- Abstract:
- 1 Introduction▲
- 2 HPHT rheology experimen...▲
- 3 Results and discussion▲
- 4 Prediction model for rh...▲
- 5 Conclusions▲
- References
- Figure
- Fig.1 Rheological curves of oil-based drilling fluids 1 at various temperatures and pressures
- Fig.2 Rheological curves of oil-based drilling fluids 2 at various temperatures and pressures
- Fig.3 Curves of apparent viscosity for oil-based drilling fluids of group 2
- Fig.4 Curves of plastic viscosity for oil-based drilling fluids of group 2
- Fig.5 Curves of yield point for oil-based drilling fluids of group 2
- Fig. 6 Comparison of calculated values with measured values of apparent viscosity of No.3 drilling fluids
J. Cent. South Univ. Technol. (2008) 15(s1): 457-461
DOI: 10.1007/s11771-008-399-7
Rheological properties of oil-based drilling fluids at high temperature and high pressure
ZHAO Sheng-ying(赵胜英), YAN Jie-nian(鄢捷年), SHU Yong(舒 勇), ZHANG Hong-xia(张洪霞)
(Key Laboratory of Petroleum Engineering of Ministry of Education, China University of Petroleum, Beijing 102249, China)
Abstract:
The rheological properties of two kinds of oil-based drilling fluids with typically composition were studied at pressures up to 138 MPa and temperatures up to 204 ℃ using the RheoChan 7400 Rheometer. The experimental results show that the apparent viscosity, plastic viscosity and yield point decrease with the increase of temperature, and increase with the increase of pressure. The effect of pressure on the apparent viscosity, plastic viscosity and yield point is considerable at ambient temperature. However, this effect gradually reduces with the increase of temperature. The major factor influencing the rheological properties of oil-based drilling fluids is temperature instead of pressure in the deep sections of oil wells. On the basis of numerous experiments, the model for predict the apparent viscosity, plastic viscosity and yield point of oil-based drilling fluids at high temperature and pressure was established using the method of regressive analysis. It is confirmed that the calculated data are in good agreement with the measured data, and the correlation coefficients are more than 0.98. The model is convenient for use and suitable for the application in drilling operations.
Key words:
oil-based drilling fluids; high temperature; high pressure; rheological property; mathematical model;
1 Introduction
Oil-based drilling fluids have become widely used in oil industry because of their distinct advantage over water-based drilling fluids. Unlike water-based drilling fluids, Oil-based drilling fluids show significant rheological properties dependence on temperature and pressure[1]. For shallow wells the temperature and pressure changes are not so large, and the effects of both temperature and pressure on rheological properties are usually ignored. But for wells with small margins between pore and fracture gradient and high temperature and high pressure (HPHT) wells, the above practice was unsatisfactory. On the one hand, statistically[2], well control incident rates for non HPHT wells were 4% to 5% i.e. an incident per 20 to 25 wells. However, for HPHT wells, the well control incident rate was as high as 100% to 200% i.e. one to two incident(s) per well; on the other hand, the rheological properties play an important role in hole cleaning, cutting lifting and calculation for friction pressure losses in annular[3]. It is highly recommended to measure rheology of the actual mud system at HPHT condition prior to drilling operations. If such measurements have not been done at the time of making calculations, the next best choice is to use theoretical or empirical models that predict pressure and temperature dependence of rheology. Therefore, it is critical to investigate the rheological properties of oil-based drilling fluids at HPHT carefully and develope equations that predict temperature and pressure effects on the rheological properties of drilling fluids.
2 HPHT rheology experiments
2.1 Experimental equipment and test drilling fluids
A rheoChan 7400 Rheometer was used for the measurement of the rheological parameters under various temperature and pressure conditions. This is a coaxial cylinder viscometer where the test material is sheared between an outer sleeve (the rotor) and an inner cylinder (the bob) which is attached to a torsional spring. The deflection of the spring is indicated on a scale reading in degrees. It is capable of operating at pressures to 206.9 MPa, maximum temperatures to 260 ℃ and viscosity range to 100 mPa·s. Temperature and pressure can be controlled automatically, so it is convenient to use.
