J. Cent. South Univ. Technol. (2008) 15: 280-284
DOI: 10.1007/s11771-008- 0052-5
Penetration grouting reinforcement of sandy gravel
YANG Ping(杨 坪)1, 2, 3, PENG Zhen-bin(彭振斌)2, TANG Yi-qun(唐益群)1,
PENG Wen-xiang(彭文祥)2, HE Zhong-ming(何忠明)2
(1. Department of Geotechnical Engineering, Tongji University, Shanghai 200092, China;
2. School of Geoscience and Environmental Engineering, Central South University,
Changsha 410083, China;
3. Key Laboratory of Geotechnical and Underground Engineering of Ministry of Education,
Tongji University, Shanghai 20092, China)
Abstract:
To study the relationship between grouting effect and grouting factors, three factors (seven parameters) directionless pressure and small cycle grouting model experiment on sandy gravel was done, which was designed according to uniform design method. And regressing was applied to analysis of the test data. The two models test results indicate that when the diffusing radius of grout changes from 26 to 51 cm, the grouted sandy gravel compressing strength changes from 2.13 to 12.30 MPa; the relationship between diffusing radius(R) and water cement ratio(m), permeability coefficient(k), grouting pressure(p), grouting time(t) is R=19.953m0.121k0.429p0.412t0.437; the relationship between compressing strength(P) and porosity(n), water cement ratio, grouting pressure, grouting time is P=0.984n0.517m-1.488p0.118t0.031. So the porosity of sandy gravel, the permeability coefficient of sandy gravel, grouting pressure, grouting time, water cement ratio are main factors to influence the grouting effect. The grouting pressure is the main factor to influence grouting diffusing radius, and the water cement ratio is the main factor to influence grouted sandy gravel compressing strength.
Key words:
penetration grouting; uniform design method; sandy gravel;
1 Introduction
Grouting was first utilized to repair washout brake of Dieppe (Charles Berigny). After that, grouting is widely used to improve soil/rock quality and, in this regard, various grouting techniques have been developed. These grouting techniques are commonly applied to soil rather than other fields[1-2]. Sandy gravel is a complex, loose, coarse fragment accumulation of Quaternary sediments[3-7]. In terms of sandy gravel, penetration grouting is commonly used to fill the voids of the sandy gravel so as to improve the gravels stiffness and strength and to reduce groundwater flow.
The aim of grouting in sandy gravel is that the grout can yield continuation and steady cement. The distance of grouting bore depends on the diffusing radius. How to determine the diffusing distance of grout and compressing strength of cement is a long-term unsolved technique problem. At present, diffusing distance of grout and compressing strength of cement are determined by empirical procedure in the design and construction of grouting.
It is possible to yield engineering problem and waste of investment because of unseemly distance of grouting bore. The authors think that diffusing distance of grout and compressing strength of cement are decided by structural parameter of medium, character of grout and technology parameter of grouting. In this work, penetration grouting injected into sandy gravel was focused on, and the relationship between diffusing distance of grout, compressing strength of cement and the influential factors of grouting were investigated both analytically and experimentally.
2 Principles of experiment
Experiment is directionless pressure and small cycle grouting. Firstly, construct the simulation sandy gravel with different proportions of sand and gravel in the experiment-bed, place the grouting pipe and detecting head in advance based on design plan, then measure the parameter of strata before grouting, which includes porosity, permeability coefficient, gravity, water content, weight density and grain content, and finally connect grouting pipe and meter, stir the grout in the designed proportion, and then be ready for grouting.
The simulation sandy gravel was grouted by penetrating grouting[8-9], and the grouting pressure was designed. The grouting pressure was monitored by pressure meter installed in the grouting pipe.
When the grouting began, the valve of circle grout was all open, all grout flowed back to grout barrel, then the valve of circle grout was turned off slowly; when the pressure reached the designed pressure, the valve of circle grout can be turned off. By adjusting the pressure of the valve of circle grout, the grouting was feasible. When the detecting head detected grout, the warning indicator gave an alarm and stopped grouting.
3 Device of grouting experiment
A cubic container with the dimensions of 1 670 mm×1 230 mm×1 023 mm was used for the experiment. This device was designed by the authors and included five parts: steel framework, movable steel plank, perspex plank, shaking table, grouting equipment and measurement sensor. Workshop size of experimenter is (0-1 500 mm)×1 220 mm×1 000 mm.
Steel cubic container is composed of steel framework, movable steel plank, perspex plank, steel soleplate. The width and height of workshop are 1 200 mm and 1 000 mm respectively, which are invariable. The length of the workshop can be adjusted from 0 to 1 500 mm, which can satisfy different size experiments. Movable steel plank is composed of feed screw and steel plank. Shaking table is composed of four springs and a eccentricity pulsator. Grouting equipment includes grouting pump, buffer and stirring barrel. Measurement system includes detecting head of grout, viscometer and pressure meter.
In order to observe the experiment clearly, the devices of experiment are made up of perspex plank except that the soleplate and movable plank are made up of steel. All perspex planks can be taken down.
