- Abstract:
- 1 Introduction▲
- 2 Experimental▲
- 3 Framework of hypoplasti...▲
- 4 Gudehus-Bauer hypoplast...▲
- 5 Stress-path hypoplastic...▲
- 6 Model verification ▲
- 7 Conclusions ▲
- References
- Figure
- Fig.1 Grading curves of rockfill
- Fig.2 Stress paths of constant stress ratio
- Fig.3 Complex stress paths with transitional features
- Fig.4 Failure line under different complex stress paths
- Fig.5 Relationship between α and cos θ
- Fig.6 Calculated and measured results of σ1—ε1 (a) and εv—ε1 (b) under paths of constant stress ratio
- Fig.7 Calculated and measured results of q—ε1 (a) and εv—ε1 (b) under No.1 complex stress path
- Fig.8 Calculated and measured results of q—ε1 (a) and εv—ε1 (b) under No.2 complex stress path
- Fig.9 Calculated and measured results of q—ε1 (a) and εv—ε1 (b) under No.3 complex stress path
- Fig.10 Complex stress paths at σ3t=0.8 MPa
- Fig.11 Calculated and measured results of q—ε1 (a) and εv—ε1 (b) under complex stress paths with σ3t=0.8 MPa
J. Cent. South Univ. Technol. (2009) 16: 1006-1013
DOI: 10.1007/s11771-009-0167-3
An improved hypoplastic constitutive model of
rockfill considering effect of stress path
XIANG Biao(相 彪)1, ZHANG Zong-liang(张宗亮)2, CHI Shi-chun(迟世春)1
(1. School of Civil and Hydraulic Engineering, Dalian University of Technology, Dalian 116024, China;
2. HydroChina Kunming Engineering Corporation, Kunming 650051, China)
Abstract:
An incrementally nonlinear hypoplastic constitutive model was introduced, which was developed without recourse to the concepts in elastoplasticity theory such as yield surface, plastic potential and the decomposition of the deformation into elastic and plastic parts. Triaxial drained tests on rockfill were conducted on a large scale triaxial apparatus under two types of stress paths, which were the stress paths of constant stress ratio and the complex stress paths with transitional features. Motivated by the effect of stress path, the Gudehus-Bauer hypoplastic model was improved by considering the parameter variations with different ratios of stress increment. Fitting parameter α presents a piecewise linear relationship with cosine of the slope angle θ determined by instantaneous stress path. The improved hypoplastic model can present peak stress increasing and volumetric strain changing from dilatancy to contractancy with the increase of transitional confining pressure σ3t and the decrease of slope angle θ of stress path. Compared with the test data, it is shown that the model is capable of fully considering the effect of stress path on rockfill.
Key words:
hypoplasticity; constitutive model; stress path; triaxial drained test; rockfill;
1 Introduction
Rockfill dams have become popular in the last 30 years as a result of their good performance and low cost compared with earth dams. A key factor in the engineering design of rockfill dams is the prediction of the deformation induced during dam construction and reservoir filling. It is well known that the behaviors of rockfill are nonlinear, inelastic and stress-path dependent[1-2]. Many researchers carried out a series of stress-path tests and analyzed the deformation cha- racteristics induced by different stress paths[3-7]. They suggested that the stress path in laboratory tests must be approximately consistent with that in the practical engineering, from which it was possible to describe the actual constitutive relationship of soils more accurately.
Current researches indicate that the stress path of rockfill during dam construction can be approximated as that the stress ratio keeps constant (q/p is constant, where deviatoric stress q=(σ1-σ3) and mean principal stress p=(σ1+2σ3)/3), and it will become a transitional stress path (dq/dp is constant) during reservoir filling. Under the above actual stress path, the stress—strain relationships of different rockfill elements present significant differences. Therefore, it is necessary to consider the effect of stress path in the constitutive modelling of rockfill.
