- Abstract:
- 1 Introduction▲
- 2 Experimental proce...▲
- 3 Results and discus...▲
- 4 Conclusions▲
- References
- Figure
- Fig. 1 Microstructure of SiC foam ceramics
- Fig. 2 Variation in corrosion rates with corrosion time for samples after static immersion in 3.5% NaCl aqueous solution at room temperature
- Fig. 3 Micro-morphology and XRD patterns of composite B before static immersion corrosion tests:
- Fig. 4 Images of corroded surface after static immersion in 3.5% NaCl solution for 7 d at room temperature:
- Fig. 5 Images of corroded surface after static immersion in 3.5% NaCl solution for 30 d at room temperature:
- Fig. 6 XRD patterns after static immersion in 3.5% NaCl solution for 30 d:
- Fig. 7 Corrosion mechanism of Al-23Si/SiC foam ceramic composites in 3.5% NaCl solution
- Fig. 8 Variation in corrosion rate with temperature after static immersion in 3.5% NaCl solution:
- Fig. 9 SEM images after static immersion in 3.5% NaCl solution for 15 d at 50 °C:
J. Cent. South Univ. (2017) 24: 1934-1940
DOI: https://doi.org/10.1007/s11771-017-3601-y
Corrosion behavior of SiC foam ceramic reinforced Al-23Si composites in NaCl solution
ZHU Jian-bin(诸建彬)1, 2, YAN Hong(闫洪)1, YE He-yuan(叶何远)1, AI Fan-rong(艾凡荣)1
1. School of Mechanical Electrical Engineering, Nanchang University, Nanchang 330031, China;
2. School of Mechanical Electrical Engineering, Nanchang Institute of Technology, Nanchang 330099, China
Central South University Press and Springer-Verlag GmbH Germany 2017
Abstract:
SiC foam ceramic reinforced aluminum matrix composites (SFCAMCs) were prepared by squeeze casting aluminum alloy (Al-23Si) into the SiC foam ceramic with different pore sizes, and the corrosion behavior of the SFCAMCs was studied in NaCl solutions. Static immersion corrosion tests were conducted at 20 °C, 50 °C and 80 °C, respectively. Corrosion morphology and products were analyzed by scanning electron microscope, energy dispersive system and X-ray diffraction. It was found that the corrosion rate of SFCAMCs increases as the temperature rising, and the bigger pore size of SiC foam ceramic reinforcement, the better corrosion resistance of SFCAMCs.
Key words:
SiC; ceramic foam; aluminum matrix composites; corrosion; NaCl;
1 Introduction
The SiC reinforced aluminum matrix composites have attracted much attention due to their excellent properties such as high-temperature behavior, high conductivity, good wear-resistance and high strength [1, 2]. These properties have made SiC particle, whisker or fiber reinforced aluminum matrix composites attractive candidates for various application fields [3-5]. Nevertheless, the reinforcements in forms of SiC particle, whisker or fiber in the reinforced aluminum matrix composites are easy to fall off from the base alloy, which limits their widespread applications. SiC foam ceramic reinforced aluminum matrix composites (SFCAMCs), consist of soft aluminum matrix and hard SiC foam ceramic with overall interpenetrating network structure, preventing the fall-off of the reinforcements from the composites. Furthermore, SFCAMCs integrate the advantages of both aluminum alloy and SiC foam ceramic, improving their application prospects in well wear-resistant filed, such as automotive brake disc, piston, cylinder and turbo compressor [6-8].
