- Abstract:
- 1 Introduction▲
- 2 Experimental▲
- 3 Experimental results▲
- 4 Discussion ▲
- 5 Conclusions▲
- References
- Figure
- Fig.1 Schematic diagram of experimental apparatus: 1—Stainless steel liquid; 2—Tundish; 3—Copper mold; 4—Graphite mold; 5—Rotary EMS
- Fig.2 Macrostructures of austenitic stainless steel billets treated at different magnetic flux densities (B) and frequencies (f ): (a) B = 0 mT; (b) B=68 mT, f=4 Hz; (c) B=70 mT, f=7 Hz; (d) B=90 mT, f=3 Hz
- Fig.3 Evolutions of magnetic flux density with frequency (I=240 A)
- Fig.4 Evolutions of electromagnetic force with frequency and magnetic flux density
- Fig.5 Calculated distribution of stirring velocity in cross-sectional view
J. Cent. South Univ. Technol. (2009) 16: 0360-0364
DOI: 10.1007/s11771-009-0061-z
Effect of low-frequency rotary electromagnetic-field on
solidification structure of continuous casting austenitic stainless steel
ZHOU Shu-cai(周书才)1, 2, BAI Chen-guang(白晨光)1, LEI Ya(雷 亚)2, REN Zheng-de(任正德)2,
CAO Peng-jun(曹鹏军)2, YANG Zhi-li(杨治立)2
(1.College of Material Science and Engineering, Chongqing University, Chongqing 400044, China;
2. College of Metallurgy and Material Engineering, Chongqing University of Science and Technology,
Chongqing 401331, China)
Abstract:
To understand the solidification behavior of austenitic stainless steel in rotary electromagnetic-field, the influence of low-frequency rotary electromagnetic-field on solidification structure of austenitic stainless steel in horizontal continuous casting was investigated based on industrial experiments. The results show that the solidification structure of austenitic stainless steel can be remarkably refined, the central porosity and shrinkage cavity can be remarkably decreased, and the equiaxed grains zone are enlarged by means of application of appropriate low-frequency electromagnetic-field parameters. The industrial trials verify that the stirring intensity of austenitic stainless steel should be higher compared with that of plain carbon steel. Electromagnetic stirring affects the macrostructure even if the average magnetic flux density of the electromagnetic stirring reaches 90 mT (amplitude reaches 141 mT) with the frequency of 3-4 Hz. Due to a higher viscosity, rotating speed of molten stainless steel is 20%-30% lower than that of molten carbon steel in the same magnetic flux density.
Key words:
1 Introduction
Horizontal continuous casting was originated from 1970s and firstly applied to producing non-ferrous metal. Afterward, it was developed rapidly in producing ferrous metal. Now industrialization of common steel and special steel produced by horizontal continuous casting have been achieved [1]. Austenitic stainless steels possess excellent properties and gain wide applications in industry. Currently, the solidification structure of austenitic stainless steel is one of the key issues that attract more attention. Due to the low thermal conductivity of austenitic stainless steel (much smaller than that of plain carbon steel), pronounced defects during horizontal continuous casting of austenitic stainless steel such as coarse columnar, center porosity and coarse bridging, greatly influence mechanical properties of finished products.
A widely used technique in metallurgy is the inductive drive of molten metals using rotational or traveling magnetic fields. Recently, rotary electromagnetic stirring (EMS) has been applied to improving the solidification structure of the metals in continuous casting steel, Al-based alloys and Mg-based alloys [2-4], molding and solidifying of casting, purifying of liquid melt. Fruits in both technology development and theoretical study have been obtained. Electromagnetic stirring of plain carbon and low alloy steel in the continuous casting bloom and slab is well established for improving the quality of cast products [5-7] and is widely used in industry. However, very few literatures on electromagnetic casting of austenitic stainless steel have reported the effects of electromagnetic stirring on austenitic stainless steel. The objects of this work are as follows: (1) to systematically study the effect of intensity and frequency of electromagnetic stirring on the solidification structure of austenitic stainless steel; (2) to discuss the regularity and mechanism of the influence of EMS on solidification casting billet.
2 Experimental
As shown in Fig.1, the experimental equipment consisted of 10 t tundish, rotary EMS and mold. Rotary EMS with inside diameter of 325 mm, outside diameter of 800 mm and height of 450 mm was installed beneath the mold (from 1 900 mold exit). The mold consisted of copper portion with length of 200 mm and a wall thickness of 8 mm and graphite portion with a length of 1 000 mm. The frequency of rotary EMS was modulated in the range of 0-10 Hz. The current of EMS was modulated in the range of 1-300 A.
