- Abstract:
- 1 Introduction▲
- 2 Experimental▲
- 3 Arrhenius constitutive ...▲
- 4 Results and discussion▲
- 5 Conclusions▲
- References
- Figure
- Fig.1 Relationship between true stress and true strain of non-oriented electrical steel at different strain rates: (a)10 s-1; (b) 1 s-1; (c)0.1 s-1; (d)0.01 s-1
- Fig.2 Relationship between steady flow stress and deformation temperature at different strain rates
- Fig.3 DSC curve of non-oriented electrical steel
- Fig.4 Microstructures of non-oriented electrical steel deformed at strain rate of 1 s-1 and different temperatures: (a) 500 ℃; (b) 800 ℃; (c) 1 050 ℃; (d) 1 150 ℃
- Fig.5 Microstructures of non-oriented electrical steel deformed at 800 ℃ and different strain rates: (a) 10 s-1; (b) 1 s-1; (c) 0.1 s-1; (d) 0.01 s-1
- Fig.6 Relationship among ln σ and σ: (a) Relationship between and ln σ in temperature range of 500-800 ℃; (b) Relationship between and ln σ in temperature range of 1 050-1 200 ℃; (c) Relationship between and σ in temperature range of 500-800 ℃; (d) Relationship between and σ in temperature range of 1 050-1 200 ℃
J. Cent. South Univ. Technol. (2009) 16: 0025-0031
DOI: 10.1007/s11771-009-0004-8
High temperature plastic deformation behavior of non-oriented electrical steel
XIAO Yu-de(肖于德)1, LI Min(李 敏)1, WANG Wei(王 伟)1,
ZHOU Juan(周 娟)1, WU Guang-liang(吴光亮)2, PENG Yue-ming(彭跃明)2
(1. School of Materials Science and Engineering, Central Sourth University, Changsha 410083, China;
2. Hunan Valin Lianyuan Iron and Steel Company, Lianyuan 417722, China)
Abstract:
High temperature plastic deformation behavior of non-orientated electrical steel was investigated by Gleeble 1500 thermo-mechanical simulator at strain rate of 0.01-10 s-1 and high temperature of 500-1 200 ℃. The stress level factor (α), stress exponent (n), structural factor (A) and activation energy (Q) of high temperature plastic deformation process of non-orientated electrical steel in different temperature ranges were calculated by the Arrhenius model. The results show that, with dynamic elevation of deformation temperature, phase transformation from α-Fe to γ-Fe takes place simultaneously during plastic deformation, dynamic recovery and dynamic recrystallization process, leading to an irregular change of the steady flow stress. For high temperature plastic deformation between 500 and 800 ℃, the calculated values of α, n, A, and Q are 0.039 0 MPa-1, 7.93, 1.9×1018 s-1, and 334.8 kJ/mol, respectively, and for high temperature plastic deformation between 1 050 and 1 200 ℃, the calculated values of α, n, A, and Q are 0.125 8 MPa-1, 5.29, 1.0×1028 s-1, and 769.9 kJ/mol, respectively.
Key words:
non-oriented electrical steel; plastic deformation; flow stress;
1 Introduction
Flow stress is one of important factors determined plastic deformation ability of the metal. During high temperature deformation process, the flow stress is related to work hardening, dynamic recovery and dynamic recrystallization of the metal. Meanwhile, variation of the relationship between strain and stress suggests evolvement of the microstructure to some degree [1-4].
Because of excellent magnetic properties and processing abilities, cold rolled non-oriented electrical steel is served as an important material for motors, rectifiers, and small transformer. Currently, Japan and Germany hold the key technology to produce electrical steel products with high performance. With combination of domestic markets with aboard markets, the market for the energy saving electrical machines is huge. At present, many ways have been tried to enhance magnetic properties of the electrical steel, including design of materials, heat treatment and control of cast process, dispersed precipitation, and hot/cold roll process [5-9].
Hot roll is one of very important processes for producing high level electrical steel. However, high temperature plastic deformation behavior for the non-oriented electrical steel is seldom reported deeply. In this work, the relationship between true stress and true strain of the electrical steel was obtained by hot compression. Based on the model of AF(σ)exp? [-Q/(RT)] [10-15], Zener-Hollomon constitutive relationship of high temperature plastic deformation of non-oriented electrical steel was established by statistical regression.
