Microstructure and tensile properties of AM50A magnesium alloy prepared by recrystallisation and partial melting process
ZHAO Zu-de(赵祖德), CHEN Qiang(陈 强), HUANG Shu-hai(黄树海),
KANG Feng(康 凤), WANG Yan-bin(王艳彬)
Southwest Technique and Engineering Institute, Chongqing 400039, China
Received 13 May 2010; accepted 25 June 2010
Abstract:
Prior to thixoextrusion, the microstructural evolution of semi-solid AM50A magnesium alloy prepared by the recrystallisation and partial remelting (RAP) route was investigated. The effect of compressive ratio on microstructure of semi-solid AM50A magnesium alloy was studied. Furthermore, tensile properties of thixoextruded components were determined. The results showed that the occurrence of recrystallised grains was closely associated with the location of the first liquid formed above the solidus. With prolonging holding time, deformed microstructure was penetrated, causing fragmentation, which resulted in the decrease of average grain size. Moreover, prolonging holding time was favorable for the improvement of the degree of spheroidization due to the increase in the amount of liquid. With the increase in compressive ratio, the size of solid grain decreased, the degree of spheroidization was improved during partial remelting, and the tensile properties of thixoextruded AM50A components were improved. The tensile properties for AM50A magnesium alloy thixoextruded from starting material produced by the RAP route were better than those of the same alloy produced by die-casting and thixomolding.
Key words:
AM50A magnesium alloy; semi-solid; microstructure; mechanical properties;
1 Introduction
Magnesium is a promising structural light material because of its low density, good recyclability and abundant resources[1-4]. Most magnesium alloy products are processed by high pressure die-casting (HPDC). However, die-cast magnesium alloy components suffer from low engineering performance due to the existence of inherent defects, such as porosity, hot cracks and oxide inclusions introduced by HPDC[5]. Furthermore, HPDC components suffer from gas porosity, which not only limits their use in safety-critical applications but also denies the opportunity for further hardening by heat treatment[6].
Thixoextrusion is one type of thixoforming. It is no longer a novelty, but rather a powerful technology for extruding alloys in the semi-solid state to near net shaped products[7-9]. In the thixoextrusion, the alloy is only partially melted and the shrinkage is much less than that of a fully molten alloy. Furthermore, the die filling process can be controlled to eliminate porosity, due to the high viscosity of semi-solid alloys[7]. The thixoextrusion requires starting material which has been treated in such a way that when it is in the semi-solid state the microstructure is spheroidal rather than dendritic. There are various routes to achieve this, such as semi-solid thermal transformation (SSTT), grain refinement, near-liquidus casting, strain induced melt activation (SIMA) and recrystallisation and partial melting (RAP)[10]. The RAP route involves working, e.g. extrusion, below the recrystallisation temperature followed by reheating to the semi-solid state. Recrystallisation occurs during the reheating, and liquid penetrates the recrystallised boundaries to give the required spheroidal microstructure[10].
Although many works have been reported on the microstructure evolution of magnesium alloys in the semi-solid state, including AZ91D[11] and AZ31B[12], there have been few report on microstructure evolution and mechanical properties of predeformed AM50A magnesium alloy. In this work, we examine the microstructure evolution of AM50A magnesium alloy produced by the RAP route that is used to provide starting material for subsequent thixoextrusion. Then, the effect of predeformation on microstructure of the alloy is investigated in the semi-solid state. Furthermore, results on tensile mechanical properties of thixoextruded AM50A magnesium alloy are also presented.
2 Experimental
The material used in the present study was an AM50A magnesium alloy. From the results of the DSC analysis, AM50A alloy is shown to have a melting range of 573-633 °C. Fig.1 shows the liquid volume fraction obtained from the DSC method. Before compression, as-cast rods were machined into billets with a diameter of 70 mm and a length of 80 mm. Then, these billets were preheated at 250 °C for 30 min isothermal holding in an electric resistance furnace. During compression, these billets were compressed with different compressive ratios between 20% and 50%. The strain was determined by ε=∑εi, where εi=(h0-h)/h0, h0 is the original height and h is the height after compression. After compression, compressed billets were quenched in cold water at room temperature. Samples with a diameter of 8 mm and a length of 12 mm were cut from compressed billets. A hole of 1.5 mm in diameter was drilled into the centre of each sample to insert a thermocouple for monitoring the temperature of the samples. The samples were heat treated isothermally at 600 °C (φL=15%) for 5-25 min. On removal from the furnace, the samples were immediately quenched in cold water.