Fig.1 Schematic diagram of experimental apparatus: 1—Stainless steel liquid; 2—Tundish; 3—Copper mold; 4—Graphite mold; 5—Rotary EMS
The speed of horizontal continuous casting machine was (1.0-1.4) m/min in all experiments; the preheating temperature of molten stainless steel was 45-55 ℃, and the magnetic flux densities were 0, 68, 70 and 90 mT, respectively. The stainless steel was refined and then poured into tundish. The d180 mm billet was produced. To assess the effects of EMS on the macrostructure of austenitic stainless steel more accurately, a plant trial was carried out on two strands cast at the same time with EMS and without EMS, separately.
3 Experimental results
3.1 Macrostructure of direct chill and electro- magnetic stirring billet
The macrostructures of the samples treated at different magnetic flux densities are shown in Fig.2. From the results of the experiments, it is noticed that the macrostructure of the billets with the electromagnetic stirring is finer than that of the billets with direct chill process. Fig.2(a) shows the coarse macrostructure of direct chill billet. Obviously, the macrostructures are characterized by coarse columnar grains, shrinkage cavity and columnar grains spreading almost the whole of billet. By contrast, casting under an electromagnetic field, the macrostructure of the billet is dominated by fine columnar and equiaxed grains as shown in Fig.2(c). In addition, EMS reduces centerline porosity and shrinkage cavity, and eliminates transcrystalline.
3.2 Effect of magnetic flux density on macrostructures
The macrostructure of EMS billets is fine columnar and equiaxed grains, as shown in Fig.2, and the macrostructures of the billets, in cross-section only, produced at various magnetic flux densities are reported. Figs.2(b)-(d) show the transition from very coarse columnar grains to finer columnar and to equiaxed grains as the magnetic flux density increases from 0 to 70 mT. But, once the magnetic flux density reaches a certain degree, such as 90 mT, the grain morphologies show apparent alternations, like the grains of the direct chill billets as shown in Figs.2(b) and (d).
4 Discussion
4.1 Measurements and analyses
The positioning of the EMS is critical. Proper position of EMS can greatly improve the effect of stirring on the quality of billet at given KVA input. So it is important to consider the evolutions of magnetic flux density with frequency and current. Magnetic flux density was measured within copper mold or graphite mold and beneath mold (from 1 900 mold exit) with different frequencies and currents by moving rotary EMS respectively. The measurement result of magnetic flux density is shown in Fig.3.
Fig.2 Macrostructures of austenitic stainless steel billets treated at different magnetic flux densities (B) and frequencies (f ): (a) B = 0 mT; (b) B=68 mT, f=4 Hz; (c) B=70 mT, f=7 Hz; (d) B=90 mT, f=3 Hz
Fig.3 shows that, the attenuation of magnetic flux density by the mold increases with its electrical conductivity such as copper (ρ=1.0×10-8 Ω?m) and graphite (ρ=1.0×10-6 Ω?m) at a given KVA input and stirrer diameter, which will increase the loss of magnetic flux density. According to actual measurement result with respect to magnetic flux density and shell thickness at mold exit, the position beneath mold is suitable for EMS, where shell thickness is about 15 mm.
Fig.3 Evolutions of magnetic flux density with frequency (I=240 A)
4.2 Effect of intensity and frequency of magnetic field on macrostructures
Generally, solidification in this work leads to two types of grain morphologies: columnar and equiaxed. When heat flows from the crystal into the undercooled melt (temperature gradient G<0), growth is generally equiaxed; When heat flows from the superheated melt into the cooler solid (G>0), growth is generally columnar [8].
According to solidification theory [9], the driving force for crystallization is expressed by:
(1)
And the degree of solute supercooling is expressed by:
(2)
where ?Tc is the degree of supercooling, ?Hm is the solidification latent heat, Tm is the melting temperature, is the alloy constant, m is the liquidus slope, c0 is solute concentration, R is the growth rate, x is the position of solidification front, G is the temperature gradient ahead of the solidification front, and D is solute diffusion coefficient (in liquid).
According to Eqns.(1) and (2), ?G will increase with the decrease of G and ?Tc. Therefore, temperature gradient (G) directly influences the type of grain morphologies. As shown in Fig.2(a), the solidification structure at the cross-section of the billet without EMS is coarse columnar grain. This is mainly due to considerable temperature gradient at the interface (G) in mold. Figs.2(b)-(d) are different for the magnetic flux density of EMS. The results suggest that the magnetic flux density of EMS has an obvious effect on the solidification structure.