In above wear-resistant applications, the service life of the part is not only determined by the wear resistance but also the corrosion resistance of the material. In recent years, much progress has been made to develop SFCAMCs and many studies have been performed on the friction, wear, mechanical, and physical properties of SFCAMCs [8-13], however, the references reported on the corrosion resistance of SFCAMCs are very rare, and the reinforcement of reported SiC reinforced aluminum matrix composites mainly focus on the SiC particles. ABBASS et al [14] studied the corrosion resistance of Al 6061 reinforced by 10% and 20% SiC (mass fraction) particles in 3.5% NaCl solution. They concluded that Al 6061 showed superior corrosion resistance than the composites with 10% and 20% SiC particles, and the corrosion rate increased with the increasing of SiC particles content. Despite of the SiC particle content, the SiC particle size also has much influence on the corrosion of the composites. The composites with a smaller SiC particle size exhibited superior corrosion resistance than those with larger particles [15]. ZAKARIA et al [16] confirmed above results and found that at elevated temperature, pure Al matrix exhibited better corrosion resistance than the Al/SiC composites. However, the corrosion behavior of composites is not only determined by the component of the reinforcement but also the reinforcement structure [17-19]. So, it is meaningful to study the corrosion behavior of SFCAMCs, which have interpenetrating network structure, so as to improve their corrosion resistance.
Al-23Si alloy, an aluminum alloy with well wear resistance, low thermal expansion, low density and well hot crack resistance, is an idea base alloy for SFCAMCs used in wear-resistant applications. Al-23Si reinforced by SiC foam ceramics with pore sizes of 10 pores per-inch (PPI) and 30 PPI were fabricated by a squeeze casting method in this work respectively. The corrosion behavior of the composites in 3.5% NaCl (mass fraction) solutions was investigated, and the corrosion mechanism of the SFCAMCs was built as well, aiming to find an effective way to improve the corrosion resistance of SFCAMCs.
2 Experimental procedure
2.1 Fabrication of composites
Silicon carbide powders with an average particle size of 10 μm and 98.5% purity were used to fabricate SiC foam ceramics by an organic foam impregnation method. Organic foams with two different pore sizes,10 PPI and 30 PPI, were used. As shown in Fig. 1, the SiC foam ceramics had continuous pore net microstructure with a porosity of 80%. The SiC foam ceramics were heated to 700 °C and placed in a 400 °C preheated cylindrical mold. Then molten Al-23Si alloy, which was melted at 810 °C, was added into the mold. Al-23Si/SiC foam ceramic composites with good interface bonding were fabricated by squeeze casting at a pressure of 25-40 MPa and a pressure-holding time of 1-2 min. The SFCAMCs reinforced by SiC foam ceramics with pore size of 30 PPI and 10 PPI were remarked as composites A and composites B, respectively. The composites A and composites B had the same volume percentage of SiC 20%.
Fig. 1 Microstructure of SiC foam ceramics
2.2 Static immersion corrosion tests and characterization
The static immersion corrosion tests were performed on composite A and composite B, and Al-23Si alloy was used as control. All samples were cut into a cube shape (10 mm×10 mm×10 mm), followed by grinding, polishing, etching by 1% HF (mass fraction) and cleaning with ultrasonic. A FA22048 electronic balance scale (precision ±0.001 g) was used to determine the masses of samples.
Static immersion corrosion tests were carried at 20, 50 and 80 °C, respectively. The corrosive medium was an aqueous solution of 3.5% NaCl. All the samples were immersed in the corrosive medium after weighting, and taken out in 3, 7, 15, 30 and 60 d. To remove off the corrosion products, the samples were cleaned by a brush, and immersed 15 min in a aqueous solution, which contained 80 g chromic anhydride and 200 mL H3PO4 per liter, and washed by deionized water, and dried [20]. Then the samples were weighed again. The mass loss of each sample was measured and converted into corrosion rate (mm/a), which was calculated by the following equation [15]:
where R is the corrosion rate (mm/a), m0 and m1 are the masses before/after corrosion (precision ±0.001 g), K is a constant (8.766×107), S is the surface area of the sample (cm2), D is the density of the sample (g/cm3) and T is the corrosion time (h).
Corrosion morphology was characterized by optical microscope and scanning electron microscope (SEM). Corrosion products were analyzed by energy dispersive system (EDS) and X-ray diffraction (XRD).