At present a large number of constitutive models with different levels of sophistication and complexity have been proposed to describe the mechanical behavior of soils, but most of the models cannot reflect the influence of stress path. When the models are examined, it is evident that the capacity of the models has been gained at the cost of their simplicity because of the complex mathematical formulations and the increasing number of model parameters. From the practical point of view, a constitutive model capable of reproducing the essential features, although not all facets, of the material behavior with simpler mathematical formulations and fewer material parameters is to be favoured.
The hypoplastic constitutive model described in the framework of continuum theory is based on simple nonlinear tensorial functions and is developed without the concepts in elastoplastic theory such as yield surface, plastic potential and the decomposition of the deformation into elastic and plastic parts. The idea of using nonlinear tensorial functions to describe the mechanical behavior of conhesionless sand was pioneered by KOLYMBAS[8]. In the later work by WU and KOLYMBAS[9], the definition of hypoplasticity was given and the general form of hypoplastic constitutive model was proposed. Remarkable progress was achieved by WU and BAUER[10] where the critical state was integrated into the hypoplastic model to account for the effect of stress level and initial density on the mechanical behavior of sand.
In this paper, the work of GUDEHUS[11] and BAUER[12] was extended to some degree. The GUDEHUS-BAUER hypoplastic model was improved by considering the parameter variation, which depended on the ratio of stress increment (dq/dp) under instantaneous stress paths. The capability of the improved hypoplastic model was demonstrated by comparing with the test data of rockfill under complex stress paths.
2 Experimental
The rockfill sample was obtained from Nuozadu Hydropower Station located at Lancang River in Yunnan Province, China, which was used as the main rockfill of core-dam body. Visual inspection indicates that the sample is hard and compact with good weatherability and erosion resistance, which belongs to a kind of high quality rockfill. The maximum particle size is 800 mm with fine content (<5 mm) of about 7%. The physical and mechanical properties of rockfill are listed in Table 1. The grading curves of specimens are plotted in Fig.1.
Table 1 Physical and mechanical properties of rockfill
Note: ρs is specific density; and e0 is initial void ratio.
Fig.1 Grading curves of rockfill
The large scale triaxial apparatus was adopted in the present study with a specimen height of 65.5 cm and a diameter of 30.2 cm. The test state is saturated and drained, which is consistent with the practical working conditions of dam rockfill. Therefore, all the stresses denote the effective stresses and the described stress paths represent the effective stress paths of rockfill.
One type of tests was conducted under the paths of constant stress ratio (CSR) starting from zero initial stress state (q/p=dq/dp=constant). Using an automated pressure controller, the specimens were loaded continuously under the target stress ratio until the confining pressure σ3 reached 2.5 MPa. There are six stress ratios in the tests, which are listed in Table 2, and the stress paths are shown in Fig.2.
Table 2 Stress ratios under paths of constant stress ratio
Fig.2 Stress paths of constant stress ratio
Another type of tests was conducted under complex stress paths with transitional features. The stress ratio before path transition also kept constant with q/p=dq/dp=1.00. Subsequently, the stress paths changed their ratios of stress increment to different directions. Some transitional paths moved close to the failure line and the others moved away from it. The tests included four transitional points corresponding to four transitional confining pressures of σ3t=0.3, 0.8, 1.4 and 2.0 MPa, where subscript t was the transitional meaning and there were three different forms of transitional paths starting from each transitional point. Thus, there were altogether 12 tests under complex stress paths. All the tests were ended until failure occurred or the confining pressure σ3 reached 2.5 MPa. The complex stress paths are shown in Fig.3, and the detailed ratios of stress increment in the tests are listed in Table 3.
The stress points in the failure state are plotted in Fig.4. The failure line presents a linear relationship in p-q plane, and the slope of which is about 1.60. It is worth noticing that the strain softening is not significant in the tests and all the failure stress—strain curves present strain hardening. Therefore, the failure line in Fig.4 approximates to the critical state line of the investigated rockfill.
