- Abstract:
- 1 Introduction▲
- 2 Experimental▲
- 3 Results and discussion▲
- 4 Conclusions▲
- References
- Figure
- Fig.1 Starting microstructure of experimental alloy used in this study
- Fig.2 Compressive flow curves as function of strain rate at 920 oC (α+β region), 1 100 oC (β region) (a), and 980 oC (near β transus region) (b)
- Fig.3 Plots of ln versus ln[sinh(ασ)] in α+β (a) and β (b) regions
- Fig.4 Arrhenius plots showing variation of flow stress with inverse of temperature in α+β and β regions
- Fig.5 Variations of Zener-Hollomon (Z) parameter with flow stress in α+β and β regions
- Fig.6 Processing maps of Ti-6.5Al-3.5Mo-1.5Zr-0.3Si alloy at strains of 0.3 (a) and 0.5 (b) (Numbers represent efficiency of power dissipation)
- Fig.7 Optical and TEM micrographs of Ti-6.5Al-3.5Mo-1.5Zr-0.3Si alloy hot compressed at 860 °C: (a) 0.01 s-1; (b) 10 s-1; (c, d, e, f) 0.1 s-1
- Fig.8 Optical micrographs of Ti-6.5Al-3.5Mo-1.5Zr-0.3Si alloy hot compressed at 1 100 °C and different strain rates: (a) 0.01 s-1; (b) 1 s-1
- Fig.9 Optical micrograph of Ti-6.5Al-3.5Mo-1.5Zr-0.3Si alloy hot compressed at 980 °C and 1 s-1
J. Cent. South Univ. Technol. (2011) 18: 296-302
DOI: 10.1007/s11771-011-0694-6
Hot deformation behavior of Ti-6.5Al-3.5Mo-1.5Zr-0.3Si alloy with acicular microstructure
LIU Gao-feng(刘高峰)1, ZHANG Shang-zhou(张尚洲)1, CHEN Li-qing(陈礼清)2
1. School of Environmental and Materials Engineering, Yantai University, Yantai 264005, China;
2. State Key Laboratory of Rolling and Automation, Northeastern University, Shenyang 110004, China
? Central South University Press and Springer-Verlag Berlin Heidelberg 2011
Abstract:
The characteristics of hot deformation of an α+β titanium alloy Ti-6.5Al-3.5Mo-1.5Zr-0.3Si with acicular microstructure were studied using isothermal hot compressive tests in a strain rate range of 0.01-10 s-1 at 860-1 100 °C. The true stress-true strain curves of alloy hot-compressed in the α+β region exhibit a peak stress followed by continuous flow softening; whereas in the β region, the flow stress attains a steady-state regime. At a strain rate of 10 s-1 and in a wide temperature range, the alloy exhibits plastic flow instability. According to the kinetic rate equation, the apparent activation energies are estimated to be about 633 kJ/mol in the α+β region and 281 kJ/mol in the β region, respectively. The processing maps show a domain of the globularization process of α colony structure and α dynamic recrystallization in the temperature range of 860-960 °C with a peak efficiency of about 60%, and a domain of β dynamic recrystallization in the β region with a peak efficiency of 80%.
Key words:
titanium alloy; Ti-6.5Al-3.5Mo-1.5Zr-0.3Si; hot compression; flow behavior; microstructure;
1 Introduction
Ti-6.5Al-3.5Mo-1.5Zr-0.3Si alloy (nominal composition, mass fraction, %) belongs to two-phase α+β type titanium alloy, which can be thermo- mechanically processed to possess a combination of excellent tensile strength, creep and low cycle fatigue resistance up to 500 °C [1-2]. The wrought processing of this alloy involves a series of primary and secondary deformation operations. Primary hot deformation in the β region is employed to take advantage of good workability of the alloy and changes the relatively coarse colony to basket-weave and fine acicular microstructures by varying the cooling rate [3-4]. Subsequent deformation in the α+β region is necessary to achieve the equiaxed alpha or bimodal microstructures. Many researchers [5-7] provided insight into the globularization kinetics and mechanisms of the transformed β microstructure. WEISS et al [6] showed that the main driving force for dynamic globularization was the formation of intense shear bands within α lamellae. SEMIATIN et al [7] emphasized that the dependence on strain rate and deformation temperature of dynamic globularization kinetics of the colony microstructure was complicated and appeared to be of second-order importance compared with the effects of strain. Strain path, effective strains, and a variety of deformation modes were evaluated for the Ti-6Al-2Sn-4Zr-2Mo alloy [8] and the Russian alloy VT9 [9]. For the hot working of TC11 alloy with starting lamellar α+β structure, LI et al [10] used processing map and concluded that the lamellar globularization of titanium alloy is best conducted in the temperature range of 900-980 °C at lower strain rates. Refining the initial microstructure has significant effect on the deformation behavior and microstructure evolution [11].
