- Abstract:
- 1 Introduction▲
- 2 Experimental▲
- 3 Results and discussion▲
- 3.1 Effect of mass ratio of NaDEHP to NaDEHPOEP on wettability of cotton grey fabric in NaOH solution
- 3.2 Wettability of NaDEHP, NaDEHPOEP and NaDEHP-NaDEHPOEP at various concen- trations of NaOH
- 3.3 Surfactivity and wettability of NaDEHP- NaDEHPOEP in NaOH solution and relativity between surfactivity and wettability
- 3.4 Effect of NaDEHP-NaDEHPOEP in NaOH solution on morphology of cotton grey fabric
- 4 Conclusions▲
- References
- Figure
- Fig.1 Effect of mass ratio of NaDEHP to NaDEHPOEP in 3.75 mol/L NaOH solution on sinking time, capillary effect and alkaline resistance
- Fig.2 Capillary effect (a), immersion time (b) and sinking time (c) of NaDEHP, NaDEHPOEP and NaDEHP-NaDEHPOEP in NaOH solution
- Fig.3 Dependence of sinking time and surface tension (a) and capillary effect and surface tension (b) on concentration of NaDEHP-NaDEHPOEP in NaOH solutions
- Fig.4 SEM images of cotton grey fabric (a), wetted in 3.75 mol/L of NaOH solution (b), wetted in alkaline NaDEHP- NaDEHPOEP solution (c)
J. Cent. South Univ. Technol. (2010) 17: 924-929
DOI: 10.1007/s11771-010-0578-1
Wettability and surfactivity of sodium phosphate surfactants in strong alkali solutions
CHEN Sheng-hui(陈胜慧)1, 2, DONG Jin-feng(董金凤)1
1. College of Chemistry and Molecular Sciences, Wuhan University, Wuhan 430072, China;
2. Key Laboratory of Catalysis and Materials Science of the State Ethnic Affair Commission and Ministry of Education,
South-Central University for Nationalities, Wuhan 430074, China
? Central South University Press and Springer-Verlag Berlin Heidelberg 2010
Abstract:
The wettability, surfactivity and the correlation between wettability and surfactivity of sodium diethylhexylphosphate, sodium diethylhexyl polyoxyethylene phosphate and their complex in NaOH solutions were studied. A complex alkali resistant phosphate surfactant with good permeability was prepared. The wettability of surfactants was investigated by measuring the immersion time, sinking time and capillary effects of nature cotton grey fabric in NaOH solutions. The surfactivity of the surfactants was characterized by measuring the surface tension. The effect of the complex on the surface appearance of cotton grey fabric was also investigated with a scanning electron microscope (SEM). The results show that all the surfactants exhibit good wettability for cotton grey fabric in 0.5-5.0 mol/L of NaOH solutions, the complex system exhibits better wettability in 5.0-7.0 mol/L of NaOH solutions, in comparison with either corresponding single surfactant component employed, and wettability is well correlative with the surfactivities of the surfactant. SEM images indicate that the cotton grey fabric is well wetted by the alkaline surfactant solution and the quality of fabric is improved.
Key words:
1 Introduction
Surfactants are widely used in the fields of both traditional and high-technology industry. Most studies on surfactants were typically carried out in neutral aqueous solutions [1-2]. Nevertheless, surfactants are also extensively used in alkaline solutions. For instance, the following processes are usually carried out in alkaline solutions with varied concentrations of NaOH [3-5], namely, cotton fabric pre-treatment, enhanced oil recovery, waste-paper deinking and the degreasing of leather. So, the wettability of surfactants in strong alkaline solutions has been a subject of increasing attention.
Most of investigations on wettability of surfactants were all performed in aqueous solutions in the absence of alkali [6-8]. To our knowledge, less attention has been paid to the wettability of surfactants in strong alkaline solutions, such as NaOH solutions. The mixture of isooctanol phosphate, polar organic compounds and secondary alkyl sulfonate possessed good permeability, and the sinking time was 3-30 s in low concentration NaOH solutions of 0-1.0 mol/L [9]. Polyethoxylate phosphate could be used in higher concentration NaOH solutions of 3.0-6.0 mol/L [10-11], and the sinking time was 30-150 s, but the wetting power was relatively small. The complex of polyethoxylate phosphonate, secondary alkyl sulfonate and fatty alcohol polyoxyethyleneether exhibited good wettability within 7-30 s of the sinking time in 5.0-6.0 mol/L NaOH solutions [12-13]. However, the phosphonate surfactants synthesized above were the mixing compounds of mono-, di- and tri-alkyl phosphonate, and these mixing phosphonate’s properties were unstable. Contemporarily, they have merely done some basic tests on capability and application, and cannot lucubrate to interpret and expound the wetting mechanism and the influence on the wettability of surfactivity, concentration of NaOH as well as surfactants.