Fig.3 Complex stress paths with transitional features
Table 3 Ratios of stress increment under complex stress paths
Fig.4 Failure line under different complex stress paths
3 Framework of hypoplasticity
。
The hypoplastic constitutive model was assumed by WU and KOLYMBAS[9] that there existed a tensorial function H such that
where σ is the Cauchy stress tensor; is the strain rate tensor; and σ is the Jaumann stress rate defined as follows:
where spin tensor and strain rate
are related to velocity ν:
where stands for the gradient and superscript T denotes a transposition. Furthermore, it is required that function H in Eq. is not differentiable in and only in condition of
=0.
Throughout the paper, a superposed dot implies material time differentiation. To comply with the sign convention in soil mechanics compressive stress, shortening strain and their rates are taken as positive.
It was shown by WU and BAUER[10] that the following tensorial function was suitable for capturing the incremental nonlinear behavior of granular materials,
where ||?|| denotes the Euclidean norm and the colon : denotes an inner product between two tensors. Eq. consists of two parts, namely a linear tensorial function L(σ): in
and a nonlinear function N(σ)||
|| in
. The main properties of hypoplastic constitutive model based on Eq. can be found from the work by WU and BAUER[10, 13].
4 Gudehus-Bauer hypoplastic model
The effect of void ratio is manifested in various kinds of tests in soil mechanics laboratory. In most constitutive models proposed in the past, granular materials with different initial void ratios were simply treated as different materials. The material constants in the model need to be re-identified if the initial void ratio varies. It is desirable to identify the material constants in the constitutive model for just one given void ratio, and the constants remain valid for the whole spectrum of void ratios ranging from the loosest to the densest packing. In order to achieve this aim, the hypoplastic constitutive equation is assumed to depend on the void ratio,
To make a specific representation of the hypoplastic model more transparent and the calibration easier, a factorized representation of Eq. was proposed by GUDEHUS[11] and BAUER[12], which can be written as
In Eq. the influence of the void ratio e and the mean pressure p is taken into account by density factor fd and stiffness factor fs. Tensorial equation can be reduced to two equations of scalar arguments in traxial condition[14],
(7)
(8)
where subscript 1 denotes the axial direction and subscript 3 denotes the radial one. Scalar factors fs and fd can be expressed as follows:
(9)
(10)
where hs, n, α and β are model parameters, and
(11)
There is a unique relationship between constant a1 and friction angle φc in the critical state,
(12)
The term in the bracket of factor fd in Eq.(10) can be considered as a pressure-dependent relative void ratio. Herein ei, ed and ec are the maximum, the minimum and the critical void ratios, respectively. The void ratios ei, ed and ec reach the limit values ei0, ed0 and ec0 at vanishing mean pressure, and they approach zero for very high p:
(13)
There are eight parameters in the Gudehus-Bauer hypoplastic model, which are φc, hs, n, ed0, ec0, ei0, α and β. The parameter determination of the model can be found from the work by HERLE and GUDEHUS[15]. The model accounting for the effect of void ratio and mean pressure can describe many mechanical properties of sand materials.
5 Stress-path hypoplastic model of rockfill
From the simulations of large amount of traxial tests on rockfill with the Gudehus-Bauer model, it is found that the calculated volumetric strain is too small because of the significant characteristics of contractancy and dilatancy of rockfill. From the recent work by CEN et al[16-17], a volumetric-strain controlling variable btr() was introduced into linear function L(σ):
in Eq., where b was another parameter to control volumetric strain. Therefore, according to Eqs.(7) and (8), the updated scalar relationship of Gudehus-Bauer model can be expressed as
(14)
(15)
where in triaxial condition.
There are six basic parameters in the updated version of Gudehus-Bauer model, which are φc, hs, n, ed0, ec0 and ei0. The basic parameters describe the intrinsic properties of rockfill materials and are independent of stress path, which keep constant under different forms of stress paths. Therefore, for considering the effect of stress path, our attention was paid to the variations of the fitting parameters α, β and b under different stress paths.
