- Abstract:
- 1 Introduction▲
- 2 Experimental▲
- 3 Results and discussion▲
- 4 Conclusions▲
- References
- Figure
- Fig.1 SEM image of carbon fibre powder
- Fig.2 Apparatus for electrical resistivity measurements: 1—Furnace; 2—Carbon cathode block; 3—TiB2 coating; 4—Graphite clamps; 5—Stainless steel rod
- Fig.3 SEM images of samples with different carbon fibre lengths: (a) 1 mm; (b) 9 mm
- Fig.4 SEM image of coating sample
J. Cent. South Univ. Technol. (2008) 15: 526-530
DOI: 10. 1007/s11771-008-0099-3
Effect of carbon fibre on properties of
TiB2/C composite cathode coating for aluminum electrolysis
LI Jie(李 劼)1, L? Xiao-jun(吕晓军)1, LAI Yan-qing(赖延清)1, LI Qing-yu(李庆余)1, 2,
TIAN Zhong-liang(田忠良)1, FANG Zhao(方 钊)1
(1. School of Metallurgical Science and Engineering, Central South University, Changsha 410083, China;
2. School of Chemistry and Chemical Engineering, Guangxi Normal University, Guilin 541004, China)
Abstract:
The tensile strength, compressive strength and electrical resistivity of TiB2/C composite cathode coating were measured with a hydraulic pressure universal test machine and an electrical resistivity test device, and the effects of carbon fibre content and carbon fibre length on tensile strength, compressive strength and electrical resistivity were investigated. The results show that the tensile strength of coating increases at the beginning and then reduces with the increase of carbon fibre content when the carbon fibre (length of 3 mm) content ranges from 0 to 4.0%; at the carbon fibre content of 1.5%, the tensile strength of coating reaches the maximum, 25.6 MPa. For the coating with carbon fibre content of 1.5%, the carbon fibre length has a great influence on tensile strength and compressive strength of coating; when the carbon fibre length is 6 mm, the tensile strength and compressive strength of coating reach the maximum, 27.6 MPa and 39.2 MPa, respectively. The electrical resistivity of coating reduces with the rise of temperature and the length of carbon fibre, and the influence of carbon fibre length on electrical resistivity of coating at low temperature (30-200 ℃) is more obvious than that at high temperature (960 ℃).
Key words:
aluminum electrolysis; TiB2 coating; electrical resistivity; tensile strength; compressive strength;
1 Introduction
The conventional Hall-Heroult process has been the unique commercial method for production of aluminum, which adopts carbon material as anode and cathode, resulting in high energy consumption and environment pollution and so on[1]. At present, a new aluminum electrolysis cell, using inert anode and wettable cathode, has been developed, which may overcome the shortcomings of the conventional aluminum electrolysis process[2-3]. TiB2 is an ideal material because of its excellent electronic conductivity, which is comparable with metal, good corrosion resistance to aluminum and molten cryolite salt, and good wettability by aluminum liquid[2]. In recent years, TiB2 material used as inert wettable cathode for aluminum electrolysis has been investigated[3-7]. For pure TiB2 plate, because of many disadvantages, such as high cost, difficulty in sintering and poor mechanical properties, many researchers have focused on developing TiB2 matrix composite materials, which are cheaper and adhered easily to substrate compared with pure TiB2, and have the same merits as pure TiB2. Among them, the most representative material is TiB2/C composite coating (TCC)[4], which can be utilized not only in the drained cathode cell to reduce energy consumption, but also in the conventional cell to extend potlife, lower energy consumption and improve efficiency of cell operation[8-12].
TCC has many advantages, such as good resistance to sodium expansion, saving energy and wettability with aluminum liquid. Since cathode material should not only bear the gravity of bath and aluminum liquid in cells, but also suffer the stress resulting from heat expansion during the preheating and start-up and sodium expansion during the electrolysis. Therefore, it is the prerequisite that TiB2/C coating must have excellent mechanical properties, especially, tensile strength and compressive strength, in order to realize excellent properties of coating. Moreover, the electrical resistivity of coating has great influence on saving energy for aluminum electrolysis. Currently, many studies on TCC for aluminum electrolysis have already been carried out [8-13], but the study on improving the properties of TCC using carbon fibre has not been reported.
