- Abstract:
- 1 Introduction▲
- 2 Experimental▲
- 3 Results and discussion▲
- 4 Conclusions▲
- References
- Figure
- Fig.1 XRD pattern of ultrafine copper powder
- Fig.2 SEM images of copper powders obtained by electrodeposition at current density of 0.10 A/cm2 and different concentrations of CuSO4: (a) 0.03 mol/L; (b) 0.09 mol/L
- Fig.3 Schematic representation of formation mode of copper particles with irregular shape: (a) Ion-exchange adsorption; (b) Formation of globular micelles; (c) Reduction; (d) Formation of organic layer; (e) Copper particles with organic layer
- Fig.4 TEM images of fishbone-like copper particles obtained by electrodeposition at current density of 0.10 A/cm2 and different concentrations CuSO4: (a) 0.01 mol/L; (b) 0.05 mol/L; (c) 0.09 mol/L
- Fig.5 Schematic representation of formation mode of copper particles with fishbone-like shape: (a) Reduction of Cu2+ and formation of copper nuclei; (b) Formation of nanorods by nuclei aggregate; (c) Formation of secondary branches; (d) Formation of high classic braches
- Fig.6 Relationship among average size of copper particles, current efficiency of electrodeposition and Cu2+ concentration
J. Cent. South Univ. Technol. (2009) 16: 0708-0712
DOI: 10.1007/s11771-009-0117-0
Characterization of ultrafine copper powder prepared by
novel electrodeposition method
HE Wei(贺 玮)1, 2, DUAN Xue-chen(段学臣)1, 2, ZHU Lei(朱 磊)1, 2
(1. Key Laboratory of Nonferrous Metal Materials Science and Engineering, Ministry of Education,
Central South University, Changsha 410083, China;
2. School of Materials Science and Engineering, Central South University, Changsha 410083, China)
Abstract:
The auto-evolved ultrafine copper powders were synthesized via a novel electrodeposition route performed by ultrasonic dispersion of the electrolyte. The properties of the samples obtained were characterized by X-ray powder diffractometry (XRD), transmission electron microscopy (TEM), scanning electron microscopy (SEM) and laser size distribution analyzer (SL) respectively. The formation mechanisms of the powders and the efficiency of the elctrodeposition were discussed. The results show that the as-prepared powders are high-purity copper nanoparticles with the fcc structure taking a mixture of fishbone-like and irregular shapes. When the concentration of Cu2+ increases from 0.03 to 0.09 mol/L, the average size of copper particles increases from 0.92 to 1.80 μm, and current efficiency of electrodeposition linearly changes from 66.5% to 91.3%.
Key words:
copper powder; electrodepositon; ultrasound;
1 Introduction
An increasing attention has been paid to synthesizing the ultrafine copper powders. Due to their outstanding physical and chemical properties, the copper powders are widely used in lubricating oil, electrically conductive paste, medicine, biological filter and other purposes [1].
Ultrafine copper powders can be prepared by many methods, such as evaporation deposition [2-3], plasma approach [4], mechanochemical approach [5], electrical explosion [6], chemical reduction [7], electrodeposition [8] and microemulsion [9]. Recently, following the development of sonochemistry, considerable interest is once again paid to the technology of electrodeposition. Combining the electrodepostion with sonochemistry provides a potential method for the preparation of ultrafine metal powders [10-11]. However, the utilization of ultrasound is mainly limited to offer an ultrasonic field for the electrodepositon environment via putting the electrolytic cell into the ultrasonic cleaner or fixing the cathodes on the converter/transducer of the ultrasonic grinder. This causes huge energy expenditure and equipment loss, and cannot greatly improve the quality of the powder and the efficiency of production.