As the model parameters are large in number and their relationships are complex to some degree, using standard optimization algorithm to determine model parameters is usually computationally expensive in terms of both memory requirement and speed, and cannot obtain satisfying solutions. In this paper a particle swarm optimization (PSO) algorithm[18] was employed to determine all the model parameters, which was proved to present good performance.
PSO was firstly developed by EBERHART and KENNEDY[19], its original concept came from the movement of organisms in bird swarm. In the algorithm, each potential solution to a problem is called a “particle”. In this work each particle contains all the information of model parameters. According to Eqs.(14) and (15), the optimizer calculates the strain increments and compares with test data to obtain the error. Through iteration process, the particles are updated until the best fitness of test data reaches and the model parameters are finally obtained.
Great efforts were devoted to determine all the nine parameters in the updated version of Gudehus-Bauer model under the stress paths of different ratios of stress increment. From the analysis on the fitting parameters α, β and b, a significant phenomenon is found that parameter α varies regularly with ratio of stress increment, while parameters β and b keep constant. A variable (θ) is defined as the slope angle of instantaneous stress path in p-q plane,
θ=arctan(dq/dp) (0≤θ<π) (16)
Thus, each stress path with certain ratio of stress increment can be represented by a relevant angle θ. The slope angle θc of critical state line in p-q plane can be expressed by the critical friction angle φc,
(17)
The relationship between α and cos θ is shown in Fig. 5. A remarkable characteristic is found that if the stress path cannot reach the failure line, the slope angle θ of stress path will be less than the slope angle θc of critical state line (θ<θc and cos θ>cos θc). Under this condition parameter α linearly increases with the increase of cos θ. However, if the stress path reaches the failure line (θ>θc and cos θ<cos θc), parameter α will keep constant in a wide range of cos θ. The plotted points in Fig.5 present two distinct linear relationships based on the dividing point of cos θc in horizontal coordinate axis. Therefore, a piecewise linear expression between α and cos θ was proposed to describe the variation of parameter α with the slope angle θ of instantaneous stress path.
where parameter α is replaced by α1 and α2 and one more parameter is introduced in the Gudehus-Bauer hypoplastic model.
For a conclusion, according to the work by CEN [16], parameter b is added to control volumetric strain so that the Gudehus-Bauer model is suitable for describing the mechanical behavior of rockfill materials. Through considering the variation of parameter α with slope angle θ of stress path, the Gudehus-Bauer model is improved to consider the effect of stress path. There are altogether 10 parameters in the improved hypoplastic model, which are basic parameters of φc, hs, n, ed0, ec0, ei0 and fitting parameters of α1, α2, β, b, respectively.
Fig.5 Relationship between α and cos θ
6 Model verification
The model parameters were calibrated by using the test data at constant stress ratios of dq/dp=0.75, 1.20, and 1.50 and transitional stress paths of dq/dp=3.00 and -1.50 under the transitional confining pressure of σ3t=2.0 MPa, which are summarized in Table 4. The verification of the parameters was achieved by recalculating laboratory tests including other cases that were not used for the parameter determination. Therefore, the calculations could be considered as genuine predictions.
Table 4 Parameters of improved Gudehus-Bauer model
Measured and calculated results under the paths of constant stress ratio are summarized in Fig.6. The calculated stress—strain curves are close to the measured ones except some discrepancies for the case dq/dp=1.50. During the process of confining pressure σ3 reaching 2.5 MPa, the maximum principal stress σ1 continuously increases and no failure occurs in the whole range of axial strain under each constant stress ratio, while the calculated volumetric—strain curves present linear relationships that accord with the test data.
