- Abstract:
- 1 Introduction▲
- 2 Experimental▲
- 3 Results and discus...▲
- 4 Conclusions▲
- References
- Figure
- Fig.1 XRD profiles of as-cast and spun alloys: (a) La0 alloy, (b) La2 alloy
- Fig.2 SEM images of as-cast alloys together with EDS spectra: (a) Image of La0 alloys; (b) Image of La2 alloys; (c), (d) and (e) EDS spectra of sections A, B and C in (b), respectively
- Fig.3 TEM micrographs (a) and (b) and SED patterns (c) and (d) of as-spun alloys (30 m/s): (a), (c) La0 alloy; (b), (d) La2 alloy
- Fig.4 DSC profiles of as-spun La2 alloy
- Fig.5 Evolution of discharge capacity of alloys with cycle number: (a) La0 alloy; (b) La2 alloy
- Fig.6 Evolution of maximum discharge capacity with spinning rate
- Fig.7 Discharge potential curves of as-cast and spun alloys: (a) La0 alloy; (b) La2 alloy
- Fig.8 Evolution of HRD values of alloys with spinning rate
- Fig.9 Evolution of capacity retaining rates of alloys with cycle number: (a) La0 alloy; (b) La2 alloy
- Fig.10 Evolution of S20 values of alloys with spinning rate
J. Cent. South Univ. Technol. (2011) 18: 1825-1832
DOI: 10.1007/s11771-011-0909-x
Influences of melt spinning on electrochemical hydrogen storage performance of nanocrystalline and amorphous Mg2Ni-type alloys
ZHANG Yang-huan(张羊换)1, 2, LI Bao-wei(李保卫)1, REN Hui-ping(任慧平)1,
HOU Zhong-hui(侯忠辉)1, HU Feng(胡峰)1, 2, WANG Xin-lin(王新林)2
1. Elected State Key Laboratory, Inner Mongolia University of Science and Technology, Baotou 014010, China;
2. Department of Functional Material Research, Central Iron and Steel Research Institute, Beijing 100081, China
? Central South University Press and Springer-Verlag Berlin Heidelberg 2011
Abstract:
In order to improve the electrochemical hydrogen storage performance of the Mg2Ni-type electrode alloys, Mg in the alloy was partially substituted by La, and the nanocrystalline and amorphous Mg2Ni-type Mg20-xLaxNi10 (x=0, 2) alloys were synthesized by melt-spinning technique. The microstructures of the as-spun alloys were characterized by X-ray diffraction (XRD), scanning electron microscopy (SEM) and transmission electron microscopy (TEM). The electrochemical hydrogen storage properties of the experimental alloys were tested. The results show that no amorphous phase is detected in the as-spun Mg20Ni10 alloy, but the as-spun Mg18La2Ni10 alloy holds a major amorphous phase. As La content increases from 0 to 2, the maximum discharge capacity of the as-spun (20 m/s) alloys rises from 96.5 to 387.1 mA·h/g, and the capacity retaining rate (S20) at the 20th cycle grows from 31.3% to 71.7%. Melt-spinning engenders an impactful effect on the electrochemical hydrogen storage performances of the alloys. With the increase in the spinning rate from 0 to 30 m/s, the maximum discharge capacity increases from 30.3 to 135.5 mA·h/g for the Mg20Ni10 alloy, and from 197.2 to 406.5 mA·h/g for the Mg18La2Ni10 alloy. The capacity retaining rate (S20) of the Mg20Ni10 alloy at the 20th cycle slightly falls from 36.7% to 27.1%, but it markedly mounts up from 37.3% to 78.3% for the Mg18La2Ni10 alloy.
Key words:
Mg2Ni-type hydrogen storage alloy; melt-spinning; structure; electrochemical performance;
1 Introduction
Mg-based (Mg2Ni-type) hydrogen storage alloys have attracted considerable interest in the last few years as hydrogen storage materials due to their major advantages such as high H/M ratio, low density and low cost. However, some disadvantages of the Mg2Ni-type electrode, such as sluggish hydriding/dehydriding kinetics and low electrochemical discharge capacity at room temperature, low diffusion rate of hydrogen and easy oxidation in alkaline solution, limit their practical applications. A variety of attempts, e.g. mechanical alloying (MA) [1], micro-encapsulation [2], F-treatment [3], heat treatment [4], alloying with other elements [5] and composite structures [6], have been developed to improve the above-mentioned imperfection.
