- Abstract:
- 1 Introduction▲
- 2 Determination of streng...▲
- 3 Engineering application▲
- 4 Conclusions▲
- References
- Figure
- Fig.1 Evolution law of cohesive and frictional strength with irreversible strains
- Fig.2 Schematic diagrams of cohesion weakening and friction strengthening process: (a) Cohesion weakening process; (b) Friction strengthening process; (c) Cohesion weakening and friction strengthening process
- Fig.3 Schematic diagram of Mine-by test tunnel and failed zones: (a) View of testing tunnel (MARTIN, 1997)[2]; (b) Slabbing from tunnel top (MARTIN, 1997)[2]; (c) Failure shape (HAJIABDOLMAJID et al, 2002)[3]
- Fig.4 Numerical simulation results with elastic-perfectly plastic model (a) and elasto-brittle-plastic model (b)
- Fig.5 Comparison of numerical simulation results with progressive damage model and field test: (a) Progressive damage model; (b) Failed shape in field test (HAJIABDOLMAJID et al, 2002)[3]
J. Cent. South Univ. Technol. (2008) 15: 493-497
DOI: 10.1007/s11771-008-0093-9
Strength evolution law of cracked rock based on localized progressive damage model
ZHANG Ping(张 平)1, 2, LI Xi-bing(李夕兵)1, LI Ning(李 宁)3
(1. School of Resources and Safety Engineering, Central South University, Changsha 410083, China;
2. Institute of Geotechnical Engineering, Hunan University, Changsha 410082, China;
3. Institute of Geotechnical Engineering, Xi’an University of Technology, Xi’an 710048, China)
Abstract:
In the light of the localized progressive damage model, the evolution law of cohesive and frictional strength with irreversible strains was determined. Then, the location and the extent of the excavation disturbed zone in one deep rock engineering were predicted by using the strength evolution law. The theoretical result is close to the result of in-situ test. The strength evolution law excels the elastic-perfectly plastic model and elasto-brittle plastic model in which the cohesive and frictional strength are mobilized simultaneously. The results obtained indicate that the essential failure mechanism of the cracked rock can be described by the cohesion weakening and friction strengthening evolution law.
Key words:
rock mechanics; strength; failure mechanism; localization; evolution law;
1 Introduction
In order to describe the real failure process, elasto- plastic mechanics, fracture mechanics and damage mechanics have been used, but the research result does not coincide with the laboratory test well. The mechanism of pure plastic deformation is slippage and dislocation along crystallographic defects. But it is difficult to explain the brittle failure of rock using the traditional plastic mechanics[2-4]. As pointed by CHEN[5], brittle rock lacks so many slippage surfaces, so that the failure essence of brittle rock is the open and propagation of these micro-cracks and it does not obey the Prager-Drucker plastic flow rule.
LING and SUN[6] also thought that the irreversible deformation of rock under isothermal process is mainly due to the micro-cracks (damage) evolution, including initiation, development and energy cumulation except for the soft rock, the rock under deep or high surrounding pressure condition. In addition, fracture mechanics theory mainly studies the initiation of limited macro-cracks. The propagation of lots of micro-cracks and flaws is hard to study one by one using fracture mechanics. Furthermore, under compressive loading conditions fracture initiation does not necessarily lead to the global failure of rock, so the result predicted by fracture mechanics is rather conservative. Damage mechanics can explore the propagation of plenty of micro-cracks, and it is suitable to study the whole failure process of brittle rock based on an internal variable. But the traditional damage models assume that the distributions of stress, strain and micro-cracks are uniform enough, the volume can be considered a continuum, which does not coincide with the heterogeneous behaviour of rock in mesoscale[7-8]. Although based on the statistical damage theory[9], the statistical strength characteristics and continuous damage theory have been combined into the constitutive model[10]. But the obvious localization deformation of rock and frictional properties of failed rock are still neglected.
Therefore, these models generally cannot represent many of the micro-mechanical processes in brittle failure of rock. The key point to describe the micro-mechanical properties and failure mechanism of rock is to determine the damage evolution law of internal structure[7, 11].