The aim of the present investigation is to evaluate the mechanisms of hot deformation of the Ti-6.5Al- 3.5Mo-1.5Zr-0.3Si (mass fraction, %) alloy with acicular microstructure over a wide range of temperature and strain rate with a view to optimize its hot workability and to achieve the microstructural control during hot processing.
2 Experimental
The material used in this work is as-received hot wrought billet with an equiaxed α microstructure. The chemical composition (in mass fraction, %) is Ti-6.2Al- 3.41Mo-1.82Zr-0.3Si-0.09O-0.02C. The β transus temperature is 1 005 °C. Several slices of the billet were heat treated at 1 020 °C for 1 h followed by water quenching to produce starting acicular microstructures. Cylindrical specimens of d 10 mm ? 15 mm were machined from the heat-treated samples. Hot compression tests were carried out at temperatures ranging from 860 to 1 100 °C and strain rates from 0.01 to 10 s-1. Samples were reheated to the test temperature within ±2 °C, soaked for 3 min and then compressed in constant strain rate to a height reduction of about 50% followed by water quenching. The temperatures of the specimens were closely monitored with a fine thermocouple soldered in the middle of each specimen. The tests were carried out in an MMS-300 thermo- mechanical simulator.
The hot-worked specimens were sectioned parallel to the compression axis and prepared by standard metallographic methods. Thin foils for transmission electron microscopy (TEM) were prepared by a twin-jet electropolishing technique in a solution of 21% perchloric acid, 50% methanol and 29% n-butyl alcohol at -30--20°C. Microstructural observations were performed using an MEF4A optical microscope and a Philips TECNAI-G2 TEM at the central part of the foils.
3 Results and discussion
The starting microstructure of the deformed alloy in the solutionized and water quenched conditions is shown in Fig.1. This type of microstructure consists of finely acicular α′ lamellae separated by retained β phase.
Fig.1 Starting microstructure of experimental alloy used in this study
3.1 Stress-strain behavior
Typical true stress-true strain curves obtained in compression at 920 °C and 1 100 °C with starting acicular microstructure are shown in Fig.2(a) which are representatives of the deformation behaviors below and above the transus temperature, respectively. The flow stress increased with decreasing the temperature at a fixed strain rate and decreased with decreasing the strain rate when the temperature was fixed. At 920 °C, the curves exhibited a peak flow stress followed by continuous flow softening. The flow softening observed on flow curves might arise from the deformation heating and microstructural changes [7]. For a strain rate of ? 0.1 s-1, adequate time was available for essentially deformation-induced heating to dissipate into the dies, and the flow softening arose from the microstructural changes. At higher strain rates (
>0.1 s-1), although the deformation heating contributed to the flow softening, most of it attributed to the bending, kinking or globularization of α platelets.
Fig.2 Compressive flow curves as function of strain rate at 920 oC (α+β region), 1 100 oC (β region) (a), and 980 oC (near β transus region) (b)
At 1 100 °C, the stress-strain flow curves showed an initial work hardening followed by a regime of steady-state flow at a strain rate from 0.01 to 1 s-1. At the strain rate of 10 s-1 and in the experimental temperature range, the curves showed broad oscillations. The steady-state curves indicated that the softening by the dislocation annihilation occurred sufficiently fast to balance the work hardening induced by the generation of dislocations and the oscillations suggested either dynamic recrystallization or flow instability like flow localization happened. The curves obtained at 980 °C (near the β transus region) were similar to those in the β region, which indicated that the deformation near the β transus region is governed essentially by the β behavior.
3.2 Kinetic analysis
The kinetic equation for hot deformation related with the flow stress (σ), deformation temperature (T) and strain rate () is
(1)
where A and α are constants, n is the stress exponent, Q is the activation energy and R is the gas constant.
The plots of ln versus ln[sinh(ασ)] in the α+β and β regions are shown in Fig.3. Over the entire range of strain rate covered in the investigation, the stress exponent n may be taken as a constant since the ln
versus ln[sinh(ασ)] plot can be considered to be a straight line. Fig.4 shows the relationship between ln[sinh(ασ)] and 1/T. By linear regression of data in Fig.4, the apparent activation energies were estimated to be 633 kJ/mol in the α+β region and 281 kJ/mol in the β region, respectively.