LEI et al [7] obtained the improved discharge capacity of around 500 mA·h/g at a current density of 20 mA/g for the Mg2Ni alloy prepared by mechanical alloying (MA). IWAKURA et al [8] also improved the discharge capacity of Mg-based alloy with graphite surface modification by mechanical grinding (MG). KOHNO et al [9] reported that they modified Mg2Ni alloys with Ni powder by ball milling and yielded a large discharge capacity of 750 mA·h/g at a current density of 20 mA/g.
However, MA Mg-based alloys exhibited extremely poor electrochemical cycle stability [10]. Additionally, the MA/MG process has some insurmountable disadvantages such as the necessity of long time to produce an amorphous alloy, difficulty for massive production, and contamination from the chamber and balls used in ball-milling. Alternatively, the melt- spinning technique is not only an effective method for obtaining an amorphous and/or nanocrystalline phase in the absence of disadvantages inherent from the MA process but also very suitable for massive production of amorphous alloys. Some advantages of an amorphous alloy, including high strength and toughness along with excellent corrosion resistance, have been clarified by researchers in this field. It was also expected that the amorphous alloys produced by melt-spinning could have excellent hydriding characteristics even at room temperature, similar to the alloys produced by the MA process. HUANG et al [11] prepared amorphous and nanocrystalline (Mg60Ni25)90Nd10 alloy by melt-spinning and obtained the highest discharge capacity of 580 mA·h/g. SPASSOV and K?STER [12] reported that Mm (Mm=Ce, La-rich mischmetal) clearly enhanced the hydrogen absorption capacity of the melt-spun nanocrystalline/amorphous Mg75Ni20Mm5 alloy.
Based on the above-mentioned literatures, it is apparently reasonable to postulate that additive La is beneficial for enhancing the glass forming ability and the hydrogen absorption capacity of the Mg2Ni-type alloy as La has the biggest atomic radius among all rare earth elements. In this work, the element Mg in Mg20Ni10 alloy was partially substituted by La in order to intensify the glass forming ability of the Mg2Ni-type alloys. The nanocrystalline and amorphous Mg2Ni-type Mg20-xLaxNi10 (x=0, 2) alloys were prepared by melt spinning technology. The thermal stability and electrochemical hydrogen storage characteristics of these alloys were examined in detail.
2 Experimental
The alloy ingots were fabricated using a vacuum induction furnace in a helium atmosphere with a pressure of 0.04 MPa in order to effectively prevent the volatilize- tion of Mg. A part of the as-cast alloys was re-melted and quenched with a rotating copper roller. The as-spun ribbons with a continuously length, a width of about 5 mm and a thickness of 20 to 30 μm were obtained. The spinning rate was approximately expressed by the linear velocity of the copper roller because it is too difficult to measure the real spinning rate, i.e. cooling rate of the sample during spinning. The spinning rates used in the experiment were 15, 20, 25 and 30 m/s, respectively. The nominal compositions of the experimental alloys were Mg20-xLaxNi10 (x=0, 2). For convenience, the alloys were denoted with La content as La0 and La2, respectively.
The phase structures and compositions of the as-cast and spun alloys were characterized by X-ray diffraction (XRD, D/max/2400). The diffraction, with the experimental parameters of 160 mA, 40 kV and 10(°)/min, respectively, was performed with Cu Kα1 radiation filtered by graphite. The morphologies of the as-cast and spun alloys were examined by scanning electron microscope (SEM, Philips QUANTA 400). The thin film samples of the as-spun alloys were prepared by ion etching for observing the morphology with transmission electron microscope (TEM, JEM-2100F), and determining the crystalline state of the samples with electron diffraction (ED).
Thermal stability and crystallization of the as-spun alloys were studied by means of differential scanning calorimetry (DSC, STA449C), and the heating temperature and the heating rate are 600 °C and 10 °C/min, respectively.