Fig.1 Liquid volume fraction against temperature estimated by DSC method
For the thixoextrusion, slugs of 58 mm in diameter and 40 mm in length were cut from the compressed billets with different compression ratios. The slugs were rapidly induction heated to 600 °C (φL=15%) for 10 min isothermal holding. During isothermal holding, argon was used as a protective atmosphere and the slugs were heated at a rate of 120 °C/min in a medium frequency induction coli. The temperature of the slug during heating was controlled with two K-type thermocouples, located at a depth of 10 mm from the top of the slug, one in the centre and the other 4 mm from the outer surface. The thermocouples were rapidly withdrawn from the slug and the slug was put into the die just before thixoextrusion. The thixoextrusion operation was carried out with a hydraulic press. The press was used to provide the maximum forging load of 500 t and the maximum velocity of ram was 300 mm/s. The preheating temperature of the die was 400 °C. Graphite was used as a lubricant. During the thixoextrusion, the pressure exerted by the ram on the slug was rapidly increased to a pre-determined level of 350 MPa and kept at this level for 40 s. The ram velocity was 300 mm/s.
Samples were ground and then etched in a solution of 100 mL ethanol, 6 g picric, 5 mL acetic and 10 mL water. The average solid grain size and shape factor were measured from resulting microstructures using an image analysis system. Moreover, the microstructure of as-cast AM50A alloy was examined by X-ray diffraction (XRD) analysis. Samples for tensile tests were machined from the lateral part of thixoextruded components and were tested using an Instron 5569 material testing machine. Fig.2 shows the thixoextruded component. Each tensile value is the average of three measurements.
Fig.2 Thixoextruded AM50A magnesium alloy component
3 Results and discussion
3.1 Microstructures of as-cast and compressed AM50A magnesium alloys
Fig.3 shows XRD pattern of as-cast AM50A magnesium alloy. It was indicated that as-cast AM50A magnesium alloy consisted of α-Mg matrix and β-Mg17Al12 phase. As shown in Fig.4, the β-Mg17Al12 phase precipitated as discontinuous network at grain boundaries. The presence of eutectic in the microstructure was attributed to non-equilibrium solidification caused by the fast cooling rate of conventional casting processes. Fig.5 shows the microstructures of compressed AM50A magnesium alloy with different compressive ratios. As shown in Fig.5(a), after being compressed with a small ratio of 20%, the deformation mainly occurred in the α-Mg. A network of brittle β-Mg17Al12 around the primary α-Mg almost kept its shape. With increasing the compressive ratio, it could be observed that the α-Mg slightly oriented in the direction vertical to the compressive direction. When the compressive ratio reached 40%, brittle β-Mg17Al12 phase ruptured and distributed over the grain boundaries like strings and showed a remarkable orientation along the deformation direction. When the compressive ratio reached 50%, the deformation structure consisted of elongated and unrecrystallised grains, which oriented in the deformation direction. It could be seen from Fig.5 that the grains were unrecrystallised and were elongated. The compressed AM50A magnesium alloys can, therefore, be classified as being consistent with the RAP route.
Fig.3 XRD pattern of as-cast AM50 magnesium alloy
Fig.4 Microstructure of as-cast AM50A magnesium alloy
3.2 Microstructure evolution of compressed AM50A magnesium alloy during partial remelting
Fig.6 shows the microstructure evolution of compressed AM50A magnesium alloy with 50% compressive ratio during partial remelting. As shown in Fig.6(a), there were some spheroidal grains, unrecrystallised massive structure and pools of liquid. The dark areas in Fig.6(a) were assumed to be quenched liquid from of EDS result (see Fig.7). As shown in Fig.7, the energy dispersive spectra displayed increased levels of aluminum and magnesium in the boundary phase compared with the matrix, confirming that this was quenched liquid. SEM observation indicated that the appearance of quenched liquid at grain boundaries was alveolate- and snowflake-like. Careful examination of Fig.6(a) indicated recrystallised grains surrounded by liquid were subjected to spheroidization and incipient spheroidal grains were associated with pools of liquid. With prolonging holding time, high angle boundaries between solid grains were penetrated causing fragmentation and the microstructure was almost fine, spheroidal solid grains, with average grain size of 85 μm (Fig.6(b)). Comparison of Figs.6(a)-(d) indicated recrystallised grains became more spheroidal and the amount of liquid increased with prolonging holding time. Fig.8 shows the variations of the solid grain size and shape factor with the isothermal holding time for the compressed AM50A magnesium alloy with 50% compressive ratio. It was shown that in the compressed alloy, the solid grain size decreased initially, then increased as the holding time increased (Fig.8). Shape factor measurement (Fig.8) showed that solid grains tended to become increasingly spheroidal after 5 min.
