 kV; and tensile test was carried out on an AG-IS 100 kN electronic tensile tester at room temperature with specimen orientation along the transverse direction of products.
3 Results and discussion
3.1 Microstructures of as-rolled products
Three-dimensional micrographs of as-rolled products are given in Fig.2. It can be seen from Fig.2(a) that fibrous structure is the microstructural characteristic of hot-rolled product, similar to the result of HALES and HAFLEY[7]. The morphology on longitudinal section shows a uniform distribution of fibrous metal throughout the thickness of plate, and no obvious grain boundaries exhibit. This means that as-cast grains of the slab have been fully broken by the hot rolling of commercial scale which has a working amount more than 95%. Also because of the high strain rate of commercial rolling, few dynamically recrystallized grains are seen, which is in a good accordance with the previous work of the author[9].
Fig.2(b) shows a “pan-caked” grain structure in the cold-rolled product. Because the total working amount of cold rolling is much less than that of hot rolling, some recrystallized grains arising from intermediate annealing are partially remained after cold working. DU et al[10] have investigated the recrystallization behavior of 2195 plate during intermediate annealing. They found that the recrystallization nucleation in 2195 plate occurred heterogeneously in some planar zones parallel to rolling direction and recrystallized grain boundaries would
Fig.2 Three-dimensional micrographs of as-rolled products (RD—Rolling direction; TD—Transverse direction; ND—Normal direction): (a) Hot-rolled plate; (b) Cold-rolled sheet
interact with undissolved particles remaining in planar zones, which resulted in the formation of elongated grains. Therefore, the observed “pan-caked” grain structure of cold-rolled sheet should be, in some sense, the structural heredity of those elongated recrystallized grains of plate after intermediate annealing.
Fig.3 gives the TEM images of as-rolled products. The morphology of hot-rolled plate shown in Fig.3(a) exhibits fine, polygonized substructures. This gives the evidence that dynamic recovery is the main softening mechanism of alloy 2195 during commercial hot rolling. Fig.3(b) shows that the cold-rolled product contains high density dislocation cells, which should be attributed to the strong deformation at room temperature.
3.2 Precipitation behavior of aged product
Fig.4 shows morphologies of precipitates inside the aged products of alloy 2195 at different aging tempers. It can be found that for 2 h aging at 160 ?C, some fine T1(Al2CuLi) plates have precipitated on {111}α planes of the aluminum matrix, and no θ′(Al2Cu) plates are observed, as shown in Fig.4(a). For near peak-aging of 16 h at 160 ℃, a uniform dispersion of T1-plates exhibits, as shown in Fig.4(b). Besides T1-plates, a small fraction of θ′-plates are also observed on {100}α planes, as given in Fig.4(c). For over-aging of 100 h at 160 ℃, it can be seen that T1-plates have obviously coarsened (Fig.4(d)) and θ′-plates are much fewer (Fig.4(e)).
Fig.3 TEM morphologies of as-rolled products: (a) Hot-rolled plate; (b) Cold-rolled sheet
Fig.4 TEM morphologies of precipitates at different aging stages for sheet products aged at 160 ℃: (a) 2 h, T1; (b) 16 h, T1; (c) 16 h, θ ′; (d) 100 h, T1; (e) 100 h, θ ′
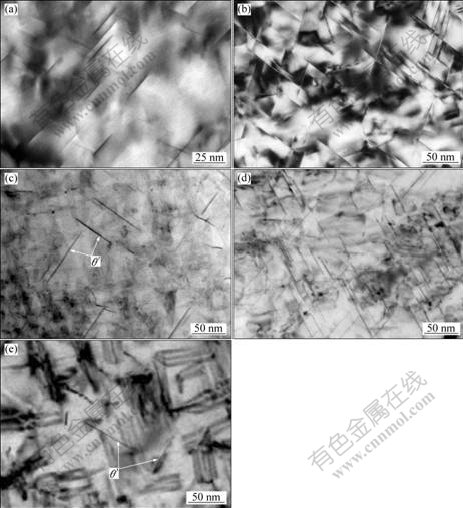
Fig.5 Back-scattering electron images displaying constituent particles existing inside all products: (a) Hot-rolled; (b) Cold-rolled; (c) Aged
Fig.6 EDS analysis results for marked particles in Fig.5
References
Foundation item: Project supported by the National Key Technologies R&D Program of China during the 10th Five-year Plan Period
Corresponding author: JIANG Na; Tel: +86-13708324937; E-mail: jiangna@live.cn
DOI: 10.1016/S1003-6326(09)60207-7