2 Experimental
The samples used for hot compression were prepared from the as-cast ingots. The chemical composition is shown in Table 1. The samples were machined to cylinders of d8 mm×15 mm. The thermo-mechanical simulation was carried out at strain rate of 0.01-10 s-1 and high temperature of 500-1 200 ℃ in Gleebe-1500 thermo-mechanical simulator. The samples were heated at a heating rate of 10 ℃/s and insulated for 5 min before deformation. The deformation mode was signal pass uniaxial hot compression and the maximum deformation ratio was 60%. To avoid oxidation of the sample, the experiments were carried out in the protection of argon gas atmosphere. The deformed samples were quenched immediately in water after hot compression. The microstructures of the samples were observed on a Polyvar-MET metallographic microscope after being eroded by nitric acid alcohol solution (3% HNO3+97% C2H5OH, volume fraction). The longitudinal section was selected as the observation section. In addition, an SDTQ600 simultaneous thermal analyzer was utilized to analyze thermal behavior of phase transfor- mation during heating at a heating rate of 10℃/min in the protective atmosphere of Ar gas.
Table 1 Chemical composition of non-oriented electrical steel (mass fraction, %)
3 Arrhenius constitutive model for high tem- perature plastic deformation
The relationship between steady flow stress (σ) and strain rate of high temperature plastic deformation can be described as follows [10, 16-17].
At low stress level,
(1)
At high stress level,
(2)
In the whole stress range,
(3)
where n, β, A1, and A2 are constants; n is stress exponent; R is gas constant, R =8.314 J/(mol·K); T is absolute temperature; and Q is the deformation activation energy. Eqn.(3) is Arrhenius constitutive equation. By partial derivative of Eqn.(3), the deformation activation energy (Q) can be described by
(4)
where and
are
the slopes of ln[sinh(ασ)]— and ln[sinh(ασ)]—1/T, respectively. For high temperature deformation, the deformation temperature (T) and the strain rate
can be described by[18-19]
(5)
where Z is Zener-Hollomon parameter, and Z can be obtained from Eqn.(5) after the activation energy (Q) is calculated.
In addition, the relationship between Z and σ can be described as
(6)
And Eqn.(6) can be modified to Eqn.(7),
(7)
By linear regression, A and n can be obtained.
According to definition of the hyperbolic sinh(x)= (ex-e-x)/2, Eqn.(6) can be modified to a function of Z, which is called as Zener-Hollomon constitutive relationship,
(8)
4 Results and discussion
4.1 True stress—true strain curve and steady flow stress—temperature curve during high tempera- ture deformation
The relationship between true stress (σ) and true strain of the non-oriented electrical steel is shown in Fig.1. Obvious peak flow stresses are observed on the σ—
curves of high temperature deformation. The curves exhibit typical characteristics of dynamic recrystallization. However, an irregular change of the peak or steady flow stress with deformation temperature increasing is observed in Fig.1. Steady flow stress at 800 ℃ is lower than that at 900 ℃ in the condition of the given strain rates (0.01-10 s-1). Hence, the steady flow stress—temperature curve is shown in Fig.2. With rising temperature, the steady flow stress declines firstly, and then increases, and finally decreases.
Fig.1 Relationship between true stress and true strain of non-oriented electrical steel at different strain rates: (a)10 s-1; (b)
1 s-1; (c)
0.1 s-1; (d)
0.01 s-1
Fig.2 Relationship between steady flow stress and deformation temperature at different strain rates
Thermal behavior determined by an SDTQ 600 simultaneous thermal analyzer is shown in Fig.3. It indicates the temperature of phase transformation from α-Fe to γ-Fe is about 900 ℃(being close to 913 ℃ for pure iron) at a heating rate of 20 ℃/min. In this sense, during high temperature plastic deformation, phase transformation from α-Fe to γ-Fe takes place, accompanied by plastic deformation, dynamic recovery and dynamic recrystallization, in a certain high temperature range nearby 900 ℃. Hence, in the temperature range of 500-800 ℃, the electrical steel material is fully composed of α-Fe single phase. With elevation of temperature, dynamic recovery and recrystallization take place, resulting in declining of α-Fe flow stress. During plastic deformation in the higher temperature range, dynamic recrystallization and grain growth should be more intensive, and it should lead to more obvious declining of flow stress. However, with deformation temperature rising into the range of 800-950 ℃, phase transformation of α-Fe to γ-Fe may cause grains of Fe matrix to become fine and grain size distribution to be inhomogeneous, which in fact leads to enhancement of flow stress. This result is consent with the result in Ref.[20]. With further increase of temperature, transition amount of phase transformation from α-Fe to γ-Fe increases gradually, and even γ-Fe grain grows rapidly. After phase transformation finishes,γ-Fe grain coarsens and its size becomes uniform, the steady flow stress is still inclined to decline. Therefore, the steady flow stress exhibits an irregular change with the increase of temperature in the range of 800-950 ℃. During high temperature deformation in the temperature range of 1 050-1 200 ℃, the flow stress declines with temperature arising. The material is almost in γ-Fe single phase region in this temperature range. Dynamic recrystallization of γ-Fe and its grain growth take place at higher temperature, resulting in further decreasing of high temperature flow stress.