Fig.5 Microstructures of compressed AM50A magnesium alloy with different compressive ratios: (a) 20%; (b) 30%; (c) 40%; (d) 50%
Fig.6 Microstructure evolution of compressed AM50A magnesium alloy with 50% compressive ratio partially remelted at 600 °C for different time: (a) 5 min; (b) 10 min; (c) 20 min; (d) 25 min
Fig.7 Scanning electron micrograph (a) and corresponding EDS spectra ((b) and (c)) of compressed AM50A magnesium alloy with 50% compressive ratio heated at 600 ?C for 5 min and quenched in cold water
Fig.8 Variations of solid grain size and shape factor with isothermal holding time for compressed AM50A magnesium alloy with 50% compressive ratio partially remelted at 600 °C
According to Fig.5, the microstructure of deformed AM50A magnesium alloy was unrecrystallised. On reheating to above the solidus, the first reaction to occur was the melting of the grain boundary eutectic phases. Because of non-homogeneity of grain boundary eutectic phases, the initial formation of liquid non-homogeneously occurred. The evidence in Fig.6(a) was that recrystallisation was clearly associated with the initial formation of liquid. It appeared that the formation of liquid stimulated the recrystallisation. With prolonging holding time, the unrecrystallised structures touched liquid and the liquid tended to penetrate unrecrystallised structures causing fragmentation. Fragmentation resulted in the decrease of average grain sizes (Fig.8). With further prolonging holding time, recrystallised grains coarsened, which resulted in the increase of average recrystallised grain size. Spheroidization is a diffusion-controlled process[13-14]. With increasing the amount of liquid phase, the corners and edges of the solid grains would melt and the distance between solid grains increased, thus the probability of coalescence decreased. Therefore, the degree of spheroidization was improved (Fig.8).
3.3 Effect of compressive ratio on microstructure during partial remelting
Fig.9 shows the microstructures of as-cast and compressed AM50A magnesium alloys with different compressive ratios isothermally treated at 600 °C for 10 min. As shown in Fig.9(a), the microstructure of as-cast AM50A magnesium alloy after partial remelting consisted of irregular solid grains with mean solid grain size of 150 μm. The solid grain size in the as-cast alloy was not accepted as a suitable size for thixoextrusion because large and irregular solid grains tended to inhibit flow into narrow sections in dies. Compared with Fig.9(a), the grains had obviously undergone spheroidization although the recrystallisation was underway (Fig.9(b)). With increasing the compressive ratio, solid grains became gradually more spheroidal and the high-energy grain boundaries of recrystallised grains were penetrated by liquid phase, leading to the entire fragmentation of original grains to small equiaxed solid grains (Fig.9(c)). Careful examination of the microstructure revealed that these newly-formed equiaxed solid grains had undergone a significant degree of spheroidization. With further increase of the compressive ratio, after partial remelting, the fragmentation of recrystallised microstructure following preferential melting at grain boundaries resulted in a billet containing fine, spheroidal solid grains (Figs.9(d)-(e)). Fig.10 shows the variations of solid grain size and shape factor with the compressive ratio. As shown in Fig.10, the increase in the compressive ratio resulted in the decrease of solid grain size. However, the predeformation had a slight effect on the decrease of solid grain size with the increase of compressive ratio from 40% to 50%. It can also be seen from Fig.10 that the increase of compressive ratio promoted the degree of spheroidization.
Comparison of Figs.9(a)-(e) indicated that the higher compressive ratio gave a finer recrystallised grain size. The fine recrystallised grain size in turn resulted in the finer solid grain size during partial remelting. The higher the compressive ratio, the more heavily regions distorted. This resulted in creating more locations of recrystallisation nucleation[14]. On the other hand, with increasing the compressed ratio, more stored energy in the form of residual strain was deposited in the alloy. The stored energy would supply the driving force for recrystallisation during reheating. The more the stored energy, the finer the recrystallised grain size. The increase of compressive ratio was also favorable for the improvement of the degree of spheroidization. With increasing the compressive ratio, the state of compressed alloy was more thermodynamically unstable in the semi-solid state, which promoted diffusion rate. The rapid diffusion rate in turn enhanced the rate of liquation and fragmentation. Due to the rapid formation of liquid phase, the dissolution-reprecipitation mechanism driven by the presence of variable curvature on the surface of each solid grain contributed to the improvement of the degree of spheroidization.