The amorphous alloy ribbons were pulverized and then mixed with carbonyl nickel powder in a mass ratio of 1:4. The mixture was cold pressed with a pressure of 35 MPa into round electrode pellets of 10 mm in diameter and total mass of about 1 g. A tri-electrode open cell, consisting of a metal hydride electrode, a sintered NiOOH/Ni(OH)2 counter electrode and a Hg/HgO reference electrode, was used for testing the electrochemical characteristics of the experimental alloy electrodes. A 6 mol/L KOH solution was used as electrolyte. The potential between the negative electrode and the reference electrode was defined as the discharge potential. In every cycle, the alloy electrode was firstly charged at a current density of 20 mA/g, after resting for 15 min, it was discharged at the same current density to cut-off potential of -0.500 V. The environment temperature of the measurement was kept at 30 °C.
3 Results and discussion
3.1 Microstructure characteristics
The XRD profiles of the as-cast and spun La0 and La2 alloys are depicted in Fig.1. It indicates that the melt-spinning renders an unascertainable change of the phase structure of the La0 alloy, but it causes a great variation of the phase structure of the La2 alloy. It is very evident that no amorphous phase is detected in the as-spun La0 alloy, but the as-spun La2 alloy displays a typical amorphous structure. Therefore, it can be surmised that the substitution of La for Mg intensifies the glass forming ability of the Mg2Ni-type alloy. A similar result was reported by TANAKA et al [13]. It is derived by comparing Fig.1(a) with (b) that the substitution of La for Mg renders a notable change of the phase composition of the as-cast alloy, forming the secondary phases (La, Mg)Ni3 and La2Mg17 instead of modifying the major phase Mg2Ni.
The SEM images as illustrated in Fig.2 exhibit a typical dendrite structure. The result obtained by energy dispersive spectrometry (EDS) indicates that the main phases of the La0 and La2 alloys are Mg2Ni phase (denoted as A). The substitution of La for Mg leads to the emergence of some secondary phases, grey massive (La, Mg)Ni3 phase (denoted as B) and square-shaped La2Mg17 phase (denoted as C), which are in agreement with the results of XRD observation. It must be pointed out that Mg peak in the Fig.2(d) is illegible, which is probably attributed the very small amount of Mg in the (La, Mg)Ni3 phase.
The TEM micrographs of the as-spun (30 m/s) La0 and La2 alloys as presented in Fig.3 exhibit that the as-spun La0 alloy has a nanocrystalline structure with grain size of about 20 nm, which is measured using linear intercept method. Its electron diffraction (ED) pattern appears sharp multi-haloes, corresponding to a crystal structure. The morphology of the as-spun La2 alloy exhibits a feature of nanocrystalline with grain size of about 20 nm embedded in the amorphous matrix, and its electron diffraction pattern consists of only broad and dull halo, which can be regarded as an credible evidence of the presence of an amorphous structure. The result conforms very well with the XRD observation in Fig.1.
Fig.1 XRD profiles of as-cast and spun alloys: (a) La0 alloy, (b) La2 alloy
Fig.2 SEM images of as-cast alloys together with EDS spectra: (a) Image of La0 alloys; (b) Image of La2 alloys; (c), (d) and (e) EDS spectra of sections A, B and C in (b), respectively
Fig.3 TEM micrographs (a) and (b) and SED patterns (c) and (d) of as-spun alloys (30 m/s): (a), (c) La0 alloy; (b), (d) La2 alloy
3.2 Thermal stability and crystallization
In order to examine the thermal stability and the crystallization of the as-spun nanocrystalline and amorphous alloys, DSC analysis was conducted. The resulting profiles in Fig.4 reveal that during heating the alloys crystallize completely, and the crystallization process of La2 alloy consists of several steps. The first crystallization reaction at about 210 °C is connected with a sharp exothermic DSC peak, followed by a smaller and wider peak (312 °C) corresponding to a second crystallization reaction. At higher temperatures the third exothermic effect (at about 396 °C) can be detected. It was ascertained that the first sharper peak corresponds to the crystallization (ordering) of the amorphous into nanocrystalline Mg2Ni [14]. It is also seen that the crystallization temperatures of the alloys slightly rises with increasing the spinning rate, which is most probably associated with the function of the spinning rate on the amorphized degree of the alloy.