Under the effect of the alternative current, the inductor generates a variable magnetic field in the melt, which, in turn, gives rise to induced currents well as an electromagnetic volume force. The force consists of two parts: the horizontal component and the vertical component. The vertical component of electromagnetic volume force is a rotational force derived from the inclination of the magnetic field lines toward the axis of the billet symmetry, which makes the low temperature melt near the mold move inwards to the center, and high temperature melt move outwards to the border. These result in a forced convection flow in the melt and a reduction of the temperature gradient ahead of the solidification front, which had been identified experimentally [10]. Therefore, the ideal flow pattern in the melt will be achievable when the overheated melt is driven from the center region of the melt to the periphery. All the effects can effectively refine the microstructures and broaden the equiaxed zone. For example, the dendritic can be remelted, detached and carried away by convection from the solidifying shell to the inner region of the melt, therefore, promote heterogeneous nucleation. So the structure of the casting billet with EMS is much finer than that of direct chill billet, as shown in Fig.2. When the magnetic flux density of EMS keeps increasing, the solidification structure of austenitic stainless has no obvious alternation until magnetic flux density reaches 90 mT as shown in Fig.2(d), which indicates that the volume force is too small. The electromagnetic stirring is a typical multiphase induction motor. The average volume force for a two-pole axisymmetric system is given by [11]:
(3)
where B is the magnetic flux density, σ is the electrical conductivity of the liquid metal, r is the radius of liquid pool, and ωs is the angular frequency of eddy current expressed as velocity slip.
According to Eqn.(3), the calculated electromagnetic force is shown in Fig.4. The notably increased volume force to the melt may be mainly attributed to an appropriate higher or an optimal frequency utilized in Fig.2(c). Therefore, these parameters will determine the input in KVA needed to generate required volume force. The effect of these parameters on the stirrer characteristics as well as metallurgical performance will be considered in context of their interaction rather than as an independent impact.
Fig.4 Evolutions of electromagnetic force with frequency and magnetic flux density
Fig.2(d) shows that the solidification structure of solidifying shell has no obvious effect, in spite of magnetic flux density growing. This is due to too weak stirring intensity. In order to enlarge equiaxed zones, reduce bridging and refine grain, the stirring intensity of the stirrer (i.e. the volume force) should be increased besides increasing magnetic flux density. Optimum frequencies and magnetic flux density can obtain a maximum internal volume force with a given KVA input and electrical conductivity. However, typically, actual operating frequencies are determined experimentally.
4.3 Effect of thermophysical properties of austenitic stainless steel on macrostructures
As shown in Fig.2, with application of electromagnetic stirring, the equiaxed and columnar grain sizes are found to be decreased, but the increase of the area of equiaxed grains is not obvious. There are mainly two reasons for this effect: the low thermal conductivity of stainless steel, as shown in Table 1 (a reduction of the temperature gradient in stainless steel melt by the magnetic forced convection is too small); and high kinematic viscosity of stainless steel, as shown in Table 1. In the low frequency and low induction limit, the magnetic Taylor number Ta can be taken as the characteristic non-dimensional parameters to describe the flow field. The Taylor number is given by [10]:
(4)
where ρ and υ denote the density and the kinematic viscosity of the fluid, separately.
The heat transfer coefficient, due to convection, increases with increasing Taylor number. A distinct
Table 1 Thermophysical properties of melt steel used in calculation [12-13]
reduction of the temperature gradient with growing Taylor number becomes visible, indicating a thermal homogenisation of the melt. Based on Eqn.(4), the magnetic Taylor number Ta of stainless steel is 40% lower than that of plain carbon steel at a given KVA input and dimensional parameters of the stirrer. Moreover, the stirring velocity calculated by the formula suggested by QI et al [11] is shown in Fig.5. Due to a higher viscosity, rotating speed of molten stainless steel is 20%-30% lower than that of molten carbon steel at the same magnetic flux density, which has been identified experimentally [14]. So a reduction of the temperature gradient of stainless steel billets is low, leading to that growth is columnar grains generally.
Fig.5 Calculated distribution of stirring velocity in cross-sectional view
5 Conclusions
(1) Under the low-frequency rotary electromagnetic- field, the rotary volume force produces a forced convection flow in the melt, as well as a reduction of the temperature gradient at the ahead of the solidification, which facilitates heat transfer and mass transfer as well as uniformity of shell solidifying shell.