Fig.3 DSC curve of non-oriented electrical steel
4.2 Evolution of microstructures during high tem- perature plastic deformation
Fig.4 shows microstructures of the electrical steel after being deformed at different temperatures and a strain rate of 1 s-1. The microstructure of the electrical steel still exhibits typical characteristics of deformed microstructure after being deformed at 500 ℃. However, with deformation temperature elevating to 800 ℃, most of the elongated grains have transformed into the equiaxed fine grains, which exhibits characteristics of dynamic recrystallization in α-Fe matrix. As deformation temperature continues increasing, the deformed structure is gradually replaced by recrystallized structure. After being deformed at 1 050 ℃, microstructure of the electrical steel is fully recrystallized grain structure to some degree. During high temperature deformation in the temperature range of 800-1 050 ℃, phase transition from α-Fe to γ-Fe takes place during heating and phase transition from γ-Fe to α-Fe occurs during cooling. Therefore, α-Fe grain is fine and the size distribution is inhomogeneous. As a result, in this temperature range, the flow stress behaves irregularly with temperature increasing at the same strain rate. When the deformation temperature continues rising to 1 150 ℃, the electrical steel sample after cooling to room temperature is composed of α-Fe with coarse grain structure, as shown in Fig.4(d), which is obtained from the undercooled γ-Fe with coarse grain, in which intensive recrystallizations and even obvious grain-growth at high temperature occur.
Fig.4 Microstructures of non-oriented electrical steel deformed at strain rate of 1 s-1 and different temperatures: (a) 500 ℃; (b) 800 ℃; (c) 1 050 ℃; (d) 1 150 ℃
Fig.5 shows microstructures of the electrical steel after being deformed at 800 ℃ and different strain rates. After being deformed at a strain rate of 10 s-1, the microstructure of the electrical steel is characterized by filamentary structure of α-Fe with little amount of recrystallized grain. With declining of the strain rate, the filamentary structure disappears gradually, and fine recrystallized grain appears. When the strain rate is 1 s-1, most of the filamentary structures are replaced by the recrystallized structures. When the strain rate decreases to 0.1 s-1, the structures are completely composed of fine recrystallized α-Fe grains. When the strain rate reduces to 0.01 s-1, the completely recrystallized grains grow obviously. This indicates that, dynamic recrystallization in the α-Fe matrix begins to occur at 800 ℃, and with strain rate decreasing, dynamic recrystallization takes place more fully. As a result, at the same deformation temperature, the flow stress declines with the decrease of strain rate.
Fig.5 Microstructures of non-oriented electrical steel deformed at 800 ℃ and different strain rates: (a) 10 s-1; (b)
1 s-1; (c)
0.1 s-1; (d)
0.01 s-1
4.3 Establishment of Zener-Hollomon constitutive relationship of high temperature plastic deformation
During plastic deformation in the temperature range of 800-1 050 ℃, the change of steady flow stress with elevation of temperature behaves irregularly, due to combined effect of plastic deformation, dynamic recrystallization of α-Fe and γ-Fe and phase transition between them. Therefore, it is difficult to establish an integral model for quantitative analysis of the constitutive relationship of the electrical steel. Since there are two different ranges, 500-800 ℃ and 1 050- 1 200 ℃, the constitutive equations may be established respectively in the two deformation temperature ranges. The stress level exponent (α), stress exponent (n), structure factor (A) and activation energy (Q) in the temperature ranges of 500-800 ℃ and 1 050-1 200 ℃ are calculated, respectively.
According to Eqns.(1) and (2), n and β can be obtained by linear regression, as shown in Fig.6. Since α can be calculated from α=β/n, in the temperature range of 500-800 ℃, α=0.039 0; and in the temperature range of 800-1 050 ℃, α=0.125 8.