In this work, the effects of the content and the length of carbon fibre on tensile strength, compressive strength and electrical resistivity of TiB2/C coating were studied. The purpose is to extend service life of TCC and reduce energy consumption.
2 Experimental
2.1 Raw materials
The performance indexes of polyacrylonitrile (PAN) carbon fibre are listed in Table 1. Its diameter is 6-7 μm, which is sheared to the length of 1, 3, 6 and 9 mm according to experimental requirement.
Carbon fibre powder is still fibrous from Fig.1, but its length is short, and its diameter is 7.4 μm, and the mean length is 43 μm.
Table 1 Performance indexes of polyacrylonitrile (PAN) carbon fibre
Fig.1 SEM image of carbon fibre powder
Compositions (mass fraction) of TCC are as follows: TiB2 powder 30%-70%, carbonaceous additive 10%-30%, organic solvent 2%-4%, mixed resin 2%-10%, toughness enhancement agent 0.5%-1.0%, reinforcing agent 1%-4% and solidified agent 0.5%-1.0%.
2.2 Preparation of TCC slurry
The carbon fiber was poured into the mixed resin solution. After 2 h, the mixture consisting of the carbonaceous additive, TiB2 powder and strength enhancement agent which was mixed in three-dimension kinetic mixer, was added to the solution and stirred thoroughly. Thus, TCC slurry was obtained.
2.3 Test of TCC properties
2.3.1 Test of TCC tensile strength and compressive strength
Test was implemented by reference to GB1431-85. Coating slurry was pressed in steel mould, and withdrawn from mold after 30 min, then thin slice coating test specimen with diameter of 30 mm and height of 5 mm was obtained after solidification and carbonization. The maximum loads of specimens abruption were measured with hydraulic pressure universal test machine(WE-300C, Ji’nan, China), and the coating tensile strength and compressive strength may be obtained through calculation using the following formula:
δ=F/S (1)
where δ is the tensile strength or compressive strength, Pa; F is the maximum load of specimen abruption, N; S is coating surface area, m2.
Three specimens with the same component were prepared and measured, the mean value was used as the ultimate experimental result.
2.3.2 Test of electrical resistivity of TCC at high temperature
Cathode carbon block was machined to the cylinder sample(diameter 20 mm, height 20 mm) and its surface was treated by acetone. Then, two cylinder blocks were bonded by coating slurry, and the thickness of the layer was 4-5 mm. After solidification, the electrical resistivity of TCC was measured with direct current four-probe method (Fig.2) at different temperatures under argon atmosphere.
Fig.2 Apparatus for electrical resistivity measurements: 1—Furnace; 2—Carbon cathode block; 3—TiB2 coating; 4—Graphite clamps; 5—Stainless steel rod
3 Results and discussion
3.1 Effect of carbon fibre content on TCC tensile strength
The tensile strength of TCC specimens containing carbon fibre (length of 3 mm) was measured and the results are listed in Table 2. From Table 2, when the coating does not contain carbon fibre, the tensile strength of coating is low, only 3.2 MPa. The tensile strength of coating is improved when carbon fibres are added. TCC tensile strength increases with the increase of carbon fibre content when the carbon fibre content is less than 1.5%. But it reduces with increasing content further. The tensile strength is only 6.5 MPa for TCC coating containing carbon fibre 4.0%. The tensile strength of coating reaches the maximum value when the carbon fibre content is 1.5%.
