J. Cent. South Univ. Technol. (2007)03-0315-04
DOI: 10.1007/s11771-007-0062-8
Influence of isochronal heat treatment on damping behavior of AZ61 alloy
LIU Chu-ming(刘楚明)1,2, LIU Zi-juan(刘子娟)1, ZHU Xiu-rong(朱秀荣)3, HU Bi-wen(胡必文)4,
WANG Rong(王 荣)2, WANG Meng-jun(王孟君)4
(1. School of Materials Science and Engineering, Central South University, Changsha 410083, China;
2. State Key Laboratory of Material Processing and Die & Mould Technology, Wuhan 430074, China;
3. Light Materials Institute, Ningbo Branch of Enginery Science Academy of China, Ningbo 315103, China;
4. Testing Technology Institute of Yichang, Yichang 443003, China)
Abstract:
Strain amplitude dependence of the logarithmic decrement was measured and studied on an AZ61 magnesium alloy at room temperature. Measurements were carried out before and after isochronal thermal treatment step by step with increasing temperature. For all specimens, the strain dependence of the logarithmic decrement exhibits two regions. At lower strains the logarithmic decrement is strain independent and in the higher strain region it depends strongly on strain amplitude. The strain-independent logarithmic decrement is mainly composed of thermoelastic damping and dislocation damping, which can be explained by Granato-Lücke theory. In addition, the strain-independent logarithmic decrement for the specimens annealed at higher temperatures is a little lower than that for as-cast specimen, and it increases with increasing temperature of heat treatment. Microstructure changes due to heat treatment are responsible for changes of the logarithmic decrement.
Key words:
AZ61 magnesium alloy; heat treatment; damping; dislocation;
1 Introdution
Numerous problems in engineering are caused by mechanical vibrations, therefore there is a need for lightmass materials that exhibit simultaneously high damping capacity and good mechanical properties, such as a high modulus, a high mechanical strength, good creep resistance or good fatigue resistance. Pure magnesium has the highest damping capacity owing to the easy motion of dislocations at room temperature[1], while its low strength limits its application as structural material. Introducing alloying elements and precipitates that are able to pin the dislocations can avoid plastic deformation and thereby can increase the tensile strength[2]. Within the magnesium alloys with aluminum and zinc as alloying elements, AZ61 alloy appears. In fact, even if this alloy is widely used in industry, some of its damping (internal friction) and elastic capacities are still not understood.
In the present investigation, the influence of isochronal heat treatment on damping behavior of an AZ61 magnesium alloy was studied.
2 Experimental
The alloy used was a commercial Mg-Al-Zn alloy obtained through semi-continuous casting with chemical composition of Mg-5.81Al-0.55Zn-0.29Mn (mass fraction, %). Test specimens for damping measurements were machined to bending beams with a length of 30 mm, a width of 3 mm and a thickness of 1 mm. Then the specimens were isochronally annealed for 1 h in a thermostated furnace filled with sublimed sulfur and then quenched in water at room temperature. The annealing temperature ranged from 453 to 773 K and increased in step of 80 K. The damping and elastic properties were measured as a function of the strain amplitude by employing a dynamic mechanical analyzer(DMA) at a vibration frequency of 20 Hz in forced mode at room temperature in air, and the vibration of strain amplitude was increased from 1×10-5 to 4×10-3. In the forced mode and for cases of relatively small damping capacity, the damping capacity (δ, also called logarithmic decrement) is given by [3]:
δ=π?tan θ (1)
where θ is the phase lag between the strain and the applied stress.
The quantitative change of solute atoms in the Mg matrix caused by isochronal annealing can be explored by employing electrical conductivity (EC) test[4]. EC measurements were performed at room temperature by using an eddy-current conductivity meter. The samples under different heat treatment conditions for EC tests were cylinders of 10 mm in radius and 2 mm in length.
3 Results and discussion
Fig.1 shows the plots of the logarithmic decrement against the strain amplitude ε. For clarity, only three curves are plotted in Fig.1(a), and the part of lower strain amplitude and that of higher strain amplitude are amplified in Figs.1(b) and (c), respectively. It can be seen that these curves exhibit two regions. In the lower strain amplitudes, i.e. for a strain from 2×10-5 to 1×10-3, the logarithmic decrement is only weakly dependent on the strain amplitude. Above a certain strain (ε≈10-3), the logarithmic decrement becomes strongly amplitude dependent. This type of dependence demonstrates that dislocation damping is present in AZ61 alloy[5].