Fig.6 Relationship among ln σ and σ: (a) Relationship between
and ln σ in temperature range of 500-800 ℃; (b) Relationship between
and ln σ in temperature range of 1 050-1 200 ℃; (c) Relationship between
and σ in temperature range of 500-800 ℃; (d) Relationship between
and σ in temperature range of 1 050-1 200 ℃
According to Eqn.(4), by linear regression, the activation energy (Q) can be obtained by taking the mean value of the slopes of —
and
—1/T. The activation energy (Q) is 334.8 kJ/mol during plastic deformation in the temperature range of 500-800 ℃ and 769.9 kJ/mol in the temperature range of 1 050-1 200 ℃. As shown in Fig.7, during plastic deformation in the temperature ranges of 500-800 ℃ and 1 050-1 200 ℃, the linear correlation factors of linear regression for both ln [sinh (ασ)]—
and ln [sinh (ασ)]—1/T are larger than 0.93. This suggests that the relationship among flow stress, strain rate and deformation temperature during plastic deformation of the non-oriented electrical steel can be described by Eqn.(3).
Flg.7 Relationship among ln [sinh (ασ)], and 1/T: (a) Relationship between ln [sinh (ασ)] and
in temperature range of 500-800 ℃; (b) Relationship between ln [sinh (ασ)] and
in temperature range of 1 050-1 200 ℃; (c) Relationship between ln [sinh (ασ)] and 1/T in temperature range of 500-800 ℃; (d) Relationship between ln [sinh (ασ)] and 1/T in temperature range of 1 050-1 200 ℃
Z can be obtained according to Eqn.(5) after the deformation conditions are given and the values of Q are calculated. By linear regression, as shown in Fig.8, the stress exponent (n) and the structure factor (A) can be obtained from the slope and the intercept of ln Z and ln [sinh (ασ)] relationship, respectively. During plastic deformation in the temperature range of 500-800 ℃, n and A are 7.93 and 1.9×1018 s-1, respectively; and during plastic deformation in the temperature range of 1 050-1 200 ℃, n and A are 5.29 and 1.0×1028 s-1, respectively.
Flg.8 Relationship between ln Z and ln [sinh (ασ)] in different temperature ranges: (a) 500-800 ℃; (b) 1 050-1 200 ℃
The linear correlation factors of linear regression for ln Z and ln [sinh (ασ)] relationships are larger than 0.99, which indicates that Zener-Hollomon constitutive relationship can well describe high temperature plastic deformation behavior of the electrical steel.
Therefore, in the temperature range of 500-800 ℃, the Zener-Hollomon constitutive relationship is as follows:
(9)
and in the temperature range of 1 050-1 200 ℃,
(10)
5 Conclusions
(1) In the temperature range of 500- 800 ℃, the electrical steel is composed of α-Fe single phase. With temperature rising, dynamic recovery and dynamic recrystallization take place in α-Fe matrix during high temperature plastic deformation, resulting in the decrease of steady flow stress. In the temperature range of 800- 1 050 ℃, with elevation of temperature, phase transition from α-Fe to γ-Fe takes place, accompanied by plastic deformation, dynamic recovery and dynamic recrystallization of Fe matrix, and thus change of the flow stress behaves irregularly. In the temperature range of 1 050-1 200 ℃, intensive dynamic recrystallization and even grain growth of γ-Fe matrix occur, and thus the steady flow stress decreases obviously with elevation of deformed temperature. At the same deformation temperature, the steady flow stress declines with the decrease of strain rate.
(2) The calculated values of stress exponent (n), stress level exponent (A) and activation energy (Q) obtained by Arrhenius constitutive equation agree well with the experiment data. The high temperature deformation process of low grade electric steel can be described by the Zener-Hollomon constitutive relationship based on the Arrhenius constitutive model.
(3) During plastic deformation in the temperature range of 500-800 ℃, the stress level exponent (α), stress exponent (n), structure factor (A), and activation energy (Q) are 0.039 0 MPa-1, 7.93, 1.9×1018 s-1, and 334.8 kJ/mol, respectively. During plastic deformation in the temperature range of 1 050-1 200 ℃, these are 0.125 8 MPa-1, 5.29, 1.0×1028 s-1, and 769.9 kJ/mol, respectively.
References
[1] COLAS R. A model for the hot deformation of the low-carbon steel [J]. Journal Materials Process and Technology, 1996, A62(1/3): 180-184.
[2] XIAO Yu-de, WANG Wei, LI Wen-xian. High temperature deformation behavior and mechanism of spray deposited Al-Fe-V-Si alloy [J]. Trans Nonferrous Met Soc China, 2007, 17(6): 1175-1180.