4 Materials and design of experiment
The model of simulation sandy gravel is composed of sand, gravels with different proportions and is shaken with shaking table for several times and compressed in responding to the required density[10].
Material of grouting is general Portland cement, labeled 425#.
Two sets of experiments were carried out. Each set experiment included seven different permeability coefficients of sandy gravels. The permeability coefficients of sandy gravels are shown in Table 1 and Table 2.
Table 1 Values of experimental factors in the first set of experiment
Table 2 Values of experimental factors in the second set of experiment
Seven values of water cement ratio and grouting pressure were chosen. Factors of experiment are shown in Table 1 and Table 2.
The experiment was designed in Table 3 according to the uniform design method founded by FANG[11] and LIANG et al[12].
Table 3 Table of uniform design
The use table of uniform design suggests that in the experiment of three factors the 2nd, 3rd, 4th columns of Table 3 should be chosen, the permeability coefficient, grouting pressure and water cement ratio are arranged at 2nd, 3rd, 4th columns of Table 3, respectively. Table 4 and Table 5 are the plans of the experiments.
Table 4 Plan of the first set of experiment
Table 5 Plan of the second set of experiment
5 Analysis of experimental results
5.1 Observation of experiment
Grouting pressure rises gradually and reaches the designed pressure. Grouting pressure fluctuates frequently in the process of rising pressure. One of the reasons is that the pressure of the grout coming from the grouting pump takes on the property of waving, although the grout has passed through the buffer. The other is that when the grout flows in the void of sandy gravel, sometimes the grout barges up against the pore of gravels, and sometimes barges up against the interface aperture of gravel. This condition takes place by turns, so the grouting pressure fluctuates ceaselessly.
After grouted, gravels and grout are fully cemented together. The degree of grout filling and cement between grout and gravels is very good in the range of grout diffusing. Out of the range of grout diffusing, water seeps from the sandy gravel. The larger the water cement ratio is, the more the distinct water seeping is, which shows that performance of separating water of grout is very strong.
The grouted gravels present cylinder or rotary table. The lower the grouting pressure is, the narrower the range of cement is. Diffusing and filling of grout are very good in all experiments.
5.2 Processing of experimental data
Table 6 and Table 7 lists experiment results of the diffusing radius and compressing strength.
By regressing the experimental data of Table 6 and Table 7, the influence of grouting pressure, grouting time, water cement ratio, permeability coefficient and porosity on diffusing radius and compressing strength can be deduced[13-15].
Table 6 Results of the first set of experiment
Table 7 Results of the second set of experiment
The relationship among water cement ratio, permeability coefficient, grouting pressure, grouting time and diffusing radius is as follows:
(1)
where R is the diffusing radius, cm; m is the water cement ratio; k is the permeability coefficient, cm/s; p is the grouting pressure, MPa; t is the grouting time, s; r is the correlation coefficient; bm, bk, bp and bt are the standard regressing coefficients of diffusing radius for water cement ratio m, permeability coefficient k, grouting pressure p and grouting time t, respectively. The larger the regression coefficient, the more the influence on the corresponding factor for diffusion radius.
The relationship among porosity, water cement ratio, grouting pressure, grouting time and compressing strength is as follows:
(2)
where P is the compressing strength, MPa; n is the porosity of the sandy gravel; bn is the standard regressing coefficient of compressing strength for porosity.
5.3 Analysis of experimental results
The curves of grouting pressure and diffusing radius are shown in Fig.1. Fig.1 shows that the diffusing radius of grout increases with the increase of grouting pressure, permeability coefficient, grouting time and water cement ratio. Eqn.(1) shows that major influential factor on grout diffusing radius is grouting pressure and the next is permeability coefficient. The influences of grouting time and water cement ratio is relatively small.
Fig.2 shows the curves of water cement ratio and compressing strength, indicating that compressing strength of grouted gravels increases with the increase of grouting pressure, porosity and grouting time, decreases with the increase of water cement ratio. Eqn.(2) shows that among all factors affecting compressing strength of grouted gravels, water cement ratio is well marked, grouting pressure is bigger, porosity takes the third place, grouting time is the least.
Fig.1 Curves of grouting pressure and diffusing radius
Fig.2 Curves of water cement ratio and cement strength
Diffusing radius of grout and compressing strength of grouted gravels are important indexes of grouting effect. Experimental results show that the diffusing radius and compressing strength are affected in varying degrees by structure of grouting media (porosity, permeability coefficient), grouting pressure, grouting time and water cement ratio. The influence of water cement ratio is weak for diffusing radius and strong for compressing strength. The influence of grouting pressure and grouting time is strong for diffusing radius and weak for compressing strength. Also the influence of structure of grouting media is strong for diffusing radius and weak for compressing strength.
5.4 Maximum pressure of grouting nozzle
Grout fills void and extrudes free water and gas from void, so the pressure of grouting nozzle p1 is relatively low in penetration grouting, p1 can be written as
p1=p+γwhw (3)
where p1 is the pressure of grouting nozzle, kPa; γw is the water weight, kN/m3; hw is the height of groundwater level at grouting point, m. Because penetration grouting does not change structure of sandy gravel, the pressure of grouting nozzle p1 must be less than that of hydraulic fracturing p0 in sandy gravel.