Outputs of the tests under complex stress paths with transitional features are shown in Figs.7-9. It can be seen that the calculations reproduce the test behaviors reliably except some differences in volumetric—strain curves in case of σ3t=0.3 MPa in Figs.7(b) and 9(b). Under No.2 complex stress path, the ratio of stress increment after transition is dq/dp=0.75, which is less than the slope of the failure line (dq/dp=1.60). Therefore, the transitional stress path cannot reach the failure line, and both the deviatoric stress and the volumetric strain continuously
Fig.6 Calculated and measured results of σ1—ε1 (a) and εv—ε1 (b) under paths of constant stress ratio
Fig.7 Calculated and measured results of q—ε1 (a) and εv—ε1 (b) under No.1 complex stress path
Fig.8 Calculated and measured results of q—ε1 (a) and εv—ε1 (b) under No.2 complex stress path
increase in the whole range of axial strain, which is consistent with the loading mode of constant stress ratio before path transition (see Fig.8). For No.1 and No.3 complex stress paths, the transitional stress paths reach the failure line and the deviatoric stress cannot increase infinitely. Each stress—strain curve reaches a plateau at a large axial strain and the amplitudes of deviatoric stress increase distinctly with the increase of transitional confining pressure while the volumetric—strain curves change from final dilatancy to progressive contractancy regularly (see Figs.7 and 9). The calculated results clearly reflect the influence of the stress history before path transition (different σ3t) on the constitutive relation- ships under different forms of transitional stress paths.
Fig.9 Calculated and measured results of q—ε1 (a) and εv—ε1 (b) under No.3 complex stress path
To show the effect of different transitional stress paths at the same transitional confining pressure, taking the transitional confining pressure of σ3t=0.8 MPa as example, three stress paths, test results and their recalculations are plotted in Figs.10 and 11, respectively. The results of the other three transitional confining pressures are similar to those in Fig.11, which are not listed herein. It can be seen from Fig.11 that with the increase of slope angle θ of stress path, the amplitude of
Fig.10 Complex stress paths at σ3t=0.8 MPa
Fig.11 Calculated and measured results of q—ε1 (a) and εv—ε1 (b) under complex stress paths with σ3t=0.8 MPa
deviatoric stress decreases obviously and the volumetric strain changes from continuous contractancy to final dilatancy regularly. Different forms of transitional stress path (different θ) make a great influence on the stress—strain—volume relationship curves of rockfill.
From the above model verification we can see that the improved Gudehus-Bauer hypoplastic model including 10 parameters can not only inherit the advantages of the previous versions of hypoplastic model but also conveniently describe the constitutive relationships of rockfill under the paths of constant stress ratio during dam construction and the transitional stress paths upon reservoir filling.
7 Conclusions
(1) The stress path of rockfill during dam construction can be approximated as the stress ratio keeps constant, and it will become a transitional stress path upon reservoir filling. Triaxial drained tests under complex stress paths are conducted to simulate the actual stress variations of dam rockfill in the practical work conditions.
(2) The hypoplastic constitutive model is represented by a stress—strain relationship embedded in a single tensorial equation without explicitly defining yield and plastic potential surfaces. In spite of its simplicity, a pressure and density coupling resulting in dilatancy, contractancy, failure state and variable stiffness can be reproduced. Based on the stress-path test data, the variation regularity of model parameters under different forms of stress paths is analyzed and the Gudehus-Bauer hypoplastic model is improved by considering the effect of stress path.
(3) The improved hypoplastic model can well predict the stress and deformation behaviors of rockfill under actual stress paths. The research in this work makes a beneficial attempt in constitutive modeling for practical engineering. In later work, the application of the model in the FEM analysis is to be concerned.
References
[1] MARACHI N D, CHAN C K, SEED H B, DUNCAN J M. Strength and deformation characteristics of rockfill materials[R]. Berkeley: University of California, 1969.
[2] DUNCAN J M, BYRNE P M, WONG K S, MABRY P. Strength, stress—strain and bulk modulus parameters for finite element analysis of stresses and movements in soil masses[R]. Berkeley: University of California, 1980.