Fig.4 DSC profiles of as-spun La2 alloy
3.3 Electrochemical hydrogen storage performance
3.3.1 Activation capability and discharge capacity
The activation capability was characterized by the cycle number of charge-discharge required for attaining the greatest discharge capacity through a charge-discharge cycle at a constant current density. The cycle number dependence of the discharge capacity of the alloys is plotted in Fig.5, at a charging-discharging current density of 20 mA/g. Figure 5 indicates that all the alloys have excellent activation capabilities, attaining their maximum discharge capacities at the first cycle. The substitution of La for Mg does not affect the activation performance of the alloys.
Fig.5 Evolution of discharge capacity of alloys with cycle number: (a) La0 alloy; (b) La2 alloy
The evolution of the maximum discharge capacity of the alloys with the spinning rate is presented in Fig.6. It is evident that the discharge capacities of the alloys always increase with growing spinning rate. As the spinning rate increases from 0 to 30 m/s, the discharge capacity grows from 30.3 to 135.5 mA·h/g for the La0 alloy, and from 197.2 to 406.5 mA·h/g for the La2 alloy. The result reported by the ORIMO and FUJII [15] ascertained that the maximum hydrogen contents existed in three nanometer-scale regions, i.e. grain region and grain boundary region as well as amorphous region, the corresponding values are 0.3%, 4.0% and 2.2% (mass fraction) respectively. It revealed that hydrides mainly exist in grain-boundary and amorphous phase regions. Hence, it seems to be self-evident that the discharge capacity of the alloys increases with rising the spinning rate. The as-cast La2 alloy shows a much larger discharge capacity than the as-cast La0 alloy which is probably associated with the secondary phases inspired by La substitution. The formed secondary phases, especially the (La, Mg)Ni3 phase, probably work not only as hydrogen reservoir but also as catalyst to activate the Mg2Ni phase to absorb/desorb reversible hydrogen in the alkaline electrolyte. It is noteworthy that, for a fixed spinning rate, the discharge capacity of the La2 alloy is much larger than the La0 alloy, which is mainly ascribed to the fact that the substitution of La for Mg markedly enhances the glass forming ability of the Mg2Ni-type alloy since amorphous Mg2Ni alloy possesses a larger discharge capacity than the crystal one. Some contrary results were reported on the hydriding/dehydriding properties of hydrogen storage alloys with amorphous structure. RYAN et al [16] reported that the discharge capacity of Ni64Zr36 amorphous alloys was 200 mA·h/g, similar to that of the conventional Ni/Cd battery, for which the large reversible hydrogen solubility of the amorphous phase is responsible. LEE and HA [17] confirmed the electrode capacity of Mg-Ni and Ti-Fe amorphous phases was greatly improved since the diffusivity and solubility of hydrogen were larger in an amorphous phase than in a crystalline phase. LIBOWITZ and MAELAND [18] considered that the absorption of hydrogen may depend not only on the crystal structure but also on the electro-magnetic structure. Therefore, the amount of absorbed hydrogen was larger in a crystalline phase than in an amorphous phase. LI and CHENG [19] investigated the electrochemical performance of the amorphous La-Mg thin film over range of composition, and confirmed that the discharge capacity of the amorphous alloy was about half as large as that of the crystalline alloy. None of the theories can satisfactorily explain the above-mentioned experimental results. The authors considered that high density crystal defects, nano- crystalline, especially an amorphous phase formed during melt-spinning can significantly improve the electrocatalytic activity and dynamic performance of the hydrogen absorption/desorption of the Mg-based hydrogen storage alloys. Consequently, the Mg-based alloys with an amorphous structure have a large discharge capacity. But the amorphization does not enhance the latent capability of the hydrogen absorption of the Mg-based alloy because the practical discharge capacity of the homogeneous amorphous Mg2Ni alloy is still much lower than its theoretical one.