Fig.1 Amplitude dependence of damping for AZ61 alloy (b) and (c) Amplified parts of (a)
Above results can be explained by a break away mechanism of dislocation segments from weak pinning points according to the model outlined by GRANATO and L?CKE[5-6]. In this model, a dislocation segment is assumed to remain solidly anchored at strong pinners determining the loop length LN. For small oscillating stresses the dislocation bows out between the weak pinners with mean distance LC, leading to the amplitude independent damping δ0. When the strain amplitude of the alternating vibration becomes larger than a critical strain, the dislocation segments will break away from this weak pinning points and, catastrophically, from all other weak pinners contained within LN, leading to a drastic instantaneous increase in dislocation damping.
3.1 Strain-independent damping
The measured strain-independent damping δ0 is superimposed by three different kinds of damping[7]:
δ0=δt+δa+δd (2)
where δt is the thermoelastic damping caused by heat flow from the compressed to the dilated surface[8], δa the apparatus damping, and δd the dislocation damping mainly of dislocation movement origin.
Light metals have high thermoelastic damping due to high coefficients of thermal expansion and low thermal conductivity[9]. Because of inhomogeneous stress distribution, a temperature gradient occurs between the compressed and the extended surface of the specimen, which leads to a transverse heat flow[3,9]. This causes damping δt that is sensitive to the frequency of vibration and is given by the following equation[8]:
=
=
,
(3)
where δmax is the maximum damping at frequency f0 and can be calculated by elastic modulus E, the coefficient of linear thermal expansion α, the absolute temperature T and the specific heat capacity C. f0 depends on the thickness a of the specimen and the thermal conductivity κ. Using the data for AZ61 alloy(E=45 GPa[10], α=27.2×10-6 K-1[10], C=1.89×106 J?cm-3?K-1[11], κ=80 J?s-1?m-1?K-1[11]), the thermoelastic damping is calculated to be 4.37×10-3. The apparatus damping δa caused by the mechanical coupling between the bending beam vibrations and the experimental setup could be estimated as 0.75×10-3 using damping measurements of low-damping materials. The remaining strain- independent damping δd is mainly influenced by the movement of dislocations and their interaction with weak pinners.
The strain-independent damping δd has been calculated according to Eqn.(2). With respect to the model of Granato and Lücke, δd can be written as[5-6]
δd (4)
where ρ is the dislocation density. According to Eqn.(4), is proportional to the mean dislocation length LC between two weak pinners. Values of
of the specimens are listed in Table 1. From Table 1 it can be seen that, the values of
for specimens annealed at 613, 693 and 773 K are lower than that for other specimens. This is reasonable because for Mg-6Al alloy Mg17Al12 phase begins to dissolve into (Mg) matrix when the annealing temperature reaches about 593 K according to the Mg-Al equilibrium phase diagram[11]. Therefore there will be more solute atoms and lower dislocation distance LC in (Mg) matrix when the specimens are annealed at temperatures above 613 K. In addition, the dislocation density may decrease during the annealing process, and apparently the quantitative variation of dislocation is very small compared with that of the solute atoms. The fact that there are more solute atoms in (Mg) matrix of specimens annealed at higher temperatures can also be confirmed by the microstructures (Fig.2) and the electrical conductivity test results (Table 1). It can be observed from Fig.2 that Mg17Al12 phase mainly dissipated along the grain boundaries gradually disappear with increasing the temperature. And it can be seen from Table 1 that the electrical conductivity value of the specimen annealed at 773 K is the lowest as a result of the highest density of defects (solute atoms), while that of the specimens annealed at 453 K and 533 K is higher and that of the specimens annealed at 613 K and 693 K is moderate.
Table 1 values and electrical conductivity of specimens
It should be noted that the specimens annealed at 453 K and 533 K have a bit higher value than the as-cast specimen. An explanation of this phenomenon may be that some impurity atoms and vacancies will slightly move and leave the dislocation cores during heat treatment[7], thereby LC will be slightly increased. This effect, however, may be covered by the dissolution of the
Fig.2 Microstructures of as-cast(a) and isochronally annealed specimens( (b) 453 K; (c) 773 K)
second phase, which results in increase of number of impurity atoms, when annealing temperature is higher.
3.2 Strain-dependent damping
For higher strain amplitudes, the sweeping motion of the dislocation segment (LN) pinned by strong pinners plays a main role in the increase of the logarithmic decrement. It can be seen from Fig.1(c) that at the same strain, the higher the annealing temperature, the higher the logarithmic decrement the specimens show, and the logarithmic decrement of the as-cast sample is the lowest. The strain-amplitude dependence of the logarithmic decrement δH can be calculated using the following relationship[5-6]:
δH=(C1/ε)exp(-C2/ε) (5)
,
(6)
where ε is the strain amplitude, E is the elastic modulus, b is the magnitude of the Burger vector, FB is the binding force between a dislocation and a solute atom (weak pinning point). C1 and C2 are constants that can be experimentally estimated. Since the compositions of specimens are the same, the parameters in Eqn.(6) except LN and LC can be treated as constants.