In this work, the alkaline resistance, wettability and surfactivity of the surfactants in aqueous caustic solutions were studied on the cotton grey fabric. Two types of sodium phosphate surfactants (Diethylhexyl phosphate (NaDEHP), diethylhexyl polyoxyethylene phosphate (DEHPOEP)) and their mixtures were used.
The relationship between the wettability on cotton grey fabric and the surfactivity in strong alkali liquor was investigated. And the effect of the complex surfactant on the surface microstructure of cotton grey fabric was also investigated with a SEM.
2 Experimental
2.1 Experimental materials
DEHP and DEHPOEP were purchased from Tokyo Chemical Industry (TCI, Japan). NaDEHP is a clear colorless viscous liquid, and DEHPOEP is a clear light yellow viscous liquid. They were neutralized with NaOH-alcohol solution and purified by the method of recrystallization in the acetone before use. NaDEHP- NaDEHPOEP was prepared by mixing the individual surfactants at the mass ratio of 3:7. Sodium hydroxide (AR, Sigma-Aldrich, USA) was used as received. Cotton grey fabric (18.22 tex×18.22 tex) was cut into pieces of about 1 cm×1 cm each.
2.2 Experimental methods
2.2.1 Wettability
The wettability of the surfactants in aqueous caustic solutions was investigated through measuring immersion time, sinking time and capillary effects of cotton grey fabric by the standard methods of GB/T5558— 1999, HG/T 2575—1994 or DIN EN 1772—2000, FZ/T 01071—2008 or DIN 53924—1997, respectively. A piece of cotton grey fabric was carefully placed on the top of the surfactant aqueous caustic solutions in the beaker. The immersion time into the liquid and the sinking time to the bottom of beaker of the fabric were measured with a stopwatch. To examine the capillary effect, a piece of grey fabric (30 cm×5 cm) was appended over the solution using clamps. The hemline (5 mm) of fabric was immerged into the solution. The water uptake of cotton fabric (cm) was measured by a ruler after 30 min.
2.2.2 Alkaline resistance
The alkaline resistance of the surfactants was measured by GB/T 5556—2003 standard method. The above described surfactants (0.01 mol/L) were separately dissolved in aqueous solutions of NaOH. Alkaline resistance was evaluated by observing the physical state of solutions at 25 ℃, herein, a clear solution implies the highest alkaline resistance grade, a cloudy solution implies alkaline resistance grade, and a precipitate or floating oil solution implies no alkaline resistance grade.
2.2.3 Surface tension
The surface tension of the surfactants in aqueous caustic solutions was measured by pendent drop method with a tensometer (DSA100, Kruss, Germany) at 25 ℃.
2.2.4 Scanning electron microscopy
The change of surface microstructure of cotton grey fabric treated with the surfactants-NaOH solutions was investigated by the scanning electron microscope (SEM, Hitachi X-650, Japan). The cotton fabric samples were wetted by one drop of the above alkaline-surfactant solutions, and then the samples were dried at room temperature and coated with Au. The accelerating voltage was 30 kV.
3 Results and discussion
3.1 Effect of mass ratio of NaDEHP to NaDEHPOEP on wettability of cotton grey fabric in NaOH solution
In practice production, fabrics are usually treated in NaOH solutions. Generally, the concentrations of NaOH used in these processes are in the range of 0.5-7.0 mol/L. In this work, 3.75 mol/L NaOH solution was used for the investigation of alkali-resistance and wettability of surfactants (0.01 mol/L), which was prepared by mixing NaDEHP and NaDEHPOEP at various mass ratios.
Fig.1 shows the effect of mass ratio of NaDEHP to NaDEHPOEP in NaOH solution on the alkali-resistance (three regions), sinking time and capillary effect. The wettability of a solution for the cotton grey fabric can be characterized by the sinking time and capillary effect. The shorter the sinking time and the larger the height of capillary effect, the better the wettability. As shown in Fig.1, the range of the surfactant complex could be divided into three regions according to the solution stability. In regionsⅠand Ⅲ, the solutions were phase separated, implying poor alkali-resistance. In region Ⅱ, the solution was clear, implying good alkali-resistance. When the mass ratio of NaDEHP to NaDEHPOEP was 3:7, the solutions were clear. Herein, the sinking time exhibited the lowest value (4.9 s) and the capillary effect exhibited the highest value (3.8 cm), indicating that the
Fig.1 Effect of mass ratio of NaDEHP to NaDEHPOEP in 3.75 mol/L NaOH solution on sinking time, capillary effect and alkaline resistance
NaDEHP-NaDEHPOEP (3:7, mass ratio) can be used as wetting agent of alkali-resistance. NaDEHP- NaDEHPOEP with a mass ratio of 3:7 was used for further experiments.