Fig.6 Evolution of maximum discharge capacity with spinning rate
3.3.2 Discharge potential characteristic and high rate discharge ability
The discharge potential characteristic of the alloy electrode is characterized by the potential plateau of the discharge curve. The longer and the more horizontal the discharge potential plateau, the better the discharge potential characteristic of the alloy. The discharge potential curves of the as-cast and spun La0 and La2 alloys are demonstrated in Fig.7. It shows that the variation of the spinning rate exerts a visible impact on the discharge potential characteristics of the alloys. With the increase of the spinning rate, both the discharge potential and the plateau characteristics are markedly improved. It can be derived by comparing Fig.7(a) with (b) that the substitution of La for Mg clearly ameliorates the discharge potential characteristics of the alloys. The plateau potential is closely associated with the internal resistance of the battery, including ohmic internal resistance and polarization resistance. The discharge reaction of the hydrogen storage electrode mainly depends on the diffusion of hydrogen atoms in the alloy, and internal resistance of the alloy electrode decreases with the increase of the diffusion coefficient of hydrogen [20]. The grain refinement caused by melt-spinning is responsible for the results shown in Fig.7(a), because the grain boundary provides good tunnels for the diffusion of hydrogen atoms [21]. The positive impact of the substitution of La for Mg on the discharge potential characteristic of the as-spun alloy is ascribed to the intensified glass forming ability by La substitution.
Fig.7 Discharge potential curves of as-cast and spun alloys: (a) La0 alloy; (b) La2 alloy
It is quite important to restrict the rapid degradation in the discharge capacity even at a high charge/discharge current density for the practical application of hydride electrode in Ni-MH battery. Usually, the electrochemical kinetics of the alloy is symbolized by its high rate discharge ability (HRD), being calculated according to formula: AHRD=C100, max/C20, max×100%, where C100, max and C20, max are the maximum discharge capacities of the alloy electrode charged-discharged at the current densities of 100 and 20 mA/g, respectively. The HRD values of the alloys as a function of the spinning rate are illustrated in Fig.8. It exhibits that the HRD values of the alloys visibly grow with rising the spinning rate. As the spinning rate increases from 0 to 30 m/s, the HRD values rise from 32.21% to 46.51% for the La0 alloy and from 34.33% to 59.62% for the La2 alloy. For a fixed spinning rate, the HRD value of the La2 alloy is much higher than the La0 alloy, suggesting that the substitution of La for Mg ameliorates the electrochemical hydrogen storage kinetics of the Mg2Ni-type alloy.
Fig.8 Evolution of HRD values of alloys with spinning rate
The HRD value of the alloy mainly depends on the electrochemical reaction kinetics of the alloy powder surface and the diffusion rate of hydrogen in the bulk of the alloy [22]. The increased HRD value of the alloy by melt spinning is attributed to the refined grain because the grain boundaries provide good tunnels for the diffusion of hydrogen atoms. The substitution of La for Mg noticeably improves the electrochemical kinetics of the as-cast and spun alloys, and two reasons are basically responsible for the improvement. On one hand, the secondary phases (La,Mg)Ni3 and La2Mg17 created by La substitution greatly facilitates the hydrogen diffusion in the alloy. On the other hand, La acts as an active site for hydriding/dehydriding, at the same time it increases the lattice parameter of the alloy, which should lead to faster hydrogen diffusion. A very similar result was reported by SPASSOV and K?STER [23].
3.3.3 Electrochemical cycling stability
The cycle stability of the alloy is evaluated by its capacity retaining rate (Sn), which is defined as Sn= Cn/Cmax×100%, where Cmax is the maximum discharge capacity and Cn is the discharge capacity at the n-th charge-discharge cycle, respectively. Hence, it can be known that the larger the capacity retaining rate (Sn), the better the cycle stability of the alloy. The Sn values of the La0 and La2 alloys as a function of the cycle number are illustrated in Fig.9. The melt-spinning has a negligible influence on the Sn value of La0 alloy. The Sn values of the as-cast and spun La0 alloy rapidly degrade to around 37% of its capacity after 15 cycles, exhibiting very poor cycle stability. Correspondingly, the melt-spinning conspicuously enhances the cycle stability of La2 alloy, for which the glass forming ability enhanced by La substitution is primarily responsible.