3 Results and discussion
3.1 Effect of SiC foam ceramic pore size on corrosion behavior of composites
3.1.1 Corrosion rates
The corrosion rates of composite A, composite B and Al-23Si alloy in 3.5% NaCl solution at room temperature with different corrosion time are shown in Fig. 2. The corrosion rates of all the samples increase firstly and then decrease with the increase of corrosion time. The corrosion rates are relatively low at the beginning, and increase rapidly attributing to the deformation of the passivation film (Al2O3) on the surface of Al-23Si (in all the samples), and then reach the maximum after static immersion for 7 d. For the clean Al-23Si, an Al2O3 film is formed quickly when exposed to the aerobic environment. At the initial stage, the Al2O3 film is able to protect the Al-23Si. Nevertheless, the Al2O3 film is destroyed after immersing into NaCl solution, resulting in the corrosion rates increase dramatically. After 15 d of static immersion, the corrosion rates decrease gradually. This is attributed to the formation of corrosion products which prevent the further spreading of the corrosion. Moreover, the Al-23Si alloy exhibits better corrosion resistance than the composites A and B. Composite B, which has the bigger pore size SiC foam ceramic shows better corrosion resistance than composite A, indicating that the pore size of SiC foam ceramic has an obvious influence on the corrosion resistance of SFCAMCs. In other words, decreasing the pore size of the SiC foam ceramic accelerates the corrosion process of SFCAMCs.
Fig. 2 Variation in corrosion rates with corrosion time for samples after static immersion in 3.5% NaCl aqueous solution at room temperature
3.1.2 Microstructure morphology and corrosion behavior
Figure 3 shows the microstructure and XRD patterns of composites B before static immersion corrosion. The interfaces between SiC foam ceramic and Al-23Si matrix are flat, smooth, and without cracks. From Fig. 3(a), it can be noted that the needle-shaped silicon particles are well distributed in the Al-23Si matrix. In addition, as shown in Fig. 3(b), many tiny silicon particles are accumulated at the interfaces and form an intermediate belt. Figures 3(c) and 3(d) show an obvious transition layer between the SiC foam ceramic (white) and the Al-23Si matrix (black), indicating that chemical reactions occur between them. XRD pattern of composite B is shown in Fig. 3(e). SiO2, Al4C3 and Al2SiO5 are the main reaction products.
Fig. 3 Micro-morphology and XRD patterns of composite B before static immersion corrosion tests:
Figures 4 and Figs. 5(a), (b) show the SEM images of the corroded surface for composite B and Al-23Si alloy after static immersion at room temperature for 7 d and 30 d, respectively. It can be seen in Fig. 4(a) and Fig. 5(a) that the SiC foam ceramic is not corroded, while the Al-23Si matrix suffers non-uniform pitting corrosion as several deep pits are found on the surface, especially at the interfaces. Additionally, the interfaces between the SiC foam ceramic and Al-23Si matrix are cracked, and the Al-23Si matrix has a tendency to break away from the SiC foam ceramic. As shown in the magnified imaging of interfaces (immerged in Fig. 4(a)), the surface of Al-23Si matrix close to the interfaces is lower than that of SiC foam ceramic. This suggests that the SFCAMCs are more susceptible to pitting corrosion in NaCl solution at the initial stage. In contrast, the Al-23Si alloy corroded surface (Fig. 4(b)) reveals less damage than the composite B (Fig. 4(a)). Only slight corrosion is found in the Al-23Si alloy and much smaller and fewer pits are observed on the surface (Fig. 4(b)). In Fig. 5(a), after static immersion in 3.5% NaCl solution for 30 d, the surface of the composite B presents more severe damage, especially along the interfaces. As can be seen in the higher magnification SEM image in Fig. 5(a), most of the Al-23Si matrix close to the interfaces is corroded, exposing long and needle-shaped matter. This matter has been further analyzed by EDS. Figures 5(c, d) show the EDS spectra of the matter (Point 1) and Al-23Si matrix (Point 2). Si phases can be detected at point 1, and Al phases can be found at point 2.
Fig. 4 Images of corroded surface after static immersion in 3.5% NaCl solution for 7 d at room temperature:
Fig. 5 Images of corroded surface after static immersion in 3.5% NaCl solution for 30 d at room temperature:
Figure 6 shows the XRD patterns of composite B and Al-23Si alloy after static immersion in 3.5% NaCl solution for 30 d. Both AlCl3 and Al(OH)3 phases are present in composite B as well as in Al-23Si alloy, due to the reactions between Cl-, Al, H2O and the oxygen dissolved in the solution.
