- Abstract:
- 1 Introduction▲
- 2 Experimental ▲
- 3 Results and discus...▲
- 4 Conclusions▲
- References
- Figure
- Fig.1 XRD patterns of 10NiO-NiFe2O4 composites doped with CaO and sintered at 1 200 ℃
- Fig.2 SEM image of 10NiO-NiFe2O4 composite doped with 4.0%CaO
- Fig.3 Effect of CaO contents on relative density and linear shrinkage ratio of 10NiO-NiFe2O4 composites
- Fig.4 SEM images of 10NiO-NiFe2O4 composites sintered at 1 200 ℃
- Fig.5 Linear shrinkage ratio of samples sintered at various sintering temperatures
- Fig.6 Linear shrinkage ratio of samples sintered at 1 150 ℃ for various holding time
J. Cent. South Univ. Technol. (2007)05-0629-04
DOI: 10.1007/s11771-007-0120-2
Densification and sintering dynamics of
10NiO-NiFe2O4 composites doped with CaO
LI Jie(李 劼), ZHANG Gang(张 刚), LAI Yan-qing(赖延清), ZHANG Yong(张 勇), TIAN Zhong-liang(田忠良)
(School of Metallurgical Science and Engineering, Central South University, Changsha 410083, China)
Abstract:The effects of CaO content in the range from 0 to 4.0%, and sintering temperature on the phase composition, relative density and electrical conductivity of 10NiO-NiFe2O4 composites doped with CaO were studied. The results show that there is no change of structure for NiO or NiFe2O4; there is apparent oxygen absorbing and releasing behavior during the heating process in air for 10NiO-NiFe2O4 composites. Introduction of CaO can accelerate the densification of 10NiO-NiFe2O4 composites. The maximum value of relative density is 98.75% for composite doped with 2.0% CaO and sintered at 1 200 ℃, which is beyond about 20% for the undoped composites. The sintering activated energy of sample containing 2% CaO decreases by 15.87 kJ/mol, compared with that of the undoped sample.
Key words:
aluminum electrolysis; inert anode; CaO doping; densification; sintering dynamics ;
1 Introduction
The application of inert anode and wettable cathode to replace the carbon anode and cathode in Hall-Heroult electrolysis cells has been an important approach to save energy and increase productive efficiency. The electrolysis of aluminum generally happens in cryolite melt at 960 ℃, so the envisaged inert anode should have high electrical conductivity, high electrocatalytic activity, good thermal stability, low chemical leachability, and low overvoltage for oxygen evolution[1-3].
In recent years, the cermet has become one of the most promising inert anode materials due to its high ceramic corrosive resistance and metallic conductivity. NiFe2O4 is the first choice as ceramic matrix for cermet inert anode because of its good performance including high melt point, good corrosive resistance, stably thermal and chemical property[2]. The pilot scale of 6 000 A experiment[4], with the support by US Department of Energy, exposed the weak corrosive resistance and unsatisfied thermal shock resistance. The densification of material is the principle factor to affect its corrosive performance. Generally, the electrolyte is easy to erode and destroy the electrode with low density. Hence, it is important to increase densification of material for improving its corrosive resistance and other properties.
Sintering is an effective method to increase densification of composite. GHOSH et al[5] obtained 99% densification in magnesium aluminate by spinel using ZnO as additive and suggested that the formation of anion vacancy in the presence of ZnO improves density and mechanical properties. RITWIK et al[6] observed that densified temperature for magnesium aluminate spinel decreased about 100 ℃ by addition of Cr2O3 up to 1.0%. JIAO et al[7] reported a gradual improvement in sintered density for NiFe2O4 products by addition of TiO2 up to 1% and above which no further betterment was observed. XI et al[8] pointed out that addition of MnO2 increases sintering density of NiFe2O4. They also found refined grain and improved thermal shock resistance for composite containing MnO2. So it can be seen that the addition has great influence on the sintering process and microstructure of composite.
In this paper, in order to obtain low-temperature densified sintering of 10NiO-NiFe2O4, 10NiO-NiFe2O4 composites doped with CaO were fabricated by cold pressing sintering. The effects of CaO content on the densification and microstructure of composites were investigated.