Fig.9 Evolution of capacity retaining rates of alloys with cycle number: (a) La0 alloy; (b) La2 alloy
The spinning rate dependence of the S20 values of the La0 and La2 alloys is plotted in Fig.10. As the spinning rate increases from 0 to 30 m/s, the S20 value rises from 37.26% to 78.33% for the La2 alloy, but it falls from 36.71% to 27.06% for the La0 alloy, which is undoubtedly attributed to the grain refined by melt spinning. It is well known that the essential reason leading to the degradation of the discharge capacity of the Mg-based alloy electrodes is the severe corrosion of Mg in the alkaline KOH solution [24-26]. The refined grain consequentially weakens the anti-corrosion ability of the alloy due to the inevitable intercrystalline corrosion. A similar result was reported by SIMI?I? et al [27]. The melt-spinning remarkably enhances the cycle stability of the La2 alloy, which is mainly attributed to the formation of an amorphous phase. It can also be derived in Fig.10 that, for a fixed spinning rate, the substitution of La for Mg markedly raises the S20 value of the alloy. The S20 value of the as-spun (30 m/s) alloy is enhanced from 27.06% to 78.33% by increasing the amount of La substitution from 0 to 2. The positive impact of such substitution on the cycle stability of the alloy is ascribed to the glass formation facilitated by La substitution because an amorphous phase improves not only the anti-pulverization ability but also the anti- corrosion and anti-oxidation abilities of the alloy electrode in a corrosive electrolyte [28]. Based on the above-mentioned results, it can be presumed that an impactful approach for improving the cycle stability of the Mg-based alloy electrodes is to intensify its anti-corrosion and anti-oxidation capabilities.
Fig.10 Evolution of S20 values of alloys with spinning rate
4 Conclusions
1) Melt-spinning causes an insignificant change of the phase structure of the La0 alloy, but it leads to an evident variation of the phase structure of the La2 alloy. No amorphous phase is detected in the as-spun La0 alloy, but the as-spun La2 alloy exhibits a feature of nanocrystalline embedded in the amorphous matrix, testifying that the substitution of La for Mg may intensify the glass forming ability of the Mg2Ni-type alloy. Additionally, La substitution results in the formation of the secondary phases (La,Mg)Ni3 and La2Mg17 instead of changing the major phase Mg2Ni in the as-cast alloy.
2) Melt-spinning exerts a negligible impact on the activation capability of the alloys, but it clearly enhances the discharge capacity of the alloys. The discharge capacity of the alloys monotonously rises with increasing the spinning rate. The cycle stability of the La2 alloy notably rises with increasing the spinning rate, which is ascribed to the glass forming ability intensified by La substitution. However, the melt-spinning causes a slight fall of the cycle stability of the La0 alloy for which the grain refined by melt-spinning is mainly responsible.
3) For a fixed spinning rate, the substitution of La for Mg evidently improves the electrochemical hydrogen storage performances of the Mg2Ni-type alloy, including both the discharge capacity and the cycle stability, which is attributed to the glass forming ability enhanced by La substitution.
References
[1] WOO J H, LEE K S. Electrode characteristics of nanostructured Mg2Ni-type alloys prepared by mechanical alloying [J]. Journal of the Electrochemical Society, 1999, 146 (3): 819-823.
[2] SAKAI T, ISHIKAWA H, OGURU K, IWAKURA C, YONEYAMA H. Effects of microencapsulation of hydrogen storage alloy on the performances of sealed nickel/metal hydride batteries [J]. Journal of the Electrochemical Society, 1987, 134 (3): 558-562.
[3] LIU F J, SUDA S. Properties and characteristics of fluorinated hydriding alloys [J]. Journal of Alloys and Compounds, 1995, 231(1/2): 742-750.
[4] YAMAMOTO M, KANDA M. Investigation of AB5 type hydrogen storage alloy corrosion behavior in alkaline electrolyte solutions [J]. Journal of Alloys and Compounds, 1997, 253/254: 660-664.