Fig. 6 XRD patterns after static immersion in 3.5% NaCl solution for 30 d:
It can be concluded that the corrosion process of SFCAMCs is promoted by the following three factors:
1) There are many interface defects such as dislocations, clearances and vacancies in the transition layer, where the stress concentration is obvious. These defects lead to the earlier corrosion in the interfaces.
2) The Cl- is able to permeate the Al2O3 film at the point of the interface defects, and a reaction between the Cl- and aluminum is able to occur and dissolve the aluminum. In addition, the stress in the Al2O3 film increases with Cl- permeating. As a result, the Al2O3 film cracks and sheds, and corrosion rate increases.
3) Squeeze casting method enhances the mechanical strength of composites greatly, but also leaves a high level of residual stress in the pores of the SiC foam ceramic and the area surrounded by SiC foam ceramic due to the different coefficient of thermal expansion between the SiC and Al-23Si matrix. Residual stress can activate the Al-23Si matrix and promote the corrosion process.
Generally, the interfaces of Al-23Si/SiC foam ceramic accelerate the corrosion process of SFCAMCs.Compared to composite B, composite A, which is reinforced by smaller pore size SiC foam ceramic, has more interfaces per unit area on the surface so as to the lower corrosion resistance. The pore size of SiC foam ceramic reinforcement has obvious effect on the corrosion resistance of SFCAMCs.
3.1.3 Corrosion mechanism
Based on above analysis, the corrosion mechanism of the SFCAMCs is built as shown in Fig. 7. In Fig. 7(a), the clean surface of the composites reaches passivity quickly after being exposed to the aerobic environment, forming an Al2O3 film on the surface of the composites that protects the composites at the initial immersion stage. However, this film is discontinuous due to the presence of SiC foam ceramic, and thus the interfaces become the weakest parts in the SFCAMCs. In addition, there are many defects such as dislocations, clearances, and vacancies in the interfaces, where a high level of stress is maintained. Therefore, in Fig. 7(b), the Cl- permeates the interfaces easily to react with the Al in the Al-23Si matrix. In Fig. 7(c), the stress in the Al2O3 film increases with the permeating of Cl-. The Al2O3 film’s thickness is gradually reduced with the increasing of corrosion time. As shown in Fig. 7(d), the Al2O3 film ruptures quickly when the stress is higher than a certain value, the Al3+ is released into the solution and then reacted with the H2O and the oxygen dissolved in the solution. Hence, the defects in the interfaces stimulate the destruction of the interfaces. The corrosion mechanism in Fig. 7 explains the corrosion behavior of SFCAMCs very well.
3.2 Effect of temperature on corrosion behavior of composites
3.2.1 Corrosion rates
Figures 8(a) and (b) show the corrosion rates of composite A, composite B and Al-23Si alloy in 3.5% NaCl solution at different temperatures for 3 d and 15 d, respectively. The corrosion rates of all the samples increase as the temperature rises. In the range of 20-80 °C, the effect of temperature on the corrosion rate of composites mainly depends on the energy of reaction particles in corrosion system at the temperature. The energy of reaction particles, such as Cl-, Al and O2, are improved at elevated temperature. The improved energy accelerates their thermal velocity and makes them having more chances to collide with each other and promotes their chemical reactions, as a result, leads to more serious corrosion of the composites. So, the temperature rising accelerates the corrosion process of SFCAMCs. Additionally, no matter at 20, 50 or 80 °C, the composite B has better corrosion resistance than the composite A, the bigger pore size of SiC foam ceramic reinforcement results in the better corrosion resistance of the composites. The corrosion mechanism in Fig. 7 also fits the corrosion behavior of SFCAMCs well at elevated temperature.