Based on the cracked rock-like model experiment, the meso failure process has been found and can be divided into bond rupture stage (rock bridge breaking) and frictional resistance mobilization stage (rupture surface sliding). Furthermore, the chain model in localized band and the homogenization method were adopted to combine the meso characteristics with the macro mechanical properties in this localized progressive damage model[12].
In this work, the cohesive and frictional strength were determined and the evolution law of these strength components and its application were further discussed using the model mentioned above.
2 Determination of strength parameters
Based on the localized progressive damage model[12], the process of cohesion weakening and friction strengthening can be learnt clearly. But the evolution of strength parameters is related to the deformation, it is hard to use in practice. So, in order to analyze and simulate the failure process of cracked rock, it is necessary to simplify the model and give the practicable evolution of the strength parameters.
2.1 Determination of cohesive strength
Because of the heterogeneity of cracked rock, the process of cohesion weakening and friction strengthening is progressive, that is to say, the peak strength contains cohesive and frictional strengths. The traditional cohesion and friction coefficient (including the peak and residual value) tested through the direct shear test or triaxial compressive test are the fitting of strength envelopes and they represent intercept and slope of the envelope curves, respectively. Actually, the cohesion and friction coefficient does not mean the cementation strength and friction efficient of the grains. Therefore, it is only named apparent cohesion and friction coefficient.
According to the progressive damage model in Ref.[12], the cohesive strength can be obtained by its equation (9), i.e. the evolution of shear stress is where τ1 is the shear stress mobilized by grains’ cementation; and
are the equivalent elastic modulus and Poisson ratio of cracked rock, respectively; Ws is the thickness of the localized shear zone; δ is the damage variable; us is the shear displacement between the upper and lower shear surfaces; m is the heterogeneous index of rock and
is the critical shear displacement when confining pressure is zero.
(1)
Let ?τ1/?us=0, the maximum of τ1 is the cohesive strength τc. That is
(2)
According to Eqn.(2), the cohesive strength of sandstone, norite and granite under uniaxial loading can be obtained as listed in Table 1.
Table 1 Cohesive strength of sandstone, norite and granite under uniaxial loading
MARTIN and CHANDLER[13] found that the ratio of cohesive strength to uniaxial compressive strength of granite is about 35%-43% in virtue of the cyclic loading experiment. The data in Table 1 indicate that the result of this model coincides with the experimental result approximately.
2.2 Determination of evolution of strength components
Based on the evolution process curves of the cohesive strength and frictional strength of sandstone (confining pressure is 5 MPa) by this model, it can be found that the process of cohesion weakening and friction strengthening is progressively developed with the irreversible strains in Fig.1. Moreover, the process can be simplified as a linear line. If we adopt the elasto-plastic model, the irreversible strain can be regarded as the plastic strain. So the relationship curves of cohesive strength—equivalent plastic strain and frictional strength—equivalent plastic strain
are plotted on τ—ε plane in Fig.2. In Fig.2 superscript ‘p’means that the strain is plastic or irreversible; subscript ‘c’ or ‘f’ indicates the cohesion or friction; εe is the elastic strain; Cp and Cr are peak and residual cohesive strength, respectively; σn is the normal stress on the shear surface; φ is the frictional angle of rock.
Fig.1 Evolution law of cohesive and frictional strength with irreversible strains
Fig.2 Schematic diagrams of cohesion weakening and friction strengthening process: (a) Cohesion weakening process; (b) Friction strengthening process; (c) Cohesion weakening and friction strengthening process
According to this method, the two plastic strains of sandstone in Fig.1 can be determined as 0.007 5,
0.01. HAJIABDOLMAJID et al[3] proposed the cohesion weakening and friction strengthening concepts, but the parameters of
and
were only determined by trial and error method. Obviously, the parameters derived through experimental and theoretical data in this work are more reasonable.