2 Experimental
2.1 Preparation of 10NiO-NiFe2O4 composites doped CaO
10NiO-NiFe2O4 composites doped with CaO (CaO/ 10NiO-NiFe2O4) composites were prepared by the conventional ceramic method with reagent grade raw materials of Fe2O3, NiO and CaO. The mixture of Fe2O3 and NiO in the molar ratio of 1.35 was mixed and calcined in a muffle furnace at 1 200 ℃for 6 h in static air atmosphere to form 10NiO-NiFe2O4 ceramic powder. The synthesized powders and CaO powder were ground in the mediums containing dispersant and adhesive. The mass fraction of CaO is 0, 0.5%, 1.0%, 2.0% and 4.0%, respectively. The dried mixtures were compacted at a pressure of 200 MPa to get cylindrical blocks (d20 mm×45 mm). Then the composites were sintered at 1 050-1 400 ℃ for 4 h in nitrogen atmosphere of efficaciously controlled oxygen partial pressure[9-10].
2.2 Characterization of composites
Phase compositions were identified by X-ray diffraction analysis using Philips PW1390 X-ray diffractometer with Cu Kα radiation. Microstructure was analyzed with JSM-6360LV scanning electron microscope and EDX-GENESIS energy dispersive spectrometer. Bulk densities were tested according to the Archimedes’ method.
3 Results and discussion
3.1 Phase analysis and microstructure of 10NiO- NiFe2O4 composites doped with CaO
X-ray diffraction patterns of 10NiO-NiFe2O4 composites doped with CaO are shown in Fig.1. It is observed only NiO and NiFe2O4 phases for all composites doped with different content of CaO. It is known that Ca2+ is soluble in NiFe2O4 to some extent and CaFe2O5 is formed by adding a certain amount of CaO[11]. However, for X-ray diffractometer it is hard to detect CaO because the additive ratio is close to the detection limit of 4.0%.
Fig.1 XRD patterns of 10NiO-NiFe2O4 composites doped with CaO and sintered at 1 200 ℃
1—Undoped sample, 2—Sample doped with 0.5% CaO; 3—Sample doped with 1.0% CaO; 4—Sample doped with 2.0% CaO; 5—Sample doped with 4.0% CaO
Fig.2 shows the microstructure for sample doped with 4.0% CaO. The dark-gray region of A and light-gray region of B represent NiFe2O4 and NiO, respectively. Moreover, the calcium element of 1.0% is found in both regions A and B, detected by energy spectra analysis, which suggests that CaO may exist in both ceramic matrix and grain boundary.
Fig.2 SEM image of 10NiO-NiFe2O4 composite doped with 4.0%CaO
3.2 Sintering mechanism
Fig.3 shows the relative densities and linear shrinkage ratios of samples doped with various contents of CaO. From Fig.3, it is clear the relative densities and linear shrinkage ratios for samples doped with CaO are apparently higher than those of the undoped sample. This with implies that addition of CaO has an active effect on densification of 10NiO-NiFe2O4 composites. The maximum relative density of 98.75% and linear shrinkage ratio of 13.52% are obtained by addition of CaO up to 2.0%. Addition of CaO content beyond 2.0% shows a decrease of relative density and linear shrinkage ratio.
Fig.3 Effect of CaO contents on relative density and linear shrinkage ratio of 10NiO-NiFe2O4 composites
For 10NiO-NiFe2O4 composite, the firing process belongs to solid sintering due to the melt points of the oxides beyond the sintering temperature. So the vacancy and defect become the driving force of diffusion and sintering[12-16]. It seems that in Fig.4(a) pure ceramic sintered at 1 200 ℃ is of low density because it cannot supply strong driving force of sintering just by bulk phase or grain boundary diffusion, which results in unexpected segregation and weak bonding strength of particles. Additionally, many connected pores in matrix represent the sintering process unfinished. However, the samples doped with 2.0% CaO in Fig.4(b) shows almost full densification due to the tight combination of particles and removing of pores. Based on thermodynamics calculation, it concludes that CaO can react with Fe2O3 at about 1 000 ℃ to generate Ca2Fe2O5, which appears liquid phase below 1 200 ℃. So the sample doped with CaO achieves densification by means of dissolution and separation of this liquid phase, which is used as transferred carrier to accelerate mass mobility and viscous flow.