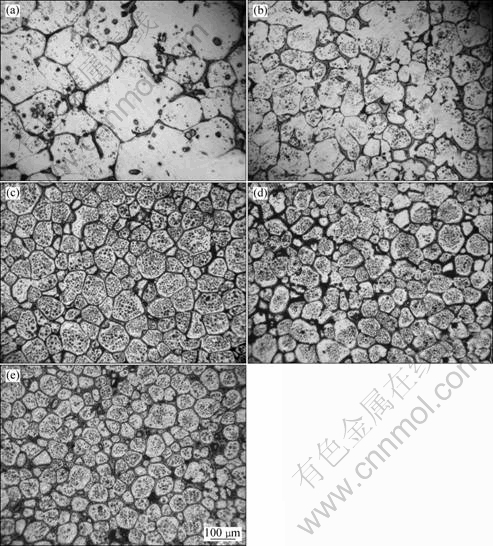
Fig.9 Microstructures of predeformed samples at 250 °C with different compression ratios after isothermal holding at 600 °C for 10 min: (a) 0%; (b) 20%; (c) 30%; (d) 40%; (e) 50%
Fig.10 Variations of solid grain size and shape factor with compressive ratio
3.4 Tensile mechanical properties of thixoextruded AM50A magnesium alloy
Fig.11 shows the mechanical properties of the thixoextruded AM50A magnesium alloys under different conditions. As shown in Fig.11, with increasing compressive ratio, the tensile properties of thixoextruded AM50A magnesium alloy components were improved. The shape and distribution of β-Mg17Al12 and the solid grain size exerted a significant influence on tensile properties of thixoextruded components. In the as-cast alloy, β-Mg17Al12 discontinuously distributed on grain boundaries. The body-centered cubic structure of β-Mg17Al12 was incompatible with the hexagonal close- packed structure of α-Mg matrix, which resulted in the fragility of Mg/Mg17Al12 interface. During plastic deformation, the brittle β-Mg17Al12 was ruptured due to the metal flow. When the predeformed alloy was reheated, β-Mg17Al12 was firstly remelted and uniformly surrounded solid grains. The disappearance of discontinuous β-Mg17Al12 was favorable for the improvement of ductility. On the other hand, with increasing compressive ratio, more energy was stored in the alloy. During partial remelting, more recrystallised solid grains were obtained. Since solid grain boundaries were effective obstacles to dislocation motion, and since small-grained alloy would have a higher density of grain boundaries per unit volume, the tensile properties were improved with decreasing solid grain size. The mechanical properties of the thixoextruded AM50A magnesium alloy produced by the RAP route (50% compressive ratio) are listed in Table 1, and compared with those of the same alloy produced by the other processes in the Ref.[15]. As shown in Table 1, the thixoextruded AM50A magnesium alloy exhibited higher ultimate tensile strength (UTS) and yield strength (YS) than die-cast and thixomolded alloy. In the die-casting process, continuous β-Mg17Al12 network was found in the alloy, which was deleterious to mechanical properties. In the thixomolding process, although solid grains were homogeneously surrounded by liquid, the microstructure still had porosity. For the alloy prepared by the RAP route, some casting deficiencies, such as gas pores, hot cracks and microstructural non-uniformity, have been eliminated or reduced during compression with 50% compressive ratio. Second, the RAP route omitted the procedure of molten metal treatment and the oxidation and combustion problems of Mg alloys could be effectively eliminated. Moreover, the RAP route was shown to produce ideal, fine and homogeneous semi- solid microstructures, in which completely spheroidal primary solid grains were entrapped with a little amount of liquid. Therefore, it was reasonable for the RAP alloy to exhibit excellent mechanical properties.
Fig.11 Mechanical properties of thixoextruded AM50A magnesium alloy with different compressive ratios
Table 1 Mechanical properties of AM50A magnesium alloys prepared by different processes
4 Conclusions
1) Compression below the recrystallisation temperature followed by partial remelting, which belongs to the recrystallisation and partial remelting (RAP) route, is an effective method to produce semi-solid AM50A magnesium alloy billet for thixoextrusion. During partial remelting, the microstructure evolution of AM50A magnesium alloy predeformed by 50% compression could be divided into four stages: the recrystallisation of deformed microstructure, the fragmentation of recrystallised grains caused by liquid penetration, spheroidization due to partial remelting of solid grains and final solid grain coarsening.