3.2 Wettability of NaDEHP, NaDEHPOEP and NaDEHP-NaDEHPOEP at various concen- trations of NaOH
The wettability of NaDEHP, NaDEHPOEP and NaDEHP-NaDEHPOEP at various concentrations of NaOH was studied. The wettability of a solution for the cotton grey fabric can be characterized by the immersion time, sinking time and capillary effect. The better the wettability, the shorter the time required for immersion and sinking to occur and the larger the height of capillary effect. Figs.2(a), (b) and (c) show the capillary effect, immersion time and sinking time of the surfactants in 0.5-7.0 mol/L NaOH, separately.
As shown in Fig.2(a), when the concentration of NaOH solution was 0.5-5.5 mol/L, the capillary effect of the cotton grey fabric in the system of three surfactants was 3-7 cm, indicating good wetting. When the concentration of NaOH solution was 5.5-7.0 mol/L, the capillary effect of NaDEHP and NaDEHPOEP decreased rapidly to 1-3 cm, indicating that their wettability became weakened obviously. But the capillary effect of the complex of NaDEHP-NaDEHPOEP was about 3 cm yet, which demonstrated that the complex exhibited better wettability. As shown in Fig.2(b), when the concentration of NaOH solution was 0.5-5.0 mol/L, the immersion time of the cotton grey fabric in the system of three surfactants was 1-2 s, and much the same all. When the concentration of NaOH solution was 5.0-7.0 mol/L, the immersion time of NaDEHP, NaDEHPOEP and NaDEHP-NaDEHPOEP increased to 19, 7 and 4 s, separately, indicating that the mixing surfactant possessed better wetting power. As shown in Fig.2(c), when the concentration of NaOH solution was 0.5-5.0 mol/L, the sinking time of the cotton grey fabric in the system of three surfactants was 2-10 s, indicating that the three surfactants possessed good wetting power. When the concentration of NaOH solution was 5.0 mol/L, the sinking time of NaDEHP increased quickly above 120 s, indicating that the wettability weakened considerably. For 5.0-6.0 mol/L NaOH solution, the sinking time of NaDEHPOEP and NaDEHP- NaDEHPOEP was 10-30 s, exhibiting good wettability. The experimental results showed that the complex of NaDEHP-NaDEHPOEP possessed better wettability in higher concentration (5.5-7.0 mol/L NaOH) strong alkaline solutions than the individual surfactants of the NaDEHP and NaDEHPOEP.
Fig.2 Capillary effect (a), immersion time (b) and sinking time (c) of NaDEHP, NaDEHPOEP and NaDEHP-NaDEHPOEP in NaOH solution
There was a special phenomenon here. When the concentration of NaOH increased, the wettability of the surfactants weakened and the sinking time became longer. When the concentration of NaOH solution reached 5.5-7.0 mol/L, the sinking time of the three surfactants was above 120 s (Fig.2(c)), indicating poor wetting. But at the same time, the immersion time became shorter, which was 7-19, 5-7 and 3-4 s (Fig.2(b)) separately, indicating good wetting. The reason why the fabric cannot sink to the bottom may be that the concentration of NaOH was too high and the density of the solution was larger, rather than that the wetting power was devitalized in the case of high concentration strong alkali. The wettability of surfactants-NaOH solution still kept good level.
3.3 Surfactivity and wettability of NaDEHP- NaDEHPOEP in NaOH solution and relativity between surfactivity and wettability
The surfactivity and wettability of NaDEHP- NaDEHPOEP at various concentrations in 3.75 mol/L NaOH solution were studied, and the relativity between surfactivity and wettability was also investigated.
Figs.3(a) and (b) show the dependence of the sinking time and the surface tension, the dependence of the capillary effect and the surface tension on the concentration of NaDEHP-NaDEHPOEP in NaOH solutions, separately. The general trend is that, in all cases, the surface tension and the sinking time rigorously decrease and then levels off with the increase of surfactant concentration, while the capillary effect follows the opposite direction. It is apparent that there exists notable relationship between the wettability and surfactivity.