The drilling fluids were prepared with typical formulations of high-temperature oil-based drilling fluids. Six kinds of samples were divided into three groups. Two samples have same compositions in each group, except that the base oil of one sample is diesel and another is mineral oil. Table 1 lists the compositions of the samples.
Table 1 Compositions of oil-based drilling fluids
2.2 Experimental procedure
The measurements were taken starting at 23.9 ℃, then heating up to 121.1 ℃ and 204.4 ℃, at each temperature, the pressures were 0, 6.895, 20.69, 41.37, 62.06, 82.74 and 103.4 MPa respectively. Recorded the dial readings at 8 rotor speeds (600, 300, 200, 100, 60, 30, 6 and 3 r/min) representing shear rates in the range 1 022 s-1 to 5.11 s-1, determined the rheological parameters based on the measured data according to the API standard test procedures[4], and plotted the rheological curves of each sample. The data collected with the RheoChan 7400 Rheometer are shown in Figs.1-5.
3 Results and discussion
3.1 Rheological model
Figs.1 and 2 show the rheological curves of oil-based drilling fluids 1 and 2 respectively at various temperatures and pressures. Figs.1 and 2 show the following main trends: The shear stress for a given shear rate decrease significantly with the increase in temperature at constant pressure; the shear stress for a given shear rate increase with increasing pressure at constant temperature. The variation amplitude is much more pronounced at high shear rates than at low shear rates.
The correct selection of rheological model to describe drilling fluids rheology is very important for hydraulic calculations during drilling operations. It can be seen from Figs.1 and 2 that the rheological curves are not through the point of origin, nearly straightlines, which show that the drilling fluids behavior like Bingham plastics at high temperature and high pressure, so we can conclude that the Bingham plastic model can be chosen to characterize the muds data[5].
Fig.1 Rheological curves of oil-based drilling fluids 1 at various temperatures and pressures
Fig.2 Rheological curves of oil-based drilling fluids 2 at various temperatures and pressures
3.2 Rheological properties
Data in Table 2 show the rheological parameters obtained with the RheoChan 7400 Rheometer. It can be seen from Table 2 and Figs.3-5 that the apparent viscosity(μa), plastic viscosity(μp) and yield point(τ0) of oil-based drilling fluids decrease with the increase of temperature, and increase with the increase of pressure, in general, the effect of temperature on the rheological properties of oil-based drilling fluids is dominate. The effect of pressure on the apparent viscosity, plastic viscosity is considerable at ambient temperature. However, this effect gradually reduces with the increase in temperature. Overall, the effect of pressure and temperature on apparent viscosity and plastic viscosity is greater than that of yield point.
Fig.3 Curves of apparent viscosity for oil-based drilling fluids of group 2
Fig.4 Curves of plastic viscosity for oil-based drilling fluids of group 2
Fig.5 Curves of yield point for oil-based drilling fluids of group 2
4 Prediction model for rheological parameters
4.1 Establish of model
With Data in Table 2 and Figs.3-5 obtained by the RheoChan 7400 Rheometer, an exponential expression was found to be able to model the pressure and temperature behaviour of the apparent viscosity, plastic viscosity and yield point using the method of regressive analysis[6]:
(1)
where T is the temperature, ℃; p is the pressure, Pa; f(p, T) stands for (μa)p, T, (μp)p, T, or (τ0)p, T, respectively; f(p0, T0) stands for (μa)0, (μp)0 or (τ0)0, respectively, at T0=23.9 ℃, p0=0 Pa.
(μa)0, (μp)0, (τ0)0, A, B, C and D are characterized constants of drilling fluids, which were determined by least-squares analysis of date obtained with the RheoChan 7400 Rheometer. Characterized constants and correlation coefficients for various drilling fluids are given in Tables 3 through 5. All of the correlation coefficients are more than 0.98 as shown in Tables 2-4 that means the data are well described by Eqn.(1).
Table 2 Characterized constants for various drilling fluids for prediction model of apparent viscosity
Table 3 Characterized constants for various drilling fluids for prediction model of plastic viscosity
Table 4 Characterized constants for various drilling fluids for prediction model of yield point
The measured values were compared with predicted values with Eqn.(1), data presented in Fig.6 show that the predicted and measured values were in excellent agreement.