Fig.4 SEM images of 10NiO-NiFe2O4 composites sintered at 1 200 ℃
(a) Undoped composite; (b) Composite doped with 2.0% CaO
Results of energy dispersive spectroscopy on the samples containing 4.0% CaO show that about 1.0% Ca2+ exists in ceramic region. That is to say, 1.4% CaO goes into the NiFe2O4 spinel grains by solid solution, which suggests that the excess CaO remains at the grain boundary to hind the further densification. It is revealed from the above study that about 2.0% CaO is beneficial for the densification of 10NiO-NiFe2O4.
3.3 Sintering dynamics
In order to study the sintering dynamics of 10NiO-NiFe2O4 composites with and without CaO, the linear shrinkage ratios of composites sintered at various temperatures and hold for 4 h are shown in Fig.5; and the linear shrinkage ratios of composites sintered at 1 150 ℃ and hold for various time are shown in Fig.6. From Fig.5, the linear shrinkage ratio increases with increasing sintering temperature for undoped samples. However, for samples containing 2.0% CaO, the linear shrinkage ratio achieves the largest value of 13.52% at 1 200 ℃ and thereafter decreases with increasing temperature. From Fig.6, the similar trend, which the linear shrinkage increases with prolonging holding time, is observed both in samples with and without CaO.
Fig.5 Linear shrinkage ratio of samples sintered at various sintering temperatures
Fig.6 Linear shrinkage ratio of samples sintered at 1 150 ℃ for various holding time
The above results show that the effect of sintering temperature and holding time on sintering properties of samples is mainly related with shrinkage of pore and grow-up of grains. Although raising temperature provides the required dynamic condition of solid reaction, in final sintering stage, the speed of grow-up of grain exceeds the speed of disappearance of pore, which results in the decrease of relative density.
According to the dynamic equation presented by KINERY[17], the sintering process of ceramics can be estimated by the activated energy.
(1)
where ΔL/L0 is linear shrinkage ratio; q is reaction order; t is sintering time; E is activated energy; T is sintering temperature; A is a constant related with boundary tension, diffusion coefficient and particle size; R is ideal gas constant.
At the certain temperature, the natural logarithm of linear shrinkage ratio(ΔL/L0) and holding time (t) are used to construct curves. According to the rate of slope, the values of reaction order (q) for 10NiO-NiFe2O4 and 2.0CaO/10NiO-NiFe2O4 samples, are 1.57 and 1.45, respectively. On the other hand, the natural logarithm of linear shrinkage (ΔL/L0) and reciprocal temperature are used to make the other curves. According to the rate of slope, the values of activated energy (E) for 10NiO-NiFe2O4 and 2.0CaO/10NiO-NiFe2O4 samples, are 29.47 and 13.60 kJ/mol. Obviously, the activated energy of samples doped 2.0%CaO is lower than that of undoped sample, which suggests that addition of sintering aid can improve the densification efficiently at low temperature.
4 Conclusions
1) With CaO addition in the mass fraction range of 0-4.0%, the composites consist of NiO phase and NiFe2O4 phase. However, there is about 1.0% calcium dispersed in NiFe2O4 and NiO regions.
2) Introduction of CaO could accelerate the densification of 10NiO-NiFe2O4 composites. The maximum relative density of 98.75% and linear shrinkage ratio of 13.52% are obtained by addition of CaO up to 2.0%. Addition of CaO content beyond 2% shows a decrease of relative density and linear shrinkage ratio.
3) Addition of 2.0%CaO achieves the purpose of activated sintering of 10NiO-NiFe2O4. The sample containing 2.0%CaO achieves the sintering activated energy up to 13.60 kJ/mol, which is decreased by 15.87 kJ/mol compared with that of undoped sample.
Reference[1] GRAY P T. Corrosion and passivation of cermet inert anodes in cryolite-type electrolytes[C]// MILLER R E. Light Metals. Warrendale, PA: TMS, 1986: 309-320.