In this situation, an electrolyzing-emulsification method was proposed, during which the electrolyte ncluding oil phase is emulsified with the help of ultrasound before performing the electrodeposition [12]. Thus, not only the auto-evolution of particles from electrodes can be solved for the first time, but also a great potential can be provided to the size- and shape- control of copper powders. Nevertheless, many problems still require further study in this technology. According to Ref.[12], to realize the auto-evolution of powders, only the anion surfactant can be used as the emulsifier. However, further study finds that this kind of electrolyte cannot keep steady because of the oriented traveling of the anion surfactant during the electrodeposition process. Besides, the electrochemical process of the reaction is not very clear and the option of emulsifier still needs to be strengthened.
In this work, the electrodeposition process in ultrasonic dispersed electrolyte without oil phase was investigated and properties of the powders so-prepared were characterized by XRD, SEM, TEM and SL. On this basis, the formation mechanism of the copper particles was discussed and the influences of Cu2+ concentration on the size of copper powders and the current efficiency were analyzed.
2 Experimental
2.1 Reagents
Copper sulfate pentahyrate (CuSO4?5H2O, AR), sodium laurylsulfonate (SDS, CP) and sulfate acid H2SO4, AR) were used as starting materials without further purification.
2.2 Synthesis
Two pieces of copperplate (25 mm×130 mm) were used as the electrodes. After washing with distilled water, they were polished by waterproof sand paper and then immersed in 5% H2SO4 solution for 30 min to remove the surface oxide and finally washed again with distilled water to remove the remnant H2SO4.
The highly dispersed electrolyte was prepared by using ultrasonic wave. An ultrasonic generator (BUG25-06, Branssion, China), equipped with a cleaning trough (200 mm×300 mm×200 mm), operating at 40 kHz and the maximum power output of 600 W, was used for the ultrasonic irradiation. After CuSO4?5H2O was completely dissolved into the distilled water, SDS was added in the solution prior to be dispersed in the ultrasonic field for 5 min. H2SO4 solution was added in the above solution to improve the conductivity of the electrolyte.
The electrodeposition was performed in a beaker at 30-40 ℃. Cu2+ concentration varying from 0.03 to 0.09 mol/L was used to investigate the effect of concentration on the morphology and the size of the final products. After the completion of electrodeposition, copper powders were separated from electrolyte with a centrifuge, and washed successively with ethanol, distilled water and ethanol again. In the end, the wet powders were dried in vacuum at 80 ℃.
2.3 Characterization
The copper powders were identified by X-ray diffractometry (XRD) using a Rigaku D/Max 2500 powder diffractometer with Cu Kα radiation (λ=0.154 06 nm). The morphology of the sample was characterized by scanning electron microscopy (SEM, JSM-6360LV) and transmission electron microscopy (TEM, Philips Tecnai 20 G2 S-TWIN) respectively. The size distribution of the copper powders was estimated from the image analysis of the laser size distribution analyzer (Omec LS-POP) with measurement error less than 3% in the scale of 0.2-500 μm. The current efficiency of the electrodeposition η was calculated according to the following equation [13]:
×100% (1)
where q is the electrochemical equivalent of copper, and M, I and t represent the mass of the copper powder prepared, the current and the time of electrodepositon, respectively.
3 Results and discussion
3.1 X-ray diffraction investigation of ultrafine copper powder
The auto-evolved ultrafine copper powders were prepared by this novel eletrodeposition method. Fig.1 shows the XRD pattern of the powders prepared in 0.05 mol/L CuSO4 at a current density of 0.10 A/cm2. The diffraction peaks can be assigned to the crystal face (111), (200) and (220) of the fcc structure respectively. The measured spaces (d) are 2.089 7, 1.809 1 and 1.279 0 nm accordingly, which match closely to the JCPDS file No. 04-836 (d=2.088, 1.808 and 1.278 nm). This clearly indicates that the as-prepared powders are high-purity copper with fcc structure, and oxide copper and other impurities are less than 2%.