Fig. 7 Corrosion mechanism of Al-23Si/SiC foam ceramic composites in 3.5% NaCl solution
Fig. 8 Variation in corrosion rate with temperature after static immersion in 3.5% NaCl solution:
3.2.2 Microstructure morphology
Figures 9(a) and (b) show the SEM images of composite B and Al-23Si alloy after static immersion in 3.5% NaCl solution for 15 d at 50 °C, respectively. Compared to Fig. 5, the severity of damage of the composite B and Al-23Si alloy in Fig. 9 are almost the same, but half of the immersion time. This indicates that temperature rising increases the corrosion rate. Additionally, the composite B (Fig. 9(a)) exhibits more severe damage on the surface than the Al-23Si alloy (Fig. 9(b)). This phenomenon further confirms that the interfaces of Al-23Si/SiC foam ceramic accelerate the corrosion process of the SFCAMCs at elevated temperature.
4 Conclusions
1) The interfaces between Al-23Si matrix and SiC foam ceramic accelerate the corrosion process of SFCAMCs. The composite B with a larger pore size of SiC foam ceramic possesses less interfaces per unit area on the surface than the composite A, resulting in a better corrosion resistance. The pore size of SiC foam ceramic has obvious effect on the corrosion resistance of SFCAMCs.
Fig. 9 SEM images after static immersion in 3.5% NaCl solution for 15 d at 50 °C:
2) At room temperature, the corrosion rates of the SFCAMCs increase at the beginning then decrease with the increasing of corrosion time, attributing to the degradation of passivation film (Al2O3) and the gradual formation of corrosion products.
3) The corrosion rates of SFCAMCs increase as the temperature rising. The temperature rising improves the energy of reaction particles in corrosion system and promotes their chemical reactions, as a result, accelerates the corrosion process of SFCAMCs.
References
[1] LEE H L, LU W H, CHAN S L. Abrasive wear of powder metallurgy Al alloy 6061-SiC particle composites [J]. Wear, 1992, 159(2): 223-231.
[2] ZHANG Zhen-fang, ZHANG Lang-chi, MAI Yiu-wing. The running-in wear of a steel/SiCp-Al composite system [J]. Wear, 1996, 194(1, 2): 38-43.
[3] CHRISTMAN T, SURESH S. Microstructural development in an aluminum alloy–SiC whisker composite [J]. Acta Metallurgic, 1988, 36 (7): 1691-1704.
[4] ARSENAULT R J. The strengthening of aluminum alloy 6061 by fiber and platelet silicon carbide [J], Materials Science and Engineering, 1984, 64(2): 171-181.
[5] ALPAS A T, EMBURY J D. Sliding and abrasive wear behavior of an aluminum (2014)-SiC particle reinforced composite [J]. Scripta Materialia, 1990, 24(5): 931-935.
[6] SHARMA S, DHANASEKARAN S, SREENIVASAN V S. Microstructure and mechanical behavior of SiC reinforced aluminum metal matrix composites for automobile applications [J]. SAE Technical Paper, No. 2014-28-0026.
[7] JIANG Lan, JIANG Yan-li, YU Liang, SU Nan, DING You-dong. Thermal analysis for brake disks of SiC/6061 Al alloy co-continuous composite for CRH3 during emergency braking considering airflow cooling [J]. Transactions of Nonferrous Metals Society of China, 2012, 22(11): 2783-2791.
[8] YAN Hong, YE He-yuan, CHEN Wei. Dry friction and wear performance of co-continuous Al-23Si/SiC composites [J]. Materials Research Innovations. 2015, 19(S9): 131-135.
[9] AGUILAR-MARTINEZ J A, PECH-CANUL M I, RODRIGUEZ- REYES M, DE-LA-PENA J L. Effect of processing parameters on the degree of infiltration of SiCp preforms by Al–Si–Mg alloys [J]. Materials Letters, 2003, 57(26): 4332-4335.
[10] ZHAO L Z, ZHAO M J, CAO X M, TIAN C, Hu W P, ZHANG J S. Thermal expansion of a novel hybrid SiC foam–SiC particles–Al composites [J]. Composites Science and Technology, 2007, 67(15, 16): 3404-3408.