[3] XU Ri-qing, GONG Xiao-nan. Nonlinear stress-path dependent behavior of soils[J]. Chinese Journal of Geotechnical Engineering, 1995, 17(4): 56-60.(in Chinese)
[4] PENG Fang-le, LI Jian-zhong. Modeling of state parameter and hardening function for granular materials[J]. Journal of Central South University of Technology, 2004, 11(2): 176-179.
[5] WANG Xue-bin. Unified analytical stress—strain curve for quasibrittle geomaterial in uniaxial tension, direct shear and uniaxial compression[J]. Journal of Central South University of Technology, 2006, 13(1): 99-104.
[6] NG W W, FUNG W T, CHEUK C Y, ZHANG L M. Influence of stress ratio and stress path on behavior of loose decomposed granite[J]. Journal of Geotechnical and Geoenvironmental Engineering, 2004, 130(1): 36-44.
[7] NG T T. Behavior of gravity deposited granular material under different stress paths[J]. Canadian Geotechnical Journal, 2005, 42(6): 1644-1655.
[8] KOLYMBAS D. A novel constitutive law for soils[C]//The 2nd International Conference on Constitutive Laws for Engineering Materials. New York: Elsevier, 1987: 319-326.
[9] WU W, KOLYMBAS D. Numerical testing of the stability criterion for hypoplastic constitutive equations[J]. Mechanics of Materials, 1990, 9(3): 245-253.
[10] WU W, BAUER E. Hypoplastic constitutive model with critical state for granular materials[J]. Mechanics of Materials, 1996, 23(1): 45-69.
[11] GUDEHUS G. A comprehensive constitutive equation for granular materials[J]. Soils and Foundations, 1996, 36(1): 1-12.
[12] BAUER E. Calibration of a comprehensive hypoplastic model for granular materials[J]. Soils and Foundations, 1996, 36(1): 13-26.
[13] WU W, BAUER E. A simple hypoplastic constitutive model for sand[J]. International Journal for Numerical and Analytical Methods in Geomechanics, 1994, 18(12): 833-862.
[14] VON W P A. Hypoplastic relation for granular materials with a predefined limit state surface[J]. Mechanics of Cohesive-Frictional Materials, 1996, 1(3): 251-271.
[15] HERLE I, GUDEHUS G. Determination of parameters of a hypoplastic constitutive model from properties of grain assemblies[J]. Mechanics of Cohesive-Frictional Materials, 1999, 4(5): 461-486.
[16] CEN Wei-jun. Hypoplastic modeling for rockfill and numerical analysis of concrete face rockfill dam[D]. Nanjing: College of Water Conservancy and Hydropower Engineering, Hohai University, 2005: 49-52.(in Chinese)
[17] CEN W J, WANG X X, BAUER E, ZHU Y M. Study on hypoplastic constitutive modeling of rockfill and its application[J]. Chinese Journal of Rock Mechanics and Engineering, 2007, 26(2): 312-322.(in Chinese)
[18] LI Liang. Application of intelligent optimization algorithms to the soil slope stability analysis[D]. Dalian: Dalian University of Technology, 2005: 36-41.(in Chinese)
[19] EBERHART R, KENNEDY J. New optimizer using particle swarm theory[C]//The 6th International Symposium on Micro Machine and Human Science. Piscataway: IEEE Service Center, 1995: 39-43.
(Edited by CHEN Wei-ping)
Foundation item: Projects(50479057, 50639060) supported by the National Natural Science Foundation of China
Received date: 2009-03-20; Accepted date: 2009-06-08
Corresponding author: XIANG Biao, PhD; Tel: +86-15912135845; E-mail: bxiangdlut@yahoo.com.cn
- An improved hypoplastic constitutive model ofrockfill considering effect of stress path
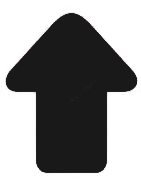