Fig.1 XRD pattern of ultrafine copper powder
3.2 Morphology analysis
In the conventional electrodepostion, it is very important to regularly tap the powders from cathodes manually to prevent particle growth. In this new method, the ultrasonic dispersion of the electrolyte not only achieves the auto-evolution, but also plays an important role in controlling the morphology of the particles. As shown in Fig.2, with some fishbone-like particles being observed (shown in circle), most particles present irregular shape. These are very different from those powders prepared by conventional electrodeposition. The latter has fishbone-like shape with size of several dozens of micron.
The formation of the irregular copper particles can be attributed to the dispersion of the electrolyte that is mainly modulated by a desire surfactant SDS with structure of C12H25—OSO3—Na+. To achieve the dissolution of the surfactant in water, the hydrogen bonds among H2O molecules must be cut off by huge external energy which can be offered by the ultrasonic wave. The high-temperature-pressure pluses resulting from instantaneous bubble collapse can make SDS completely dispersed and C12H25—OSO3—Cu2+ formed via ion- exchange adsorption (Fig.3(a)) [14-15]. However, owing to its hydrophilic and hydrophobic property, the C—H link of SDS has a strong trend to escape from water phase. When the concentration is slight higher than the critical micelle concentration (CMC), the surfactant molecules easily agglomerate to numerous globular micelles with net positive charge according to the lowest energy rule (Fig.3(b)) [16]. Thus, during the period of electrodeposition, these micelles move towards the cathode, and then capture electrons and make Cu2+ reduced in the near-electrode layer (Fig.3(c)). For the instability of the electrolyte in thermodynamics, the micelles collide with each other and quickly sedimentate, flocculate and agglomerate. Consequently, an organic layer can easily be coated on the surface of the copper grains, which makes the metal particles auto-evolved from the cathode, and the copper particles present irregular sharp (Figs.3(d) and (e)).
For those fishbone-like copper particles observed in Fig.2, there must have a distinct formation mechanism compared with those of irregular Cu powders. It is very difficult to prepare a monodispersed solution as surfactant micelles in some regions are insufficient to form C12H25—OSO3—Cu2+ structure. As a result, Cu2+ moves toward cathode area lonely due to electrostatic force rather than being absorbed on the surfactant micelles and transferring together. Without the restrain of the organic film, the formed Cu nuclei prefer to fabricate the fishbone-like particles as those in conventional electrodeposition. However, this growth is limited because exist there a large number of surfactant micelles in the system.
The morphology of these fishbone-like copper particles is influenced by the Cu2+ concentration as shown in Fig.4. The increase of Cu2+ concentration accelerates the formation and growth of the copper nuclei, resulting in the perfect fishbone-like particles. At Cu2+ concentration of 0.01 mol/L, only the copper nanorods with length of about 0.5 μm are produced (Fig.4(a)). At Cu2+ concentration of 0.03 mol/L, the fishbone-like particles with length of about 1.0 μm are obtained. At Cu2+ concentration of 0.09 mol/L, the secondary branches of fishbone begin to form (Fig.4(c)). A schematic illustration of major steps involved in the growth of fishbone-like copper particles is proposed in Fig.5. When the over-potential is enough, the copper nuclei prefer growing in the lowest energy direction and form copper nanorods. Then, following great increase of the nuclei, other directions also get developed and high-classic branches are formed.
3.3 Particle size of copper powder
The particle size is the most important property of the copper powders, which is influenced by the condition of the electrodeposition process. The solid line in Fig.6 shows the average size of the copper powders prepared at different Cu2+ concentrations. With the increase of Cu2+
Fig.2 SEM images of copper powders obtained by electrodeposition at current density of 0.10 A/cm2 and different concentrations of CuSO4: (a) 0.03 mol/L; (b) 0.09 mol/L
Fig.3 Schematic representation of formation mode of copper particles with irregular shape: (a) Ion-exchange adsorption; (b) Formation of globular micelles; (c) Reduction; (d) Formation of organic layer; (e) Copper particles with organic layer
Fig.4 TEM images of fishbone-like copper particles obtained by electrodeposition at current density of 0.10 A/cm2 and different concentrations CuSO4: (a) 0.01 mol/L; (b) 0.05 mol/L; (c) 0.09 mol/L
Fig.5 Schematic representation of formation mode of copper particles with fishbone-like shape: (a) Reduction of Cu2+ and formation of copper nuclei; (b) Formation of nanorods by nuclei aggregate; (c) Formation of secondary branches; (d) Formation of high classic braches
Fig.6 Relationship among average size of copper particles, current efficiency of electrodeposition and Cu2+ concentration
concentration, the average size of powders linearly changes from 0.92 to 1.80 μm.