Therefore, the progressive damage process of rock can be simulated only by introducing the strength parameter and the equivalent plastic strain. Moreover, the softening process and post-peak properties can be simulated simultaneously.
3 Engineering application
3.1 Introduction of field test
Between 1990 and 1995 Atomic Energy of Canada Limited Company carried out a Mine-by test at the URL in Pinawa, Manitoba, Canada. This well documented experiment involved the excavation of a 3.5 m-diameter circular test tunnel with the depth of 420 m in massive granite. To achieve this objective the tunnel was excavated by using a boring technique, and displacements, strains, stress changes and acoustic emissions were monitored with current instruments[2].
The in-situ stresses near the tunnel were determined accurately: σ1=(60±3) MPa, σ2=(45±4) MPa, σ3= (11±2) MPa. Extensive laboratory tests were carried out. The mechanical parameters of granite are listed in Table 2.
Table 2 Mechanical parameters of granite
The failure shapes of the tunnel in the roof and the floor are in classic V-shaped notches, and the tensile zones lie in the side walls of the tunnel. The shapes of the failed zone observed around the circular test tunnel are shown in Fig.3.
3.2 Validation of model
According to the initial stress in situ and the geometrical size of the tunnel, the numerical model was established and the excavation response of tunnel was simulated by numerical code[14]. Firstly, the elastic-perfectly plastic model with the traditional failure criterion (Mohr-Coulomb criterion) in which the cohesion and the normal stress-dependent frictional strength components were assumed to be simultaneously mobilized was used to calculate (see Table 3, scheme A).
The predicted failed zone with elastic-perfectly plastic model is shown in Fig.4(a). The elasto-brittle- plastic model with residual strength parameters were chosen, and the two strength components were also assumed to be simultaneously mobilized and then lost in the post-peak range (see Table 3, scheme B). The predicted failed zone and elasto-brittle-plastic model is shown in Fig.4(b). It can be seen from Fig.4 that plastic areas at the top and bottom of the tunnel are not similar to the failure shape in situ. These two models with typical strength parameters have not been successful in predicting the depth and extent of failed rock in deep underground opening in hard rock.
Fig.3 Schematic diagram of Mine-by test tunnel and failed zones: (a) View of testing tunnel (MARTIN, 1997)[2]; (b) Slabbing from tunnel top (MARTIN, 1997)[2]; (c) Failure shape (HAJIABDOLMAJID et al, 2002)[3]
Table 3 Numerical parameters in different schemes
According to the shear test result on intermittent rock joints[15] and the progressive damage model[12], it is known that the cohesive strength and frictional strength cannot be mobilized simultaneously. Moreover, the strength parameters and the equivalent plastic strains can be obtained through the analytical result of the theoretical model.
Fig.4 Numerical simulation results with elastic-perfectly plastic model (a) and elasto-brittle-plastic model (b)
Fig.5(a) shows the simulated failed zone by using the cohesion weakening and friction strengthening evolution law with the parameters (see Table 3, scheme C). Despite several simplifications, the predicted depth and extent of the failed zone are in excellent agreement with the measured failed zone shown in Figs.3(b) and 5(b).
The numerical results indicate that strength parameters should be adopted according to the cohesion weakening and friction strengthening evolution law and the progressive damage process of brittle rock can be modeled well by this model.
4 Conclusions
1) Based on the localized progressive damage model, the evolution law of cohesive and frictional strength with the irreversible strains is determined.
2) The strength evolution law can be described as cohesion weakening and then friction strengthening in the post-peak stress-strain curve. Both of them are not mobilized simultaneously.
Fig.5 Comparison of numerical simulation results with progressive damage model and field test: (a) Progressive damage model; (b) Failed shape in field test (HAJIABDOLMAJID et al, 2002)[3]
3) By virtue of the strength evolution law, the location and the extent of the excavation failed zone in one deep rock engineering are predicted well. The theoretical result is close to the result of in-situ test, which means that the strength evolution law excels the elastic-perfectly plastic model and elasto-brittle-plastic model in which the cohesive and frictional strength are mobilized simultaneously.