Table 2 Tensile strength of TCC samples with different contents of carbon fiber
The characteristic of composite materials is the interface formation between reinforcing agent and matrix, and the interface acts as transferring load[14]. In TCC coating, the interface is formed by carbon fibre and resin, when coating endures an external force. The interface can transfer the external force to carbon fibre, and bridge the gap between resin and carbon fibre. The interface can impede crack propagation, and slow up the stress concentration. Consequently, mechanical property of TCC, i.e. tensile strength, is improved. Evidently, bonding state and intensity of interface can affect the coating properties. When a few carbon fibres are added to coating, carbon fibres can be dispersed uniformly, and are rather wettable with resin. The carbon fibres can act as strength enhancement since the interface bond between carbon fibre and resin is tight. Thus, the tensile strength of coating increases. Due to enhancing strength of carbon fibres, tensile strength of coating reduces gradually with the increase in carbon fibre content. When the content of carbon fibre is above 1.5%, the dispersibility of carbon fibres becomes worse[15]. The carbon fibre intertwines each other and aggregation appears, and resin(its content is invariable to the same recipe) in coating is also not complete wettability with carbon fibre, which results in poor interface bond, so that defects are left in the coating. Therefore, carbon fibre cannot completely play the function of strength enhancement, and TiB2 coating tensile strength reduces. The higher the content of carbon fibre is, the more the defects in coating are, the lower the tensile strength of TCC is. Therefore, the effect of length of carbon fibre on TCC properties was further investigated when the content of carbon fibre is 1.5% in the present study.
3.2 Effect of carbon fibre length on tensile strength and compressive strength of TCC
Table 3 lists the results of the compressive strength and tensile strength of TCC samples containing 1.5% carbon fibre powder or various carbon fibre (the length of 1, 3, 6 and 9 mm).
Table 3 Tensile strength and compressive strength of samples with different lengths of carbon fibre
As shown in Table 3, when carbon fibre powder is used as reinforcing agent, both compressive strength and tensile strength are minimum, which are 20.3 and 14.4 MPa, respectively. When the length of the carbon fiber increases, the strength of coating improves slightly. When the length of carbon fibre is 6 mm, both the compressive strength and the tensile strength reach maximum, which are 39.2 and 27.6 MPa, respectively. When the length of carbon fiber is extended to 9 mm, the compressive strength and the tensile strength of the coating decrease somewhat. The results show that influence of carbon fibre length on compressive strength and tensile strength of coating is significant. At first, both compressive strength and tensile strength increase with increasing length of carbon fibre. After the length reaches 6 mm, the compressive strength and the tensile strength tend to drop.
Since there are three ways by which composite material absorbs impact strength: fibre breakage, fibre extraction and base breakage. Generally, long carbon fibre makes fibre extraction consume more energy and facilitate the enhancement of impact strength. Meanwhile, the end of the fibre is the starting point of the crack growth. If carbon fibre content is the same, long fibre, compared with short fibre, has fewer ends, which enhances the impact strength[16]. But as the length of carbon fibre is 9 mm, the compressive strength and tensile strength decrease. The reason is that the difficulty of carbon fibre dispersing in coating augments after extending the length of carbon fibre, which makes the dispensability of carbon fiber bad and tend to aggregation. SEM images of samples with different lengths of carbon fibre are shown in Fig.3. From Fig.3(a), it can be seen that the disgregation of carbon fibre is homogeneous; the aggregation of carbon fibre appears in Fig.3(b). The local flaws in coating appear easily, and the enhancement function of carbon fiber cannot be exerted completely, so the compressive strength and the tensile strength of TCC decrease.
3.3 Effect of carbon fibre length on electrical resistivity of TCC
In order to study the effect of carbon fibre length on electrical resistivity of coating, coating specimens with the carbon fibre powder and carbon fibre length of 1, 3, 6 and 9 mm were prepared when the carbon fibre content was 1.5%, and electrical resistivities of coating from room temperature to 960 ℃ were measured. The results are listed in Table 4.