Fig.3 Dependence of sinking time and surface tension (a) and capillary effect and surface tension (b) on concentration of NaDEHP-NaDEHPOEP in NaOH solutions
For NaDEHP-NaDEHPOEP, when the concentration was extremely low in a NaOH solution, such as 10-5 mol/L, the surface tension of the solution was 36.9 mN/m. When the concentration of the surfactant increased to 5×10-3 mol/L, the surface tension was roughly to 28.2 mN/m. Consequently, the sinking time reached a minimum value (4 s) and capillary effect reached a maximum value (3.8 cm). When the surfactant concentration was further increased, the surface tension, sinking time and capillary effect were essentially unchanged. This indicates that the complex of surfactant possesses good wetting power and surfactivity.
As shown in sections 3.2 and 3.3 above, the three surfactants all were of good wettablility in lower concentration NaOH (0.5-5.0 mol/L), but the complex surfactant exhibited better wettability than either single NaDEHP or NaDEHPOEP in higher concentration NaOH (5.0-7.0 mol/L). At the same time, the complex showed stronger surfactivity, and there was an obvious correlation between the surface tension and the sinking time as well as the capillary effect along with the increase of the concentration of surfactant. Those observations can be explained using the surface and colloid theory.
The adsorption of surfactants on the solution surface and at the interface between the fabric and liquid leaded to the reduction of interface (surface) tension and enhancement of wetting power. Natural cotton fiber contains hydrophobic compounds such as cotton wax, and pectin, which create more lipophilic and poor wetting in NaOH solutions. With addition of surfactants, some of the surfactant molecules were expelled to the surface and interface. At the interface, the hydrophobic groups of surfactants were adsorbed onto the surface of the fabric with the hydrophilic group oriented toward the aqueous phase, forming a close packed monolayer with the molecules perpendicular to the surface of fabric. On the surface of solution, the hydrophobic group escaped to the liquid and the hydrophilic group oriented toward the aqueous phase to form a close packed monolayer. The adsorption behavior resulted in the reduction of interface (surface) tension and enhancement of wettability.
For the charge on the surface of fabric, there was weaker polar group just as —OH, so the surface charge density was lower. While a close packed monolayer of surfactants at the interface was formed, the surface of the fabric was covered with a single layer of surfactant molecules, and the hydrophilic head groups of phosphonate negative ion increased fabrics’ surface charge density, making it more hydrophilic and wettable.
When NaOH is added, due to the reaction of static gravitation, the adsorption layer on the fabric with higher charge density of phosphonate negative ion could attract the ions of Na+ to form electrical double-layers which could attract OH- in the solution. Because of the strong interreaction between Na+ and OH- as well as surfactants, increasing the counterions’ concentration could decrease the electronic repulsions of surfactants’ head group ions, leading to rapidly decreasing the surface tension of solution and the interface tension between fabric and solution. Uniformity, surfactants were prone to adsorb onto the surface of fabrics and penetrate into the fabric, resulting in good wetablility in strong alkali solutions.
For the mixing surfactant, the interaction of two different types of surfactants with each other can result in synergistic enhancement of their interfacial properties. Such a synergistic enhancement can result in improved properties, such as surface activity, wetting, foaming, and solubilization [14]. In this case, the enhancement of the wetting of complex surfactant in strong alkali solution on cotton grey fabric is the result of synergistic interaction.
3.4 Effect of NaDEHP-NaDEHPOEP in NaOH solution on morphology of cotton grey fabric
In this portion, the cotton grey fabric was treated with a NaOH solution and a NaDEHP-NaDEHPOEP- NaOH solution, and screened for the appearance structure by a SEM. The results are shown in Fig.4.
Fig.4(a) shows the original morphology of cotton grey fabric without wetting. It is clear that there were many fibrils on the surface of the fabric, and the cotton fibre was not smooth and pliable. Fig.4(b) shows the SEM image of cotton grey fabric wetted in 3.75 mol/L NaOH solution. It is explicit that there still existed fibrils on the surface of the original cotton fabric, and the fiber surface shrank and corrugated substantially, normally leading to that the feature of spontaneous wetting became worse in practical production. Fig.4(c) shows the SEM image of cotton grey fabric wetted in the mixing phosphate surfactant-NaOH solution. It is explicit that the fibrils on the surface of the fabric disappeared and the fiber surface became even and lubricious without any shrinking. This indicates that the fabric treated in surfactant-NaOH solution can be wetted rapidly and uniformly. It is believed that this surface morphology is beneficial to the high quality of cotton fabric.