[3] LIN Qi-quan, PENG Da-shu, ZHANG Hui, LIN Gao-yong. Dynamic and static softening behaviors of 2519 aluminum alloy during multi-stage hot compression deformation [J]. Journal of Central South University: Science and Technology, 2005, 36(2): 183-187. (in Chinese)
[4] WANG Jin, CHEN Jun, ZHAO Zhen, RUAN Xue-yu. Hot deformation behavior and flow stress model of F40MnV steel [J]. Journal of Central South University of Technology, 2007, 14(1): 19-23.
[5] SIDOR Y, KOVAC F. Microstructural aspects of grain growth kinetics in non-oriented electrical steels [J]. Materials Characterization, 2005, 55(1): 1-11.
[6] KOVAC F, DZUBINSKY M, SIDOR Y. Columnar grain growth in non-oriented electrical steels [J]. Journal of Magnetism and Magnetic Materials, 2004, 269(3): 333-340.
[7] PAOLINELLI S C, CUNHA M A D. Effect of stress relief annealing temperature and atmosphere on the magnetic properties of silicon steel [J]. Journal of Magnetism and Magnetic Materials, 2006, 304(2): e599-e601.
[8] CHANG S K. Texture change from primary to secondary recrystallization by hot-band normalizing in grain-oriented silicon steels [J]. Mater Sci Eng A, 2007, A452/453(2): 97-98.
[9] HOUBAERT Y, ROS-YANEZ T, MONSALVE A, LORENZO J B. Texture evolution in experimental grades of high-silicon electrical steels [J]. Physica B, 2006, 384(1/2): 310-312.
[10] POIRIER J P. Hot plastic deformation of crystal [M]. GUAN De-lin, trans. Dalian: Dalian University of Technology Press, 1989: 218-224.
[11] RAO K P, HAWBOLT E B. Development of constitutive relationship using compressing testing of medium carbon steel [J]. Journal of Materials and Process Technology, 1992, 114(3): 116-123.
[12] PETER A L, RICHARD P D. An artificial neural network approach to multiphase continua constitutive modeling [J]. Composites (Part B): Engineering, 2007, 38(7/8): 817-823.
[13] LIN J, DEAN T A. Modelling of microstructure evolution in hot forming using unified constitutive equations [J]. Journal of Materials Processing Technology, 2005, 167(2/3): 354-362.
[14] MCQUEEN J, RYAN N D. Constitutive analysis in hot working [J]. Mater Sci Eng A, 2002, A322(1/2): 43-63.
[15] MA A, ROTERS F, RAABE D. On the consideration of interactions between dislocations and grain boundaries in crystal plasticity finite element modeling—Theory, experiments, and simulations [J]. Acta Material, 2006, 54(8): 2181-2194.
[16] CASTEO-FERNANDEZ F R, SELLAR C M, WHITEMAN J A. Change of stress and microstructure during hot deforming of Al-Mg-1Mn [J]. Material Science and Technology, 1990, 6(5): 453-460.
[17] JONAS J, SELLARS C M, TEGART W J, MC G. Strength and structure under hot working condition [J]. Int Metal Reviews, 1969, 130(14): 1-24.
[18] IMBERT C, RYAN N D, MCQUEEN H J. Hot workability of the three grade of tool steel [J]. Metal Tran A, 1984, 15(10): 1855-1864.
[19] MILOVIC C, MANOJLOVIC D, ANDJELIC M. Hot workability of M2 type high-speed steel [J]. Steel Research, 1992, 63(2): 78-84.
[20] ZHANG Wen-kang, MAO Wen-min, WANG Yi-de, XUE Zhi-yong, BAI Zhi-hao. Influence of hot-rolling parameters on microstructure and magnetic properties of non-oriented electrical steel [J]. Iron and Steel, 2006,41(4): 77-81. (in Chinese )
Foundation item: Project(2005038560) supported by the Postdoctoral Foundation of China; Project(05GK1002-2) supported by Key Program of Hunan Province
Received date: 2008-05-11; Accepted date: 2008-07-20
Corresponding author: XIAO Yu-de, Professor, PhD; Tel: +86-731-8830261; E-mail: xiaoyude@mail.csu.edu cn
(Edited by CHEN Wei-ping)
- High temperature plastic deformation behavior of non-oriented electrical steel
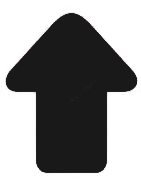