[2] LIU Ye-xiang. Advance on the research and development of inert anode and wettable cathode in the aluminum electrolysis[J]. Light Metals, 2001(5): 26-29. (in Chinese).
[3] PAWLEK R P. Inert anodes: An update[C]// SCHNEIDER W. Light Metals. Warrendale, PA: TMS, 2002: 449-456.
[4] XIAO H, HOVLAND R, ROLSETH S, et al. Studies on the corrosion and the behavior of inert anodes in aluminum electrolysis[J]. Metallurgical and Materials Transactions B: Process Metallurgy and Materials Processing Science, 1996, 27 (2): 185-193.
[5] GHOSH A, DAS S K, BISWAS J R, et al. The effect of ZnO addition on the densification and properties of magnesium aluminum spinel[J]. Ceramics International, 2000, 26(6): 605-608.
[6] RITWIK S, KUMAR D S, GOUTAM B. Effect of addition of Cr2O3 on the properties of reaction sintered MgO-Al2O3 spinels[J]. Journal of the European Ceramic Society, 2002, 22(8): 1243-1250.
[7] JIAO Wan-li, ZHANG Lei, YAO Guang-chun, et al. Sintering process of NiFe2O4 spinel with and without TiO2 adding[J]. Journal of the Chinese Ceramic Society, 2004, 32(9): 1150-1153. (in Chinese)
[8] XI Jin-hui, LIU Yi-han, YAO Guang-chun. Effect of MnO2 on properties of inert anode of NiFe2O4 spinel [J]. Journal of Functional Materials, 2005, 3(36): 374-376. (in Chinese)
[9] LAI Yan-qing, ZHANG Gang, LI Jie, et al. Effect of adding Cu-Ni on mechanical capacity and electrical conductivity of NiFe2O4-based cermets[J]. Journal of Central South University: Natural Science, 2004, 35(6): 880-884. (in Chinese)
[10] LI Jie, ZHANG Gang, YE Shao-long, et al. Effect of metallic content on mechanical property of Ni/(10NiO-NiFe2O4) cermets [J]. Journal of Central South University of Technology, 2006, 13(4): 347-351.
[11] Junzo T, Toyohiko I. Effect of additives on magnetization of ferrites[C]// HIROSHI W. Ferrite: Proceedings of International Conference. Tokyo: D Reidel Publishing Company, 1980.
[12] Huang Pei-yun. Powder Metallurgical Theory[M]. 2nd ed. Beijing: Metallurgical Industrial Press, 1997. (in Chinese)
[13] Shi Jian-lin. Progress in the study of solid state sintering theory of ceramics[J]. World Science Technology Research and Development, 1998, 20(5): 124-128. (in Chinese)
[14] Shi Jian-lin. Solid state sintering-Ⅱ: Relation between coarsening and densification and mass transport path[J]. Journal of the Chinese Ceramic Society, 1997, 25(6): 657. (in Chinese)
[15] Lu Pei-wen. Inorganic Material Science Foundation[M]. Wuhan : Wuhan University of Technology Press, 1996. (in Chinese)
[16] FAN Jin-lian, HUANG Bo-yun, ZHANG Chuan-fu. Densification and grain growth of nano-structured tungsten alloy powder during pressureless sintering[J]. Journal of Central South University of Technology: Natural Science, 2001, 32(4): 390-393.(in Chinese)
[17] Kinery W D, Yeqer T A. The equilibrium defect structure of iron-doped MgO in the range 600-1 200 ℃[J]. Journal of Materials Science, 1981,16(2): 489-494.
Foundation item: Project (2005CB623703) supported by the National Key Fundamental Research and Development Program of China; Project (50474051) supported by the National Natural Science Foundation of China;Project (03JJY3080) supported by the Natural Science Foundation of Hunan Province, China
Received date: 2007-03-20; Accepted date: 2007-05-23
Corresponding author: ZHANG Gang, Doctoral candidate; Tel: +86-731-8830474; E-mail: zg0805@163.com
(Edited by YANG Hua)
- Densification and sintering dynamics of 10NiO-NiFe2O4 composites doped with CaO
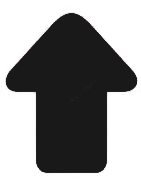