4 Conclusions
(1) Sodium diethylhexylphosphate, sodium diethylhexyl polyoxyethylene phosphate and their complex possess good alkaline resistance and wettability in lower concentration NaOH solutions of 0.5-5.0 mol/L. None but the complex NaDEHP-NaDEHPOEP exhibits excellent wettability in higher concentration NaOH solution of 5.5-7.0 mol/L.
(2) There is the same general trend between the surface tension and the sinking time as well as the
Fig.4 SEM images of cotton grey fabric (a), wetted in 3.75 mol/L of NaOH solution (b), wetted in alkaline NaDEHP- NaDEHPOEP solution (c)
capillary effect along with the increase of the surfactant’s concentration; consequently, there is an obvious correlation between the surfactivity and the wettability.
(3) Through the analysis of surface morphologies of cotton grey fabric wetted in NaDEHP-NaDEHPOEP alkali solution, the smooth surface without fibrils and shrinking is gained, which is beneficial to the high quality of cotton fabric.
References
[1] BUSCHLE-DILLER G, INGLESBY M K, WU Y. Physicochemical properties of chemically and enzymatically modified cellulosic surfaces [J]. Colloids Surf A,2005, 260(6): 63-70.
[2] FANG Bo, CAO Dan-hong, JIANG Ti-qian. Rheological properties of novel viscoelastic micelle systems containing anionic-nonionic dimeric surfactant [J]. Journal of Central South University of Technology, 2008, 15: 176-180.
[3] LIU J, VANDENBERGHE J, MASLIYAH J, XU Z, YORDAN J. Fundamental study on talc-ink adhesion for talc-assisted flotation deinking of wastepaper [J]. Minerals Engineering,2007, 20(5): 566-573.
[4] SUN Jing-lun, SUN Li-xin, LIU Wei-dong, LIU Xian-gui, LI Xin, SHEN Qiang. Alkaline consumption mechanisms by crude oil: A comparison of sodium carbonate and sodium hydroxide [J]. Colloids Surf A,2008, 315(2): 38-43.
[5] LEI Zheng-dong, YUAN Hi-yi, SONG Jie. Rheological behavior of alkali-surfactant-polymer/oil emulsion in porous media [J]. Journal of Central South University of Technology, 2008, 15: 462-466.
[6] ECKMANN D M, CAVANAGH D P, BRANGER A B. Wetting characteristics of aqueous surfactant-laden drops [J]. J Coll Interf Sci, 2001, 242: 386-394.
[7] DUTSCHK V, BREITZKE B, GRUNDKE K. Wetting of aqueous surfactant solutions on polymer surfaces [J]. Tenside, Surfactants, Deterg, 2003, 5: 250-255.
[8] SIMON?I? B, VERONIKA R. Wettability of cotton fabric by aqueous solutions of surfactants with different structures [J]. Colloids Surf A, 2007, 292: 236-245.
[9] HUANG Yan-ping, DI Qun-ying. Study on the preparation of alkali-resistant penetrant ND-96 [J]. Textile Auxiliaries, 2004, 21(2): 23-26. (in Chinese)
[10] LAI Hong-min; YU Xian-hu. Study on synthesis and performance of phosphates of high alkali-resistant penetrant [J]. Chemistry & Bioengineering, 2009, 26(3): 27-27. (in Chinese)
[11] AI Qiang, LI Nian-kang, QIAN Hao-liang, TAN Xiao-xian. Characteristics and application of high-efficient and alkali-resistant penetrant CHS [J]. Textile Auxiliaries, 2001, 18(4): 32-33. (in Chinese)
[12] CHEN Sheng-hui. Preparation and application of alkaline resistant penetrating agent CP [J]. Journal of Wuhan University of Science and Engineering, 2003, 16: 60-63. (in Chinese)
[13] ZHANG Xun-tian, LAN Shu-xian, FANG Dong-lin, LI Yuan-zhong. Preparation and application of alkaline resist penetrating agent [J]. Dyeing and Finishing, 2004, 30(14): 43-45. (in Chinese)
[14] ROSEN M J. Surfactants and interfacial phenomena [M]. Hoboken, New Jersey: John Wiley & Sons Inc, 2004: 35-38, 208-214, 258- 269.
(Edited by YANG You-ping)
Foundation item: Project(20573079) supported by the National Natural Science Foundation of China
Received date: 2010-01-29; Accepted date: 2010-05-07
Corresponding author: DONG Jin-feng, PhD, Professor; Tel: +86-27-68752702; E-mail: jfdong@whu.edu.cn
- Wettability and surfactivity of sodium phosphate surfactants instrong alkali solutions
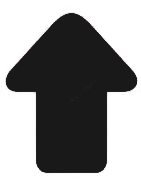