[5] YE H, LEI Y Q, CHEN L S, ZHANG H. Electrochemical characteristics of amorphous Mg0.9M0.1Ni (M=Ni, Ti, Zr, Co and Si) ternary alloys prepared by mechanical alloying [J]. Journal of Alloys and Compounds, 2000, 311(2): 194-199.
[6] CRACCO D, PERCHERON-GUEGAN A. Morphology and hydrogen absorption properties of an AB2 type alloy ball milled with Mg2Ni [J]. Journal of Alloys and Compounds, 1998, 268(1/2): 248-255.
[7] LEI Y Q, WU YM, YANG Q M, WU J, WANG Q D. Electrochemical behavior of some mechanicalloy alloyed Mg-Ni- based amorphous hydrogen storage alloys [J]. International Journal of Research in Physical Chemistry and Chemical Physics, 1994, 183(1/2): 379-384.
[8] IWAKURA C, NOHARA S, INOUE H, FUKUMOTO Y. Surface modification of MgNi alloy with graphite by ball-milling for use in nickel-metal hydride batteries [J]. Chemical Communications, 1996(15): 1831-1832.
[9] KOHNO T, KANDA M. Effect of partial substitution on hydrogen storage properties of Mg2Ni alloy [J]. Journal of the Electrochemical Society, 1997, 144(7): 2384-2388.
[10] NOHARA S, FUJITA N, ZHANG S G, INOUE H, IWAKURA C. Electrochemical characteristics of a homogeneous amorphous alloy prepared by ball-milling Mg2Ni with Ni [J]. Journal of Alloys and Compounds, 1998, 267(1/2): 76-78.
[11] HUANG L J, LIANG G Y, SUN Z B, WU D C. Electrode properties of melt-spun Mg-Ni-Nd amorphous alloys [J]. Journal of Power Sources, 2006, 160(1): 684-687.
[12] SPASSOV T, K?STER U. Hydrogenation of amorphous and nanocrystalline Mg-based alloys [J]. Journal of Alloys and Compounds, 1999, 287(1/2): 243-250.
[13] TANAKA K, KANDA Y, FURUHASHI M, SAITO K, KURODA K, SAKA H. Improvement of hydrogen storage properties of melt-spun Mg-Ni-RE alloys by nanocrystallization [J]. Journal of Alloys and Compounds, 1999, 293/294/295: 521-525.
[14] SPASSOV T, SOLSONA P, SURI?ACH S, BAR? M D. Optimization of the ball-milling and heat treatment parameters for synthesis of amorphous and nanocrystalline Mg2Ni-based alloys [J]. Journal of Alloys and Compounds, 2003, 349(1/2): 242-254.
[15] ORIMO S, FUJII H. Materials science of Mg-Ni-based new hydrides [J]. Applied Physics A, 2001, 72(2): 167-186.
[16] RYAN D H, DUMAIS F, PATEL B, KYCIA J, STR?M-OLSEN J O. A rechargeable cell based on amorphous Ni-Zr [J]. Journal of the Less Common Metals, 1991, 172/173/174(3): 1246-1251.
[17] LEE K S, HA C J. Development of Ti-Fe-X metal hydride electrode by mechanical alloying [J]. Korean Journal of Materials Research, 1995, 5(1): 112-120.
[18] LIBOWITZ G G, MAELAND A J. Interactions of hydrogen with metallic glass alloys [J]. Journal of the Less Common Metals, 1984, 101: 131-143.
[19] LI Y, CHENG Y T. Amorphous La-Ni thin film electrodes [J]. Journal of Alloys and Compounds, 1995, 223(1): 6-12.
[20] LAI W H, YU C Z. Research survey of improving discharge voltage platform for Ni-MH battery [J]. Chinese Battery Industry, 1996, 26(4): 189-191.
[21] WU Y, HAN W, ZHOU S X, LOTOTSKY M V, SOLBERG J K, YARTYS V A. Microstructure and hydrogenation behavior of ball-milled and melt-spun Mg-10Ni-2Mm alloys [J]. Journal of Alloys and Compounds, 2008, 466(1/2): 176-181.