It has been confirmed that the loose powders can evolve only when the concentration of the ion in near-electrode layer decreases to an instant value. To achieve this target, a critical condition between the current density and anion concentration must be satisfied the following equation [13]:
(2)
where J is the current density, c is the concentration of CuSO4, and K is a constant. According to Eq.(2), the lower the anion concentration is, the lower the current density is needed for the reaction. With equal energy, the higher the over-potential is, the more nuclei the system will produce. The relationship between the speed of the nucleation W and the over-potential ηk is as follows [13]:
(3)
where ρ is nuclei density, h is height of an atom, σ is interfacial tension between nuclei and solution, N is Arogadro constant, M is relative atomic mass of deposit, n is valence of metal ion, F is Faraday constant, R is critical radius of nuclei and T is reaction temperature.
The size of the metallic powders is determined by the speed ratio between nucleation and growth of nuclei. If the nucleation speed is much faster than the growth speed of nuclei, more crystal nuclei can be formed and finer powders can be obtained; otherwise, larger particle size can be induced.
It is rightly because the over-potential is decreased with the increase of Cu2+ concentration, the nucleation of the copper particles is restrained, which further increases the powder size.
3.4 Current efficiency of electrodeposition
The amount of metallic powders prepared by electrodeposition does not correspond to that calculated according to the Faraday Law. The current efficiency is proposed to evaluate the energy consumption during electrodeposition. In this experiment, the current efficiency at different Cu2+ concentrations is shown as the dash line in Fig.6. Current efficiency of 66.5% reaches at Cu2+ concentration of 0.03 mol/L, and it reaches the highest value of 91.3% at Cu2+ concentration of 0.09 mol/L. This phenomenon is explained as follows.
In electrolyte, H+ can also capture electron. And then it is reduced to H atom as the secondary reaction during the metal electrodepostion process. This greatly changes the energy consumption in practical production. As expatiated above, the increase of Cu2+ concentration decreases the over-potential, thus leading to the lessening of hydrogen and increase of the current efficiency.
4 Conclusions
(1) The auto-evolved technology of ultrafine copper powders is achieved via this novel electrodeposition route. This is totally attributed to dispersion of the electrolyte in ultrasonic field.
(2) The powders prepared are high-purity copper ones with fcc structure. They take both fishbone-like and irregular shapes. The formation mechanisms depend strongly on the distribution of surfactant in the electrolyte. Further study should focus on the option of the surfactants and uniformity of the morphology of the particles.
(3) The average size of powders increases linearly from 0.92 μm in 0.03 mol/L electrolyte to 1.80 μm in 0.09 mol/L electrolyte. The over-potential is decreased with the increase of Cu2+ concentration, which further restrains the nucleation of the copper particles and increases particle sizes.
(4) The current efficiency of electrodepostion increases linearly from 66.5% in 0.03 mol/L electrolyte to 91.3% in 0.09 mol/L electrolyte. This is resulted from the lessening of hydrogen evolution at lower over- potential.
References
[1] YU He-long, XU Yi, SHI Pei-jing. Tribological properties and lubricating mechanisms of Cu nanoparticles in lubricant [J]. Transactions of Nonferrous Metals Society of China, 2008, 18(3): 636-641.