Fig.3 Plots of ln versus ln[sinh(ασ)] in α+β (a) and β (b) regions
Activation energies reported for titanium alloys in the α+β working are usually much higher than those for self-diffusion in α titanium and consistent with the findings in the present work [12-14]. The activation energies for the IMI834 [12], Ti-6Al-4V [14], and Ti-3Al- 5V-5Mo [15] alloys were reported to be 703, 720, and 662 kJ/mol, respectively. The large apparent activation energy has been cited as the evidence of different deformation mechanisms in terms of the occurrence of globularization or dynamic recrystallization [14]. However, BRIOTTET et al [16] suggested that the activation energy can be related to the different flow stress values of the hard α phase and the soft β phase, as well as the temperature dependency of the volume fraction of the hard α phase, which has been reported to be applicable for interpreting the plastic flow behavior during the hot working of Ti-6Al-4V alloy.
Fig.4 Arrhenius plots showing variation of flow stress with inverse of temperature in α+β and β regions
The activation energy in the β working was estimated to be 281 kJ/mol in this work. With respect to self-diffusion in the β phase of pure titanium, BROWN and ASHBY [17] calculated a value of 250 kJ/mol while WALSCOE DE RECA and LIBANATI [18] obtained 152 kJ/mol. WEISS and SEMIATIN [19] reported the activation energy in the range of 130-175 kJ/mol for the hot deformation of many β titanium alloys and 180- 220 kJ/mol for the deformation of α titanium alloys in the β region [13]. However, in single-phase metals, it has been frequently observed that the activation energy is appreciably higher when the dynamic recrystallization is the rate controlling mechanism as opposed to the dynamic recovery due to climb and cross-slip dislocation mechanisms [20]. Hence, the dynamic recrystallization likely occurred in the experimental alloy.
The temperature compensated strain rate parameter or the Zener-Hollomon parameter is defined as
(2)
Variations of Z with σ are shown in Fig.5. Due to the different activation energy values for the α+β and β regions, the data were divided into two distinct plots with a well-defined linear segment. The slope of the plot obtained by linear fitting gave a stress exponent of about 3.5 in the α+β region, while the n values decreased to about 3.2 in the β region.
Fig.5 Variations of Zener-Hollomon (Z) parameter with flow stress in α+β and β regions
3.3 Processing map and microstructural evolution
The processing map was adopted to understand the mechanisms during processing, and to recognize the instability regime. The efficiency of power dissipation, η, through the microstructural changes is given by
(3)
where m is the strain rate sensitivity. The variation of η with temperature and strain rate constitutes the power dissipation map.
A continuum criterion for the flow instability is obtained from the principles of the maximum rate of entropy production and given by
<0 (4)
where is the instability parameter. The processing map is obtained through superimposing an instability map on a power dissipation map, which exhibits not only the domains of different mechanisms but also the regions of microstructure instabilities.
The processing maps at the strains of 0.3 and 0.5 are shown in Fig.6(a) and Fig.6(b), respectively. The contour numbers indicate the efficiency of power dissipation, and the shaded regions represent the unstable regions.
Fig.6 reveals a domain in the temperature range of 860-960 °C and the strain rate range of 0.01-0.1 s-1 with a peak power dissipation efficiency of 60%, in which the alloy represents the spheroidization of acicular microstructure. This may be considered to be a type of α dynamic recrystallization where lamellae are sheared during the deformation and subsequently globularized by the diffusion processes to minimize the surface energy. Typical microstructures obtained in a specimen deformed in this domain at 860 °C are shown in Fig.7. The microstructures show almost full globularization of the lamellar α structure. With increasing the strain rate, the refinement of α grains becomes more apparent. Globular α grains are not elongated along the deformation direction, indicating that α dynamic recrystallization occurs.
Fig.6 Processing maps of Ti-6.5Al-3.5Mo-1.5Zr-0.3Si alloy at strains of 0.3 (a) and 0.5 (b) (Numbers represent efficiency of power dissipation)
TEM observations show that the microstructures comprising bent and kinked lamellae, and shearing and break-up of the lamellar structure are observed, as confirmed in Figs.7(c) and (d). The nucleation sites for the globularization would occur at these kinks in the lamellae. WEISS and SEMIATIN [13] attributed the lamellar α phase separation into shorter segments to two possible mechanisms that can occur during the thermomechanical processing, and hot working leads to the development of both low and high angle sub-boundary formation across the α plates. After the deformation at 860 °C with a strain rate of 0.1 s-1, the α phase exhibits high dislocation density (Fig.7(e)). Curved and pinned dislocations at the α/β boundaries and complex three-dimensional dislocation network in the interior of α phase are observed. The deformation is accompanied by the formation of a well-developed dislocation cell, as shown in Fig.7(f). Thermally activated glide within the subgrain interior as well as the recovery within the subgrains walls may be climb- controlled along the prism and pyramidal planes at elevated temperatures [21].