[22] IWAKURA C, MATSUOKA M, ASAI K, KOHNO T. Surface modification of metal hydride negative electrodes and their charge/discharge performance [J]. Journal of Power Sources, 1992, 38(3): 335-343.
[23] SPASSOV T, K?STER U. Thermal stability and hydriding properties of nanocrystalline melt-spun Mg63Ni30Y7 alloy [J]. Journal of Alloys and Compounds, 1998, 279: 279-286.
[24] LIU W H, LEI Y Q, SUN D L, WU J, WANG Q D. A study of the degradation of the electrochemical capacity of amorphous Mg50Ni50 alloy [J]. Journal of Power Sources, 1996, 58(2): 243-247.
[25] WANG L B, TANG Y H, WANG Y J, LI Q D, SONG H N, YANG H B. The hydrogenation properties of Mg1.8Ag0.2Ni alloy [J]. Journal of Alloys and Compounds, 2002, 336(1/2): 297-300.
[26] JIANG J J, GASIK M. An electrochemical investigation of mechanical alloying of MgNi-based hydrogen storage alloys [J]. Journal of Power Sources, 2000, 89(1): 117-124.
[27] SIMI?I? M V, ZDUJI? M, DIMITRIJEVI? R, NIKOLI?- BUJANOVI? LJ, POPOVI? N H. Hydrogen absorption and electrochemical properties of Mg2Ni-type alloys synthesized by mechanical alloying [J]. Journal of Power Sources, 2006, 158(1): 730-734.
[28] ZHANG Y H, CHEN M Y, WANG X L, WANG G Q, LIN Y F, QI Y. Effect of boron additive on the cycle life of low-Co AB5-type electrode consisting of alloy prepared by cast and rapid quenching [J]. Journal of Power Sources, 2004, 125(2): 273-279.
(Edited by HE Yun-bin)
Foundation item: Projects(50871050, 50961009) supported by the National Natural Science Foundation of China; Project(2010ZD05) supported by the Natural Science Foundation of Inner Mongolia, China; Project(NJzy08071) supported by the Higher Education Science Research Project of Inner Mongolia, China
Received date: 2010-11-24; Accepted date: 2011-04-11
Corresponding author: ZHANG Yang-huan, Professor, PhD; Tel: +86-10-62183115; E-mail: zyh59@yahoo.com.cn
Abstract: In order to improve the electrochemical hydrogen storage performance of the Mg2Ni-type electrode alloys, Mg in the alloy was partially substituted by La, and the nanocrystalline and amorphous Mg2Ni-type Mg20-xLaxNi10 (x=0, 2) alloys were synthesized by melt-spinning technique. The microstructures of the as-spun alloys were characterized by X-ray diffraction (XRD), scanning electron microscopy (SEM) and transmission electron microscopy (TEM). The electrochemical hydrogen storage properties of the experimental alloys were tested. The results show that no amorphous phase is detected in the as-spun Mg20Ni10 alloy, but the as-spun Mg18La2Ni10 alloy holds a major amorphous phase. As La content increases from 0 to 2, the maximum discharge capacity of the as-spun (20 m/s) alloys rises from 96.5 to 387.1 mA·h/g, and the capacity retaining rate (S20) at the 20th cycle grows from 31.3% to 71.7%. Melt-spinning engenders an impactful effect on the electrochemical hydrogen storage performances of the alloys. With the increase in the spinning rate from 0 to 30 m/s, the maximum discharge capacity increases from 30.3 to 135.5 mA·h/g for the Mg20Ni10 alloy, and from 197.2 to 406.5 mA·h/g for the Mg18La2Ni10 alloy. The capacity retaining rate (S20) of the Mg20Ni10 alloy at the 20th cycle slightly falls from 36.7% to 27.1%, but it markedly mounts up from 37.3% to 78.3% for the Mg18La2Ni10 alloy.
- Influences of melt spinning on electrochemical hydrogen storage performance of nanocrystalline and amorphous Mg2Ni-type alloys
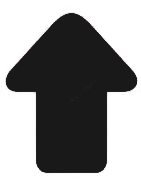