2) The microstructure of AM50A magnesium alloy during partial remelting could be improved effectively by pre-deformation. The microstructure of as-cast alloy during partial remelting showed irregular shape and large size. However, with the increase in compressive ratio, the size of solid grain decreased and the degree of spheroidization was improved during partial remelting.
3) With increasing compressive ratio, the tensile properties of thixoextruded AM50A components were improved. The tensile properties for AM50A magnesium alloy thixoextruded from starting material produced by the RAP route were better than those of the same alloy produced by die-casting and thixomolding.
References
[1] LIN H Q, WANG J G, WANG H Y, JIANG Q C. Effect of predeformation on the globular grains in AZ91D alloy during strain induced melt activation (SIMA) process [J]. J Alloys Compd, 2007, 431: 141-147.
[2] ZHANG Q Q, CAO Z Y, LIU Y B, WU J H, ZHANG Y F. Study on the microstructure evolution and rheological parameter of semi-solid Mg-10Al-4Zn alloys [J]. Mater Sci Eng A, 2008, 478: 195-200.
[3] YANG M B, PAN F S, CHENG R J, SHEN J. Effects of holding temperature and time on semi-solid isothermal heat-treated microstructure of ZA84 magnesium alloy [J]. Trans Nonferrous Met Soc China, 2008, 18(3): 566-572.
[4] CHINO Y, KOBATA M, IWASAKI H, MABUCHI M. An investigation of impressive deformation for AZ91 Mg alloy containing a small volume of liquid [J]. Acta Mater, 2003, 51: 3309-3318.
[5] WANG Y, LIU G, FAN Z. Microstructural evolution of rheo-diecast AZ91D magnesium alloy during heat treatment [J]. Acta Mater, 2006, 54: 689-699.
[6] BIROL Y. Comparison of thixoformability of AA6082 reheated from the as-cast and extruded states [J]. J Alloys Compd, 2008, 461: 132-138.
[7] CHAYONG S, ATKINSON H V, KAPRANOS P. Multistep induction heating regimes for thixoforming 7075 aluminum alloy [J]. Mater Sci Tech, 2004, 20: 490-496.
[8] ASHOURI S, NILI-AHMADABADI M, MORADI M, IRANPOUR M. Semi-solid microstructure evolution during reheating of aluminum A356 alloy deformed severely by ECAP [J]. J Alloys Compd, 2008, 466: 67-72.
[9] ATKINSON H V. Modelling the semisolid processing of metallic alloys [J]. Prog Mater Sci, 2005, 50: 341-412.
[10] ATKINSON H V, BURKE K, VANEETVELD G. Recrystallisation in the semi-solid state in 7075 aluminium alloy [J]. Mater Sci Eng A, 2008, 490: 266-276.
[11] ZHANG Q Q, CAO Z Y, ZHANG Y F, SU G H, LIU Y B. Effect of compression ratio on the microstructure evolution of semisolid AZ91D alloy [J]. J Mater Process Technol, 2007, 184: 195-200.
[12] JI Z S, HU M L, SUGIYAMA S, YANAGIMOTO J. Formation process of AZ31B semi-solid microstructures through strain-induced melt activation method [J]. Mater Character, 2008, 59: 905-911.
[13] TZIMAS E, ZAVALIANGOS A. Evolution of near-equiaxed microstructure in the semisolid state [J]. Mater Sci Eng A, 2000, 289(1/2): 228-240.
[14] ATKINSON H V, BURKE K, VANEETVELD G. Recrystallisation in the semi-solid state in 7075 aluminium alloy [J]. Mater Sci Eng A, 2008, 490: 266-276.
[15] LEBEAU S, DECKER R. Microstructural design of thixomolded magnesium alloys [C]//Proceedings 5th International Conference on Semi-solid Processing of Alloys and Composites. Golden City, Colorado, 1998: 301-306.
(Edited by YANG Bing)
Foundation item: Project(51005217) supported by the National Natural Science Foundation of China
Corresponding author: CHEN Qiang; Tel: +86-23-68792284; E-mail: 2009chenqiang@163.com
DOI: 10.1016/S1003-6326(09)60350-2