Fig.7 Optical and TEM micrographs of Ti-6.5Al-3.5Mo-1.5Zr-0.3Si alloy hot compressed at 860 °C: (a) 0.01 s-1; (b) 10 s-1; (c, d, e, f) 0.1 s-1
The processing maps in Fig.6 also exhibit a domain in the temperature range of 1 020-1 100 °C and strain rate range of 0.01-10 s-1 with a peak power dissipation efficiency of 80%. This domain is interpreted to represent the dynamic recrystallization of β phase. The typical microstructures of the alloy deformed in the β region are shown in Fig.8. The degree of dynamic recrystallization increases with the decrease of the strain rate. At the strain rate of 0.01 s-1, the recrystallized β grains have enough time to nucleate and grow, and homogeneous equiaxed β microstructure can be obtained, as depicted in Fig.8(a). At the strain rate of 1 s-1, elongated β grains with serrations developed at the grain boundaries are observed, where dynamically recrystallized grains can be easily distinguished, leading to the formation of mixed grain microstructure consisting of small equiaxed recrystallized β grains in a localized region as well as large pancaked prior β grains. Such a microstructural evolution has also been observed during the β processing of the Ti-6Al-4V alloy [4-5].
The optical micrograph for the compressed sample at 980 °C is shown in Fig.9. At the strain rate of 1 s-1, elongated β grains with dynamic recrystallization are observed. Thermal distribution remarkably influences the material behavior during the deformation. The effect is relatively minor at low strain rates due to the sufficient time for the heat dissipation. At large strain rates, most of plastic power converts to heat and results in an immediate temperature rise. The homogeneous temperature rise can be calculated as [22]
(5)
where η′ is an adiabaticity factor (?0.48, 0.88 and 0.98 for hot deformation at strain rates of 0.1, 1 and 10 s-1, respectively) [22], ρ is the density, and cp is the specific heat. According to Eq.(5), the temperature rise in the isothermal compression at 980 °C is calculated and illustrated in Table 1. The actual deformation temperature will be increased by Dt that results from serious plastic deformation. As strain rate is higher than 0.1 s-1, the temperature (t+Dt) is higher than the β transus temperature. Thus, during the deformation at 980 °C, the process of β-phase recrystallization is greatly accelerated. New equiaxed β grains form at the boundaries of the pancaked β grains and the true stress-strain curves are governed essentially by the β behavior.
Fig.8 Optical micrographs of Ti-6.5Al-3.5Mo-1.5Zr-0.3Si alloy hot compressed at 1 100 °C and different strain rates: (a) 0.01 s-1; (b) 1 s-1
Fig.9 Optical micrograph of Ti-6.5Al-3.5Mo-1.5Zr-0.3Si alloy hot compressed at 980 °C and 1 s-1
Table 1 Calculated temperature rise during hot deformation at 980 °C
4 Conclusions
1) The true stress-true strain curves exhibit a peak stress followed by the extensive flow softening behavior in the α+β region, and the flow stress has a steady-state regime in the β region.
2) The constitutive analysis shows that the apparent activation energies are estimated to be 633 kJ/mol in the α+β region and 281 kJ/mol in the β region, respectively. The variations of Z with σ follow a well-defined linear fit.
3) The processing maps exhibit the spheroidization of the acicular microstructure and α dynamic recrystallization at lower temperatures, and β dynamic recrystallization in the β region. When the alloy is deformed at 980 °C with ?1 s-1, the flow behavior and microstructural evolution are resulted from the deformation heating and are governed by the β behavior.
References
[1] FILIP R, KUBIAK K, ZIAJA W, SIENIAWSKI J. The effect of microstructure on the mechanical properties of two-phase titanium alloys [J]. J Mater Proc Technol, 2003, 133: 84-89.
[2] JACKSON M, DRING K. Materials perspective: A review of advances in processing and metallurgy of titanium alloys [J]. Mater Sci Technol, 2006, 22: 881-887.
[3] CHUN Y B, HWANG S K. Static recrystallization of warm-rolled pure Ti influenced by microstructural inhomogeneity [J]. Acta Mater, 2008, 56: 369-379.
[4] DING R, GUO Z X, WILSON A. Microstructural evolution of a Ti-6Al-4V alloy during thermomechanical processing [J]. Mater Sci Eng A, 2002, 327: 233-245.