(2) Stirring intensity produced by EMS and its metallurgical performance at a given KVA input are determined by the relationships between intensity and frequency of magnetic field and the electrical conductivity of the melt.
(3) EMS with appropriate electromagnetic stirring parameters reduces centerline porosity and shrinkage cavity, removes transcrystalline, improves the width of equiaxed grains zone, provokes a distinct grain refinement, but the increase of the area of equiaxed grain zone is not obvious as expected.
(4) Electromagnetic stirring affects on macro- structure of austenitic stainless steel, even if the magnetic flux density of the electromagnetic stirring reaches 90 mT in average (amplitude reaches 141 mT) at frequency of 3-4 Hz.
References
[1] HAISSIG M.Horizontal continuous casting: A technology for the future [J]. Iron Steel Eng, 1984, 61(6): 65-71.
[2] BIRAT J P, CHONE J. Electromagnetic stirring on billet, bloom and slab continuous casters: State of the art in 1982 [J]. Ironmaking and Steelmaking, 1983, 10 (6): 401-408.
[3] LIU Sheng-fa, KANG Liu-gen, HAN Hui, LIU Lin-yan, ZOU Xiao-qiang, GUO Hong-he. Influence of electromagnetic stirring on microstructure of AZ91-0.8%Ce magnesium alloy [J]. J Cent South Univ Technol, 2006, 13(6): 613-617.
[4] YANG Jing, DANG Jing-zhi, PENG You-gen, CHENG Jun. Design method of electromagnetic field applied to Al-alloy electromagnetic casting [J]. Trans Nonferrous Met Soc China, 2006, 16(S): s1437-s1441.
[5] TAKEHIKO T, EIICHI T, MASATAKE H, HIROYUKI K, SHOGO M. Electromagnetic control of initial solidification in continuous casting of steel by low frequency alternating magnetic field [J]. ISIJ International, 1997, 37(11): 1112-1119.
[6] CHO Y W, OH Y J, CHUNG S H, SHIM J D. Mechanism of surface quality improvement in continuous cast slab with rectangular cold crucible mold [J]. ISIJ International, 1998, 38(7): 723-729.
[7] KOLESINCHENKO A F, KOLESICHENKO A A, BURYAK V V. Improvement of in mold electromagnetic stirrer by feeding of magnetic system with polyharmonic current [J]. ISIJ International, 2004, 44(2): 342-349.
[8] KURZ W, BEZENCON C, G?UMANN M. Columnar to equiaxed transition in solidification processing [J]. Science and Technology of Advanced Materials, 2001, 2(1): 185-191.
[9] LI Qing-Chun. The theoretical foundation of casting forming [M]. Beijing: China Machine Press, 1982. (in Chinese)
[10] WILLERS B, ECKERT S, MICHEL U, HAASE I, ZOUHAR G. The columnar-to-equiaxed transition in Pb-Sn alloys affected by electromagnetically driven convection [J]. Materials Science and Engineering A, 2005, A402(1/2): 55-65.
[11] QI Ya-li, JIA Guang-lin, ZHANG Guo-zhi. Effect of electromagnetic stirring on liquid metal fluid flow and solidification structure [J]. Foundry Technology, 2005, 26(2): 118-120. (in Chinese)
[12] KEISUKE F. In-mold electromagnetic stirring in continuous casting [J]. IEEE Transactions on Industry Application, 2001, 37(4): 1098-1104.
[13] MILLS K C, SU Y C, LI Z S, BROOKS R F. Equations for the calculation of the thermo-physical properties of stainless steel [J]. ISIJ International, 2004, 44(10): 1661-1668.
[14] ZHONG Yun-bo, MENG Xian-jian, NI Dan, REN Zhong-ming, DENG Kang, XU Kuang-di. Experimental study on purifying molten steel by superimposing rotating magnetic field [J]. Shanghai Metals, 2006, 28(2): 9-14. (in Chinese)
(Edited by YANG You-ping)
Foundation item: Project(CSTC2007BB4216) supported by the Natural Science Foundation of Chongqing, China
Received date: 2008-07-23; Accepted date: 2008-11-11
Corresponding author: ZHOU Shu-cai, PhD; Tel: +86-13102345792; E-mail: zhoushucai71@126.com
- Effect of low-frequency rotary electromagnetic-field on solidification structure of continuous casting austenitic stainless steel
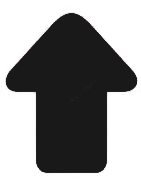