Fig.3 SEM images of samples with different carbon fibre lengths: (a) 1 mm; (b) 9 mm
Table 4 Electrical resistivity of coatings with different carbon fibre lengths
As listed in Table 4, the electrical resistivity of coating reduces rapidly with the increase of temperature no matter whether carbon fibre is long or short. At a low temperature, resin can hardly conduct electricity, or the ability of electrical conduction is poor. With the escape of water, small resin molecules and organic solvent, the carbonization of resin occurs as temperature increases, then the electrical conductivity of coating increases. But the electrical resistivity of coating at low temperature is greatly influenced by the length of carbon fibre. As listed in Table 4, the electrical resistivity of coating containing the same content of carbon fibre remarkably decreases with the increase in the length of carbon fibre in the range of room temperature to 200 ℃. When the length of carbon fibre is 9 mm, the electrical resistivities of coating at room temperature and 200 ℃ are 98 117.5 and 54 145.8 μΩ?m, respectively. Both of them are obviously lower than those of counterparts with carbon fibre length of 1, 3, 6 mm. The resin is gelatinous at low temperature, although there are many TiB2 particles with good electrical conductivity in the coating. These small electricparticles are easily packed by resin, and the formation of electric-access or network run-through the whole coating is difficult. The electrical resistivity of carbon fibre is 10-100 μΩ·m, but it is good electrical conductor compared with the resin in the coating. Although the content of carbon fibres is low, carbon fibres also have synergistic effects on the formation of electric-access and network with increasing their length, therefore the electrical resistivity of TCC is reduced. In industrial aluminum electrolysis cell, the smaller the electrical resistivity of coating at low temperature, the higher the impulse voltage of coating-cell reduced during preheating and startup. To this significance, the longer the carbon fibre, the smaller the electrical resistivity of coating at low temperature, which is better to the preheating and startup of coating cell. Again from Table 4, the electrical resistivity of coating slowly decreases with the increase in the length of carbon fibre at 960 ℃. When the length of carbon fibre is 9 mm, the electrical resistivity of coating is 28.9 μΩ·m, while those of the counterparts with carbon fibre length of 1, 3 and 6 mm, are 38.0, 34.2, 30.4 μΩ·m, respectively. The influence of carbon fibre length on the electrical resistivity of coating at high temperature is smaller than that at low temperature. The reason is that after carbonization of resin at 960 ℃, TiB2 and carbon particles turn into chief current-conducting phase due to their large quantities, so the current-conducting effect of carbon fibre on coating is weakened compared with the situation at low temperature. In spite of how about the production process, it is certain that there are some tiny interspaces generating as the resin or organic solvent carbonizes in coating, which increases the electrical resistivity of coating. With the increase in the length of carbon fibre, the probability of formation of electric-access or network with tiny interspaces run-through the whole coating increases, as shown in Fig.4. That is to say, long carbon fibres have synergistic effects on the formation of electric-network and can intensify the migration ability of electron, and reduce the electrical resistivity of coating. Taking the electrical resistivity of coating at low and high temperatures and the dispersion of carbon fibre into consideration, the best length of carbon fibre used in TiB2 coating is 6 mm.
Fig.4 SEM image of coating sample
4 Conclusions
1) Increasing content of carbon fibre (length of 3 mm) from 0 to 4.0% leads to a first increase of coating tensile strength up to a maximum, followed by a decreasing trend for further additions. When the content of carbon fibre is 1.5%, its tensile strength is 25.6 MPa, which is the maximum.
2) For the coating containing 1.5% carbon fibre, its tensile strength and compressive strength increase firstly and then reduce with the length of carbon fibre. The tensile strength and the compressive strength of TCC reach the maximum, 27.6 and 39.2 MPa, respectively, when the carbon fibre length is 6 mm. For coating with carbon fibre of 9 mm, its tensile strength and compressive strength are 26.8 and 38.7 MPa, respectively.
3) The electrical resistivity of coating containing carbon fibre 1.5% decreases with increasing temperature and length of the carbon fibre, and influence of the length of carbon fibre on its electrical resistivity at low temperature (30-200 ℃) is more obvious than that at high temperature (960 ℃). At 960 ℃, the electrical resistivity of coating with the carbon fibre length of 9 mm is 28.9 μΩ·m, which is as those of much as counterparts with carbon fibre powders and the carbon fibre length of 1, 3 and 6 mm. But the electrical resistivities of coating with carbon fibre length of 9 mm at room temperature and 200 ℃, which are 98 117.5 and 54 145.8 μΩ·m, respectively, are much smaller than those of coatings with other four shorter carbon fibres at the corresponding temperature.
References
[1] WELCH B J. Future materials requirements for the high-energy- intensity production of aluminum [J]. Journal of Metal, 2001, 53(2): 13-15.