References
[1] CHEN Feng, SUN Zong-qi, XU Ji-cheng, ZHANG Jing-yi. A composite material model for investigation of micro-fracture mechanism of brittle rock subjected to uniaxial compression [J]. Journal of Central South University of Technology, 2001, 8(4): 258-262.
[2] MARTIN C D. Seventeenth Canadian geotechnical colloquium: The effect of cohesion loss and stress path on brittle rock strength [J]. Canadian Geotechnical Journal, 1997, 34(5): 698-725.
[3] HAJIABDOLMAJID V, KAISER P K, MARTIN C D. Modelling brittle failure of rock [J]. International Journal of Rock Mechanics and Mining Sciences, 2002, 39(6): 731-741.
[4] LABUZ J F, BIOLZI L. Experiments with rock: Remarks on strength and stability issues [J]. International Journal of Rock Mechanics and Mining Sciences, 2007, 44: 525-537.
[5] CHEN Zong-ji. Engineering record, theory and control of rock burst [J]. Chinese Journal of Rock Mechanics and Engineering, 1987, 6(1): 1-17. (in Chinese)
[6] LING Jian-ming, SUN Jun. A constitutive relation of rock mass expressed in strain space [J]. Journal of Tongji University, 1994, 22(2): 135-140. (in Chinese)
[7] SHEN Zhu-jiang, CHEN Tie-lin. Breakage mechanics for geological materials basic concepts, goal and task [C]// Proceedings of the 7th Rock Mechanics and Engineering Conference. Beijing: China Science and Technology Press, 2002: 9-12. (in Chinese)
[8] WONG T F, WONG R H C, CHAU K T, TANG C A. Microcrack statistics, Weibull distribution and micromechanical modeling of compressive failure in rock [J]. Mechanics of Materials, 2006, 38: 664-681.
[9] KRAJCINOVIC D, SILVA M A G. Statistical aspects of the continuous damage theory [J]. International Journal of Solids and Structures, 1982, 18(7): 551-562.
[10] CAO Wen-gui, ZHAO Ming-hua, TANG Xue-jun. Study on simulation of statistical damage in the full process of rock failure [J]. Chinese Journal of Geotechnical Engineering, 2003, 25(2): 184-187. (in Chinese)
[11] HAO S W, WANG H Y, XIA M F, KE F J, BAI Y L. Relationship between strain localization and catastrophic rupture [J]. Theoretical and Applied Fracture Mechanics, 2007, 48: 41-49.
[12] ZHANG Ping, LI Ning, HE Ruo-lan. Research on localized progressive damage model for fractured rocklike materials [J]. Chinese Journal of Rock Mechanics and Engineering, 2006, 25(10): 2043-2050. (in Chinese)
[13] MARTIN C D, CHANDLER N A. The progressive fracture of Lac du Bonnet granite [J]. International Journal of Rock Mechanics and Mining Sciences & Geomechanics Abstracts, 1994, 31(6): 643-659.
[14] SWOBODA G. Program system final-finite element analysis program for linear and nonlinear structures. Version 7.1 [M]. Innsbruck: Publisher of Innsbruck University, 2001.
[15] GEHLE C, KUTTER H K. Breakage and shear behaviour of intermittent rock joints [J]. International Journal of Rock Mechanics and Mining Sciences, 2003, 40(5): 687-700.
Foundation item: Project(50708034) supported by the National Natural Science Foundation of China; Project(20060400263) supported by China Postdoctoral Science Foundation; Project(2007RS4031) supported by the Provincial Science and Technology Plan of Hunan, China
Received date: 2007-10-09; Accepted date: 2008-03-18
Corresponding author: ZHANG Ping, Associate Professor, PhD; Tel: +86-731-6710353; E-mail: zp_75@163.com
(Edited by YANG Hua)
- Strength evolution law of cracked rock based on localized progressive damage model
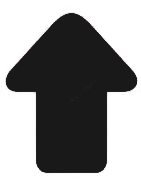