If experimental results are plotted as ln (δH?ε) against 1/ε, one may obtain information on the concentration of weak and strong pinning points[12]. According to the Granato-Lücke theory, the dependence of ln(δH?ε) as a function of 1/ε (G-L plot) would be linear. The G-L plots based on experimental results are shown in Fig.3 and values of C1 and C2 obtained according to the relation are given in Table 2.
Table 2 Values of C1 and C2 of specimens
Fig.3 G-L plots of AZ61 alloy at room temperature
It can be observed that with the increase of annealing temperature, C2 values change slightly, while C1 values change rapidly. This may be because heat treatment has a greater influence on the parameter LC than on the parameter LN. The as-cast specimen and specimens annealed at lower temperatures have lower C1 values, while the other specimens annealed at higher temperatures have higher C1 values and the values increase with increasing the temperature. This may be explained by the dissolution of Mg17Al12 phase into (Mg) matrix, because Mg17Al12 phase acts as one kind of strong pinning points, and with its dissolution into the matrix when the annealing temperatures reach or are higher than 613 K the number of strong pinning points decreases, which results in the extension of LN[13].
4 Conclusions
1) For all specimens, the strain dependence of the logarithmic decrement exhibits two regions. At lower strains the logarithmic decrement is strain independent and in the higher strain region it depends strongly on strain amplitude. The strain-independent logarithmic decrement is mainly composed of thermoelastic damping and dislocation damping, which can be explained by Granato-Lücke theory.
2) The heat treatment causes the dissolution of Mg17Al12 phase into matrix, which leads to the increase of weak pinners and the decrease of strong pinners. Therefore, the strain-independent logarithmic decrement for the specimens annealed at higher temperatures is slightly lower than that for cast specimen, while the strain-dependent logarithmic decrement is higher and increases with increasing temperature of heat treatment.
References
[1] LAMBRI O A, RIEHEMANN W, TROJANOV? Z. Mechanical spectroscopy of commercial AZ91 magnesium alloy[J]. Scripta Materialia, 2002, 45: 1365-1371.
[2] MAYENCOURT C, SCHALLER R. Mechanical-stress relaxation in magnesium-based composites[J]. Materials Science and Engineering, 2002, A325: 286-291.
[3] HIROYUKI W, TOSHIJI M, MASAMI S, et al. Elastic and damping properties from room temperature to 673 K in an AZ31 magnesium alloy[J]. Scripta Materialia, 2004, 51: 291-295.
[4] CERRI E, BARBAGALLO S. The influence of high temperature on aging kinetics of a die cast magnesium alloy[J]. Materials letters, 2002, 56: 716-720.
[5] GRANATO A, L?CKE K. Theory of mechanical damping due to dislocations[J]. Journal of Applied Physics, 1956, 27: 583-593.
[6] GRANATO A, L?CKE K. Application of dislocation theory to internal friction phenomena at high frequencies[J]. Journal of Applied Physics, 1956, 27: 789-805.
[7] G?KEN J, RIEHEMANN W. Dependence of internal friction of fibre-reinforced and unreinforced AZ91 on heat treatment[J]. Materials Science and Engineering A, 2002, A324: 127-133.
[8] NOWICK A S, BERRY B S. Anelastic Relaxation in Crystalline Solids[M]. New York: Academic Press, 1972: 500.
[9] G?KEN J, RIEHEMANN W. Thermoelastic damping of the low density metals AZ91 and DISPAL[J]. Materials Science and Engineering A, 2002, A324: 134-140.
[10] ZHOU Hai-tao. Study of Plastic Deformation Behavior at Elevated Temperature and Tube Hot Extrusion of AZ61 Magnesium Alloy[D]. Shanghai: Shanghai Jiaotong University, 2004.
[11] AVEDESIAN M M, BAKER H. Magnesium and Magnesium Alloys[M]. ASM International, 1999: 75.
[12] TROJANOV? Z, LUK?C P, RIEHEMANN W, et al. Influence of rapid solidification on the damping behaviour of some magnesium alloys[J]. Materials Science and Engineering A, 1997, A226/228: 867-870.
[13] ZHANG Zhen-yan, ZENG Xiao-qin, DING Wen-jiang. The influence of heat treatment on damping response of AZ91D magnesium alloy[J]. Materials Science and Engineering, 2005, A392: 150-155.
(Edited by YANG Bing)
Received date: 2006-07-24; Accepted date: 2006-10-27
Corresponding author: LIU Chu-ming, PhD, Professor; Tel: +86-731-8830257; E-mail: CMLiu@mail.csu.edu.cn
- Influence of isochronal heat treatment on damping behavior of AZ61 alloy
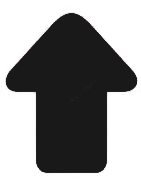