Fig. 6 Comparison of calculated values with measured values of apparent viscosity of No.3 drilling fluids
4.2 Application of model
Eqn.(1) can be used to predict downhole oil-based drilling fluids rheology in the fields. A possible procedure for implementing the model is: Firstly, according to our model experiments should be made at HPHT in order to determine the characterized constants for the specific drilling fluid in use, which are required for accurate extrapolation of rheological parameters to downhole conditions. Secondly, to accurately predict the rheological parameters throughout the wellbore requires an accurate transient temperature and pressure profile to be calculated[7]. It can be obtained using a transient temperature and pressure simulator, and it has been described in detail elsewhere[8]. Finally, the characterized constants, temperature and pressure values should be substituted into Eqn.(1), and the rheological parameters at downhole could be obtained.
5 Conclusions
1) The shear stress of oil-based drilling fluids for a given shear rate decrease significantly with increasing temperature and increase with increasing pressure. The variation amplitude is much more pronounced at high shear rates than at low shear rates. The Bingham plastic model can be used to characterize the mud data.
2) The apparent viscosity, plastic viscosity and yield point of oil-based drilling fluids decrease with increasing temperature, and increase with increasing pressure, and the effect of temperature on the rheological properties is dominate. The effect of pressure on apparent viscosity, plastic viscosity are considerable at ambient temperature and gradually reduces with increasing temperature.
3) Compared with typical water-in-oil emulsions, the mineral oil-based drilling fluids have better rheological properties at high pressure and high temperature.
4) The model for predict the apparent viscosity, plastic viscosity and yield point of oil-based drilling fluids at high temperature and pressure has been established. It is confirmed that the calculated data are in good agreement with the measured data. The model is suitable for accurate hydraulic calculation during drilling operations.
References
[1] GALATE J W, MITCHELL R F. Behavior of oil muds during drilling operations[C]// SPE Drilling Engineering. 1986: 97-106.
[2] GAO E, ESTENSEN O, MACDONALD C, CASTLE S. Critical requirements for successful fluid engineering in HPHT wells: Modeling tools, design procedures & bottom hole pressure management in the field[C]// SPE European Petroleum Conference. Hague, 1998: 1-14.
[3] ZHOU Fu-jian, LIU Yu-qing, YANG Xian-you, SONG Guang-shun. A study on rheological properties of oil-in water emulsion at high temperature and high pressure[J]. Acta Petrolei Sinica, 1999, 20(3): 77-81. (in Chinese)
[4] YAN Jie-nian. A model for predicting the apparent viscosity of invert emulsion muds[J]. Petroleum Drilling Techniques, 1990, 14(1): 9-15. (in Chinese)
[5] DONG Shu-li, YAN Jie-nian. Optimization of drilling fluid rheology model using least square fitting method[J]. Petroleum Drilling Techniques, 2000, 28(5): 27-29. (in Chinese)
[6] ZHANG Rui, WANG Rui-he, QIU Zheng-song. Temperature/ pressure relationships of yield stress and plastic viscosity for foamed drilling fluids[J]. Oilfield Chemistry, 2005, 22(1): 6-12. (in Chinese)
[7] DAVISON J M, CLARY S, SAASEN A, ALLOUCHE M. Rheology of various drilling fluid systems under deepwater drilling conditions and the importance of accurate predictions of downhole fluid hydraulics[C]// SPE Annual Technical Conference and Exhibition. Houston, 1999: 1-13
[8] Bjorkevoll K S, Vefring E H, Rommetveit R, Aadnoy B. Changes in active volume due to variations in pressure and temperature in HPHT Wells[C]// 7th Northern European Drilling Conference. Kristiansand, 1994.
Foundation item: Project(50574061) supported by the National Natural Science Foundation of China; Project(IRT0411) supported by the Changjiang Scholars and Innovative Research Team, Ministry of Education
Received date: 2008-06-25; Accepted date: 2008-08-05
Corresponding author: YAN Jie-nian, Master; Tel: +86-10-89733893; E-mail: yanjienian@sina.com
- Rheological properties of oil-based drilling fluids at high temperature and high pressure
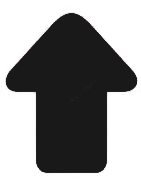