[11] ZHAO Long-zhi, ZHAO Ming-juan, YAN Hong, CAO Xiao-ming, ZHANG Jin-song. Mechanical behavior of SiC foam-SiC particles/Al hybrid composites [J]. Transactions of Nonferrous Metals Society of China, 2009, 19(3): s547-s551.
[12] LIU Jun-wu, ZHENG Zhi-xiang, WANG Jian-min, TANG Wen-ming, LV Jun. Pressureless infiltration of liquid aluminum alloy into SiC performs to form near-net-shape SiC/Al composites [J]. Jounal of Alloys and Compounds, 2008, 465 (1, 2): 239-243.
[13] CANDAN E. Effect of alloying additions on the porosity of SiCp preforms infiltrated by aluminium [J]. Materials Letters, 2006, 60 (9, 10): 1204-1208.
[14] ABBASS M K, HASSAN K S, ALWAN A S. Study of corrosion resistance of aluminum alloy 6061/SiC composites in 3.5% NaCl solution [J]. International Journal of Materials, Mechanics and Manufacturing, 2015, 3(1): 31-35.
[15] CANDAN S. Effect of SiC particle size on corrosion behavior of pressure infiltrated Al matrix composites in a NaCl solution [J]. Materials Letters, 2004, 58(27, 28): 3601-3605.
[16] ZAKARIA H M. Microstructural and corrosion behavior of Al/SiC metal matrix composites [J]. Ain Shams Engineering Journal, 2014, 5(3): 831-838.
[17] DURAI T G, DAS K, DAS S. Effect of mechanical milling on the corrosion behavior of Al–Zn/Al2O3 composite in NaCl solution [J]. Journal of Materials Science, 2007, 42(19): 8209-8214.
[18] LIU Zhang-sheng, HUANG Bo, GU Ming-yuan. Corrosion behavior of Al/AlNp composite in alkaline solution [J]. Materials Letters, 2006, 60(16): 2024-2028.
[19] SEAK K H W, KRISHNA M, VIJAYALAKSHMI V T, UCHIL J. Effects of the temperature and reinforcement content on corrosion characteristics of LM13/Albite composites [J]. Corrosion Science, 2002, 44(4): 761-772.
[20] HB 5257-83. Determination of weight loss of corrosion test results and removal of corrosion products [S]. (in Chinese)
(Edited by HE Yun-bin)
Cite this article as:
ZHU Jian-bin, YAN Hong, YE He-yuan, AI Fan-rong. Corrosion behavior of SiC foam ceramic reinforced Al-23Si composites in NaCl solution [J]. Journal of Central South University, 2017, 24(9): 1934–1940.
DOI:https://dx.doi.org/https://doi.org/10.1007/s11771-017-3601-yFoundation item: Project(00008713) supported by the Program of the Science and Technology Creative Team of Universities in Jiangxi, China; Project(2013-KLP-04) supported by the Open Foundation of Jiangxi Key Laboratory for Advanced Copper and Tungsten Materials, China
Received date: 2016-04-05; Accepted date: 2016-10-06
Corresponding author: YAN Hong, Professor, PhD; Tel: +86-791-83969633; E-mail: hyan@ncu.edu.cn
Abstract: SiC foam ceramic reinforced aluminum matrix composites (SFCAMCs) were prepared by squeeze casting aluminum alloy (Al-23Si) into the SiC foam ceramic with different pore sizes, and the corrosion behavior of the SFCAMCs was studied in NaCl solutions. Static immersion corrosion tests were conducted at 20 °C, 50 °C and 80 °C, respectively. Corrosion morphology and products were analyzed by scanning electron microscope, energy dispersive system and X-ray diffraction. It was found that the corrosion rate of SFCAMCs increases as the temperature rising, and the bigger pore size of SiC foam ceramic reinforcement, the better corrosion resistance of SFCAMCs.
- Corrosion behavior of SiC foam ceramic reinforced Al-23Si composites in NaCl solution
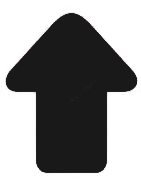