[2] MCMINN C J. A review of RHM cathode development [C]// CUTSHALL E R. Light Metals 1992. Warrendale: TMS, 1992: 419-425.
[3] PAWLEK R P. Aluminum wettable cathodes: An update [C]// PETERSON R D. Light Metals 2000. Warrendale: TMS, 2000: 449-454.
[4] DIONNE M, LESPERANCE G, MIRTCHI A. Wetting of TiB2-carbon material composite[C]// ECKERT C E. Light Metals 1999. Warrendale: TMS, 1999: 389-394.
[5] BROWN C W. Wettability of TiB2-based cathodes in low- temperature slurry-electrolyte reduction cells [J]. Journal of Metal, 1998, 50(2): 38-40.
[6] SEKHAR J A, de NORA V, LIU J, WANG X. TiB2/colloidal alumina carbon cathode coating in Hall-Heroult and drained cells [C]// WELCH B. Light Metals 1998. Warrendale: TMS, 1998: 605-615.
[7] ALTON T, BROWN J, IVAN E, WILLIAM M. The operational performance of 70 kA prebake cells retrofitted with TiB2-G cathode elements [C]// WELCH B. Light Metals 1998. Warrendale: TMS, 1998: 257-264.
[8] LAI Yan-qing, LI Qing-yu, YANG Jian-hong, LI Jie. Ambient temperature cured TiB2 cathode coating for aluminum electrolysis [J]. Trans Nonferrous Met Soc China, 2003, 13(3): 704-707.
[9] LIAO Xian-an, ?YE H A. Effects of carbon-bonded coatings on sodium expansion of the cathode in aluminum electrolysis [C]// ECKERTC E. Light Metals 1999. Warrendale: TMS, 1999: 629-636.
[10] LI Qing-yu, LAI Yan-qing, LI Jie, YANG Jian-hong, CHEN Zhu. The effect of sodium-containing additives on the sodium-penetration resistance of TiB2/C composite cathode in aluminum electrolysis [C]// KVANDE H. Light Metals 2005. Warrendale: TMS, 2005: 789-791.
[11] LIAO Xian-an, HUANG Yong-zhong, LIU Ye-xiang. Potline-scale application of TiB2 coating in Hefei Aluminum & Carbon Plant [C]// WELCH B. Light Metals1998. Warrendale: TMS, 1998: 685-688.
[12] LI Qing-yu, LAI Yan-qing, LI Jie, YANG Jian-hong, LIU Ye-xiang. Sodium penetration resistance of ambient temperature cured TiB2 cathode coating [J]. Journal of Central South University: Natural Science, 2004, 35(6): 907-910. (in Chinese)
[13] LI Jie, L? Xiao-jun, LI Qing-yu, LAI Yan-qing, YANG Jian-hong. Electrical resistivity of TiB2/C composite cathode coating for aluminum electrolysis [J]. Journal of Central South University of Technology, 2006, 13(3): 209-213.
[14] HU Fu-zeng, CHEN Guo-rong. Material surface and interface [M]. Shanghai: East China Science and Technology University Press, 2001. (in Chinese)
[15] LI Qing-yu. Development and industrial application of wettable inert TiB2 cathodic composite coating for aluminum electrolysis [D]. Changsha: Central South University, 2003. (in Chinese)
[16] NING Ping, HU Jian, YI Feng, XIA Lin. Structure and performance of TLCP composite material as a reinforcing agent of carbon fibre [J]. Transactions of South China Science and Technology: Science and Technology, 2003, 31(9): 62-65. (in Chinese)
Foundation item: Project(2005CB623703) supported by the Major State Basic Research Development Program of China
Received date: 2007-12-15; Accepted date: 2008-03-18
Corresponding author: L? Xiao-jun, Doctoral candidate; Tel: +86-731-8876454; E-mail: lxj8886@yahoo.com.cn
(Edited by YANG Hua)
- Effect of carbon fibre on properties of TiB2/C composite cathode coating for aluminum electrolysis
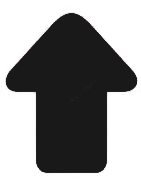