[2] OUYANG Hong-wu, YU Wen-tao, HE Shi-wen, CHEN Xin, HUANG Jing-song. Microstructure and properties of nano-copper powders prepared by flow-levitation method [J]. The Chinese Journal of Nonferrous Metals, 2007, 17(5): 623-628. (in Chinese)
[3] SAITO M, YASUKAWA K, UMEDA T, AOI Y. Copper nanoparticles fabricated by laser ablation in polysiloxane [J]. Optical Materials, 2007, 30(7): 1201-1204.
[4] GAI Guo-sheng. Ultrafine powder technology [M]. Beijing: Chemical Industry Press, 2004: 102-106. (in Chinese)
[5] BAL?? P, GODO??KOV? E, KRIL’OV? L, LOBOTKA P, GOCK E. Preparation of nanocrystalline materials by high-energy milling [J]. Materials Science and Engineering A, 2004, 386(1/2): 442-446.
[6] KWON Y S, ILYIN A P, TIKHONOV D V, YABLUNOVSKY G V, AN V V. Characteristics of nanopowders produced by wire electrical explosion of tinned copper conductor in argon [J]. Material Letters, 2008, 62(17/18): 3143-3145.
[7] WAGNER J, TSHIKHUDO T R, KOHLER J M. Microfluidic generation of metal nanoparticles by borohydride reduction [J]. Chemical Engineering Journal, 2008, 135(S1): 104-109.
[8] YU Lin-po, SUN Hui-jiao, HE Juan, WANG Di-hua, JIN Xian-bo, HU Xiao-hong, CHEN G Z. Electro-reduction of cuprous chloride powder to copper nanoparticles in an ionic liquid [J]. Electrochemistry Communications, 2007, 9(6): 1374-1381.
[9] CASON J P, MILLER M E, THOMPSON J B. Metallic copper nanoparticle synthesis in AOT reverse micelles in compressed propane and supercritical ethane solutions [J]. Phys Chem B, 2001, 105: 2297-2301.
[10] WANG De-zhi, WANG Guang-jun, ZHOU Jie, WU Zhuang-zhi. Preparation of Mo/Cu composite powders with ultrasonic electroless plating copper [J]. Journal of Central South University: Science and Technology, 2008, 39(5): 945-950. (in Chinese)
[11] KOLTYPIN Y, KATABI G, CAO X, PROZOROV R, GEDANKEN A. Sonochemical preparation of amorphous nickel [J]. Journal of Non-Crystalline Solids, 1999, 287(3/4): 461-467.
[12] LI Miao. Research of technics and mechanism on preparing particle-controlled ultrafine copper powder by electrolyzing emulsification [D]. Chengdu: Sichuan University, 2005: 16-19. (in Chinese)
[13] HUANG Pei-yun. Theory of powder metallurgy [M]. Beijing: Metallurgical Industry Press, 2004: 86-92. (in Chinese)
[14] LI Ling. Surfactant and nanotechnology [M]. Beijing: Chemical Industry Press, 2004: 103. (in Chinese)
[15] AVVARU B, PANDIT A. Experimental investigation of cavitational bubble dynamics under multi-frequency system [J]. Ultrasonic Sonochemistry, 2008, 15(4): 578-589.
[16] TAKAGI E, MIZUKOSHI Y, OSHIMA R, NAGATA Y, BANDOW H, MAEDA Y. Sonochemical preparation of noble metal nanoparticles in the presence of various surfactants [J]. Studies in Surface Science and Catalysis, 2001, 132: 335-338.
(Edited by YANG You-ping)
Foundation item: Project(08JJ3104) support by Hunan Provincial Natural Science Foundation of China
Received date: 2008-10-06; Accepted date: 2009-03-17
Corresponding author: DUAN Xue-chen, Professor, PhD; Tel: +86-731-88830503; E-mail: d_xc@163.net
- Characterization of ultrafine copper powder prepared bynovel electrodeposition method
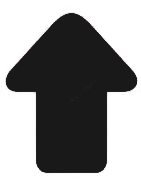