(4)
where φ is the effective angle of internal friction; c is the cohesion, kPa; γ is the weight of sandy gravel, kN/m3; h is the depth of grouting section, m; k is the principal stress ratio.
The pressure of grouting nozzle is decided by the structure of sandy gravel, so the maximum of diffusing radius is determined by the structure of sandy gravel.
6 Conclusions
1) The structures of grouting media (porosity, permeability coefficient), grouting pressure, grouting time, water cement ratio are the four factors controlling the compressing strength of grouted gravels and diffusing radius of grout in sandy gravel layers. The effect of grouting is affected by the four factors in varying degrees.
2) The maximum of diffusing radius depends on structure of sandy gravel. Diffusing radius of grout is determined by the character of grout and technological parameter of grouting when the condition of strata is fixed. The major influential factor on diffusing radius of grout is grouting pressure. The standard regressing coefficient of diffusing radius for grouting pressure is 1.338.
3) Compressing strength of grouted gravels increases with the increase of grouting pressure, porosity, grouting time and decreases with the increase of water cement ratio. In all factors affecting strength of grouted gravels, the water cement ratio is well marked, the standard regressing coefficient of compressing strength of grouted gravels for water cement ratio is 0.905.
4) The empirical formulations supply references to evaluation of effect of penetration grouting in sandy gravel.
References
[1] LEE J S, BANG C S, MOK Y J, MOK Y J, JOH S J. Numerical and experimental analysis of penetration grouting in jointed rock masses[J]. International Journal of Rock Mechanics and Mining Sciences, 2000, 37(7): 1027-1037.
[2] ZHANG Ke-neng, CHEN Yong-gui, DENG Fei-yue, TIAN Qing-yu. Retention of clay-solidified grouting curtain to Cd2+, Pb2+ and Hg2+ in landfill of municipal solid waster[J]. Journal of Central South University of Technology, 2004, 11(4): 405-409.
[3] PETER V, AHMAD S. Fabric analyses of some Saudi Arabian pediment gravels[J]. Journal of Arid Environments, 1995, 30(4): 371-384.
[4] KIM J W, CHOUGH S K. A gravel lobe deposit in the prodelta of the Doumsan fan delta (Miocene), SE Korea[J]. Sedimentary Geology, 2000, 130(3): 183-203.
[5] ZHOU Bing-gen, LI Dian-you. An analysis on the characteristics and formation of the different gravels in Mountain Huangshan[J]. Journal of Anhui Normal University: Natural Science, 2000, 23(1): 57-60. (in Chinese)
[6] JIANG Zhi-wei. Understand engineering geologic character of fourth age diluvial gravels in south Anhui[J]. Anhui Architecture, 2002, 9(6): 78-79. (in Chinese)
[7] JACQUES ?, BROCHIER-MICHEL L. An original anthropic sedimentary deposit from Vauclusian Mesolithic sites: The black earth with small alluvial gravels[J]. L’anthropologie, 2003, 107(11): 153-165.
[8] PENG Zhen-bin. Design calculate and construct of grouting engineering[M]. Wuhan: China University of Geosciences Press, 1997. (in Chinese)
[9] CHEN Xiao, ZHANG Fen-xiang. Construct and effect inspect of grouting in engineering[M]. Shanghai: Tongji University Press, 1998. (in Chinese)
[10] FRANSSON A. Characterisation of a fractured rock mass for a grouting field experiment[J]. Tunnelling and Underground Space Technology, 2001, 16(4): 331-339.
[11] FANG Kai-tai. Uniform design and uniform design table[M]. Beijing: Science Press, 1994. (in Chinese)
[12] LIANG Yi-zeng, FANG Kai-tai, XU Qing-song. Uniform design and its applications in chemistry and chemical engineering[J]. Chemometrics and Intelligent Laboratory Systems, 2001, 58(1): 43-47.
[13] ERIKSSON M, STILLE H, ANDERSSON J. Numerical calculations for prediction of grout spread with account of filtration and varying aperture[J]. Tunnelling and Underground Space Technology, 2000, 15(4): 353-364.
[14] HE Shao-hua, WEN Zhu-qing. Experiment design and data processing[M]. Changsha: National University of Defense Technology Press, 2002. (in Chinese)
[15] PICHLER B, LACKNER R, MANG H A. Back analysis of model parameters in geotechnical engineering by means of soft computing[J]. International Journal for Numerical Methods in Engineering, 2003, 57(14): 1943-1978.
(Edited by YANG Hua)
Foundation item: Project(40372124) supported by the National Natural Science of China; project(05R214145) supported by Postdoctor Research Foundation of China; project(B308) supported by Shanghai Leading Academic Discipline
Received date: 2007-10-28; Accepted date: 2007-12-21
Corresponding author: YANG Ping, PhD; Tel: +86-13611665248; E-mail: csuyangp@163.com
- Penetration grouting reinforcement of sandy gravel
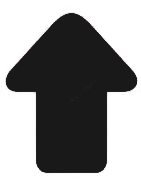