[5] MARTIN P L. Effects of hot working on the microstructure of Ti-base alloys [J]. Mater Sci Eng A, 1998, 243: 25-31.
[6] WEISS I, FROES F H, EYLON D, WELSCH G E. Modification of alpha morphology in Ti-6Al-4V by thermomechanical processing [J]. Metall Trans A, 1986, 17: 1935-1947.
[7] SEMIATIN S L, SEETHARAMAN V, WEISS I. Flow behavior and globularization kinetics during hot working of Ti-6Al-4V with a colony alpha microstructure [J]. Mater Sci Eng A, 1999, 263: 257- 271.
[8] SAVAGE M F, TATALOVICH J, ZUPAN M. Deformation mechanisms and microtensile behavior of single colony Ti-6242Si [J]. Mater Sci Eng A, 2001, 319/320/321: 398-403.
[9] LI M Q, LIU X M, XIONG A M. Prediction of the mechanical properties of forged TC11 titanium alloy by ANN [J]. J Mater Process Technol, 2002, 121: 1-4.
[10] LI A B, HUANG L J, MENG Q Y. Hot working of Ti-6Al-3Mo- 2Zr-0.3Si alloy with lamellar α+β starting structure using processing map [J]. Materials and Design, 2009, 30: 1625-1631.
[11] POORGANJI B, YAMAGUCHI M, ITSUMI Y, MATSUMOTO K. Microstructure evolution during deformation of a near-α titanium alloy with different initial structures in the two-phase region [J]. Scripta Mater, 2009: 61, 419-422.
[12] WANJARA P, JAHAZI M, MONAJATI H, YUE S. Influence of thermomechanical processing on microstructural evolution in near-α alloy IMI834 [J]. Mater Sci Eng A, 2006, 416: 300-311.
[13] WEISS I, SEMIATIN S L. Thermomechanical processing of alpha titanium alloys—An overview [J]. Mater Sci Eng A, 1999, 263: 243-256.
[14] SHEPPARD T, NORLEY J. Deformation characteristics of Ti-6Al-4V [J]. Mater Sci Technol, 1988, 4: 903-908.
[15] LOU L X, YANG Y, PENG L B. Flow stress behavior and deformation characteristics of Ti-3Al-5V-5Mo compressed at elevated temperatures [J]. Mater Design, 2002, 23: 451-457.
[16] BRIOTTET L, JONAS J J, MONTHEILLET F. A mechanical interpretation of the activation energy of high temperature deformation in two phase materials [J]. Acta Mater, 1996, 44: 1665- 1672.
[17] BROWN A M, ASHBY M F. Correlations for diffusion coefficients [J]. Acta Metall, 1980, 28: 1085-1101.
[18] WALCOE DE RECA N E, LIBANATE C M. Self-diffusion in β- titanium and β-hafnium [J]. Acta Metall, 1968, 16: 1297-1305.
[19] WEISS I, SEMIATIN S L. Thermomechanical processing of beta titanium alloys—An overview [J]. Mater Sci Eng A, 1998, 243: 46-65.
[20] SEMIATIN S L, MONTHEILLET F, SHEN G. Self-consistent modeling of the flow behavior of wrought alpha/beta titanium alloys under isothermal and nonisothermal hot-working conditions [J]. Metall Mater Trans A, 2002, 33: 2719-2727.
[21] MYTHILI R, SAROJA S, VIJAYALAKSHMI M. Study of mechanical behavior and deformation mechanism in an α-β Ti-4.4Ta-1.9Nb alloy [J]. Mater Sci Eng A, 2007, 454/455: 43-51.
[22] OH S I, SEMIATIN S L, JONAS J J. An analysis of the isothermal hot compression test [J]. Metall Trans A, 1992, 23: 963-975.
(Edited by YANG Bing)
Foundation item: Project(50901063) supported by the National Natural Science Foundation of China; Project(2007DS0414, 2007BS05006) supported by the Science and Technology Program of Shangdong Province, China; Project supported by the Open Research Fund from State Key Laboratory of Rolling and Automation, Northeastern University, China
Received date: 2010-01-27; Accepted date: 2010-04-22
Corresponding author: ZHANG Shang-zhou, Professor, PhD; Tel: +86-535-6706731; E-mail: szzhangyt@163.com
- Hot deformation behavior of Ti-6.5Al-3.5Mo-1.5Zr-0.3Si alloy withacicular microstructure
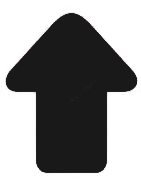